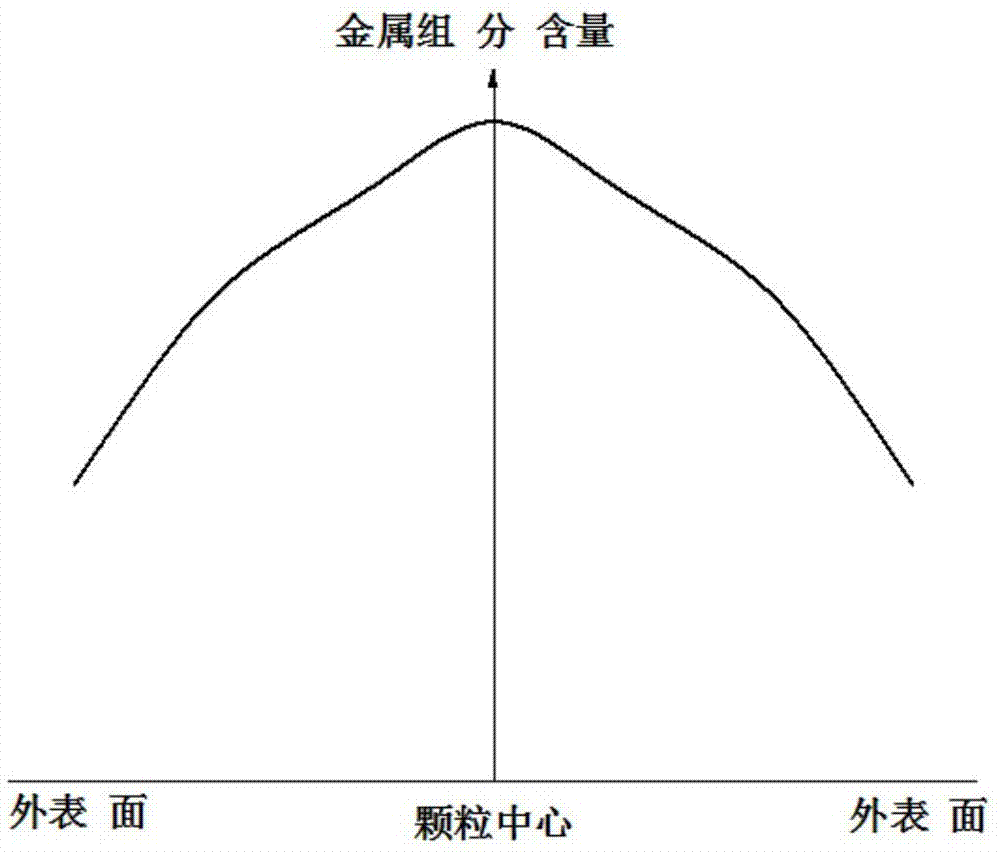
本發(fā)明是關(guān)于一種渣油加氫脫金屬催化劑及其制備方法,更具體的說是關(guān)于一種同時具有雙峰孔結(jié)構(gòu)和金屬組分梯度減少分布特征的渣油加氫脫金屬催化劑及其制備方法。本發(fā)明催化劑用于劣質(zhì)重油特別是渣油的加氫處理過程。
背景技術(shù):
:劣質(zhì)重油如渣油等含有較高的ni、v等金屬雜質(zhì),通常需要經(jīng)過加氫處理進(jìn)行脫除,以便經(jīng)過后續(xù)的加工(如催化裂化),生產(chǎn)出清潔的汽、柴油等油品和化工原料。研究表明,渣油中金屬雜質(zhì)主要存在于膠質(zhì)和瀝青質(zhì),這部分物質(zhì)分子量大、結(jié)構(gòu)復(fù)雜,擴(kuò)散困難,因此要求催化劑具有優(yōu)良的孔道結(jié)構(gòu)和良好的活性金屬分散特性,促進(jìn)大分子反應(yīng)物質(zhì)向催化劑顆粒內(nèi)部擴(kuò)散、反應(yīng)和沉積,從而獲得高的脫雜質(zhì)活性和穩(wěn)定性。一種提高催化劑擴(kuò)散性能的有效途徑是采用雙峰孔結(jié)構(gòu)載體,即催化劑同時存在直徑在10-30nm的孔道結(jié)構(gòu)和直徑在100nm以上的孔道結(jié)構(gòu)。在反應(yīng)過程中,孔直徑在100nm以上的大孔為大分子反應(yīng)物質(zhì)的擴(kuò)散提供通道,促進(jìn)雜質(zhì)向催化劑的內(nèi)部孔道擴(kuò)散和反應(yīng);而孔直徑在10-30nm的孔道則為雜質(zhì)提供反應(yīng)表面和沉積場所。兩類孔道協(xié)同作用,從而使催化劑具有高的脫金屬活性和高的容雜質(zhì)能力。cn1103009a公開了一種具有雙重孔氧化鋁載體的制備方法,該方法由兩種孔徑分布不同的氧化鋁或其前身物與炭黑粉、表面活性劑、膠溶劑和水混合成型,經(jīng)干燥和焙燒制成。當(dāng)采用炭黑粉作為擴(kuò)孔劑時,擴(kuò)孔效果較差,且載體強(qiáng)度較低,同時,膠溶劑的加入會降低載體的孔容和孔徑。cn1647857a公開了一種大孔氧化鋁載體的制備方法,該方法將含有機(jī)物擴(kuò)孔劑的擬薄水鋁石組合物進(jìn)行成型和焙燒,得到具有雙峰孔結(jié)構(gòu)的氧化鋁載體。該方法需先將有機(jī)擴(kuò)孔劑和擬薄水鋁石打漿并噴霧干燥,制備過程較為復(fù) 雜。上述方法的一個共同缺點是,所制備載體中大孔孔徑多集中在500nm以下,500nm以上以及1000nm以上孔道較少,不能最大程度的改善催化劑的擴(kuò)散性能。另外,通過優(yōu)化催化劑的活性金屬分散特性,即采用非均勻分布的方式,使催化劑中活性金屬的含量從顆粒中心至外表面逐漸降低,降低催化劑外表面處的加氫活性,從而在反應(yīng)過程中促進(jìn)渣油原料中金屬雜質(zhì)更多的向催化劑顆粒內(nèi)部沉積,避免催化劑發(fā)生孔口堵塞,以此提高催化劑容金屬能力和活性金屬利用效率,進(jìn)而提高催化劑使用壽命,確保裝置的長周期運轉(zhuǎn)。