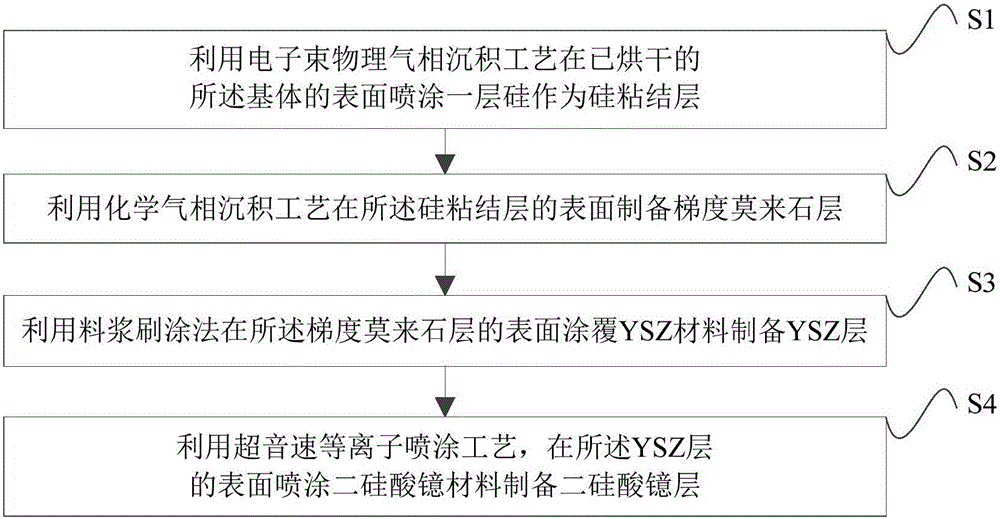
本發(fā)明涉及功能涂層材料領域,尤其涉及了一種用于連續(xù)纖維增強的熱結(jié)構(gòu)復合材料的多層高溫涂層及其制備方法。
背景技術:
:連續(xù)纖維增強的熱結(jié)構(gòu)復合材料由于具有耐高溫、高韌性、密度低、耐腐蝕和抗氧化等優(yōu)勢,采用其制備航空發(fā)動機高壓渦輪靜子件等關鍵構(gòu)件,可顯著降低發(fā)動機構(gòu)件的重量,并大幅降低航空發(fā)動機中冷卻空氣用量及油耗率。然而,面對航空發(fā)動機中復雜的水氧和熔鹽環(huán)境,由上述連續(xù)纖維增強的熱結(jié)構(gòu)復合材料制備的熱端部件并不能達到長時間有效工作的要求,因此,需要添加防護涂層以保護由上述材料制備的基體。目前常用的涂層材料包括熱障涂層和環(huán)境障涂層,但上述兩種涂層材料均存在一定的缺陷。如傳統(tǒng)的熱障涂層主要是以氧化釔穩(wěn)定的氧化鋯(ZrO2-Y2O3,YSZ)作為涂層的最外層材料,在大氣氧化的環(huán)境中表現(xiàn)出很好的抗氧化性能,但在復雜的水汽環(huán)境中無法適用,在1300℃的航空發(fā)動機環(huán)境條件下有效工作時間(有效工作時間是指涂層發(fā)生失重失效之前的工作時間)尚不足150小時;而現(xiàn)有的最為先進的環(huán)境障涂層,即稀土硅酸鹽涂層體系(以二硅酸鐿為例),在航空發(fā)動機環(huán)境條件下有效工作時間僅為200小時左右。因此,現(xiàn)有的涂層材料均不能在航空發(fā)動機環(huán)境下長時間的有效工作。技術實現(xiàn)要素:本發(fā)明的目的是提供一種用于連續(xù)纖維增強的熱結(jié)構(gòu)復合材料的多層高溫涂層及其制備方法,可大幅延長上述涂層材料在航空發(fā)動機環(huán)境下的有效工作時間。為達到上述目的,本發(fā)明提供的技術方案為:第一方面,本發(fā)明提供了一種用于連續(xù)纖維增強的熱結(jié)構(gòu)復合材料的多層高溫涂層,上述涂層自基體向外依次包括硅粘結(jié)層、梯度莫來石層、YSZ層和二硅酸鐿層;其中,硅粘結(jié)層的厚度為40~60μm,梯度莫來石層的厚度為110~140μm,YSZ層的厚度為120~140μm,二硅酸鐿層的厚度為140~170μm。本發(fā)明所提供的用于連續(xù)纖維增強的熱結(jié)構(gòu)復合材料的多層高溫涂層,自基體向外依次包括硅粘結(jié)層、梯度莫來石層、YSZ層和二硅酸鐿層,二硅酸鐿的材料相結(jié)構(gòu)更加穩(wěn)定,使用其作為最外層,可有效地抵抗航空發(fā)動機中的水汽和熔鹽侵蝕;且位于二硅酸鐿層和梯度莫來石層之間的YSZ層起到較好的隔熱作用,可防止航空發(fā)動機中的熱量透過二硅酸鐿層對內(nèi)層涂層材料進行熱侵蝕;上述梯度莫來石層是指熱膨脹系數(shù)具有梯度性變化的莫來石層,在上述涂層中最內(nèi)層的硅粘結(jié)層的熱膨脹系數(shù)較小,一般為3.5~4.5×10-6/℃,而YSZ層的熱膨脹系數(shù)較大,一般為10.6×10-6/℃,兩者的熱膨脹系數(shù)存在較大的差異,因此,兩者之間難以直接配合,需要在其間添加過渡層,莫來石是由氧化鋁和二氧化硅組成的化合物,其中氧化鋁的熱膨脹系數(shù)大于二氧化硅,在梯度莫來石層的制備過程中,可通過改變氧化鋁和二氧化硅的比例來調(diào)整梯度莫來石層的熱膨脹系數(shù),使之與硅粘結(jié)層及YSZ層的相接觸處均有良好的配合,從而較大程度地避免了涂層內(nèi)部各層間內(nèi)應力的產(chǎn)生。