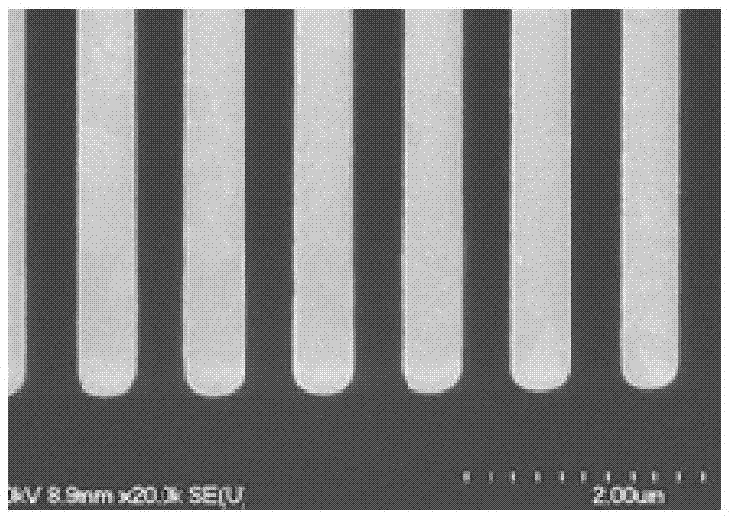
本發(fā)明涉及一種用于金屬基板拋光后的清洗液及其使用方法。
背景技術(shù):
:金屬材料如銅,鋁,鎢等是集成電路中常用的導(dǎo)線材料。在制造器件時(shí),化學(xué)機(jī)械拋光(cmp)成為晶片平坦化的主要技術(shù)。金屬化學(xué)機(jī)械拋光液通常含有研磨顆粒、絡(luò)合劑、金屬腐蝕抑制劑、氧化劑等。其中研磨顆粒主要為二氧化硅、三氧化二鋁、摻雜鋁或覆蓋鋁的二氧化硅、二氧化鈰、二氧化鈦、高分子研磨顆粒等。在金屬cmp工序以后,晶片表面會(huì)受到金屬離子以及拋光液中研磨顆粒本身的污染,這種污染會(huì)對(duì)半導(dǎo)體的電氣特性以及器件的可靠性產(chǎn)生影響。而且,金屬離子和研磨顆粒的殘留都會(huì)影響晶片表面的平坦度,從而可能降低器件的性能影響后續(xù)工序或者器件的運(yùn)行。所以,在金屬cmp工藝后,去除殘留在晶片表面的金屬離子、金屬腐蝕抑制劑和研磨顆粒,改善晶片表面的親水性,降低表面缺陷是非常有必要的。專利cn100543124c,提供了一種基板的清洗劑和清洗方法,此清洗劑可以去除基本表面顆粒劑金屬雜質(zhì),不影響表面粗糙;還可以在不去除防金屬腐蝕劑-cu涂層同時(shí),去除存在于基板表面的碳缺陷。此種清洗劑含有至少1個(gè)羧基的有機(jī)酸、有機(jī)磷酸組成的絡(luò)合劑和一種以上有機(jī)溶劑。該清洗液另含選自由還原劑、防金屬腐蝕劑及表面活性劑中的至少一種。其中所述的表面活性劑選自下述物質(zhì)組成的組中的至少一種:分子中具有聚氧亞烷基的非離子類表面活性劑;分子中具有選自磺酸基、羧酸、膦酸基、次硫酸基和膦酰氧基的基團(tuán)的陰離子類表面活性劑,兩性表面活性劑。但是該技術(shù)方案使用有機(jī)溶劑不環(huán)保。清洗液中所添加的防腐蝕抑制劑為銅拋光漿料中含 有的防腐蝕抑制劑,同樣有可能會(huì)殘留在晶片表面形成碳缺陷。另外,無實(shí)施例證明添加由還原劑、防金屬腐蝕劑及表面活性劑組成的清洗液的效果。us2001/0051597a1公開了一種用檸檬酸和螯合劑組成的清洗液,其目的在于將晶片上殘留的金屬離子去除。us2005/0197266,提供了一種由酸性化學(xué)物質(zhì)及腐蝕抑制劑組成的清洗液,去除晶片表面殘留的金屬離子,調(diào)節(jié)清洗液的ph值跟拋光液的ph值匹配。us2005/0199264a1提供了一種含有羥基羧酸/鹽和殺菌劑的清洗液,可去除晶片表面殘留的研磨顆粒和抑制晶片表面的細(xì)菌的生長。tw416987b提供了一種含有羥基羧酸/鹽和殺菌劑的清洗液,可去除晶片表面殘留的研磨顆粒和抑制晶片表面的細(xì)菌的生長。cn1225529c提供了一種洗凈電子材料用基板的洗凈液,其包含有機(jī)酸化合物,分散劑磷酸酯和陰離子型或者非離子型表面活性劑,可以清除硅片表面的顆粒和鐵離子。但是這些清洗液均存在清洗效果單一的缺點(diǎn),僅可以起到去除金屬離子,去除研磨顆粒以及殺菌等的單一效果,對(duì)有機(jī)物如金屬腐蝕抑制劑的去除也沒有涉及。技術(shù)實(shí)現(xiàn)要素:本發(fā)明提供了一種用于金屬基板拋光后的清洗液及其使用方法。