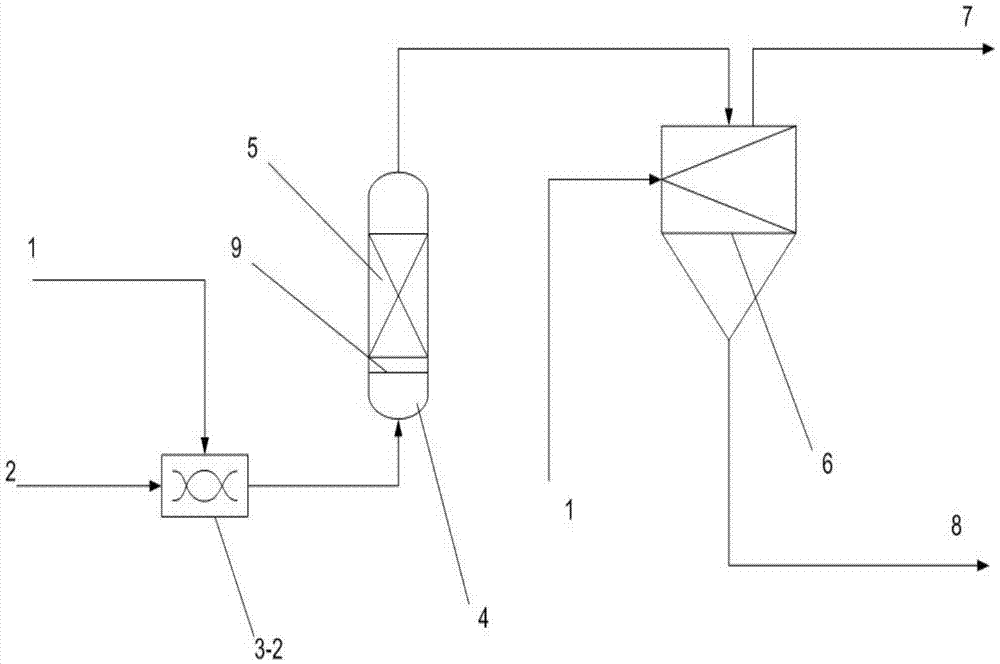
本發(fā)明屬于煉油化工領(lǐng)域,涉及一種含硫醇鹽堿液的預(yù)氧化再生方法。
背景技術(shù):
:由于原油不同程度地含有硫化物,在原油煉制過程中,輕重不同的形態(tài)硫會根據(jù)沸點差異進(jìn)入到相應(yīng)的產(chǎn)品中,液化氣產(chǎn)品根據(jù)其餾程特點,進(jìn)入其中的硫形態(tài)主要為硫化氫、甲硫醇和乙硫醇。目前,液化氣脫硫醇工藝主要是采用堿洗,在一定溫度、壓力和充分接觸條件下,液化氣所含硫醇與氫氧化鈉溶液反應(yīng)生成硫醇鈉,變成無機硫進(jìn)入到堿液中,從而實現(xiàn)液化氣脫硫醇目的。含硫醇鈉的堿液在富氧條件下,通過催化劑可實現(xiàn)在低溫狀態(tài)下的氧化再生,再生后堿液中無機硫?qū)⑥D(zhuǎn)化為有機硫,主要以二甲二硫、二乙基二硫、甲基乙基二硫為主(統(tǒng)稱二硫化物)。所有生成的有機硫密度與堿液相近,常規(guī)的沉降分離方法難以實現(xiàn)油堿有效分離,導(dǎo)致再生后的堿液中夾帶大量的二硫化物,這些二硫化物被再生堿帶到液化氣抽提系統(tǒng),被反抽提到液化氣中,導(dǎo)致液化氣脫后硫含量高,影響以液化氣為原料的下游產(chǎn)品硫含量。中國專利cn85103113對含有硫醇鹽的堿液再生工藝進(jìn)行改進(jìn),利用堿液再生后所生成的二硫化物油相特點,采用有機溶劑進(jìn)行萃取分離,該方法改善了沉降法分離二硫化物的時間長、效果差的弊端,但是該方法存在氧化性氣體與溶劑直接導(dǎo)致的安全風(fēng)險。另外,溶劑本身因為易出現(xiàn)堿夾帶,溶劑的后續(xù)處理流程長,操作成本高。中國專利cn200910100785給出一種堿液氧化再生的方法,該方法在完成堿液硫醇鈉初步在生后,采用二硫化物吹脫塔完成二硫化物與堿液的分離,但是由于受限于吹脫塔的操作工藝所限,吹脫后的堿液二硫化物濃度只能控制到200ppm,當(dāng)該再生堿液進(jìn)入抽提塔與液化氣接觸,會導(dǎo)致堿液中的二流化物被反抽提到液化氣中,無法滿足作為生產(chǎn)超低硫mtbe產(chǎn)品原料的液化氣脫硫要求。中國專利cn201310655920給出一種含硫醇鹽堿液的氧化再生方法,該方法針對堿洗精制(c3~c6)液態(tài)烴脫硫醇后的堿液,利用超重力反應(yīng)器一次完成含硫醇鹽堿液的氧化再生,根據(jù)工業(yè)實施效果,在堿液中硫醇鈉含量較低(小于0.5wt%)時,最高可以實現(xiàn)堿液中硫醇鈉的轉(zhuǎn)化率達(dá)到90%。但在硫醇鈉含量較高(大于或等于0.5wt%)時,工業(yè)運行數(shù)據(jù)顯示,隨著堿液中硫醇鈉含量的增加,含硫醇鈉堿液在超重力反應(yīng)器內(nèi)一次反應(yīng)通過的硫醇鈉轉(zhuǎn)化率呈下降趨勢,使得再生后堿液中殘留的硫醇鈉過高,影響了堿液去抽提裝置的循環(huán)利用,導(dǎo)致精制后(c3~c6)液態(tài)烴硫醇硫含量偏高,以此為原料生產(chǎn)的mtbe含量無法滿足低硫含量要求。