此外,上述涂層中各層之間由于涂層材料的不同,在各涂層之間存在一定的界面剪切應力,上述界面剪切應力與各層的厚度的平方存在正相關關系(例如硅粘結(jié)層與基體之間的界面剪切應力與硅粘結(jié)層的厚度的平方呈正相關關系),即各層厚度越大,界面剪切應力也就越大,當涂層的厚度過大時,涂層的穩(wěn)定性就會變差,出現(xiàn)涂層開裂或剝落的現(xiàn)象,但若各層的厚度過薄,在航空發(fā)動機的環(huán)境下亦較容易損壞。經(jīng)過大量的實驗研究,上述各層的厚度優(yōu)選為:硅粘結(jié)層的厚度為40~60μm,梯度莫來石層的厚度為110~140μm,YSZ層的厚度為120~140μm,二硅酸鐿層的厚度為140~170μm,當上述各層的厚度在上述范圍時,本發(fā)明所提供的用于連續(xù)纖維增強的熱結(jié)構(gòu)復合材料的多層高溫涂層,在航空發(fā)動機的環(huán)境中使用時可獲得較長的有效工作時間。因此,本發(fā)明所提供用于連續(xù)纖維增強的熱結(jié)構(gòu)復合材料的多層高溫涂層,可大幅延長其在航空發(fā)動機環(huán)境下的有效工作時間。第二方面,本發(fā)明還提供了一種上述用于連續(xù)纖維增強的熱結(jié)構(gòu)復合材料的多層高溫涂層的制備方法,上述制備方法包括:步驟S1,利用電子束物理氣相沉積工藝在已烘干的所述基體的表面噴涂一層硅作為硅粘結(jié)層;步驟S2,利用化學氣相沉積工藝在硅粘結(jié)層的表面制備梯度莫來石層;步驟S3,利用料漿刷涂法在所述梯度莫來石層的表面涂覆YSZ材料制備YSZ層;步驟S4,利用超音速等離子噴涂工藝,在所述YSZ層的表面噴涂二硅酸鐿材料制備二硅酸鐿層。進一步地,上述硅粘結(jié)層的厚度為40~60μm,梯度莫來石層的厚度為110~140μm,YSZ層的厚度為120~140μm,二硅酸鐿層的厚度為140~170μm。進一步地,在步驟S1之前還包括:將上述基體的表面進行打磨;將打磨后的基體放入無水乙醇中利用超聲波進行清洗;將清洗后的基體放入烘箱中,在80-100℃條件下烘干2-5h。進一步地,上述電子束物理氣相沉積工藝的參數(shù)設置為:電壓為8~11.0KV,電流為0.55~0.65A,真空度為6~15.0×10-3Pa,硅靶材與基體的間距為180~220mm,上述基體的轉(zhuǎn)速為9~11r/min,沉積速率為10~14μm/h,沉積時間為4~6h。進一步地,上述化學氣相沉積工藝是在化學氣相沉積爐中進行,上述化學氣相沉積爐中的真空度設置為5×104Pa~7×104Pa,上述化學氣相沉積爐中所用氣相為AlCl3、SiCl4、CO2和H2組成的混合氣體;以SiCl4氣體為標準,上述混合氣體的流量為2.5×10-5m3/s~3.5×10-5m3/s。進一步地,在上述化學氣相沉積工藝的開始階段,AlCl3氣體的流量為7×10-5m3/s~10×10-5m3/s;隨著上述化學氣相沉積工藝的不斷進行,逐漸增加所述AlCl3氣體的流量,AlCl3氣體的流量的增加速率為0.1×10-5m3/min~0.15×10-5m3/min;在上述化學氣相沉積工藝的最后階段,AlCl3氣體的流量為9×10-5m3/s~12×10-5m3/s。