為了解決上述技術(shù)問題,本發(fā)明一方面提供了一種清洗液,包含有機(jī)酸,有機(jī)磷酸類化合物,陰離子表面活性劑和非離子表面活性劑。其中,所述有機(jī)酸為檸檬酸,蘋果酸,草酸,酒石酸和水楊酸中的一種或多種。優(yōu)選為檸檬酸。有機(jī)酸濃度為質(zhì)量百分比0.05-5%,優(yōu)選為質(zhì)量百分比0.1-3%。本發(fā)明的清洗液,其中,所述有機(jī)磷酸類化合物為氨基三亞甲基膦酸、羥基亞乙基二膦酸、乙二胺四亞甲基膦酸、二乙烯三胺五甲叉膦酸、2-膦酸丁烷-1,2,4三羧酸、己二胺四甲叉膦酸、雙1,6-亞己基三胺五甲叉膦酸、羥基膦?;宜峒捌潲}、有機(jī)膦磺酸及其鹽,可一種或者多種組合使用。其中,羥基膦?;宜猁}類和有機(jī)膦磺酸鹽類優(yōu)選氨鹽、鉀鹽。所述有機(jī)磷酸 類化合物的濃度為質(zhì)量百分比0.005-1%,優(yōu)選為質(zhì)量百分比0.01-0.5%。其中,所述陰離子表面活性劑為磺酸鹽類、硫酸鹽類和羧酸鹽類陰離子表面活性劑中的一種或多種?;撬猁}類陰離子表面活性劑較佳為烷基磺酸鹽類、芳基磺酸鹽類。所述陰離子表面活性劑的親油基為c8~c18的脂肪醇、c8~c18的脂肪醇聚氧乙烯醚、c8~c12的烷基酚聚氧乙烯醚中的一種或多種,其中聚氧乙烯醚的重復(fù)單元數(shù)為3~25。其中,所述陰離子表面活性劑濃度為質(zhì)量百分比0.0005-0.5%,優(yōu)選為質(zhì)量百分比0.001-0.1%。本發(fā)明的清洗液,其中,所述非離子表面活性劑為聚氧乙烯型非離子表面活性劑,較佳為烷基聚氧乙烯醚,烷基酚聚氧乙烯醚,脂肪醇聚氧乙烯醚,脂肪酸聚氧乙烯酯,脂肪胺聚氧乙烯醚,脂肪酰胺聚氧乙烯醚及聚氧乙烯醚-聚氧丙烯醚共聚物中的一種或多種,更佳為辛基苯基聚氧乙烯醚,壬基酚聚氧乙烯醚,月桂醇聚氧乙烯醚,十八醇聚氧乙烯酯,十二胺聚氧乙烯醚,棕櫚酸單乙醇酰胺聚氧乙烯醚,蓖麻油聚氧乙烯醚,聚氧乙烯醚-聚氧丙烯醚共聚物。其中,所述非離子表面活性劑濃度為質(zhì)量百分比0.0005-0.5%,優(yōu)選為質(zhì)量百分比0.001-0.1%。本發(fā)明的清洗液ph值1-7,優(yōu)選為:1-3。本發(fā)明另一方面提供了一種清洗液在金屬襯底上的清洗用途,該清洗液可用在拋光結(jié)束后在拋光盤上清洗晶片,或者用于清洗機(jī)中清洗晶片。金屬襯底為鋁、銅、鉭、氮化鉭、鈷、鈦、氮化鈦、鎢、鎳、鎳-磷、鐵、銀、金中的一種或多種的組合。本發(fā)明的積極進(jìn)步效果在于:a)本發(fā)明的清洗液用于清洗拋光后的含金屬的晶片,可以去除拋光后晶片表面殘留的研磨顆粒、金屬離子及有機(jī)物殘留。降低金屬表面粗糙度,改善清洗后晶片表面的親水性,降低清洗后的表面缺陷。b)通過加入有機(jī)磷酸類化合物可以增加金屬表面殘留的金屬離子及金屬氧化物的去除。c)通過加入陰離子表面活性劑,可以改善去除有機(jī)物殘留的能力,降低 表面粗糙度,抑制金屬的腐蝕,并可增加研磨顆粒的去除能力。d)通過加入非離子表面活性劑,進(jìn)一步增加了對(duì)晶片表面殘留研磨顆粒的去除;并可進(jìn)一步改善晶片表面的親水性和清洗液的防腐蝕性能。