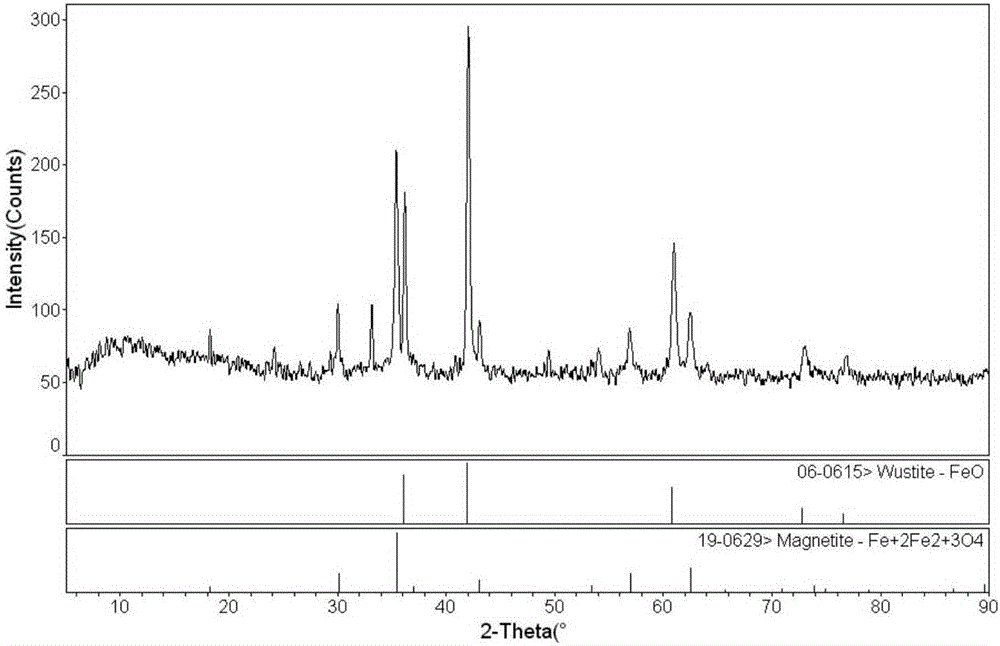
本發(fā)明屬于化工和鋼鐵冶金
技術(shù)領域:
,特別是鋼廠污泥和低熱值高爐煤氣資源化利用領域,涉及一種鋼廠高含油含鐵污泥超臨界水氣化資源化處理方法及裝置。
背景技術(shù):
:在軋鋼生產(chǎn)過程中,需要大量直接冷卻水,沖洗鋼材和設備,會產(chǎn)生大量的廢水,廢水中主要含有噴淋冷卻軋機軋輥輥道和軋制鋼材的表面產(chǎn)生的氧化鐵,機械設備上的油類物質(zhì),固體雜質(zhì)等廢棄物及污泥等,主要污染物是大量的粒度不同的氧化鐵、潤滑油類及乳化液,其中冷軋廢水中的乳化液的油脂濃度高、乳化濃度高,普遍含表面活性劑。據(jù)統(tǒng)計,我國鋼廠平均每軋制1噸鋼板約排出廢水30-40m3。廢水中含氧化鐵皮約5000mg/L,懸浮物100-1250mg/L,殘渣800-1500mg/L,油類50-500mg/L。鋼鐵行業(yè)很多都采用簡單的混凝沉淀處理工藝對鋼廠廢水進行處理,處理后產(chǎn)生的高含油含鐵污泥脫水后進行焚燒或者填埋處理。但是對于高含水量的污泥,焚燒法處理設施的投入和運營成本較高,增加了鋼鐵的生產(chǎn)成本。此外,高溫焚燒容易產(chǎn)生二噁英、氮氧化物等有毒物質(zhì),造成二次污染。填埋法占地面積大,而且污泥穩(wěn)定性差,會腐爛變質(zhì)產(chǎn)生臭氣體,污泥中的水分滲漏易污染地下水。此外,鋼廠污泥含高濃度氧化鐵,直接填埋會造成資源浪費,填埋處理費也逐年增加,這在鋼鐵行業(yè)去產(chǎn)能的大背景下,無疑增加了鋼廠的生存壓力。因此很多學者一直尋求一些新技術(shù)、新工藝對污泥進行資源化利用。超臨界水氣化技術(shù)是利用超臨界水的特性,在溫度、壓力高于水的臨界溫度和壓力(374℃,22.1MPa)條件下,水的密度、粘度和介電常數(shù)快速下降,導致超臨界水可以與有機物和氣體以任意比例混合,強化傳質(zhì)。加之在超臨界狀態(tài)下,水的離子積遠小于10-14,水中的化學反應主要以自由基反應為主,污泥中的有機物可以被快速的分解為二氧化碳、水和氮氣等物質(zhì),氧化鐵轉(zhuǎn)化為帶有磁性的四氧化三鐵,可以通過磁選分離回收利用,或者直接返回煉鋼爐重復利用。然而作為一種新興的污泥處理技術(shù),超臨界水氣化技術(shù)很少應用在鋼廠污泥處理中,而且以往的研究發(fā)現(xiàn),為達到良好的污泥處理效果,系統(tǒng)溫度必須提高,這無疑增加了能源的消耗。鋼鐵企業(yè)煉鋼生產(chǎn)中產(chǎn)生的副產(chǎn)能源高爐煤氣,由于熱值較低,含塵含水量大,壓力波動大等因素在鋼鐵企業(yè)中難以適應生產(chǎn)需要,大部分鋼鐵廠出高爐熱風爐、焦爐以及部分與焦爐煤氣混合使用外,剩余的煤氣被白白地放散掉,造成資源的浪費。