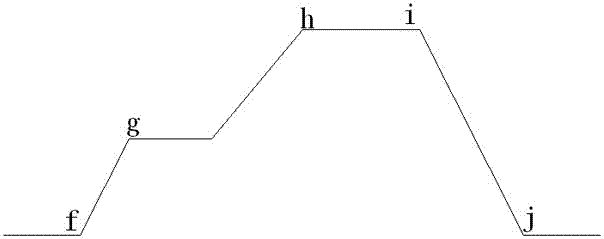
本發(fā)明涉及一種錦包棉羅馬布一浴染色工藝,屬于紡織制造業(yè)印染
技術(shù)領(lǐng)域:
。
背景技術(shù):
:羅馬布是常見的一種針織面料,相對普通面料而言,由于其布面不是很平整,且有暗橫條,因此,不僅染色過程中需要消耗大量的染料進(jìn)行染色,上染結(jié)束后還要進(jìn)行多次水洗、皂洗,導(dǎo)致羅馬布加工過程中需要消耗大量的水和染料,并在生產(chǎn)過程中和生產(chǎn)結(jié)束時(shí)會(huì)產(chǎn)生大量的印染廢水,不僅造成了生態(tài)污染,還需要投入大量的財(cái)力進(jìn)行凈水添加和污水處理,從而增加了其加工成本。羅馬布面料的特殊性也導(dǎo)致其染色效果不佳?;诖?,做出本發(fā)明。技術(shù)實(shí)現(xiàn)要素:針對現(xiàn)有羅馬布加工過程中所存在的上述缺陷,本申請?zhí)峁┮环N耗水量少、加工均勻性好、工藝流程短、染色效果佳的錦包棉(一般是指含錦量≤30%的狀況)羅馬布一浴染色工藝。為實(shí)現(xiàn)上述目的,發(fā)明人經(jīng)過多年研究,采用特定的染色助劑配合特殊的染色工藝獲得了本發(fā)明的技術(shù)方案,解決了現(xiàn)在羅馬布染色的上述問題。具體的技術(shù)方案如下:錦包棉羅馬布一浴染色工藝,其加工流程為:翻布→氣蒸→預(yù)定型→染色→對色→水洗→皂洗→烘干→成品,所述預(yù)定型工序中,定型方式采用天然氣明火熱定型,溫度為185-195℃,面料運(yùn)行速度為50-60碼/min,風(fēng)量80-120r/min;所述的染色采用一浴染色,待處理羅馬布進(jìn)缸,浴比為1:3-4,控制升溫速率為3-5℃/min,浴溫升至35-55℃,加入冰醋酸;降低升溫速率,并控制升溫速率為1-3℃/min,升溫至60-80℃,加入酸性染料、氯化稀土染色助劑,保溫10-20min;降低升溫速率,并控制升溫速率為0.5-1.5℃/min,升溫至92-98℃,保溫20-35min,加入元明粉,保溫12-20min,加入純堿和活性染料,保溫20-40min,染色完畢;所述的皂洗工序中,控制升溫速率為2-5℃/min,浴溫升至65-75℃;降低升溫速率,并控制升溫速率為1-3℃/min,升溫至75-85℃,保溫12-18min;以2-5℃/min降溫至35-45℃,控制ph為4.5-8.5,完成皂洗。進(jìn)一步的,作為優(yōu)選:所述的氯化稀土試劑為氯化鑭、氯化鈰等,優(yōu)選為氯化鑭,添加量0.1-1%,優(yōu)選0.5%。所述的染色工序中,升溫速率在a→b階段對處理效果的影響并不顯著,其影響主要表現(xiàn)在處理周期的長短上,因此,基于生產(chǎn)效率的考慮,其升溫速率宜控制在3-5℃/min,浴溫升至40℃,加入冰醋酸再次升溫;由b→c階段,此時(shí)溫度已經(jīng)處于中溫階段,且加入了冰醋酸,則升溫速率不宜過高,將升溫速率控制在1-3℃/min時(shí),可確保了浴液的穩(wěn)定,避免溫度過高引起冰醋酸形態(tài)變化,升溫至70℃,加入酸性染料和染色助劑再次升溫;由c→d階段,此時(shí),浴液中已經(jīng)包含有酸性染料,考慮到酸性染料的適用性,溫度過高容易導(dǎo)致染料失活,同時(shí),當(dāng)升溫速率高于1.5℃/min時(shí),由于升溫過快,還易引起面料的僵硬,導(dǎo)致手感變差,因此該階段升溫速率為控制在0.5-1.5℃/min,升溫至98℃,先保溫30min,待酸性染料浸潤充分后,再加入元明粉進(jìn)行促染;而后保溫15min,完成酸性染料上染充分,加入純堿和活性染料(耐高溫k系列),進(jìn)行活性染料的浸潤和上染,最后保溫30min,完成上染平衡。