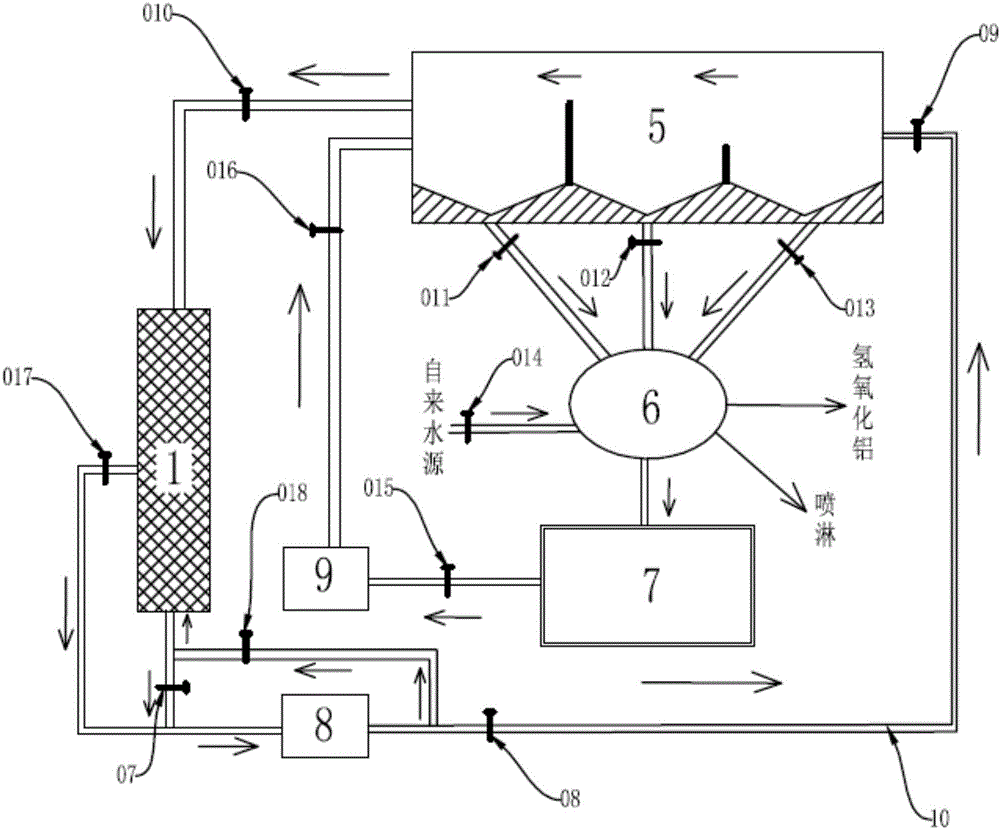
本發(fā)明涉及鋁合金陽極氧化表面前處理
技術(shù)領(lǐng)域:
,尤其涉及鋁前處理堿性三合一及堿液再生和氫氧化鋁在線回收工藝。
背景技術(shù):
:傳統(tǒng)的鋁合金堿蝕工藝已沿用了100多年。堿蝕具有鋁耗高、堿耗高、堿渣多、工藝難控制、缺陷多、生產(chǎn)成本高、環(huán)境污染大等弊端,早已被業(yè)界所公認(rèn)?,F(xiàn)有的標(biāo)準(zhǔn)堿蝕氧化線槽位布置圖3所示,其中、4#、7#、10#、13#和16#槽為工作槽,每個(gè)工作槽配兩個(gè)流動(dòng)水洗槽,氧化前處理需要9個(gè)槽位,4#堿蝕槽為表面前處理主要工作槽。氧化前處理各槽功能如下:(1)1#除油槽:除油的目的是除去自然氧化膜、手指紋及與油脂粘在一起的污物,以保障鋁材表面能均勻腐蝕,并保護(hù)堿蝕槽的清潔。除油不好,堿蝕就不均勻,氧化著色后存在花斑、表面不均等瑕疵?;瘜W(xué)除油可采用堿性、中性或酸性除油劑。國內(nèi)一般采用氧化廢酸除油,有時(shí)加入少量陽離子或兩性表面活性劑,提高除油效率。存在如下不足:1、對(duì)存放時(shí)間長的鋁材,除油不好,自然氧化膜不能脫干凈,堿蝕不均勻,鋁材表面出現(xiàn)不同光澤,氧化著色不均勻;2、除油槽含150-200g/L硫酸,容易帶入堿蝕槽,中和燒堿;為了加強(qiáng)除油能力,部分生產(chǎn)廠家在除油槽中添加5-15g/L左右的氟化氫銨,徹底消除除油隱患,但增加了處理含氟和氨氮廢水的壓力。(2)2#和3#流動(dòng)水洗槽:2#和3#為流動(dòng)水洗槽,自來水由3#槽流入,2#槽流出,反向串聯(lián)。設(shè)置兩道水洗的目的是清洗1#槽帶出的酸液,保護(hù)堿蝕槽。鋁材從1#槽的強(qiáng)酸到4#的強(qiáng)堿,中間水洗槽的用水量是關(guān)鍵,一般為3.0-5.0噸/噸材。如此大的水量,依然會(huì)有部分酸液帶進(jìn)堿蝕槽。(3)4#堿蝕槽:堿蝕的目的是去自然氧化膜,進(jìn)一步除油,增加鋁材亮度,或起砂、去紋,做亞光材。堿蝕時(shí)鋁和堿蝕液發(fā)生如下化學(xué)反應(yīng):Al2O3+2NaOH=2NaAlO2+H2O(去自然氧化膜)(1)Al+2NaOH+2H2O=2NaAlO2+3H2↑(溶解鋁、整平、起砂)(2)NaAlO2+2H2O=Al(OH)3↓+NaOH(生成氫氧化鋁、再生堿液)(3)2Al(OH)3=Al2O3.3H2O(槽壁結(jié)垢、堵塞管道)(4)(2)+(3)式,鋁材在堿槽反應(yīng)的本質(zhì)為2Al+6H2O=2Al(OH)3↓+3H2↑(5)即鋁跟水反應(yīng),生成氫氧化鋁的同時(shí),可再生全部氫氧化鈉。按反應(yīng)式(2)-(5),目前采用了兩種堿蝕方案,一是不加絡(luò)合劑的堿回收方案,二是加絡(luò)合劑的起砂去紋方案。日本采用的堿蝕工藝,一般堿蝕槽不加添加劑,利用拜耳法,再生堿液,回收氫氧化鋁。4#槽配備抽渣系統(tǒng),如4圖所示;當(dāng)游離堿控制在60g/L、鋁離子濃度接近30g/L時(shí),偏鋁酸鈉分解成氫氧化鋁和氫氧化鈉,氫氧化鋁沉渣由抽渣系統(tǒng)處理,回收氫氧化鋁,清渣后的清液抽回4#槽,堿液再生。意大利采用的堿蝕工藝,在堿蝕槽加添加劑,如山梨醇、葡鈉等,利用多羥基化合物中的仲醇基CHOH絡(luò)合鋁離子,反應(yīng)式為:C6H14O6+3NaAlO2=Al3C6H11O9+3NaOH(山梨醇絡(luò)合鋁離子)(6)3NaC6H11O7+NaAlO2+2H2O=Al(C6H11O7)3+4NaOH(葡鈉絡(luò)合鋁離子)(7)當(dāng)鋁的溶解和鋁離子的帶出平衡時(shí),鋁離子濃度可達(dá)80-120g/L,槽液穩(wěn)定,不清槽。(4)5#和6#流動(dòng)水洗槽:設(shè)置這兩道流動(dòng)水洗槽的目的是清洗堿液,保護(hù)中和槽。同樣,自來水從6#槽進(jìn),5#槽出,反向串聯(lián)。鋁材從強(qiáng)堿到強(qiáng)酸,需大量水洗,一般水耗為3.0-5.0噸/噸材,4#槽加堿蝕劑后,粘度更大,水洗壓力更大,部分堿液帶進(jìn)7#中和槽在所難免,消耗中和槽酸液。(5)7#中和槽:設(shè)置7#中和槽的目的是除去殘留于鋁材上灰狀附著物,溶去在堿槽不溶的錳、銅、鐵等合金元素或雜質(zhì),以獲得較光亮的金屬表面,同時(shí)中和鋁材表面殘留的堿液。如果掛灰沒有除凈,將導(dǎo)致著色后光澤發(fā)暗。國內(nèi)鋁型材廠很長一段時(shí)間采用單一硫酸中和,雜質(zhì)少的型材用單一硫酸可以達(dá)到質(zhì)量要求,既可利用氧化廢酸,還可避免交叉污染,成本低。對(duì)于一些用廢鋁多的企業(yè),型材中鐵、銅、錳嚴(yán)重超標(biāo),堿蝕后鋁材表面上有一層厚厚的黑灰,這時(shí)僅硫酸很難除凈。許多廠家采用150-200g/L的硫酸,30-50g/L的硝酸混合,能徹底除灰。添加硝酸的另一個(gè)好處是利用其鈍化作用,保護(hù)鋁材,使其在氧化前的水洗待料期間不產(chǎn)生點(diǎn)蝕和雪花狀腐蝕。但硝酸的使用,需要大量水洗,以防帶入氧化槽;含硝酸根的廢水,增加了處理氨氮的壓力。(6)8#和9#水洗槽:設(shè)置這兩道水洗槽的目的是清洗中和槽液,保護(hù)氧化槽。同樣,自來水從9#槽進(jìn),8#槽出,反向串聯(lián)。鋁材從中和槽到氧化槽,需大量水洗,降低硝酸帶進(jìn)氧化槽的風(fēng)險(xiǎn),一般水耗為3.0-5.0噸/噸材。