而這部分煤氣可以用于超臨界水氣化系統(tǒng)的供熱,因此有必要根據(jù)鋼鐵企業(yè)自身優(yōu)勢和資源,研究開發(fā)鋼廠污泥處理處理處置的新工藝。技術(shù)實現(xiàn)要素:有鑒于此,本發(fā)明的目的在于提供一種鋼廠高含油含鐵污泥超臨界水氣化資源化處理方法及裝置,該方法和裝置利用超臨界水氣化技術(shù)回收利用鋼廠高含鐵污泥,并充分利用鋼廠低熱值高爐煤氣作為加熱器燃料,通過超臨界水氣化技術(shù)將污泥中的油脂轉(zhuǎn)化為高熱值甲烷和氫氣燃氣。為達到上述目的,本發(fā)明提供如下技術(shù)方案:一種鋼廠高含油含鐵污泥超臨界水氣化資源化處理方法,該方法包括以下步驟:S1:將鋼廠高含油含鐵生產(chǎn)污泥在預處理池中進行調(diào)質(zhì)預處理;S2:將步驟S1中預處理后的污泥,通過柱塞泵輸送到加熱器,在加熱器中進行預加熱,預加熱后的污泥輸入超臨界水氣化反應器;S3:經(jīng)過步驟S2處理后,將超臨界水氣化反應后的泥漿通過換熱器進行降溫和熱交換處理;S4:降溫后的泥漿進入氣液分離器,使氣體混合物從泥漿中充分分離出來,經(jīng)分離處理后,得到甲烷和氫氣的混合燃氣;而渣水混合物進入排水池中,在排水池中加入絮凝劑,靜置30-60min后,上清液排放到鋼廠污水處理廠繼續(xù)處理,池底污泥進行壓濾,將壓濾后的污泥通過換熱器傳下來的余熱進行脫水烘干,烘干后的污泥直接送入煉鋼爐,作為煉鋼原料。進一步,在步驟S1中,經(jīng)過調(diào)質(zhì)處理后,水/泥質(zhì)量比為5:1,pH值為6-10。進一步,在步驟S2中,加熱器所用燃料為鋼廠產(chǎn)生的低熱值高爐煤氣。進一步,在步驟S2中,反應器的溫度控制在600-700℃,壓力控制在25-30MPa,停留時間為10-20min。在步驟S4中,氣液分離處理后,產(chǎn)生的混合氣經(jīng)分離處理,產(chǎn)生的高熱值的甲烷和氫氣混合燃氣可以作為煉鋼高爐燃氣;超臨界氣化反將污泥中所有鐵質(zhì)轉(zhuǎn)化為四氧化三鐵,可以直接作為煉鋼原料;超臨界水氣化處理后的水直接排入鋼廠污水處理廠,無需進一步處理。本發(fā)明還提供了一種鋼廠高含油含鐵污泥超臨界水氣化資源化處理裝置,該裝置包括依次相連的鋼廠污泥池1、污泥調(diào)質(zhì)池2、柱塞泵3、加熱器4、超臨界氣化反應器5、換熱器6、氣液分離器7;鋼廠污泥池1中的高含油含鐵生產(chǎn)污泥通過污泥調(diào)質(zhì)池2進行調(diào)質(zhì)預處理后通過柱塞泵3輸送到加熱器4,在加熱器4中進行預加熱后的污泥輸入超臨界氣化反應器5,經(jīng)過超臨界水氣化反應后的泥漿通過換熱器6進行降溫和熱交換處理;降溫后的泥漿進入氣液分離器7,使氣體混合物從泥漿中充分分