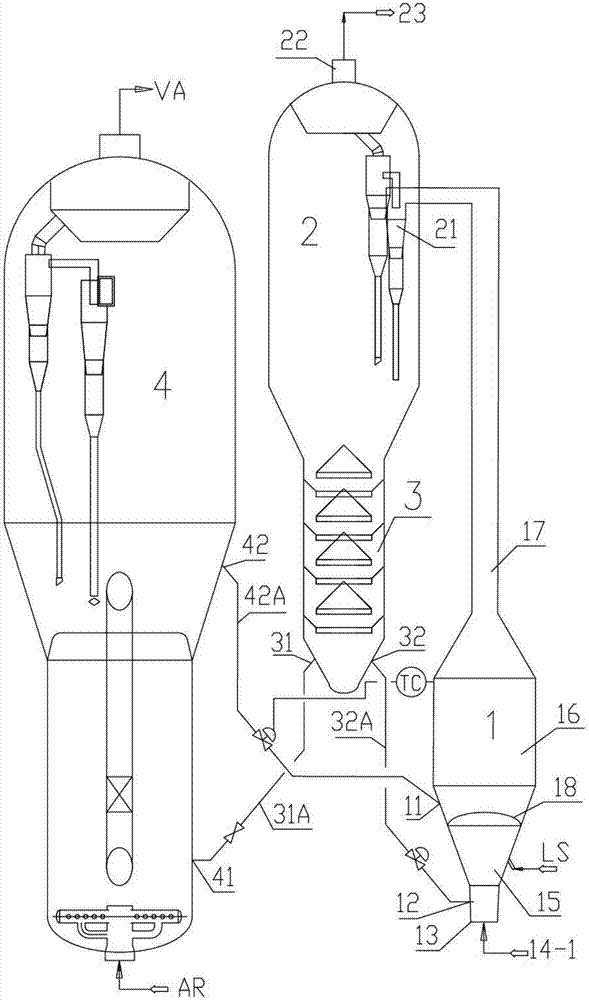
本發(fā)明屬于石油烴類催化轉化
技術領域:
,特別涉及一種輕烴裂解制烯烴的催化轉化方法,該方法能提高低碳烯烴尤其是丙烯產(chǎn)率。
背景技術:
:丙烯、乙烯是最重要的石油化工原料之一。乙烯主要來源于蒸汽裂解,70%的丙烯來源于蒸汽裂解,另外30%的丙烯由催化裂化工藝過程提供。與蒸汽裂解相比,催化裂解可以借助催化劑的作用降低反應溫度,簡化烯烴急冷分離,提高丙烯比例,是有價值的烯烴生產(chǎn)技術方案。催化裂解制取低碳烯烴是蒸汽裂解以外的制取低碳烯烴的技術途徑。本發(fā)明采用循環(huán)循環(huán)流化床或氣固輸送流態(tài)化條件進行石腦油催化裂解生產(chǎn)烯烴。輕烴如石腦油催化裂解遠不向蒸汽裂解那樣成熟,甚至還罕見可以工業(yè)化的技術應用。目前催化裂解技術開發(fā)關注點在催化劑開發(fā),相應的反應工程技術尚未引起重視。技術實現(xiàn)要素:本發(fā)明的目的在于提供一種輕烴流化裂解制烯烴的催化轉化方法,通過催化劑的分配和反應器形式,實現(xiàn)低溫預接觸和高溫裂解組合反應條件,優(yōu)化反應器的溫度分布和催化劑環(huán)境,實現(xiàn)了輕烴氣相裂解反應,可以提高產(chǎn)品選擇性;實現(xiàn)了反應后的催化劑和來自再生器的催化劑的組合利用,實現(xiàn)反應原料與適度含碳催化劑的接觸與氣化,提高目的產(chǎn)品的選擇性。本發(fā)明技術方案如下:一種輕烴裂解制烯烴的催化轉化方法,設置一個反應系統(tǒng)和一個催化劑再生器;所述反應系統(tǒng)包括反應器、沉降器和汽提器;反應器自下而上依次由預接觸區(qū)(即輕烴原料和催化劑預接觸區(qū),在預接觸區(qū),液態(tài)進料先氣化并與低含炭催化劑形成催化劑環(huán)境,然后再與再生劑接觸升溫,氣態(tài)進料則無需氣化)、主反應區(qū)、反應產(chǎn)物輸送管組成;液態(tài)或氣態(tài)的輕烴原料從預接觸區(qū)進入反應器,來自再生器的催化劑進入反應區(qū),向反應器提供熱量;主反應區(qū)采用氣固循環(huán)流化床或氣固輸送流化床條件;從汽提器引出部分待生劑或者從反應器引出部分反應后的催化劑,返回預接觸區(qū)或者在來自再生器的催化劑下方返回主反應區(qū);主反應區(qū)的溫度高于預接觸區(qū);主反應區(qū)的反應溫度由來自再生器的催化劑量控制;反應原料先在預接觸區(qū)與催化劑接觸實現(xiàn)原料與催化劑活性材料的預接觸氣化,然后在主反應區(qū)進行催化裂解反應;反應原料為液態(tài)時,在預接觸區(qū)實現(xiàn)氣化;輕烴反應產(chǎn)物與催化劑一起經(jīng)反應產(chǎn)物輸送管進入沉降器,在沉降器內(nèi)完成氣固分離后流出沉降器;氣固分離器分離出的催化劑進入汽提器,被蒸汽汽提后進入再生器進行待生劑再生;反應器1與沉降器和汽提器同軸設置或反應器設置在沉降器和汽提器的外部;當反應器設置在沉降器和汽提器外部時,沉降器和汽提器獨立設置或者設置在再生器的再生區(qū)上部。