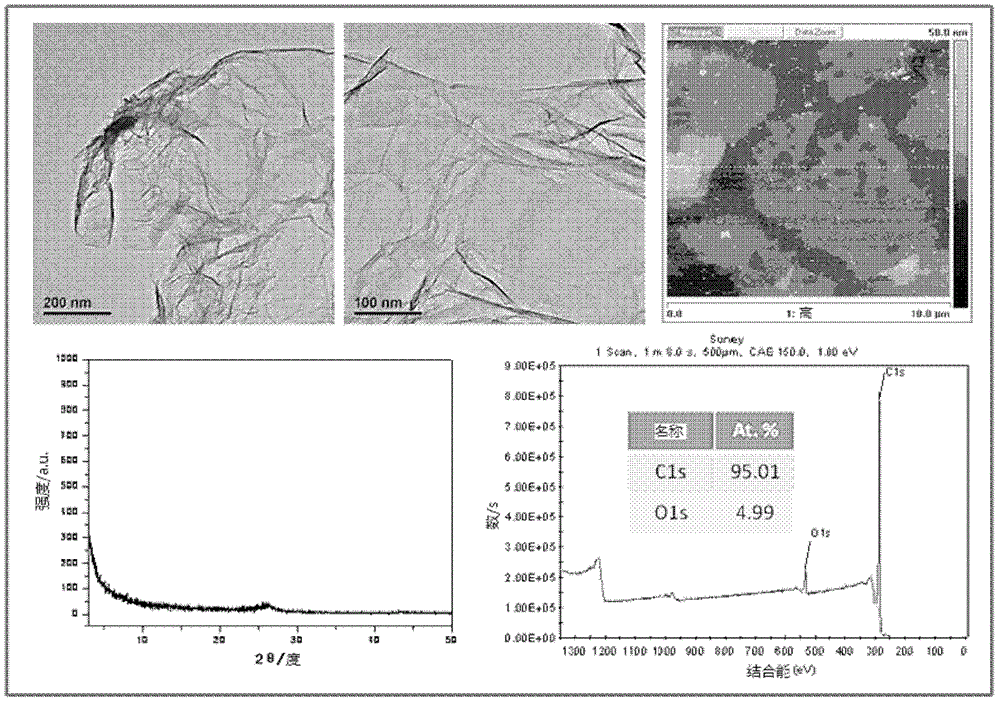
本發(fā)明涉及一種環(huán)氧復(fù)合材料的制備方法,以及由該方法制備的環(huán)氧復(fù)合材料。
背景技術(shù):電氣絕緣材料(又稱電介質(zhì))具有很高的擊穿強度和電阻率,通常用來隔離不同電位的物體,起到電絕緣和承力作用。電氣絕緣材料(以下簡稱“絕緣材料”)在電力設(shè)備和電子器件中得到廣泛應(yīng)用,是其安全運行的保障。擁有優(yōu)良的電擊穿性能是電氣絕緣材料最基本的要求之一。由于優(yōu)良的物理和化學(xué)性能、良好的加工工藝性,多種聚合物已經(jīng)被應(yīng)用于絕緣材料,環(huán)氧樹脂是其中最重要的品種之一。采用環(huán)氧樹脂及其復(fù)合材料可以制備電子元件的封裝材料、絕緣漆料、變壓器絕緣層、高壓輸變電設(shè)備絕緣部件等等。近年來,電力設(shè)備和電子器件向小型化和輕量化的發(fā)展對環(huán)氧材料的電氣絕緣性能特別是電擊穿性能提出了越來越高的要求。在工業(yè)應(yīng)用中,通常向環(huán)氧樹脂中添加催化劑、稀釋劑、增韌劑、各種填料等助劑,以改善其某一項或多項性能。傳統(tǒng)上用于改善環(huán)氧樹脂的電氣絕緣性能的填料大多數(shù)是微米級的無機氧化物,如:層狀硅酸鹽、三氧化鋁、氧化鎂、二氧化硅等微米級填料。一般情況下,微米填料需要在較高添加量時(質(zhì)量分數(shù)大于50%)才能明顯改善材料的擊穿性能。然而,填料添加量過高會導(dǎo)致絕緣材料的重量增加,不利于其向輕量化方向發(fā)展。高添加量的填料也會使聚合物材料脆性增加,力學(xué)性能劣化。近年來隨著納米技術(shù)的迅速發(fā)展,納米復(fù)合材料(納米電介質(zhì))的宏量制備成為可能。由于納米填料的小尺寸效應(yīng)、量子效應(yīng)、界面效應(yīng)等,納米復(fù)合材料與傳統(tǒng)材料相比具有獨特的物理化學(xué)性能。相關(guān)研究表明較低添加量的納米填料可使高聚物的各項電絕緣性能得到比較顯著的改善。如TakahiroImai等[1,2]用納米層狀硅酸鹽來改善環(huán)氧復(fù)合材料的電絕緣性能,含1.5%體積分數(shù)納米粘土的復(fù)合材料的擊穿強度(2683kV/mm)比傳統(tǒng)的微米復(fù)合材料(2509kV/mm)提高了7%。5%質(zhì)量分數(shù)的納米層狀硅酸鹽可以使復(fù)合材料在常溫下的耐電壓時間提高為純環(huán)氧樹脂的2倍。Nelson等[3]的研究表明,10%質(zhì)量分數(shù)的納米氧化鈦能夠很好地抑制環(huán)氧樹脂中空間電荷的形成,在5-11kV的電壓范圍內(nèi)納米復(fù)合材料的局部放電電荷量小于對應(yīng)的微米復(fù)合材料,從而提高了納米復(fù)合材料的擊穿強度。王霞等[4]發(fā)現(xiàn)納米氧化鋅能有效提高聚乙烯的體積電阻率和交流擊穿強度;含有5%質(zhì)量分數(shù)的納米氧化鋅/聚乙烯復(fù)合材料擊穿強度為145kV/mm,而純低密度聚乙烯的擊穿強度為126kV/mm。為降低納米體系粘度,通常需要對納米顆粒進行表面修飾或改性來提高其在樹脂基體的相容性和分散度。Roy等[5]用乙烯基硅烷對納米二氧化硅顆粒進行表面改性以增強與聚乙烯基體的界面相互作用;結(jié)果表明納米二氧化硅顆粒的加入提高了復(fù)合材料的擊穿強度和耐壓性能;當針尖附件電場強度超過500kV/mm時,純聚乙烯的耐壓時間小于1小時,而納米復(fù)合材料的耐壓時間比純聚乙烯高1-2個數(shù)量級。