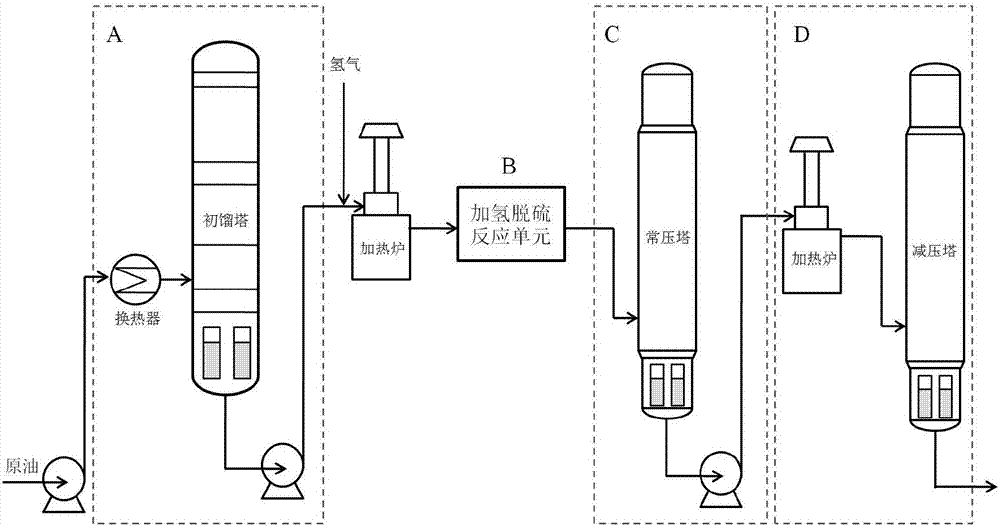
本發(fā)明涉及一種原油預處理的方法,更具體的,是一種含硫/高硫原油加氫脫硫預處理的方法,屬于石油加工和石油化工
技術(shù)領(lǐng)域:
。
背景技術(shù):
:隨著常規(guī)原油儲量的逐步減少,世界煉油加工業(yè)正面臨著原油資源日益重質(zhì)化與劣質(zhì)化的嚴峻挑戰(zhàn)。世界原油的硫含量在不斷增加,目前硫含量在1%以上的原油占世界原油總產(chǎn)量的55%以上。近年來,隨著國際油價持續(xù)低位震蕩運行,以及國內(nèi)油品市場的不斷發(fā)展變化,進口原油已成為我國石化企業(yè)的主要原料。2015年,我國原油加工量為5.22億噸,原油進口量3.355億噸,同比上漲8.8%,除新增石油儲備和庫存因素外,我國原油對外依存度達到60.6%,進口原油大部分是含硫劣質(zhì)原油。我國原油的進口國主要有俄羅斯、安哥拉、巴西、委內(nèi)瑞拉以及沙特等中東地區(qū),進口原油與我國國產(chǎn)原油有較大差別。進口原油屬于含硫原油或高硫原油,如阿拉伯地區(qū)的原油屬于含硫或高硫原油,而俄羅斯原油和安哥拉原油均屬于含硫原油。目前中石油的煉廠所采用的加工流程對不同的原油有不同適應(yīng)性,待加工原油的性質(zhì)發(fā)生變化時,會對裝置負荷、產(chǎn)品質(zhì)量平衡、氫平衡、硫平衡、產(chǎn)品結(jié)構(gòu)等帶來一系列影響。我國目前近一半的煉油廠是按照加工國內(nèi)低硫原油建廠,并不適合加工進口含硫原油,若以現(xiàn)有流程加工進口原油,由于其硫、氮、金屬和殘?zhí)康入s質(zhì)較高,將導致(1)二次加工裝置產(chǎn)生的含硫酸性氣和酸性水增多,加快設(shè)備腐蝕老化;(2)增加脫硫與硫回收裝置的加工負荷;(3)影響催化劑壽命,縮短裝置生產(chǎn)周期。目前具有加工含硫、高硫原油的能力的煉油企業(yè),通常將原油經(jīng)常減壓后分別進行脫硫處理。常減壓渣油主要通過延遲焦化、減粘裂化、溶劑脫瀝青和渣油加氫處理+催化裂化等技術(shù)進行加工。延遲焦化、減粘裂化和溶劑脫瀝青等屬于脫碳技術(shù),輕油收率低、“黑色”產(chǎn)品多、油品質(zhì)量差;渣油加氫處理技術(shù)一方面需要在高溫、高壓條件下操作,通過在多個反應(yīng)器中級配裝填不同性能的催化劑,達到雜質(zhì)的逐級脫除,裝置投資巨大,另一方面由于渣油中金屬等雜質(zhì)含量高,導致裝置運行周期短,催化劑壽命短,增加企業(yè)生產(chǎn)成本。此外,含硫/高硫原油對常減壓裝置腐蝕嚴重,給煉廠帶來了嚴重的安全隱患,腐蝕過程中生成的fes還存在自燃的危險。為了使我國已建煉油廠適應(yīng)進口原油,需對原廠的設(shè)備和流程進行改造。我國多家企業(yè)在加工含硫/高硫原油時,嘗試了多種辦法,如對現(xiàn)有的裝置材料進行防腐蝕處理,將含硫/高硫原油與低硫原油混煉,“一脫三注”等,然而結(jié)果均不理想。