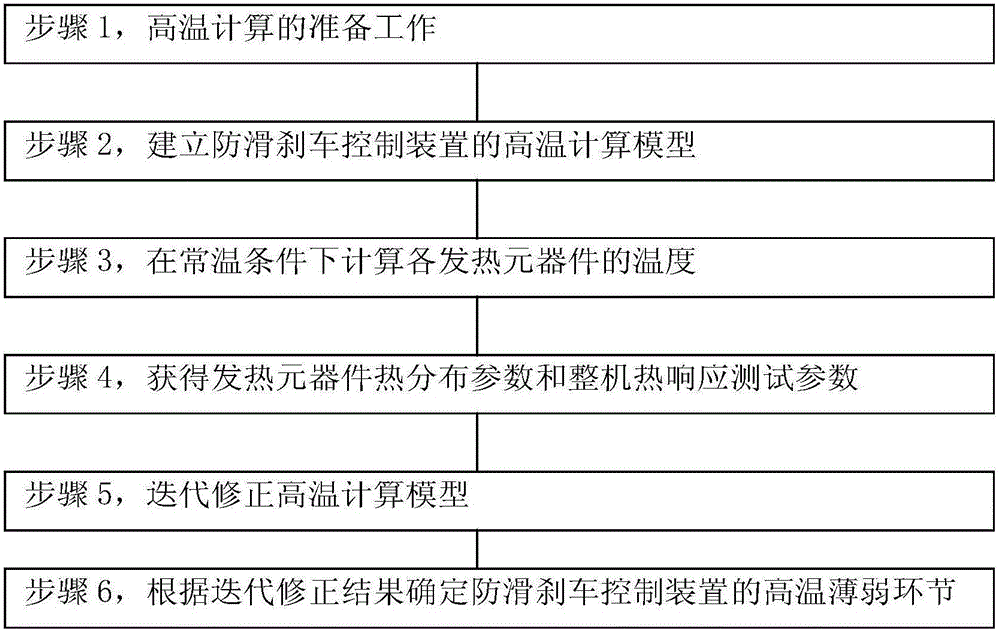
本發(fā)明涉及民用運(yùn)輸類飛機(jī)電子產(chǎn)品的高溫故障分析領(lǐng)域,具體是采用計(jì)算機(jī)技術(shù)確定防滑剎車控制裝置高溫薄弱環(huán)節(jié)的方法。
背景技術(shù):
:防滑剎車控制裝置由飛機(jī)供電,接收機(jī)輪轉(zhuǎn)速變化電信號(hào),進(jìn)行著陸防滑剎車過程中的剎車壓力控制。該防滑剎車控制裝置能夠完成正常著落防滑剎車控制,起飛線剎車控制,車輪間保護(hù)控制,接地保護(hù)控制,起落架收上后機(jī)輪止轉(zhuǎn)剎車等控制功能。防滑剎車控制裝置的高溫計(jì)算溫度指在高溫條件下和防滑剎車控制裝置工作狀態(tài)下,計(jì)算得到的高溫溫度。國外現(xiàn)狀:為了減少高溫引起的故障,國外采用下列技術(shù)確定電子產(chǎn)品的高溫薄弱環(huán)節(jié):1)按照MIL-STD-2164《電子設(shè)備環(huán)境應(yīng)力篩選》標(biāo)準(zhǔn)進(jìn)行元器件篩選;2)按照MIL-STD-781《產(chǎn)品研制,鑒定和生產(chǎn)中的可靠性試驗(yàn)》進(jìn)行可靠性試驗(yàn),將試驗(yàn)中出現(xiàn)高溫故障的元器件作為高溫薄弱環(huán)節(jié);3)按照美國標(biāo)準(zhǔn)GMW8287《高加速壽命、高加速應(yīng)力篩選和抽檢》采用高加速壽命試驗(yàn)的方法,將試驗(yàn)中出現(xiàn)高溫故障的元器件作為高溫薄弱環(huán)節(jié);4)采用計(jì)算的方法確定電子產(chǎn)品的高溫薄弱環(huán)節(jié);5)采用MIL-STD-217F《電子產(chǎn)品可靠性預(yù)計(jì)》確定薄弱環(huán)節(jié),預(yù)計(jì)過程中采用指數(shù)分布。上述技術(shù)雖然可以確定一部分電子產(chǎn)品的高溫薄弱環(huán)節(jié);但存在下列不足:1)整機(jī)進(jìn)行高加速壽命試驗(yàn)確定高溫薄弱環(huán)節(jié)資金浪費(fèi)太大;2)在環(huán)境應(yīng)力篩選中出現(xiàn)高溫故障的元器件可能是制造原因、老化引起的故障,具有不確定因素;3)可靠性試驗(yàn)中出現(xiàn)高溫故障的元器件可能是制造原因,但也可能真是高溫薄弱環(huán)節(jié),具有不確定因素;4)采用計(jì)算的方法確定高溫薄弱環(huán)節(jié)還未完成由理論研究到工程使用的過渡,對計(jì)算模型的修正不足,計(jì)算精度差;5)采用MIL-STD-217F《電子產(chǎn)品可靠性預(yù)計(jì)》確定薄弱環(huán)節(jié),預(yù)計(jì)過程中采用指數(shù)分布,西安航空制動(dòng)科技有限公司在申請?zhí)枮?01610373996.X的發(fā)明創(chuàng)造中提出了一種確定防滑剎車控制裝置高溫故障分布的方法,該方法證明元器件的高溫故障不服從指數(shù)分布,按照指數(shù)分布預(yù)計(jì)結(jié)果會(huì)產(chǎn)生大于103的誤差。國內(nèi)現(xiàn)狀:國內(nèi)電子產(chǎn)品采用下列技術(shù)確定電子產(chǎn)品的高溫薄弱環(huán)節(jié):1、按照美國標(biāo)準(zhǔn)GMW8287《高加速壽命、高加速應(yīng)力篩選和抽檢》采用高加速壽命試驗(yàn)的方法,將試驗(yàn)中出現(xiàn)高溫故障的元器件作為高溫薄弱環(huán)節(jié);2、按照GJB1032《電子設(shè)備環(huán)境應(yīng)力篩選》標(biāo)準(zhǔn)進(jìn)行元器件篩選;3、按照GJB899《可靠性試驗(yàn)和驗(yàn)收試驗(yàn)》進(jìn)行試驗(yàn),將試驗(yàn)中出現(xiàn)高溫故障的元器件作為高溫薄弱環(huán)節(jié);4、采用計(jì)算的方法確定電子產(chǎn)品的高溫薄弱環(huán)節(jié);5、采用GJB299C《電子產(chǎn)品可靠性預(yù)計(jì)》確定薄弱環(huán)節(jié),模型為指數(shù)分布。6、在ZL201110310885.1中公開了一種確定飛機(jī)防滑剎車控制盒高溫工作應(yīng)力極限的方法。該方法采用可靠性強(qiáng)化實(shí)驗(yàn)設(shè)備確定了模擬電路防滑剎車控制盒的高溫工作極限;7、在ZL201310169039.1中公開了一種防滑剎車控制盒高溫破壞極限的方法。