在國ⅴ汽油超低硫的背景下,要求控制汽油池組分油硫平均含量不高于10ppm,催化汽油深度加氫汽油導(dǎo)致辛烷值有較大損失,需高辛烷值mtbe組分來調(diào)合平衡汽油產(chǎn)品辛烷值,因此,在平衡辛烷值和總硫不得高于10ppm的要求下,在國內(nèi)許多煉廠汽油池組分中,具有高辛烷值特點的mtbe成為關(guān)鍵的少數(shù)。技術(shù)實現(xiàn)要素:本發(fā)明的目的是提供一種含硫醇鹽堿液的預(yù)氧化再生方法。該方法首先在氧化塔完成含硫醇鈉堿液的初步再生,然后利用超重力反應(yīng)器內(nèi)氣液高接觸效率,迅速地將再生后堿液中的二硫化物轉(zhuǎn)移到氣相中,實現(xiàn)堿液的深度氧化再生。為達(dá)到上述目的,本發(fā)明提供一種含硫醇鹽堿液的預(yù)氧化再生方法,包括以下步驟:s1:預(yù)混入磺化鈦菁酤類催化劑的含硫醇鹽堿液與非凈化風(fēng)在第一反應(yīng)器內(nèi)混合形成氣液混合介質(zhì),然后從氧化塔底部進(jìn)入其中,在堿液中所含磺化鈦菁酤類催化劑作用下進(jìn)行反應(yīng),硫醇鹽與氧氣反應(yīng)生成二硫化物和再生堿液;s2:由s1得到的二硫化物和再生堿液從氧化塔頂抽出后進(jìn)入超重力反應(yīng)器,與同時進(jìn)入超重力反應(yīng)器的非凈化風(fēng)接觸,利用非凈化風(fēng)將堿液中的二硫化物攜帶出超重力反應(yīng)器形成含硫尾氣,得到脫硫后的再生堿液。本發(fā)明所述的含硫醇鹽堿液的預(yù)氧化再生方法,其中,所述氧化塔優(yōu)選為立式罐,操作條件優(yōu)選為:氣液比1~5、壓力0.4~0.8mpa、溫度30~60℃。本發(fā)明所述的含硫醇鹽堿液的預(yù)氧化再生方法,其中,所述氧化塔操作條件優(yōu)選為:溫度40~50℃。本發(fā)明所述的含硫醇鹽堿液的預(yù)氧化再生方法,其中,優(yōu)選的是,所述氧化塔的罐底設(shè)有氣體分布板,氣體分布板上方為填料段,填料段填充有規(guī)整填料或散堆填料,填料段總高度為2~8米,進(jìn)入氧化塔的氣液混合介質(zhì)首先經(jīng)過氣體分布板分配后再進(jìn)入填料段。本發(fā)明所述的含硫醇鹽堿液的預(yù)氧化再生方法,其中,所述氣體分布板的開孔率優(yōu)選為5%~40%。本發(fā)明所述的含硫醇鹽堿液的預(yù)氧化再生方法,其中,所述第一反應(yīng)器優(yōu)選為文丘里管或靜態(tài)混合器。本發(fā)明所述的含硫醇鹽堿液的預(yù)氧化再生方法,其中,所述超重力反應(yīng)器最好是氣液逆流、并流或折流形式操作的;超重力反應(yīng)器操作條件優(yōu)選為:氣液體積比20~2000:1,壓力0.101~0.3mpa,溫度30~60℃;更優(yōu)選為:氣液體積比50~1000:1,壓力0.11~0.15mpa,溫度40~50℃。本發(fā)明所述的含硫醇鹽堿液的預(yù)氧化再生方法,其中,所述非凈化風(fēng)優(yōu)選為空氣、氧氣體積含量高于1%的含氧氣體或非酸性氣體。本發(fā)明所述的含硫醇鹽堿液的預(yù)氧化再生方法,其中,所述含硫醇鹽堿液的氫氧化鈉含量優(yōu)選為8~25wt%。