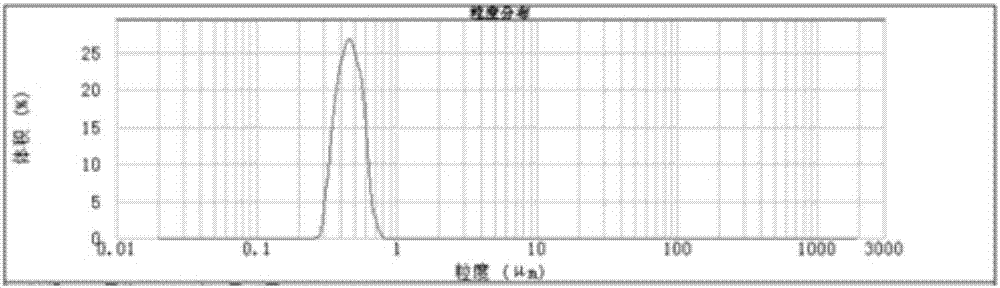
本發(fā)明涉及一種利用鈦白粉副產(chǎn)物制備磷酸鐵的方法,屬于新能源電池材料領(lǐng)域。
背景技術(shù):
:磷酸鐵,又名磷酸高鐵、正磷酸鐵,分子式為fepo4,是一種白色、灰白色單斜晶體粉末。是鐵鹽溶液和磷酸鈉作用的鹽,其中的鐵為正三價。其主要用途在于制造磷酸鐵鋰電池材料、催化劑及陶瓷等。高純度的二水磷酸鐵的顏色為近白色或淺(淡)黃白色粉末,隨著結(jié)晶水的丟失,顏色逐漸變黃,純無水物呈黃白色粉末。二水物磷酸鐵中磷(p)超標(biāo)時外觀呈灰白色或暗灰白色;如鐵超標(biāo)時呈暗黃色。磷鐵比是衡量磷酸鐵品質(zhì)最關(guān)鍵的指標(biāo),也是決定磷酸鐵鋰品質(zhì)最關(guān)鍵的因素。磷酸鐵中如存在大量的二價鐵或鈉、鉀、硫酸根、銨根離子時,二水磷酸鐵則呈暗黑色或灰白色。振實密度:1.13~1.59g/cm3,松裝密度0.75~0.97g/cm3。加熱時易溶于鹽酸,但難溶于其它酸,幾乎不溶于水、醋酸、醇。隨著磷酸鐵鋰電池的大規(guī)模使用,磷酸鐵做為磷酸鐵鋰正極材料的主要原料,其需求量大大提高,預(yù)計每年的需求量大于5萬噸。但是現(xiàn)在的磷酸鐵制備一般采用亞鐵鹽、氧化劑和磷酸鹽反應(yīng)的工藝,但是存在的問題是:1.由于三價鐵離子特別容易水解沉淀,所以在制備磷酸鐵過程中,容易產(chǎn)生氫氧化鐵等雜質(zhì)導(dǎo)致磷酸鐵純度不高;2.鐵溶液的凈化,特別是其中的錳、鎂、鎳、鈉等離子,難以用較低的成本進行除掉,所以必須采用高純度的鐵原料,如高純鐵粉、高純硫酸亞鐵來制備,造成成本高;3.液相沉淀來制備磷酸鐵存在粒徑太粗等問題,而采用溶膠等方法制備的超細磷酸鐵存在雜質(zhì)不容易洗掉等缺點;4.粒徑不可控,團聚現(xiàn)象嚴(yán)重,粒徑較大,一般大于1微米;5.廢水產(chǎn)生量大,一般一噸磷酸鐵廢水產(chǎn)生量高達100噸。同時針對鈦白粉副產(chǎn)物硫酸亞鐵,每年的產(chǎn)生量達到百萬噸,其回收利用一般用作凈水劑等低附加值,由于其中含有大量的鎂、錳、鋅等雜質(zhì)離子,對于其高端循環(huán)利用有很大的障礙作用。技術(shù)實現(xiàn)要素:有鑒于此,本發(fā)明提供了一種利用鈦白粉副產(chǎn)物制備磷酸鐵的方法,通過鈦白粉副產(chǎn)物,可以制備磷酸鐵,得到的磷酸鐵純度高,粒度為0.45-0.5微米,粒徑分布窄,成本低,比表面積小,分散性好,磷鐵比為1.0-1.01,廢水產(chǎn)生量少。本發(fā)明通過以下技術(shù)手段解決上述技術(shù)問題:本發(fā)明的一種利用鈦白粉副產(chǎn)物制備磷酸鐵的方法,其為以下步驟:(1)萃取劑的制備,將異壬烷、正丁醇鈉、氨氣、氫氣在催化劑的存在下反應(yīng)得到萃取劑,得到的萃取劑與乙酸丁酯和磺化煤油按照體積比20-30:40-50:20-40攪拌混合均勻,再加入質(zhì)量分數(shù)為10-20%的次氯酸溶液,按照萃取劑與次氯酸溶液質(zhì)量比為1:2-4混合,在溫度為20-30℃攪拌混合60-75min,靜置分層,得到有機相和水相;(2)將鈦白粉副產(chǎn)物加水溶解后,溶解至溶液中總鐵含量為0.5-1mol/l,加入鐵粉調(diào)節(jié)溶液的ph為5-6,過濾得到第一濾