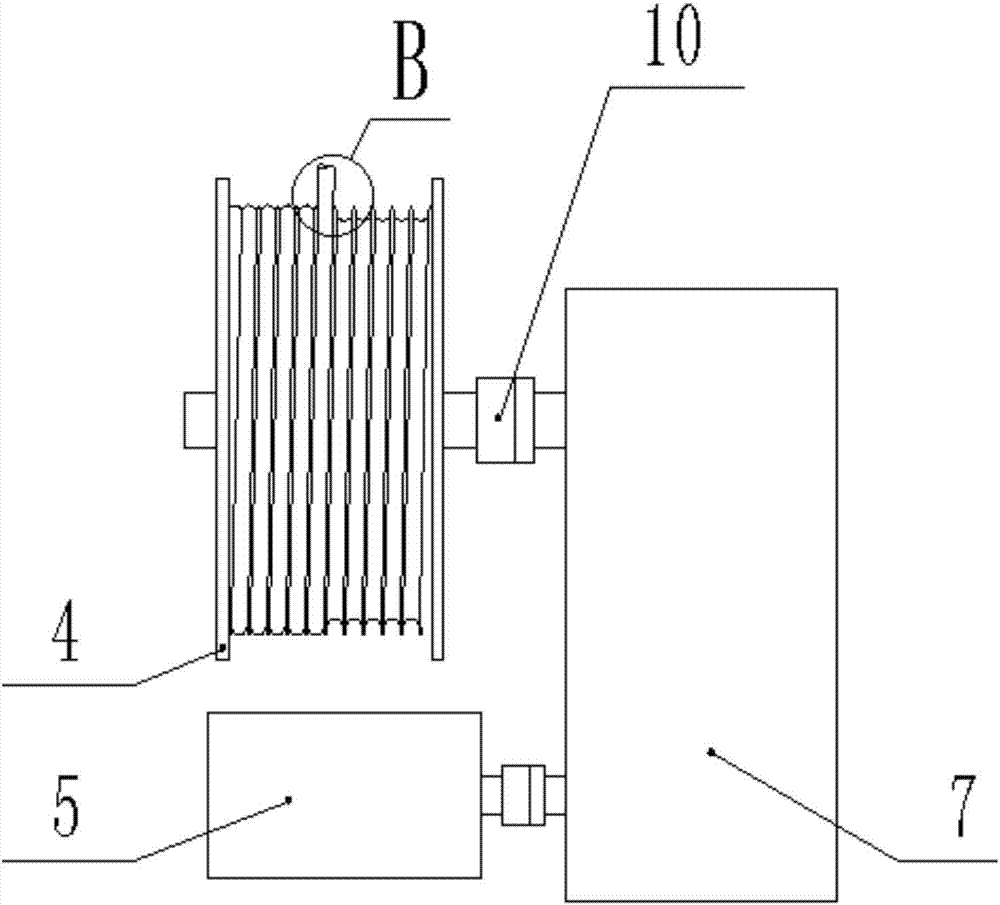
本發(fā)明屬于油田采油設備領域,尤其涉及一種抽油泵智能驅動裝置及卷揚式抽油機系統(tǒng)。
背景技術:抽油機是石油生產過程中常用的一種采油設備,采油時,抽油機通過抽油桿帶動井下的抽油泵泵桿上下往復運動,從而將地層內的石油等液體泵送至地面?,F(xiàn)有的抽油機大多為游梁式抽油機,受結構所限,這種抽油機的沖程較短、沖次較高,因此機械效率較低,單位產量的能耗較大。為了進一步降低能耗,提高生產效益,申請?zhí)枮镃N201010299647.0的發(fā)明專利公開了一種智能卷揚式提拉采油系統(tǒng),這種采油系統(tǒng)通過卷揚機和盤繞在卷揚機上的鋼絲繩帶動井下的抽油泵的泵桿運動,從抽油機的結構上實現(xiàn)了提高沖程和降低沖次的目的(沖程可達百米),進而降低能耗,提高生產效益。然而,使用鋼絲繩作為抽油繩具有一定的缺陷:1、油井生產時,需要在井口處對上下往復運動的抽油繩進行密封,以防止井下的油和水從井口噴出而污染環(huán)境,但鋼絲繩的表面粗糙且內部的鋼絲與鋼絲之間充滿縫隙,因此密封效果較差。為了解決上述的問題,技術人員在鋼絲繩的表面設置了塑料層,在鋼絲繩的內部設置了熱熔膠,在一定程度上解決了鋼絲繩的井口密封問題。然而,由于鋼絲與塑料和熱熔膠的附著強度均比較差,這種新型鋼絲繩在使用一段時間后便會出現(xiàn)鋼絲與塑料或鋼絲與熱熔膠分離的問題,進而再次產生密封不嚴的問題。2、鋼絲繩的耐磨性較差,使用壽命較短,因此需要頻繁更換,并且,磨損后的鋼絲繩不能再次修復使用,只能報廢處理,因此,采用鋼絲繩時,設備的維護成本比較高。3、鋼絲繩的密度較大,因此對設備的動力性能要求較高,據省能耗也比較大。4、生產時,常常需要在地面與井下的電子設備(傳感器、測試儀器等)進行通信,由于現(xiàn)有的抽油桿本身無法實現(xiàn)這一功能,進行測試時,只能先將抽油桿起出,再向井中下入測試電纜和測試儀器,這種方式不但測試過程繁瑣,而且必須在停產狀態(tài)下進行,會影響生產的正常進行;5、在使用過程中,抽油桿表面會大量結蠟,進而對生產造成不利影響。另外,當需要進行井下作業(yè)時,需要將現(xiàn)有的此類抽油機上的導輪(甚至是井口支架的整體)拆下,從而避免導輪或井口支架妨礙井下作業(yè)的進行,而拆卸導輪時通常需要工人攀登至高處并需要動用起重機。因此拆卸過程比較繁瑣。