除了給常減壓裝置帶來嚴重的腐蝕,一旦原油中硫含量增加,各個出口餾分的硫含量也隨之增加,導致后續(xù)處理裝置原料中含硫量超過設(shè)計值,帶來一系列設(shè)備、管線的腐蝕問題,給裝置安全生產(chǎn)帶來了重大隱患,并導致產(chǎn)品含硫量增加,無法滿足生產(chǎn)標準。若采用傳統(tǒng)流程,在已建成的適應(yīng)于煉制低硫原油的煉油廠上,需要至少進行以下升級:(1)常減壓部分精餾塔的防腐升級;(2)各餾分油脫硫模塊的處理量升級;(3)各餾分油脫硫前的設(shè)備防腐升級。這樣的改造方式投資成本高、改造周期長,且較高的硫含量給設(shè)備各個環(huán)節(jié)帶來了更高的腐蝕風險,易造成裝置操作不穩(wěn)定。因此,本發(fā)明提出了一種在常減壓精餾塔之前的原油預脫硫工藝,一方面大幅降低了裝置的升級改造成本,另一方面提高了裝置操作的穩(wěn)定性。技術(shù)實現(xiàn)要素:本發(fā)明的目的是為了解決現(xiàn)有技術(shù)無法滿足含硫原油的處理需求的問題,提供一種含硫/高硫原油預加氫脫硫工藝。該工藝只需在已建成設(shè)備間加設(shè)加氫處理單元,即可在原設(shè)備上進行含硫/高硫原油的煉制。本發(fā)明的目的是通過下述技術(shù)方案實現(xiàn)的。一種含硫/高硫原油預加氫脫硫工藝,在初餾塔或者常壓塔前通過加氫脫硫反應(yīng)單元對原油進行脫硫處理。所述加氫脫硫反應(yīng)單元中的反應(yīng)器為一段或多段固定床、漿態(tài)床或沸騰床反應(yīng)器中的一種或多種組合。所述反應(yīng)器的操作溫度為220-400℃,優(yōu)選280-360℃;操作壓力為2-15mpa,優(yōu)選2-8mpa;氫油比為10-3000;液體體積空速為0.1-10h-1,優(yōu)選0.5-5h-1。根據(jù)不同原油的性質(zhì),加氫脫硫處理裝置中還可以引入其他種類原油處理劑,如加氫保護劑、加氫脫金屬劑、脫殘?zhí)縿?、加氫脫氮劑和加氫裂化劑中的一種或多種組合。工作過程方案一:加氫處理單元(b)位于初餾塔(a)之前a.經(jīng)脫鹽脫水處理后的原油與氫氣混合后,經(jīng)加熱爐加熱后達到反應(yīng)溫度(280-360℃),進入加氫處理單元(b),在催化劑的存在下,進行加氫脫硫處理。b.加氫脫硫處理后的產(chǎn)物經(jīng)冷卻分離后獲得富氫氣體,富氫氣體中主要成分為氫氣和硫化氫,分離后的氫氣用于循環(huán)使用,硫化氫進入硫回收單元進行廢氣處理;經(jīng)脫硫處理后的原油經(jīng)冷卻后,先后進入初餾塔(a)、常壓精餾塔(c)和減壓精餾塔(d)進行后續(xù)石油煉制過程。方案二:加氫處理單元(b)位于初餾塔(a)與常壓塔(c)之間a.經(jīng)脫鹽脫水處理后的原油經(jīng)蒸汽換熱后進入初餾塔(a),入口溫度為150-220℃,塔頂獲得初頂油,初頂油組分冷卻后一部分進入儲罐或進入下游工序,另一部分回流至初餾塔;塔中獲得初側(cè)油;塔底獲得拔頂油。b.初餾塔塔底所獲得的拔頂油與氫氣混合,經(jīng)加熱爐加熱后達到反應(yīng)溫度(280-360℃),進入加氫脫硫處理裝置(b),在催化劑的存在下,進行加氫脫硫處理。