液和第一濾渣,第一濾液加入鹽酸調(diào)節(jié)溶液的ph為1.5-2,然后加入氯化鈉使得溶液中的氯離子與總鐵的摩爾比為4.5-4.8:1,得到調(diào)配后的鐵溶液;(3)將步驟(1)得到的有機相和步驟(2)得到的調(diào)配后的鐵溶液在溫度為35-40℃下混合,經(jīng)過3-4級逆流萃取和2-3級逆流洗滌,萃取過程有機相與水相的體積比為4-5:1,每一級萃取混合時間為20-25min,萃取溫度為35-40℃,澄清時間為40-50min,洗滌過程的洗滌劑為0.1-0.2mol/l的鹽酸溶液,洗滌過程有機相與水相的體積比為4-5:1,洗滌水并入調(diào)配后的鐵溶液中,得到含鐵有機相;(4)將步驟(3)得到的含鐵有機相加入磷酸二氫銨溶液混合,含鐵有機相中的鐵與磷酸二氫銨溶液中的磷酸根摩爾比為1:2.98-2.995,混合采用分散盤攪拌槳,混合時的溫度為35-40℃,攪拌至有機物液滴的粒徑為0.1-0.2mm,攪拌時間為30-45min,攪拌速度為500-700r/min,然后再離心機中高速離心分離,固液分離,將得到固體經(jīng)過用0.005-0.01mol/l的碳酸氫鈉溶液在30-35℃下洗滌,過濾,將濾渣加入純水漿化得到漿化料;(5)將步驟(4)得到的漿化料按照升溫速度2-5℃/min升溫,升溫至溫度為85-90℃,然后在此溫度下反應(yīng)30-60min,待物料由灰色變成白色為止,然后過濾,得到母液和磷酸鐵,將磷酸鐵繼續(xù)加入80-85℃的熱水洗滌,洗滌至溶液的ph為5-5.5,然后得到洗滌后的磷酸鐵,經(jīng)過烘干、篩分和除鐵后得到磷酸鐵。所述催化劑為將氫氧化鐵與鈦酸混合,氫氧化鐵與鈦酸的摩爾比為1:5-6,在壓力為5-6個大氣壓下,溫度為200-220℃反應(yīng),得到的固體經(jīng)過洗滌之后,在還原性氣氛下高溫還原,得到催化劑,碳酸鎳與鈦酸的摩爾比1:1-1.2,還原性氣氛為氫氣、一氧化碳或甲烷氣氛,還原溫度為250-275℃,每小時通入還原性氣體的摩爾數(shù)與鎳摩爾數(shù)之比為5-6:1,還原時間為4-5小時,即得催化劑,所述催化劑的組分為四氧化三鐵和二氧化鈦的混合物,四氧化三鐵均勻分散在二氧化鈦上,四氧化三鐵的粒徑為10-20nm,四氧化三鐵中的亞鐵與三價鐵的比例為0.4975-0.5025:1,二氧化鈦的粒徑為30-50nm。所述步驟(1)中異壬烷、正丁醇鈉、氨氣、氫氣的摩爾比為2.1-2.2:1.1-1.2:1-1.5:0.3-0.5,萃取劑制備的反應(yīng)條件為溫度為120-140℃,壓力為2-2.2個大氣壓,反應(yīng)時間為2-2.5小時,反應(yīng)完畢,收集135-145℃的餾分,得到純度為99-99.5%的萃取劑,蒸餾后剩余的物質(zhì)返回繼續(xù)制備萃取劑,催化劑的加入量為異壬烷、正丁醇鈉、氨氣和氫氣總質(zhì)量的0.01-0.02%,得到的水相搭配高濃度的次氯酸溶液返回繼續(xù)使用。所述步驟(2)中第一濾渣加入氫氧化鈉溶液,在ph為13-13.5下、溫度為95-105℃下反應(yīng),過濾,得到的濾液加入鹽酸調(diào)節(jié)溶液的ph為6-9,過濾,得到鈦酸,返回步驟(1)制備催化劑。