(7)10#氧化槽:本槽的功能是制氧化膜。隨著氧化量的增加,氧化槽的鋁離子不斷上升,當(dāng)鋁離子濃度超過20g/L時(shí),氧化膜疏松,部分廠家倒掉一些氧化液,部分廠家采用樹脂交換。前者浪費(fèi)大量硫酸,后者浪費(fèi)大量用水。另外,本槽的氧化溫度控制在18-22℃,需要制冷,低溫下電阻太大,耗電量太大,標(biāo)準(zhǔn)膜下,噸材耗電量為1000度,有很大的節(jié)能降耗空間。氧化槽的氧化溫度、電導(dǎo)率、極板距離和鋁離子的方法處理亟需改進(jìn)。除西飛鋁業(yè)等少數(shù)廠家采用日本堿蝕工藝外,我國大部分鋁加工廠采用意大利工藝,兩種方法各有利弊。日本的堿蝕工藝,采用堿液再生,回收氫氧化鋁的生產(chǎn)方式,如圖4所示。抽渣系統(tǒng)由沉淀池、晶析池、回收池及配套的閥門、管道和泵組成。打開閥門1、2,開啟泵1,抽取沉淀池清液至堿蝕槽槽底,利用泵1的正向推力,將4#堿蝕槽中分解的氫氧化鋁攪動(dòng),浮起,通過溢流,渾濁的堿蝕液流回沉淀池,沉淀氫氧化鋁,沉淀池清液再由泵1抽回4#堿蝕槽。如此循環(huán),氫氧化鋁在沉淀池中不斷累積。打開閥門4、5、6,開啟泵2,將沉淀池池底的沉淀抽至析晶池,開啟攪拌,氫氧化鋁逐步析出。打開閥門7、8,開啟離心機(jī),堿液流進(jìn)回收池,固體作為氫氧化鋁初級(jí)品回收。關(guān)閉閥門2,打開閥門1、3,開啟泵1,將回收池的堿液抽回堿蝕槽,完成堿回收。意大利的堿蝕工藝,采用鋁離子絡(luò)合方法,堿蝕槽中鋁離子不分解析出,不產(chǎn)生氫氧化鋁,不用抽渣,不配備抽渣系統(tǒng)。絡(luò)合后鋁離子濃度可達(dá)100g/L以上,鋁的溶解和槽液帶出的鋁可動(dòng)態(tài)平衡。按粘性理論,鋁材表面的反應(yīng)速度大于機(jī)械紋溝底的反應(yīng)速度,可去紋、能做砂面材。兩種堿蝕方法,各有利弊:1、從堿蝕后鋁合金的外觀來看,采用堿回收方法,槽液鋁離子濃度低于30g/L,堿蝕時(shí)反應(yīng)過快,鋁耗太高,鋁表面容易產(chǎn)生點(diǎn)蝕和過腐蝕,特別是按圖2的抽渣系統(tǒng)運(yùn)行,泵1不是抽渣,而是吹渣,沉淀從槽底吹起,懸浮于整槽堿蝕液中,鋁合金堿蝕時(shí),懸浮的固體顆粒粘附鋁合金表面,形成點(diǎn)蝕等表面缺陷。若做砂面材,堿蝕時(shí)間在10分鐘以上,由于槽液鋁離子濃度太低,鋁合金腐蝕量太大,去機(jī)械紋不徹底,鋁表面容易形成過腐蝕。采用添加堿蝕劑方法,鋁離子濃度可達(dá)100g/L以上,堿蝕液中無固體顆粒析出,鋁表面無點(diǎn)蝕,無過腐蝕;做磨砂材時(shí),可徹底去機(jī)械紋,砂面細(xì)膩,鋁耗低。2、從藥劑消耗來看,采用堿回收方法,槽液粘度低,槽液帶出消耗??;按(3)式,偏鋁酸鈉分解成氫氧化鋁和氫氧化鈉,回收氫氧化鋁的同時(shí),也回收氫氧化鈉,進(jìn)一步降低堿耗。采用添加堿蝕劑方法,堿蝕槽液粘度高,槽液帶出消耗巨大;按(6)、(7)式,偏鋁酸鈉完全被絡(luò)合,不分解氫氧化鋁,不回收氫氧化鈉。從實(shí)際大生產(chǎn)運(yùn)行來看,添加堿蝕劑方法比堿回收方法,氫氧化鈉的消耗量在3倍以上。3、從鋁消耗來看,采用堿回收方法,槽液鋁離子濃度低,按(1)(2)式,偏鋁酸鈉濃度低,鋁耗高。采用添加堿蝕劑方法,按(6)、(7)式,偏鋁酸鈉完全被絡(luò)合,不分解氫氧化鋁,鋁離子濃度高,按(1)(2)式,鋁耗低。從實(shí)際大生產(chǎn)運(yùn)行來看,添加堿蝕劑方法比堿回收方法,鋁的消耗量在40%以下。4、從槽液管理來看,采用堿回收方法,按圖2的抽渣系統(tǒng)運(yùn)行。按(4)式,氫氧化鋁轉(zhuǎn)化成氧化鋁的水合物鋁垢,附著在堿蝕液經(jīng)過的槽壁、管道、閥門和泵等處,損壞泵和閥門,堵塞管道。為了避免堵塞管道,設(shè)計(jì)泵1不是抽渣,而是吹渣,沉淀物從槽底吹起,利用泵1的正向推力,將4#堿蝕槽中分解的氫氧化鋁攪動(dòng),浮起,通過溢流,渾濁的堿蝕液流回沉淀池,沉淀氫氧化鋁,沉淀池上表面清液通過泵1再抽回堿蝕槽。如此循環(huán),氫氧化鋁在沉淀池中不斷累積。泵1不采用抽渣而用吹渣,根本原因是擔(dān)心4#堿蝕槽槽底的吹渣管結(jié)垢,堵塞管道的緣故。如此吹渣,固體顆粒懸浮于整槽堿蝕液中,鋁合金堿蝕時(shí),懸浮的固體顆粒粘附鋁合金表面,形成點(diǎn)蝕等表面缺陷。盡管部分解決管道堵塞問題,卻埋下了影響鋁合金表面質(zhì)量的隱患。恐怖的是,如圖2所示,抽渣系統(tǒng)由沉淀池、晶析池、回收池及配套的閥門、管道和泵組成,這些池、管、閥和泵,處處都有結(jié)垢堵塞的風(fēng)險(xiǎn),維護(hù)這套系統(tǒng)的正常運(yùn)行,十分困難。采用添加堿蝕劑方法,偏鋁酸鈉被完全絡(luò)合,鋁離子濃度可達(dá)100g/L以上,堿蝕液中無固體顆粒析出,不需要抽渣,鋁的溶解和槽液中帶出的鋁自動(dòng)平衡,槽液非常容易管理,生產(chǎn)簡(jiǎn)單易行。5、從環(huán)保角度來看,采用堿回收方法,槽液粘度低,藥劑帶出消耗小,廢水處理中心處理的廢堿液少,產(chǎn)生的廢堿渣少;按(3)式,偏鋁酸鈉分解成氫氧化鋁和氫氧化鈉,在線回收氫氧化鋁的同時(shí),也回收氫氧化鈉,進(jìn)一步降低堿耗。采用添加堿蝕劑方法,堿蝕槽液粘度高,藥劑帶出消耗巨大;按(6)、(7)式,偏鋁酸鈉完全被絡(luò)合,不分解氫氧化鋁,不回收氫氧化鈉。鋁的溶解完全靠槽液帶出實(shí)現(xiàn)自動(dòng)平衡。