酸性染料的添加溫度控制在80℃以下的中溫階段,保證了酸性染料的活性,使面料在該階段即完成酸性染料的上染;而后將溫度升高,完成面料對活性染料上染的同時(shí)對其上染效果進(jìn)行固色,最后在該溫度下繼續(xù)保溫一段時(shí)間,確保上染充分。整個(gè)上染過程中浴比控制在1:4以下,并將活性染料與酸性染料在一個(gè)染缸中完成,避免了更換浴液造成的用水量增大,在確保上染效果的同時(shí),使上染過程中實(shí)際用水量大大降低。所述的皂洗工序中,溫度升至65-75℃的速率與溫度由75-85℃降低至35-45℃的降溫速率相同。皂洗工序中,升溫或降溫速率過慢則影響主要表現(xiàn)在處理周期的長短上或在同樣處理時(shí)間內(nèi)處理不充分。由于處理對象為連續(xù)結(jié)構(gòu)的布料,處理過程中升溫速率會(huì)對織物表面的折痕、手感都會(huì)造成影響,低溫階段,這種影響不大,因此升溫速率可適當(dāng)?shù)奶岣撸?dāng)溫度較高時(shí),如繼續(xù)采用較快的升溫速率,則會(huì)造成折痕的形成,從而影響面料表面的光滑度和手感。在皂洗開始階段,皂洗液逐漸的侵入到面料中,如果溫度過高、升溫速度過快,則會(huì)影響皂洗液與面料的接觸效率,造成皂洗不均勻;皂洗結(jié)束階段是皂洗效果穩(wěn)定的階段,升溫速率過快,則會(huì)導(dǎo)致染料活性較高,出現(xiàn)染料反染(即清洗液中的染料重新回到面料上)現(xiàn)象,升溫速率同樣不宜過高。所述的染色為非黑色(優(yōu)選為彩色或本白或漂白)時(shí),預(yù)定型后還設(shè)置有前處理,將待處理布料置于添加有去油助劑(如:去油靈)和雙氧水的溶液中,控制前處理溫度為85-95℃,處理時(shí)長為20-35min。對于黑色而言,預(yù)定型后可直接進(jìn)行上染,而對于非黑色,尤其是彩色、本白或者漂白時(shí),羅馬布表面所沾染的雜質(zhì)極易粘附在布料表面,并造成染色的不勻,影響染色效果,因此在處理溶液中添加去油助劑和雙氧水,對羅馬布表面進(jìn)行粗糙化的同時(shí),確保布料表面干凈無油漬,從而提高染料的粘附性,改善上染效果。所述的預(yù)定型工序中,采用天然氣明火熱定型,溫度為190℃,面料運(yùn)行速度為55碼/min,風(fēng)量100r/min。預(yù)定型采用該工序,確保羅馬面料處于伸展?fàn)顟B(tài),使面料在染色過程中可以更加充分的與染料接觸,從而有利于其染色的有效進(jìn)行,從而減少了染色過程和皂洗過程中水和染料的使用量。所述的皂洗結(jié)束時(shí),ph控制在6.5-7.5。所述的烘干工序中,烘干溫度為182-188℃,面料運(yùn)行速度為55-65碼/min。烘干過程是染色、皂洗效果后期定型的階段,本申請中,其溫度相對較高,而烘干速度相對較慢,使面料充分與熱量接觸,確保烘干均勻的同時(shí),避免烘干過程中染料隨蒸汽游離,造成后期染色變異。所述的成品工序階段,控制溫度為185-192℃,面料運(yùn)行速度為20-30碼/min。成品階段是染色加工最后的一個(gè)工序,也是染色加工最后的一道保型過程,本申請將該階段的溫度與烘干階段溫度接近,并將運(yùn)行速度進(jìn)一步降低,確保成品均勻。所述的染色工序和皂洗工序中,染液和皂洗液中的水采用河水過濾軟化至硬度降低至40ppm以下,或者采用收集的一浴染色加工中的回用水,該回用水是將印染廢水、皂洗廢水通過厭氧法深度處理后至硬度不超過0.01ppm。