歐洲專利ep0204314提供了一種具有不均勻活性金屬組分分布的加氫處理催化劑,該催化劑采用了一種分步、多次浸漬的方法擔(dān)載活性金屬組分,即先把載體浸入到含有部分活性金屬組分的a溶液中,取出后經(jīng)水洗、干燥和焙燒,再浸入含有其它活性組分的b溶液中,取出后經(jīng)水洗、干燥和焙燒得到催化劑。由于該方法需要多次、分步浸漬、水洗和焙燒,制備過程過于復(fù)雜。專利cn101927196公開了一種活性金屬組分溶液呈梯度減少分布的加氫催化劑,其制備方法是在噴浸活性金屬溶液的過程中逐漸降低溶液中金屬組分濃度或先后噴浸濃度由高到低的不同溶液。這種方法雖然具有理論可行性,但操作難度較大,噴浸時難以保證溶液均勻噴灑至不同的載體顆粒上,所得催化劑上不同顆粒間金屬組分的梯度分布均一性較差;加之不同金屬組分其在載體孔道內(nèi)的吸附及擴(kuò)散特性存在差異,易導(dǎo)致同一催化劑顆粒內(nèi)不同區(qū)域的金屬組分配比存在差異,從而影響其催化性能。此外,現(xiàn)有氧化鋁載體制備技術(shù)中,在氧化鋁成型時均需加入諸如硝酸、醋酸、硝酸鋁等酸性物質(zhì)作為膠溶劑,而酸性物質(zhì)的加入會破壞氧化鋁的粒子結(jié)構(gòu),降低載體的孔容和孔徑。降低酸性膠溶劑對氧化鋁孔結(jié)構(gòu)的破壞是制備大孔氧化鋁載體的一種有效技術(shù)路線,如cn1154668和cn1611578均在氧化鋁混捏成型過程中加入一定的氨對膠溶酸進(jìn)行部分中和,從而達(dá)到增大載體孔容孔徑的目的,但此種方法不能徹底消除酸性物質(zhì)對載體孔結(jié)構(gòu)的不利影響,效果有限。技術(shù)實現(xiàn)要素:針對現(xiàn)有技術(shù)的不足,本發(fā)明提供一種同時具有雙峰孔結(jié)構(gòu)和金屬組分梯度減少分布特征的加氫催化劑及其制備方法,本發(fā)明方法制備的催化劑擴(kuò)散性能優(yōu)異,具有反應(yīng)活性高、容雜質(zhì)能力強(qiáng)、使用壽命長的優(yōu)點,可作為重質(zhì)油加氫催化劑特別是渣油加氫脫金屬催化劑使用。本發(fā)明提供一種渣油加氫脫金屬催化劑,其中,孔容為0.2~1.2ml/g;比表面積為40~200m2/g;孔直徑在500nm以上的孔所對應(yīng)的孔容占總孔容的比例為5%~30%,孔直徑在1000nm以上的孔所對應(yīng)的孔容占總孔容的比例為5%~15%;以氧化鋁為載體,催化劑中含有占催化劑總重量4~12%的鉬和/或鎢和0.4~4%的鈷和/或鎳的氧化物;催化劑顆粒中金屬組分濃度從顆粒中心至外面表逐漸減少;催化劑顆粒外表面與中心處金屬重量之比為0.05~0.60,0.66r處與中心處金屬重量之比為0.40~0.80,0.33r處與中心處金屬重量之比為0.60~0.95,r為以催化劑顆粒中心為初始點的催化劑的顆粒半徑。