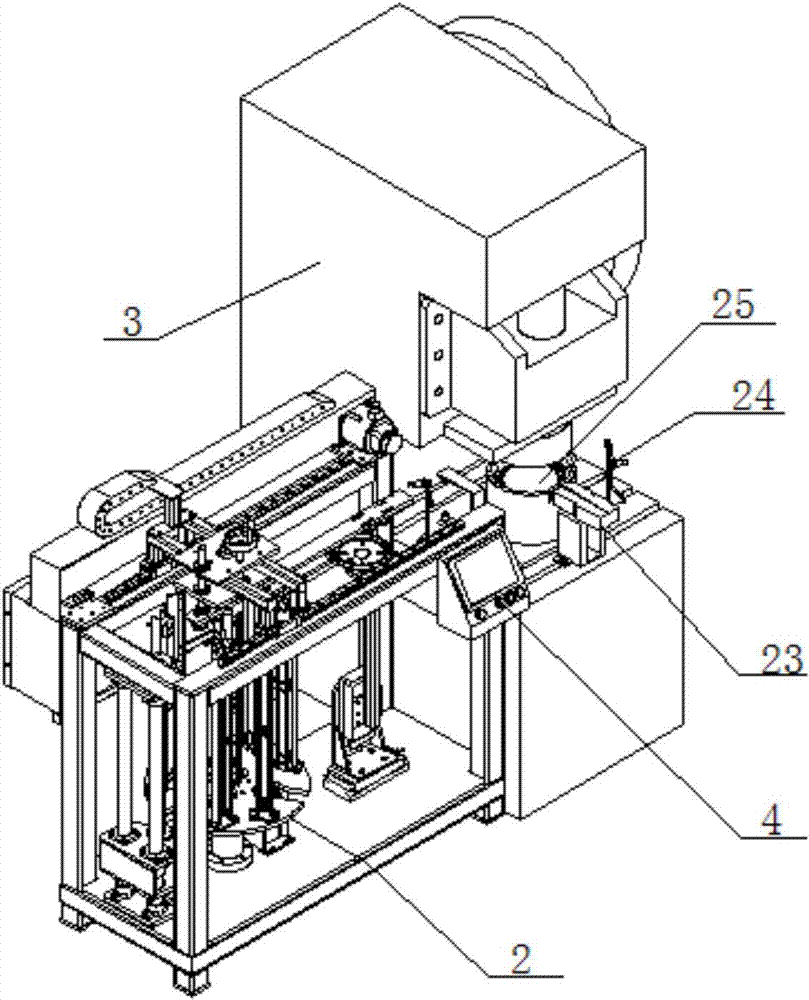
本發(fā)明涉及一種沖壓機坯件供給裝置,特別是一種沖壓機連續(xù)自動送料裝置。
背景技術(shù):沖床就是一臺沖壓式壓力機。在國民生產(chǎn)中的用途越來越廣泛。對于將常規(guī)的彼此獨立的坯件沖制成具有特定形狀的工件而言,一般通過工人或者機械手一個個的將工件放入沖床中進行,但是對于大批量的工件加工而言,通過工人或者機械手把工件放入沖床中,效率會很低,由此設計一種自動化送料機構(gòu)尤為重要。首先,要實現(xiàn)自動化送料,最重要的問題就是怎么能夠讓原料每次都能很精準的放到加工位置,即把坯件放入到模具中,放置好以后坯件不能放偏,傾斜或者其他情況,由于坯件與模具配合比較緊密,如果坯件放置不準,會把模具沖壞,所以怎樣能實現(xiàn)精準上料,是自動化送料最重要的問題;其次,怎么保證每次取料的時候只取一片而不是兩片,因為坯件是一個個的疊放在一起,每個坯件上面有油或者清洗液之類的東西,所以不能保證每次取料的時候都剛好取一片,如果兩片坯件放入到?jīng)_床里面也會把模具給沖壞。由此設計出一種沖壓機連續(xù)自動送料裝置,此裝置通過取料機械臂、檢測盤和沖壓機上的光電檢測器,對待沖壓的坯件進行準確的地位,保證讓坯件每次都能很精準的放置到加工位置;除此之外,檢測盤上設置重力傳感器,檢測取料吸盤每次吸取的坯件個數(shù),當吸取的坯件個數(shù)大于1時,通過報警或者特殊工序把坯件分離,保證每次放到壓力機模具上的坯件都只有一片,避免模具被損壞。
技術(shù)實現(xiàn)要素:本發(fā)明為解決現(xiàn)有技術(shù)中人工送料費力費時,效率低等問題,提供一種沖壓機連續(xù)自動送料裝置,此裝置可實現(xiàn)自動輸送上料,同時能滿足不同規(guī)格板料的上料。本發(fā)明通過以下技術(shù)方案來實現(xiàn)上述目的:包括機架、上料機構(gòu)、提升機構(gòu)、取料機構(gòu)及沖壓機,其特征在于:還包括檢測盤、坯件檢測定位機構(gòu)、控制面板。所述上料機構(gòu)、取料機構(gòu)、檢測盤、控制面板均安裝在機架上,檢測盤位于取料機構(gòu)取料位置與沖壓機沖壓位置之間的中點處,坯件檢測定位機構(gòu)安裝在沖壓機上,機架連接沖壓機,上料機構(gòu)上的坯件通過提升機構(gòu)提升至取料位置,然后經(jīng)取料機構(gòu)運送到?jīng)_壓機上。所述上料機構(gòu)從下往上依次設置有交流電機、槽輪、轉(zhuǎn)盤和擋柱,交流電機固定在機架上,交流電機帶動槽輪轉(zhuǎn)動,槽輪與轉(zhuǎn)盤互相固定,擋柱垂直的固定在轉(zhuǎn)盤上。所述提升機構(gòu)包括第一導向桿、托板和絲桿,第一導向桿固定在機架上,托板安裝在第一導向桿上,絲桿穿過托板的螺紋孔帶動托板上下運動。