本發(fā)明中:反應器需要的熱量由來自再生器的催化劑在主反應區(qū)提供;反應器主反應區(qū)為最高溫度區(qū),下方的預接觸區(qū)為低溫區(qū);經(jīng)汽提的催化劑稱為“待生劑”,未經(jīng)汽提的催化劑稱為“反應后的催化劑”;本發(fā)明反應原料進入預接觸區(qū)與催化劑接觸,再進入主反應區(qū)進行催化裂化反應;從汽提器或反應器引出部分待生劑或反應后的催化劑返回主反應區(qū)或預接觸區(qū);反應后的催化劑或待生劑返回主反應區(qū)時,優(yōu)先使反應后的催化劑或待生劑在來自在再生器的催化劑下方返回主反應區(qū);反應器采用輸送流化床或循環(huán)流化床反應器;所述輸送流化床和循環(huán)流化床是氣固流態(tài)化專業(yè)的技術名稱,有明確的定義;所述輕烴原料包括石腦油組分、催化輕汽油組分、焦化汽油組分、c4組分及其他沸點低于200℃的含有烯烴或烷烴的烴類組分;當產(chǎn)品以丙烯為目的時,主反應區(qū)的反應溫度按540℃~600℃控制;當產(chǎn)品按多產(chǎn)丙烯和乙烯為目的時,主反應區(qū)的反應溫度按640℃~690℃控制;當反應器與沉降器和汽提器同軸設置時,反應系統(tǒng)中沉降器和汽提器設置在反應器主反應區(qū)上方;當反應器設置在沉降器和汽提器外部時,沉降器和汽提器可以獨立設置,也可以設置在再生器再生區(qū)上部;當沉降器和汽提器設置在再生器上方即同軸布置時,從反應器引出部分催化劑返回主反應區(qū)或預接觸區(qū),實現(xiàn)催化劑在反應器循環(huán);來自再生器的催化劑從再生斜管(再生催化劑斜管或立管)直接進入主反應區(qū),催化劑流量由滑閥控制;主反應區(qū)的反應溫度由來自再生器的催化劑量控制,增加該催化劑量提高反應溫度;從汽提器或反應器本身引出部分催化劑返回反應器,通過反應后的催化劑或待生劑的返回量調節(jié)控制反應器主反應區(qū)的空速,增加該催化劑流量降低空速;反應產(chǎn)物在沉降器內(nèi)實現(xiàn)氣固分離后流出沉降器,分離出的待生劑經(jīng)過汽提后進入再生器再生,然后從再生器進入反應器的主反應區(qū);在輕烴反應器出口直接設置氣固分離器,在催化裂化反應區(qū)完成反應后反應產(chǎn)物和催化劑快速進行氣固分離,實現(xiàn)在流化床或循環(huán)流化床內(nèi)完成催化裂化反應后的反應快速終止。上述的輕烴裂解制烯烴的催化轉化方法,進一步地,預接觸區(qū)獨立設置在主反應區(qū)下方或設置在主反應區(qū)內(nèi)并位于來自再生器的催化劑入口下方;從沉降器待生劑汽提區(qū)或反應器引出部分反應后的催化劑或待生劑返回輕烴反應器的主反應區(qū)或返回反應器的預接觸區(qū);當輕烴以氣態(tài)形式進入反應器并且主反應區(qū)為循環(huán)流化床條件時,反應后的催化劑或待生劑從來自再生器的催化劑入口下方進入主反應區(qū)。上述的輕烴裂解制烯烴的催化轉化方法,進一步地,當輕烴為液態(tài)時,反應后的催化劑或待生劑先返回預接觸區(qū),使輕烴實現(xiàn)氣化,同時輕烴氣體輸送催化劑進入主反應區(qū)進行催化裂解反應。