本發(fā)明所述的含硫醇鹽堿液的預(yù)氧化再生方法,其中,所述磺化鈦菁酤類催化劑最好選自由磺化酞菁鈷、聚磺化酞菁鈷和酞菁鈷所組成群組中的至少一種,所述磺化鈦菁酤類催化劑加入量優(yōu)選為1~300mg/kg;更優(yōu)選為50~150mg/kg。本發(fā)明具有以下效果:針對含有硫醇鹽堿液,在氧化塔完成初步的堿液再生后,利用超重力場條件下氣液傳遞效率遠(yuǎn)高于常規(guī)重力場的特點,堿液與非凈化風(fēng)充分接觸,實現(xiàn)二硫化物與堿液有效分離,再生后堿液二硫化物含量低于20ppm,硫醇鈉含量低于0.1%wt。附圖說明圖1是本發(fā)明含硫醇鹽堿液的預(yù)氧化再生方法實施例1的裝置圖;圖2是本發(fā)明含硫醇鹽堿液的預(yù)氧化再生方法實施例4的裝置圖。其中,1、非凈化風(fēng),2、含硫醇鹽堿液,3-1、文丘里管,3-2、靜態(tài)混合器,4、氧化塔,5、填料段,6、超重力反應(yīng)器,7、含硫尾氣,8、再生堿液,9、氣體分布板。具體實施方式實施例1參見圖1所示,預(yù)先加入磺化鈦菁酤(含量為50mg/kg)的硫醇鈉含量3.5wt%的8wt%堿液2與非凈化風(fēng)1(空氣)在文丘里管3-1內(nèi)混合形成氣液混合介質(zhì),然后從氧化塔4底部進(jìn)入其中。氧化塔4為立式罐,操作條件為:氣液體積比比1、0.4mpa(表壓)、溫度40℃。氧化塔4的罐底設(shè)有氣體分布板9,氣體分布板的開孔率為5%,氣體分布板9上方為填料段5,填料段5填充有規(guī)整填料,填料段5總高度為8米,進(jìn)入氧化塔4的氣液混合介質(zhì)首先經(jīng)過氣體分布板9分配后再進(jìn)入填料段5。在堿液中磺化鈦菁酤的催化作用下進(jìn)行反應(yīng),硫醇鹽與氧氣反應(yīng)生成二硫化物和再生堿液。二硫化物和再生堿液從氧化塔4的頂部抽出后進(jìn)入從液相入口進(jìn)入超重力反應(yīng)器6,與同時從氣相入口進(jìn)入超重力反應(yīng)器6的非凈化風(fēng)接觸,超重力反應(yīng)器為氣液逆流形式,操作范圍為:氣液體積比500:1,壓力0.101mpa,溫度40℃利用非凈化風(fēng)將堿液中的二硫化物由氣相出口攜帶出超重力反應(yīng)器6形成含硫尾氣7,得到脫硫后的再生堿液8從超重力反應(yīng)器6的液相出口排出。脫硫后的再生堿液的二硫化物含量小于20ppm,硫醇鈉含量0.03wt%。實施例2參見圖1所示,與實施例1相比,對部分工藝條件和操作參數(shù)調(diào)整,具體如下:堿液中磺化酞菁鈷含量:150mg/kg;堿液濃度:16wt%;超重機:氣液體積比20:1,壓力0.3mpa,溫度60℃;氧化塔操作條件為:氣液體積比3、0.6mpa(表壓)、溫度60℃。在其它條件不變的情況下,實施效果如表1所示:表1再生前硫醇鈉含量再生后硫醇鈉含量再生后二硫化物含量wt%wt%mg/kg3.51.00.04512實施例3參見圖1所示,與實施例1相比,對部分工藝條件和操作參數(shù)調(diào)整,具體如下:堿液中磺化酞菁鈷含量:300mg/kg;堿液濃度:25wt%;超重機:氣液體積比2000:1,壓力0.15mpa,溫度50℃;氧化塔操作條件為:氣液體積比5、0.8mpa(表壓)、溫度50℃。