所述取料機構(gòu)包括取料臂、取料吸盤和放料吸盤,取料臂兩端分別安裝取料吸盤和放料吸盤,取料吸盤和放料吸盤之間的距離為上料機構(gòu)的取料位置與沖壓機的沖壓位置之間距離的一半;此外,取料臂還設置有調(diào)節(jié)機構(gòu)。所述調(diào)節(jié)機構(gòu)上面設置有調(diào)節(jié)輪、取料氣缸、連接板、第二導向桿,調(diào)節(jié)輪安裝在調(diào)節(jié)機構(gòu)支架上,取料氣缸和第二導向桿均固定在連接板上,第二導向桿穿過調(diào)節(jié)機構(gòu)支架上的導向孔,連接板底部安裝有滑塊,水平電機通過驅(qū)動滑塊進而驅(qū)動取料臂的運動;通過轉(zhuǎn)動調(diào)節(jié)輪可以調(diào)節(jié)取料臂整體距離地面的高度,取料氣缸驅(qū)動取料臂整體的上下運動,第二導向桿起導向作用。所述檢測盤底部連接支架,支架下端與上下調(diào)節(jié)氣缸固定,左右調(diào)節(jié)氣缸固定在機架上,上下調(diào)節(jié)氣缸底部安裝有滑塊,左右調(diào)節(jié)氣缸通過驅(qū)動滑塊進而驅(qū)動上下調(diào)節(jié)氣缸和支架整體運動,上下調(diào)節(jié)氣缸用來調(diào)節(jié)檢測盤的上下高度。所述坯件檢測定位機構(gòu)包括推料氣缸、光電檢測器和模具均固定在沖壓機上,推料氣缸安裝在模具的推料口處,模具在直徑方向上開有一個通槽,在坯件準確放入模具時,光電檢測器發(fā)射端發(fā)射出的光線剛好被接收端接收到。進一步,所述擋柱頂端安裝有磁性分離器和光電檢測裝置。進一步,所述擋柱上設有擋板和調(diào)節(jié)螺母,擋板與擋柱之間為活動連接。進一步,所述轉(zhuǎn)盤上的三個擋柱作為一組,每組在半徑方向上關(guān)于轉(zhuǎn)盤圓心呈120度對稱。進一步,所述托板的工作端為半圓形,半圓形剛好與槽輪的圓弧部分相吻合。進一步,所述轉(zhuǎn)盤在半徑方向上關(guān)于轉(zhuǎn)盤圓心呈120度對稱開有三個開口,該開口可使托板順利通過轉(zhuǎn)盤。進一步,所述托板運動行程的最上端與最下端位置設置限位開關(guān)。進一步,所述檢測盤上安裝有電磁吸力器和壓力傳感器。進一步,所述檢測盤上安裝有吸盤和壓力傳感器。本發(fā)明相比較現(xiàn)有技術(shù)具有以下優(yōu)點:1.取料機構(gòu)包括取料臂上設置有調(diào)節(jié)機構(gòu),通過調(diào)節(jié)機構(gòu)上面的調(diào)節(jié)輪,可以調(diào)節(jié)取料臂距地面的距離,即改變?nèi)×媳劬嗳×宵c的距離,以適應不同規(guī)格的坯件。2.上料機構(gòu)的擋柱頂端安裝磁性分離器和光電檢測裝置,磁性分離器利用磁極原理使相鄰的兩個坯件分離開來,保證每次吸盤每次只能吸取一片坯件,光電檢測裝置檢測料堆最上面那個坯件是否到達抓取位置,配合吸盤每次順利吸取坯件。