本發(fā)明還提供一種渣油加氫脫金屬催化劑的制備方法,其是上述渣油加氫脫金屬催化劑的制備方法,包括如下步驟:(1)在擬薄水鋁石干膠粉中加入非酸性粘合劑、復(fù)合擴(kuò)孔劑和水,充分混捏、成型并干燥和焙燒,得載體;(2)配制含有鉬和/或鎢和鎳和/或鈷的金屬溶液,并對(1)中所得載體以飽和浸漬的方式負(fù)載金屬;(3)采用振動流化床干燥設(shè)備對(2)中所得的顆粒物進(jìn)行預(yù)干燥,熱風(fēng)溫度控制在40~100℃,催化劑最終水含量控制在20~60%;(4)將(3)中所得物料浸于凈水中,浸入時間1~60分鐘,凈水溫度20~80℃;(5)步驟(4)中水洗后的物料在80~150℃下經(jīng)振動流化床干燥,控制水含量小于8%,然后在400~650℃下焙燒2~6小時,催化劑中含有占催化劑總重量4~12%的鉬和/或鎢和0.4~4%的鈷和/或鎳的氧化物。本發(fā)明所述的渣油加氫脫金屬催化劑的制備方法,其中,所述非酸性粘合劑優(yōu)選為甲基纖維素、乙基纖維素、羥丙基甲基纖維素和羥乙基甲基纖維素中 的一種或幾種。本發(fā)明所述的渣油加氫脫金屬催化劑的制備方法,其中,所述非酸性粘合劑的加入量優(yōu)選為擬薄水鋁石干膠粉中對應(yīng)的氧化鋁重量的1~5%。本發(fā)明所述的渣油加氫脫金屬催化劑的制備方法,其中,所述復(fù)合擴(kuò)孔劑優(yōu)選為含硼化合物和聚乙烯醇。本發(fā)明所述的渣油加氫脫金屬催化劑的制備方法,其中,所述含硼化合物優(yōu)選為硼酸、氧化硼和硼酸鹽中的一種或幾種。本發(fā)明所述的渣油加氫脫金屬催化劑的制備方法,其中,以硼計,所述含硼化合物的加入量優(yōu)選為擬薄水鋁石干膠粉中對應(yīng)的氧化鋁重量的1~4%。本發(fā)明所述的渣油加氫脫金屬催化劑的制備方法,其中,所述聚乙烯醇優(yōu)選為聚乙烯醇溶液或聚乙烯醇粉末。本發(fā)明所述的渣油加氫脫金屬催化劑的制備方法,其中,所述聚乙烯醇的加入量優(yōu)選為擬薄水鋁石干膠粉中對應(yīng)的氧化鋁重量的5~20%。本發(fā)明還可詳述如下:本發(fā)明的加氫催化劑,孔容為0.2~1.2ml/g,比表面積為40~200m2/g,孔直徑在500nm以上的孔所對應(yīng)的孔容占總孔容的比例為5%~30%,孔直徑在1000nm以上的孔所對應(yīng)的孔容占總孔容的比例為5%~15%;催化劑中含有催化劑總重量4-12%的鉬和/或鎢和0.4-4%的鈷和/或鎳的氧化物;催化劑顆粒中金屬組分濃度從顆粒中心至外面表逐漸減少;催化劑顆粒外表面與中心處金屬重量之比為0.05-0.60,0.66r處與中心處金屬重量之比為0.40-0.80,0.33r處與中心處金屬重量之比為0.60-0.95。r為以催化劑顆粒中心為初始點的催化劑的顆粒半徑。本發(fā)明提供方法的要點包括:1)將水合氧化鋁與非酸性粘合劑、復(fù)合擴(kuò)孔劑和水等混合、成型、干燥和焙燒,得到載體;2)配制含有鉬和/或鎢和鎳和/或鈷的金屬溶液,并對所得載體以飽和浸漬的方式負(fù)載金屬;3)采用振動流化床干燥設(shè)備對2)中所得的顆粒物進(jìn)行預(yù)干燥,熱風(fēng)溫度控制在40-100℃,催化劑最終水含量控制在20-60%;4)將3)中所得物料浸于凈水中,浸入時間1-60分鐘,凈水溫度20-80℃;5)水洗后的物料在80-150℃下經(jīng)振動流化床干燥,控制水含量小于8%,然后在400-650℃下焙燒2-6小時,催化劑中含有催化劑總重量4-12%的鉬和/或鎢和0.4-4%的鈷和/或鎳的氧化物。所述非酸性粘合劑選自甲基纖維素、乙基纖維素、羥丙基甲基纖維素、羥乙基甲基纖維素中的一種或幾種,加入量為氧化鋁重量的1-5%。