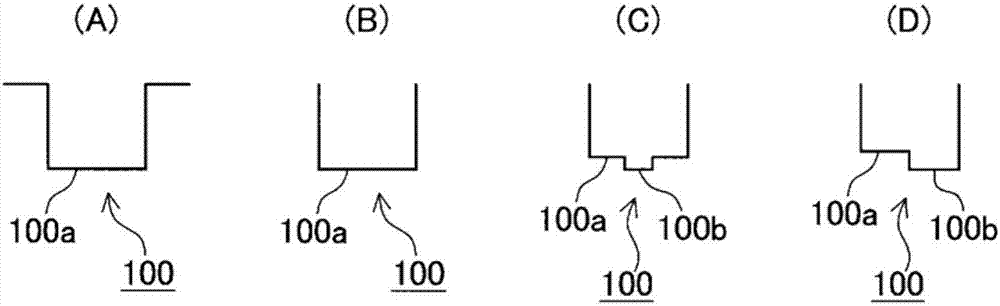
本申請是申請日為2014年8月6日、申請?zhí)枮?01480050350.7(國際申請?zhí)枮閜ct/jp2014/070682)、發(fā)明名稱為“壓制成型品和壓制成型品的制造方法以及壓制成型品的制造裝置”的申請的分案申請。本發(fā)明涉及適合用于例如汽車車身用加強(qiáng)構(gòu)件的、剛度和強(qiáng)度優(yōu)良的壓制成型品和壓制成型品的制造方法以及用于制造這樣的壓制成型品的制造裝置。
背景技術(shù):
:汽車車身構(gòu)成為箱體,該箱體是通過將許多成型板彼此的緣部彼此重疊起來并通過例如電阻點(diǎn)焊進(jìn)行接合而得到的。在該箱體的主要部位通過例如電阻點(diǎn)焊接合有加強(qiáng)構(gòu)件、強(qiáng)度構(gòu)件(以下,統(tǒng)稱為“加強(qiáng)構(gòu)件”)。作為該汽車車身用加強(qiáng)構(gòu)件,存在保險杠加強(qiáng)件、車門檻(側(cè)梁)、車身腰線、橫梁、縱梁等。所述加強(qiáng)構(gòu)件是通過例如壓制成型而得到的構(gòu)件,具有由頂板、與頂板相連的兩條棱線以及分別與兩條棱線相連的兩個凸緣形成的大致帽型或大致槽型的截面形狀。在該加強(qiáng)構(gòu)件的棱線延伸方向上的開口的端部,通過向內(nèi)或向外彎折而形成有凸緣。在使該凸緣與其他構(gòu)件重疊之后,通過例如電阻點(diǎn)焊進(jìn)行接合,從而組裝汽車車身用加強(qiáng)構(gòu)件。根據(jù)原材料的板厚,有時不使用點(diǎn)焊而是使用電弧焊。在此,在本說明書中,將加強(qiáng)構(gòu)件的端部彎折向分別與棱線的兩端相連的兩個面所成的角度小于180°的區(qū)域側(cè)而得到的凸緣稱作向內(nèi)凸緣。并且,將加強(qiáng)構(gòu)件的端部彎折向分別與棱線的兩端相連的兩個面所成的角度超過180°的區(qū)域側(cè)而得到的凸緣稱作向外凸緣。在加強(qiáng)構(gòu)件的端部形成向內(nèi)凸緣的情況下,位于棱線的延長線上的棱線部凸緣成型為壓縮凸緣,因此在棱線部凸緣產(chǎn)生褶皺。因此,在想要使這樣的向內(nèi)凸緣與其他構(gòu)件重疊并進(jìn)行點(diǎn)焊時,有可能因產(chǎn)生的褶皺而與其他構(gòu)件之間產(chǎn)生間隙,導(dǎo)致在組裝時產(chǎn)生問題。因而,在使用端部具有向內(nèi)凸緣的加強(qiáng)構(gòu)件的情況下,不得不在棱線部凸緣設(shè)置缺口等以避免產(chǎn)生褶皺,并且將向內(nèi)凸緣作為接合材料進(jìn)行與其他構(gòu)件之間的焊接。然而,若在形成為朝向內(nèi)側(cè)的棱線部凸緣設(shè)置使凸緣不連續(xù)那樣的缺口,則會不可避免地導(dǎo)致扭轉(zhuǎn)剛度、載荷傳遞特性這樣的汽車車身用加強(qiáng)構(gòu)件的性能降低。因而,為了借助向內(nèi)凸緣使加強(qiáng)構(gòu)件與其他構(gòu)件接合并確保加強(qiáng)構(gòu)件被要求的性能,需要在不在向內(nèi)凸緣設(shè)置缺口的前提下抑制在棱線部凸緣產(chǎn)生的褶皺,并且實(shí)現(xiàn)壓縮凸緣部的成型。其中,在本說明書中,“在凸緣設(shè)置缺口”是指,缺口設(shè)于凸緣的整個寬度方向上,而使凸緣不連續(xù)。另外,凸緣的寬度與凸緣的高度以相同的意思使用。因而,將凸緣的寬度局部減小而殘留有一部分凸緣的情況視為在凸緣未設(shè)置缺口。以往也提出有一種抑制在這樣的壓縮凸緣成型時產(chǎn)生褶皺的技術(shù)。例如,在專利文獻(xiàn)1中公開了這樣的技術(shù):在具有遮陽頂棚用開口的頂板形成用于吸收壓縮凸緣部的基部與頂端部的長度差的凹凸形狀。另外,在專利文獻(xiàn)2中公開了這樣的技術(shù):在方筒拉深成型的壓縮凸緣部設(shè)置特定的拉深筋,從而防止產(chǎn)生褶皺。而且,在專利文獻(xiàn)3中公開了這樣的技術(shù):利用凸輪構(gòu)造對壓縮凸緣部施加按壓壓力而進(jìn)行成型,從而抑制褶皺產(chǎn)生。另外,在專利文獻(xiàn)4中公開了一種板體的成型方法,在該方法中,針對應(yīng)該成為彎曲部的部位,形成沿著與彎曲載荷方向交叉的方向延伸的凸緣相當(dāng)部,之后對該凸緣相當(dāng)部進(jìn)行拉延加工使其轉(zhuǎn)換為凸緣并定形。該板體的成型方法能抑制凸緣處的褶皺所導(dǎo)致的撕裂。此外,在專利文獻(xiàn)5中公開了一種金屬面材的加工方法,在該方法中,彎折金屬面材,并且將兩側(cè)部的立起部向外側(cè)放倒,之后利用接收模具的側(cè)面的按壓面的加工輥強(qiáng)壓被放倒的兩側(cè)部并使它們依次立起。該加工方法能減少立起部的褶皺、變形?,F(xiàn)有技術(shù)文獻(xiàn)專利文獻(xiàn)專利文獻(xiàn)1:日本特許第2554768號說明書專利文獻(xiàn)2:日本特許第2560416號說明書專利文獻(xiàn)3:日本特開平4-118118號公報專利文獻(xiàn)4:日本特開昭59-144530號公報專利文獻(xiàn)5:日本特開平1-104420號公報技術(shù)實(shí)現(xiàn)要素:發(fā)明要解決的問題專利文獻(xiàn)1、2所公開的技術(shù)是利用預(yù)先形成的余量部分吸收會成為產(chǎn)生褶皺和飛邊的主要原因的剩余線長(日文原文:余剰線長)的技術(shù)。因而,難以利用該余量部分進(jìn)行點(diǎn)焊的情況當(dāng)然不用說,還存在該余量部分妨礙其他部位的點(diǎn)焊的情況。在這樣的情況下,難以實(shí)施專利文獻(xiàn)1、2所公開的技術(shù)。另外,專利文獻(xiàn)3所公開的技術(shù)能夠抑制凸緣部的壓縮率和凸輪構(gòu)造所承受的反作用力較小那樣的具有例如曲率半徑為2100mm這樣的較大的曲率半徑的部位的凸緣部產(chǎn)生褶皺。但是,難以抑制凸緣部的壓縮率和凸輪構(gòu)造所承受的反作用力較大那樣的具有例如曲率半徑為5mm這樣的較小的曲率半徑的部位的凸緣部產(chǎn)生褶皺。特別是,在使用拉伸強(qiáng)度較大的高強(qiáng)度鋼板的情況下,產(chǎn)生過大的褶皺,因此來自凸緣部的反作用力較大。因此,利用專利文獻(xiàn)3所公開的凸輪構(gòu)造無法抑制褶皺的產(chǎn)生。另外,專利文獻(xiàn)4所公開的技術(shù)是通過拉延加工抑制褶皺產(chǎn)生的技術(shù)。因而,形成的凸緣的板厚變薄,有可能導(dǎo)致加強(qiáng)構(gòu)件的剛度、凸緣部的強(qiáng)度降低。另外,專利文獻(xiàn)5所公開的技術(shù)是使多個加工輥依次進(jìn)行強(qiáng)壓而形成立起部的技術(shù),以金屬面材的彎折的部分的曲率半徑比較大的加工品為對象。因而,難以抑制具有例如曲率半徑為5mm這樣的較小的曲率半徑的部位的凸緣部產(chǎn)生褶皺。像這樣,從壓制成型性的觀點(diǎn)而言,難以在具有大致帽型或大致槽型等的截面形狀的構(gòu)件中的棱線部延伸方向上的開口的端部以不設(shè)置缺口的方式形成向內(nèi)凸緣。特別是,所述引用文獻(xiàn)1~5都不是著眼于在拉伸強(qiáng)度為340mpa以上的高強(qiáng)度鋼板形成凸緣的文獻(xiàn)。因此,迄今為止,從未將具有在棱線部凸緣不存在缺口的連續(xù)的向內(nèi)凸緣的、由高強(qiáng)度鋼板形成的壓制成型體用作汽車車身用加強(qiáng)構(gòu)件。對于具有向外凸緣的壓制成型品,與具有向外凸緣相應(yīng)地,無法將帽狀截面或槽狀截面擴(kuò)大至整個設(shè)計截面。換言之,如果能夠代替向外凸緣而是借助向內(nèi)凸緣進(jìn)行與其他構(gòu)件之間的接合,則與沒有向外凸緣相應(yīng)地,能夠?qū)褐瞥尚推返慕孛鏀U(kuò)大至整個設(shè)計截面。因此,能夠提高汽車車身用加強(qiáng)構(gòu)件與其他構(gòu)件之間的接合強(qiáng)度、汽車車身的彎曲剛度或者扭轉(zhuǎn)剛度。因而,期望實(shí)現(xiàn)一種由高強(qiáng)度鋼板形成的具有向內(nèi)凸緣的壓制成型品。本發(fā)明的目的在于提供一種如下這樣的壓制成型品:不用為了避免在壓制成型時可能產(chǎn)生的不良而在棱線部凸緣設(shè)置缺口,能夠提高加強(qiáng)構(gòu)件與其他構(gòu)件之間的接合強(qiáng)度、汽車車身的剛度等性能,具有不存在缺口的向內(nèi)連續(xù)凸緣。并且,本發(fā)明的目的還在于提供一種這樣的壓制成型品的制造方法以及壓制成型品的制造裝置。用于解決問題的方案為了解決所述問題,根據(jù)本發(fā)明的某一技術(shù)方案提供一種壓制成型品,該壓制成型品是金屬板的壓制成型品,由拉伸強(qiáng)度為340mpa以上的鋼板形成,包括以沿著規(guī)定方向延伸的方式形成的棱線部以及以分別自構(gòu)成所述棱線部的棱線的兩端延伸的方式形成的第1面部和第2面部,其中,該壓制成型品在所述規(guī)定方向上的至少一端部具有由棱線部凸緣、第1凸緣和第2凸緣相連續(xù)而形成的向內(nèi)連續(xù)凸緣,該棱線部凸緣以朝向內(nèi)側(cè)的方式形成于所述棱線部的所述端部,該第1凸緣以朝向內(nèi)側(cè)的方式形成于所述第1面部的所述端部的至少一部分區(qū)域,該第2凸緣以朝向內(nèi)側(cè)的方式形成于所述第2面部的所述端部的至少一部分區(qū)域,所述棱線部凸緣的凸緣寬度lf、所述棱線部的曲率半徑rf以及所述第1面部與所述第2面部所成的角度θ滿足下述式(1):lf≤0.22×rf+0.13×θ-5.9…(1)(其中,0mm≤rf≤35mm,并且,90°≤θ≤145°)。