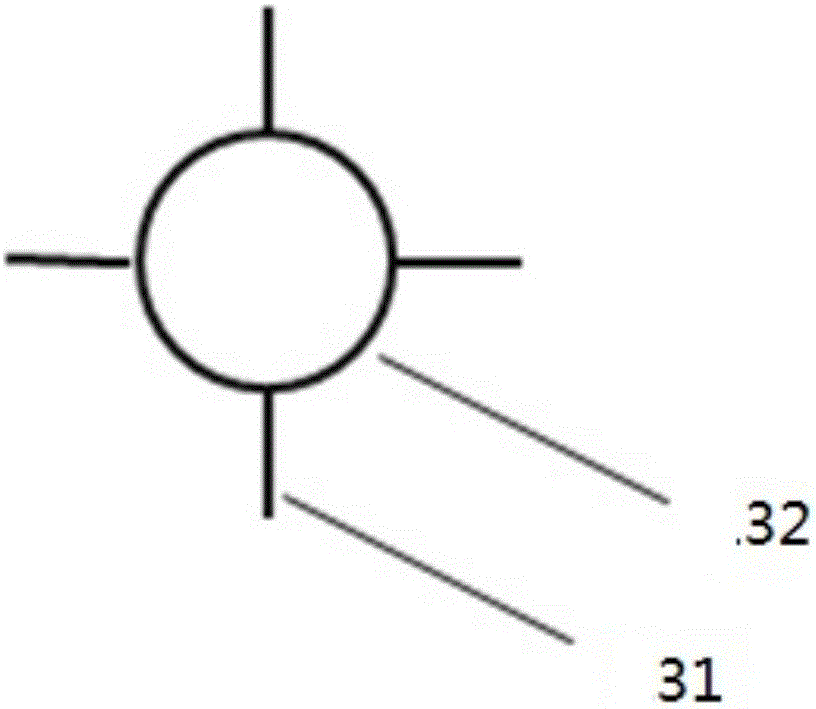
本發(fā)明屬于合成氣制備領(lǐng)域,具體涉及一種合成氣的制備系統(tǒng)及方法。
背景技術(shù):
:我國能源結(jié)構(gòu)特點是“富煤貧油少氣”,資源稟賦現(xiàn)狀決定了我國必須要發(fā)展煤化工,實現(xiàn)對石油和天然氣的部分替代,以保障我國經(jīng)濟發(fā)展和能源安全。我國煤化工事業(yè)經(jīng)過幾十年的發(fā)展,目前已經(jīng)取得了可喜的成績,但是現(xiàn)代煤化工依然普遍存在著“投資大、污染嚴重、能耗高、水耗高”等問題。合成氣的主要成分為一氧化碳(CO)和氫氣(H2),可作為化學(xué)工業(yè)的基礎(chǔ)原料,生產(chǎn)各種化工產(chǎn)品。經(jīng)過多年的發(fā)展,以天然氣(CH4)、煤為原料制備合成氣的工藝已很成熟。近年來,煤炭分質(zhì)梯級利用,也就是常說的煤熱解,由于其特有的優(yōu)勢,越來越得到重視和認可。煤熱解后產(chǎn)生的熱解氣中含有天然氣、一氧化碳和氫氣,可用于制備合成氣,但熱解氣也含有大量的雜質(zhì)。要想用熱解氣制備合成氣,必須先將熱解氣凈化、分離,然后再將天然氣制成合成氣,工藝十分復(fù)雜。技術(shù)實現(xiàn)要素:本發(fā)明的目的是提供一種合成氣的制備系統(tǒng)及方法。本發(fā)明提供的一種合成氣的制備系統(tǒng),包括熱解單元和氣體處理單元;所述熱解單元設(shè)有煤入口和熱解氣出口;所述熱解氣出口位于所述熱解單元的頂部,所述熱解氣出口的兩側(cè)設(shè)有水蒸氣噴傘;所述熱解單元的熱源為加熱管,所述加熱管為催化劑載體;所述氣體處理單元設(shè)有熱解氣入口和合成氣出口,所述熱解氣入口和所述熱解單元的熱解氣出口相連。進一步地,所述加熱管為翅片加熱管。進一步地,所述水蒸氣噴傘的開口面向所述熱解氣出口,所述水蒸氣噴傘向所述熱解單元內(nèi)噴灑水蒸氣。本發(fā)明提供的一種利用上述系統(tǒng)制備合成氣的方法,其特征在于,所述方法包括以下步驟:將甲烷分解催化劑涂覆于加熱管表面,并將煤送入所述熱解單元進行熱解,制得熱解氣;將所述熱解氣送入所述氣體處理單元進行凈化、除塵和分離,得到合成氣。進一步地,所述加熱管的溫度為700-900℃。進一步地,所述熱解的時間為1-2h。進一步地,所述熱解單元的壓力為0.05-0.3MPa。進一步地,所述煤的尺寸為5-50mm。本發(fā)明提供的合成氣的制備系統(tǒng)及方法,不僅工藝簡單、成本低廉,而且能制得濃度較高的合成氣。附圖說明圖1為實施例中熱解單元的結(jié)構(gòu)示意圖;圖2為實施例中翅片加熱管橫截面的結(jié)構(gòu)示意圖;圖3為實施例中翅片加熱管的俯視圖;圖4為實施例中制備合成氣的工藝流程圖。圖中:1、煤入口;2、熱解氣出口;3、加熱管;31、管體;32、翅片;4、水蒸氣噴傘;5、出料裝置。具體實施方式以下結(jié)合附圖和實施例,對本發(fā)明的具體實施方式進行更加詳細的說明,以便能夠更好地理解本發(fā)明的方案及其各個方面的優(yōu)點。然而,以下描述的具體實施方式和實施例僅是說明的目的,而不是對本發(fā)明的限制。下述實施例中所取工藝條件數(shù)值均為示例性的,其可取數(shù)值范圍如前述