所述步驟(3)中萃取過程中,拌時將有機相的液滴分散為粒徑為0.3-0.4mm的直徑,水相為連續(xù)相,在鹽酸溶液洗滌過程中,攪拌時將有機相的液滴分散為粒徑為0.01-0.0.03mm的直徑,水相為連續(xù)相,萃取過程得到的萃余液加入氫氧化鈉溶液調(diào)節(jié)溶液的ph為9-9.5,然后過濾,得到的濾液為氯化鈉溶液,返回步驟(2)中使用,得到的濾渣漿化后通入空氣氧化,氧化至濾渣中的錳完全轉(zhuǎn)化成四價態(tài),然后加入硫酸調(diào)節(jié)漿料的ph為1.0-1.5,過濾,濾渣為錳含量大于30%的錳渣,濾液經(jīng)過濃縮結(jié)晶得到純度>95%的硫酸鎂晶體。所述步驟(4)中磷酸二氫銨溶液的濃度為0.2-0.3mol/l,離心分離得到的濾液靜置15-30min分層,然后再外加超聲波進行分層,超聲波的功率密度為0.3-0.35w/cm2,超聲時間為10-15min,分層后進行有機相和水相的分離,得到的有機相返回步驟(1)使用,得到的水相為氯化銨溶液,離心分離得到的固體與碳酸氫鈉溶液的質(zhì)量比為1:5-6進行洗滌,洗滌后得到的濾液加入鹽酸調(diào)節(jié)溶液的ph為5-6,然后靜置分層,得到的有機相返回步驟(1)使用,含鐵有機相加入磷酸二氫銨溶液混合時采用的反應(yīng)釜高與直徑之比為1:0.7-0.75,分散盤攪拌槳的直徑為反應(yīng)釜直徑的0.15-0.2倍,分散盤攪拌槳的齒高為其直徑的0.1-0.15倍,分散盤攪拌槳距離反應(yīng)釜底部的高度為反應(yīng)釜高度的0.05-0.1倍。所述步驟(5)漿化料升溫過程采用的反應(yīng)釜高與直徑之比為1:0.7-0.75,攪拌器采用折葉渦輪攪拌器,攪拌器的寬度為反應(yīng)釜直徑的0.2-0.25倍,攪拌器為四葉,每葉傾角為30-45°,每葉寬度為其長度的0.2-0.25倍,反應(yīng)釜內(nèi)設(shè)置有三個均勻分布的擋板,擋板的寬度為反應(yīng)釜直徑的0.05-0.1倍,擋板與反應(yīng)釜壁之間的間隙為擋板寬度的0.1-0.15倍,高溫反應(yīng)后得到的母液為磷酸溶液。步驟(4)中離心固液分離之后,液體靜置分層得到的水相加入氫氧化鈉調(diào)節(jié)溶液的ph為9-10,再進行蒸氨,蒸發(fā)的氨經(jīng)過步驟(5)得到的母液吸收,按照氨與磷酸的摩爾比1:1混合,得到磷酸二氫銨溶液,返回步驟(4)使用,蒸氨后的溶液為氯化鈉溶液,返回步驟(2)使用。步驟(5)中洗滌磷酸鐵得到的洗滌水加入步驟(1)得到的萃取劑混合攪拌,按照有機相與水相的體積比1:3-5混合,混合時間為10-20min,將磷酸萃取到有機相中,加入氨水反萃得到磷酸二氫銨溶液返回步驟(4)使用,萃余液中的磷酸含量低于10ppm,萃余液體積的60-70%返回做磷酸鐵洗滌水使用,剩余30-40%外排。本發(fā)明采用鈦白粉副產(chǎn)物硫酸亞鐵為原料,鈦白粉副產(chǎn)物的組分如下:從數(shù)據(jù)來看,鈦白粉副產(chǎn)物成分比較復(fù)雜,雜質(zhì)含量較高的為mg、ti、mn等離子,同時含有鈷鎳鋅等重金屬和硅酸等膠狀物,常規(guī)的工藝為經(jīng)過絮凝沉淀,將鈦、硅等沉淀下來后,加入硫化物或者重金屬捕捉劑來沉淀重金屬,加入氟化物來除鈣鎂,再來制備磷酸鐵,但是存在流程長、成本高、廢水產(chǎn)生量少,鐵的回收率低等缺點。