c.加氫脫硫處理后的產(chǎn)物經(jīng)冷卻分離后獲得富氫氣體,富氫氣體中主要成分為氫氣和硫化氫,分離后的氫氣用于循環(huán)使用,硫化氫進入硫回收單元進行廢氣處理;經(jīng)脫硫處理后的原油無需換熱,直接進入常壓精餾塔(c)和減壓精餾塔(d)進行后續(xù)石油煉制過程。方案一適用于煉制全餾分所含硫含量均較高的原油,或適用于原設(shè)備耐腐蝕能力較差的情況。此方案將加氫脫硫單元設(shè)于初餾塔之前,含硫/高硫原油經(jīng)過第一步脫硫過程后,全餾分的硫含量均有大幅降低,不增加對后續(xù)設(shè)備的腐蝕壓力;但由于從加氫脫硫單元出來的油溫度較高,需增設(shè)冷凝裝置,不利于熱量高效利用,且相對于方案二,需多設(shè)一個加熱爐,投資較高。方案二適用于煉制輕餾分所含硫含量不太高的原油,或適用于廠區(qū)面積有限、投資有限的情況。此方案中將加氫脫硫單元設(shè)于初餾塔之后,原油在流程中無熱量損失,設(shè)備投資較方案一低,但由于含硫/高硫原油直接進入初餾塔,大幅增加了初餾塔的腐蝕壓力,需對其進行耐腐蝕改造或進行頻繁檢修。有益效果1、為我國石油煉制企業(yè)提供煉制含硫/高硫原油的方法,尤其適用于對已建成的石油煉制企業(yè)進行升級改造,在原廠已有設(shè)備上進行改造,節(jié)省投資成本。全餾分的硫含量降低,大幅降低后續(xù)原油處理單元的脫硫壓力,中間產(chǎn)品質(zhì)量無需進行額外處理可直接進入下游深加工單元。2、有效降低原油中的硫含量和其他雜質(zhì)(金屬、氮、殘?zhí)康?含量,使處理后的原油適應(yīng)低硫原油的設(shè)備,降低設(shè)備投資,減弱腐蝕,提高產(chǎn)品質(zhì)量。3、采用多段固定床、漿態(tài)床或沸騰床的一種或幾種組合,相較于傳統(tǒng)加氫脫硫反應(yīng)裝置,有效降低催化床層的溫升,并提高催化劑利用效率。4、所采用的操作參數(shù)較溫和(壓力較低、溫度較低、空速較高),既降低了加氫裝置中的設(shè)備成本(高壓容器設(shè)計壓力降低、催化劑裝填量降低、反應(yīng)器設(shè)計體積降低),也降低了操作成本。同時,相較于重質(zhì)油加氫過程,催化劑使用壽命較長。附圖說明圖1是本發(fā)明中方案一的含硫/高硫原油預脫硫工藝流程圖;圖2是本發(fā)明中方案二的含硫/高硫原油預脫硫工藝流程圖。其中,a為初餾單元,b為加氫脫硫處理單元,c為常壓精餾單元,d為減壓精餾單元。具體實施方式下面的實施例將對本發(fā)明予以進一步的說明,但并不因此限制本發(fā)明。實施例1一種含硫/高硫原油預加氫脫硫工藝,如圖1所示,在初餾塔(a)前通過加氫脫硫反應(yīng)單元(b)對原油進行脫硫處理。加氫脫硫反應(yīng)單元(b)中的反應(yīng)器為三段固定床反應(yīng)器。加氫脫硫反應(yīng)單元(b)中的反應(yīng)器的原油處理劑為加氫保護劑、加氫脫金屬劑和加氫脫硫劑。工作過程如下:經(jīng)脫鹽脫水處理后的原油x與氫氣混合后,經(jīng)加熱爐加熱后達到反應(yīng)溫度320℃,進入加氫處理單元(b),此處(b)為三段固定床反應(yīng)器,依次經(jīng)過加氫保護劑、加氫脫金屬劑和加氫脫硫劑,在催化劑的存在下,進行加氫脫硫處理。