進一步地,在步驟S3之后、步驟S4之前,還包括:將涂覆有YSZ材料的基體放入高溫爐中,對高溫爐先進行抽真空操作,然后通入高純氬氣;以15~20℃/min的升溫速率將高溫爐的爐溫升至650~700℃,保溫2~5h;以20~25℃/min的降溫速率將高溫爐的爐溫降至300~450℃,關閉高溫爐的電源,并自然降溫至室溫。進一步地,上述YSZ材料為ZrO2和Y2O3組成的混合物,其中,所述Y2O3的質(zhì)量占所述混合物總質(zhì)量的比例為6%~8%。進一步地,上述步驟S4具體包括:步驟S41,將粒度為10μm~20μm的SiO2和Yb2O3粉末按摩爾比2:1~2.5:1的比例制成懸浮液并放入氧化鋁坩堝中混合;步驟S42,將混合后的所述懸浮液放入烘箱中,在110~130℃的條件下烘干,得到完全烘干的混合粉末;步驟S43,將混合粉末在1400~1500℃下反應20~24h,將反應后的混合粉末自然降溫得到二硅酸鐿粉體;步驟S44,使用無水乙醇對帶有三層涂層的基體的表面進行超聲波清洗,然后使用剛玉砂礫對其表面進行噴砂處理,最后使用壓縮空氣對其表面進行除雜;步驟S45,利用超音速等離子噴涂工藝,將所述二硅酸鐿粉體噴涂于除雜后的帶有三層涂層的基體的表面制備二硅酸鐿層。本發(fā)明所提供的用于連續(xù)纖維增強的熱結(jié)構(gòu)復合材料的多層高溫涂層的制備方法,自基體向外依次設置有硅粘結(jié)層、梯度莫來石層、YSZ層和二硅酸鐿層,二硅酸鐿的材料相結(jié)構(gòu)更加穩(wěn)定,使用其作為最外層,可有效地抵抗航空發(fā)動機中的水汽和熔鹽環(huán)境;且位于二硅酸鐿層和梯度莫來石層之間的YSZ層可起到較好的隔熱作用,防止航空發(fā)動機中的熱量透過二硅酸鐿層對內(nèi)層涂層材料進行熱侵蝕;上述梯度莫來石層是指熱膨脹系數(shù)具有梯度性變化的莫來石層,在上述涂層中最內(nèi)層的硅粘結(jié)層的熱膨脹系數(shù)較小,一般為3.5~4.5×10-6/℃,而YSZ層的膨脹系數(shù)較大,一般為10.6×10-6/℃,兩者之間存在較大地熱膨脹系數(shù)的差異,因此,兩者之間難以直接配合,需要在其間添加過渡層,莫來石是由氧化鋁和二氧化硅組成的混合物,其中氧化鋁的熱膨脹系數(shù)大于二氧化硅,在梯度莫來石層的制備過程中,保持SiCl4氣體的流量不變,通過逐漸增加AlCl3氣體的流量來增加梯度莫來石層中氧化鋁的含量,從而使得整個梯度莫來石層與硅粘結(jié)層及YSZ層相接觸處都能得到良好的配合,從而較大程度地避免了涂層內(nèi)部各層間內(nèi)應力的產(chǎn)生。此外,上述涂層中各層之間由于涂層材料的不同,在各涂層之間存在一定的界面剪切應力,上述界面剪切應力與各層的厚度的平方存在正相關關系(例如硅粘結(jié)層與基體之間的界面剪切應力與硅粘結(jié)層的厚度的平方呈正相關關系),即各層厚度越大,界面剪切應力也就越大,當涂層的厚度過大時,涂層的穩(wěn)定性就會變差,出現(xiàn)涂層開裂或剝落的現(xiàn)象,但若各層的厚度過薄,在航空發(fā)動機的環(huán)境下亦較容易損壞。經(jīng)過大量的實驗研究,上述各層的厚度優(yōu)選為:硅粘結(jié)層的厚度為40~60μm,梯度莫來石層的厚度為110~140μm,YSZ層的厚度為120~140μm,二硅酸鐿層的厚度為140~170μm,當上述各層的厚度在上述范圍時,本發(fā)明所提供的制備方法所獲得的涂層,在航空發(fā)動機的環(huán)境中使用時可獲得較長的有效工作時間。