專利CN101020800A公開了一種使用長碳鏈型氨基硅烷偶聯(lián)劑對無機納米填料進行表面改性的方法;表面改性改善了納米填料在環(huán)氧基體中的分散度,環(huán)氧材料的擊穿強度也有一定程度的提高。然而,由于納米顆粒添加量(5wt.%-8wt.%)偏高,此專利中采用有機溶劑(丙酮)來降低混合體系粘度,大量有機溶劑處理可能會造成環(huán)保問題,不利于該發(fā)明的工業(yè)化。近來一些研究者根據(jù)“庫侖阻塞效應(yīng)”嘗試向聚合物中添加納米金屬填料來改善復(fù)合材料的擊穿性能。如蘇麗等[6]通過光化學(xué)反應(yīng)法合成不同粒徑的納米銀顆粒,并制備納米銀/環(huán)氧復(fù)合材料,研究發(fā)現(xiàn):納米銀的粒徑越小,復(fù)合材料擊穿強度的提升越明顯;粒徑固定時,復(fù)合材料的擊穿強度隨銀含量的增多出現(xiàn)先增加后降低的趨勢。然而該研究中可能仍然存在一些問題:如納米銀的制備、提純等步驟較復(fù)雜,且納米銀的穩(wěn)定性不好;另外納米銀顆粒的添加量還是比較高——需要10%質(zhì)量分數(shù)的納米銀才能使環(huán)氧材料的擊穿電壓達到最大值。綜上所述,盡管納米電介質(zhì)的研究已經(jīng)取得一定的進展,目前仍然存在一些亟待解決的問題。對環(huán)氧體系而言,納米填料的加入會帶來顯著的增粘效應(yīng),使體系流變性能變差,澆注時容易產(chǎn)生氣泡,形成缺陷,最終破壞材料的絕緣性能。當納米顆粒的添加量較大時,這種情況尤為突出。另外,納米顆粒在環(huán)氧中的均勻分散也是納米復(fù)合材料制備的關(guān)鍵問題。參考文獻[1]TakahiroImai,F(xiàn)umioSawa,TamonOzaki,ToshioShimizu.InfluenceofTemperatureonMechanicalandInsulationPropertiesofEpoxy-LayeredSilicateNanocomposite.IEEETransactionsonDielectricsandElectricalInsulation.2006,13(1)445-451.[2]TakahiroImai,F(xiàn)umioSawa,ToshiyukiNakano,TamonOzaki,ToshioShimizu.EffectsofNano-andMicro-fillerMixtureonElectricalInsulationPropertiesofEpoxyBasedComposites.IEEETransactionsonDielectricsandElectricalInsulation.2006,13(1)319-326.[3]NelsonJK,HuY.Nanocompositedielectrics-propertiesandimplicationsJ.Phys.D:Appl.Phys.2005,38:213-222.[4]王霞,鄭曉泉等.納米ZnO/低密度聚乙烯復(fù)合材料的介電特性.中國電機工程學(xué)報.2008,28(19):13-20.[5]RoyM,NelsonJK.Polymernanocompositedielectrics-theroleoftheinterface.IEEETransactionsonDielectricsandElectricalInsulation.2005,12(4)629-640.[6]蘇麗,馬寒冰,楊莉,李秀云.納米銀/環(huán)氧復(fù)合材料的制備及其介電性能.化工進展.2011,30(8):1800-1804.