該方法采用三綜合實(shí)驗(yàn)設(shè)備確定了數(shù)字電路防滑剎車控制盒的高溫破壞極限。國內(nèi)采用的上述技術(shù)雖然可以發(fā)現(xiàn)電子產(chǎn)品的高溫薄弱環(huán)節(jié),但仍存在下列不足:1、整機(jī)進(jìn)行高加速壽命試驗(yàn)確定高溫薄弱環(huán)節(jié)資金浪費(fèi)太大;2、在環(huán)境應(yīng)力篩選中出現(xiàn)高溫故障的元器件不能排除制造原因、老化引起的故障,具有不確定因素;3、可靠性試驗(yàn)中出現(xiàn)高溫故障的元器件不能排除制造原因,具有不確定因素;4、采用計(jì)算的方法確定高溫薄弱環(huán)節(jié)還未完成由理論研究到工程推廣使用的過渡,計(jì)算方法不成熟,對計(jì)算模型的修正不足,計(jì)算精度差;5、采用GJB299C確定高溫薄弱環(huán)節(jié),預(yù)計(jì)過程中采用指數(shù)分布,在申請?zhí)枮?01610373996.X的發(fā)明創(chuàng)造中公開了一種確定防滑剎車控制裝置高溫故障分布函數(shù)的方法,該方法證明元器件的高溫故障不服從指數(shù)分布,當(dāng)采用指數(shù)分布預(yù)計(jì)高溫故障時(shí)會(huì)產(chǎn)生上千倍的誤差,這是現(xiàn)有標(biāo)準(zhǔn)的不足。GJB299C是參照MIL-STD-217F編寫的,國外依據(jù)217F預(yù)計(jì),國內(nèi)依據(jù)299C預(yù)計(jì),犯得是同一個(gè)錯(cuò)誤。6、ZL201110310885.1中的目的是確定模擬電路防滑剎車控制盒性能發(fā)生飄移的高溫工作極限,是一種帶有破壞性質(zhì)的試驗(yàn),試驗(yàn)結(jié)束后可以更換損傷元器件修復(fù)產(chǎn)品。雖然可以根據(jù)試驗(yàn)數(shù)據(jù)分析高溫薄弱環(huán)節(jié),但是一次試驗(yàn)投入2套防滑剎車控制盒經(jīng)濟(jì)損失就是50萬元,試驗(yàn)費(fèi)用30萬元。而且2套數(shù)量少,確定高溫薄弱環(huán)節(jié)的精度低。7、ZL201310169039.1中目的是確定數(shù)字電路防滑剎車控制盒的高溫破壞極限。這是一種破壞性試驗(yàn),試驗(yàn)結(jié)束后修復(fù)產(chǎn)品已經(jīng)沒有經(jīng)濟(jì)價(jià)值。雖然可以根據(jù)試驗(yàn)數(shù)據(jù)分析高溫薄弱環(huán)節(jié),但是一次試驗(yàn)投入2套防滑剎車控制盒經(jīng)濟(jì)損失就是200萬元。而且2套數(shù)量少,確定高溫薄弱環(huán)節(jié)的精度低。技術(shù)實(shí)現(xiàn)要素:為克服現(xiàn)有技術(shù)存在的高溫試驗(yàn)時(shí)間長、試驗(yàn)費(fèi)用高,計(jì)算精度低,不能準(zhǔn)確確定電子產(chǎn)品高溫薄弱環(huán)節(jié),采用標(biāo)準(zhǔn)中的故障率預(yù)計(jì)方法產(chǎn)生誤差大的現(xiàn)狀,本發(fā)明提出一種確定防滑剎車控制裝置高溫薄弱環(huán)節(jié)的方法。本發(fā)明的具體步驟是:步驟1,高溫計(jì)算的準(zhǔn)備工作:所述高溫計(jì)算的準(zhǔn)備工作包括采集該防滑剎車控制裝置的結(jié)構(gòu)信息、采集各類元器件的信息,以及繪制該防滑剎車控制裝置的三維幾何圖形。具體是過程是:第一步,準(zhǔn)備該防滑剎車控制裝置的結(jié)構(gòu)信息所述的結(jié)構(gòu)信息包括該防滑剎車控制裝置的組成及連接方式。第二步,準(zhǔn)備各類元器件的信息所述2塊電路板共包含12個(gè)集成模塊,集成模塊上元器件的型號(hào)、重量、尺寸、封裝形式等信息,作為計(jì)算高溫薄弱環(huán)節(jié)的信息。第三步,繪制該防滑剎車控制裝置的三維幾何圖形采用CITIA軟件繪制該防滑剎車控制裝置的三維幾何圖形,分為下列3部分內(nèi)容:1)該防滑剎車控制裝置成品狀態(tài)的三維幾何圖形;2)該防滑剎車控制裝置電路板的三維幾何圖形;3)該防滑剎車控制裝置的集成模塊、元器件的三維幾何圖形。至此,完成了防滑剎車控制裝置高溫計(jì)算的準(zhǔn)備工作。步驟2,建立防滑剎車控制裝置的高溫計(jì)算模型:防滑剎車控制裝置高溫計(jì)算的建模步驟為:第一步,根據(jù)該防滑剎車控制裝置的三維幾何圖形進(jìn)行修訂;所述對防滑剎車控制裝置的三維幾何圖形進(jìn)行的修訂包括:去掉直徑小于0.65mm的孔;去掉尺寸小于0.65mm的凸臺(tái);刪除與熱分析無關(guān)的螺釘、連接器、電纜等連接件。