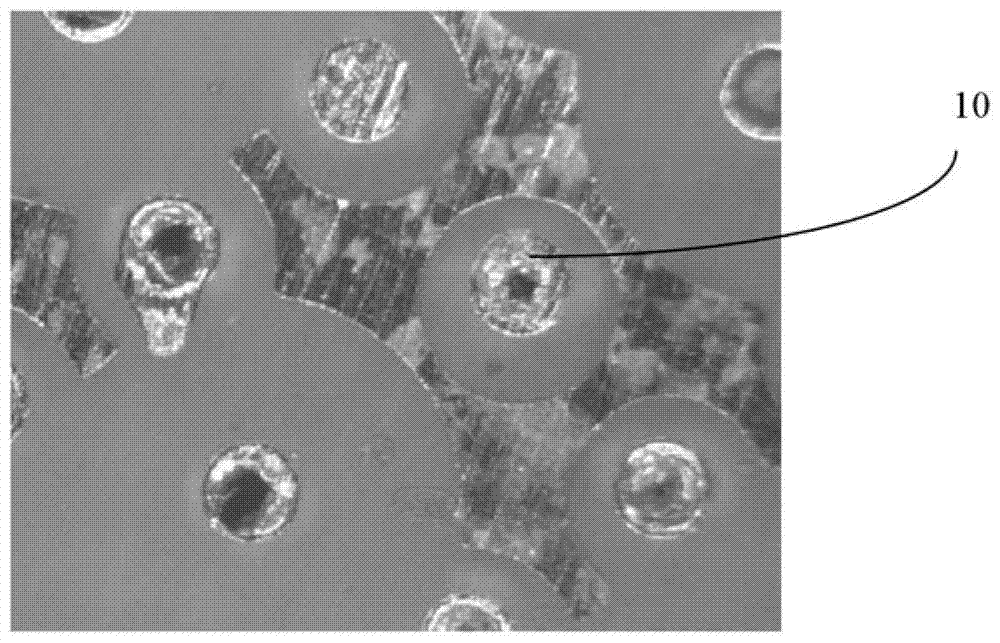
本發(fā)明屬于PCB背板制作領(lǐng)域,尤其涉及PCB背板的壓合制程的作業(yè)方法。
背景技術(shù):隨著集成電路等元件的集成度提高及其I/O數(shù)的增加、電子組裝技術(shù)的進(jìn)步和信號(hào)傳輸?shù)母哳l化和高速數(shù)字化的發(fā)展,以及電子設(shè)備高速發(fā)展的升級(jí)與換代需求,PCB背板能夠承載功能子板、信號(hào)傳輸及電源傳輸?shù)裙δ?,而其信?hào)處理功能逐漸弱化。該P(yáng)CB背板具有板于尺寸大、層數(shù)高、厚度大、孔徑縱橫比高等特點(diǎn),該P(yáng)CB背板的尺寸為660*810mm,而普通PCB的尺寸為550*610mm?,F(xiàn)有技術(shù)中壓合PCB的過(guò)程包括棕化步驟、鉚合步驟、排板步驟、壓合步驟及拆板步驟,其中,棕化時(shí)的溫度為80℃,棕化后烤板的方式為疊在一起烤板;鉚合時(shí),鉚釘機(jī)臺(tái)面平鋪壓合用的鋼板,且鉚合方式為在鉚釘機(jī)上邊排邊鉚,且鉚釘機(jī)下模沖針為10mm,由于鉚釘機(jī)下模沖針太短,可能使沖針不會(huì)露出來(lái),從而不能牢固的將背板各芯板進(jìn)行鉚合;在排板的時(shí)候,排版的層數(shù)為4-5層,排版的方式如圖1所示,為鉚合好的PCB21的兩側(cè)加鋁片22,鋁片22之后加鋼板23,鋼板23之后加20張牛皮紙24,即牛皮紙24+銅板23+鋁片22+鉚合好PCB背板21的方式;在壓合的時(shí)候,壓合的壓力為350-380PSI,溫度為90℃。通過(guò)上述制程壓合后的板于,芯板與芯板之間存在圖2所示的空洞10,且由于氣泡沿有排出,形成在圖3所示裸銅區(qū)11,所以在鉆孔,沉銅,板電之后,藥水容易滲入空洞10及裸銅區(qū)11中,導(dǎo)致內(nèi)層短路。
技術(shù)實(shí)現(xiàn)要素:本發(fā)明實(shí)施例的目的在于提供一種超大尺寸PCB背板壓合制作方法,旨在解決由于現(xiàn)有技術(shù)中的PCB制作中,壓合之后容易出現(xiàn)空洞,氣泡,從而使在后續(xù)鉆孔,沉銅,板電之后,藥水滲入,導(dǎo)致內(nèi)層短路的問(wèn)題。本發(fā)明實(shí)施例是這樣實(shí)現(xiàn)的,一種超大尺寸PCB背板壓合制作方法,該P(yáng)CB背板包括多個(gè)芯板,該制作方法包括:棕化步驟:將各所述芯板進(jìn)行棕化處理后烘干;鉚合步驟:在每?jī)蓚€(gè)芯板之間加入PP片,并將加入PP片的多個(gè)所述芯板在鉚釘機(jī)上鉚合在一起形成多層芯板;排板步驟:對(duì)鉚合好的多層芯板在鋼板上進(jìn)行排板,并與其他壓合需要的材料進(jìn)行疊合;壓合步驟:將疊合后的的多層芯板推入熱壓機(jī),經(jīng)過(guò)高溫、高壓使PP片融化,使各所述芯板結(jié)合在一起。。優(yōu)選地,該方法還包括鉆孔排氣的步驟,在芯板鉚合后或鉚合前容易產(chǎn)生氣泡的位置鉆排氣孔。