并且,也可以是,所述棱線部凸緣的至少一部分的凸緣寬度小于所述第1凸緣和所述第2凸緣這兩者各自的至少一部分的凸緣寬度。并且,也可以是,所述壓制成型品的沿著所述規(guī)定方向看到的截面形狀是閉合截面形狀,或者是帽型或槽形的開放截面形狀。并且,也可以是,所述壓制成型品為汽車車身用加強(qiáng)構(gòu)件。并且,也可以是,至少所述棱線部凸緣的寬度方向上的緣部區(qū)域的板厚為壓制成型前的板厚以上。并且,也可以是,至少所述棱線部凸緣的寬度方向上的緣部區(qū)域的板厚為壓制成型前的板厚的1.5倍以下。并且,為了解決所述問題,根據(jù)本發(fā)明的另一技術(shù)方案提供一種壓制成型品的制造方法,其中,該壓制成型品的制造方法包括第1中間成型工序和第1壓制成型工序,在該第1中間成型工序中,對由拉伸強(qiáng)度為340mpa以上的鋼板形成的坯料的規(guī)定方向上的至少一端部進(jìn)行彎折,將所述坯料成型為具有凸緣的第1中間構(gòu)件,在該第1壓制成型工序中,將所述凸緣夾持在規(guī)定的第1間隙內(nèi),同時對所述第1中間構(gòu)件進(jìn)行壓制成型,從而使所述第1中間構(gòu)件沿著所述規(guī)定方向彎折,從而成型以沿著所述規(guī)定方向延伸的方式形成的棱線部以及以分別自構(gòu)成所述棱線部的棱線的兩端延伸的方式形成的第1面部和第2面部,并且將所述凸緣成型為由棱線部凸緣、第1凸緣和第2凸緣相連續(xù)而形成的向內(nèi)連續(xù)凸緣,該棱線部凸緣以朝向內(nèi)側(cè)的方式形成于所述棱線部的所述端部,該第1凸緣以朝向內(nèi)側(cè)的方式形成于所述第1面部的所述端部的至少一部分區(qū)域,該第2凸緣以朝向內(nèi)側(cè)的方式形成于所述第2面部的所述端部的至少一部分區(qū)域。并且,也可以是,在所述第1壓制成型工序中,使用壓制成型模具,該壓制成型模具包括:沖模;沖頭,其與所述沖模相對地配置;以及面外變形抑制工具,其在所述壓制成型時與所述沖頭的側(cè)面相對地配置,用于抑制所述凸緣發(fā)生面外變形,將所述第1中間構(gòu)件配置在所述沖頭上,并且將所述凸緣夾持在由所述沖頭的側(cè)面和所述面外變形抑制工具形成的所述第1間隙內(nèi),同時利用所述沖模和所述沖頭對所述第1中間構(gòu)件進(jìn)行壓制成型。并且,也可以是,墊板用于按壓所述第1中間構(gòu)件,所述沖模以所述墊板在按壓方向上移動自如的方式支承該墊板。并且,也可以是,在所述第1壓制成型工序中,作為所述壓制成型模具,使用還包括與所述沖模相對的坯料保持件(日文原文:ブランクホルダ)的壓制成型模具,利用所述沖模和所述坯料保持件約束所述第1中間構(gòu)件的一部分,同時對該第1中間構(gòu)件進(jìn)行拉深成型。并且,也可以是,所述壓制成型模具的所述沖頭以內(nèi)墊板在合模方向上移動自如的方式支承該內(nèi)墊板,該內(nèi)墊板能與所述第1中間構(gòu)件的一表面抵接,在所述第1壓制成型工序中,將所述凸緣夾持在由所述沖頭的側(cè)面、所述內(nèi)墊板的側(cè)面與所述面外變形抑制工具形成的所述第1間隙內(nèi),同時利用所述沖模與所述沖頭、所述內(nèi)墊板對所述第1中間構(gòu)件進(jìn)行壓制成型。并且,根據(jù)本發(fā)明的又另一技術(shù)方案提供一種壓制成型品的制造方法,其中,該壓制成型品的制造方法包括第1中間成型工序、第2中間成型工序和第2壓制成型工序在該第1中間成型工序中,對由拉伸強(qiáng)度為340mpa以上的鋼板形成的坯料的規(guī)定方向上的至少一端部進(jìn)行彎折,將所述坯料成型為具有凸緣的第1中間構(gòu)件,在該第2中間成型工序中,將所述凸緣夾持在規(guī)定的第1間隙內(nèi),同時對所述第1中間構(gòu)件進(jìn)行壓制成型,從而使所述第1中間構(gòu)件沿著所述規(guī)定方向彎折,從而形成以沿著所述規(guī)定方向延伸的方式形成的中間棱線部以及以分別自構(gòu)成所述中間棱線部的棱線的兩端延伸的方式形成的第1中間面部和第2中間面部,并且將所述凸緣成型為由中間棱線部凸緣、第1中間凸緣和第2中間凸緣相連續(xù)而形成的中間連續(xù)凸緣,該中間棱線部凸緣形成于所述中間棱線部的所述端部,該第1中間凸緣形成于所述第1中間面部的所述端部的至少一部分區(qū)域,該第2中間凸緣形成于所述第2中間面部的所述端部的至少一部分區(qū)域,從而將所述第1中間構(gòu)件成型為第2中間構(gòu)件,在該第2壓制成型工序中,將所述中間連續(xù)凸緣夾持在規(guī)定的第2間隙內(nèi),同時使在所述第2中間構(gòu)件形成的所述第1中間面部和所述第2中間面部中的至少一者沿著所述規(guī)定方向進(jìn)一步彎折,從而成型以沿著所述規(guī)定方向延伸的方式形成的棱線部以及以分別自構(gòu)成所述棱線部的棱線的兩端延伸的方式形成的第1面部和第2面部,并且將所述中間連續(xù)凸緣成型為由棱線部凸緣、第1凸緣和第2凸緣相連續(xù)而形成的向內(nèi)連續(xù)凸緣,該棱線部凸緣以朝向內(nèi)側(cè)的方式形成于所述棱線部的所述端部,該第1凸緣以朝向內(nèi)側(cè)的方式形成于所述第1面部的所述端部的至少一部分區(qū)域,該第2凸緣以朝向內(nèi)側(cè)的方式形成于所述第2面部的所述端部的至少一部分區(qū)域。并且,也可以是,在所述第2中間成型工序中,使用壓制成型模具,該壓制成型模具包括:沖模;沖頭,其與所述沖模相對地配置;以及面外變形抑制工具,其在所述壓制成型時與所述沖頭的側(cè)面相對地配置,用于抑制所述凸緣發(fā)生面外變形,將所述第1中間構(gòu)件配置在所述沖頭上,并且將所述凸緣夾持在由所述沖頭的側(cè)面和所述面外變形抑制工具形成的所述第1間隙內(nèi),同時利用所述沖模和所述沖頭對所述第1中間構(gòu)件進(jìn)行壓制成型。并且,也可以是,在所述第2中間成型工序中,作為所述壓制成型模具,使用還包括與所述沖模相對的坯料保持件的壓制成型模具,利用所述沖模和所述坯料保持件約束所述第1中間構(gòu)件的一部分,同時對該第1中間構(gòu)件進(jìn)行拉深成型。并且,也可以是,所述壓制成型模具的所述沖頭以內(nèi)墊板在合模方向上移動自如的方式支承該內(nèi)墊板,該內(nèi)墊板能與所述第1中間構(gòu)件的一表面抵接,在所述第2中間成型工序中,將所述凸緣夾持在由所述沖頭的側(cè)面、所述內(nèi)墊板的側(cè)面與所述面外變形抑制工具形成的所述第1間隙內(nèi),同時利用所述沖模與所述沖頭、所述內(nèi)墊板對所述第1中間構(gòu)件進(jìn)行壓制成型。并且,也可以是,在所述第2壓制成型工序中,使用壓制成型模具,該壓制成型模具包括:沖模;沖頭,其與所述沖模相對地配置;以及面外變形抑制工具,其在所述壓制成型時與所述沖頭的側(cè)面相對地配置,用于抑制所述凸緣發(fā)生面外變形,將所述第2中間構(gòu)件配置在所述沖頭上,并且將所述中間連續(xù)凸緣夾持在由所述沖頭的側(cè)面和所述面外變形抑制工具形成的所述第2間隙內(nèi),同時利用所述沖模和所述沖頭對所述第2中間構(gòu)件進(jìn)行壓制成型。并且,也可以是,墊板用于按壓所述第1中間構(gòu)件,所述沖模以所述墊板在按壓方向上移動自如的方式支承該墊板。并且,也可以是,所述第1間隙的距離x滿足下述式(2):1.00×t≤x<1.40×t…(2)t:坯料的板厚(mm)x:間隙的距離(mm)。并且,為了解決所述問題,根據(jù)本發(fā)明的又另一技術(shù)方案提供一種壓制成型品的制造裝置,該壓制成型品的制造裝置用于制造壓制成型品,該壓制成型品具有以沿著規(guī)定方向延伸的方式形成的棱線部以及以分別自構(gòu)成所述棱線部的棱線的兩端延伸的方式形成的第1面部和第2面部,并且,該壓制成型品在所述規(guī)定方向上的至少一端部具有由棱線部凸緣、第1凸緣和第2凸緣相連續(xù)而形成的向內(nèi)連續(xù)凸緣,該棱線部凸緣以朝向內(nèi)側(cè)的方式形成于所述棱線部的所述端部,該第1凸緣以朝向內(nèi)側(cè)的方式形成于所述第1面部的所述端部的至少一部分區(qū)域,該第2凸緣以朝向內(nèi)側(cè)的方式形成于所述第2面部的所述端部的至少一部分區(qū)域,其中,該壓制成型品的制造裝置包括:沖頭,其能與在所述規(guī)定方向上的至少一端部具有凸緣的中間構(gòu)件的一表面抵接;沖模,其與所述沖頭相對地配置;以及面外變形抑制工具,在對所述中間構(gòu)件進(jìn)行壓制成型時,該面外變形抑制工具與所述沖頭的側(cè)面相對地配置,并且該面外變形抑制工具以與所述沖頭的側(cè)面之間設(shè)有能夠夾持所述凸緣的規(guī)定間隙的方式配置,用于抑制所述凸緣發(fā)生面外變形。并且,也可以是,所述沖頭的側(cè)面與所述面外變形抑制工具之間的所述間隙的距離x滿足下述式(2):1.00×t≤x<1.40×t…(2)t:坯料的板厚(mm)x:間隙的距離(mm)。