所述復(fù)合擴(kuò)孔劑為含硼化合物和聚乙烯醇。所述含硼化合物選自硼酸、氧化硼、硼酸鹽中的一種或幾種,以單質(zhì)硼計,所述含硼化合物的加入量為氧化鋁重量的1-4%。所述聚乙烯醇為各種規(guī)格的聚乙烯醇溶液或聚乙烯醇粉末,加入量為氧化鋁重量的5-20%。本發(fā)明催化劑制備方法可在載體成型過程中根據(jù)需要加入p、ti、si、zr等不同助劑和田菁粉、淀粉等助擠劑。本發(fā)明催化劑的形狀可以根據(jù)不同的要求進(jìn)行改變。與現(xiàn)有技術(shù)相比,本發(fā)明催化劑同時具有雙峰孔結(jié)構(gòu)和金屬組分梯度減少分布特征,催化劑反應(yīng)活性、容雜質(zhì)能力和使用壽命更優(yōu)。本發(fā)明提供方法在載體成型過程中不使用酸性膠溶劑,降低了酸對水合氧化鋁粒子結(jié)構(gòu)的破壞,因而載體孔容和孔徑均較大;使用含硼化合物與聚乙烯醇復(fù)合擴(kuò)孔,所得大孔孔徑更大,大孔比例更高;對浸漬金屬溶液后的催化劑先低溫預(yù)干燥再進(jìn)行水洗處理,金屬組分分布梯度性好,操作性較強(qiáng),不同催化劑顆粒間金屬梯度分布均一性較好,同一催化劑顆粒內(nèi)不同部位金屬配比均一性較好。本方法中采用含硼化合物與聚乙烯醇復(fù)合擴(kuò)孔,擴(kuò)孔效果更好,這是因為聚乙烯醇遇到含硼化合物時會發(fā)生“凝膠化”反應(yīng),使處于溶解或分散狀態(tài)的聚乙烯醇物質(zhì)產(chǎn)生一定程度的縮合和交聯(lián),在高溫焙燒時通過碳化和分解,更易形成貫通的孔道結(jié)構(gòu),且孔徑更大。本方法中采用振動流化床干燥設(shè)備對催化劑進(jìn)行預(yù)干燥或干燥,具有干燥效果均勻、干燥溫度低、干燥速度快的優(yōu)點,以振動流化床對浸漬后的催化劑先低溫預(yù)干燥,然后再水洗和振動流化干燥,可以減少因金屬組分?jǐn)U散造成的分布梯度降低,同時顆粒間梯度分布均一性較好。本發(fā)明加氫催化劑,可作為重油加氫處理催化劑、特別是渣油加氫脫金屬催化劑使用。由本發(fā)明提供方法制備的氧化鋁載體具有典型的雙峰孔結(jié)構(gòu)和金屬組分梯度減少分布特征。例如,按照本發(fā)明提供方法制備的催化劑經(jīng)500℃焙燒3小時,孔容為0.76cm3/g,比表面積為145m2/g,孔直徑在500納米以上的孔所對應(yīng)孔容占總孔容的24.1%,孔直徑在1000納米以上的孔所對應(yīng)孔容占總 孔容的12.4%;催化劑含有占其總重量8.1%moo3和1.0%的nio;催化劑顆粒外表面與中心處金屬重量之比為0.32,0.66r處與中心處金屬重量之比為0.55,0.33r處與中心處金屬重量之比為0.78。附圖說明圖1:實施例1催化劑壓汞孔徑分布示意圖;圖2:實施例1催化劑金屬組分分布示意圖。具體實施方式以下對本發(fā)明的實施例作詳細(xì)說明:本實施例在以本發(fā)明技術(shù)方案為前提下進(jìn)行實施,給出了詳細(xì)的實施方式和過程,但本發(fā)明的保護(hù)范圍不限于下述的實施例,下列實施例中未注明具體條件的實驗方法,通常按照常規(guī)條件。