優(yōu)選地,所述棕化步驟中包括烘干子步驟,烘干子步驟中的烘干溫度為90℃。優(yōu)選地,所述棕化步驟包括烤板子步驟,烤板子步驟中的烤板方式為插架式,烤板溫度為120℃,烤板時(shí)間為1小時(shí)。優(yōu)選地,所述鉚合步驟中鉚合的方式為:先將需要鉚合的芯板用鋼板支承,然后用Pin釘套好四角或四邊,再放到鉚釘機(jī)上鉚合。本發(fā)明實(shí)施例通過(guò)增加鉆排氣孔的步驟,且對(duì)棕化,鉚合,壓合各個(gè)步驟中的參數(shù)進(jìn)行改進(jìn),有效的減少了PCB背板制作中,壓合制程中產(chǎn)生的空洞及氣泡,從而有效的減少了后續(xù)經(jīng)過(guò)鉆孔,沉銅,板電制程之后的內(nèi)層短路問(wèn)題。附圖說(shuō)明圖1是現(xiàn)有技術(shù)中的PCB制作方法中疊板方式的示意圖;圖2及圖3為現(xiàn)有技術(shù)中的PCB制作方法中芯板經(jīng)壓合后產(chǎn)生的空洞及有氣泡產(chǎn)生的裸銅區(qū)的照片;圖4是本發(fā)明一實(shí)施例中的PCB制作方法中壓合制程的流程圖;圖5是圖4所示方法中排板步驟中的疊板方式的示意圖。具體實(shí)施方式為了使本發(fā)明的目的、技術(shù)方案及優(yōu)點(diǎn)更加清楚明白,以下結(jié)合附圖及實(shí)施例,對(duì)本發(fā)明進(jìn)行進(jìn)一步詳細(xì)說(shuō)明。應(yīng)當(dāng)理解,此處所描述的具體實(shí)施例僅僅用以解釋本發(fā)明,并不用于限定本發(fā)明。以下結(jié)合具體實(shí)施例對(duì)本發(fā)明的具體實(shí)現(xiàn)進(jìn)行詳細(xì)描述:如圖4所示,為本發(fā)明一實(shí)施方式中制作PCB背板的的方法的工藝流程圖。該P(yáng)CB背板包括多個(gè)芯板(圖未示),該多個(gè)芯片經(jīng)過(guò)壓合工藝之后形成PCB背板,本實(shí)施方式中,該P(yáng)CB背板為背板,具體的壓合工藝流程如圖4所示。步驟S40為棕化步驟:將所述芯板進(jìn)行棕化處理后烘干,該步驟又包括烘干子步驟及烤板子步驟,其中烘干子步驟中芯板的烘干溫度從正常的80℃提高到90℃,在烤板子步驟中,烘烤芯板的方式為由原來(lái)疊在一起的方式改為插架方式,而且保持120℃的溫度烤一個(gè)小時(shí),以保證板內(nèi)水汽充分蒸發(fā)。插架方式具體為將芯板放在一個(gè)架子上,且芯板在該架子上被互相隔開(kāi),從而縮短烤板時(shí)間,且有利于水蒸氣的蒸發(fā)。步驟S41為鉚合步驟:在每?jī)蓚€(gè)芯板之間加入PP片(膠片),并將加入PP片的多個(gè)芯板在鉚釘機(jī)上鉚合在一起形成多層芯板,在鉚合時(shí),鉚釘機(jī)臺(tái)面平鋪壓合用鋼板,鉚合方式由原來(lái)的在鉚釘機(jī)上邊排邊鉚的方式改成用鋼板支承先用PIN釘套好四角或四邊再放在鉚釘機(jī)上鉚合,如此,防止層與層之間產(chǎn)生偏位,滑板;同時(shí),調(diào)整上、下模具在同一直線,并將鉚釘機(jī)下模沖針由原來(lái)的10mm更換成15mm的沖針,使芯板套上去后沖針能夠露出來(lái),從而保證鉚釘開(kāi)花均勻,如此使芯板之間的空隙減少,從而減小后續(xù)空度及氣泡的產(chǎn)生。