在其它條件不變的情況下,實施效果如表2所示:表2再生前硫醇鈉含量再生后硫醇鈉含量再生后二硫化物含量wt%wt%mg/kg5.20.0615實施例4參見圖2所示,與實施例1不同之處在于,預(yù)混磺化鈦菁酤的含硫醇鹽堿液2與非凈化風(fēng)1(空氣)在靜態(tài)混合器3-2內(nèi)混合形成氣液混合介質(zhì),并在堿液中磺化鈦菁酤催化劑作用下硫醇鈉部分反應(yīng)轉(zhuǎn)化為二硫化物,然后從氧化塔底部進(jìn)入其中,硫醇鹽與氧氣進(jìn)一步反應(yīng)生成二硫化物和再生堿液;二硫化物和再生堿液從氧化塔頂抽出后進(jìn)入從液相入口進(jìn)入超重力反應(yīng)器,與同時從氣相入口進(jìn)入超重力反應(yīng)器的非凈化風(fēng)接觸,利用非凈化風(fēng)將堿液中的二硫化物由氣相出口攜帶出超重力反應(yīng)器形成含硫尾氣,得到脫硫后的再生堿液從超重力反應(yīng)器的液相出口排出。氧化塔4為立式罐,設(shè)有氣體分布板9,氣體分布板的開孔率為20%,氣體分布板9上方為填料段5,填料段5填充有規(guī)整填料,填料段5總高度為4 米,進(jìn)入氧化塔4的氣液混合介質(zhì)首先經(jīng)過氣體分布板9分配后再進(jìn)入填料段5。操作參數(shù)如下:堿液中磺化酞菁鈷含量:50mg/kg;堿液濃度:8wt%;超重機:氣液體積比100:1,壓力0.11mpa,溫度30℃;氧化塔操作條件為:氣液體積比5、0.4mpa(表壓)、溫度30℃。實施效果如表3所示:表3再生前硫醇鈉含量再生后硫醇鈉含量再生后二硫化物含量wt%wt%mg/kg1.60.041513實施例5參見圖2所示,與實施例4相比,對工藝條件和操作參數(shù)調(diào)整,具體如下:堿液中磺化酞菁鈷含量:150mg/kg;堿液濃度:16wt%;超重機:氣液體積比600:1,壓力0.3mpa,溫度40℃;氧化塔操作條件為:氣液體積比5、0.8mpa(表壓)、溫度40℃。其它條件不變,實施效果如表4所示:表4再生前硫醇鈉含量再生后硫醇鈉含量再生后二硫化物含量wt%wt%mg/kg42.20.0312實施例6參見圖2所示,與實施例4相比,對工藝條件和操作參數(shù)調(diào)整,具體如下:堿液中磺化酞菁鈷含量:300mg/kg;堿液濃度:25wt%;超重機:氣液體積比2000:1,壓力0.15mpa,溫度50℃;氧化塔操作條件為:氣液體積比3、0.6mpa(表壓)、溫度50℃。其它條件不變,實施效果如表5所示:表5再生前硫醇鈉含量再生后硫醇鈉含量再生后二硫化物含量wt%wt%mg/kg4.30.0518當(dāng)然,本發(fā)明還可有其它多種實施例,在不背離本發(fā)明精神及其實質(zhì)的情況下,熟悉本領(lǐng)域的技術(shù)人員可根據(jù)本發(fā)明作出各種相應(yīng)的改變和變形,但這些相應(yīng)的改變和變形都應(yīng)屬于本發(fā)明的保護(hù)范圍。當(dāng)前第1頁12