上述的輕烴裂解制烯烴的催化轉化方法,進一步地,將二次原料在主反應區(qū)出口或在反應產(chǎn)物輸送管進入反應器1,利用主反應區(qū)催化劑和反應產(chǎn)物的熱量,和催化劑接觸實現(xiàn)該部分物流的反應,同時降低主反應區(qū)反應產(chǎn)物物流的溫度,降低反應產(chǎn)物的后反應程度;所述二次原料為液態(tài)輕烴或輕烴反應產(chǎn)物在分餾塔分出c5以上的組分(即輕烴裂解產(chǎn)物的重組分)。上述的輕烴裂解制烯烴的催化轉化方法,進一步地,所述的再生器,將催化劑再生需要的空氣與再生煙氣進行換熱,提高空氣的溫度。上述的輕烴裂解制烯烴的催化轉化方法,進一步地,將所述的輕烴反應產(chǎn)物與液態(tài)輕烴原料進行換熱,實現(xiàn)液態(tài)輕烴的氣化后再進入反應器。本發(fā)明中,設置反應產(chǎn)物和液體輕烴原料加熱氣化器,利用輕烴反應器的反應產(chǎn)物的熱量實現(xiàn)液態(tài)輕烴反應原料的氣化。上述的輕烴裂解制烯烴的催化轉化方法,進一步地,所述主反應區(qū)和預接觸區(qū)之間設置分布板或分布管,進入反應器的輕烴原料為液態(tài)時,來自預接觸區(qū)的反應原料氣化后經(jīng)過分布板進入主反應區(qū);進入反應器的輕烴原料為氣態(tài)時,原料氣經(jīng)過分布板或分布管進入主反應區(qū)。本發(fā)明中,輕烴原料以液態(tài)進入預接觸區(qū)時,輕烴原料在預接觸區(qū)氣化,同時輸送催化劑通過分布板進入主反應區(qū);輕烴原料以氣態(tài)進入預接觸區(qū)時,通過分布板或分布管進入主反應區(qū)。上述的輕烴裂解制烯烴的催化轉化方法,進一步地,當催化劑進入預接觸區(qū)時,進入的催化劑為反應后的催化劑或待生劑,或來自再生器的催化劑,或待生劑與來自再生器的催化劑的混合。優(yōu)先采用反應后的催化劑或待生劑進入預接觸區(qū)和反應原料接觸。本發(fā)明的效果在于:1.本發(fā)明反應器采用低溫預氣化和高溫裂解組合反應條件,優(yōu)化了反應器的溫度分布,實現(xiàn)了輕烴氣相裂解反應,可以提高產(chǎn)品選擇性;2.本發(fā)明實現(xiàn)了反應后的催化劑和來自再生器的催化劑的組合利用,使含碳的反應后的催化劑先與反應原料接觸,實現(xiàn)反應原料與適度含碳催化劑的接觸與氣化,提高目的產(chǎn)品的選擇性。附圖說明:圖1為本發(fā)明輕烴裂解制烯烴的催化轉化方法實施方式一示意圖;圖2為本發(fā)明輕烴裂解制烯烴的催化轉化方法實施方式二示意圖;圖3為本發(fā)明輕烴裂解制烯烴的催化轉化方法實施方式三示意圖;圖4為本發(fā)明輕烴裂解制烯烴的催化轉化方法實施方式四示意圖。