并且,也可以是,所述沖模具有墊板,該墊板被支承為在合模方向上移動自如,能與所述中間構(gòu)件的另一表面抵接。并且,也可以是,所述沖頭具有內(nèi)墊板,該內(nèi)墊板被支承為在合模方向上移動自如,能與所述中間構(gòu)件的所述一表面抵接,在對所述中間構(gòu)件進(jìn)行壓制成型時,所述面外變形抑制工具與所述沖頭的側(cè)面和所述內(nèi)墊板的側(cè)面相對地配置,并且所述面外變形抑制工具以與所述沖頭的側(cè)面和所述內(nèi)墊板的側(cè)面之間設(shè)有能夠夾持所述凸緣的規(guī)定間隙的方式配置。并且,也可以是,壓制成型品的制造裝置在所述壓制成型的過程中對所述中間構(gòu)件進(jìn)行彎曲成型。并且,也可以是,壓制成型品的制造裝置還包括與所述沖模相對的坯料保持件,在所述壓制成型的過程中,利用所述沖模和所述坯料保持件約束所述中間構(gòu)件,同時對所述中間構(gòu)件進(jìn)行拉深成型。發(fā)明的效果采用本發(fā)明,在由鋼板形成的壓制成型品的情況下,不用為了避免在壓制成型時可能產(chǎn)生的不良而在棱線部凸緣設(shè)置缺口,能夠抑制在向內(nèi)連續(xù)凸緣處產(chǎn)生褶皺。因而,若將這樣的壓制成型品應(yīng)用于汽車車身用加強(qiáng)構(gòu)件,則能夠提高加強(qiáng)構(gòu)件與其他構(gòu)件之間的接合強(qiáng)度、汽車車身的剛度等性能。附圖說明圖1的(a)是示意性地表示本發(fā)明的第1實(shí)施方式的具有帽型的截面形狀的壓制成型品的說明圖,圖1的(b)是圖1的(a)的a向視圖,圖1的(c)是圖1的(a)的b向視圖。圖2是表示該實(shí)施方式的壓制成型品的截面形狀的一例子的說明圖。圖3的(a)和圖3的(b)是示意性地表示在第2實(shí)施方式的壓制成型品的制造方法中自坯料壓制成型為第1中間構(gòu)件的情況的說明圖,圖3的(a)表示將坯料設(shè)于壓制成型裝置的情況,圖3的(b)表示壓制成型結(jié)束時的情況。圖4是示意性地表示用于拉深成型的壓制成型裝置的結(jié)構(gòu)例的概略圖。圖5是示意性地表示在該實(shí)施方式的壓制成型品的制造方法中通過使用拉深成型裝置的拉深成型自第1中間構(gòu)件得到壓制成型品的情況的說明圖。圖6是示意性地表示在該實(shí)施方式的壓制成型品的制造方法中通過內(nèi)墊板拉深成型自第1中間構(gòu)件得到壓制成型品的狀況的說明圖。圖7是在成型中途示意性地表示將要成型為棱線部的部分的曲率半徑的說明圖,圖7的(a)表示拉深成型的情況,圖7的(b)表示內(nèi)墊板拉深成型的情況。圖8是示意性地表示在該實(shí)施方式的壓制成型品的制造方法中代替拉深成型而是通過彎曲成型自第1中間構(gòu)件得到壓制成型品的情況的說明圖。圖9的(a)是示意性地表示拉深成型裝置的結(jié)構(gòu)例的說明圖,圖9的(b)是表示通過該拉深成型得到的第2中間構(gòu)件的外觀例的照片。圖10是示意性地表示在第3實(shí)施方式的壓制成型品的制造方法中通過基于拉深成型裝置的拉深成型自第1中間構(gòu)件得到第2中間構(gòu)件的情況的說明圖。圖11是示意性地表示在該實(shí)施方式的壓制成型品的制造方法中通過基于內(nèi)墊板拉深成型裝置的拉深成型自第1中間構(gòu)件得到第2中間構(gòu)件的狀況的說明圖。圖12的(a)是示意性地表示用于彎曲成型的壓制成型裝置的結(jié)構(gòu)例的說明圖,圖12的(b)是表示通過該彎曲成型得到的壓制成型品的外觀例的照片。圖13是示意性地表示在該實(shí)施方式的壓制成型品的制造方法中自第2中間構(gòu)件得到壓制成型品的情況的說明圖。圖14是得到的壓制成型品的棱線部凸緣附近的外觀照片,圖14的(a)表示利用面外變形抑制工具并將面外變形抑制工具與沖頭的側(cè)面之間的間隔設(shè)為1.33mm的情況,圖14的(b)表示利用面外變形抑制工具并將面外變形抑制工具與沖頭的側(cè)面之間的間隔設(shè)為1.41mm的情況,圖14的(c)表示沒有使用面外變形工具的情況。圖15是表示在作為彎曲成型的第1中間工序之后分別通過拉深成型、內(nèi)墊板拉深成型和彎曲成型實(shí)施第1壓制成型工序而制造出的壓制成型品的棱線部凸緣的緣部的板厚增大率的分布的曲線圖。圖16是表示由凸緣寬度lf、棱線部的曲率半徑rf以及第1面部與第2面部所成的角度θ確定的褶皺產(chǎn)生狀況的曲線圖。具體實(shí)施方式以下,參照附圖詳細(xì)地說明本發(fā)明的優(yōu)選的實(shí)施方式。其中,在本說明書和附圖中,對實(shí)質(zhì)上具有同一功能結(jié)構(gòu)的構(gòu)成部件標(biāo)注同一附圖標(biāo)記,從而省略重復(fù)說明。<1.第1實(shí)施方式>首先,說明本發(fā)明的第1實(shí)施方式的壓制成型品。(1-1.整體結(jié)構(gòu))本實(shí)施方式的壓制成型品100是通過對鋼板進(jìn)行壓制成型而得到的成型品。該壓制成型品100適合用于例如保險杠加強(qiáng)件、車門檻(側(cè)梁)、車身腰線、橫梁等汽車車身用加強(qiáng)構(gòu)件。用于這樣的用途的壓制成型品100也可以是利用拉伸強(qiáng)度為340mpa以上、優(yōu)選為590mpa以上的高強(qiáng)度鋼板進(jìn)行壓制成型而得到的成型品。拉伸強(qiáng)度是通過基于jisz2241的拉伸試驗(yàn)測量到的值。另外,由鋼板形成的坯料的板厚可以設(shè)在例如0.8mm~2.0mm的范圍內(nèi)。圖1的(a)是示意性地表示本實(shí)施方式的壓制成型品100的立體圖。另外,圖1的(b)是圖1的(a)的a向視圖(棱線部凸緣115a的主視圖)。圖1的(c)是圖1的(a)的b向視圖(棱線部凸緣115a的立體圖)。在本實(shí)施方式中,壓制成型品100或坯料的長度方向與壓制成型品100的棱線部112a、112b的延伸方向相當(dāng),但棱線部112a、112b的延伸方向并不限定于壓制成型品100的長度方向。其中,在本實(shí)施方式中,棱線部112a、112b所延伸的規(guī)定方向并不限定于被識別為直線的方向。在眾多汽車車身用加強(qiáng)構(gòu)件中能夠看到的程度的、被識別為除直線以外的彎曲形狀(曲線)的方向也包含在規(guī)定方向內(nèi)。在規(guī)定方向被識別為曲線的情況下,該規(guī)定方向還包括例如向加強(qiáng)構(gòu)件的左右方向彎曲的方向、向上下方向彎曲的方向或者將這些方向組合而成的方向。并且,規(guī)定方向上的全長包括從例如保險杠、縱梁那樣的1000mm左右的長度到立方體狀的隔板那樣的100mm左右的長度為止的全部長度。圖2是表示壓制成型品100的與其長度方向正交的截面處的截面形狀的一例子的說明圖。本實(shí)施方式的壓制成型品100的截面形狀能夠設(shè)為圖2的(a)所示的帽型的截面形狀、圖2的(b)所示的槽型的截面形狀,但并不限定于此。如圖2的(c)、圖2的(d)所示,壓制成型品100的截面形狀也包括對帽型、槽型的截面形狀的壁面100a賦予各種凸形狀100b、凹形狀(未圖示)而成的截面形狀。另外,壓制成型品100的截面形狀除包括圖2的(a)~圖2的(d)所示那樣的開放截面形狀以外,還包括例如大致日文片假名“ロ”字型等閉合截面形狀。而且,壓制成型品100并不限定于是這些截面形狀的壓制成型品,也可以是例如v字型截面形狀這樣的包括棱線部以及分別自構(gòu)成該棱線部的棱線的兩端延伸的第1面部和第2面部的截面形狀的壓制成型品。圖1的(a)所示的壓制成型品100是具有帽型的截面形狀的壓制成型品100。以下,以具有帽型的截面形狀的壓制成型品100為例進(jìn)行說明。如圖1的(a)所示,壓制成型品100包括棱線部112a、112b、第1面部113a、113b以及第2面部114。棱線部112a、112b均以沿著壓制成型品100的長度方向延伸的方式形成。一第1面部113a與棱線部112a相連,以沿著與壓制成型品100的長度方向交叉的第1方向延伸的方式形成。另一第1面部113b與棱線部112b相連,以沿著與壓制成型品100的長度方向交叉的第1方向延伸的方式形成。一第1面部113a延伸形成的第1方向與另一第1面部113b延伸形成的第1方向也可以不同。第2面部114與棱線部112a、112b相連,以沿著與壓制成型品100的長度方向交叉且與第1方向不同的第2方向延伸的方式形成。第2面部114形成在棱線部112a、112b之間。像這樣,壓制成型品100包括分別以沿著壓制成型品100的長度方向延伸的方式形成的棱線部112a、112b、以及與這些棱線部112a、112b相連續(xù)的第1面部113a、113b和第2面部114,具有大致帽型的開放截面形狀。為了將利用高強(qiáng)度鋼板成型的壓制成型品100應(yīng)用于例如汽車車身用加強(qiáng)構(gòu)件,優(yōu)選棱線部112a、112b的曲率半徑rf在0mm~35mm的范圍內(nèi)。棱線部的曲率半徑是指棱線部的內(nèi)表面的曲率半徑。并且,為了將壓制成型品100應(yīng)用于例如汽車車身用加強(qiáng)構(gòu)件,優(yōu)選第1面部113a與第2面部114所成的角度、第1面部113b與第2面部114所成的角度在90°~145°的范圍內(nèi)。