技術實現(xiàn)要素:本發(fā)明提供一種抽油泵智能驅動裝置及卷揚式抽油機系統(tǒng),實現(xiàn)了長沖程、低沖次采油,從而大大增加采油效率,以解決上述背景技術中提出的問題。本發(fā)明所解決的技術問題采用以下技術方案來實現(xiàn):本發(fā)明提供了一種抽油泵智能驅動裝置,包括電機、減速器、絞盤、抽油桿和變頻控制裝置,所述的電機的輸出軸通過聯(lián)軸器與減速器的輸入軸連接,所述的絞盤的旋轉軸通過聯(lián)軸器與減速器的輸出軸連接,所述的抽油桿為柔性抽油桿,抽油桿的一端固定在絞盤上,另一端引入井口內。所述的抽油桿共分為兩段,分別稱為抽油桿上段和抽油桿下段,兩段抽油桿通過抽油桿接頭連接,所述的抽油桿上段為玻璃纖維桿,抽油桿下段為碳纖維桿,抽油桿上段和抽油桿下段的內部均設置有通信電纜和電熱帶,抽油泵的泵桿上提至上極限位置時,抽油桿接頭剛好到達井口處。所述的絞盤的邊緣設置有沿圓周陣列分布的制動槽,絞盤的側面設置有制動爪,制動爪的一端鉸接在絞盤支架上,制動爪的另一端設置有與所述的制動槽匹配的制動塊,制動爪的中部設置有一個軸孔,軸孔內安裝有一個凸輪,凸輪上的偏心孔內安裝有制動軸,制動軸的軸端固定連接有制動手柄。作為優(yōu)選方案,所述的抽油桿上段的結構包括縱向玻璃纖維層、纏繞玻璃纖維層和環(huán)氧樹脂層,所述的通信電纜、電熱帶、縱向玻璃纖維層、纏繞玻璃纖維層和環(huán)氧樹脂層由內向外依次設置,所述的環(huán)氧樹脂層內摻有金剛砂。所述的絞盤上設置有螺旋狀的纏繞引導槽。所述的變頻控制裝置內設置有變頻器和制動電阻。所述的抽油桿接頭包括上連接套、錐套、轉接頭和下連接套,所述的上連接套和下連接套分別通過螺紋連接在轉接頭的兩端,上連接套和下連接套的內部各設置有一個錐套,錐套的外側與上連接套或下連接套通過錐面配合,錐套上設置有沿其軸線方向切出的切口,錐套與上連接套或下連接套相對滑動后產生夾緊作用,從而將抽油桿上段和抽油桿下段夾緊在抽油桿接頭上。本發(fā)明提供了一種卷揚式抽油機系統(tǒng),包括上述的智能抽油機驅動裝置、井口支架和抽油泵,所述的井口支架豎立在井口處,井口支架的頂部設置有導輪,從抽油泵智能驅動裝置上引出的抽油桿繞過導輪的上側之后,沿豎直方向垂下,繼而引入井口內并與抽油泵的泵桿連接。所述的井口支架安裝在位于地面的混凝土基座上,井口支架的底部設置有轉盤,混凝土基座的頂部預制有井口支架安裝板,轉盤與井口支架安裝板在其二者的中部通過銷軸旋轉連接,在其二者的邊緣通過螺栓固定連接,轉盤和井口支架安裝板的一組相對面上均設置有圓環(huán)形凹槽,圓環(huán)形凹槽內設置有鋼球,所述的井口支架與混凝土基座之間設置有連桿,連桿的一端通過插銷連接在井口支架的中部,另一端通過插銷連接在混凝土基座的邊緣。從抽油泵智能驅動裝置上引出的抽油桿的下端設置有帶有標準抽油桿螺紋的泵桿接頭,泵桿接頭內設置有壓力傳感器。作為優(yōu)選方案,所述的泵桿接頭包括泵桿連接體、鎖緊螺母和壓力傳感器,鎖緊螺母通過螺紋連接在泵桿連接體的上端,壓力傳感器設置在泵桿連接體的內部,泵桿連接體的上端設置有環(huán)形排布的夾爪,所有夾爪的外側面與鎖緊螺母的內側面通過錐面配合,所述的抽油桿的下端插在夾爪之間,鎖緊螺母旋進過程中,通過錐面配合迫使夾爪緊靠在抽油桿下段的外側,從而將泵桿接頭固定連接在抽油桿上,壓力傳感器與抽油桿下段內的通信電纜連接。