從實(shí)際大生產(chǎn)運(yùn)行來看,添加堿蝕劑方法比堿回收方法,槽液帶出消耗在4倍以上。如此大量的堿蝕液帶入5#、6#流動(dòng)水洗槽,流入廢水處理中心,既需要大量的酸中和,還消耗大量的聚丙烯酰胺,產(chǎn)生大量的含鋁廢渣。統(tǒng)計(jì)表明,日產(chǎn)1000噸的鋁加工企業(yè),每天消耗0.5噸聚丙烯酰胺,產(chǎn)生100噸以上廢渣。這些含鋁廢渣,來源于煲模液、堿蝕液和氧化液,其中,堿蝕液的貢獻(xiàn)占80%以上。經(jīng)近百年應(yīng)用,堿蝕工藝的弊端早已暴露無遺。特別是強(qiáng)調(diào)清潔文明生產(chǎn)的今天,這套工藝有以下幾方面需要大幅度改進(jìn):1、工藝設(shè)計(jì)理念不合理。1#和7#為強(qiáng)酸性槽液,4#為強(qiáng)堿性槽液,鋁材需從強(qiáng)酸到強(qiáng)堿、再從強(qiáng)堿到強(qiáng)酸進(jìn)行處理,盡管中間各設(shè)置兩道水洗槽,也難免串槽,工作槽的藥劑互相消耗;2、工藝復(fù)雜,槽位多。氧化槽前面一共9個(gè)槽位,3個(gè)工作槽,6個(gè)水洗槽,過于繁雜;3、功效低。鋁材氧化前要經(jīng)過9個(gè)槽,其中3個(gè)工作槽還要占用反應(yīng)時(shí)間,一般一掛材從1#除油槽到9#水洗待料槽需要25-30分鐘。耗時(shí)長,嚴(yán)重制約了氧化線的產(chǎn)能;4、工作槽多,化學(xué)藥劑消耗量大。1#、4#、7#為工作槽,總藥劑消耗量為60-80公斤/噸材,為處理含這些化學(xué)藥劑的廢水,鋁材廠要花更大的成本;5、水洗槽多,用水量大。6個(gè)水洗槽,總水消耗量為10.0-15.0噸/噸材。除用水成本外,這些廢水的處理和排放,都需額外付出環(huán)保成本;6、1#槽含氟,妨礙了廢水回用;7、1#和7#槽含氨氮,使廢水處理的難度雪上加霜。含氟廢水不能回用,含氨氮廢水又不能排放,廠家陷入氨氮處理的困局。8、4#堿蝕槽,少部分鋁加工廠選用堿回收方法,大部分廠家選用添加堿蝕劑方法。前者損失鋁合金外觀質(zhì)量,抽渣系統(tǒng)結(jié)垢,難以控制;后者堿耗高,廢水處理成本高,廢渣太多,環(huán)保壓力大;9、堿蝕液中的鋁離子,經(jīng)過5#、6#流動(dòng)水洗槽,進(jìn)入廢水中心,形成工業(yè)廢渣,既浪費(fèi)鋁資源,又增加環(huán)保壓力。鋁加工企業(yè)所產(chǎn)生的工業(yè)廢渣,主要來自煲模液、堿蝕液和氧化液,其中堿蝕液貢獻(xiàn)80%以上。堿蝕槽添加絡(luò)合劑,鋁離子不分解析出,鋁的溶解和帶出可實(shí)現(xiàn)動(dòng)態(tài)平衡,除滿足鋁材外觀質(zhì)量要求外,槽液管理非常簡(jiǎn)單,但忽略一個(gè)致命的缺陷,即高鋁離子濃度、高粘度的堿蝕液帶入5#、6#流動(dòng)水洗槽,進(jìn)入廢水中心,形成工業(yè)廢渣,既浪費(fèi)鋁資源,帶來巨大的環(huán)保處理壓力。技術(shù)實(shí)現(xiàn)要素:本發(fā)明的目的在于提出鋁前處理堿性三合一及堿液再生和氫氧化鋁在線回收工藝,具有廢水零排放、減少工業(yè)廢渣、藥耗低、節(jié)約用水,不結(jié)垢堵塞,同時(shí)實(shí)現(xiàn)堿液和氫氧化鋁在線回收等特點(diǎn)。為達(dá)此目的,本發(fā)明采用以下技術(shù)方案:鋁前處理堿性三合一及堿液再生和氫氧化鋁在線回收工藝,包括藥劑回收系統(tǒng)和兩個(gè)流動(dòng)水洗槽;所述藥劑回收系統(tǒng)包括堿性三合一磨砂槽和不流動(dòng)水洗槽子系統(tǒng);所述不流動(dòng)水洗槽子系統(tǒng)通過第一閥門與所述堿性三合一磨砂槽反向串聯(lián)設(shè)置;所述不流動(dòng)水洗槽子系統(tǒng)包括第一不流動(dòng)水洗槽和第二不流動(dòng)水洗槽,所述第一不流動(dòng)水洗槽和所述第二不流動(dòng)水洗槽通過第二閥門反向串聯(lián)設(shè)置,且所述第二不流動(dòng)水洗槽沿水流動(dòng)方向的始端還設(shè)有補(bǔ)水口和第三閥門;兩個(gè)所述流動(dòng)水洗槽反向串聯(lián)設(shè)置,且沿水流動(dòng)方向的始端設(shè)有進(jìn)水口,終端的出水口連接于所述第二不流動(dòng)水洗槽的補(bǔ)水口。進(jìn)一步說明,所述堿性三合一磨砂槽的槽底設(shè)計(jì)為120°的楔形凹面,所述楔形凹面最低位設(shè)置有貫穿所述堿性三合一磨砂槽的抽渣管。進(jìn)一步說明,所述堿性三合一磨砂槽內(nèi)的槽液為堿性槽液,所述堿性槽液中的游離堿濃度NaOH與鋁離子濃度Al3+之比為3.5-4.0。進(jìn)一步說明,所述堿性三合一磨砂槽內(nèi)的槽液還含有氯化鈉,所述氯化鈉的濃度為20-40g/L。進(jìn)一步說明,所述堿性三合一磨砂槽還設(shè)置有堿液再生及氫氧化鋁的回收系統(tǒng),所述堿液再生及氫氧化鋁的回收系統(tǒng)包括沉淀池、離心機(jī)、收集池、一號(hào)泵,二號(hào)泵和管道;所述堿性三合一磨砂槽通過管道從其抽渣管的抽渣輸出端依次連接所述一號(hào)泵和所述沉淀池的抽渣輸入端,并由所述沉淀池的抽渣輸出端回至其抽渣輸入端,并通過第一控制裝置調(diào)控,形成抽渣循環(huán)子系統(tǒng);所述堿性三合一磨砂槽通過管道從其疏渣輸出端連接所述一號(hào)泵回至其疏渣輸入端,并通過第二控制裝置調(diào)控,形成堵塞自救子系統(tǒng);所述沉淀池通過管道從其離心輸出端依次連接所述離心機(jī)、收集池和二號(hào)泵回至其離心輸入端,并通過第三控制裝置調(diào)控,形成氫氧化鋁和堿液的回收子系統(tǒng)。