3.上料機構(gòu)的擋柱上設有擋板和調(diào)節(jié)螺母,通過調(diào)節(jié)螺母可以調(diào)節(jié)擋板與擋柱之間的距離,這樣可以適應不同規(guī)格的坯件進行上料。4.沖壓機上設置光電檢測器,用來檢測坯件是否精確放入模具中,避免了因坯件沒有放置準確而沖壞模具,也確保了沖壓時的安全性。5.整個上料、取料過程采用自動化進行,中間無人工干預,相比較傳統(tǒng)上料機構(gòu),大大減少了停工等待時間和操作誤差,提高了上料效率。附圖說明圖1是本發(fā)明的坯件示意圖;圖2是本發(fā)明整體機構(gòu)示意圖;圖3是本發(fā)明上料機構(gòu)示意圖;圖4是本發(fā)明上料機構(gòu)部分機構(gòu)示意圖;圖5是本發(fā)明取料臂上的調(diào)節(jié)機構(gòu)示意圖;圖6是本發(fā)明取料機構(gòu)示意圖。具體實施方式下面結(jié)合附圖對本發(fā)明作進一步說明:如附圖1-6所示,本發(fā)明中所提及的坯件1,是指兩面為平面的的圓形金屬片。一種沖壓機連續(xù)自動送料裝置,包括機架2、上料機構(gòu)、提升機構(gòu)、取料機構(gòu)、檢測盤11、坯件檢測定位機構(gòu)、控制面板4及沖壓機3。上料機構(gòu)、取料機構(gòu)、檢測盤11、控制面板4均安裝在機架2上,檢測盤11位于取料機構(gòu)取料位置與沖壓機3沖壓位置之間的中點處,坯件檢測定位機構(gòu)安裝在沖壓機3上,機架2連接沖壓機3,坯件通過送料機構(gòu)送到取料位置,然后取料機構(gòu)吸取坯件,把吸取的坯件先放置到檢測盤11上等待檢測坯件的個數(shù),檢測完之后,取料機構(gòu)把坯件運送至沖壓機上的坯件檢測定位機構(gòu),待坯件檢測定位機構(gòu)對坯件檢測定位之后,沖壓機對坯件進行加工。所述上料機構(gòu)從下往上依次設置有交流電機5、槽輪、轉(zhuǎn)盤6和擋柱9,交流電機5固定在機架2上,交流電機5帶動槽輪轉(zhuǎn)動,槽輪與轉(zhuǎn)盤6互相固定,擋柱9垂直的固定在轉(zhuǎn)盤6上,擋柱9上設有擋板和調(diào)節(jié)螺母,擋板與擋柱9之間為活動連接,通過調(diào)節(jié)螺母可以調(diào)節(jié)擋板與擋柱9之間的距離,擋柱9頂端安裝磁性分離器和光電檢測裝置。所述提升機構(gòu)包括第一導向桿8、托板7和絲桿10,第一導向桿8固定在機架2上,托板7安裝在第一導向桿8上,絲桿10穿過托板7的螺紋孔帶動托板7上下運動。轉(zhuǎn)盤6上的三個擋柱9作為一組,每組在半徑方向上關(guān)于轉(zhuǎn)盤圓心呈120度對稱,這樣當一堆坯件加工完之后,盛放料堆的轉(zhuǎn)盤6旋轉(zhuǎn)一次,另一料堆可以繼續(xù)上料,使上料過程連續(xù)不間斷的進行;擋柱9頂端安裝的磁性分離器利用磁極原理使相鄰的兩個坯件分離開來,保證每次吸盤每次只能吸取一片坯件,另外擋柱9頂端安裝的光電檢測裝置檢測料堆最上面那個坯件是否到達抓取位置,配合吸盤每次順利吸取坯件。