壓力傳感器的承壓面與壓力傳感器的外部通過壓力平衡孔連通。本發(fā)明的有益效果為:本發(fā)明提供了一種新型的抽油泵智能驅動裝置及卷揚式抽油機系統(tǒng),在本發(fā)明中,采用玻璃纖維桿作為抽油繩,代替了現(xiàn)有技術中使用的鋼絲繩,與現(xiàn)有技術相比,具有如下優(yōu)點:1、玻璃纖維桿(即玻璃鋼桿)的外表面十分光滑平整,與鋼絲繩相比更容易在井口處進行可靠的密封,從而改善密封效果;玻璃纖維桿的內部為實心結構,井下的高壓液體無法從抽油繩的內部泄漏至井外,從而進一步改善了密封性。需要說明的是,玻璃纖維桿雖然為桿狀,但柔性較好,因此足以作為柔性抽油桿(抽油繩)使用。2、通過在玻璃纖維桿的外層環(huán)氧樹脂內添加金剛砂,可使得玻璃纖維桿的耐磨性能遠高于鋼絲繩或者鋼絲繩外的塑料層,因此,玻璃纖維桿與鋼絲繩相比,使用壽命更長。另外,在玻璃纖維桿的外層,作為耐磨層的環(huán)氧樹脂層磨損后,可用同樣組份的環(huán)氧樹脂進行修復,而不用完全報廢,從而節(jié)省了物料成本,而修復前后,玻璃纖維桿的抗拉性能幾乎不會降低。3、與鋼絲繩相比,玻璃纖維桿和碳纖維桿的密度低得多,從而大大降低了舉升載荷,也降低了舉升能耗。眾所周知,抽油桿在使用過程中,不但要承受很大的拉力載荷,而且必須具備極好的耐磨性能和耐腐蝕性能,而碳纖維桿具有超強的抗拉強度和耐腐蝕性,同時在碳纖維桿外側的環(huán)氧樹脂層中摻入金剛砂也可有效改善其耐磨性能,因此非常適合在井下環(huán)境中使用。另外,與玻璃纖維桿相比,碳纖維桿的密度更細小,可進一步較小舉升載荷,從而進一步降低據省能耗。但是,碳纖維桿的柔韌性較差,滿足抽油桿性能需求的碳纖維桿的最小彎曲半徑至少在1.5米以上,如果將碳纖維桿盤繞在絞盤上,那么絞盤的尺寸會很大,不但增加了抽油機的成本,而且不利于抽油機的安裝和運輸。為了解決在井上部分使用碳纖維抽油桿時絞盤尺寸過大的問題,本發(fā)明中的柔性抽油桿采用兩段式結構,抽油桿上段采用最小彎曲半徑較小的玻璃纖維桿制作,與碳纖維桿相比,在保證同樣抗拉強度的同時,玻璃纖維桿的最小彎曲半徑可達到0.5米左右,從而有效減小了絞盤的尺寸。需要說明的是,在油井內,靠近井口的區(qū)段內的抽油桿的受磨損和腐蝕的侵害較少,因此,雖然與碳纖維桿相比,玻璃纖維桿的性能稍差,但足以滿足抽油桿上段的使用要求。4、本發(fā)明在抽油桿的內部設置了通信電纜,通過通信電纜可實現(xiàn)地面與井下的通信,從而將井下的傳感器采集到的信號實時傳回地面,以實現(xiàn)對井下狀況的實時監(jiān)測。