第二步,根據(jù)所有元器件的位置信息,以及每一種類元器件的封裝形式、溫度范圍、電壓電流、接插方式、重量及外形尺寸,進(jìn)行電路板建模。所述的各種類元器件的上述信息均通過采購手冊得到。第三步,輸入相關(guān)參數(shù)輸入功耗大于等于0.05W的元器件的功耗、殼體材料、防滑剎車控制裝置的工作環(huán)境條件。將防滑剎車控制裝置的重力方向按照水平裝機(jī)方向設(shè)置。第四步,網(wǎng)格劃分:功耗大于等于0.05W的區(qū)域設(shè)置為域網(wǎng)格進(jìn)行控制。該區(qū)域以外的部位通過軟件自動(dòng)生成。至此,完成了防滑剎車控制裝置的高溫建模工作。步驟3,在常溫條件下計(jì)算各發(fā)熱元器件的溫度根據(jù)高溫計(jì)算模型,將功耗大于等于0.05W的元器件均確定為發(fā)熱元器件計(jì)算的溫度條件:環(huán)境溫度設(shè)定為25℃。向計(jì)算機(jī)中輸入所述各發(fā)熱元器件的功耗,并且該發(fā)熱元器件的最大功耗和該低功耗元器件的常用功耗各占50%。步驟4,獲得發(fā)熱元器件熱分布參數(shù)和整機(jī)熱響應(yīng)測試參數(shù)通過測試的方式獲得所述發(fā)熱元器件熱分布參數(shù)和整機(jī)熱響應(yīng)測試參數(shù)。當(dāng)測試得到的發(fā)熱元器件熱分布的計(jì)算數(shù)據(jù)大于實(shí)測數(shù)據(jù)時(shí),需要根據(jù)實(shí)測數(shù)據(jù)修正高溫計(jì)算模型;當(dāng)整機(jī)熱響應(yīng)測試中有工作狀態(tài)下溫升大的發(fā)熱元器件時(shí),需對高溫計(jì)算模型進(jìn)行迭代修正。測試溫度為常溫。第一步,進(jìn)行發(fā)熱元器件熱分布測試:用啞光漆涂于電路板被測表面,在各集成模塊的發(fā)熱元器件上布置熱測試點(diǎn),防滑剎車控制裝置分別按照最大功耗和常用功耗狀態(tài)下運(yùn)行,熱平衡時(shí)間為1h,待溫度平衡后用熱成像儀進(jìn)行測試,最終得到各電路板上各模塊發(fā)熱器件的溫度數(shù)據(jù)。第二步,整機(jī)熱響應(yīng)測試:在環(huán)境溫度25℃條件下分別按照最大功耗和常用功耗狀態(tài)給該防滑剎車控制裝置通電;通電時(shí)間為至測試結(jié)束。在通電1h后開始測試,用表2中所列儀器采集該防滑剎車控制裝置中模塊與防滑剎車控制裝置殼體的接觸點(diǎn),以及防滑剎車控制裝置殼體外表面中心的溫度。1)根據(jù)實(shí)測數(shù)據(jù)和計(jì)算數(shù)據(jù)之間的差值,在各元器件額定功耗范圍內(nèi)修改各發(fā)熱元器件的功耗值,以縮小熱測試數(shù)據(jù)與計(jì)算數(shù)據(jù)之間的差異。當(dāng)實(shí)測值與計(jì)算值的差值大于5%時(shí),需修改原確定的該發(fā)元熱器件的功耗值,提高高溫計(jì)算模型的精度。修改時(shí),若實(shí)測溫度值高于計(jì)算溫度值,,則提高該發(fā)熱元器件的功耗值;反之,若實(shí)測溫度值低于計(jì)算溫度值,,則降低該發(fā)熱元器件的功耗值。所述發(fā)熱元器件功耗值的提高幅度或降低幅度為0.01~0.02W。2)根據(jù)GJB299C《電子設(shè)備可靠性預(yù)計(jì)手冊》,修改發(fā)熱元器件封裝材料;在此基礎(chǔ)上,對高溫計(jì)算模型的進(jìn)行調(diào)整,完成第一次修正工作。步驟5,迭代修正高溫計(jì)算模型所述迭代修正的環(huán)境溫度為40~60℃。迭代修正中,以5℃的步長逐步增高各發(fā)熱元器件的溫度。在設(shè)定的當(dāng)前溫度下按實(shí)測發(fā)熱元器件的溫度數(shù)據(jù),并按步驟4中所述高溫計(jì)算模型的修正過程對高溫計(jì)算模型進(jìn)行迭代修正,并將每次迭代修正后的數(shù)據(jù)與實(shí)測數(shù)據(jù)進(jìn)行比較,若二者間的最大誤差大于5%,繼續(xù)高溫計(jì)算模型的修正工作;若二者間的最大誤差小于5%,修正可以結(jié)束。步驟6,根據(jù)迭代修正結(jié)果確定防滑剎車控制裝置的高溫薄弱環(huán)節(jié)利用防滑剎車控制裝置修正后的高溫計(jì)算模型進(jìn)行高溫薄弱環(huán)節(jié)分析。采用環(huán)境設(shè)置溫度和高溫控制溫度均為修正后確定該防滑剎車控制裝置的高溫薄弱環(huán)節(jié)至此,確定該防滑剎車控制裝置的高溫薄弱環(huán)節(jié)的過程結(jié)束。