實施例1稱取煙臺恒輝化工有限公司生產(chǎn)的大孔擬薄水鋁石干膠粉(干基含量71.5wt%)500g,加入粘度為15萬mpa·s(指2%水溶液的粘度)的羥丙基甲基纖維素10.7g、規(guī)格為17-88的聚乙烯醇粉末53.6g,混合均勻;將40.9g硼酸溶解于570g凈水中,緩慢加入前述物料中,混捏成可塑體,然后在單螺桿擠條機(jī)上擠成直徑為1.6mm的三葉草形。120℃干燥2.0小時,再置入焙燒爐中,850℃恒溫3小時,得到載體。配制含有(10.7gmoo3+1.3gnio)/100ml的穩(wěn)定金屬浸漬液,以飽和浸漬的方法對所得載體進(jìn)行浸漬;浸漬所得物料在振動流化床中進(jìn)行預(yù)干燥,熱風(fēng)溫度70℃,控制催化劑水含量為50%;預(yù)干燥后的催化劑置于溫度為40℃的凈水中,浸泡20分鐘;水洗后的催化劑于振動流化床中干燥,熱風(fēng)溫度120℃,干燥后水含量為6%;焙燒爐中500℃恒溫3小時,得催化劑a。催化劑物性見表1。實施例2稱取前述擬薄水鋁石500g,加入粘度為15萬mpa·s(指2%水溶液的粘度)的羥丙基甲基纖維素3.6g、規(guī)格為17-99的的聚乙烯醇粉末28.6g,混合均勻;將20.5克硼酸溶解于570g凈水中,按照前述方法進(jìn)行成型和干燥,在焙燒爐 中以900℃恒溫2小時,得到載體。配制含有(16.0gwo3+0.6gnio)/100ml的穩(wěn)定金屬浸漬液,以飽和浸漬的方法對所得載體進(jìn)行浸漬;浸漬所得物料在振動流化床中進(jìn)行預(yù)干燥,熱風(fēng)溫度40℃,控制催化劑水含量為60%;預(yù)干燥后的催化劑置于溫度為80℃的凈水中,浸泡1分鐘;水洗后的催化劑于振動流化床中干燥,熱風(fēng)溫度150℃,干燥后水含量為4%;焙燒爐中400℃恒溫6小時,得催化劑b。催化劑物性見表1。實施例3稱取前述擬薄水鋁石500g,加入粘度為10萬mpa·s(指2%水溶液的粘度)的羥乙基甲基纖維素17.9g、氧化硼28.6g混合均勻;將31.0克硼酸和規(guī)格為17-88的聚乙烯醇粉末17.9g溶解于570g凈水中,按照前述方法進(jìn)行成型和干燥,在焙燒爐中以700℃恒溫4小時,得到載體。配制含有(6.7gwo3+5.3gmoo3+1.3gnio+1.3gco2o3)/100ml的穩(wěn)定金屬浸漬液,以飽和浸漬的方法對所得載體進(jìn)行浸漬;浸漬所得物料在振動流化床中進(jìn)行預(yù)干燥,熱風(fēng)溫度100℃,控制催化劑水含量為20%;預(yù)干燥后的催化劑置于溫度為20℃的凈水中,浸泡60分鐘;水洗后的催化劑于振動流化床中干燥,熱風(fēng)溫度80℃,干燥后水含量為7%;焙燒爐中650℃恒溫2小時,得催化劑c。催化劑物性見表1。實施例4稱取前述擬薄水鋁石500g,加入粘度為15萬mpa·s(指2%水溶液的粘度)的羥丙基甲基纖維素6.7g和粘度為10萬mpa·s(指2%水溶液的粘度)的甲基纖維素4.0g、氧化硼28.6g,混合均勻;規(guī)格為24-88的聚乙烯醇粉末71.5g溶解于570g凈水中,按照前述方法進(jìn)行成型和干燥,在焙燒爐中以800℃恒溫3小時,得到載體。