加氫脫硫處理后的產(chǎn)物經(jīng)冷卻分離后獲得富氫氣體,富氫氣體中主要成分為氫氣和硫化氫,分離后的氫氣用于循環(huán)使用,硫化氫進入硫回收單元進行廢氣處理;經(jīng)脫硫處理后的原油經(jīng)冷卻后,先后進入初餾塔(a)、常壓精餾塔(c)和減壓精餾塔(d)進行后續(xù)石油煉制過程。催化劑性質(zhì)如表1所示,操作條件如表2所示,脫硫前后的原油性質(zhì)如表3所示。表1催化劑性質(zhì)保護劑脫金屬劑脫硫劑化學組成,質(zhì)量%氧化鎳1.51.73.2氧化鈷//0.8氧化鉬6.28.118.5氧化鎢//2.6其他助劑//1.3物理性質(zhì)比表面積,m2/g190160200孔容,ml/g0.70.720.77外徑,mm1.51.11.1形狀拉西環(huán)圓柱圓柱裝填體積,%102070使用周期,年1.51.52表2操作條件入口溫度300℃氫氣分壓8mpa體積空速0.5h-1氫油比(體積)1000表3脫硫前后原油性質(zhì)脫硫前脫硫后脫除率硫含量,μg/g700035095%氮含量,μg/g150022585%ni,μg/g6.3<0.01>99.9%v,μg/g6.5<0.01>99.9%殘?zhí)亢?%2.390.7270%實施例2一種含硫/高硫原油預加氫脫硫工藝,如圖2示,在初餾塔(a)與常壓塔(c)之間添加加氫脫硫反應(yīng)單元(b)對原油進行脫硫處理。加氫脫硫反應(yīng)單元(b)中的反應(yīng)器為三段固定床反應(yīng)器。加氫脫硫反應(yīng)單元(b)中的反應(yīng)器的原油處理劑為加氫保護劑、加氫脫金屬劑和加氫脫硫劑。經(jīng)脫鹽脫水處理后的原油x經(jīng)蒸汽換熱后進入初餾塔(a),入口溫度為210℃,塔頂獲得初頂油,初頂油組分冷卻后一部分進入儲罐或進入下游工序,另一部分回流至初餾塔;塔中獲得初側(cè)油;塔底獲得拔頂油。初餾塔塔底所獲得的拔頂油與氫氣混合,經(jīng)加熱爐加熱后達到反應(yīng)溫度340℃,進入加氫脫硫處理裝置(b),此處(b)為三段固定床反應(yīng)器,依次經(jīng)過加氫保護劑、加氫脫金屬劑和加氫脫硫劑,在催化劑的存在下,進行加氫脫硫處理。加氫脫硫處理后的產(chǎn)物經(jīng)冷卻分離后獲得富氫氣體,富氫氣體中主要成分為氫氣和硫化氫,分離后的氫氣用于循環(huán)使用,硫化氫進入硫回收單元進行廢氣處理;經(jīng)脫硫處理后的原油無需換熱,直接進入常壓精餾塔(c)和減壓精餾塔(d)進行后續(xù)石油煉制過程。催化劑性質(zhì)如表1所示,操作條件如表4所示,原油脫硫率可達90%以上,脫氮率80%以上,脫金屬率達99.9%以上。表4操作條件入口溫度360℃氫氣分壓2mpa體積空速1h-1氫油比(體積)300實施例3一種含硫/高硫原油預加氫脫硫工藝,如圖1示,在初餾塔(a)之前添加加氫脫硫反應(yīng)單元(b)對原油進行脫硫處理。加氫脫硫反應(yīng)單元(b)中的反應(yīng)器為兩段漿態(tài)床反應(yīng)器。