其中以河水作為原始水源時(shí),只需要將其硬度進(jìn)行控制即可滿足本申請的一浴染色工藝要求;采用廢水回用時(shí),由于染色過程中冰醋酸、純堿和皂洗中堿性皂洗液的添加,本身就中和了其自身的ph,并將加工過程中的染料等物質(zhì)轉(zhuǎn)化為固體沉淀,因此,厭氧法深度處理后的硬度通常都會(huì)在0.01ppm以下,其品質(zhì)較自來水更佳,而生產(chǎn)中的回用率可達(dá)到50-60%左右,從而減少了廢水的排放和實(shí)際廢水的產(chǎn)生。所述的活性染料采用高溫型活性染料,即常規(guī)的k系列染料?;钚匀玖鲜窃谌旧ば虻暮笃谕斗?,既可以適應(yīng)前段酸性染料中低溫染色的要求,又能避免染色串色。本申請的染色工序中,將活性染料染色與酸性染料染色形成一浴染色,在染色過程中,酸性染料的添加溫度控制在80℃以下的中溫階段,保證了酸性染料的活性,使面料在該階段即完成酸性染料的上染;而后將溫度升高,先加入元明粉促進(jìn)面料對酸性染料的上染,而后再加入純堿和活性染料,完成面料對活性染料上染的同時(shí)對其上染效果進(jìn)行固色,最后在該溫度下繼續(xù)保溫一段時(shí)間,確保上染充分。整個(gè)上染過程中浴比控制在1:4以下,并將活性染料與酸性染料在一個(gè)染缸中完成,避免了更換浴液造成的用水量增大,在確保上染效果的同時(shí),使上染過程中實(shí)際用水量大大降低。本申請的技術(shù)方案中,染色工藝與染色助劑的配合獲得了較好的技術(shù)效果。實(shí)現(xiàn)了活性染料與酸性染料染色的一浴染色,耗水量至少降低40-60%,工序縮短。通過不同階段溫度和升溫速率的控制,以及配特定的染色助劑和添加工藝實(shí)現(xiàn)了羅馬布染色性的提高,表現(xiàn)出染色的均勻性、色牢度均得到改善。產(chǎn)品不僅手感柔軟,面料應(yīng)用于內(nèi)衣等加工時(shí),穿著舒適性好,染色性好。附圖說明圖1為本申請中染色工序的工藝路線圖;圖2為本申請中皂洗工序的工藝路線圖。具體實(shí)施方式手感測試以未染色處理織物為基準(zhǔn)樣品,染色后織物與基準(zhǔn)樣品手感比較得到。色牢度測試標(biāo)準(zhǔn)iso105ced4:2008,勻染性測試標(biāo)準(zhǔn)gb/t21881-2008。色牢度和勻染性級別中一級最差,五級最好。實(shí)施例1:預(yù)定型工序?qū)α_馬布手感的影響本實(shí)施例錦包棉羅馬布一浴染色工藝,其加工流程為:翻布→氣蒸→預(yù)定型→染色→對色→水洗→皂洗→烘干→成品。其中:(1)預(yù)定型工序中:①定型方式分別采用蒸汽定型和天然氣明火熱定型,溫度為190℃,面料運(yùn)行速度為55碼/min,風(fēng)量100r/min,其中蒸汽定型作為對比試驗(yàn)1,天然氣明火熱定型作為實(shí)驗(yàn)1。②定型采用天然氣明火熱定型,面料運(yùn)行速度為55碼/min,風(fēng)量100r/min,定型溫度分別以低于185℃(選取其中的170℃、180℃和183℃作為代表)、185-195℃(選取其中的185℃、187℃、189℃、191℃、193℃、195℃作為代表)、高于195℃(選取其中的197℃、200℃作為代表)三個(gè)區(qū)間對預(yù)定型溫度的影響進(jìn)行實(shí)驗(yàn)。③定型采用天然氣明火熱定型,溫度為190℃,風(fēng)量100r/min,面料運(yùn)行速度分別以低于50碼/min(選取其中的45碼/min、47碼/min作為代表)、50-60碼/min(選取其中的50碼/min、54碼/min、56碼/min、60碼/min作為代表)、高于60碼/min(選取其中的62碼/min、65碼/min作為代表)三個(gè)區(qū)間對運(yùn)行速度的影響進(jìn)行實(shí)驗(yàn)。