附圖說明圖1為本發(fā)明的清洗液實(shí)施例10清洗后的銅圖形晶片掃描電鏡圖圖2為本發(fā)明的清洗液實(shí)施例10浸泡后的銅圖形晶片掃描電鏡圖具體實(shí)施方式下面通過具體實(shí)施例進(jìn)一步闡述本發(fā)明的優(yōu)點(diǎn),但本發(fā)明的保護(hù)范圍不僅僅局限于下述實(shí)施例。表1給出了本發(fā)明的清洗液的實(shí)施例和對(duì)比例,按表中所給配方,將所有組分溶解混合均勻,用水補(bǔ)足質(zhì)量百分比至100%。用koh或hno3調(diào)節(jié)到所需要的ph值。表1本發(fā)明實(shí)施例及對(duì)比實(shí)施例的組分和含量為了考察該類清洗液的清洗情況,本發(fā)明采用了如下技術(shù)手段:晶片表面粗糙度的測(cè)定:利用xe-300p原子力顯微鏡測(cè)定用清洗液清洗和浸泡后的銅晶片表面粗糙度ra。金屬離子的去除能力測(cè)試:將空白的二氧化硅晶片浸入200毫升濃度為c0的銅離子溶液中,浸泡30分鐘后取出,用同樣體積的清洗液洗滌晶片3次,并將洗液與銅離子溶液收集在一起(共800毫升),利用icp測(cè)定洗液中銅離子的濃度并乘以4為c1,c1/c0越接近于1,金屬離子的去除能力越強(qiáng)。清洗液清洗后金屬表面親水性測(cè)試:在清洗劑內(nèi)用清洗液刷洗銅晶片表面1分鐘,然后用水刷洗1分鐘,氮?dú)飧稍锖?,測(cè)定水在晶片表面的接觸角,接觸角越小則晶片表面越親水,晶片表面更容易被清洗,表面缺陷越少。金屬氧化物的溶解能力:在清洗液液中加入0.1%氧化銅顆粒,攪拌30min取樣離心,取出上層清液。利用icp測(cè)定上層清液中銅離子的含量。 含量越高,清洗液溶解金屬氧化物的能力越強(qiáng)。研磨顆粒的去除能力:將二氧化硅研磨顆粒加入清洗液中測(cè)定研磨顆粒在溶液的zeta電位,zeta電位的絕對(duì)值|ξ|越低,研磨顆粒越容易團(tuán)聚,在清洗過程中易被清洗刷帶走而不易吸附在晶片表面,清洗液對(duì)研磨顆粒的去除能力越強(qiáng)。表2給出了具體實(shí)施例及對(duì)比例在研磨顆粒的去除能力、金屬氧化物溶解能力,銅晶片表面的親水性,清洗后銅晶片表面的粗糙度的數(shù)據(jù)。表2對(duì)比實(shí)施例和部分實(shí)施例的清洗能力及清洗后晶片表面的理化性質(zhì)從表2可以看出,從對(duì)比例1~6和實(shí)施例可以看出有機(jī)磷酸類化合物的使用增加了溶液溶解金屬氧化物的能力和晶片表面金屬離子去除的能力,降低了研磨顆粒的表面zeta電位。而陰離子表面活性劑和非離子表面活性劑的加入,進(jìn)一步降低了研磨顆粒的zeta電位,一方面使得研磨顆粒本身更容易聚集,另一方面降低了與晶片表面的相互作用,更容易在清洗過程中被去除。同時(shí)非離子表面活性劑也更進(jìn)一步改善了晶片表面的親水性有利于晶片的清洗,降低了清洗后晶片表面的粗糙度,增加了清洗液對(duì)晶片表面殘留研磨顆粒的去除。從對(duì)比例5和實(shí)施例10可以得出非離子表面活性劑的加入對(duì)金屬氧化物以及金屬離子的去除沒有明顯的影響。