本發(fā)明采用計(jì)算機(jī)技術(shù)和常規(guī)軟件,確定防滑剎車控制裝置的高溫薄弱環(huán)節(jié),不產(chǎn)生試驗(yàn)污染和試驗(yàn)設(shè)備消耗、能源消耗,節(jié)約防滑剎車控制裝置的試驗(yàn)樣件。本發(fā)明中:1)采用三維圖形軟件,做出防滑剎車控制裝置殼體、防滑剎車控制裝置的電路板、防滑剎車控制裝置的元器件的三維圖形;2)簡化防滑剎車控制裝置的三維圖形,采用流體力學(xué)軟件建立防滑剎車控制裝置的三維高溫計(jì)算模型;該計(jì)算模型用于替代防滑剎車控制裝置的實(shí)物產(chǎn)品;3)采用常溫?zé)釡y試的方法實(shí)測防滑剎車控制裝置殼體、發(fā)熱器件的溫度,該測試為一個(gè)常溫點(diǎn)的數(shù)據(jù);西安航空制動(dòng)科技有限公司在申請?zhí)枮?01610584291.2的發(fā)明創(chuàng)造中提出了一種測試防滑剎車控制裝置高溫計(jì)算模型數(shù)據(jù)的方法,根據(jù)該方法中測試得到的各高溫測試點(diǎn)數(shù)據(jù),逐點(diǎn)修正低溫計(jì)算模型。,保證高溫計(jì)算結(jié)果的精度。在環(huán)境溫度70℃時(shí)和工作狀態(tài)下高于100℃的元器件確定為高溫薄弱環(huán)節(jié)。本發(fā)明的實(shí)施效果:采用計(jì)算機(jī)技術(shù)確定防滑剎車控制裝置的高溫薄弱環(huán)節(jié),和現(xiàn)有實(shí)物試驗(yàn)技術(shù)相比具有節(jié)約試驗(yàn)時(shí)間、節(jié)省經(jīng)費(fèi)開支、降低能源消耗的效果。具體的實(shí)施效果的有:1)節(jié)約時(shí)間的效果,采用高加速壽命試驗(yàn)確定高溫薄弱環(huán)節(jié)需要7天時(shí)間,采用本發(fā)明技術(shù)僅需1天時(shí)間就可確定防滑剎車控制裝置的高溫薄弱環(huán)節(jié);2)節(jié)約試驗(yàn)樣件費(fèi)用的效果,采用計(jì)算機(jī)技術(shù)不存在消耗試驗(yàn)樣件的問題;3)節(jié)約經(jīng)費(fèi)的效果,高加速壽命試驗(yàn)每小時(shí)的費(fèi)用是1500元,7天的試驗(yàn)費(fèi)用為:7天×8h/每天×1500元/h=84000元,采用計(jì)算機(jī)就不需要支出這筆費(fèi)用;4)具有降低能源消耗的效果,高加速壽命試驗(yàn)中的高溫步進(jìn)試驗(yàn)功率為130kw,能源消耗大;5)本發(fā)明實(shí)測高溫各點(diǎn)的溫度值,沒有損壞防滑剎車控制裝置,沒有產(chǎn)生高溫步進(jìn)試驗(yàn)的開支,這樣做的目的是提高高溫計(jì)算模型的計(jì)算精度。本發(fā)明和現(xiàn)有技術(shù)實(shí)施效果的綜合比較:1)和環(huán)境應(yīng)力篩選的效果比較:環(huán)境應(yīng)力篩選是一種事后100%檢驗(yàn)的方法,篩選中未出現(xiàn)故障的可以出廠,發(fā)生故障的不能出廠;采用計(jì)算的方法可以在研制過程中發(fā)現(xiàn)和排除高溫薄弱環(huán)節(jié),提高了產(chǎn)品研制質(zhì)量;2)每套控制盒高溫計(jì)算和環(huán)境應(yīng)力篩選的時(shí)間、費(fèi)用比較:環(huán)境應(yīng)力篩選費(fèi)用80h×500元/h=40000元;計(jì)算機(jī)的計(jì)算費(fèi)用:15h×100/h=1500元;3)和可靠性試驗(yàn)的時(shí)間、費(fèi)用比較;根據(jù)GJB899A短時(shí)高風(fēng)險(xiǎn)試驗(yàn)方案,當(dāng)控制盒的MTBF為3000h時(shí),試驗(yàn)時(shí)間為3300h,試驗(yàn)費(fèi)用為:3300h×500元/h=1650000元;計(jì)算機(jī)進(jìn)行高溫薄弱環(huán)節(jié)計(jì)算費(fèi)用:15h×100/h=1500元;4)和現(xiàn)有計(jì)算技術(shù)的效果比較,本發(fā)明的計(jì)算模型采用HB5830.8《機(jī)載設(shè)備環(huán)境條件及試驗(yàn)方法高溫》規(guī)定的高溫范圍,用8個(gè)高溫溫度測試點(diǎn)的數(shù)據(jù)修正高溫計(jì)算模型,而現(xiàn)有技術(shù)為1點(diǎn)實(shí)測數(shù)據(jù)修正,現(xiàn)有技術(shù)電子產(chǎn)品高溫計(jì)算誤差范圍能達(dá)到±10%,本發(fā)明的計(jì)算誤差小于±5%。