5、本發(fā)明在抽油桿的內部設置了電熱帶(電熱帶可纏繞在通信電纜的外側),通過電熱帶可對抽油桿進行加熱,從而有效避免抽油桿結蠟。6、本發(fā)明在抽油桿的下端設置了壓力傳感器,通過壓力傳感器測得的壓力參數(shù),可準確換算出井下液面高度,以便對井下情況進行實時監(jiān)控。另外,測量液面時,無需停產停機,不會對生產進度造成影響。7、本發(fā)明采用兩種制動方式:一種是通過變頻控制裝置內的制動電阻對電機進行電氣制動,另一種是采用了凸輪式的制動機構進行機械制動。電氣制動可通過常見的的自動化控制方式實現(xiàn)自動制動,可在無人看管的情況下自主動作,防止發(fā)生事故;機械制動保證了制動的可靠性,避免電器制動斷電失效后產生無法制動的問題。通過制動軸帶動凸輪旋轉,進而調整制動爪與絞盤邊緣之間的距離,當制動爪上的制動塊剛好卡在絞盤邊緣的制動槽內時,絞盤被制動。與現(xiàn)有的抱緊制動機構相比,這種制動機構的制動力更大,制動更可靠。8、本發(fā)明中的井口支架采用可旋轉連接,進行井下作業(yè)前,先撤掉抽油桿,然后將連接井口支架和混凝土基座的螺栓拆掉,便可將井口支架沿銷軸旋轉180°,從而讓出井口上方的空間,井下作業(yè)完成后,將井口支架轉回原位即可。與拆卸導輪或井口支架相比,這樣的設計不但操作省力,拆裝方便,而且工人在地面即可完成轉動井口支架的操作,消除了高空作業(yè)存在的安全隱患。另外,上述結構非常簡單,以非常低廉的成本投入,達到了較好的技術效果。附圖說明圖1是卷揚式抽油機系統(tǒng)的整體結構示意圖;圖2是電機、減速器和絞盤的連接結構示意圖;圖3是圖1中A處的局部放大圖;圖4是圖2中B處的局部放大圖;圖5是抽油桿接頭的結構示意圖;圖6是圖5中C處的截面圖;圖7是泵桿接頭的結構示意圖;圖8是玻璃纖維桿的結構示意圖;圖9是井口支架與混凝土基座的連接結構示意圖。圖中:1-井口,2-井口支架,3-絞盤支架,4-絞盤,5-電機,6-變頻控制裝置,7-減速器,8-抽油桿上段,9-導輪,10-聯(lián)軸器,11-纏繞引導槽,12-上連接套,13-轉接頭,14-電連接器,15-下連接套,16-抽油桿下段,17-電熱帶,18-標準抽油桿螺紋,19-壓力傳感器,20-鎖緊螺母,21-夾爪,22-壓力平衡孔,23-錐套,24-制動爪,25-制動軸,26-制動塊,27-制動槽,28-制動手柄,29-凸輪,30-通信電纜,31-切口,32-泵桿連接體,33-混凝土基座,34-連桿,35-井口支架安裝板,36-鋼球,37-螺栓,38-轉盤,39-銷軸,40-縱向玻璃纖維層,41-纏繞玻璃纖維層,42-環(huán)氧樹脂層。具體實施方式以下結合附圖對本發(fā)明做進一步描述:本實施例是一種卷揚式抽油機系統(tǒng),包括抽油泵智能驅動裝置、井口支架2和抽油泵。