圖中編號標記內(nèi)容如下:1反應器,11來自再生器的催化劑入口,12反應器待生劑入口管,13輕烴入口管,14液體輕烴,14-1氣體輕烴,15預親和區(qū),16主反應區(qū),17反應產(chǎn)物輸送管,18分布板,19預接觸區(qū)反應后的催化劑入口管,19-1反應器待生劑出口管;19a反應后的催化劑,2沉降器,21氣固旋風分離器,22反應油氣出口管,23輕烴反應產(chǎn)物,24換熱冷卻后的反應產(chǎn)物;3汽提器,31待生劑去再生器待生立管,31a待生劑,32待生劑去主反應區(qū)出口管,32a待生劑,4再生器,41再生器待生劑入口管,42再生劑去反應器出口管,42a來自再生器的催化劑;5輕烴加熱氣化器,51液態(tài)輕烴,52加熱后的氣態(tài)輕烴,53二次原料;6空氣-再生煙氣換熱器;ar空氣,ar-1加熱后的空氣;gas,干氣;va再生煙氣,va-1冷卻后的煙氣;ls蒸汽;w催化劑藏量;t溫度;c控制;tc溫度控制;wc催化劑藏量控制。具體實施方式:以下以具體實施例來說明本發(fā)明的技術方案,但本發(fā)明的保護范圍不限于此。具體實施過程如下:實施方式一:如圖1所示,設置一個反應系統(tǒng)和一個催化劑再生器;所述反應系統(tǒng)包括反應器1、沉降器2和汽提器3;反應器1自下而上依次由預接觸區(qū)15、主反應區(qū)16、反應產(chǎn)物輸送管17組成;反應器1設置在沉降器2和汽提器3外部,沉降器2和汽提3獨立設置;液態(tài)輕烴原料14經(jīng)輕烴入口管13從預接觸區(qū)15進入反應器1,來自再生器的催化劑42a進入主反應區(qū)16,向反應器1提供熱量;主反應區(qū)16采用氣固輸送流化床條件;從汽提器3經(jīng)待生劑去主反應區(qū)出口管32引出部分待生劑32a,返回預接觸區(qū)15,主反應區(qū)16的溫度高于預接觸區(qū)15;主反應區(qū)16的反應溫度由來自再生器的催化劑42a的量控制;反應原料即液態(tài)輕烴14先在預接觸區(qū)15實現(xiàn)原料與催化劑活性材料待生劑32a的預接觸和氣化,并向上流動進入主反應區(qū)16,來自再生器的催化劑42a從主反應區(qū)16的來自再生器的催化劑入口11進入反應器1,向反應器提供熱量,然后在主反應區(qū)16進行催化裂解反應;反應油氣即輕烴反應產(chǎn)物23與催化劑一起經(jīng)反應產(chǎn)物輸送管17進入沉降器2,在沉降器2內(nèi)經(jīng)氣固旋風分離器21分離出夾帶的催化劑,完成氣固分離后,從反應油氣出口管22流出沉降器2;分離出的催化劑進入汽提器3,被蒸汽汽提后進入再生器4進行待生劑再生。實施方式二:如圖2所示,設置一個反應系統(tǒng)和一個催化劑再生器;所述反應系統(tǒng)包括反應器1、沉降器2和汽提器3;反應器1自下而上依次由預接觸區(qū)15、主反應區(qū)16、反應產(chǎn)物輸送管17組成;反應器1設置在沉降器2和汽提器3外部,沉降器2和汽提3獨立設置;氣態(tài)輕烴原料14-1經(jīng)輕烴入口管13從預接觸區(qū)15進入反應器1,來自再生器的催化劑42a進入主反應區(qū)16,向反應器1提供熱量;主反應區(qū)16采用氣固循環(huán)流化床條件;從汽提器3經(jīng)待生劑去主反應區(qū)出口管32引出部分待生劑32a,返回