而本發(fā)明將異壬烷、正丁醇鈉、氨氣、氫氣在催化劑的存在下反應(yīng)得到萃取劑,通過在催化劑的作用下,一步法合成得到萃取劑,由于其碳鏈更長,親油性更強,且對鐵氯絡(luò)離子的選擇性更強,萃取鐵的萃取率更高,最終萃余液中的鐵含量可以低至5ppm以下,鐵的萃取率高達99.5%以上,且對其他雜質(zhì)的共萃非常少,保證了本發(fā)明鐵源的純度,針對本發(fā)明的萃取劑,通過液相合成和高溫還原得到納米催化劑,為四氧化三鐵負載在二氧化鈦上,四氧化三鐵的粒徑為10-20nm,四氧化三鐵中的亞鐵與三價鐵的比例為0.4975-0.5025:1,二氧化鈦的粒徑為30-50nm,由于四氧化三鐵為三價態(tài)與二價態(tài)共存的化合物,再加上為納米顆粒,活性高,其催化時,可以明顯降低反應(yīng)溫度和反應(yīng)壓力,縮短反應(yīng)時間,提高效率,本發(fā)明萃取劑制備的反應(yīng)條件為溫度為120-140℃,壓力為2-2.2個大氣壓,反應(yīng)時間為2-2.5小時,經(jīng)過蒸餾可以得到高純度的萃取劑。鈦白粉副產(chǎn)物經(jīng)過鐵粉還原和提高ph,可以將鈦水解成點,同時將鋁、鉻等離子水解沉淀,過濾,得到的濾液為硫酸亞鐵溶液。按照萃取劑與次氯酸溶液質(zhì)量比為1:2-4混合,可以得到氧化性的陰離子,在與亞鐵離子接觸時,會將亞鐵離子氧化成三價鐵離子,三價鐵離子與氯離子絡(luò)合得到絡(luò)合陰離子,再與萃取劑結(jié)合,從而實現(xiàn)鐵的萃取,而其他雜質(zhì)與氯離子的絡(luò)合較差,基本不會被萃取,實現(xiàn)了鐵的凈化。萃取后的含鐵有機,加入磷酸二氫銨溶液反萃得到磷酸二氫鐵沉淀,通過控制有機相的液滴粒徑,通過界面反應(yīng),可以得到粒徑可控的沉淀,再經(jīng)過高溫分解,得到磷酸鐵,在分解過程,控制分解溫度和攪拌形式,得到粒徑為0.45-0.5微米,粒徑分布非常窄的磷酸鐵。最終得到的產(chǎn)品的指標(biāo)如下:指標(biāo)鐵含量磷鐵摩爾比d10d50d90數(shù)值28.9-29.5%1.0-1.01350-400nm450-500nm550-600nmd100camgnanico<900nm2-3ppm3-5ppm1-5ppm1-2ppm0.1-0.5ppmmnzncutialsi1-3ppm1-3ppm0.1-0.5ppm0.1-0.5ppm1-2ppm1-2ppm振實密度硫酸根氯離子betph1.1-1.2g/ml1-2ppm2-3ppm5-10m2/g3-3.5經(jīng)過萃取劑萃取提純并分離之后,可以得到高純度的鐵源,從而使得產(chǎn)品中的雜質(zhì)含量大大降低,基本都低于5ppm,且粒徑分布非常窄,(d90-d10)/d50≤0.,56,同時每批次的穩(wěn)定性非常好,分散性好,基本無團聚,且相比較普通的磷酸鐵,本發(fā)明的磷酸鐵內(nèi)部無空心或者間隙,振實密度高,比表面積小。本發(fā)明的廢水產(chǎn)生量少,一般常規(guī)的磷酸鐵制備工藝,如液相法合成,至少得廢水產(chǎn)生包括:原料如亞鐵溶液、磷酸、氧化劑等引入的廢水、洗滌廢水,由于原料中雜質(zhì)含量較高,一般一噸產(chǎn)品產(chǎn)生的廢水量為80-100噸。