抽油泵智能驅動裝置包括電機5、減速器7、絞盤4、抽油桿和變頻控制裝置6,所述的電機5的輸出軸通過聯(lián)軸器10與減速器7的輸入軸連接,所述的絞盤4的旋轉軸通過聯(lián)軸器10與減速器7的輸出軸連接。本發(fā)明中采用了減速器7作為電機5與絞盤4之間的傳動裝置,而現(xiàn)有技術中采用了鏈傳動機構。與鏈傳動機構相比,減速器7可以提供更大的減速比,從而降低對電機5的功率的要求。所述的抽油桿共分為兩段,分別稱為抽油桿上段8和抽油桿下段16,兩段抽油桿通過抽油桿接頭連接,所述的抽油桿上段8為玻璃纖維桿,抽油桿下段16為碳纖維桿。與鋼絲繩相比,玻璃纖維桿和碳纖維桿的密度低得多,從而大大降低了舉升載荷,也降低了舉升能耗。玻璃纖維桿(即玻璃鋼桿)的外表面十分光滑平整,與鋼絲繩相比更容易在井口處進行可靠的密封,從而改善密封效果;玻璃纖維桿的內部為實心結構,井下的高壓液體無法從抽油繩的內部泄漏至井外,從而進一步改善了密封性。需要說明的是,玻璃纖維桿雖然為桿狀,但柔性較好,因此足以作為柔性抽油桿(抽油繩)使用。另外,使用表面光潔度比較差的鋼絲繩時,對井口密封盒內的密封件的損耗比較大,密封件需要頻繁更換,密封件的成本雖然很低,但更換密封件時所消耗的人力以及對生產的影響會產生很大的經濟損失,而采用本發(fā)明所述的玻璃纖維桿可有效解決這一問題。在油井的井下,抽油桿所處的理化環(huán)境非常復雜,既要承受高溫、高壓,又要承受多種酸、堿等多種化學藥劑的腐蝕,因此,抽油桿不但要承受很大的拉力載荷,而且必須具備極好的耐磨性能和耐腐蝕性能,而碳纖維桿具有超強的抗拉強度和耐腐蝕性,同時在碳纖維桿外側的環(huán)氧樹脂層中摻入金剛砂也可有效改善其耐磨性能,因此非常適合在井下環(huán)境中使用。另外,與玻璃纖維桿相比,單位長度的碳纖維桿的重量更小,可進一步減小舉升載荷,從而進一步降低舉升能耗。但是,在全井均使用碳纖維桿并不合理,原因在于:碳纖維桿的柔韌性較差,滿足抽油桿性能需求的碳纖維桿的最小彎曲半徑至少在1.5米以上,如果將碳纖維桿盤繞在絞盤4上,那么絞盤4的外徑至少達到3米,這不但會增加了抽油機的成本,而且難以進行安裝和運輸。為了解決在井上部分使用碳纖維抽油桿時絞盤4尺寸過大的問題,本發(fā)明中的柔性抽油桿采用兩段式結構,需要在絞盤4上盤繞的抽油桿上段8采用最小彎曲半徑較小的玻璃纖維桿制作,與碳纖維桿相比,在保證同樣抗拉強度的同時,玻璃纖維桿的最小彎曲半徑可達到0.5米左右,從而有效減小了絞盤4的尺寸。需要說明的是,在油井內,靠近井口的區(qū)段內的抽油桿的受磨損和腐蝕的侵害較少,因此,雖然與碳纖維桿相比,玻璃纖維桿的性能稍差,但足以滿足抽油桿上段8的使用要求。退一步講,即使抽油桿上段8損壞失效,也只需更換抽油桿上段8即可,而不需要更換全部抽油桿。