進(jìn)一步說明,所述第一控制裝置包括七號(hào)閥門、八號(hào)閥門、九號(hào)閥門和十號(hào)閥門,其分別設(shè)置于所述管道上;所述七號(hào)閥門位于所述堿性三合一磨砂槽的抽渣輸出端和所述一號(hào)泵之間;所述八號(hào)閥門位于所述一號(hào)泵的輸出端;所述九號(hào)閥門位于所述沉淀池的抽渣輸入端;所述十號(hào)閥門位于所述沉淀池的抽渣輸出端和所述堿性三合一磨砂槽的抽渣輸入端之間。進(jìn)一步說明,所述第二控制裝置包括氫氧化鋁回收控制裝置和堿液回收控制裝置,分別設(shè)置于所述管道上;所述氫氧化鋁回收控制裝置包括十一號(hào)閥門、十二號(hào)閥門、十三號(hào)閥門和十四號(hào)閥門;所述十一號(hào)閥門、十二號(hào)閥門和十三號(hào)閥門分別設(shè)置于所述沉淀池的離心輸出端和所述離心機(jī)之間的不同管道上;所述十四號(hào)閥門設(shè)置于所述離心機(jī)連接自來水源的管道上;所述堿液回收控制裝置包括十五號(hào)閥門和十六號(hào)閥門;所述十五號(hào)閥門設(shè)置于所述收集池的輸出端和所述二號(hào)泵之間,所述十六號(hào)閥門設(shè)置于所述二號(hào)泵和沉淀池的離心輸入端。進(jìn)一步說明,所述第三控制裝置包括十七號(hào)閥門和十八號(hào)閥門,分別設(shè)置于所述管道上;所述十七號(hào)閥門設(shè)置于所述堿性三合一磨砂槽的疏渣輸入端和所述一號(hào)泵之間,所述十八號(hào)閥門設(shè)置于所述堿性三合一磨砂槽的疏渣輸出端和所述一號(hào)泵之間;所述疏渣輸入端設(shè)置于所述堿性三合一磨砂槽的上表面,所述疏渣輸出端設(shè)置于所述堿性三合一磨砂槽的槽底。本發(fā)明的有益效果:(1)本發(fā)明吸取了傳統(tǒng)堿蝕前處理使用含氟及氨氮化學(xué)藥品的教訓(xùn),擯棄沿用多年的氟化氫銨和硝酸,重新設(shè)計(jì)鋁合金陽極氧化前處理方案,杜絕含氟、含銨的成分,確保整條氧化線前處理無氟無銨,實(shí)現(xiàn)鋁加工廠充分回收、循環(huán)用水,廢水零排放,降低廢水處理成本;(2)吸取了傳統(tǒng)工藝功能槽太多、工藝太復(fù)雜、藥耗太高的教訓(xùn),將除油、堿蝕、中和三槽的功能集于一槽,三槽合一,采用一個(gè)藥槽處理鋁材,省去了原有堿蝕工藝的二個(gè)功能槽,藥劑消耗量由堿蝕工藝的60-80公斤/噸材,減少為20-30公斤/噸材,少用藥劑60%以上,降低藥耗,省水,不串槽,提高功效;(3)吸取了傳統(tǒng)堿蝕工藝水洗槽太多、水耗太高的教訓(xùn),將原堿蝕工藝的6個(gè)水洗槽減少為4個(gè),其中兩個(gè)為不流動(dòng)水洗,耗水量由10.0-15.0噸/噸材減少為3-4噸/噸材,節(jié)水60%以上;并將由堿性三合一磨砂槽與不流動(dòng)水洗槽子系統(tǒng)組成的藥劑回收系統(tǒng),通過反向串聯(lián),反向流動(dòng),不流動(dòng)水洗槽子系統(tǒng)清洗鋁材、逐級(jí)截留回收藥劑,藥劑回收率80%以上,降低堿性三合一磨砂槽的葯耗;(4)選用堿回收方案,改進(jìn)堿性槽液,大幅提高游離堿濃度,堿液中可分解氫氧化鋁并在線回收,但不能形成鋁垢,徹底杜絕鋁垢堵塞管道、閥門和泵的弊端;(5)重新設(shè)計(jì)抽渣系統(tǒng),改堿蝕槽吹渣為抽渣,保持堿蝕槽槽液清晰,避免鋁合金表面產(chǎn)生點(diǎn)蝕等缺陷;(6)取消晶析池及其攪拌系統(tǒng),確保氫氧化鋁晶粒長大,晶粒大于45微米的質(zhì)量分?jǐn)?shù)大于85%,滿足國標(biāo)GB4294-2010的要求;綜上所述,在確保少用水、少用藥、少出渣的前提下,實(shí)現(xiàn)了氫氧化鋁在線回收,變廢為寶,減少鋁資源的巨大浪費(fèi)。附圖說明圖1是本發(fā)明一個(gè)實(shí)施例的鋁前處理堿性三合一及堿液再生和氫氧化鋁在線回收工藝的槽位布置圖;圖2是本發(fā)明一個(gè)實(shí)施例的堿液再生及氫氧化鋁的回收系統(tǒng)圖;圖3是現(xiàn)有的標(biāo)準(zhǔn)堿蝕氧化線槽位布置圖;圖4是現(xiàn)有的堿蝕槽利用拜耳法再生堿液、回收氫氧化鋁的示意圖;其中:堿性三合一磨砂槽1,第一不流動(dòng)水洗槽2,第二不流動(dòng)水洗槽3,流動(dòng)水洗槽4,沉淀池5,離心機(jī)6,收集池7,一號(hào)泵8,二號(hào)泵9,管道10,第一閥門01,第二閥門02,第三閥門03,補(bǔ)水口04,進(jìn)水口05,出水口06,七號(hào)閥門07,八號(hào)閥門08,九號(hào)閥門09,十號(hào)閥門010,十一號(hào)閥門011,十二號(hào)閥門012,十三號(hào)閥門013,十四號(hào)閥門014,十五號(hào)閥門015,十六號(hào)閥門016,十七號(hào)閥門017,十八號(hào)閥門018。具體實(shí)施方式下面結(jié)合附圖并通過具體實(shí)施方式來進(jìn)一步說明本發(fā)明的技術(shù)方案。