因此,本發(fā)明所提供用于連續(xù)纖維增強的熱結(jié)構(gòu)復合材料的多層高溫涂層的制備方法所獲得的涂層,可大幅延長其在航空發(fā)動機環(huán)境下的有效工作時間。附圖說明以下附圖僅旨在對本發(fā)明做示意性說明和解釋,并不限定本發(fā)明的范圍。圖1為本發(fā)明實施例提供的用于連續(xù)纖維增強的熱結(jié)構(gòu)復合材料的多層高溫涂層的結(jié)構(gòu)示意圖;圖2為本發(fā)明實施例提供的用于連續(xù)纖維增強的熱結(jié)構(gòu)復合材料的多層高溫涂層的制備方法的流程圖。具體實施方式下面將結(jié)合本發(fā)明實施例中的附圖,對本發(fā)明實施例中的技術方案進行清楚、完整地描述,顯然,所描述的實施例僅僅是本發(fā)明一部分實施例,而不是全部的實施例。基于本發(fā)明中的實施例,本領域普通技術人員在沒有做出創(chuàng)造性勞動前提下所獲得的所有其他實施例,都屬于本發(fā)明保護的范圍。實施例一本發(fā)明實施例提供了一種用于連續(xù)纖維增強的熱結(jié)構(gòu)復合材料的多層高溫涂層,上述涂層自基體1向外依次包括硅粘結(jié)層2、梯度莫來石層3、YSZ層4和二硅酸鐿層5;其中,硅粘結(jié)層2的厚度為50μm,梯度莫來石層3的厚度為120μm,YSZ層4的厚度為120μm,二硅酸鐿層5的厚度為160μm。本發(fā)明實施例所提供的用于連續(xù)纖維增強的熱結(jié)構(gòu)復合材料的多層高溫涂層,自基體向外依次包括硅粘結(jié)層2、梯度莫來石層3、YSZ層4和二硅酸鐿層5,二硅酸鐿的材料相結(jié)構(gòu)更加穩(wěn)定,使用其作為最外層,可有效地抵抗航空發(fā)動機中的水汽和熔鹽侵蝕;且位于二硅酸鐿層5和梯度莫來石層3之間的YSZ層4起到較好的隔熱作用,可防止航空發(fā)動機中的熱量透過二硅酸鐿層5對內(nèi)層涂層材料進行熱侵蝕;上述梯度莫來石層3是指熱膨脹系數(shù)具有梯度性變化的莫來石層,在上述涂層中最內(nèi)層的硅粘結(jié)層2的熱膨脹系數(shù)較小,一般為3.5~4.5×10-6/℃,而YSZ層4的熱膨脹系數(shù)較大,一般為10.6×10-6/℃,兩者的熱膨脹系數(shù)存在較大的差異,因此,兩者之間難以直接配合,需要在其間添加過渡層,莫來石是由氧化鋁和二氧化硅組成的化合物,其中氧化鋁的熱膨脹系數(shù)大于二氧化硅,在梯度莫來石層3的制備過程中,可通過改變氧化鋁和二氧化硅的比例來調(diào)整梯度莫來石層3的熱膨脹系數(shù),使之與硅粘結(jié)層2及YSZ層4的相接觸處均有良好的配合,從而較大程度地避免了涂層內(nèi)部各層間內(nèi)應力的產(chǎn)生。此外,上述涂層中各層之間由于涂層材料的不同,在各涂層之間存在一定的界面剪切應力,上述界面剪切應力與各層的厚度的平方存在正相關關系(例如硅粘結(jié)層2與基體1之間的界面剪切應力與硅粘結(jié)層2的厚度的平方呈正相關關系),即各層厚度越大,界面剪切應力也就越大,當涂層的厚度過大時,涂層的穩(wěn)定性就會變差,出現(xiàn)涂層開裂或剝落的現(xiàn)象,但若各層的厚度過薄,在航空發(fā)動機的環(huán)境下亦較容易損壞。經(jīng)過大量的實驗研究,本發(fā)明實施例中上述各層的厚度優(yōu)選為:硅粘結(jié)層2的厚度為50μm,梯度莫來石層3的厚度為120μm,YSZ層4的厚度為120μm,二硅酸鐿層5的厚度為160μm,此時,上述涂層的有效工作時間最長。