技術(shù)實現(xiàn)要素:本發(fā)明的目的是為了克服現(xiàn)有的環(huán)氧復(fù)合材料的上述缺陷,提供一種新的環(huán)氧復(fù)合材料及其制備方法。在本發(fā)明的所述環(huán)氧復(fù)合材料的制備方法中,通過加入少量的導(dǎo)電納米填料,能夠顯著提高環(huán)氧復(fù)合材料的擊穿強度,并且保證該環(huán)氧復(fù)合材料具有較好的介電性能。本發(fā)明提供了一種環(huán)氧復(fù)合材料的制備方法,該方法包括:(1)將導(dǎo)電納米填料與一部分環(huán)氧樹脂攪拌混合,并將攪拌混合后得到的混合物進行研磨,得到母料;(2)在50-80℃,將步驟(1)中得到的母料與另一部分環(huán)氧樹脂和固化劑混合,然后脫除氣泡;(3)將脫除氣泡后得到的物料進行固化成型;其中,步驟(1)和(2)中環(huán)氧樹脂的總用量與步驟(1)中導(dǎo)電納米填料的重量比為100∶0.001-0.5,步驟(1)中環(huán)氧樹脂的用量與步驟(2)中環(huán)氧樹脂的重量比為1∶0.1-100,且步驟(1)中的所述攪拌混合的條件使得所述攪拌混合后得到的混合物在60℃的動力粘度為5-18Pa·s。本發(fā)明還提供了由上述方法制備的納米環(huán)氧復(fù)合材料。根據(jù)本發(fā)明所述的環(huán)氧復(fù)合材料制備方法具有以下優(yōu)點:(1)通過控制導(dǎo)電納米填料與環(huán)氧樹脂的攪拌混合條件,以獲得特定動力粘度范圍內(nèi)的混合物,使得導(dǎo)電納米填料能夠均勻地分散于環(huán)氧樹脂中,這樣有利于最終制備的環(huán)氧復(fù)合材料的固化成型;并且如此制備的環(huán)氧復(fù)合材料具有顯著提高的擊穿強度,同時具有較好的介電性能;(2)本發(fā)明中導(dǎo)電納米填料的用量很小,使得導(dǎo)電納米填料、環(huán)氧樹脂和固化劑的混合漿料的粘度較小,從而有利于脫除混合漿料中的氣泡,而不需要額外加入其他溶劑(如丙酮等)來降低粘度以協(xié)助脫除氣泡;(3)在本發(fā)明中,導(dǎo)電納米填料無需經(jīng)過改性或修飾即可直接使用,從而簡化了生產(chǎn)工藝,并降低了生產(chǎn)成本。本發(fā)明的其他特征和優(yōu)點將在隨后的具體實施方式部分予以詳細說明。附圖說明附圖是用來提供對本發(fā)明的進一步理解,并且構(gòu)成說明書的一部分,與下面的具體實施方式一起用于解釋本發(fā)明,但并不構(gòu)成對本發(fā)明的限制。在附圖中:圖1為環(huán)氧復(fù)合材料模壓成型示意圖。圖2為實施例1中使用的還原氧化石墨烯基本參數(shù)。具體實施方式以下結(jié)合附圖對本發(fā)明的具體實施方式進行詳細說明。應(yīng)當理解的是,此處所描述的具體實施方式僅用于說明和解釋本發(fā)明,并不用于限制本發(fā)明。本發(fā)明提供了一種環(huán)氧復(fù)合材料的制備方法,該方法包括:(1)將導(dǎo)電納米填料與一部分環(huán)氧樹脂攪拌混合,并將攪拌混合后得到的混合物進行研磨,得到母料;(2)在50-80℃,將步驟(1)中得到的母料與另一部分環(huán)氧樹脂和固化劑混合,然后脫除氣泡;(3)將脫除氣泡后得到的物料進行固化成型;其中,步驟(1)和(2)中環(huán)氧樹脂的總用量與步驟(1)中導(dǎo)電納米填料的重量比為100∶0.001-0.5,步驟(1)中環(huán)氧樹脂的用量與步驟(2)中環(huán)氧樹脂的重量比為1∶0.1-100,且步驟(1)中的所述攪拌混合的條件使得所述攪拌混合后得到的混合物在60℃的動力粘度為5-18Pa·s。