而本發(fā)明在步驟(1)過程中,次氯酸溶液與萃取劑混合,混合后的剩余的次氯酸溶液繼續(xù)加入次氯酸,可以循環(huán)使用,不產(chǎn)生廢水,步驟(3)萃余液加入氫氧化鈉溶液調(diào)節(jié)溶液的ph為9-9.5,然后過濾,得到的濾液為氯化鈉溶液,返回步驟(2)中使用,得到的濾渣漿化后通入空氣氧化,氧化至濾渣中的錳完全轉(zhuǎn)化成四價態(tài),然后加入硫酸調(diào)節(jié)漿料的ph為1.0-1.5,過濾,濾渣為錳含量大于30%的錳渣,濾液經(jīng)過濃縮結(jié)晶得到純度>95%的硫酸鎂晶體,鎂的濃縮結(jié)晶過程中產(chǎn)生的蒸餾水,這一部分為純水,可以直接外排或者循環(huán)利用,步驟(4)中固液分離得到的水相為氯化銨溶液,液加入氫氧化鈉調(diào)節(jié)溶液的ph為9-10,再進行蒸氨,蒸發(fā)的氨經(jīng)過步驟(5)得到的母液吸收,按照氨與磷酸的摩爾比1:1混合,得到磷酸二氫銨溶液,返回步驟(4)使用,蒸氨后的溶液為氯化鈉溶液,返回步驟(2)使用,主要產(chǎn)生的廢水為碳酸鈉洗滌廢水,步驟(5)產(chǎn)生的廢水為母液和洗滌磷酸鐵的洗滌廢水,母液為濃度較高的磷酸溶液,投入氨氣制備得到磷酸二氫銨溶液,返回使用,而洗滌廢水為濃度較低的磷酸溶液,經(jīng)過本萃取劑的萃取,再經(jīng)過氨水反萃液會得到濃度較高的磷酸二氫銨溶液,萃余液的組分如下:電導(dǎo)率ph磷酸fe20-30μs/cm3.5-4.5<10ppm<5ppmmn/mgca/zn/cu/co/ni油分硫酸根/氯離子<5ppm<3ppm<5ppm<5ppm由于最后磷酸鐵的洗滌主要是洗滌掉殘留的磷酸,所以,上述的萃余液可以部分返回磷酸鐵的洗滌,特別是在磷酸鐵前期的洗滌,外排的廢水主要為不能重復(fù)利用的萃余液。綜上所述,本發(fā)明每噸磷酸鐵產(chǎn)品的廢水量在15-25噸,大大低于常規(guī)的磷酸鐵的廢水排量。本發(fā)明的成本低,本發(fā)明主要的原料中,如氯化鈉可以實現(xiàn)循環(huán)利用,磷酸二氫銨中的60%以上可以實現(xiàn)循環(huán)利用,萃取劑可以完全實現(xiàn)循環(huán)利用,且本發(fā)明能夠綜合處理鈦白粉副產(chǎn)物中的鈦、錳、鎂等組分,鐵的回收率也大大提高,從而使得成本降低。本發(fā)明的有益效果是:1.利用鈦白粉副產(chǎn)物來制備磷酸鐵,成本低。2.廢水排放量少,液相沉淀每噸磷酸鐵產(chǎn)生廢水100噸左右,而本發(fā)明僅僅只產(chǎn)生15-25噸。3.本發(fā)明采用萃取和分解法,可以制備高純磷酸鐵,得到的磷酸鐵純度高,粒徑分布窄且為半微米級別的,比表面積小,磷鐵比為1.0-1.01,雜質(zhì)含量低。附圖說明附圖1為本發(fā)明實施例1的激光粒度分布圖;附圖2為本發(fā)明實施例2的激光粒度分布圖;附圖3為本發(fā)明實施例3的激光粒度分布圖;附圖4為本發(fā)明實施例1的磷酸鐵的剖面圖。具體實施方式以下將結(jié)合附圖和具體實施例對本發(fā)明進行詳細說明,本實施例的一種利用鈦白粉副產(chǎn)物制備磷酸鐵的方法,為以下步驟:(1)萃取劑的制備,將異壬烷、正丁醇鈉、氨氣、氫氣在催化劑的存在下反應(yīng)得到萃取劑,得到的萃取劑與乙酸丁酯和磺化煤油按照體積比20-30:40-50:20-40攪拌混合均勻,再加入質(zhì)量分數(shù)為10-20%的次氯酸溶液,按照萃取劑與次氯酸溶液質(zhì)量比為1:2-4混合,在溫度為20-30℃攪拌混合60-75min,靜置分層,得到有機相和水相;(2)將