配制含有(5.3gmo3+5.3gnio)/100ml的穩(wěn)定金屬浸漬液,以飽和浸漬的方法對所得載體進(jìn)行浸漬;浸漬所得物料在振動流化床中進(jìn)行預(yù)干燥,熱風(fēng)溫度80℃,控制催化劑水含量為40%;預(yù)干燥后的催化劑置于溫度為60℃的凈水中,浸泡15分鐘;水洗后的催化劑于振動流化床中干燥,熱風(fēng)溫度110℃,干燥后水含量為5%;焙燒爐中500℃恒溫3小時,得催化劑d。催化劑物性見表1。比較例1-2說明現(xiàn)有方法和由現(xiàn)有方法制備的催化劑。比較例1本比較例中載體按照cn1103009a所描述的方法制得,常規(guī)方法負(fù)載金屬。將34.1克氫氧化鋁干膠粉(含氧化鋁75%的烷基鋁水解產(chǎn)物)和硫酸鋁法制得的氫氧化鋁粉39.3克混合后加入高耐磨炭黑4.7克及表面活性劑sa-203.5克和2.1克硝酸鋁、66毫升水充分碾混,在單螺桿擠條機(jī)上擠成直徑1.6毫米三葉草形,120℃烘干,800℃焙燒4小時,得到載體。配制含有(8.9gmoo3+1.1gnio)/100ml的穩(wěn)定金屬浸漬液,以飽和浸漬的方法對所得載體進(jìn)行浸漬,鼓風(fēng)干燥箱中120℃干燥3小時,焙燒爐中500℃恒溫3小時,得催化劑e。催化劑物性見表1。比較例2本比較例中載體按照常規(guī)方法制得,金屬負(fù)載按照cn101927196方法進(jìn)行。稱取煙臺恒輝化工有限公司生產(chǎn)的大孔擬薄水鋁石干膠粉(干基含量71.5wt%)500g,加入10.7克田菁粉,混合均勻;將17.9克乙酸溶解于430g凈水中,緩慢加入前述物料中,混捏成可塑體,然后在單螺桿擠條機(jī)上擠成直徑為1.6mm的三葉草形。在120℃干燥2.0小時,再置入焙燒爐中,于900℃恒溫3小時,得到載體。先后以含有(10.7gmoo3+1.3gnio)/100ml的金屬溶液和含有(7.4gmoo3+0.9gnio)/100ml的金屬溶液對載體進(jìn)行噴浸,直至飽和。鼓風(fēng)干燥箱中120℃干燥3小時,焙燒爐中500℃恒溫3小時,得催化劑f。催化劑物性見表1。實施例5本例為以上各例催化劑的理化性質(zhì)和活性評價結(jié)果。采用bet,壓汞,sem-edx,xrf等分析方法對催化劑物性進(jìn)行分析,結(jié)果見表1。表1催化劑物化性質(zhì)表1的結(jié)果表明,與比較例相比較,本發(fā)明方法制備的催化劑同時具備雙峰孔結(jié)構(gòu)特征和活性金屬梯度分布特征,孔容、孔徑更大,具有相當(dāng)比例的500nm以上及1000nm以上孔道結(jié)構(gòu),金屬分布梯度更優(yōu)異。對表1催化劑進(jìn)行活性穩(wěn)定性評價,評價條件見表2,評價結(jié)果見表3。表2催化劑評價條件原料油性質(zhì)中東渣油密度(20℃)/g·cm-30.99(ni+v),μg.g-1103工藝條件反應(yīng)溫度,℃385氫分壓,mpa16體積空速,h-10.85氫/油比750表3催化劑金屬脫除率(hd(ni+v))由表3評價結(jié)果知,本發(fā)明催化劑具有更高的脫金屬活性和更優(yōu)的活性穩(wěn)定性。當(dāng)前第1頁12