附圖說明附圖1是防滑剎車控制裝置殼體各面板的示意圖。圖中:1.第一側(cè)面板;2.第二側(cè)面板;3.安裝插頭面板;4.后面板;5.上面板;6.下面板;7.插頭。附圖2是本發(fā)明的流程圖。具體實(shí)施方式本實(shí)施例以某民用運(yùn)輸機(jī)防滑剎車控制裝置為例,由飛機(jī)提供電源,接收機(jī)輪轉(zhuǎn)速變化量電信號(hào),進(jìn)行防滑剎車壓力控制。該防滑剎車控制裝置能夠完成正常著落防滑剎車控制,輪間保護(hù),接地保護(hù),飛機(jī)起飛后的機(jī)輪止轉(zhuǎn)剎車各種功能。本實(shí)施例的具體過程是:步驟1,高溫計(jì)算的準(zhǔn)備工作所述高溫計(jì)算的準(zhǔn)備工作包括采集該防滑剎車控制裝置的結(jié)構(gòu)信息、采集各類元器件的信息,以及繪制該防滑剎車控制裝置的三維幾何圖形。具體是:第一步,準(zhǔn)備該防滑剎車控制裝置的結(jié)構(gòu)信息所述的結(jié)構(gòu)信息包括該防滑剎車控制裝置的組成及連接方式。該防滑剎車控制裝置由殼體和2塊電路板組成,2快電路板分別為:控制板、記錄板;采用插槽方式和殼體相連。所采集的殼體的信息包括該殼體的外形及尺寸、材料、密封形式。第二步,準(zhǔn)備各類元器件的信息所述2塊電路板共包含12個(gè)集成模塊,集成模塊上元器件的型號(hào)、重量、尺寸、封裝形式等信息,作為計(jì)算高溫薄弱環(huán)節(jié)的信息。第三步,繪制該防滑剎車控制裝置的三維幾何圖形采用CITIA軟件繪制該防滑剎車控制裝置的三維幾何圖形,分為下列3部分內(nèi)容:4)該防滑剎車控制裝置成品狀態(tài)的三維幾何圖形;5)該防滑剎車控制裝置電路板的三維幾何圖形;6)該防滑剎車控制裝置的集成模塊、元器件的三維幾何圖形。至此,完成了防滑剎車控制裝置高溫計(jì)算的準(zhǔn)備工作。步驟2,建立防滑剎車控制裝置的高溫計(jì)算模型從本步驟起用到下列設(shè)備、軟件。試驗(yàn)設(shè)備:HPZ800計(jì)算機(jī)工作站。所用軟件見表1,所用測試儀器見表2。表1確定高溫薄弱環(huán)節(jié)所用軟件表序名稱生產(chǎn)商版本用途1CITIA美國DS公司V5R18繪制三維圖形2FLOTHERM美國MENTORGRAPHICS公司8.1進(jìn)行高溫計(jì)算表2熱測試儀器匯總表序名稱型號(hào)生產(chǎn)廠家用途1熱成像儀TI55美國FLUX公司采集熱信號(hào)2數(shù)據(jù)采集儀ANGILENT34970A美國ANGILENT公司采集熱數(shù)據(jù)3熱電偶T型美國ANGILENT公司采集高溫器件的溫度防滑剎車控制裝置高溫計(jì)算的建模步驟為:第一步,根據(jù)該防滑剎車控制裝置的三維幾何圖形進(jìn)行下列修訂:1)去掉直徑小于0.65mm的孔;2)去掉尺寸小于0.65mm的凸臺(tái);3)刪除與熱分析無關(guān)的螺釘、連接器、電纜等連接件。第二步,根據(jù)所有元器件的位置信息,以及每一種類元器件的封裝形式、溫度范圍、電壓電流、接插方式、重量及外形尺寸,進(jìn)行電路板建模。所述的各種類元器件的上述信息均通過采購手冊得到。第三步,輸入相關(guān)參數(shù)輸入功耗大于等于0.05W的元器件的功耗、殼體材料、防滑剎車控制裝置的工作環(huán)境條件。本實(shí)施例中,是:1)殼體材料:鋁合金材料;2)元器件功耗:對所有功耗大于等于0.05W的元器件進(jìn)行功耗設(shè)定,功耗小于0.05W的元器件及整板功耗附加在電路板上;3)環(huán)境條件:GJB150最高為70℃;本發(fā)明確定當(dāng)計(jì)算誤差小于±5%時(shí),在70℃前結(jié)束計(jì)算;當(dāng)誤差大于±5%時(shí),環(huán)境條件高于70℃,直至達(dá)到計(jì)算誤差和實(shí)測誤差小于±5%。將防滑剎車控制裝置的重力方向按照水平裝機(jī)方向設(shè)置。第四步,網(wǎng)格劃分:功耗大于0.05W的區(qū)域設(shè)置為域網(wǎng)格進(jìn)行控制。該區(qū)域以外的部位通過軟件自動(dòng)生成。至此,完成了防滑剎車控制裝置的高溫建模工作。步驟3,在常溫條件下計(jì)算各發(fā)熱元器件的溫度根據(jù)高溫計(jì)算模型,將功耗大于等于0.05W的元器件均確定為發(fā)熱元器件。發(fā)熱元器件所屬模塊見表3。計(jì)算的溫度條件:環(huán)境溫度設(shè)定為25℃。向計(jì)算機(jī)中輸入所述各發(fā)熱元器件的功耗,并且該低功耗元器件的最大功耗和該低功耗元器件的常用功耗各占50%。