鈦白粉副產(chǎn)物加水溶解后,溶解至溶液中總鐵含量為0.5-1mol/l,加入鐵粉調(diào)節(jié)溶液的ph為5-6,過濾得到第一濾液和第一濾渣,第一濾液加入鹽酸調(diào)節(jié)溶液的ph為1.5-2,然后加入氯化鈉使得溶液中的氯離子與總鐵的摩爾比為4.5-4.8:1,得到調(diào)配后的鐵溶液;(3)將步驟(1)得到的有機相和步驟(2)得到的調(diào)配后的鐵溶液在溫度為35-40℃下混合,經(jīng)過3-4級逆流萃取和2-3級逆流洗滌,萃取過程有機相與水相的體積比為4-5:1,每一級萃取混合時間為20-25min,萃取溫度為35-40℃,澄清時間為40-50min,洗滌過程的洗滌劑為0.1-0.2mol/l的鹽酸溶液,洗滌過程有機相與水相的體積比為4-5:1,洗滌水并入調(diào)配后的鐵溶液中,得到含鐵有機相;(4)將步驟(3)得到的含鐵有機相加入磷酸二氫銨溶液混合,含鐵有機相中的鐵與磷酸二氫銨溶液中的磷酸根摩爾比為1:2.98-2.995,混合采用分散盤攪拌槳,混合時的溫度為35-40℃,攪拌至有機物液滴的粒徑為0.1-0.2mm,攪拌時間為30-45min,攪拌速度為500-700r/min,然后再離心機中高速離心分離,固液分離,將得到固體經(jīng)過用0.005-0.01mol/l的碳酸氫鈉溶液在30-35℃下洗滌,過濾,將濾渣加入純水漿化得到漿化料;(5)將步驟(4)得到的漿化料按照升溫速度2-5℃/min升溫,升溫至溫度為85-90℃,然后在此溫度下反應(yīng)30-60min,待物料由灰色變成白色為止,然后過濾,得到母液和磷酸鐵,將磷酸鐵繼續(xù)加入80-85℃的熱水洗滌,洗滌至溶液的ph為5-5.5,然后得到洗滌后的磷酸鐵,經(jīng)過烘干、篩分和除鐵后得到磷酸鐵。所述催化劑為將氫氧化鐵與鈦酸混合,氫氧化鐵與鈦酸的摩爾比為1:5-6,在壓力為5-6個大氣壓下,溫度為200-220℃反應(yīng),得到的固體經(jīng)過洗滌之后,在還原性氣氛下高溫還原,得到催化劑,碳酸鎳與鈦酸的摩爾比1:1-1.2,還原性氣氛為氫氣、一氧化碳或甲烷氣氛,還原溫度為250-275℃,每小時通入還原性氣體的摩爾數(shù)與鎳摩爾數(shù)之比為5-6:1,還原時間為4-5小時,即得催化劑,所述催化劑的組分為四氧化三鐵和二氧化鈦的混合物,四氧化三鐵均勻分散在二氧化鈦上,四氧化三鐵的粒徑為10-20nm,四氧化三鐵中的亞鐵與三價鐵的比例為0.4975-0.5025:1,二氧化鈦的粒徑為30-50nm。所述步驟(1)中異壬烷、正丁醇鈉、氨氣、氫氣的摩爾比為2.1-2.2:1.1-1.2:1-1.5:0.3-0.5,萃取劑制備的反應(yīng)條件為溫度為120-140℃,壓力為2-2.2個大氣壓,反應(yīng)時間為2-2.5小時,反應(yīng)完畢,收集135-145℃的餾分,得到純度為99-99.5%的萃取劑,蒸餾后剩余的物質(zhì)返回繼續(xù)制備萃取劑,催化劑的加入量為異壬烷、正丁醇鈉、氨氣和氫氣總質(zhì)量的0.01-0.02%,得到的水相搭配高濃度的次氯酸溶液返回繼續(xù)使用。所述步驟(2)中第一濾渣加入氫氧化鈉溶液,在ph為13-13.5下、溫度為95-105℃下反應(yīng),過濾,得到的濾液加入鹽酸調(diào)節(jié)溶液的ph為6-9,過濾,得到鈦酸,返回步驟(1)制備催化劑。