離出來;經(jīng)分離處理后,得到甲烷和氫氣的混合燃氣,混合燃氣隨后進入儲氣柜8和氣體分離系統(tǒng)9;渣水混合物進入排水池10中,在排水池10中加入絮凝劑,靜置30-60min后,上清液排放到鋼廠污水處理廠繼續(xù)處理,池底污泥進行壓濾,將壓濾后的污泥送入廢渣干燥系統(tǒng)11,通過換熱器傳下來的余熱進行脫水烘干,烘干后的污泥直接送入煉鋼爐,作為煉鋼原料。本發(fā)明的有益效果在于:1)本發(fā)明充分利用鋼廠高含油含鐵污泥有機質(zhì)含量高、熱值高等特點,結(jié)合鋼廠現(xiàn)有資源,如大量低熱值煤氣、鋼廠自建污水處理廠、高溫煉鋼爐等,將鋼廠低熱值高爐煤氣作為超臨界水氣化反應系統(tǒng)的加熱燃氣,含油含鐵污泥經(jīng)超臨界水氣化處理后,產(chǎn)生了高熱值的甲烷和氫氣的混合燃氣,達到了利用低熱值高爐煤氣結(jié)合超臨界水氣化技術(shù),產(chǎn)生高熱值燃氣的目的。2)本發(fā)明充分利用鋼廠自建污水處理廠,將超臨界水氣化處理后的水直接排入鋼廠污水處理廠,無需進一步處理,工藝簡單,可操作性強。3)本發(fā)明充分利用超臨界水的性質(zhì),含鐵污泥在經(jīng)超臨界水氣化處理后,其中的含鐵物質(zhì)完全轉(zhuǎn)化為四氧化三鐵,經(jīng)簡單的磁選后,廢渣中的鐵質(zhì)返回煉鋼爐,作為煉鋼原料,達到了污泥資源化利用的目的。附圖說明為了使本發(fā)明的目的、技術(shù)方案和有益效果更加清楚,本發(fā)明提供如下附圖進行說明:圖1為本發(fā)明所采用的系統(tǒng)結(jié)構(gòu)示意圖,其中:1-鋼廠污泥池、2-污泥調(diào)質(zhì)池、3-柱塞泵、4-加熱器、5-超臨界氣化反應器、6-換熱器、7-氣液分離器、8-儲氣柜、9-氣體分離系統(tǒng)、10-排水池、11-廢渣干燥系統(tǒng);圖2為污泥原泥的XRD圖譜;圖3為污泥SCW反應后殘渣XRD譜圖。具體實施方式下面將結(jié)合附圖,對本發(fā)明的優(yōu)選實施例進行詳細的描述。圖1為本發(fā)明所采用的系統(tǒng)結(jié)構(gòu)示意圖,如圖所示,該裝置包括依次相連的鋼廠污泥池1、污泥調(diào)質(zhì)池2、柱塞泵3、加熱器4、超臨界氣化反應器5、換熱器6、氣液分離器7;鋼廠污泥池1中的高含油含鐵生產(chǎn)污泥通過污泥調(diào)質(zhì)池2進行調(diào)質(zhì)預處理后通過柱塞泵3輸送到加熱器4,在加熱器4中進行預加熱后的污泥輸入超臨界氣化反應器5,經(jīng)過超臨界水氣化反應后的泥漿通過換熱器6進行降溫和熱交換處理;降溫后的泥漿進入氣液分離器7,使氣體混合物從泥漿中充分分離出來;經(jīng)分離處理后,得到甲烷和氫氣的混合燃氣,混合燃氣隨后進入儲氣柜8和氣體分離系統(tǒng)9;渣水混合物進入排水池10中,在排水池10中加入絮凝劑,靜置30-60min后,上清液排放到鋼廠污水處理廠繼續(xù)處理,池底污泥進行壓濾,將壓濾后的污泥送入廢渣干燥系統(tǒng)11,通過換熱器傳下來的余熱進行脫水烘干,烘干后的污泥直接送入煉鋼爐,作為煉鋼原料。