抽油桿上段8和抽油桿下段16的內部均設置有通信電纜30和電熱帶17,通信電纜30和電熱帶17在抽油桿接頭處通過電連接器14對接。。在抽油桿的內部設置通信電纜30,通過通信電纜30可實現(xiàn)地面與井下的通信,從而將按需設置在井下的各種傳感器采集到的信號實時傳回地面,以實現(xiàn)對井下狀況的實時監(jiān)測。在抽油桿的內部設置電熱帶17(電熱帶17可纏繞在通信電纜30的外側),通過電熱帶17可對抽油桿進行加熱,從而有效避免抽油桿結蠟。在上述結構中,通信電纜30、電熱帶17和電連接器14均為市售產品,很容易買到,因此具體結構不再贅述。具體實施時,使抽油桿上段8的長度最小,可保證全井抽油桿的重量最小,而抽油泵的泵桿上提至上極限位置,抽油桿接頭剛好到達井口1處時,抽油桿上段8的長度為最小。所述的抽油桿的下端設置有帶有標準抽油桿螺紋18的泵桿接頭,泵桿接頭內設置有壓力傳感器19。通過壓力傳感器19測得的壓力參數(shù),可準確換算出井下液面高度,以便對井下情況進行實時監(jiān)控,當液面較高時,相應地配以較大的沖程,當液面較低時相應地配以較小的沖程,從而實現(xiàn)對沖程的智能化調整,通過這種調整實現(xiàn)液面與沖程的匹配,可起到防止“干抽”現(xiàn)象的作用,即有利于延長抽油泵的使用壽命,又能降低電機5的載荷,節(jié)能增效。另外,測量液面時,無需停產停機,不會對生產進度造成影響。所述的絞盤4的邊緣設置有沿圓周陣列分布的制動槽27,絞盤4的側面設置有制動爪24,制動爪24的一端鉸接在絞盤支架3上,制動爪24的另一端設置有與所述的制動槽27匹配的制動塊26,制動爪27的中部設置有一個軸孔,軸孔內安裝有一個凸輪29,凸輪29上的偏心孔內安裝有制動軸25,制動軸25的軸端固定連接有制動手柄28。制動時,向下壓動制動手柄28,以使制動軸25旋轉,進而帶動凸輪29旋轉,由于制動軸25與絞盤4相對靜止,所以,轉動的凸輪29迫使制動爪24向絞盤4靠近,進而使制動塊26與制動槽27卡合,卡合后,凸輪29應該已轉過死點,從而保證松開制動手柄28后,制動不會自動解除。本發(fā)明采用兩種制動方式:一種是通過變頻控制裝置6內的制動電阻對電機進行電氣制動(此為通用的電機制動方式),另一種是采用了凸輪式的制動機構進行機械制動。電氣制動可通過常見的自動化控制方式實現(xiàn)自動制動,可在無人看管的情況下自主動作,防止發(fā)生事故;機械制動保證了制動的可靠性,避免電器制動斷電失效后產生無法制動的問題。另外,現(xiàn)有技術中,某些抽油機上也設置了機械制動機構,但通常是采用摩擦制動原理制成的,采用這種制動方式時,人需要施加的驅動力較大,而制動力仍然較小。與摩擦制動機構相比,上述的機械制動機構的驅動力更小,制動力更大,制動更可靠,結構也更加簡單,使用壽命也更長。