需要說明的是,上述涂層中各層的厚度設置僅為本發(fā)明實施例的一種優(yōu)選方案,不能作為對本發(fā)明所提供的用于連續(xù)纖維增強的熱結(jié)構(gòu)復合材料的多層高溫涂層的涂層的實施范圍的限定,上述各層的厚度設置只要在下述范圍內(nèi),硅粘結(jié)層2:40~60μm,梯度莫來石層3:110~140μm,YSZ層4:120~140μm,二硅酸鐿層5:140~170μm,所得涂層均具有較長的有效工作時間。以下本發(fā)明實施例將針對不同厚度設置的各層材料所組合的涂層在1400℃的模擬發(fā)動機環(huán)境下的有效工作時間進行測試。此處,為了便于表述,本發(fā)明將厚度設置在上述優(yōu)選范圍內(nèi)的各層定義為P,厚度設置小于上述優(yōu)選范圍的各層定義為P1,厚度設置大于上述優(yōu)選范圍的各層定義為P2。對本發(fā)明實施例而言,上述硅粘結(jié)層2的厚度分別設置為25μm(記為P1),50μm(記為P),75μm(記為P2);上述梯度莫來石層3的厚度分別設置為95μm(記為P1),120μm(記為P),155μm(記為P2);上述YSZ層4的厚度分別設置為105μm(記為P1),120μm(記為P),155μm(記為P2);上述二硅酸鐿層5的厚度分別設置為125μm(記為P1),160μm(記為P),185μm(記為P2)。則若只有硅粘結(jié)層2的厚度設置小于優(yōu)選范圍,其他各層的厚度設置均在優(yōu)選范圍內(nèi)時,上述涂層可以表述為P1PPP。表1顯示的為本發(fā)明實施例所設計的九種方案所得涂層的有效工作時間(T)測試。表1序號123456789方案PPPPP1PPPP2PPPPP1PPPP2PPPPP1PPPP2PPPPP1PPPP2T/h400312307287280264247207202從表1中可以看出,無論是哪一層,若其厚度設置不在優(yōu)選范圍之內(nèi),均會對涂層的有效工作時間產(chǎn)生影響。而從最內(nèi)層的硅粘結(jié)層2到最外層的二硅酸鐿層5,當二硅酸鐿層5的厚度不在優(yōu)選范圍內(nèi)時,對上述涂層的有效工作時間影響最大,這是最外層材料為最先接觸使用環(huán)境的材料,其性能的優(yōu)劣將對涂層性能的好壞帶來直接影響。需要關注的是,上述九種方案任意方案所得涂層在1400℃的模擬航空發(fā)動機環(huán)境下有效工作時間均在200h以上,當各層材料均設置在上述優(yōu)選范圍內(nèi)時,所得涂層的有效工作時間更達到400h,遠遠超過現(xiàn)有的單一使用時的熱障涂層(YSZ)及環(huán)境障涂層(二硅酸鐿)的有效工作時間。此外,本發(fā)明實施例還對上述優(yōu)選方案(PPPP方案)所得涂層在不同的溫度時的模擬航空發(fā)動機環(huán)境下的有效工作時間進行測試,其具體測試結(jié)果如表2所示。表2序號123456789溫度/℃140014501500155016001650170017501800T/h400385373361349336321312303從表2可以看出,區(qū)別于傳統(tǒng)的熱障涂層和環(huán)境障涂層,本發(fā)明所提供用于連續(xù)纖維增強的熱結(jié)構(gòu)復合材料的的多層高溫涂層不僅可以在1400℃的模擬航空發(fā)動機的環(huán)境中有效工作時間達到400h,其在更高的溫度下同樣有較長的工作時間,為保證上述涂層的有效工作時間在300h以上,本發(fā)明所提供的涂層的適宜使用溫度范圍為1400~1800℃。