(1-2.向內(nèi)連續(xù)凸緣)壓制成型品100在長度方向上的至少一最外端部100a具有棱線部凸緣115a、115b、第1凸緣116a、116b以及第2凸緣117。棱線部凸緣115a、115b形成于棱線部112a、112b的長度方向上的最外端部100a。第1凸緣116a、116b形成于第1面部113a、113b的長度方向上的最外端部100a的至少一部分區(qū)域。而且,第2凸緣117形成于第2面部114的長度方向上的最外端部100a的至少一部分區(qū)域。在本實(shí)施方式中,第1凸緣116a、116b和第2凸緣117分別形成在第1面部113a、113b和第2面部114的最外端部100a的整個區(qū)域。棱線部凸緣115a、115b、第1凸緣116a、116b和第2凸緣117均作為向內(nèi)凸緣連續(xù)地形成。這些棱線部凸緣115a、115b、第1凸緣116a、116b和第2凸緣117構(gòu)成向內(nèi)連續(xù)凸緣118。通過將設(shè)于壓制成型品100的端部的凸緣設(shè)為向內(nèi)連續(xù)凸緣118,能夠?qū)⒗缙囓嚿碛眉訌?qiáng)構(gòu)件的截面擴(kuò)大至整個設(shè)計截面。因而,能夠進(jìn)一步提高加強(qiáng)構(gòu)件與其他構(gòu)件之間的接合強(qiáng)度、汽車車身的剛度。本實(shí)施方式的壓制成型品100在長度方向上的最外端部100a具有在第1面部113a、113b、棱線部112a、112b和第2面部114的全長上連續(xù)的向內(nèi)連續(xù)凸緣118。其中,只要第1凸緣116a、116b、第2凸緣117分別與棱線部凸緣115a、115b連續(xù)地形成即可,向內(nèi)連續(xù)凸緣118也可以不在全長上連續(xù)。例如,第1凸緣116a、116b或第2凸緣117也可以形成于第1面部113a、113b或第2面部114的最外端部100a的一部分區(qū)域。在第2凸緣117未形成于第2面部114的整個區(qū)域的情況下,形成被分割成兩部分的向內(nèi)連續(xù)凸緣118。(1-3.棱線部凸緣)本實(shí)施方式的壓制成型品100在棱線部凸緣115a、115b具有使凸緣寬度減小而得到的凹部119。由此,棱線部凸緣115a、115b的寬度lf在棱線部112a、112b的頂點(diǎn)處小于第1凸緣116a、116b、第2凸緣117各自的寬度lfs1、lfs2。凸緣的寬度是指,除在凸緣自棱線部、第1面部、第2面部立起的基部形成的彎曲部分之外的、形成為平坦?fàn)畹牟糠值膶挾?。例如,在棱線部凸緣115a的情況下,如圖1的(b)所示,棱線部凸緣115a的寬度lf是指,在長度方向最外端部100a處除與棱線部112a連續(xù)并形成為彎曲狀的彎曲部115ab之外、形成為平坦?fàn)畹钠教共?15aa的寬度lf。棱線部凸緣115a、115b的寬度lf小于第1凸緣116a、116b、第2凸緣117各自的寬度,從而棱線部凸緣115a、115b的凸緣頂端的剩余伸長較小,能夠減少褶皺的產(chǎn)生。特別是,本實(shí)施方式的壓制成型品100適合用于汽車車身用加強(qiáng)構(gòu)件,利用高強(qiáng)度鋼板成型。為了抑制在該由高強(qiáng)度鋼板形成的壓制成型品100的棱線部凸緣115a、115b處產(chǎn)生褶皺,棱線部凸緣115a、115b的平坦部115aa的寬度lf(mm)滿足下述式(1):lf≤0.22rf+0.13θ-5.9…(1)rf(mm):棱線部112a(112b)的曲率半徑(棱線部的內(nèi)表面的曲率半徑)θ:第1面部113a(113b)與第2面部114所成的角度(其中,0mm≤rf≤35mm,并且,90°≤θ≤145°)。若棱線部凸緣115a、115b的寬度lf超過所述式(1)所限定的范圍,則棱線部凸緣115a、115b的緣部側(cè)的剩余伸長變大,容易產(chǎn)生褶皺。其中,為了確保適合用于汽車車身用加強(qiáng)構(gòu)件的壓制成型品100的強(qiáng)度,優(yōu)選棱線部凸緣115a、115b的寬度lf滿足lf≥0.2rf的關(guān)系。另外,在將棱線部凸緣115a、115b的凸緣寬度lf設(shè)為小于第1凸緣116a、116b和第2凸緣117各自的凸緣寬度lfs1、lfs2的情況下,可以是棱線部凸緣115a、115b的至少一部分的凸緣寬度lf小于第1凸緣116a、116b和第2凸緣117各自的至少一部分的凸緣寬度lfs1、lfs2。即,在凹部119形成于棱線部凸緣115a、115b內(nèi)的情況等,可以是棱線部凸緣115a、115b的一部分的凸緣寬度lf小于第1凸緣116a、116b和第2凸緣117各自的凸緣寬度lfs1、lfs2。另外,在凹部119形成至第1凸緣116a、116b和第2凸緣117的范圍內(nèi)的情況等,可以是第1凸緣116a、116b和第2凸緣117各自的一部分的凸緣寬度lfs1、lfs2與棱線部凸緣115a、115b的凸緣寬度lf相同。并且,優(yōu)選向內(nèi)連續(xù)凸緣118的寬度方向上的緣部的板厚為壓制成型前的板厚以上。通過使向內(nèi)連續(xù)凸緣118的緣部具有這樣的板厚,能夠提高用作汽車車身用加強(qiáng)構(gòu)件的壓制成型品100的剛度、載荷傳遞強(qiáng)度。并且,優(yōu)選向內(nèi)連續(xù)凸緣118的寬度方向上的緣部的板厚為壓制成型前的板厚的1.5倍以下。特別優(yōu)選棱線部凸緣115a、115b的緣部的板厚為壓制成型前的板厚的1.5倍以下。通過使向內(nèi)連續(xù)凸緣118的緣部具有這樣的板厚,從而在將向內(nèi)凸緣作為接合材料與其他構(gòu)件重疊并進(jìn)行點(diǎn)焊等焊接的情況下,會導(dǎo)致焊接不良的重疊部分的間隙減小。因而,在將用作汽車車身用加強(qiáng)構(gòu)件的壓制成型品100與其他構(gòu)件接合時,能夠維持充分的接合強(qiáng)度。如上述那樣,本實(shí)施方式的壓制成型品100在棱線部凸緣115a、115b沒有缺口,并且在向內(nèi)連續(xù)凸緣118沒有褶皺。因而,在將壓制成型品100用作例如汽車車身用加強(qiáng)構(gòu)件的情況下,能夠提高壓制成型品100與其他構(gòu)件之間的接合強(qiáng)度,并且能夠提高加強(qiáng)構(gòu)件的剛度、載荷傳遞效率等性能。<2.第2實(shí)施方式>接著,將本發(fā)明的第2實(shí)施方式的壓制成型品100的制造方法的例子與壓制成型品100的制造裝置的結(jié)構(gòu)例一并進(jìn)行說明。本實(shí)施方式的壓制成型品100的制造方法和制造裝置用于制造例如第1實(shí)施方式的壓制成型品100。本實(shí)施方式的壓制成型品100的制造方法包括第1中間成型工序和第1壓制成型工序。(2-1.第1中間成型工序)首先,說明在第1中間成型工序中進(jìn)行的壓制成型方法以及能夠在該工序中使用的壓制成型裝置,該第1中間成型工序用于自由鋼板形成的坯料120得到第1中間構(gòu)件130。圖3的(a)、(b)是示意性地表示通過壓制成型自坯料120得到第1中間構(gòu)件130的情況的說明圖。圖3的(a)表示將坯料120設(shè)于壓制成型裝置90的情況。圖3的(b)表示壓制成型結(jié)束時的情況。如圖3的(a)所示,在將坯料120設(shè)于壓制成型裝置90之后,利用沖頭95和以在合模方向上移動自如的方式安裝于沖模91的墊板92夾持坯料120。接著,如圖3的(b)所示,使沖模91下降,從而進(jìn)行利用沖模91彎折坯料120的長度方向上的兩端部121的彎曲成型。通過該彎曲成型,能夠得到在坯料120的長度方向上的兩端部具有凸緣131的第1中間構(gòu)件130。在此,示出了彎折坯料120的長度方向上的兩端部121的例子,但也可以彎折長度方向上的兩端部121中的任意一端部。該第1中間成型工序所使用的壓制成型裝置90可以是具有沖頭95以及以墊板92在合模方向上移動自如的方式安裝有墊板92的沖模91的、公知的基于彎曲成型的壓制成型裝置90。(2-2.第1壓制成型工序)接著,說明在第1壓制成型工序中進(jìn)行的壓制成型方法以及能夠在第1壓制成型工序中使用的壓制成型裝置,該第1壓制成型工序用于自第1中間構(gòu)件130得到壓制成型品100。(2-2-1.壓制成型裝置)圖4是示意性地表示第1壓制成型工序所使用的壓制成型裝置10的結(jié)構(gòu)例的一部分的概略圖。該第1壓制成型工序所使用的壓制成型裝置相當(dāng)于本發(fā)明的壓制成型品的制造裝置的一形態(tài)。其中,圖4表示壓制成型裝置10在坯料120的長度方向(圖4中的空心箭頭方向)上的端部的周邊處的部分。如圖4所示,壓制成型裝置10包括沖模30、坯料保持件32、沖頭35、墊板31和內(nèi)墊板33。沖模30和坯料保持件32用于約束并保持坯料120的與長度方向交叉的寬度方向上的端部。墊板31以在合模方向上移動自如的方式支承于沖模30。內(nèi)墊板33以在合模方向上移動自如的方式支承于沖頭35。并且,內(nèi)墊板33在與第1中間構(gòu)件130的長度方向交叉的方向上的寬度小于沖頭35在與第1中間構(gòu)件130的長度方向交叉的方向上的寬度。因而,墊板31和內(nèi)墊板33用于約束坯料120的寬度方向上的中央部。