鋁前處理堿性三合一及堿液再生和氫氧化鋁在線回收工藝,包括藥劑回收系統(tǒng)和兩個(gè)流動(dòng)水洗槽4;所述藥劑回收系統(tǒng)包括堿性三合一磨砂槽1和不流動(dòng)水洗槽子系統(tǒng);所述不流動(dòng)水洗槽子系統(tǒng)通過第一閥門01與所述堿性三合一磨砂槽1反向串聯(lián)設(shè)置;所述不流動(dòng)水洗槽子系統(tǒng)包括第一不流動(dòng)水洗槽2和第二不流動(dòng)水洗槽3,所述第一不流動(dòng)水洗槽2和所述第二不流動(dòng)水洗槽3通過第二閥門02反向串聯(lián)設(shè)置,且所述第二不流動(dòng)水洗槽3沿水流動(dòng)方向的始端還設(shè)有補(bǔ)水口04和第三閥門03;兩個(gè)所述流動(dòng)水洗槽4反向串聯(lián)設(shè)置,且沿水流動(dòng)方向的始端設(shè)有進(jìn)水口05,終端的出水口06連接于所述第二不流動(dòng)水洗槽的補(bǔ)水口04。本發(fā)明提出鋁前處理堿性三合一及堿液再生和氫氧化鋁在線回收工藝,所述藥劑回收系統(tǒng)的工作原理為:當(dāng)堿性三合一磨砂槽1截留回收藥劑或補(bǔ)充液位時(shí),打開所述第三閥門,使所述不流動(dòng)水洗槽中的自來水由所述補(bǔ)水口進(jìn)入所述第二不流動(dòng)水洗槽;打開所述第二閥門,則所述第二不流動(dòng)水洗槽中的截留液進(jìn)入所述第一不流動(dòng)水洗槽;打開所述第一閥門,所述第一不流動(dòng)水洗槽中的截留液進(jìn)入所述堿性三合一磨砂槽1,從而實(shí)現(xiàn)了梯級(jí)截留回收藥劑和補(bǔ)充所述三合一磨砂槽1液位的效果。本發(fā)明不僅將所述堿性三合一磨砂槽取代傳統(tǒng)工藝的堿除油、堿蝕和中和三道工序,實(shí)現(xiàn)了三槽合一,其具有脫脂、去自然氧化膜、去紋、起砂、調(diào)整鋁合金底色、去灰,同時(shí)分解生成氫氧化鋁的功能;而且還通過所述不流動(dòng)水洗槽子系統(tǒng),與堿性三合一磨砂槽1形成了藥劑回收系統(tǒng),通過相互反向串聯(lián)設(shè)置,從而達(dá)到了截留藥劑、清洗鋁材、補(bǔ)充所述堿性三合一磨砂槽1液位的效果;并且將兩個(gè)所述流動(dòng)水洗槽反向串聯(lián)設(shè)置,所述流動(dòng)水洗槽的進(jìn)水口可連接氧化槽,則進(jìn)水為氧化槽后的清洗用水,故所述流動(dòng)水洗槽的進(jìn)水為酸性,正好中和鋁合金表面的堿液,有效將傳統(tǒng)堿蝕前處理清洗水需要有3個(gè)進(jìn)水口和3個(gè)出水口變成只需一個(gè)1進(jìn)水口和1出水口。進(jìn)一步說明,所述堿性三合一磨砂槽1的槽底設(shè)計(jì)為120°的楔形凹面,所述楔形凹面最低位設(shè)置有貫穿所述堿性三合一磨砂槽1的抽渣管。將所述堿性三合一磨砂槽1設(shè)置為120°的楔形凹面,并將所述楔形凹面與抽渣管相互配合,從而使槽底內(nèi)的沉淀物更好地匯聚沉積于一起,再由所述抽渣管進(jìn)出充分地將沉淀物抽走,避免積累過多而導(dǎo)致堵塞。進(jìn)一步說明,所述堿性三合一磨砂槽1內(nèi)的槽液為堿性槽液,所述堿性槽液中的游離堿濃度NaOH與鋁離子濃度Al3+之比為3.5-4.0。游離堿濃度NaOH(g/L)與鋁離子濃度Al3+(g/L)之比在3.5-4.0為阻垢區(qū)間,可滿足堿性槽液的阻垢要求,使所述堿性槽液的工作參數(shù)在阻垢區(qū)間內(nèi)運(yùn)行,確保堿性三合一工藝的槽位長期大規(guī)模生產(chǎn)時(shí)不結(jié)垢,不會(huì)因鋁垢堵塞管道、閥門和泵而停產(chǎn),延長使用壽命,既可完全阻垢,又能適當(dāng)降低鋁耗。進(jìn)一步說明,所述堿性三合一磨砂槽1內(nèi)的槽液還含有氯化鈉,所述氯化鈉的濃度為20-40g/L。通過在所述槽液內(nèi)添加氯化鈉作為起砂去紋的主要成分,并將氯化鈉濃度控制在20-40g/L,可滿足生產(chǎn)磨砂材的要求,從而實(shí)現(xiàn)了所述堿性三合一磨砂槽1還具有起砂去紋的功能。進(jìn)一步說明,所述堿性三合一磨砂槽1還設(shè)置有堿液再生及氫氧化鋁的回收系統(tǒng),所述堿液再生及氫氧化鋁的回收系統(tǒng)包括沉淀池5、離心機(jī)6、收集池7、一號(hào)泵8,二號(hào)泵9和管道10;所述堿性三合一磨砂槽1通過管道10從其抽渣管的抽渣輸出端依次連接所述一號(hào)泵8和所述沉淀池5的抽渣輸入端,并由所述沉淀池5的抽渣輸出端回至其抽渣輸入端,并通過第一控制裝置調(diào)控,形成抽渣循環(huán)子系統(tǒng);所述堿性三合一磨砂槽1通過管道10從其疏渣輸出端連接所述一號(hào)泵8回至其疏渣輸入端,并通過第二控制裝置調(diào)控,形成堵塞自救子系統(tǒng);所述沉淀池5通過管道10從其離心輸出端依次連接所述離心機(jī)6、收集池7和二號(hào)泵9回至其離心輸入端,并通過第三控制裝置調(diào)控,形成氫氧化鋁和堿液的回收子系統(tǒng)。所述堿液再生及氫氧化鋁的回收系統(tǒng)主要形成了抽渣循環(huán)子系統(tǒng)、堵塞自救子系統(tǒng)以及氫氧化鋁和堿液回收子系統(tǒng);所述抽渣循環(huán)子系統(tǒng)由堿性三合一磨砂槽1、沉淀池5、一號(hào)泵8、第一控制裝置和管道10組成;所述堵塞自救子系統(tǒng)由堿性三合一磨砂槽1、一號(hào)泵8、第三控制裝置和管道10組成;所述氫氧化鋁和堿液回收子系統(tǒng)由沉淀池5、離心機(jī)6、收集池7、二號(hào)泵9、第二控制裝置的和管道10組成,從而有效對(duì)所述堿性三合一磨砂槽1進(jìn)行抽渣、對(duì)氫氧化鋁和堿液進(jìn)行在線回收,減少鋁資源的巨大浪費(fèi)和大幅提高游離堿濃度,徹底杜絕鋁垢堵塞管道、閥門和泵的問題。