預接觸區(qū)15,主反應區(qū)16的溫度高于預接觸區(qū)15;主反應區(qū)16的反應溫度由來自再生器的催化劑42a的量控制;反應原料氣態(tài)輕烴14-1先在預接觸區(qū)15實現(xiàn)原料與催化劑活性材料待生劑32a的預接觸,并向上流動,在分布板18的作用下均勻分配進入主反應區(qū)16,來自再生器的催化劑42a從主反應區(qū)16的來自再生器的催化劑入口11進入反應器1,向反應器提供熱量,然后在主反應區(qū)16進行催化裂解反應;輕烴反應產(chǎn)物23與催化劑一起經(jīng)反應產(chǎn)物輸送管17進入沉降器2,在沉降器2內(nèi)經(jīng)氣固旋風分離器21分離出夾帶的催化劑,完成氣固分離后,從反應油氣出口管22流出沉降器2;分離出的催化劑進入汽提器3,被蒸汽汽提后進入再生器4進行待生劑再生。實施方式三:如圖3所示,設置一個反應系統(tǒng)和一個催化劑再生器;所述反應系統(tǒng)包括反應器1、沉降器2和汽提器3;反應器1自下而上依次由預接觸區(qū)15、主反應區(qū)16、反應產(chǎn)物輸送管17組成;反應器1與沉降器2和汽提器3同軸設置,沉降器2和汽提器3設置在輕烴反應器1的上部;液態(tài)輕烴原料14經(jīng)輕烴入口管13從預接觸區(qū)15進入反應器1,來自再生器的催化劑42a進入主反應區(qū)16,向反應器1提供熱量;主反應區(qū)16采用氣固循環(huán)流化床條件;從汽提器3經(jīng)待生劑去主反應區(qū)出口管32引出部分待生劑32a,由反應器待生劑入口管12返回預接觸區(qū)15,主反應區(qū)16的溫度高于預接觸區(qū)15;主反應區(qū)16的反應溫度由來自再生器的催化劑42a的量控制;反應原料液態(tài)輕烴14先在預接觸區(qū)15實現(xiàn)原料與催化劑活性材料待生劑32a的預接觸和氣化,并向上流動,在分布板18的作用下均勻分配進入主反應區(qū)16,來自再生器的催化劑42a從主反應區(qū)16的來自再生器的催化劑入口11進入反應器1,向反應器提供熱量,然后在主反應區(qū)16進行催化裂解反應;輕烴反應產(chǎn)物23與催化劑一起經(jīng)反應產(chǎn)物輸送管17進入沉降器2,在沉降器2內(nèi)經(jīng)氣固旋風分離器21分離出夾帶的催化劑,完成氣固分離后,從反應油氣出口管22流出沉降器2;分離出的催化劑進入汽提器3,被蒸汽汽提后進入再生器4進行待生劑再生。實施方式四:如圖4所示,設置一個反應系統(tǒng)、一個催化劑再生器4、輕烴加熱氣化器5和空氣-再生煙氣換熱器6;所述反應系統(tǒng)包括反應器1、沉降器2和汽提器3;反應器1自下而上依次由預接觸區(qū)15、主反應區(qū)16、反應產(chǎn)物輸送管17組成;反應器1設置在沉降器2和汽提器3外部,沉降器2和汽提3與再生器4同軸設置;將液態(tài)輕烴51與輕烴反應產(chǎn)物23在輕烴加熱氣化器5內(nèi)進行換熱,實現(xiàn)液態(tài)輕烴51的氣化,得到的加熱后的氣態(tài)輕烴52經(jīng