計(jì)算數(shù)據(jù)見表3。表3采用模型計(jì)算得到的發(fā)熱元器件溫度,環(huán)境溫度:25℃步驟4,獲得發(fā)熱元器件熱分布參數(shù)和整機(jī)熱響應(yīng)測試參數(shù)通過測試的方式獲得所述發(fā)熱元器件熱分布參數(shù)和整機(jī)熱響應(yīng)測試參數(shù)。測試溫度為常溫。本實(shí)施例中,測試溫度為25℃。第一步,進(jìn)行發(fā)熱元器件熱分布測試:用啞光漆涂于電路板被測表面,在各集成模塊的發(fā)熱元器件上布置熱測試點(diǎn),發(fā)熱模塊、元器件見表4,防滑剎車控制裝置分別按照最大功耗和常用功耗狀態(tài)下運(yùn)行,熱平衡時(shí)間為1h,待溫度平衡后用熱成像儀進(jìn)行測試,最終得到各電路板上各模塊發(fā)熱器件的溫度數(shù)據(jù),見表4。表4實(shí)測得到的各發(fā)熱器件數(shù)據(jù)匯總表,環(huán)境溫度25℃表3計(jì)算數(shù)據(jù)比表4實(shí)測數(shù)據(jù)實(shí)測數(shù)據(jù)普遍大,其中高溫16位定點(diǎn)信號(hào)處理器的誤差為:(86-73)/73=17.3,不能用于工程,根據(jù)表4實(shí)測數(shù)據(jù)修正高溫計(jì)算模型。第二步,整機(jī)熱響應(yīng)測試:整機(jī)熱響應(yīng)測試:在環(huán)境溫度25℃條件下分別按照最大功耗和常用功耗狀態(tài)給該防滑剎車控制裝置通電;通電時(shí)間為至測試結(jié)束。在通電1h后開始測試,用表2中所列儀器采集該防滑剎車控制裝置中模塊與防滑剎車控制裝置殼體的接觸點(diǎn),以及防滑剎車控制裝置殼體外表面中心的溫度,見表5。表5防滑剎車控制裝置整機(jī)熱響應(yīng)測試數(shù)據(jù),環(huán)境溫度25℃表5中所述的第一側(cè)面板1和第二側(cè)面板2分別位于面向插頭7時(shí)防滑剎車控制裝置殼體的左側(cè)和右側(cè);所述后面板4為面向插頭時(shí)防滑剎車控制裝置殼體的后面。根據(jù)表4與表5中得到的實(shí)測數(shù)據(jù),修正高溫計(jì)算模型的邊界條件、參數(shù)。1)根據(jù)表4的實(shí)測數(shù)據(jù)和表3計(jì)算數(shù)據(jù)之間的差值,在各元器件額定功耗范圍內(nèi)修改各發(fā)熱元器件的功耗值,以縮小熱測試數(shù)據(jù)與計(jì)算數(shù)據(jù)之間的差異。當(dāng)實(shí)測值與計(jì)算值的差值大于5%時(shí),需修改原確定的該發(fā)熱元器的功耗值,提高高溫計(jì)算模型的精度。修改時(shí),若實(shí)測溫度值高于計(jì)算溫度值,則提高該發(fā)熱元器件的功耗值;反之,若實(shí)測溫度值低于計(jì)算溫度值,則降低該發(fā)熱元器件的功耗值。所述發(fā)熱元器件功耗值的提高幅度或降低幅度為0.01~0.02W。2)根據(jù)GJB299C電子設(shè)備可靠性預(yù)計(jì)手冊,修改這部分發(fā)熱元器件封裝材料;在此基礎(chǔ)上,對高溫計(jì)算模型的進(jìn)行調(diào)整,完成第一次修正工作。步驟5,迭代修正高溫計(jì)算模型迭代修正高溫計(jì)算模型時(shí),當(dāng)一次修正得到的結(jié)果不能滿足精度要求時(shí),進(jìn)行下一次修正,直至計(jì)算精度滿足要求為止。所述迭代修正的環(huán)境溫度為40~60℃。迭代修正中,以5℃的步長逐步增高各發(fā)熱元器件的溫度。在設(shè)定的當(dāng)前溫度下按實(shí)測發(fā)熱元器件的溫度數(shù)據(jù),并按步驟4中所述高溫計(jì)算模型的修正過程對高溫計(jì)算模型進(jìn)行迭代修正,并將每次迭代修正后的數(shù)據(jù)與實(shí)測數(shù)據(jù)進(jìn)行比較,若二者間的最大誤差大于5%,繼續(xù)高溫計(jì)算模型的修正工作;若二者間的最大誤差小于5%,修正可以結(jié)束。對高溫計(jì)算模型進(jìn)行第一次迭代修正。由表5得到,第二側(cè)面板的熱測試溫度為57℃,高出環(huán)境溫度32℃,在工作狀態(tài)下的溫升大。修正時(shí),根據(jù)表4的實(shí)測數(shù)據(jù)和表3計(jì)算數(shù)據(jù)之間的差值,將各元器件的功耗值提高0.01~0.02W,以縮小熱測試數(shù)據(jù)與計(jì)算數(shù)據(jù)之間的差異。