所述步驟(3)中萃取過程中,拌時將有機相的液滴分散為粒徑為0.3-0.4mm的直徑,水相為連續(xù)相,在鹽酸溶液洗滌過程中,攪拌時將有機相的液滴分散為粒徑為0.01-0.0.03mm的直徑,水相為連續(xù)相,萃取過程得到的萃余液加入氫氧化鈉溶液調(diào)節(jié)溶液的ph為9-9.5,然后過濾,得到的濾液為氯化鈉溶液,返回步驟(2)中使用,得到的濾渣漿化后通入空氣氧化,氧化至濾渣中的錳完全轉(zhuǎn)化成四價態(tài),然后加入硫酸調(diào)節(jié)漿料的ph為1.0-1.5,過濾,濾渣為錳含量大于30%的錳渣,濾液經(jīng)過濃縮結(jié)晶得到純度>95%的硫酸鎂晶體。所述步驟(4)中磷酸二氫銨溶液的濃度為0.2-0.3mol/l,離心分離得到的濾液靜置15-30min分層,然后再外加超聲波進行分層,超聲波的功率密度為0.3-0.35w/cm2,超聲時間為10-15min,分層后進行有機相和水相的分離,得到的有機相返回步驟(1)使用,得到的水相為氯化銨溶液,離心分離得到的固體與碳酸氫鈉溶液的質(zhì)量比為1:5-6進行洗滌,洗滌后得到的濾液加入鹽酸調(diào)節(jié)溶液的ph為5-6,然后靜置分層,得到的有機相返回步驟(1)使用,含鐵有機相加入磷酸二氫銨溶液混合時采用的反應(yīng)釜高與直徑之比為1:0.7-0.75,分散盤攪拌槳的直徑為反應(yīng)釜直徑的0.15-0.2倍,分散盤攪拌槳的齒高為其直徑的0.1-0.15倍,分散盤攪拌槳距離反應(yīng)釜底部的高度為反應(yīng)釜高度的0.05-0.1倍。所述步驟(5)漿化料升溫過程采用的反應(yīng)釜高與直徑之比為1:0.7-0.75,攪拌器采用折葉渦輪攪拌器,攪拌器的寬度為反應(yīng)釜直徑的0.2-0.25倍,攪拌器為四葉,每葉傾角為30-45°,每葉寬度為其長度的0.2-0.25倍,反應(yīng)釜內(nèi)設(shè)置有三個均勻分布的擋板,擋板的寬度為反應(yīng)釜直徑的0.05-0.1倍,擋板與反應(yīng)釜壁之間的間隙為擋板寬度的0.1-0.15倍,高溫反應(yīng)后得到的母液為磷酸溶液。步驟(4)中離心固液分離之后,液體靜置分層得到的水相加入氫氧化鈉調(diào)節(jié)溶液的ph為9-10,再進行蒸氨,蒸發(fā)的氨經(jīng)過步驟(5)得到的母液吸收,按照氨與磷酸的摩爾比1:1混合,得到磷酸二氫銨溶液,返回步驟(4)使用,蒸氨后的溶液為氯化鈉溶液,返回步驟(2)使用。步驟(5)中洗滌磷酸鐵得到的洗滌水加入步驟(1)得到的萃取劑混合攪拌,按照有機相與水相的體積比1:3-5混合,混合時間為10-20min,將磷酸萃取到有機相中,加入氨水反萃得到磷酸二氫銨溶液返回步驟(4)使用,萃余液中的磷酸含量低于10ppm,萃余液體積的60-70%返回做磷酸鐵洗滌水使用,剩余30-40%外排。實施例1一種利用鈦白粉副產(chǎn)物制備磷酸鐵的方法,為以下步驟:(1)萃取劑的制備,將異壬烷、正丁醇鈉、氨氣、氫氣在催化劑的存在下反應(yīng)得到萃取劑,得到的萃取劑與乙酸丁酯和磺化煤油按照體積比25:45:30攪拌混合均勻,再加入質(zhì)量分數(shù)為15%的次氯酸溶液,按照萃取劑與次氯酸溶液質(zhì)量比為1:2.8混合,在溫度為28℃攪拌混合71min,靜置分層,得到有機相和水相;(2)將鈦白粉副產(chǎn)物加水溶解后,溶解至溶液