而且,壓制成型裝置10還包括在壓制成型時與沖頭35的側(cè)面35a和內(nèi)墊板33的側(cè)面33a相對地配置的面外變形抑制工具34。在圖4中僅示意性地示出了例如沖模30的表面、面外變形抑制工具34的表面。沖模30、坯料保持件32、沖頭35、墊板31和內(nèi)墊板33均為在這種基于拉深成型的壓制成型裝置中以往使用的結(jié)構(gòu)即可。因而,此處省略說明。面外變形抑制工具34被配置為在壓制成型時與沖頭35的側(cè)面35a和內(nèi)墊板33的側(cè)面33a相對且與該側(cè)面33a、35a之間設(shè)有規(guī)定距離的間隙(第1間隙)。在壓制成型時,在沖頭35的側(cè)面35a和內(nèi)墊板33的側(cè)面33a這兩者與面外變形抑制工具34之間的間隙(第1間隙)內(nèi)夾持形成于第1中間構(gòu)件130的凸緣131而進(jìn)行壓制成型。因而,能夠限制凸緣131的板厚的增大、變動,能夠抑制褶皺的產(chǎn)生。間隙的距離可以是例如凸緣131的板厚與規(guī)定余隙加在一起而得到的值。例如,能夠?qū)㈤g隙設(shè)為滿足下述式(2):1.00×t≤x<1.40×t…(2)t:坯料的板厚(mm)x:間隙的距離(mm)。間隙的距離x滿足所述式(2),從而能夠在不使凸緣131的板厚小于壓制成型前的板厚的前提下可靠地抑制凸緣131發(fā)生面外變形。特別是,能夠抑制在容易產(chǎn)生褶皺的棱線部凸緣115a、115b處發(fā)生面外變形。此時,為了抑制壓制成型時的粘模,也可以在凸緣131的表面與面外變形抑制工具34之間設(shè)置很小的余隙。并且,凸緣131的板厚越薄,越容易發(fā)生面外變形。因而,更加優(yōu)選的是,將間隙設(shè)為滿足下述式(3):1.03×t≤x<1.35×t…(3)t:坯料的板厚(mm)x:間隙的距離(mm)。圖4所示的壓制成型裝置10是在沖頭35具有內(nèi)墊板33的壓制成型裝置10的結(jié)構(gòu)例,但也可以是沒有內(nèi)墊板33的壓制成型裝置。對于該沒有內(nèi)墊板33的壓制成型裝置,除沖頭35沒有內(nèi)墊板33這一點(diǎn)以外,其余部分能夠采用與壓制成型裝置10相同的結(jié)構(gòu)。在本說明書中,將沒有內(nèi)墊板33的壓制成型裝置簡稱為“拉深成型裝置”,將具有內(nèi)墊板33的壓制成型裝置稱為“內(nèi)墊板拉深成型裝置”。(2-2-2.利用拉深成型裝置進(jìn)行的第1壓制成型工序)接著,說明利用沒有內(nèi)墊板的拉深成型裝置10a對第1中間構(gòu)件130進(jìn)行拉深成型的情況。拉深成型裝置10a是在圖4所示的壓制成型裝置10中不具有內(nèi)墊板33的裝置,因此也同時參照圖4進(jìn)行以下的說明。圖5是示意性地表示通過使用拉深成型裝置10a的拉深成型自第1中間構(gòu)件130得到壓制成型品100的情況的說明圖。圖5中的(a)列是從與第1中間構(gòu)件130的長度方向交叉的方向看到的圖,圖5中的(b)列是從第1中間構(gòu)件130的長度方向看到的圖。即,在圖5中的(b)列,能夠從正面觀察凸緣131。并且,圖5的(a)表示將第1中間構(gòu)件130設(shè)于拉深成型裝置10a的情況,圖5的(b)表示第1中間構(gòu)件130與墊板31接觸的情況。并且,圖5的(c)表示拉深成型的中途的情況,圖5的(d)表示拉深成型結(jié)束時的情況。如圖5所示,在拉深成型的過程中,在將第1中間構(gòu)件130設(shè)于拉深成型裝置10a之后,利用沖模30和坯料保持件32約束并保持第1中間構(gòu)件130的與長度方向交叉的寬度方向上的端部132。在該狀態(tài)下,利用以在合模方向上移動自如的方式支承于沖模30的平坦?fàn)畹膲|板31和具有平坦?fàn)畹捻敳康臎_頭35夾持第1中間構(gòu)件130,在該狀態(tài)下,使沖模30靠近沖頭35。通過這樣,對第1中間構(gòu)件130進(jìn)行拉深成型。在該拉深成型時,第1中間構(gòu)件130的凸緣131配置在由沖頭35的側(cè)面35a和與沖頭35的側(cè)面35a相對地配置的面外變形抑制工具34形成的間隙(第1間隙)內(nèi)。因而,在進(jìn)行拉深成型的期間,凸緣131被面外變形抑制工具34和沖頭35的側(cè)面35a約束。由此,能夠抑制在拉深成型時凸緣131發(fā)生面外變形,能夠通過面內(nèi)壓縮成型形成棱線部凸緣115a、115b。因而,成為產(chǎn)生褶皺的主要原因的棱線部凸緣115a、115b的板厚的增大以及變動減少。如上述那樣,形成在沖頭35的側(cè)面35a與面外變形抑制工具34之間的間隙被設(shè)為滿足下述式(2):1.00×t≤x<1.40×t…(2)t:坯料的板厚(mm)x:間隙的距離(mm)。通過滿足所述式(2),能夠可靠地抑制第1凸緣116a(116b)、棱線部凸緣115a(115b)和第2凸緣117連續(xù)而成的向內(nèi)連續(xù)凸緣118發(fā)生面外變形。特別是,能夠抑制容易產(chǎn)生褶皺的棱線部凸緣115a、115b發(fā)生面外變形。而且,如上述那樣,為了抑制壓制成型時的粘模并且抑制凸緣131的板厚較薄時的面外變形,優(yōu)選間隙滿足下述式(3):1.03×t≤x<1.35×t…(3)t:坯料的板厚(mm)x:間隙的距離(mm)。在圖5所示的例子中,面外變形抑制工具34被設(shè)為與沖模30成為一體,但面外變形抑制工具34的結(jié)構(gòu)并不限定于該例子。面外變形抑制工具34只要能夠約束第1中間構(gòu)件130的凸緣131即可,面外變形抑制工具34的設(shè)置位置并不限定于特定的位置。并且,面外變形抑制工具34并不限定于如本實(shí)施方式的例子那樣附屬于上模,也可以附屬于下模。而且,面外變形抑制工具34并不限定于與沖頭35的側(cè)面35a相協(xié)作來約束凸緣131,面外變形抑制工具34也可以獨(dú)立地約束凸緣131。通過利用該拉深成型裝置10a進(jìn)行的拉深成型,能夠成型如圖1所示那樣包括棱線部112a、112b、第1面部113a、113b、第2面部114和向內(nèi)連續(xù)凸緣118的壓制成型品100。此時,利用沖頭35的側(cè)面35a和面外變形抑制工具34夾持凸緣131而進(jìn)行拉深成型,因此能夠在不在凸緣131設(shè)置缺口的前提下抑制所形成的向內(nèi)連續(xù)凸緣118產(chǎn)生褶皺。其中,以上的說明是針對形成有在第1面部113a、113b、棱線部112a、112b、第2面部114的長度方向上的最外端部100a的整個區(qū)域內(nèi)連續(xù)的向內(nèi)連續(xù)凸緣118的壓制成型品100進(jìn)行的。但是,第1凸緣116a、116b也可以不是形成于第1面部113a、113b的最外端部100a的整個區(qū)域而是形成于第1面部113a、113b的最外端部100a的一部分。并且,第2凸緣117也可以不是形成于第2面部114的最外端部100a的整個區(qū)域而是形成于第2面部114的最外端部100a的一部分。即,只要第1凸緣116a、116b和第2凸緣117分別與棱線部凸緣115a、115b連續(xù)地形成即可。(2-2-3.利用內(nèi)墊板拉深成型裝置進(jìn)行的第1壓制成型工序)接著,說明利用內(nèi)墊板拉深成型裝置10b對第1中間構(gòu)件130進(jìn)行內(nèi)墊板拉深成型的情況。圖6是示意性地表示通過使用內(nèi)墊板拉深成型裝置10b的內(nèi)墊板拉深成型自第1中間構(gòu)件130得到壓制成型品100的情況的說明圖。圖6中的(a)列是從與第1中間構(gòu)件130的長度方向交叉的方向看到的圖,圖6中的(b)列是從第1中間構(gòu)件130的長度方向看到的圖。并且,圖6的(a)表示將第1中間構(gòu)件130設(shè)于內(nèi)墊板拉深成型裝置10b的情況,圖6的(b)表示第1中間構(gòu)件130與墊板31接觸的情況。并且,圖6的(c)表示內(nèi)墊板拉深成型的中途的情況,圖6的(d)表示內(nèi)墊板拉深成型即將結(jié)束之前的情況,圖6的(e)表示內(nèi)墊板拉深成型結(jié)束時的情況。其中,對于圖6中的附圖標(biāo)記,除增加了內(nèi)墊板33以外,其余部分與圖5相同。如圖6所示,在內(nèi)墊板拉深成型時,利用具有內(nèi)墊板33的沖頭35進(jìn)行拉深成型,該內(nèi)墊板33被支承為在合模方向上移動自如,除這一點(diǎn)以外,其余部分能夠與圖5所示的拉深成型同樣地進(jìn)行。因而,在進(jìn)行內(nèi)墊板拉深成型的期間,凸緣131被沖頭35的側(cè)面35a、內(nèi)墊板33的側(cè)面33a與面外變形抑制工具34夾持,能夠抑制凸緣131發(fā)生面外變形。由此,棱線部凸緣115a、115b通過面內(nèi)壓縮成型形成。并且,利用具有內(nèi)墊板33的沖頭35,從而能夠減小所形成的向內(nèi)連續(xù)凸緣118的緣部的板厚、特別是棱線部凸緣115a、115b的緣部的板厚的增大,能夠進(jìn)一步抑制褶皺的產(chǎn)生。圖7是示意性地表示在拉深成型或內(nèi)墊板拉深成型的中途形成的棱線部112a、112b的曲率半徑的說明圖。圖7的(a)表示不使用內(nèi)墊板的拉深成型的情況。圖7的(b)表示內(nèi)墊板拉深成型的情況。