同時(shí)根據(jù)GJB299C電子設(shè)備可靠性預(yù)計(jì)手冊,修改模型中所述發(fā)熱元器件的封裝材料信息,并對高溫計(jì)算模型進(jìn)行調(diào)整,完成第一次修正工作。按照表4實(shí)測數(shù)據(jù)修正高溫計(jì)算模型后的計(jì)算數(shù)據(jù)見表6。表6第一次修正高溫計(jì)算模型后發(fā)熱元器件的溫度計(jì)算數(shù)據(jù)環(huán)境溫度25℃表6中,第一次修正后的計(jì)算數(shù)據(jù)與實(shí)測數(shù)據(jù)的最大誤差為:(80-73)/73=9.5%,需繼續(xù)進(jìn)行高溫計(jì)算模型的修正工作。本發(fā)明的修正目標(biāo)是計(jì)算誤差小于±5%。為了達(dá)到使用要求,繼續(xù)采用西安航空制動(dòng)科技有限公司在申請?zhí)枮?01610584291.2的發(fā)明創(chuàng)造中提出的測試防滑剎車控制裝置高溫計(jì)算模型數(shù)據(jù)的方法中得到的測試數(shù)據(jù)進(jìn)行高溫計(jì)算模型修正。對高溫計(jì)算模型進(jìn)行第二次迭代修正。第二次迭代修正的環(huán)境溫度為40℃時(shí)實(shí)測各發(fā)熱元器件的溫度。所述實(shí)測發(fā)熱元器件溫度的方法同步驟4中發(fā)熱元器件熱分布測試方法。采用發(fā)明201610584291.2實(shí)測防滑剎車控制裝置在環(huán)境溫度40℃時(shí)的溫度數(shù)據(jù)見表7。表7在環(huán)境溫度40℃和防滑剎車控制裝置工作狀態(tài)下的測試數(shù)據(jù)將計(jì)算模型中的環(huán)境溫度設(shè)置為40℃,得到在40℃下的各發(fā)熱元器件的溫度。按照表7中實(shí)測發(fā)熱元器件的溫度數(shù)據(jù),并按步驟4中所述高溫計(jì)算模型的修正過程對高溫計(jì)算模型進(jìn)行第二次修正。修正后的數(shù)據(jù)見表8。表8第二次修正高溫計(jì)算模型后發(fā)熱元器件的計(jì)算數(shù)據(jù)環(huán)境溫度40℃表8中,第二次修正后的計(jì)算數(shù)據(jù)與實(shí)測數(shù)據(jù)的最大誤差為:(96-88)/88=9%,需繼續(xù)進(jìn)行高溫計(jì)算模型的修正工作。對高溫計(jì)算模型進(jìn)行第三次迭代修正。第三次迭代修正的環(huán)境溫度為45℃時(shí)實(shí)測各發(fā)熱元器件的溫度所述實(shí)測各發(fā)熱元器件溫度的方法同步驟4中的發(fā)熱元器件熱分布測試方法。采用發(fā)明201610584291.2實(shí)測防滑剎車控制裝置在環(huán)境溫度45℃時(shí)的溫度數(shù)據(jù)見表9。表9在環(huán)境溫度45℃和防滑剎車控制裝置工作狀態(tài)下的測試數(shù)據(jù)將計(jì)算模型中的環(huán)境溫度設(shè)置為45℃,得到在45℃下各發(fā)熱元器件的溫度。將表9中實(shí)測發(fā)熱元器件的溫度數(shù)據(jù)與45℃下計(jì)算模型中的數(shù)據(jù)進(jìn)行比較,并按步驟4中所述高溫計(jì)算模型的修正過程對高溫計(jì)算模型進(jìn)行第三次修正。修正后的數(shù)據(jù)見表10。表10第三次修正后各發(fā)熱元器件的計(jì)算數(shù)據(jù)環(huán)境溫度45℃表10中,第三次修正后的計(jì)算數(shù)據(jù)與實(shí)測數(shù)據(jù)的最大誤差為:(100-93)/93=7.5%,需繼續(xù)進(jìn)行高溫計(jì)算模型的修正工作。對低溫計(jì)算模型進(jìn)行第四次迭代修正。第四次迭代修正的環(huán)境溫度為50℃時(shí)實(shí)測各發(fā)熱元器件的溫度所述實(shí)測各發(fā)熱元器件溫度的方法同步驟4中的發(fā)熱元器件熱分布測試方法。采用發(fā)明201610584291.2實(shí)測防滑剎車控制裝置在環(huán)境溫度50℃時(shí)的溫度數(shù)據(jù)見表11。表11在環(huán)境溫度50℃和防滑剎車控制裝置工作狀態(tài)下的測試數(shù)據(jù)將計(jì)算模型中的環(huán)境溫度設(shè)置為50℃,得到在50℃下各發(fā)熱元器件的溫度。將表11中實(shí)測發(fā)熱元器件的溫度數(shù)據(jù)與50℃下計(jì)算模型中的數(shù)據(jù)進(jìn)行比較,并按步驟4中所述高溫計(jì)算模型的修正過程對高溫計(jì)算模型進(jìn)行第四次修正。修正后的數(shù)據(jù)見表12。