效果實(shí)施例2將拋光后的銅圖形芯片在0.02%的苯并三氮唑(bta)溶液中浸泡1分鐘,取出后用本發(fā)明的清洗液清洗,將清洗后的圖形芯片用complus缺陷掃描儀進(jìn)行掃描測(cè)試有機(jī)物苯并三氮唑的殘留結(jié)果見表3。拋光工藝條件:拋光機(jī)臺(tái)為8”mirra,拋光盤及拋光頭轉(zhuǎn)速93/87rpm,拋光液流速150ml/min,銅拋光所用拋光墊為ic1010,阻擋層拋光所用拋光墊為fujiboh7000。銅拋光液為安集公司產(chǎn)品aepu3000,阻擋層拋光液為安集公司產(chǎn)品anjitcu2000h4。表3對(duì)比例和部分實(shí)施例的bta去除情況實(shí)施例bta殘留對(duì)比例1很多(++++)對(duì)比例2較多(+++)對(duì)比例3多(++)對(duì)比例5無(-)對(duì)比例6少(+)實(shí)施例2無(-)實(shí)施例3無(-)實(shí)施例10無(-)實(shí)施例11無(-)+:有bta殘留,-:無bta殘留表3中,對(duì)比例2和3的bta去除結(jié)果比較,可以看出:在有機(jī)酸中單獨(dú)添加有機(jī)磷酸類化合物和陰離子表面活性劑均能增強(qiáng)溶液去除bta的能力但去除不完全。對(duì)比例6的bta去除結(jié)果表明,陰離子表面活性劑含量較低時(shí),不能完全去除bta。而根據(jù)實(shí)施例3的bta去除結(jié)果表明:以對(duì)比例6的基礎(chǔ),加入非離子表面活性劑后,增強(qiáng)了溶液去除bta的能力,就能有效地去除bta。效果實(shí)施例3將本發(fā)明的清洗液10清洗拋光后的銅圖形晶片并將清洗后的圖形晶片 在清洗液中浸泡30分鐘,取出后用清洗液清洗、干燥后用掃描電子顯微鏡觀察銅線表面的狀況,見圖1和2。拋光工藝條件:拋光機(jī)臺(tái)為8”mirra,拋光盤及拋光頭轉(zhuǎn)速93/87rpm,拋光液流速150ml/min,銅拋光所用拋光墊為ic1010,阻擋層拋光所用拋光墊為fujiboh7000。銅拋光液為安集公司產(chǎn)品aepu3000,阻擋層拋光液為安集公司產(chǎn)品anjitcu2000h4。從圖1和2可見,用本發(fā)明的清洗液清洗后的銅圖形晶片表面無污染,無研磨顆粒殘留,無腐蝕等缺陷。用清洗液浸泡后的銅圖形晶片的銅線邊緣清晰、銅線無腐蝕。綜上所述,本發(fā)明的積極進(jìn)步效果在于:本發(fā)明的清洗液可以去除拋光后晶片表面殘留的研磨顆粒、金屬離子等殘留。降低金屬表面粗燥度,改善清洗后晶片表面的親水性,降低清洗后的表面缺陷,并且可以防止晶片在等待下一步工序的過程中可能產(chǎn)生的金屬腐蝕。應(yīng)當(dāng)理解的是,本發(fā)明所述wt%均指的是質(zhì)量百分含量。以上對(duì)本發(fā)明的具體實(shí)施例進(jìn)行了詳細(xì)描述,但其只是作為范例,本發(fā)明并不限制于以上描述的具體實(shí)施例。對(duì)于本領(lǐng)域技術(shù)人員而言,任何對(duì)本發(fā)明進(jìn)行的等同修改和替代也都在本發(fā)明的范疇之中。因此,在不脫離本發(fā)明的精神和范圍下所作的均等變換和修改,都應(yīng)涵蓋在本發(fā)明的范圍內(nèi)。當(dāng)前第1頁12