進(jìn)一步說明,所述第一控制裝置包括七號(hào)閥門07、八號(hào)閥門08、九號(hào)閥門09和十號(hào)閥門010,其分別設(shè)置于所述管道10上;所述七號(hào)閥門07位于所述堿性三合一磨砂槽1的抽渣輸出端和所述一號(hào)泵8之間;所述八號(hào)閥門08位于所述一號(hào)泵8的輸出端;所述九號(hào)閥門09位于所述沉淀池5的抽渣輸入端;所述十號(hào)閥門010位于所述沉淀池的抽渣輸出端和所述堿性三合一磨砂槽1的抽渣輸入端之間。通過依次打開所述七號(hào)閥門07、八號(hào)閥門08、九號(hào)閥門09和十號(hào)閥門010,同時(shí)開啟一號(hào)泵8,從而將所述堿性三合一磨砂槽槽底的沉淀物通過所述管道10抽至沉淀池,在所述沉淀池5中,鋁渣沉淀于池底,而沉淀池上表面的清液則經(jīng)過所述十號(hào)閥門010回流至所述堿性三合一磨砂槽1中,從而完成抽渣循環(huán)。進(jìn)一步說明,所述第二控制裝置包括氫氧化鋁回收控制裝置和堿液回收控制裝置,分別設(shè)置于所述管道10上;所述氫氧化鋁回收控制裝置包括十一號(hào)閥門011、十二號(hào)閥門012、十三號(hào)閥門013和十四號(hào)閥門014;所述十一號(hào)閥門011、十二號(hào)閥門012和十三號(hào)閥門013分別設(shè)置于所述沉淀池5的離心輸出端和所述離心機(jī)6之間的不同管道10上;所述十四號(hào)閥門014設(shè)置于所述離心機(jī)連接自來水源的管道10上;所述堿液回收控制裝置包括十五號(hào)閥門015和十六號(hào)閥門016;所述十五號(hào)閥門015設(shè)置于所述收集池7的輸出端和所述二號(hào)泵9之間,所述十六號(hào)閥門016設(shè)置于所述二號(hào)泵9和沉淀池5的離心輸入端。隨著所述抽渣循環(huán)子系統(tǒng)的不斷運(yùn)轉(zhuǎn),則所述沉淀池5中鋁渣不斷積累增多,氫氧化鋁的顆粒不斷變大;當(dāng)所述沉淀池5收集到足夠氫氧化鋁時(shí),則打開所述十一號(hào)閥門011、十二號(hào)閥門012和十三號(hào)閥門013,使鋁渣進(jìn)入離心機(jī)6,同時(shí)開啟離心機(jī)6分離氫氧化鋁和堿液;再打開十四號(hào)閥門014,通過自來水源漂洗氫氧化鋁中的堿液,當(dāng)離心機(jī)的出水口的清洗水為中性時(shí),則停止漂洗,回收氫氧化鋁;最后打開所述十五號(hào)閥門015和十六號(hào)閥門016,同時(shí)開啟二號(hào)泵9,將所述收集池7收集的堿液回收至所述沉淀池5,回收堿液;從而完成所述氫氧化鋁和堿液回收子系統(tǒng)對(duì)氫氧化鋁和堿液的在線回收。進(jìn)一步說明,所述第三控制裝置包括十七號(hào)閥門017和十八號(hào)閥門018,分別設(shè)置于所述管道10上;所述十七號(hào)閥門017設(shè)置于所述堿性三合一磨砂槽1的疏渣輸入端和所述一號(hào)泵8之間,所述十八號(hào)閥門018設(shè)置于所述堿性三合一磨砂槽1的疏渣輸出端和所述一號(hào)泵8之間;所述疏渣輸入端設(shè)置于所述堿性三合一磨砂槽1的上表面,所述疏渣輸出端設(shè)置于所述堿性三合一磨砂槽1的槽底。由于當(dāng)所述堿性三合一磨砂槽1的槽底的沉淀物過多時(shí),則會(huì)影響所述抽渣循環(huán)子系統(tǒng)的有效運(yùn)轉(zhuǎn),因此通過所述堵塞自救子系統(tǒng)進(jìn)行調(diào)控,即打開所述十七號(hào)閥門017和十八號(hào)閥門018,開啟一號(hào)泵8,使槽液通過所述十七號(hào)閥門017從所述堿性三合一磨砂槽1上表面的疏渣輸入端抽入,并且通過所述十八號(hào)閥門018從所述堿性三合一磨砂槽1槽底的疏渣輸出端壓出,從而擠出堵塞于所述管道10中的沉淀物,并且將所述堵塞自救子系統(tǒng)定期進(jìn)行反向循環(huán)運(yùn)行,可確保抽所述抽渣循環(huán)子系統(tǒng)的正常運(yùn)行。關(guān)于堿性三合一磨砂槽1的工作機(jī)理如下:(1)堿性槽液:當(dāng)將鋁材進(jìn)入所述堿性三合一磨砂槽1后,根據(jù)原電池原理,以純鋁相為陽極,合金相為陰極,陽離子向合金相、陰離子向純鋁相移動(dòng),按反應(yīng)式(1)和(2)進(jìn)行化學(xué)反應(yīng):(2)去膜脫脂:根據(jù)反應(yīng)式(1)可知,鋁材進(jìn)該槽后,先去自然氧化膜,在高濃度氫氧化鈉作用下,可除去油污和指紋,省去除油槽。(3)起砂去紋:所述堿性三合一磨砂槽1還具有起砂去紋的功能,即通過在所述槽液內(nèi)添加氯化鈉作為起砂去紋的主要成分。根據(jù)反應(yīng)式(2)可知,純鋁相作為陽極被溶解,與被陽極吸引而來的氯離子相遇;從而點(diǎn)蝕起砂,且砂粒均勻,鋁耗低,去機(jī)械紋徹底;并且氯化物易溶于水,好清洗,不影響待回收氫氧化鋁的品質(zhì)。依據(jù)下述實(shí)驗(yàn)列表,選取槽液中氯化鈉濃度,取游離堿112.5g/L,Al3+30g/L,R=游離堿濃度/鋁離子濃度(NaOH/Al3+)=3.75,60℃,堿蝕12分鐘,結(jié)果如表1所示:表1不同濃度氯化鈉在槽液中的起砂能力NaCl0g/L1020304050鋁材少砂鋁材少砂鋁材好砂鋁材好砂鋁材好砂鋁材好砂由表1可知,將氯化鈉濃度控制在20-40g/L,可滿足生產(chǎn)磨砂材的要求。