在步驟(1)中,將所述導(dǎo)電納米填料與一部分環(huán)氧樹脂攪拌混合并通過控制攪拌混合的條件以獲得特定動力粘度范圍內(nèi)的混合物,其目的是為了將所述導(dǎo)電納米填料均勻地分散于環(huán)氧樹脂中。當所述導(dǎo)電納米填料均勻地分散于環(huán)氧樹脂中時,最終制備的環(huán)氧復(fù)合材料中的導(dǎo)電納米填料能夠限制電荷在環(huán)氧樹脂中的傳輸,而且無機納米粒子的界面作用也可以對電荷的遷移有一定的阻礙作用,從而能夠提高所述環(huán)氧復(fù)合材料的擊穿強度。而且,本發(fā)明中導(dǎo)電納米填料可能在環(huán)氧復(fù)合材料中建立許多隧穿結(jié),通過庫倫阻塞效應(yīng)阻礙電子在電場下的定向遷移,進而提高擊穿強度。優(yōu)選情況下,步驟(1)和(2)中環(huán)氧樹脂的總用量與步驟(1)中導(dǎo)電納米填料的重量比為100∶0.01-0.15,更優(yōu)選為100∶0.01-0.10。更優(yōu)選地,步驟(1)中環(huán)氧樹脂的用量與步驟(2)中環(huán)氧樹脂的重量比為1∶1-20,更優(yōu)選為1∶2-10。在步驟(1)中,在將導(dǎo)電納米填料與環(huán)氧樹脂攪拌混合的過程中,所述導(dǎo)電納米填料可以一次性加入,也可以分批加入。優(yōu)選地,將所述導(dǎo)電納米填料分批加入環(huán)氧樹脂中。具體的,所述導(dǎo)電納米填料可以分2-5批加入環(huán)氧樹脂中,且每批加入的量可以為步驟(1)中環(huán)氧樹脂重量的10-60%,優(yōu)選為20-50%。在步驟(1)中,所述攪拌混合的條件只要能夠?qū)⑺鰯嚢杌旌虾蟮玫降幕旌衔锏膭恿φ扯日{(diào)節(jié)至上述范圍即可。優(yōu)選情況下,所述攪拌混合的條件包括:轉(zhuǎn)速為1500轉(zhuǎn)/分鐘以上,更優(yōu)選為2000-4000轉(zhuǎn)/分鐘;時間為1-5小時,更優(yōu)選為1-2小時。在本發(fā)明中,所述攪拌混合可以采用各種常規(guī)的高速攪拌器實施。所述高速攪拌器例如可以為購自VMA-Getzmann公司(德國)的型號為DISPERMATAE的攪拌器。在步驟(1)中,所述研磨的目的是通過剪切力和摩擦力的作用進一步促使導(dǎo)電納米填料均勻分散于環(huán)氧樹脂中。所述研磨的操作條件和實施設(shè)備均沒有特別的限定。在一種實施方式中,所述研磨可以用三輥研磨機實施,先后在兩個模式下進行操作。其中,間距模式下,前后輥間距比例為3∶1;壓力模式下,前后輥之間的線壓力分別可以為5-7N/mm和7-9N/mm,分別最優(yōu)選為6N/mm和8N/mm。在一種優(yōu)選實施方式中,在步驟(1)中,在將所述攪拌混合后得到的混合物進行研磨之前,優(yōu)選將所述混合物在密閉容器中放置12-24小時,使得導(dǎo)電納米填料有充足的時間與環(huán)氧樹脂接觸和浸潤。在該優(yōu)選實施方式中,所述導(dǎo)電納米填料可以更均勻地分散于環(huán)氧樹脂中,使得最終制備的環(huán)氧復(fù)合材料具有進一步改善的擊穿強度和介電性能。