與圖7的(a)所示的拉深成型相比,如圖7的(b)所示,在內(nèi)墊板拉深成型的情況下,在成型中途形成于棱線部112a、112b的彎曲部分b的曲率半徑較大。因此,能夠緩和在成型后形成的棱線部凸緣115a、115b的緣部處的板厚增大。結(jié)果,能夠形成褶皺的產(chǎn)生得到抑制的良好的向內(nèi)連續(xù)凸緣118。另外,在圖7的(b)所示的內(nèi)墊板拉深成型的情況下,在拉深成型結(jié)束的時刻內(nèi)墊板33下降而收納于沖頭35的內(nèi)部,因此棱線部112a、112b的曲率半徑由沖頭35的角部的曲率半徑?jīng)Q定。因而,相比圖7的(a)所示的拉深成型而言,形成的棱線部112a、112b的曲率半徑未出現(xiàn)差異。(2-2-3.利用彎曲成型裝置進(jìn)行的第1壓制成型)在此之前所說明的第1壓制成型工序是通過拉深成型進(jìn)行的,但第1壓制成型工序也可以不是通過拉深成型進(jìn)行而是通過彎曲成型進(jìn)行。圖8是示意性地表示通過代替拉深成型裝置10a或內(nèi)墊板拉深成型裝置10b而使用彎曲成型裝置50的彎曲成型自第1中間構(gòu)件130得到壓制成型品100的情況的說明圖。圖8中的(a)列是從與第1中間構(gòu)件130的長度方向交叉的方向看到的圖,圖8中的(b)列是從第1中間構(gòu)件130的長度方向看到的圖。并且,圖8的(a)表示將第1中間構(gòu)件130設(shè)于彎曲成型裝置50的情況,圖8的(b)表示第1中間構(gòu)件130與墊板31接觸的情況。并且,圖8的(c)表示彎曲成型的中途的情況,圖8的(d)表示彎曲成型結(jié)束時的情況。如圖8所示,在彎曲成型的過程中,將第1中間構(gòu)件130設(shè)于彎曲成型裝置50。此時,第1中間構(gòu)件130的凸緣131配置在由沖頭35的側(cè)面35a、內(nèi)墊板33的側(cè)面33a與同該側(cè)面33a、35a相對地配置的面外變形抑制工具34形成的間隙(第1間隙)內(nèi)。由此,第1中間構(gòu)件130的凸緣131被沖頭35的側(cè)面35a、內(nèi)墊板33的側(cè)面33a與面外變形抑制工具34約束。在該狀態(tài)下,利用沖頭35和安裝于沖模30的墊板31夾持第1中間構(gòu)件130,在該狀態(tài)下,使沖模30與沖頭35靠近。由此,第1中間構(gòu)件130的與長度方向交叉的寬度方向上的兩端部被彎折。結(jié)果,能夠抑制在彎曲成型時凸緣131發(fā)生面外變形,能夠通過面內(nèi)壓縮成型形成棱線部凸緣115a、115b。與拉深成型相比,像這樣進(jìn)行的彎曲成型能夠利用簡單的結(jié)構(gòu)的模具進(jìn)行。另一方面,與拉深成型相比,在彎曲成型的情況下,棱線部凸緣115a、115b的板厚的增大容易變大,但能夠形成第1實(shí)施方式所說明的那樣的壓制成型品100。但是,從能夠減小壓制成型品100的粘模痕跡這一點(diǎn)、能夠減小模具的損耗這一點(diǎn)而言,拉深成型相比彎曲成型而言是有利的。以上,采用本實(shí)施方式的壓制成型品的制造方法,能夠利用高強(qiáng)度鋼板在不設(shè)置缺口的前提下制造具有抑制了褶皺的產(chǎn)生的向內(nèi)連續(xù)凸緣118的壓制成型品100。因而,能夠得到一種能夠用于汽車車身用加強(qiáng)構(gòu)件等的剛度較高且載荷傳遞特性優(yōu)良的壓制成型品100。<3.第3實(shí)施方式>接著,將本發(fā)明的第3實(shí)施方式的壓制成型品100的制造方法的例子與壓制成型裝置的結(jié)構(gòu)例一并進(jìn)行說明。本實(shí)施方式的壓制成型品100的制造方法和壓制成型裝置也用于制造第1實(shí)施方式的壓制成型品100。本實(shí)施方式的壓制成型品100的制造方法包括第1中間成型工序、第2中間成型工序和第2壓制成型工序。本實(shí)施方式的壓制成型品100的制造方法在例如壓制成型品100的第1面部113a、113b在與棱線部112a、112b的延伸方向正交的方向上的長度較長的情況下實(shí)施。其中,第1中間成型工序能夠與第2實(shí)施方式的第1中間成型工序同樣地進(jìn)行,因此此處省略說明。(3-1.第2中間成型工序)以下,說明在第2中間成型工序中進(jìn)行的壓制成型方法以及能夠在第2中間成型工序中使用的壓制成型裝置,該第2中間成型工序用于自第1中間構(gòu)件130得到第2中間構(gòu)件140。與第2實(shí)施方式的第1壓制成型工序同樣地,第2中間成型工序也可以通過不使用內(nèi)墊板的拉深成型和使用內(nèi)墊板的拉深成型中的任一方法實(shí)施。(3-1-1.利用拉深成型裝置進(jìn)行的第2中間成型)首先,說明利用沒有內(nèi)墊板的拉深成型裝置60對第1中間構(gòu)件130進(jìn)行拉深成型的情況。與用于第1壓制成型的拉深成型裝置10a同樣地,拉深成型裝置60可以在圖4所示的壓制成型裝置10中不具有內(nèi)墊板33。圖9的(a)是示意性地表示拉深成型裝置60的結(jié)構(gòu)例的一部分的概略圖。并且,圖9的(b)是表示通過使用該拉深成型裝置60的拉深成型得到的第2中間構(gòu)件140的外觀的一例子的立體圖。拉深成型裝置60的基本結(jié)構(gòu)能夠采用與第2實(shí)施方式的第1壓制成型工序所使用的拉深成型裝置10a相同的結(jié)構(gòu)。其中,圖9的(a)表示拉深成型裝置60在第1中間構(gòu)件130的長度方向(圖9的(a)中的空心箭頭方向)上的端部的周邊處的部分。圖10是示意性地表示通過使用拉深成型裝置60的拉深成型自第1中間構(gòu)件130得到第2中間構(gòu)件140的情況的說明圖。圖10中的(a)列是從與第1中間構(gòu)件130的長度方向交叉的方向看到的圖,圖10中的(b)列是從第1中間構(gòu)件130的長度方向看到的圖。并且,圖10的(a)表示將第1中間構(gòu)件130設(shè)于拉深成型裝置60的情況,圖10的(b)表示第1中間構(gòu)件130與墊板31接觸的情況,圖10的(c)表示拉深成型結(jié)束時的情況。如圖10所示,基于拉深成型的第2中間成型工序基本上能夠與第2實(shí)施方式的第1壓制成型工序同樣地進(jìn)行。即,在將第1中間構(gòu)件130設(shè)于拉深成型裝置60之后,利用沖模30和坯料保持件32約束并保持第1中間構(gòu)件130的端部132。在該狀態(tài)下,利用以在合模方向上移動自如的方式支承于沖模30的平坦?fàn)畹膲|板31和具有平坦?fàn)畹捻敳康臎_頭35夾持第1中間構(gòu)件130,同時使沖模30靠近沖頭35。由此,對第1中間構(gòu)件130進(jìn)行拉深成型。該拉深成型可以采用被稱作所謂的淺拉深的拉深成型。在該拉深成型時,第1中間構(gòu)件130的凸緣131被約束在由沖頭35的側(cè)面35a和面外變形抑制工具34形成的間隙(第1間隙)內(nèi),能夠抑制凸緣131發(fā)生面外變形。但是,在第2中間成型工序的過程中,在使沖模30靠近沖頭35時,不使沖模30完全靠近沖頭35,使沖模30和坯料保持件32的移動在中途停止。此時,被沖模30和坯料保持件32夾持的第1中間構(gòu)件130的端部132被保持為未被完全彎折的狀態(tài)。如圖9的(b)所示,通過該拉深成型而形成中間棱線部142a、142b、分別與中間棱線部142a、142b相連的第1中間面部143a、143b和第2中間面部144。在本實(shí)施方式中,第2中間構(gòu)件140中的第1中間面部143a、143b與第2中間面部144呈相互平行狀態(tài)。并且,通過該拉深成型,形成于第1中間構(gòu)件130的凸緣131成型為中間棱線部凸緣145a、145b、第1中間凸緣146a、146b和第2中間凸緣147相連續(xù)而成的中間連續(xù)凸緣148。中間棱線部凸緣145a、145b是形成于中間棱線部142a、142b的端部的凸緣。第1中間凸緣146a、146b是形成于第1中間面部143a、143b的長度方向上的端部的至少一部分區(qū)域的凸緣。第2中間凸緣147是形成于第2中間面部144的長度方向上的端部的至少一部分區(qū)域的凸緣。在進(jìn)行拉深成型的期間,形成于第1中間構(gòu)件130的凸緣131被沖頭35的側(cè)面35a和面外變形抑制工具34夾持,能夠抑制凸緣131發(fā)生面外變形。因而,中間棱線部凸緣145a、145b通過面內(nèi)壓縮成型形成,能夠抑制在中間連續(xù)凸緣148處產(chǎn)生褶皺。像這樣,對第1中間構(gòu)件130進(jìn)行拉深成型,從而得到包括中間棱線部142a、142b、第1中間面部143a、143b、第2中間面部144和中間連續(xù)凸緣148的第2中間構(gòu)件140。該第2中間構(gòu)件140也是壓制成型品的一形態(tài)。因而,拉深成型裝置60是用于制造作為最終成型品的壓制成型品100的、本發(fā)明的壓制成型品的制造裝置的一形態(tài)。(3-1-2.利用內(nèi)墊板拉深成型裝置進(jìn)行的第2中間成型)接著,說明利用具有內(nèi)墊板的內(nèi)墊板拉深成型裝置70對第1中間構(gòu)件130進(jìn)行拉深成型的情況。內(nèi)墊板拉深成型裝置70的基本結(jié)構(gòu)能夠采用與第2實(shí)施方式的第1壓制成型工序所使用的內(nèi)墊板拉深成型裝置10b相同的結(jié)構(gòu)。