(4)分解氫氧化鋁、釋放氫氧化鈉:堿性三合一磨砂槽1不添加絡(luò)合劑,按反應(yīng)式(3),當(dāng)鋁離子升高至堿蝕液能容忍的上限時(shí),偏鋁酸鈉分解成氫氧化鋁和氫氧化鈉。(5)徹底阻垢、杜絕反應(yīng)式(4)的化學(xué)反應(yīng)發(fā)生:按(4)式,堿垢為Al2O3.3H2O,附著在槽壁、管道、閥門、泵等一切槽液接觸到的地方,非常堅(jiān)固,很難人工清除。但氧化鋁是兩性化合物,既溶于強(qiáng)酸,也溶于強(qiáng)堿,鋁礬土中的氧化鋁,正是用強(qiáng)堿溶解的,因此在所述堿性槽液中適當(dāng)提高游離堿的濃度,使之既可以分解氫氧化鋁,又可以阻止堿垢的產(chǎn)生。依據(jù)下述實(shí)驗(yàn)列表,可科學(xué)地選取堿性槽液中游離堿濃度NaOH(g/L)與鋁離子濃度Al3+(g/L)之比,即R值(NaOH/Al3+)的阻垢范圍,來回避槽液結(jié)垢。取不同R值,60℃,堿蝕12分鐘,反復(fù)堿蝕鋁材,結(jié)果如表2所示:表2不同R值下堿性槽液的阻垢能力R=1.51.52.02.53.03.54.04.5重垢重垢重垢輕垢略垢無垢無垢無垢由表2可知,將R值控制在3.5-4.0,為阻垢區(qū)間,可滿足堿性槽液的阻垢要求。關(guān)于不流動(dòng)水洗槽子系統(tǒng)的工作機(jī)理如下:(1)清洗鋁材:所述第一不流動(dòng)水洗槽2的清洗時(shí)間為1.5分鐘;所述第二不流動(dòng)水洗槽3的清洗時(shí)間為1分鐘;徹底清洗鋁材帶出的藥劑;(2)截留藥劑:兩個(gè)不流動(dòng)水洗槽逐級(jí)截留。所述堿性三合一磨砂槽1被帶出的藥劑,其濃度成梯級(jí)分布;第一不流動(dòng)水洗槽2的藥劑濃度高,第二不流動(dòng)水洗槽3的藥劑濃度低;(3)回收藥劑、補(bǔ)充液位:堿性三合一磨砂槽1中,水分的蒸發(fā)和藥劑的帶出損失,液位不斷下降,需要補(bǔ)充液位;打開第三閥門,自來水從第二不流動(dòng)水洗槽3進(jìn)入,流經(jīng)第一不流動(dòng)水洗槽2,最后進(jìn)入堿性三合一磨砂槽1,既補(bǔ)充了液位,又實(shí)現(xiàn)了藥劑的逐級(jí)回收。生產(chǎn)方式如下:(1)機(jī)械噴砂材噴砂鋁材直接進(jìn)入堿性三合一磨砂槽1,R=3.75,反應(yīng)5-10分鐘,50-60℃,滴流1分鐘,再經(jīng)第一不流動(dòng)水洗槽2和第二不流動(dòng)水洗槽3,進(jìn)入兩個(gè)所述流動(dòng)水洗槽4清洗;完成氧化前處理。(2)化學(xué)磨砂材鋁材直接進(jìn)入堿性三合一磨砂槽1,反應(yīng)10-15分鐘,50-60℃,滴流1分鐘,再經(jīng)第一不流動(dòng)水洗槽2和第二不流動(dòng)水洗槽3,進(jìn)入兩個(gè)所述流動(dòng)水洗槽4清洗;完成氧化前處理。鋁合金表面前處理堿性三合一工藝是各槽和堿液再生及氫氧化鋁的回收系統(tǒng)密切配合的結(jié)果;堿性三合一磨砂槽1、不流動(dòng)水洗槽子系統(tǒng),以及堿液再生及氫氧化鋁的回收系統(tǒng)是體現(xiàn)本發(fā)明技術(shù)特征的關(guān)鍵。實(shí)施例1(砂面材)鋁材直接進(jìn)入堿性三合一磨砂槽1,R(NaOH/Al3+)3.75,NaCl30g/L,反應(yīng)10-15分鐘,50-60℃,滴流1分鐘;經(jīng)第一不流動(dòng)水洗槽2清洗1.5分鐘,滴流1分鐘,第二不流動(dòng)水洗槽3清洗1分鐘,滴流1分鐘;進(jìn)入兩個(gè)流動(dòng)水洗槽,分別清洗1分鐘,1滴流分鐘,完成氧化前處理。實(shí)施例2(噴砂材)鋁材直接進(jìn)入堿性三合一磨砂槽1,R(NaOH/Al3+)3.75,NaCl30g/L,反應(yīng)5-10分鐘,50-60℃,滴流1分鐘;經(jīng)第一不流動(dòng)水洗槽2清洗1.5分鐘,滴流1分鐘,第二不流動(dòng)水洗槽3清洗1分鐘,滴流1分鐘;進(jìn)入兩個(gè)流動(dòng)水洗槽,分別清洗1分鐘,1滴流分鐘,完成氧化前處理。由實(shí)施例1-2表明,本發(fā)明的堿蝕液可生產(chǎn)化學(xué)磨砂材和機(jī)械噴砂材。實(shí)施例3(NaCl的起砂能力)依據(jù)表1,鋁材直接進(jìn)入堿性三合一磨砂槽1,R(NaOH/Al3+)3.75,NaCl0g/L,反應(yīng)5-10分鐘,50-60℃,滴流1分鐘;經(jīng)第一不流動(dòng)水洗槽2清洗1.5分鐘,滴流1分鐘,第二不流動(dòng)水洗槽3清洗1分鐘,滴流1分鐘;進(jìn)入兩個(gè)流動(dòng)水洗槽,分別清洗1分鐘,1滴流分鐘,完成氧化前處理。實(shí)施例4(NaCl的起砂能力)依據(jù)表1,鋁材直接進(jìn)入堿性三合一磨砂槽1,R(NaOH/Al3+)3.75,NaCl10g/L,反應(yīng)5-10分鐘,50-60℃,滴流1分鐘;經(jīng)第一不流動(dòng)水洗槽2清洗1.5分鐘,滴流1分鐘,第二不流動(dòng)水洗槽3清洗1分鐘,滴流1分鐘;進(jìn)入兩個(gè)流動(dòng)水洗槽,分別清洗1分鐘,1滴流分鐘,完成氧化前處理。