在本發(fā)明中,所述導(dǎo)電納米填料可以為本領(lǐng)域常規(guī)使用的各種導(dǎo)電納米填料。優(yōu)選情況下,所述導(dǎo)電納米填料為還原氧化石墨烯、金納米顆粒、銀納米顆粒、銅納米顆粒和碳納米管中的至少一種。在本發(fā)明中,所述導(dǎo)電納米填料是指在其中的一個維度上的尺寸為納米級的導(dǎo)電填料。所述導(dǎo)電納米填料的顆粒尺寸沒有特別的限定,常規(guī)的導(dǎo)電納米填料的顆粒尺寸即可適用于本發(fā)明中。優(yōu)選情況下,所述導(dǎo)電納米填料的至少一個維度上的尺寸為5-200納米,更優(yōu)選為20-100納米。在步驟(2)中,所述混合過程優(yōu)選在攪拌下進行。所述攪拌的條件可以包括:轉(zhuǎn)速為700-1200轉(zhuǎn)/分鐘,時間為30-60分鐘。所述混合過程可以常規(guī)的攪拌器中實施。所述攪拌器例如可以為購自德國IKA公司的牌號為IKARW20的攪拌器。在所述混合過程中,所述固化劑的用量沒有特別的限定,只要能夠?qū)崿F(xiàn)將所述環(huán)氧樹脂全部或者基本全部固化即可。優(yōu)選情況下,步驟(1)和(2)中環(huán)氧樹脂的總用量與步驟(2)中固化劑的重量比為100∶90-120,最優(yōu)選為100∶100。在本發(fā)明中,所述環(huán)氧樹脂是指分子中含有兩個或兩個以上環(huán)氧基團的有機化合物。所述環(huán)氧樹脂在步驟(1)的攪拌混合條件下以及在步驟(2)的混合條件下均呈液態(tài)。所述環(huán)氧樹脂可以選用本領(lǐng)域常規(guī)使用的各種環(huán)氧樹脂。優(yōu)選情況下,所述環(huán)氧樹脂為選自雙酚A型環(huán)氧樹脂、雙酚S型環(huán)氧樹脂、雙酚F型環(huán)氧樹脂和酚醛環(huán)氧樹脂中的至少一種。進一步優(yōu)選地,所述環(huán)氧樹脂的環(huán)氧值為0.15-0.55mol/100g,更優(yōu)選為0.52-0.54mol/100g。在本發(fā)明中,步驟(1)和步驟(2)中分別加入的環(huán)氧樹脂可以相同或不同,優(yōu)選相同。在一種最優(yōu)選的實施方式中,所述環(huán)氧樹脂為雙酚A型環(huán)氧樹脂,所述導(dǎo)電納米填料為還原氧化石墨烯,而且,所述雙酚A型環(huán)氧樹脂的總用量與所述還原氧化石墨烯的重量比為100∶0.01-0.02。在這種情況下,根據(jù)本發(fā)明的方法制備的環(huán)氧復(fù)合材料具有最優(yōu)的擊穿強度和介電性能。在本發(fā)明中,介電性能由介電常數(shù)表征。在本發(fā)明中,所述固化劑可以為各種常規(guī)的環(huán)氧樹脂固化劑,例如可以為胺系固化劑和/或酸酐系固化劑,所述胺系固化劑包括酚醛胺類固化劑和聚酰胺固化劑。優(yōu)選情況下,所述固化劑為選自4,4-二氨基二苯砜、四氫化鄰苯二甲酸酐、六氫化鄰苯二甲酸酐、甲基六氫苯酐、咪唑、二乙烯三胺、2,4,6-三(二甲胺基甲基)苯酚和二乙氨基丙胺中的至少一種。在步驟(2)中,在所述混合過程中還可以加入其他常規(guī)的添加劑,如促進劑。所述促進劑例如可以為選自二甲基氨基丙胺、二甲基芐胺和鄰苯二甲酸二甲酯中的至少一種。所述促進劑的加入量與步驟(1)和(2)中環(huán)氧樹脂的總重量比為0.01-2∶100,優(yōu)選為0.01-0.1∶100。在步驟(2)中,所述脫除氣泡的過程是為了脫除步驟(1)的攪拌混合和步驟(2)的混合過程中帶入的氣泡。