發(fā)明內(nèi)容中所示。下述實施例所用的檢測方法均為本行業(yè)常規(guī)的檢測方法。實施例1本實施例提供的合成氣的制備系統(tǒng),包括熱解單元和氣體處理單元。如圖1所示,熱解單元設(shè)有煤入口1和熱解氣出口2;熱解氣出口2位于熱解單元的頂部,熱解氣出口2的兩側(cè)設(shè)有水蒸氣噴傘3;熱解單元的熱源為加熱管,加熱管為催化劑載體;氣體處理單元設(shè)有熱解氣入口和合成氣出口,熱解氣入口和熱解單元的熱解氣出口2相連。本實施例中,熱解單元為無熱載體旋轉(zhuǎn)床,加熱管為輻射管,輻射管布置在無熱載體旋轉(zhuǎn)床中料層的上方。本實施例將加熱管3作為催化劑的載體,而不是在熱解單元中另外設(shè)置催化劑載體。這樣一方面可以使催化劑的溫度快速達到起活溫度,另一方面可以減少熱解單元中裝置的數(shù)量。加熱管3的形狀并不需要特別限定,本實施例采用翅片加熱管作為熱源,翅片加熱管的具體形狀請見圖2和圖3。翅片加熱管的表面積大,采用翅片加熱管作為熱源,既能夠增加催化劑與熱解氣的接觸面積,使得反應(yīng)進行得更充分;又可以增加加熱管的熱輻射面積,增強傳熱,有利于提升熱效率。水蒸氣噴傘3開口的方向并不需要特別限定。本實施例中,水蒸氣噴傘3的開口面向熱解氣出口2,水蒸氣噴傘3向熱解單元內(nèi)噴灑水蒸氣,水蒸氣能更好的和天然氣反應(yīng)。實施例2參見圖4,本實施例提供一種利用實施例1提供的系統(tǒng)制備合成氣的方法,其特征在于,所述方法包括以下步驟:將甲烷分解催化劑涂覆于加熱管表面,并將煤送入所述熱解單元進行熱解,制得熱解氣;將所述熱解氣送入所述氣體處理單元進行凈化、除塵和分離,得到合成氣。在甲烷分解催化劑的作用下,煤熱解后生成的CH4和水蒸氣噴傘3噴出的水蒸汽反應(yīng)生成合成氣的反應(yīng)方程式如下:CH4+H2O=CO+3H2ΔH=205.8KJ/mol上述方程式中的ΔH為反應(yīng)熱。本實施例采用的煤的具體參數(shù)請見表1。CH4和H2O生成合成氣的反應(yīng)為吸熱反應(yīng),煤熱解也是吸熱反應(yīng)。發(fā)明人通過大量的實驗發(fā)現(xiàn),加熱管的溫度為700-900℃時,煤熱解的效果較好,制得的合成氣的濃度較高。本實施例中,加熱管表面的溫度為800℃。上述方法中,熱解的時間為1-2h。熱解的時間太短,煤熱解不充分,制得的合成氣少;熱解時間太長,浪費能源。發(fā)明人通過大量的實驗發(fā)現(xiàn),熱解的時間為1-2h時,制得的合成氣多。本實施例中,熱解的時間為1h。上述方法中,熱解單元的壓力為0.05-0.3MPa。CH4和H2O生成合成氣,熱解單元內(nèi)氣體的體積會增加,若壓力過高,CH4和H2O的轉(zhuǎn)化率低,反應(yīng)生成的合成氣少。發(fā)明人通過大量的實驗發(fā)現(xiàn),熱解單元的壓力為0.05-0.3MPa比較合適。本實施例中,熱解單元的壓力為0.1MPa。上述方法中,煤的顆粒尺寸為5-50mm。顆粒尺寸越小,煤的比表面積越大,越容易熱解,但太小則難加工。發(fā)明人通過大量的實驗發(fā)現(xiàn),煤的顆粒尺寸為5-50mm比較合適。本實施例中,所用的煤的最大顆粒尺寸為50mm。本實施例制得的熱解氣中,合成氣的體積含量為87%,CH4的含量為8%。表1煤的主要性質(zhì)項目單位數(shù)值備注全水wt%11.9收到基固定碳wt%50.3干基揮發(fā)分wt%33.1干基灰分wt%16.6干基從上述實施例可見,采用本發(fā)明提供的技術(shù)方案,制得的熱解氣中合成氣的含量很高。綜上,可以得出,本發(fā)明提供的合成氣的制備系統(tǒng)及方法,不僅工藝簡單、成本低廉,而且能制得濃度較高的合成氣。需要說明的是,以上參照附圖所描述的各個實施例僅用以說明本發(fā)明而非限制本發(fā)明的范圍,本領(lǐng)域的普通技術(shù)人員應(yīng)當(dāng)理解,在不脫離本發(fā)明的精神和范圍的前提下對本發(fā)明進行的修改或者等同替換,均應(yīng)涵蓋在本發(fā)明的范圍之內(nèi)。此外,除非特別說明,那么任何實施例的全部或一部分可結(jié)合任何其它實施例的全部或一部分來使用。當(dāng)前第1頁1 2 3