實(shí)施例5(NaCl的起砂能力)依據(jù)表1,鋁材直接進(jìn)入堿性三合一磨砂槽1,R(NaOH/Al3+)3.75,NaCl20g/L,反應(yīng)5-10分鐘,50-60℃,滴流1分鐘;經(jīng)第一不流動(dòng)水洗槽2清洗1.5分鐘,滴流1分鐘,第二不流動(dòng)水洗槽3清洗1分鐘,滴流1分鐘;進(jìn)入兩個(gè)流動(dòng)水洗槽,分別清洗1分鐘,1滴流分鐘,完成氧化前處理。實(shí)施例6(NaCl的起砂能力)依據(jù)表1,鋁材直接進(jìn)入堿性三合一磨砂槽1,R(NaOH/Al3+)3.75,NaCl40g/L,反應(yīng)5-10分鐘,50-60℃,滴流1分鐘;經(jīng)第一不流動(dòng)水洗槽2清洗1.5分鐘,滴流1分鐘,第二不流動(dòng)水洗槽3清洗1分鐘,滴流1分鐘;進(jìn)入兩個(gè)流動(dòng)水洗槽,分別清洗1分鐘,1滴流分鐘,完成氧化前處理。實(shí)施例7(NaCl的起砂能力)依據(jù)表1,鋁材直接進(jìn)入堿性三合一磨砂槽1,R(NaOH/Al3+)3.75,NaCl50g/L,反應(yīng)5-10分鐘,50-60℃,滴流1分鐘;經(jīng)第一不流動(dòng)水洗槽2清洗1.5分鐘,滴流1分鐘,第二不流動(dòng)水洗槽3清洗1分鐘,滴流1分鐘;進(jìn)入兩個(gè)流動(dòng)水洗槽,分別清洗1分鐘,1滴流分鐘,完成氧化前處理。由實(shí)施例3-7表明,依據(jù)表1,本發(fā)明氯化鈉低于15g/L時(shí),起砂效果有限,大于20g/L時(shí)可獲得均勻細(xì)膩的化學(xué)砂。實(shí)施例8(藥劑回收系統(tǒng)測(cè)試)按圖1所示,打開第三閥門03,自來水進(jìn)入第二不流動(dòng)水洗槽3;打開第二閥門02,第二不流動(dòng)水洗槽3的截留液進(jìn)入第一不流動(dòng)水洗槽2;打開第一閥門01,第一不流動(dòng)水洗槽2的截留液進(jìn)入堿性三合一磨砂槽1,完成藥劑截留、回收和堿性三合一磨砂槽1補(bǔ)充液位。由實(shí)施例8表明,按圖1所示,本發(fā)明所述藥劑回收系統(tǒng)可梯級(jí)截留堿性三合一磨砂槽1的藥劑,可依次從第二不流動(dòng)水洗槽3向第一不流動(dòng)水洗槽2至堿性三合一磨砂槽1補(bǔ)水,梯級(jí)回收藥劑。實(shí)施例9(抽渣循環(huán)子系統(tǒng)測(cè)試)按圖2所示,關(guān)閉閥門017、018,打開閥門07、08、09、010,開啟一號(hào)泵8,將堿性三合一磨砂槽槽底的沉淀物抽至沉淀池,沉淀池上表面清液經(jīng)閥門010循環(huán)回本槽,完成抽渣循環(huán)。由實(shí)施例9表明,按圖2所示,本發(fā)明抽渣循環(huán)子系統(tǒng)可實(shí)現(xiàn)堿性三合一磨砂槽1抽渣,沉淀池收集沉渣和清液回流至堿性三合一磨砂槽1。實(shí)施例10(氫氧化鋁和堿液的回收子系統(tǒng)測(cè)試)按圖2所示,打開閥門011、012、013,沉渣進(jìn)入離心機(jī)。開啟離心機(jī),分離氫氧化鋁和堿液。打開閥門014,漂洗氫氧化鋁中的堿液,當(dāng)離心機(jī)出水口的清洗水為中性時(shí),停止漂洗,回收氫氧化鋁。打開閥門015、016,開啟二號(hào)泵9,將收集池收集的堿液送回沉淀池,完成堿液回收。由實(shí)施例10表明,按圖2所示,本發(fā)明氫氧化鋁和堿液的回收子系統(tǒng)可有效分離氫氧化鋁和堿液,漂洗、回收氫氧化鋁;并可將堿液送回沉淀池,完成堿液回收。實(shí)施例11(堵塞自救子系統(tǒng)測(cè)試)按圖2所示,關(guān)閉閥門07、08,打開閥門017、018,開啟一號(hào)泵8,槽液從堿性三合一磨砂槽1上表面抽入,從堿性三合一磨砂槽1槽底抽渣管壓出,擠出堵塞抽渣管的沉淀物,完成管道疏通自救。由實(shí)施例11表明,按圖2所示,本發(fā)明堵塞自救子系統(tǒng)可有效完成管道疏通自救。實(shí)施例12(堿蝕液阻垢能力測(cè)試)依據(jù)表2,取同R=2.0,60℃,堿蝕12分鐘,重復(fù)堿蝕100次。實(shí)施例13(堿蝕液阻垢能力測(cè)試)依據(jù)表2,取同R=2.5,60℃,堿蝕12分鐘,重復(fù)堿蝕100次。實(shí)施例14(堿蝕液阻垢能力測(cè)試)依據(jù)表2,取同R=3.0,60℃,堿蝕12分鐘,重復(fù)堿蝕100次。實(shí)施例15(堿蝕液阻垢能力測(cè)試)依據(jù)表2,取同R=3.5,60℃,堿蝕12分鐘,重復(fù)堿蝕100次。實(shí)施例16(堿蝕液阻垢能力測(cè)試)依據(jù)表2,取同R=4.0,60℃,堿蝕12分鐘,重復(fù)堿蝕100次。實(shí)施例17(堿蝕液阻垢能力測(cè)試)依據(jù)表2,取同R=4.5,60℃,堿蝕12分鐘,重復(fù)堿蝕100次。實(shí)施例18(堿蝕液阻垢能力測(cè)試)依據(jù)表2,取同R=5.0,60℃,堿蝕12分鐘,重復(fù)堿蝕100次。由實(shí)施例12-18表明,依據(jù)表2,本發(fā)明R值低于3.0時(shí),容易結(jié)垢,大于3.5時(shí),可完全阻垢,可長期運(yùn)行。以上結(jié)合具體實(shí)施例描述了本發(fā)明的技術(shù)原理。這些描述只是為了解釋本發(fā)明的原理,而不能以任何方式解釋為對(duì)本發(fā)明保護(hù)范圍的限制?;诖颂幍慕忉專绢I(lǐng)域的技術(shù)人員不需要付出創(chuàng)造性的勞動(dòng)即可聯(lián)想到本發(fā)明的其它具體實(shí)施方式,這些方式都將落入本發(fā)明的保護(hù)范圍之內(nèi)。當(dāng)前第1頁1 2 3