所述脫除氣泡的過程可以采用常規(guī)的方法實施。在本發(fā)明中,由于導(dǎo)電納米填料的用量很小,使得導(dǎo)電納米填料、環(huán)氧樹脂和固化劑的混合漿料的粘度較小,從而無需額外加入其他溶劑(如丙酮)來降低粘度以協(xié)助脫除氣泡。本發(fā)明的所述脫除氣泡的方法可以采用的方法實施,例如可以將所述導(dǎo)電納米填料、環(huán)氧樹脂和固化劑的混合漿料放置在真空環(huán)境中抽除氣泡,在這種情況下,所述脫除氣泡的操作條件可以包括:溫度為50-80℃,絕對壓力為4-86kPa。在一種實施方式中,所述脫除氣泡的方法在真空烘箱中進行。在步驟(3)中,所述固化成型的方法沒有特別的限定,可以按照本領(lǐng)域常規(guī)使用的方法實施。在一種實施方式中,所述固化成型的方法包括將所述脫除氣泡后得到的物料進行壓制,然后進行加熱固化。具體的,如圖1所示,所述固化成型的方法可以包括:在兩塊不銹鋼鐵板1之間放置兩張聚酰亞胺薄膜2,在兩張聚酰亞胺薄膜2之間夾置一張中空的聚丙烯塑料模子3,將步驟(2)中制備的脫除氣泡后得到的物料注入所述聚丙烯塑料模子3的中空部分,并用壓膜機進行壓制,然后進行加熱固化。該實施方式通常用于制備環(huán)氧復(fù)合材料的薄膜產(chǎn)品。在該實施方式中,所述壓制的條件可以包括:溫度為45-60℃,壓力為1-3MPa,時間為10-20分鐘;所述加熱固化的過程可以包括:在75-100℃保持1-8小時,然后在125-200℃保持5-12小時。在另一種實施方式中,所述固化成型的方法可以包括:將步驟(2)中制備的脫除氣泡后得到的物料注入模具(如不銹鋼模具)中,然后進行程序加熱固化。該實施方式通常用于制備環(huán)氧復(fù)合材料的塊體產(chǎn)品。在該實施方式中,所述程序加熱固化的條件包括:在75-100℃保持1-8小時,然后在125-200℃保持5-12小時。本發(fā)明還提供了由上述方法制備的環(huán)氧復(fù)合材料。所述環(huán)氧復(fù)合材料具有顯著提高的擊穿強度,同時該環(huán)氧復(fù)合材料具有較好的介電性能。以下通過實施例對本發(fā)明作進一步說明,但本發(fā)明的保護范圍并不僅限于以下實施例。實施例1本實施例用于說明本發(fā)明的所述環(huán)氧復(fù)合材料及其制備方法。將30重量份的雙酚A環(huán)氧樹脂(Huntsman公司,型號為環(huán)氧值約為0.52mol/100g,下同)加入高速攪拌器(德國VMA-Getzmann公司,型號DISPERMATAE),接著將0.01重量份的還原氧化石墨烯(購自中國科學(xué)院成都有機化學(xué)有限公司,其相關(guān)參數(shù)如圖2所示)平均分成兩批加入其中,在3000轉(zhuǎn)/分鐘的轉(zhuǎn)速下攪拌混合1.5小時,得到在60℃動力粘度為10Pa·s的混合物,然后將得到的混合物在密閉容器中在室溫下放置20小時,之后將得到的物料用三輥研磨機(型號EXAKT80E)進行研磨,先后在兩個模式下進行操作。其中,間距模式下,前后輥間距比例為3∶1;壓力模式下,前后輥之間的線壓力分別為6N/mm和8N/mm,得到母料。在800轉(zhuǎn)/分鐘的轉(zhuǎn)速、60℃的條件下,將上述制備的母料與70重量份的雙酚A環(huán)氧樹脂和100重量份的酸酐類固化劑HY905(Huntsman公司)攪拌混合,然后在真空烘箱(上海一恒科技公司,牌號BPZ-6033)中在60℃、絕對壓力為4kPa的條件下放置1小時,得到漿料。