圖11是示意性地表示通過使用內(nèi)墊板拉深成型裝置70的內(nèi)墊板拉深成型自第1中間構(gòu)件130得到第2中間構(gòu)件140的情況的說明圖。圖11中的(a)列是從與第1中間構(gòu)件130的長度方向交叉的方向看到的圖,圖11中的(b)列是從第1中間構(gòu)件130的長度方向看到的圖。并且,圖11的(a)表示將第1中間構(gòu)件130設(shè)于內(nèi)墊板拉深成型裝置70的情況,圖11的(b)表示第1中間構(gòu)件130與墊板31接觸的情況,圖11的(c)表示內(nèi)墊板拉深成型即將結(jié)束之前的情況。如圖11所示,在內(nèi)墊板拉深成型的情況下,利用具有內(nèi)墊板33的沖頭35進(jìn)行拉深成型,該內(nèi)墊板33被支承為在合模方向上移動自如,除這一點(diǎn)以外,其余部分能夠與圖10所示的拉深成型同樣地進(jìn)行。因而,在進(jìn)行內(nèi)墊板拉深成型的期間,凸緣131被夾持在由沖頭35的側(cè)面35a、內(nèi)墊板33的側(cè)面33a與面外變形抑制工具34形成的間隙(第1間隙)內(nèi),能夠抑制凸緣131發(fā)生面外變形。由此,中間棱線部凸緣145a、145b通過面內(nèi)壓縮成型形成。并且,利用具有內(nèi)墊板33的沖頭35,從而能夠減小所形成的中間連續(xù)凸緣148的寬度方向上的緣部區(qū)域的板厚的增大。特別是,能夠減小中間棱線部凸緣145a、145b的緣部區(qū)域的板厚的增大。因而,能夠進(jìn)一步抑制形成于作為最終成型品的壓制成型品100的向內(nèi)連續(xù)凸緣118產(chǎn)生褶皺。像這樣,在第2中間成型工序的過程中,對第1中間構(gòu)件130進(jìn)行內(nèi)墊板拉深成型,從而得到包括中間棱線部142a、142b、第1中間面部143a、143b、第2中間面部144和中間連續(xù)凸緣148的第2中間構(gòu)件140。該第2中間構(gòu)件140也是壓制成型品的一形態(tài)。因而,內(nèi)墊板拉深成型裝置70是用于制造作為最終成型品的壓制成型品100的、本發(fā)明的壓制成型品的制造裝置的一形態(tài)。(3-1-3.利用彎曲成型裝置進(jìn)行的第2中間成型工序)在此之前所說明的第2中間成型工序是通過拉深成型進(jìn)行的,但第2中間成型工序也可以不是通過拉深成型進(jìn)行而是通過彎曲成型進(jìn)行。在通過彎曲成型進(jìn)行第2中間成型工序時所使用的彎曲成型裝置的基本結(jié)構(gòu)能夠采用與第2實(shí)施方式的第1壓制成型工序所使用的彎曲成型裝置相同的結(jié)構(gòu)。但是,在通過彎曲成型形成第2中間構(gòu)件140的情況下,使沖模30靠近沖頭35時的移動距離比在第1壓制成型工序時的移動距離短。例如,通過使沖頭35進(jìn)入到?jīng)_模30的區(qū)域較淺,能夠縮短所述移動距離。由此,第1中間構(gòu)件130的端部132維持未被完全彎折的狀態(tài)。通過該彎曲成型,形成中間棱線部142a、142b、分別與中間棱線部142a、142b相連的第1中間面部143a、143b和第2中間面部144。在本實(shí)施方式中,并不是第2中間構(gòu)件140中的第1中間面部143a、143b與第2中間面部144平行的狀態(tài),第1中間面部143a、143b沿相對于第2中間面部144傾斜的方向延伸而形成。在進(jìn)行該彎曲成型的期間,形成于第1中間構(gòu)件130的凸緣131被夾持在由沖頭35的側(cè)面35a和面外變形抑制工具34形成的間隙(第1間隙)內(nèi),能夠抑制凸緣131發(fā)生面外變形。因而,中間棱線部凸緣145a、145b通過面內(nèi)壓縮成型形成,能夠抑制在中間連續(xù)凸緣148處產(chǎn)生褶皺。在本實(shí)施方式中,也是,與拉深成型相比,彎曲成型能夠利用簡單的結(jié)構(gòu)的模具進(jìn)行。另一方面,與拉深成型相比,在彎曲成型的情況下,棱線部凸緣115a、115b的板厚的增大容易變大。但是,從能夠減小第2中間構(gòu)件140或者作為最終成型品的壓制成型品100的粘模痕跡這一點(diǎn)、能夠減小模具的損耗這一點(diǎn)而言,拉深成型相比彎曲成型而言是有利的。像這樣,在第2中間成型工序中,對第1中間構(gòu)件130進(jìn)行彎曲成型,從而得到包括中間棱線部142a、142b、第1中間面部143a、143b、第2中間面部144和中間連續(xù)凸緣148的第2中間構(gòu)件140。該第2中間構(gòu)件140也是壓制成型品的一形態(tài)。因而,用于該彎曲成型的彎曲成型裝置是用于制造作為最終成型品的壓制成型品100的、本發(fā)明的壓制成型品的制造裝置的一形態(tài)。(3-2.第2壓制成型工序)在第2壓制成型工序中,只要通過基于例如彎曲成型的壓制成型自第2中間構(gòu)件140得到壓制成型品100即可,壓制成型方法、壓制成型裝置的結(jié)構(gòu)并不特別限定。以下,參照圖12和圖13說明自第2中間構(gòu)件140得到作為最終成型品的壓制成型品100的壓制成型方法以及能夠在第2壓制成型工序中使用的壓制成型裝置80的一例子。圖12的(a)是示意性地表示用于彎曲成型的壓制成型裝置80的結(jié)構(gòu)例的一部分的概略圖。并且,圖12的(b)是表示通過使用該壓制成型裝置80的彎曲成型得到的壓制成型品100的外觀的一例子的立體圖。壓制成型裝置80的基本結(jié)構(gòu)能夠采用與第2實(shí)施方式的第1中間成型工序所使用的壓制成型裝置90相同的結(jié)構(gòu)。但是,第2壓制成型工序所使用的壓制成型裝置80包括在壓制成型時與沖頭39的側(cè)面39a相對地配置的面外變形抑制工具40。由沖頭39的側(cè)面39a和面外變形抑制工具40形成的間隙(第2間隙)的距離能夠設(shè)為與第1壓制成型工序或第2中間成型工序所使用的成型裝置中形成的間隙(第1間隙)相同的距離。其中,圖12的(a)表示壓制成型裝置80在第2中間構(gòu)件140的長度方向(圖12的(a)中的空心箭頭方向)上的端部的周邊處的部分。圖13是示意性地表示通過使用壓制成型裝置80的彎曲成型自第2中間構(gòu)件140得到壓制成型品100的情況的說明圖。圖13中的(a)列是從與第2中間構(gòu)件140的長度方向交叉的方向看到的圖,圖13中的(b)列是從第2中間構(gòu)件140的長度方向看到的圖。并且,圖13的(a)表示第2中間構(gòu)件140與墊板38接觸的情況,圖13的(b)表示彎曲成型結(jié)束時的情況。如圖13所示,基于彎曲成型的第2壓制成型工序基本上能夠與第2實(shí)施方式的第1中間成型工序同樣地進(jìn)行。即,在將第2中間構(gòu)件140設(shè)在沖頭39上之后,利用沖頭39和以在合模方向上移動自如的方式支承于沖模37的墊板38約束并保持第2中間構(gòu)件140的第2中間面部144。在該狀態(tài)下,使沖頭39與沖模37相對靠近,從而進(jìn)行彎折第1中間面部143a、143b的壓制成型。在進(jìn)行該彎曲成型的期間,形成于第2中間構(gòu)件140的中間連續(xù)凸緣148被夾持在由沖頭39的側(cè)面39a和面外變形抑制工具40形成的間隙內(nèi),能夠抑制中間連續(xù)凸緣148發(fā)生面外變形。因而,棱線部凸緣115a、115b通過面內(nèi)壓縮成型形成,能夠抑制在向內(nèi)連續(xù)凸緣118處產(chǎn)生褶皺。如圖12的(b)所示,通過該彎曲成型得到具有棱線部112a、112b、第1面部113a、113b、第2面部114和向內(nèi)連續(xù)凸緣118的壓制成型品100。向內(nèi)連續(xù)凸緣118沒有缺口,是棱線部凸緣115a、115b、第1凸緣116a、116b和第2凸緣117在截面上朝向內(nèi)側(cè)連續(xù)地形成而得到的。其中,在本實(shí)施方式中,在壓制成型品100的端部形成有遍及棱線部112a、112b、第1面部113a、113b和第2面部114的端部的整個區(qū)域的向內(nèi)連續(xù)凸緣118。但是,第1凸緣116a、116b和第2凸緣117也可以形成于第1面部113a、113b和第2面部114的端部的一部分區(qū)域。只要第1凸緣116a、116b和第2凸緣117分別與棱線部凸緣115a、115b連續(xù)地形成即可。另外,在第2壓制成型工序的彎曲成型中,根據(jù)加工條件的不同,要么不對棱線部施加追加的彎曲加工,要么即使對棱線部施加彎曲加工,其負(fù)荷也非常小。因此,由沖頭35的側(cè)面35a和面外變形抑制工具40形成的間隙(第2間隙)的距離可以大于第1壓制成型工序、第2中間成型工序所使用的成型裝置中形成的間隙(第1間隙)。以上,采用本實(shí)施方式的壓制成型品的制造方法,能夠利用高強(qiáng)度鋼板在不設(shè)置缺口的前提下制造具有抑制了褶皺的產(chǎn)生的向內(nèi)連續(xù)凸緣118的壓制成型品100。因而,能夠得到一種能夠用于汽車車身用加強(qiáng)構(gòu)件等的剛度較高且載荷傳遞特性優(yōu)良的壓制成型品100。實(shí)施例以下,說明本發(fā)明的實(shí)施例。