步驟S42為鉆孔排氣步驟,在PCB背板尺寸大,板較厚,內(nèi)層銅厚較厚時(shí),壓合時(shí)因氣體不能完全排出釋放形成氣泡殘留在PCB背板內(nèi),在鉚合后的多層芯板上填膠不良或者容易產(chǎn)生氣泡的地方鉆排氣孔,具體所選擇的排氣孔的位置應(yīng)當(dāng)為后續(xù)鉆孔制作中有需要鉆孔的位置,即在有鉆孔位的地方鉆排氣孔,所鉆排氣孔大小比所實(shí)際要鉆的孔的孔徑小0.3mm,這樣可以保證壓合時(shí)氣體從這些排氣孔中釋放出來(lái),同時(shí)這些排氣孔孔在壓合后重新填膠被封住,后續(xù)鉆孔時(shí)再用原孔徑鉆掉,后續(xù)正常制作即可。在其他實(shí)施方式中,該步驟也可在鉚合步驟之前對(duì)單個(gè)芯板鉆排氣孔。步驟S43為排板步驟:對(duì)鉚合好的多層芯板在鋼板上進(jìn)行排板,并與其他壓合需要的材料進(jìn)行疊合,其他壓合需要的材料包括鋁片、鋼板、及牛皮紙等,本實(shí)施方式中,還包括離型膜和硅膠墊,本實(shí)施方式中,排板的層數(shù)為2層,每層板的疊板如圖4所示,即在圖1所示疊板方式的基礎(chǔ)上,在鋼板22與鋁片21之間加離型膜25及硅膠墊26,其中,硅膠墊25在鋁片21之后,離型膜26在硅膠墊25之后,加了硅膠墊25及離型膜26之后,有助于在壓合時(shí)緩沖熱量,使鉚合好的PCB21受熱均勻,從而使氣泡緩慢排出。在其他實(shí)施方式中,其他壓合需要的材料不限于上述材料,疊板的次序也不限于本實(shí)施方所描述的方式,具體可以根據(jù)實(shí)際情況進(jìn)行變化。步驟S44為壓合步驟:將疊好的PCB背板推入熱壓機(jī),經(jīng)過(guò)高溫,高壓使PP片融化,從而使芯板緊密的結(jié)合在一起,壓合時(shí)的轉(zhuǎn)高壓時(shí)間不能太早也不能太遲,本實(shí)施方式中為35分鐘,如此可保證PP在充分流動(dòng)使填高壓,保證填膠的均勻性。轉(zhuǎn)高壓壓力由普通的350-380PSI提高到450PSI,轉(zhuǎn)高壓的溫度為由原來(lái)的90℃左右提高到106℃,且根據(jù)材料特性來(lái)調(diào)整升溫速率,本實(shí)施方式中,溫度為80-140℃之間的升溫速率為2.0-2.5℃/分鐘,如此在壓合的時(shí)候,可使流膠均勻,從而有效的減少了空洞及氣泡。本發(fā)明通過(guò)對(duì)壓合制成中的各個(gè)步驟進(jìn)行改進(jìn),從而有效減少了PCB背板在壓合后產(chǎn)生的空洞和氣泡,從而減少了PCB背板后續(xù)滲銅短路的問(wèn)題。以上所述僅為本發(fā)明的較佳實(shí)施例而已,并不用以限制本發(fā)明,凡在本發(fā)明的精神和原則之內(nèi)所作的任何修改、等同替換和改進(jìn)等,均應(yīng)包含在本發(fā)明的保護(hù)范圍之內(nèi)。