表12第四次修正后的各發(fā)熱元器件的溫度計(jì)算數(shù)據(jù)環(huán)境溫度50℃表12中,第四次修正后的計(jì)算數(shù)據(jù)與實(shí)測數(shù)據(jù)的最大誤差為:(104-98)/98=6.1%,需繼續(xù)進(jìn)行高溫計(jì)算模型的修正工作。對高溫計(jì)算模型進(jìn)行第五次迭代修正。第五次迭代修正的環(huán)境溫度為55℃時(shí)實(shí)測各發(fā)熱元器件的溫度所述實(shí)測各發(fā)熱元器件溫度的方法同步驟4中的發(fā)熱元器件熱分布測試方法。采用發(fā)明201610584291.2實(shí)測防滑剎車控制裝置在環(huán)境溫度55℃時(shí)的溫度數(shù)據(jù)見表13。表13在環(huán)境溫度55℃和防滑剎車控制裝置工作狀態(tài)下的測試數(shù)據(jù)將計(jì)算模型中的環(huán)境溫度設(shè)置為55℃,得到在55℃下各發(fā)熱元器件的溫度。將表13中實(shí)測發(fā)熱元器件的溫度數(shù)據(jù)與55℃下計(jì)算模型中的數(shù)據(jù)進(jìn)行比較,并按步驟4中所述高溫計(jì)算模型的修正過程對高溫計(jì)算模型進(jìn)行第五次修正。修正后的數(shù)據(jù)見表14。表14第五次修正后的各發(fā)熱元器件的溫度計(jì)算數(shù)據(jù)環(huán)境溫度55℃表14中,第五次修正后的計(jì)算數(shù)據(jù)與實(shí)測數(shù)據(jù)的最大誤差為:(108-103)/103=4.9%,在5%誤差的邊界線上,繼續(xù)進(jìn)行高溫計(jì)算模型的修正工作。對高溫計(jì)算模型進(jìn)行第六次迭代修正。第六次迭代修正的環(huán)境溫度為60℃時(shí)實(shí)測各發(fā)熱元器件的溫度所述實(shí)測各發(fā)熱元器件溫度的方法同步驟4中的發(fā)熱元器件熱分布測試方法。采用發(fā)明201610584291.2實(shí)測防滑剎車控制裝置在環(huán)境溫度60℃時(shí)的溫度數(shù)據(jù)見表15。表15在環(huán)境溫度60℃和防滑剎車控制裝置工作狀態(tài)下的測試數(shù)據(jù)將計(jì)算模型中的環(huán)境溫度設(shè)置為60℃,得到在60℃下各發(fā)熱元器件的溫度。將表15中實(shí)測發(fā)熱元器件的溫度數(shù)據(jù)與60℃下計(jì)算模型中的數(shù)據(jù)進(jìn)行比較,并按步驟4中所述高溫計(jì)算模型的修正過程對高溫計(jì)算模型進(jìn)行第六次修正。修正后的數(shù)據(jù)見表16。表16第六次修正后的各發(fā)熱元器件的溫度計(jì)算數(shù)據(jù)環(huán)境溫度60℃表16中第六次修正后的計(jì)算數(shù)據(jù)與實(shí)測數(shù)據(jù)最大誤差為:(112-108)/108=3.7%,小于規(guī)定5%的誤差,高溫計(jì)算模型的修正工作結(jié)束。步驟6,根據(jù)迭代修正結(jié)果確定防滑剎車控制裝置的高溫薄弱環(huán)節(jié)利用防滑剎車控制裝置修正后的高溫計(jì)算模型進(jìn)行高溫薄弱環(huán)節(jié)分析。采用的高溫設(shè)置溫度和高溫控制溫度見表17,表中的70℃來源于HB5830.8高溫試驗(yàn),表中所述的出口溫度為計(jì)算機(jī)模擬的三綜合試驗(yàn)箱的高溫氣體出口溫度。所述環(huán)境溫度與高溫氣體出口溫度均為70℃。防滑剎車控制裝置的高溫薄弱環(huán)節(jié)指在70℃環(huán)境條件下和工作狀態(tài)下溫度高于100℃的模塊、元器件。表17確定防滑剎車控制裝置高溫計(jì)算的設(shè)定條件防滑剎車控制裝置殼體溫升計(jì)算結(jié)果見表18,各模塊、元器件的計(jì)算結(jié)果見表19。表18防滑剎車控制裝置的殼體高溫分析結(jié)果,殼體平均溫度℃環(huán)境溫度℃殼體平均溫升℃897019表19在環(huán)境溫度70℃和防滑剎車控制裝置工作狀態(tài)下各模塊溫度計(jì)算結(jié)果采用修正后的高溫計(jì)算模型計(jì)算,在環(huán)境溫度70℃和防滑剎車控制裝置工作狀態(tài)下,高溫微控制器芯片、高溫16位定點(diǎn)信號(hào)處理器、記錄板高溫存儲(chǔ)器、高溫集成器件、高溫可編程邏輯電路、高溫總線收發(fā)器的溫度達(dá)到了100℃,是防滑剎車控制裝置的高溫薄弱環(huán)節(jié)。至此,確定該防滑剎車控制裝置的高溫薄弱環(huán)節(jié)的過程結(jié)束。當(dāng)前第1頁1 2 3