(實(shí)施例1、2和比較例1)首先,利用兩個除面外變形抑制工具的有無以外具有相同結(jié)構(gòu)的壓制成型裝置制造壓制成型品,對該情況下的向內(nèi)連續(xù)凸緣的狀態(tài)進(jìn)行比較。壓制成型品的制造按照第2實(shí)施方式的壓制成型品的制造方法進(jìn)行。在實(shí)施例1、2的情況下,使用由板厚為1.0mm、拉伸強(qiáng)度為980mpa級的冷軋鋼板形成的坯料,通過第2實(shí)施方式的壓制成型品的制造方法,試著制造具有向內(nèi)連續(xù)凸緣的帽型截面形狀的壓制成型品。即,在第1中間成型工序中在坯料的長度方向上的端部形成凸緣,之后,在第1壓制成型工序中利用具有面外變形抑制工具的拉深成型裝置進(jìn)行壓制成型。此時,對于在面外變形抑制工具與沖頭的側(cè)面之間形成的間隙的距離x,在實(shí)施例1中,將該間隙的距離x設(shè)為1.33mm,在實(shí)施例2中,將該間隙的距離x設(shè)為1.41mm。并且,在比較例1的情況下,在不使用面外變形抑制工具的前提下進(jìn)行第1壓制成型工序。將所制造的壓制成型品的棱線部的曲率半徑rf設(shè)為5mm,將棱線部凸緣的平坦部的寬度lf設(shè)為2mm。并且,將所形成的壓制成型品的第1面部與第2面部所成的角度θ設(shè)為90°。該凸緣的寬度lf是比0.22×rf+0.13×θ-5.9的值6.9小的值。即,得到的壓制成型品滿足所述式(1)。其中,實(shí)施例1、2、比較例1全都使用相同結(jié)構(gòu)的坯料。圖14的(a)~(c)表示實(shí)施例1、2、比較例1所得到的壓制成型品的棱線部凸緣附近的外觀照片。圖14的(a)是實(shí)施例1的壓制成型品,圖14的(b)是實(shí)施例2的壓制成型品。并且,圖14的(c)是比較例1的壓制成型品。圖14的(c)所示的比較例1的壓制成型品是在不使用面外變形抑制工具的前提下進(jìn)行第1壓制成型而得到的,因此棱線部凸緣向外側(cè)較大程度地變形。相對于此,圖14的(a)、(b)所示的實(shí)施例1、2的壓制成型品是使用面外變形抑制工具進(jìn)行第1壓制成型而得到的,因此棱線部凸緣被面內(nèi)壓縮,能夠形成褶皺較少的良好的形狀的向內(nèi)連續(xù)凸緣。另外,在圖14的(b)所示的實(shí)施例2的壓制成型品的情況下,在自第1凸緣到棱線部凸緣、第2凸緣的范圍內(nèi),在向內(nèi)連續(xù)凸緣的表面能夠發(fā)現(xiàn)通過目測能夠識別的較小的波紋。相對于此,在圖14的(a)所示的實(shí)施例1的壓制成型品的情況下,未發(fā)現(xiàn)這樣的波紋。因而可知,在由沖頭的側(cè)面和面外變形抑制工具形成的間隙的距離較小的情況下,能夠形成良好的形狀的向內(nèi)連續(xù)凸緣。(實(shí)施例3、4、5)接著,在利用面外變形抑制工具進(jìn)行壓制成型時,對拉深成型、內(nèi)墊板拉深成型和彎曲成型各情況下的向內(nèi)連續(xù)凸緣的板厚的增大率進(jìn)行比較。壓制成型品的制造按照第2實(shí)施方式進(jìn)行。在實(shí)施例3~5的情況下,使用由板厚為1.0mm、拉伸強(qiáng)度為980mpa級的冷軋鋼板形成的坯料,通過第2實(shí)施方式的壓制成型品的制造方法,試著制造具有向內(nèi)連續(xù)凸緣的帽型截面形狀的壓制成型品。即,在第1中間成型工序中在坯料的長度方向上的端部形成凸緣,之后,在第1壓制成型工序中利用具有面外變形抑制工具的彎曲成型裝置或拉深成型裝置進(jìn)行壓制成型。對于在第1壓制成型工序中使用的壓制成型裝置,在實(shí)施例3中使用拉深成型裝置,在實(shí)施例4中使用內(nèi)墊板拉深成型裝置,在實(shí)施例5中使用彎曲成型裝置。這些成型裝置全都具有面外變形抑制工具,以沖頭的側(cè)面或內(nèi)墊板的側(cè)面與面外變形抑制工具之間的間隙的距離x為坯料的板厚t的1.18倍的方式配置面外變形抑制工具。將所制造的壓制成型品的棱線部的曲率半徑rf設(shè)為5mm,將棱線部凸緣的平坦部的寬度lf設(shè)為2mm。實(shí)施例3~5全都使用相同結(jié)構(gòu)的坯料。圖15是表示分別在實(shí)施例3~5的壓制成型品形成的棱線部凸緣的緣部的板厚增大率的分布的曲線圖。圖15中的曲線圖的橫軸表示凸緣的緣部的距離(mm),圖15中的曲線圖的縱軸表示板厚增大率(%)。如圖1的(b)所示,“凸緣的緣部的距離”是指,在棱線部凸緣115a處,以緣部的板厚自坯料的板厚開始增大的位置(圖1的(b)中的位置s)為起點(diǎn)0的、棱線部凸緣115a的緣部的位置。如圖15所示,與通過彎曲成型進(jìn)行第1壓制成型工序的情況相比,在通過拉深成型和內(nèi)墊板拉深成型進(jìn)行第1壓制成型工序的情況下,板厚的增大分散在較大的范圍,板厚增大率的峰值較小。因而,通過拉深成型或內(nèi)墊板拉深成型進(jìn)行第1壓制成型工序,能夠?qū)⒗饩€部凸緣的板厚變動抑制得較小,能夠得到具有更加良好的形狀的向內(nèi)連續(xù)凸緣的壓制成型品。其中,與通過不使用內(nèi)墊板的拉深成型進(jìn)行的情況相比,在通過內(nèi)墊板拉深成型進(jìn)行的情況下,板厚增大率的峰值較小,可知內(nèi)墊板拉深成型的效果更大。(實(shí)施例6~17、比較例2~13)接著,利用面外變形抑制工具進(jìn)行壓制成型,對在凸緣寬度lf、棱線部的曲率半徑rf以及第1面部與第2面部所成的角度θ的不同的情況下的褶皺產(chǎn)生狀況進(jìn)行比較。在實(shí)施例6~17、比較例2~13的情況下,使用由板厚為1.0mm、拉伸強(qiáng)度為980mpa級的冷軋鋼板形成的坯料,通過第2實(shí)施方式的制造方法,試著制造具有向內(nèi)連續(xù)凸緣的帽型截面形狀的壓制成型品。實(shí)施例6~17、比較例2~13全都利用拉深成型進(jìn)行第1壓制成型工序。評價分別在實(shí)施例6~17、比較例2~13中得到的壓制成型品的向內(nèi)連續(xù)凸緣處的褶皺產(chǎn)生狀況。將實(shí)施例6~17、比較例2~13各自的壓制成型品的棱線部的凸緣寬度lf、曲率半徑rf、角度θ以及有無產(chǎn)生褶皺的情況表示在表1中。[表1]θ(°)rf(mm)lf(mm)褶皺的產(chǎn)生實(shí)施例61455.013.0○(無)實(shí)施例71455.012.0○(無)比較例21455.015.0×(有)比較例31455.014.0×(有)實(shí)施例814515.015.0○(無)實(shí)施例914515.014.0○(無)比較例414515.018.0×(有)比較例514515.016.0×(有)實(shí)施例1014525.017.0○(無)實(shí)施例1114525.016.0○(無)比較例614525.019.0×(有)比較例714525.018.0×(有)實(shí)施例12905.06.0○(無)實(shí)施例13905.05.0○(無)比較例8905.08.0×(有)比較例9905.07.0×(有)實(shí)施例149015.08.0○(無)實(shí)施例159015.07.5○(無)比較例109015.09.5×(有)比較例119015.09.0×(有)實(shí)施例169025.010.0○(無)實(shí)施例179025.09.0○(無)比較例129025.013.0×(有)比較例139025.011.0×(有)圖16是表示實(shí)施例6~17、比較例2~13的壓制成型品的褶皺產(chǎn)生狀況的曲線圖。在第1面部與第2面部所成的角度θ為90°的情況和145°的情況中的任一情況下,均是棱線部的曲率半徑rf越小,不產(chǎn)生褶皺的凸緣寬度lf的極限值越小。該凸緣寬度lf的極限值能夠通過下述的近似式(3)表示:lf=0.22×rf+0.13×θ-5.9…(3)(其中,0mm≤rf≤35mm,并且,90°≤θ≤145°)。因而可知,為了抑制所形成的向內(nèi)連續(xù)凸緣產(chǎn)生褶皺,棱線部的凸緣寬度lf滿足下述式(1)較好:lf≤0.22×rf+0.13×θ-5.9…(1)(其中,0mm≤rf≤35mm,并且,90°≤θ≤145°)。附圖標(biāo)記說明10、壓制成型裝置(壓制成型品的制造裝置);10a、拉深成型裝置(壓制成型品的制造裝置);10b、內(nèi)墊板拉深成型裝置(壓制成型品的制造裝置);30、沖模;31、墊板;32、坯料保持件;33、內(nèi)墊板;34、面外變形抑制工具;35、沖頭;35a、側(cè)面;37、沖模;38、墊板;39、沖頭;39a、側(cè)面;40、面外變形抑制工具;50、彎曲成型裝置;60、拉深成型裝置;70、內(nèi)墊板拉深成型裝置(壓制成型品的制造裝置);80、壓制成型裝置(壓制成型品的制造裝置);90、壓制成型裝置;91、沖模;92、墊板;95、沖頭;100、壓制成型品;112a、112b、棱線部;113a、113b、第1面部;114、第2面部;115a、115b、棱線部凸緣;116a、116b、第1凸緣;117、第2凸緣;118、向內(nèi)連續(xù)凸緣;120、坯料;130、第1中間構(gòu)件;131、凸緣;140、第2中間構(gòu)件;142a、142b、中間棱線部;143a、143b、第1中間面部;144、第2中間面部;145a、145b、中間棱線部凸緣;146a、146b、第1中間凸緣;147、第2中間凸緣;148、中間連續(xù)凸緣。當(dāng)前第1頁12