另外需要說明的是,上述用于連續(xù)纖維增強的熱結(jié)構(gòu)復合材料主要是指炭纖維增強碳基的熱結(jié)構(gòu)復合材料、炭纖維增強的碳化硅基的熱結(jié)構(gòu)復合材料、碳化硅纖維增強的碳化硅基的熱結(jié)構(gòu)復合材料、氧化鋁纖維增強的碳化硅基熱結(jié)構(gòu)復合材料及氧化鋁纖維增強的氧化鋁基的熱結(jié)構(gòu)復合材料。當上述涂層用于碳化硅纖維增強的碳化硅基的熱結(jié)構(gòu)復合材料,涂層在1400℃的模擬航空發(fā)動機的環(huán)境中的有效工作時間在400h以上(如上所述),當上述涂層用于其他形式的連續(xù)纖維增強的熱結(jié)構(gòu)復合材料時,涂層的有效工作時間有所下降,但均在300h以上。實施例二本發(fā)明實施例還提供了一種實施例一中所述用于連續(xù)纖維增強的熱結(jié)構(gòu)復合材料的多層高溫涂層的制備方法,所述制備方法包括:步驟S1,利用電子束物理氣相沉積工藝在已烘干的基體1的表面噴涂一層硅作為硅粘結(jié)層2;步驟S2,利用化學氣相沉積工藝在硅粘結(jié)層2的表面制備梯度莫來石層3;步驟S3,利用料漿刷涂法在所述梯度莫來石層3的表面涂覆YSZ材料制備YSZ層4;步驟S4,利用超音速等離子噴涂工藝,在所述YSZ層4的表面噴涂二硅酸鐿材料制備二硅酸鐿層5。本發(fā)明實施例所提供的用于連續(xù)纖維增強的熱結(jié)構(gòu)復合材料的多層高溫涂層的制備方法,自基體1向外依次設置有硅粘結(jié)層2、梯度莫來石層3、YSZ層4和二硅酸鐿層5,二硅酸鐿的材料相結(jié)構(gòu)更加穩(wěn)定,使用其作為最外層,可有效地抵抗航空發(fā)動機中的水汽和熔鹽環(huán)境;且位于二硅酸鐿層5和梯度莫來石層3之間的YSZ層4可起到較好的隔熱作用,防止航空發(fā)動機中的熱量透過二硅酸鐿層5對內(nèi)層涂層材料進行熱侵蝕;上述梯度莫來石層3是指熱膨脹系數(shù)具有梯度性變化的莫來石層,在上述涂層中最內(nèi)層的硅粘結(jié)層2的熱膨脹系數(shù)較小,一般為3.5~4.5×10-6/℃,而YSZ層4的膨脹系數(shù)較大,一般為10.6×10-6/℃,兩者之間存在較大地熱膨脹系數(shù)的差異,因此,兩者之間難以直接配合,需要在其間添加過渡層,莫來石是有氧化鋁和二氧化硅組成的混合物,其中氧化鋁的熱膨脹系數(shù)大于二氧化硅,在梯度莫來石層3的制備過程中,通過改變莫來石中氧化鋁與二氧化硅的含量,使得整個梯度莫來石層3與硅粘結(jié)層2及YSZ層4相接觸處都能得到良好的配合,從而較大程度地避免了涂層內(nèi)部各層間內(nèi)應力的產(chǎn)生;且上述二硅酸鐿層5采用的是先進的超音速等離子噴涂技術,減少了制備過程中孔洞的產(chǎn)生,較大程度地保證了涂層的質(zhì)量,有利于延長上述涂層在航空發(fā)動機環(huán)境下的有效工作時間。優(yōu)選地,在上述步驟S1之前還包括:將基體1的表面進行打磨;將打磨后的基體1放入無水乙醇中利用超聲波進行清洗;將清洗后的基體1放入烘箱中,在80-100℃條件下烘干2-5h。