實施例1:鋼廠高含油含鐵污泥采集于某鋼廠冷軋污泥池,污泥為黑色,有潤滑油氣味,含油量較高。污泥的工業(yè)分析和元素分析如表1所示,污泥的無機元素組成如表2所示,污泥的XRD晶相分析如圖2所示:表1污泥工業(yè)分析和元素分析M-水分;A-灰分;V-揮發(fā)分,oil-油含量,溶劑萃取法測定。*收到基**差減計算表2污泥無機元素組成(wt.%,db)Fe2O3CaOMgOAl2O3SiO2SO3P2O5Na2OTiO297.000.89523ppm0.210.700.350.10--Cr2O3MnOCuOK2OMoO3Tb4O7ZnOCuONiO777ppm0.45472ppm--123ppm516ppm472ppm397ppm在水/污泥質(zhì)量比為5,反應溫度660℃,壓力23.4±0.4MPa,停留時間20min條件下,添加不同質(zhì)量的CaO,氣體產(chǎn)物組成和收率如表3和表4所示。由于水煤氣變換反應進行得較為完全,氣體中CO含量極低,氣相產(chǎn)物以氫氣、二氧化碳、甲烷和乙烷為主,其中氫氣和甲烷各占三分之一左右。表3氣相產(chǎn)物組成(vol.%)表4氣相產(chǎn)物收率(ml/g干污泥)和氣化率反應后殘渣元素分析結(jié)果列于表5,污泥中的碳轉(zhuǎn)化率為94.7%,未添加CaO時氣化率接近60%,添加CaO后氣化率達到90%左右。表5超臨界水中反應后殘渣元素分析(wt%,db)樣品CHNS碳轉(zhuǎn)化率(%)2#污泥反應后0.5470.0430.0030.02194.7圖3為反應后殘渣的XRD譜圖,反應后殘渣幾乎全部轉(zhuǎn)化為磁鐵礦,添加CaO的殘渣中有碳酸鈣,其中圖3(a)為SCW反應殘渣,圖3(b)為SCW添加CaO反應殘渣。污泥在超臨界水中反應后,水中總有機碳(TOC)和化學需氧量(COD)列于表6。表6污泥反應后水質(zhì)CaO/污泥質(zhì)量比Ca/C摩爾比TOC(mg/L)COD(g/L)100307.50.6620.330.782656.09.0430.471.091264.05.18最后說明的是,以上優(yōu)選實施例僅用以說明本發(fā)明的技術(shù)方案而非限制,盡管通過上述優(yōu)選實施例已經(jīng)對本發(fā)明進行了詳細的描述,但本領域技術(shù)人員應當理解,可以在形式上和細節(jié)上對其做出各種各樣的改變,而不偏離本發(fā)明權(quán)利要求書所限定的范圍。當前第1頁1 2 3