此外,轉(zhuǎn)盤6上開有比托板7外輪廓大一點的開口,這樣當轉(zhuǎn)盤6不動的時候,托板7可以順利把料堆向上抬起。托板7運動行程的最上端與最下端位置設置限位開關(guān),當托板7運動到最上端或者最下端的時候控制絲桿10停止運動。所述取料機構(gòu)包括取料臂15、取料吸盤和放料吸盤,取料臂15兩端分別安裝取料吸盤和放料吸盤,取料吸盤和放料吸盤之間的距離為上料機構(gòu)的取料位置與沖壓機3的沖壓位置之間距離的一半,此外,取料臂15還設置有調(diào)節(jié)機構(gòu)。所述調(diào)節(jié)機構(gòu)上面設置有調(diào)節(jié)輪17、取料氣缸18、連接板19、第二導向桿20,調(diào)節(jié)輪17安裝在調(diào)節(jié)機構(gòu)支架上,取料氣缸18和第二導向桿20均固定在連接板19上,第二導向桿20穿過調(diào)節(jié)機構(gòu)支架上的導向孔,連接板19底部安裝有滑塊21,水平電機16通過驅(qū)動滑塊21進而驅(qū)動取料臂15的運動;通過轉(zhuǎn)動調(diào)節(jié)輪17可以調(diào)節(jié)取料臂15整體距離地面的高度,取料氣缸18驅(qū)動取料臂15整體的上下運動,第二導向桿20起導向作用。所述檢測盤11底部連接支架12,支架12下端與上下調(diào)節(jié)氣缸13固定,左右調(diào)節(jié)氣缸14固定在機架2上,上下調(diào)節(jié)氣缸13底部安裝有滑塊,左右調(diào)節(jié)氣缸14通過驅(qū)動滑塊進而驅(qū)動上下調(diào)節(jié)氣缸13和支架12整體運動,上下調(diào)節(jié)氣缸13用來調(diào)節(jié)檢測盤11的上下高度;此外,檢測盤11上安裝有電磁吸力器和壓力傳感器,當壓力傳感器檢測到取料臂15的取料吸盤一次取到的坯件為兩塊,可通過電磁吸力器與放料吸盤把兩塊坯件分開。所述坯件檢測定位機構(gòu)包括推料氣缸23、光電檢測器24和模具25均固定在沖壓機3上,推料氣缸23安裝在模具25的推料口處,當坯件加工完之后,推料氣缸23把加工完的坯件推出模具25,模具25在直徑方向上開有一個通槽,在坯件準確放入模具25時,光電檢測器24發(fā)射端發(fā)射出的光線剛好被接收端接收到,這樣可以用來檢測坯件是否精確放入模具25中,避免了因坯件沒有放置準確而沖壞模具25。本發(fā)明的工作過程和原理如下:每次開工之前,操作人員把轉(zhuǎn)盤6上的三個料堆都放滿,放滿之后按下控制面板4上的啟動按鈕,絲桿10帶動托板7向上運動,托板7推動料堆向上運動,當料堆運動至取料位置時,取料臂15通過取料氣缸18帶動向下運動,取料吸盤吸附住坯件,取料臂15快速上升,取料臂15在水平電機16的帶動下把吸附住的坯件運送到檢測盤11正上方,取料臂15向下運動,取料吸盤松開坯件,坯件放置在檢測盤11上。