采用上述處理方法,使得基體1的表面性能更加優(yōu)異,有利于提高基體1與涂層之間的機械結(jié)合強度。優(yōu)選地,上述電子束物理氣相沉積工藝的參數(shù)設置為:電壓為8~11.0KV,電流為0.55~0.65A,真空度為6~15.0×10-3Pa,硅靶材與基體1的間距為180~220mm,所述基體1的轉(zhuǎn)速為9~11r/min,沉積速率為10~14μm/h,沉積時間為4~6h。需要說明的是,上述電子束物理氣相沉積工藝的參數(shù)設置僅為本發(fā)明實施例的一種優(yōu)選方案,不能作為對本發(fā)明所提供的用于連續(xù)纖維增強的熱結(jié)構(gòu)復合材料的多層高溫涂層的制備方法的實施范圍的限定,上述參數(shù)設置需根據(jù)涂層制備時的實際情況而定。優(yōu)選地,上述化學氣相沉積工藝是在化學氣相沉積爐中進行,上述化學氣相沉積爐中的真空度設置為5×104Pa~7×104Pa,上述化學氣相沉積爐中所用氣相為AlCl3、SiCl4、CO2和H2組成的混合氣體;以SiCl4氣體為標準,所述混合氣體的流量為3.5×10-5m3/s。需要說明的是,上述化學氣相沉積工藝的參數(shù)設置僅為本發(fā)明實施例的一種優(yōu)選方案,不能作為對本發(fā)明所提供的用于連續(xù)纖維增強的熱結(jié)構(gòu)復合材料的多層高溫涂層的制備方法的實施范圍的限定,上述參數(shù)設置需根據(jù)涂層制備時的實際情況而定。優(yōu)選地,在化學氣相沉積工藝的開始階段,AlCl3氣體的流量為7×10-5m3/s;隨著化學氣相沉積工藝的不斷進行,逐漸增加所述AlCl3氣體的流量,所述AlCl3氣體的流量的增加速率為0.1×10-5m3/min;在化學氣相沉積工藝的最后階段,所述AlCl3氣體的流量為12×10-5m3/s。在上述化學氣相沉積工藝中所發(fā)生的沉積反應為:6AlCl3(g)+2SiCl4(g)+13CO2(g)+13H2(g)→3Al2O3·2SiO2(s)+13CO(g)+26HCl(g),上述反應若恰好反應完全,AlCl3氣體的流量需為SiCl4氣體流量的三倍。在上述反應的初始階段,即制備靠近硅粘結(jié)層2一側(cè)的梯度莫來石層3,此時所制備的莫來石,其熱膨脹系數(shù)需和硅粘結(jié)層2的熱膨脹系數(shù)相匹配,因此,需要保證SiCl4氣體過量,而經(jīng)過一定的試驗研究,當SiCl4氣體的流量設置為3.5×10-5m3/s,AlCl3氣體的流量設置為7×10-5m3/s,可保證梯度莫來石層3和硅粘結(jié)層2熱膨脹系數(shù)的匹配;在上述反應的最后階段,即制備靠近YSZ層4一側(cè)的梯度莫來石層3,此時所制備的莫來石,其熱膨脹系數(shù)需和YSZ層4箱匹配,因此,要保證AlCl3氣體過量,而經(jīng)過一定的試驗研究,當SiCl4氣體的流量設置為3.5×10-5m3/s,AlCl3氣體的流量設置為12×10-5m3/s,可保證梯度莫來石層3和YSZ層4熱膨脹系數(shù)的匹配;而上述AlCl3氣體的流量的增加速率的設置,僅為本發(fā)明實施例的一種優(yōu)選方案不能作為對本發(fā)明實施范圍的限定,其具體設置值需結(jié)合沉積時間及上述梯度莫來石層3的厚度而定。優(yōu)選地,在步驟S3之后、步驟S4之前,還包括:將涂覆有YSZ材料的基體1放入高溫爐中,對高溫爐先進行抽真空操作,然后通入高純氬氣;以15~20℃/min的升溫速率將高溫爐的爐溫升至650~700℃,保溫2~5h;以20~25℃/min的降溫速率將高溫爐的爐溫降至300~450℃,關閉高溫爐的電源,并自然降溫至室溫。