將上述制備的漿料注入如圖1所示的模壓成型裝置中:在兩塊不銹鋼鐵板1之間放置兩張聚酰亞胺薄膜2,在兩張聚酰亞胺薄膜2之間夾置一張中空的聚丙烯塑料模子3,中空部分的厚度為200微米,將上述制備的漿料注入所述聚丙烯塑料模子3的中空部分,用壓膜機進行壓制,壓制的條件包括:溫度為50℃,壓力為2MPa,時間為15分鐘;然后在80℃保持6小時,之后在135℃保持10小時,得到厚度約為200微米的環(huán)氧復(fù)合材料薄膜A1。對比例1根據(jù)實施例1的方法制備環(huán)氧復(fù)合材料,所不同的是,在制備母料的過程中,所述攪拌混合的轉(zhuǎn)速為1200轉(zhuǎn)/分鐘,攪拌混合后得到的混合物在60℃的動力粘度為20Pa·s。由此制得厚度約為200微米的環(huán)氧復(fù)合材料薄膜DA1。對比例2根據(jù)實施例1的方法制備環(huán)氧復(fù)合材料,所不同的是,在制備母料的過程中,用相同重量的二氧化硅納米顆粒(德國EvonikDegussaAG公司)代替還原氧化石墨烯。由此制得厚度約為200微米的環(huán)氧復(fù)合材料薄膜DA2。實施例2-6本實施例用于說明本發(fā)明的所述環(huán)氧復(fù)合材料及其制備方法。分別根據(jù)實施例1的方法制備環(huán)氧復(fù)合材料,所不同的是,還原氧化石墨烯的加入量分別如下表1所示,從而分別相應(yīng)制得厚度約為200微米的環(huán)氧復(fù)合材料薄膜。表1導(dǎo)電納米填料用量(重量份)薄膜實施例20.03A2實施例30.05A3實施例40.07A4實施例50.10A5實施例60.15A6實施例7本實施例用于說明本發(fā)明的所述環(huán)氧復(fù)合材料及其制備方法。將10重量份的雙酚S環(huán)氧樹脂(購自天津來和商貿(mào)發(fā)展有限公司,型號為185S,環(huán)氧值約為0.54mol/100g,下同)加入高速攪拌器(德國VMA-Getzmann公司,型號DISPERMATAE),接著將0.01重量份的銀納米顆粒(北京納匯科貿(mào)有限公司)平均分成三批加入其中,在2000轉(zhuǎn)/分鐘的轉(zhuǎn)速下攪拌混合2小時,得到在60℃動力粘度為9Pa·s的混合物,然后將得到的混合物在密閉容器中在室溫下放置24小時,之后將得到的物料用三輥研磨機(型號EXAKT80E)進行研磨,先后在兩個模式下進行操作。其中,間距模式下,前后輥間距比例為3∶1;壓力模式下,前后輥之間的線壓力分別為6N/mm和8N/mm,得到母料。在700轉(zhuǎn)/分鐘的轉(zhuǎn)速、50℃的條件下,將上述制備的母料與90重量份的雙酚S環(huán)氧樹脂和45重量份的聚酰胺固化劑651(廣州維立納公司)攪拌混合,然后在真空烘箱(購自上海一恒科技公司,牌號BPZ-6033)中在60℃、絕對壓力為4kPa的條件下放置0.5小時,得到漿料。將上述制備的漿料注入如圖1所示的模壓成型裝置中:在兩塊不銹鋼鐵板1之間放置兩張聚酰亞胺薄膜2,在兩張聚酰亞胺薄膜2之間夾置一張中空的聚丙烯塑料模子3,中空部分的厚度為200微米,將上述制備的漿料注入所述聚丙烯塑料模子3的中空部分,用壓膜機進行壓制,壓制的條件包括:溫度為50℃,壓力為1MPa,時間為15分鐘;然后在80℃保持6小時,之后在180℃保持10小時,得到厚度約為200微米的環(huán)氧復(fù)合材料薄膜A7。實施例8本實施例用于說明本發(fā)明的所述環(huán)氧復(fù)合材料及其制備方法。