④定型采用天然氣明火熱定型,溫度為190℃,面料運(yùn)行速度為55碼/min,風(fēng)量分別以低于80r/min(選取其中的70r/min、75r/min作為代表)、80-120r/min(選取其中的82r/min、89r/min、97r/min、105r/min、112r/min、120r/min作為代表)和高于120r/min(選取其中的123r/min、125r/min、130r/min作為代表)三個(gè)區(qū)間對風(fēng)量的影響進(jìn)行實(shí)驗(yàn)。(2)染色工序中,結(jié)合圖1,染色采用一浴染色,待處理錦包棉羅馬布進(jìn)氣流缸,浴比為1:3,從a→b階段,升溫速率為4℃/min,浴溫升至40℃,加入冰醋酸再次升溫,由b→c階段,升溫速率為2℃/min,升溫至70℃,加入黑色酸性染料0.5%(浙江龍盛控股有限公司),加入氯化稀土助劑0.8%后,保溫20min,再次升溫由c→d階段,升溫速率為1.3℃/min,升溫至98℃,保溫30min,加入元明粉,保溫15min,加入純堿和黑色活性染料0.5%(耐高溫k系列),保溫30min,完成染色。染色后的羅馬布對色、水洗后出缸進(jìn)入皂洗機(jī)。(3)結(jié)合圖2,皂洗工序中,皂洗機(jī)內(nèi)皂洗液溫度逐漸升溫,升溫速率為4℃/min,至70℃后,將升溫速率降低至2℃/min,升溫至80℃后,保溫15min后,再以4℃/min降溫至40℃,控制ph為4.5-8.5,出缸,完成皂洗。(4)烘干工序中,烘干溫度為185℃,面料運(yùn)行速度為60碼/min。(5)成品工序中,控制溫度為190℃,面料運(yùn)行速度為20-30碼/min。本實(shí)施例對預(yù)定型的各參數(shù)影響進(jìn)行實(shí)驗(yàn),通過上述四組實(shí)驗(yàn)可以看出,①蒸汽定型則容易因?yàn)檎羝霈F(xiàn)波動(dòng)和流動(dòng)導(dǎo)致預(yù)定型不穩(wěn)定,從而影響羅馬布表面的手感不勻。采用天然氣明火熱定型,預(yù)定型氛圍較為干燥,且不需要考慮空氣的濕度等動(dòng)態(tài)因素,因此預(yù)定型效果穩(wěn)定且均勻,體現(xiàn)在面料上則表現(xiàn)為織物表面的手感均勻且沒有濕、潮觸感。②定型溫度過低,則定型時(shí)間會(huì)延長,相同運(yùn)行速度和風(fēng)量下,隨著定型溫度的增加,面料舒展程度越高,當(dāng)溫度超過185℃時(shí),這種舒展性較為適宜,此時(shí),面料的手感、預(yù)定型的均勻性俱佳,為后續(xù)的染色、皂洗提供了前提;繼續(xù)增加定型溫度,則由于溫度過高,會(huì)出現(xiàn)定型過度,導(dǎo)致面料僵化,染料不易上染,處理效果反倒不佳,且能耗較大;③相同預(yù)定型溫度和風(fēng)量下,面料運(yùn)行速度越慢,則面料受熱定型時(shí)間越長,則定型效果越顯著,但速度過慢,一則影響處理效率和整體加工量,二則對實(shí)際處理效果提升不顯著,面料運(yùn)行速度在50-60碼之間時(shí),處理效率和處理效果匹配較好;④相同與定型溫度和面料運(yùn)行速度下,隨著風(fēng)量的增大,處理效率逐漸提高,尤其是當(dāng)風(fēng)量超過80r/min時(shí),定型效率較佳,但風(fēng)量過大,容易引起面料波動(dòng),不利于平整處理,因此風(fēng)量最高不宜超過120r/min。