優(yōu)選地,上述YSZ材料為ZrO2和Y2O3組成的混合物,其中,所述Y2O3的質(zhì)量占所述混合物總質(zhì)量的比例為6%。優(yōu)選地,上述步驟S4具體包括:步驟S41,將粒度為10μm~20μm的SiO2和Yb2O3粉末按摩爾比2:1的比例制成懸浮液并放入氧化鋁坩堝中混合;步驟S42,將混合后的所述懸浮液放入烘箱中,在110~130℃的條件下烘干,得到完全烘干的混合粉末;步驟S43,將混合粉末在1400~1500℃下反應20~24h,將反應后的混合粉末自然降溫得到二硅酸鐿粉體;步驟S44,使用無水乙醇對帶有三層涂層的基體1的表面進行超聲波清洗,然后使用剛玉砂礫對其表面進行噴砂處理,最后使用壓縮空氣對其表面進行除雜;步驟S45,利用超音速等離子噴涂工藝,將所述二硅酸鐿粉體噴涂于除雜后的帶有三層涂層的基體的表面制備二硅酸鐿層5。需要說明的是,上述YSZ的材料中Y2O3的質(zhì)量占混合物總質(zhì)量的比例設置及二硅酸鐿的制備過程中SiO2和Yb2O3粉末的摩爾比比例設置均僅為本發(fā)明實施例的一種優(yōu)選方案,不能作為本發(fā)明所提供的用于連續(xù)纖維增強的熱結(jié)構(gòu)復合材料的多層高溫涂層的涂層的制備方法的實施范圍的限定。以下本發(fā)明實施例將對不同的Y2O3質(zhì)量比及不同SiO2和Yb2O3摩爾比設置下所制備的涂層在1400℃的模擬航空發(fā)動機中的有效工作時間進行測定。為了便于表述,本發(fā)明實施例將Y2O3的質(zhì)量占混合物總質(zhì)量的比例為6%的方案定義為A1,將Y2O3的質(zhì)量占混合物總質(zhì)量的比例為7%的方案定義為A2,將Y2O3的質(zhì)量占混合物總質(zhì)量的比例為7%的方案定義為A3,將SiO2和Yb2O3摩爾比為2:1的方案定義為B1,將SiO2和Yb2O3摩爾比為2.2:1的方案定義為B2,將SiO2和Yb2O3摩爾比為2.5:1的方案定義為B3,則上述實施例中的優(yōu)選方案可以表述為A1B1。表3顯示的為本發(fā)明實施例設計的六種方案所制備涂層的有效工作時間的測試結(jié)果。表3序號12345方案A1B1A1B2A1B3A2B1A3B1T/h410392367396389如表3所示,其中序號為1、2和3的方案,僅改變了制備二硅酸鐿過程中的SiO2和Yb2O3的摩爾比,所獲得涂層的有效工作時間即存在較大的差異。其中,當SiO2和Yb2O3的摩爾比為2:1時,涂層的有效工作時間最長,可達410小時,由此可見,上述SiO2和Yb2O3的比例優(yōu)選為2:1。如表2所示,其中序號為1、4和5的方案,僅改變了制備YSZ材料中Y2O3的質(zhì)量占混合物總質(zhì)量的比例,所獲得涂層的有效工作時間即存在較大的差異。其中,當Y2O3的質(zhì)量占混合物總質(zhì)量的比例為6%時,涂層的有效工作時間最長,可達410小時,由此可見,Y2O3的質(zhì)量占混合物總質(zhì)量的比例優(yōu)選為6%。以上對本發(fā)明的一個實施例進行了詳細說明,但所述內(nèi)容僅為本發(fā)明的較佳實施例,不能被認為用于限定本發(fā)明的實施范圍。凡依本發(fā)明申請范圍所作的均等變化與改進,均應歸屬于本發(fā)明的專利涵蓋范圍之內(nèi)。當前第1頁1 2 3