需要說明的是,在本發(fā)明中,只需要在停機的情況下,而不需要在運轉過程中制動?,F(xiàn)有技術中,通常采用復雜的排繩機構對抽油繩的排列進行引導,以使其整齊地纏繞在絞盤4上。而在本發(fā)明中,所述的絞盤4上設置有螺旋狀的纏繞引導槽11,纏繞引導槽11可在絞盤4旋轉過程中對抽油桿上段8的纏繞路徑進行引導,從而使抽油桿上段整齊排列。與現(xiàn)有技術相比,本發(fā)明省去了復雜的排繩機構,從而使設備的結構得到顯著的簡化。所述的抽油桿接頭包括上連接套12、錐套23、轉接頭13和下連接套15,所述的上連接套12和下連接套15分別通過螺紋連接在轉接頭13的兩端,上連接套12和下連接套15的內部各設置有一個錐套23,錐套23的外側與上連接套12或下連接套15通過錐面配合,錐套23上設置有沿其軸線方向切出的切口31,錐套23與上連接套12或下連接套15相對滑動后產生夾緊作用,從而將抽油桿上段8和抽油桿下段16夾緊在抽油桿接頭上。抽油桿接頭是專門為連接抽油桿上段8和抽油桿下段16而設計的,其結構上采用錐面配合的夾緊原理,抽油桿承受的拉力載荷越大,夾緊力越大,從而保證了兩段抽油桿之間牢固可靠地連接。所述的泵桿接頭包括泵桿連接體32、鎖緊螺母20和壓力傳感器19,鎖緊螺母20通過螺紋連接在泵桿連接體32的上端,壓力傳感器19設置在泵桿連接體32的內部,泵桿連接體32的上端設置有環(huán)形排布的夾爪21,所有夾爪21的外側面與鎖緊螺母20的內側面通過錐面配合,所述的抽油桿的下端插在夾爪21之間,鎖緊螺母20旋進過程中,通過錐面配合迫使夾爪21緊靠在抽油桿下段16的外側,從而將泵桿接頭固定連接在抽油桿上,壓力傳感器19與抽油桿下段內的通信電纜30連接。壓力傳感器19的承壓面與壓力傳感器19的外部通過壓力平衡孔22連通。泵桿接頭的基礎功能是將抽油桿與井下的泵桿連接,本發(fā)明在滿足其基本功能的基礎上設置了容納壓力傳感器19的空間,壓力傳感器19的上端直接電連接在通信電纜30上,壓力傳感器19的下端與外界連通,使得壓力傳感器19的安裝結構最簡化,壓力傳感器19的周圍與泵桿連接體32的內壁之間設置有O型密封圈,防止井下的液體進入通信電纜30與壓力傳感器19的接線頭處而導致短路事故。所述的井口支架2豎立在井口處,井口支架2的頂部設置有導輪9,抽油桿的一端固定在絞盤4上,另一端繞過導輪9的上側之后,沿豎直方向垂下,繼而引入井口1內并與抽油泵的泵桿連接。井口支架2安裝在位于地面的混凝土基座33上,井口支架3的底部設置有轉盤38,混凝土基座33的頂部預制有井口支架安裝板35,轉盤38與井口支架安裝板35在其二者的中部通過銷軸39旋轉連接,在其二者的邊緣通過螺栓37固定連接。