預(yù)定型溫度、運(yùn)行速度和風(fēng)量三者相互影響,當(dāng)溫度為185-195℃,面料運(yùn)行速度為50-60碼/min,風(fēng)量80-120r/min時(shí),尤其是當(dāng)溫度為190℃、運(yùn)行速度55碼/min、風(fēng)量100r/min時(shí),羅馬面料處于最佳伸展?fàn)顟B(tài),使面料在染色過程中可以更加充分的與染料接觸,從而有利于其染色的有效進(jìn)行,從而減少了染色過程和皂洗過程中水和染料的使用量。實(shí)施例2:染色工序和皂洗工序?qū)μ幚硇Ч挠绊懕緦?shí)施例錦包棉羅馬布一浴染色工藝,其加工流程為:翻布→氣蒸→預(yù)定型→染色→對色→水洗→皂洗→烘干→成品。其中:(1)預(yù)定型工序,定型方式采用天然氣明火熱定型,溫度為190℃,面料運(yùn)行速度為55碼/min,風(fēng)量100r/min。(2)染色工序中,結(jié)合圖1,染色采用一浴染色,染色浴比為1:3,a→b階段升溫速率為4℃/min,浴溫升至40℃,加入冰醋酸;b→c階段升溫速率為2℃/min,升溫至70℃,加入酸性染料0.5%、氯化稀土助劑1%后,保溫10min,;c→d階段升溫速率為1.3℃/min,升溫至98℃后,保溫30min,加入元明粉40g/l,保溫15min,加入純堿和活性染料0.5%,保溫30min上染完畢;(3)皂洗工序中,f→g階段升溫速率為4℃/min,浴溫升至70℃;g→h階段升溫速率為2℃/min,升溫至80℃,保溫15min(即h→i);i→j階段以4℃/min降溫至40℃,控制ph為7左右出缸,完成皂洗。(4)烘干工序中,烘干溫度為185℃,面料運(yùn)行速度為60碼/min。(5)成品工序中,控制溫度為190℃,面料運(yùn)行速度為20-30碼/min。對比實(shí)施例2a染色工序升溫速率均為4℃/min,其他工藝與實(shí)施例2相同。對比實(shí)施例2b染色工序升溫速率均為1.3℃/min,其他工藝與實(shí)施例2相同。對比實(shí)施例2c皂洗工序中升溫和降溫速率均為4℃/min,其他工藝與實(shí)施例2相同。對比實(shí)施例2d皂洗工序中升溫和降溫速率均為2℃/min,其他工藝與實(shí)施例2相同。表1不同時(shí)是狀態(tài)下的染色效果對照表勻染性(級別)色牢度(級別)手感實(shí)施例24.5-54.5-5柔軟對比例2a4.53-4發(fā)硬對比例2b43.5柔軟對比例2c3-44發(fā)硬對比例2d43.5柔軟實(shí)施例2的產(chǎn)品不僅手感柔軟,面料應(yīng)用于內(nèi)衣等加工時(shí),穿著舒適性好,而且通過不同階段溫度和升溫速率的控制,實(shí)現(xiàn)了活性染料與酸性染料染色的一浴染色,耗水量至少降低40-60%,工序縮短,皂洗和染色的均勻性、色牢度均得到改善。實(shí)施例3:染色水和皂洗水的利用本實(shí)施例錦包棉羅馬布一浴染色工藝,其加工流程為:翻布→氣蒸→預(yù)定型→染色→對色→水洗→皂洗→烘干→成品。其中:(1)預(yù)定型工序中:采用天然氣明火熱定型,溫度為190℃,面料運(yùn)行速度為55碼/min,風(fēng)量100r/min。(2)染色工序中,結(jié)合圖1,染色采用一浴染色,染色浴比為1:3,a→b階段升溫速率為4℃/min,浴溫升至40℃,加入冰醋酸;b→c階段升溫速率為2℃/min,升溫至70℃,加入酸性染料1.2%、氯化稀土助劑0.1%后,保溫20min;c→d階段升溫速率為1.3℃/min,升溫至98℃后,保溫30min,加入元明粉,保溫15min,加入純堿和活性染料1.2%,保溫30min上染完畢;(3)皂洗工序中,f→g階段升溫速率為4℃/min,浴溫升至70℃;g→h階段升溫速率為2℃/min,升溫至80℃,保溫15min(即h→i);i→j階段以4℃/min降溫至40℃,控制ph為6.5出缸,完成皂洗。