將20重量份的酚醛環(huán)氧樹脂(購自無錫藍星樹脂公司,型號為F44(644),環(huán)氧值約為0.40mol/100g,下同)加入高速攪拌器(德國VMA-Getzmann公司,型號DISPERMATAE),接著將0.01重量份的碳納米管(拜爾公司,碳管長度為1-10μm,內(nèi)徑為約13nm,外徑為約4nm)平均分成三批加入其中,在4000轉(zhuǎn)/分鐘的轉(zhuǎn)速下攪拌混合1小時,得到在60℃動力粘度為5Pa·s的混合物,然后將得到的混合物在密閉容器中在室溫下放置24小時,之后將得到的物料用三輥研磨機(型號EXAKT80E)進行研磨,先后在兩個模式下進行操作。其中,間距模式下,前后輥間距比例為3∶1;壓力模式下,前后輥之間的線壓力分別為6N/mm和8N/mm,得到母料。在1000轉(zhuǎn)/分鐘的轉(zhuǎn)速、80℃的條件下,將上述制備的母料與80重量份的酚醛環(huán)氧樹脂和40重量份的酚醛胺類固化劑T31(無錫藍星樹脂公司)攪拌混合,然后在真空烘箱(上海一恒科技公司,牌號BPZ-6033)中在60℃、絕對壓力為4kPa的條件下放置0.7小時,得到漿料。將上述制備的漿料注入如圖1所示的模壓成型裝置中:在兩塊不銹鋼鐵板1之間放置兩張聚酰亞胺薄膜2,在兩張聚酰亞胺薄膜2之間夾置一張中空的聚丙烯塑料模子3,中空部分的厚度為200微米,將上述制備的漿料注入所述聚丙烯塑料模子3的中空部分,用壓膜機進行壓制,壓制的條件包括:溫度為70℃,壓力為1.5MPa,時間為15分鐘;然后在100℃保持2小時,之后在200℃保持8小時,得到厚度約為200微米的環(huán)氧復(fù)合材料薄膜A8。測試例根據(jù)GB/T1408.1-2006的方法分別檢測上述實施例和對比例制備的環(huán)氧復(fù)合材料薄膜以及分別由純雙酚A環(huán)氧樹脂、純雙酚S環(huán)氧樹脂和純酚醛環(huán)氧樹脂制備的厚度為約200微米的薄膜的擊穿強度;根據(jù)GB/T1409-2006的方法分別檢測上述實施例和對比例制備的環(huán)氧復(fù)合材料薄膜以及分別由純雙酚A環(huán)氧樹脂、純雙酚S環(huán)氧樹脂和純酚醛環(huán)氧樹脂制備的厚度為約200微米的薄膜的介電常數(shù);上述檢測結(jié)果如下表2所示。表2環(huán)氧復(fù)合材料薄膜擊穿強度(kV/mm)介電常數(shù)(1000Hz)純雙酚A環(huán)氧樹脂薄膜32.404.14A153.344.25DA144.134.01DA233.514.03A230.144.72A326.615.08A424.835.15A510.457.88A64.3221.49純雙酚S環(huán)氧樹脂薄膜30.323.37A732.153.45純酚醛環(huán)氧樹脂薄膜25.613.75A823.4517.4由表2的數(shù)據(jù)可以看出,根據(jù)本發(fā)明的方法制備的環(huán)氧復(fù)合材料薄膜同時具有較高的擊穿強度和較好的介電性能。具體的,通過將環(huán)氧復(fù)合材料薄膜A1與環(huán)氧復(fù)合材料薄膜DA1和DA2進行比較可以看出,環(huán)氧復(fù)合材料薄膜A1具有較高的擊穿強度;而且,雖然環(huán)氧復(fù)合材料薄膜A2-A6的擊穿強度比環(huán)氧復(fù)合材料薄膜DA1-DA2以及純雙酚A環(huán)氧樹脂薄膜小,但是,環(huán)氧復(fù)合材料薄膜A2-A6的介電常數(shù)較高,使得環(huán)氧復(fù)合材料薄膜A2-A6的綜合性能(即擊穿強度和介電性能)較好。