)輕烴入口管13從預接觸區(qū)15進入反應器1,來自再生器的催化劑42a進入主反應區(qū)16,向反應器1提供熱量;主反應區(qū)16采用氣固循環(huán)流化床條件;從主反應區(qū)16經(jīng)反應器待生劑出口管19-1引出部分反應后的催化劑19a,從預接觸區(qū)反應后的催化劑入口管19返回預接觸區(qū)15,主反應區(qū)16的溫度高于預接觸區(qū)15;主反應區(qū)16的反應溫度由來自再生器的催化劑42a的量控制;加熱后的氣態(tài)輕烴52先在預接觸區(qū)15實現(xiàn)原料與催化劑活性材料即反應后的催化劑19a的預接觸,并向上流動進入主反應區(qū)16,來自再生器的催化劑42a從主反應區(qū)16的來自再生器的催化劑入口11進入反應器1,向反應器提供熱量,然后在主反應區(qū)16進行催化裂解反應;反應油氣即輕烴反應產(chǎn)物23與催化劑一起經(jīng)反應產(chǎn)物輸送管17進入沉降器2,在沉降器2內(nèi)經(jīng)氣固旋風分離器21分離出夾帶的催化劑,完成氣固分離后,輕烴反應產(chǎn)物23從反應油氣出口管22流出沉降器2,進入輕烴加熱氣化器5進行換熱;分離出的催化劑進入汽提器3,被蒸汽汽提后進入再生器4進行待生劑再生;在預接觸區(qū)15和主反應區(qū)16間設置分布板18;在主反應區(qū)上部的反應產(chǎn)物輸送管17底部引入新的二次原料53,利用反應區(qū)的熱量和催化劑實現(xiàn)該部分物流的反應,同時降低主反應區(qū)反應物流的溫度,降低反應產(chǎn)物的后反應程度;設置空氣-再生煙氣換熱器6,再生器催化劑再生需要的空氣ar首先與再生煙氣va進行換熱,提高空氣的溫度,加熱后的空氣ar-1進入再生器4參與再生。實施例1:本實施例使用的裝置見圖4,以產(chǎn)丙烯為目的。反應器:采用循環(huán)流化床形式,反應原料為液態(tài)直餾輕烴,性質見表1。采用來自再生器的680℃再生劑進行反應,反應溫度560℃,流化床反應區(qū)重時空速41/h,流化床內(nèi)油氣流速1.2m/s,停留時間3.5s,再生器再生溫度680℃。對比例:采用常規(guī)提升管輕烴催化裂化。實施例1與對比例的實施結果在表2中給出。從表2可以看出,本發(fā)明與常規(guī)提升管工藝相比,轉化率增加了2.66個百分點,低價值產(chǎn)品產(chǎn)率明顯下降,高價值產(chǎn)品產(chǎn)率明顯提高,其中干氣產(chǎn)率下降了2.47個百分點,焦炭產(chǎn)率降低0.19個百分點,總烯烴產(chǎn)率增加3.69個百分點,丙烯產(chǎn)率增加了2.3個百分點,乙烯產(chǎn)率降低了0.73個百分點。可見,本發(fā)明大幅的增加了烯烴產(chǎn)率,干氣和焦炭產(chǎn)率大幅下降。表1直餾輕烴性質項目數(shù)據(jù)密度g/cm3(20℃)0.75直鏈烷烴,w%16.67異構烷烴,w%34.16環(huán)烷烴,w%31.25芳香烴,w%17.75餾程,℃32~194表2實施例與對比例實施結果當前第1頁12