(4)烘干工序中,烘干溫度為185℃,面料運(yùn)行速度為60碼/min。(5)成品工序中,控制溫度為190℃,面料運(yùn)行速度為20-30碼/min。不僅手感柔軟,面料應(yīng)用于內(nèi)衣等加工時(shí),穿著舒適性好,而且通過不同階段溫度和升溫速率的控制,實(shí)現(xiàn)了活性染料與酸性染料染色的一浴染色,耗水量至少降低40-60%,工序縮短,皂洗和染色的均勻性、色牢度均得到改善。染色工序和皂洗工序中,染液和皂洗液中的水直接以河水作為水源,將該河水(如曹娥江水)過濾、軟化至硬度在40ppm以下,也可將加工過程中產(chǎn)生的染液廢水、皂洗廢水進(jìn)行收集,通過厭氧法深度處理后至硬度不超過0.01ppm作為回用水回用至染色或皂洗工序中。其中以河水作為原始水源時(shí),只需要將其硬度進(jìn)行控制即可滿足本申請的一浴染色工藝要求;采用廢水回用時(shí),由于染色過程中冰醋酸、純堿和皂洗中堿性皂洗液的添加,本身就中和了其自身的ph,并將加工過程中的染料等物質(zhì)轉(zhuǎn)化為固體沉淀,因此,厭氧法深度處理后的硬度通常都會(huì)在0.01ppm以下,其品質(zhì)較自來水更佳,而生產(chǎn)中的回用率可達(dá)到50-60%左右,從而減少了廢水的排放和實(shí)際廢水的產(chǎn)生。實(shí)施例4:染色助劑對羅馬布處理效果的影響本實(shí)施例錦包棉羅馬布一浴染色工藝,其加工流程為:翻布→氣蒸→預(yù)定型→染色→對色→水洗→皂洗→烘干→成品。其中:(1)預(yù)定型工序,定型方式采用天然氣明火熱定型,溫度為190℃,面料運(yùn)行速度為55碼/min,風(fēng)量100r/min。(2)染色工序中,結(jié)合圖1,染色采用一浴染色,染色浴比為1:3,a→b階段升溫速率為4℃/min,浴溫升至40℃,加入冰醋酸;b→c階段升溫速率為2℃/min,升溫至70℃,加入酸性染料1%、氯化稀土助劑0.5%后,保溫15min,;c→d階段升溫速率為1.3℃/min,升溫至98℃后,保溫30min,加入元明粉45g/l,保溫15min,加入純堿和活性染料1%,保溫30min上染完畢;(3)皂洗工序中,f→g階段升溫速率為4℃/min,浴溫升至70℃;g→h階段升溫速率為2℃/min,升溫至80℃,保溫15min(即h→i);i→j階段以4℃/min降溫至40℃,控制ph為4.5-8.5(國標(biāo)要求)或6.5-7.5(歐標(biāo)要求)出缸,完成皂洗。(4)烘干工序中,烘干溫度為185℃,面料運(yùn)行速度為60碼/min。(5)成品工序中,控制溫度為190℃,面料運(yùn)行速度為20-30碼/min。本實(shí)施4中氯化稀土助劑為氯化鑭、氯化鈰,對比例4a中不添加氯化稀土試劑,對比例4b中采用勻染劑o代替氯化稀土助劑,其他工藝步驟與實(shí)施例4相同。對比例4c中氯化鑭在加入冰醋酸后添加,對比例4d中氯化鑭在加入活性染料后添加,其他工藝步驟與實(shí)施例4相同。表2不同實(shí)施條件對染色效果的影響勻染性(級別)色牢度(級別)實(shí)施例4氯化鑭4.5-54.5-5實(shí)施例4氯化鈰44對比例4a3.54對比例4b43-4對比例4c44對比例4d3.5-43.5本發(fā)明的產(chǎn)品不僅手感柔軟,面料應(yīng)用于內(nèi)衣等加工時(shí),穿著舒適性好,而且通過不同階段溫度和升溫速率的控制,實(shí)現(xiàn)了活性染料與酸性染料染色的一浴染色,耗水量至少降低40-60%,工序縮短。通過上述幾組實(shí)驗(yàn)可以看出皂洗和染色的均勻性、色牢度均得到改善。當(dāng)前第1頁12