之后取料氣缸18回縮,取料臂15返回去再次取料,在取料臂15返回的這一過程中,檢測盤11對其上面的坯件進行檢測,如果檢測到吸附過來的坯件為一片,那么當取料臂15運動到取料位置取料的同時,放料吸盤吸附住坯件,然后取料臂15上的取料吸盤再次把坯件運送到檢測盤11正上方的時候,放料吸盤同時把坯件運送到?jīng)_壓機3的模具25的正上方,取料臂15向下運動,取料吸盤和放料吸盤同時把坯件放下,此時檢測盤重復之前過程,沖壓機3上的光電檢測器24對放置在模具25上的坯件位置進行檢測,如果坯件的位置放置精確,那么當取料臂15返程運動的時候,放料吸盤移開模具25,沖壓機3對坯件進行沖壓,之后重復這一過程。當料堆上的坯件全部被取料吸盤取走之后,絲桿10快速反向運動把托板7帶動至最底端,此時托板7在轉(zhuǎn)盤6的下面,交流電機5帶動轉(zhuǎn)盤6轉(zhuǎn)動120度,此時新的一個料堆轉(zhuǎn)動到托板7的正上方,絲桿10再次帶動托板7向上運動,托板7帶動料堆向上運動直至料堆上的坯件全部被吸盤取走,重復上面過程,這里空出來的料堆再由操作人員把坯件放滿,這樣在不停機的情況下,就可實現(xiàn)連續(xù)上料。此外,如果在檢測盤11上檢測到的坯件為兩片,或者兩片以上及其他特殊情況時,那么檢測盤11上的電磁吸力器、取料氣缸18的工作過程通過以下容錯控制方法進行工作:假設A、B分別表示檢測盤11上的電磁吸力器、取料氣缸18工作狀態(tài),那么不工作狀態(tài)表示為D表示水平電機16正常運動狀態(tài),半程運動狀態(tài)表示為這里的正常運動為水平電機驅(qū)動取料機械臂15從始端運動到末端的運動狀態(tài),半程運動為第三驅(qū)動電機驅(qū)動取料機械臂15運動了從始端到末端一半距離的運動狀態(tài)。(1)為系統(tǒng)正常工作狀態(tài),表示檢測盤11上只有一塊坯件。(2)為系統(tǒng)重放工作狀態(tài),表示檢測盤11上有兩塊坯件或者三塊坯件。(3)為系統(tǒng)重放工作狀態(tài),表示坯件在檢測盤11中沒放平、坯件在模具25中沒放平。(4)為系統(tǒng)返回重新定位工作狀態(tài),表示坯件在模具25中重新放置仍然放不平。此外,系統(tǒng)還有報警工作狀態(tài),表示坯件在檢測盤11或模具25中放置不平、放料吸盤無法吸取坯件。上述實施例只是本發(fā)明的較佳實施例,并不是對本發(fā)明技術(shù)方案的限制,只要是不經(jīng)過創(chuàng)造性勞動即可在上述實施例的基礎(chǔ)上實現(xiàn)的技術(shù)方案,均應視為落入本發(fā)明專利的權(quán)利保護范圍內(nèi)。