加氫脫硫反應(yīng)單元(b)中的反應(yīng)器的原油處理劑為加氫脫金屬劑和加氫脫硫劑。經(jīng)脫鹽脫水處理后的原油y氫氣混合后,經(jīng)加熱爐加熱后達到反應(yīng)溫度320℃,進入加氫處理單元(b),此處(b)為三段固定床反應(yīng)器,依次經(jīng)過加氫保護劑、加氫脫金屬劑和加氫脫硫劑,在催化劑的存在下,進行加氫脫硫處理。加氫脫硫處理后的產(chǎn)物經(jīng)冷卻分離后獲得富氫氣體,富氫氣體中主要成分為氫氣和硫化氫,分離后的氫氣用于循環(huán)使用,硫化氫進入硫回收單元進行廢氣處理;經(jīng)脫硫處理后的原油經(jīng)冷卻后,先后進入初餾塔(a)、常壓精餾塔(c)和減壓精餾塔(d)進行后續(xù)石油煉制過程。催化劑性質(zhì)如表5所示,操作條件如表6所示,脫硫前后的原油性質(zhì)如表7所示。表5催化劑性質(zhì)表6操作條件入口溫度360℃氫氣分壓6mpa體積空速2h-1氫油比(體積)1500表7脫硫前后原油性質(zhì)脫硫前脫硫后脫除率硫含量,μg/g800040095%氮含量,μg/g160016090%ni,μg/g7.1<0.01>99.9%v,μg/g6.9<0.01>99.9%殘?zhí)亢?%2.560.5180%實施例4一種含硫/高硫原油預加氫脫硫工藝,如圖2示,在初餾塔(a)與常壓塔(c)之間添加加氫脫硫反應(yīng)單元(b)對原油進行脫硫處理。加氫脫硫反應(yīng)單元(b)中的反應(yīng)器為一段固定床和兩段漿態(tài)床反應(yīng)器的組合。加氫脫硫反應(yīng)單元(b)中的反應(yīng)器的原油處理劑為加氫保護劑、加氫脫金屬劑和加氫脫硫劑。原油y經(jīng)脫鹽脫水處理后的原油經(jīng)蒸汽換熱后進入初餾塔(a),入口溫度為210℃,塔頂獲得初頂油,初頂油組分冷卻后一部分進入儲罐或進入下游工序,另一部分回流至初餾塔;塔中獲得初側(cè)油;塔底獲得拔頂油。初餾塔塔底所獲得的拔頂油與氫氣混合,經(jīng)加熱爐加熱后達到反應(yīng)溫度300℃,進入加氫脫硫處理裝置(b),在催化劑的存在下,進行加氫脫硫處理。加氫脫硫處理后的產(chǎn)物經(jīng)冷卻分離后獲得富氫氣體,富氫氣體中主要成分為氫氣和硫化氫,分離后的氫氣用于循環(huán)使用,硫化氫進入硫回收單元進行廢氣處理;經(jīng)脫硫處理后的原油無需換熱,直接進入常壓精餾塔(c)和減壓精餾塔(d)進行后續(xù)石油煉制過程。催化劑性質(zhì)如表8所示,操作條件如表9所示,原油脫硫率可達90%以上,脫氮率80%以上,脫金屬率達99.9%以上。表8催化劑性質(zhì)保護劑脫金屬劑脫硫劑化學組成,質(zhì)量%氧化鎳1.51.73.2氧化鈷//0.8氧化鉬6.28.118.5氧化鎢//2.6其他助劑//1.3物理性質(zhì)比表面積,m2/g190160220孔容,ml/g0.70.720.77使用周期,年123裝填段一段固定床二段漿態(tài)床三段漿態(tài)床表9操作條件入口溫度300℃氫氣分壓8mpa體積空速5h-1氫油比(體積)400當前第1頁12