井口支架2采用可旋轉連接,進行井下作業(yè)前,先撤掉抽油桿,然后將連接井口支架2和混凝土基座33的螺栓37拆掉,便可將井口支架2沿銷軸39旋轉180°,從而讓出井口1上方的空間,井下作業(yè)完成后,將井口支架2轉回原位即可。與拆卸導輪9或井口支架2相比,這樣的設計不但操作省力,拆裝方便,而且工人在地面即可完成轉動井口支架2的操作,消除了高空作業(yè)存在的安全隱患。另外,上述結構非常簡單,以非常低廉的成本投入,達到了較好的技術效果。轉盤38和井口支架安裝板35的一組相對面上均設置有圓環(huán)形凹槽,圓環(huán)形凹槽內設置有鋼球36。鋼球36與位于其上下兩側的轉盤38和井口支架安裝板35共同構成了一個與推力軸承類似的軸承機構,其功能是降低井口支架2旋轉時的摩擦阻力,使得井口支架2可由單人進行旋轉操作,達到了減少人員投入的目的。所述的井口支架2與混凝土基座33之間設置有連桿34,連桿34的一端通過插銷連接在井口支架2的中部,另一端通過插銷連接在混凝土基座33的邊緣。連桿34的作用是對井口支架2的結構進行加固,使其具有更高的結構強度。連桿34通過插銷安裝連接,是為了在旋轉井口支架2時進行拆卸。所述的抽油桿上段8的結構包括縱向玻璃纖維層40、纏繞玻璃纖維層41和環(huán)氧樹脂層42,所述的通信電纜30、電熱帶17、縱向玻璃纖維層40、纏繞玻璃纖維層41和環(huán)氧樹脂層42由內向外依次設置。在上述結構中,縱向玻璃纖維層40是承受拉力載荷的核心結構,其中的玻璃纖維沿玻璃纖維桿的軸向設置,并且其中的各股玻璃纖維通過環(huán)氧樹脂粘結在一起。纏繞玻璃纖維層41內的玻璃纖維螺旋纏繞在縱向玻璃纖維層40的外側,螺旋纏繞結構可有效改善玻璃纖維桿的抗彎、抗扭和抗壓強度,防止玻璃纖維桿在承受彎矩、扭矩或受壓時劈裂。環(huán)氧樹脂層42作為耐磨層,在抵抗磨損的同時,也有效保護了玻璃纖維桿內部的玻璃纖維,防止其損傷。通過在玻璃纖維桿的外層環(huán)氧樹脂內添加金剛砂,可使得玻璃纖維桿的耐磨性能遠高于鋼絲繩或者鋼絲繩外的塑料層,生產實踐證明,在環(huán)氧樹脂層42內添加5%的金剛砂,耐磨強度至少提高三倍。因此,玻璃纖維桿與鋼絲繩相比,使用壽命更長。另外,在玻璃纖維桿的外層,作為耐磨層的環(huán)氧樹脂層42磨損后,可用同樣組份的環(huán)氧樹脂進行修復,而不用完全報廢,從而節(jié)省了物料成本,而修復前后,只要玻璃纖維桿的中的玻璃纖維沒有磨損,玻璃纖維桿的抗拉性能幾乎不會降低。由此可見,與鋼絲繩相比,玻璃纖維桿具有“壽命更長”和“可修復”這兩個重要特征,通過延長抽油桿(繩)的使用壽命,并對抽油桿(繩)進行重復利用,可節(jié)省抽油桿(繩)投入,從而產生可觀的經濟效益。所述的碳纖維桿的結構可參考玻璃纖維桿的結構(即只把玻璃纖維桿中的玻璃纖維成分換成碳纖維)來制造。