中總鐵含量為0.76mol/l,加入鐵粉調(diào)節(jié)溶液的ph為5.5,過濾得到第一濾液和第一濾渣,第一濾液加入鹽酸調(diào)節(jié)溶液的ph為1.8,然后加入氯化鈉使得溶液中的氯離子與總鐵的摩爾比為4.59:1,得到調(diào)配后的鐵溶液;(3)將步驟(1)得到的有機相和步驟(2)得到的調(diào)配后的鐵溶液在溫度為39℃下混合,經(jīng)過3級逆流萃取和3級逆流洗滌,萃取過程有機相與水相的體積比為4.5:1,每一級萃取混合時間為23min,萃取溫度為39℃,澄清時間為46min,洗滌過程的洗滌劑為0.17mol/l的鹽酸溶液,洗滌過程有機相與水相的體積比為4.7:1,洗滌水并入調(diào)配后的鐵溶液中,得到含鐵有機相;(4)將步驟(3)得到的含鐵有機相加入磷酸二氫銨溶液混合,含鐵有機相中的鐵與磷酸二氫銨溶液中的磷酸根摩爾比為1:2.987,混合采用分散盤攪拌槳,混合時的溫度為38.9℃,攪拌至有機物液滴的粒徑為0.18mm,攪拌時間為39min,攪拌速度為670r/min,然后再離心機中高速離心分離,固液分離,將得到固體經(jīng)過用0.009mol/l的碳酸氫鈉溶液在32℃下洗滌,過濾,將濾渣加入純水漿化得到漿化料;(5)將步驟(4)得到的漿化料按照升溫速度3.5℃/min升溫,升溫至溫度為89℃,然后在此溫度下反應(yīng)45min,待物料由灰色變成白色為止,然后過濾,得到母液和磷酸鐵,將磷酸鐵繼續(xù)加入83℃的熱水洗滌,洗滌至溶液的ph為5.25,然后得到洗滌后的磷酸鐵,經(jīng)過烘干、篩分和除鐵后得到磷酸鐵。所述催化劑為將氫氧化鐵與鈦酸混合,氫氧化鐵與鈦酸的摩爾比為1:5.5,在壓力為5.2個大氣壓下,溫度為210℃反應(yīng),得到的固體經(jīng)過洗滌之后,在還原性氣氛下高溫還原,得到催化劑,碳酸鎳與鈦酸的摩爾比1:1.1還原性氣氛為甲烷氣氛,還原溫度為272℃,每小時通入還原性氣體的摩爾數(shù)與鎳摩爾數(shù)之比為5.2:1,還原時間為4.2小時,即得催化劑,所述催化劑的組分為四氧化三鐵和二氧化鈦的混合物,四氧化三鐵均勻分散在二氧化鈦上,四氧化三鐵的粒徑為13nm,四氧化三鐵中的亞鐵與三價鐵的比例為0.4995:1,二氧化鈦的粒徑為40nm。所述步驟(1)中異壬烷、正丁醇鈉、氨氣、氫氣的摩爾比為2.2.1:1.15:1.25:0.45,萃取劑制備的反應(yīng)條件為溫度為135℃,壓力為2.1個大氣壓,反應(yīng)時間為2.35小時,反應(yīng)完畢,收集139℃的餾分,得到純度為99.25%的萃取劑,蒸餾后剩余的物質(zhì)返回繼續(xù)制備萃取劑,催化劑的加入量為異壬烷、正丁醇鈉、氨氣和氫氣總質(zhì)量的0.018%,得到的水相搭配高濃度的次氯酸溶液返回繼續(xù)使用。所述步驟(2)中第一濾渣加入氫氧化鈉溶液,在ph為13.35下、溫度為99℃下反應(yīng),過濾,得到的濾液加入鹽酸調(diào)節(jié)溶液的ph為7.2,過濾,得到鈦酸,返回步驟(1)制備催化劑。所述步驟(3)中萃取過程中,拌時將有機相的液滴分散為粒徑為0.35mm的直徑,水相為連續(xù)相,在鹽酸溶液洗滌過程中,攪拌時將有機相的液滴分散為粒徑為0.02mm的直徑,水相為連續(xù)相,萃取過程得到的萃余液加入氫氧化鈉溶液調(diào)節(jié)溶液的ph為9.35,然后過濾,得到的濾液為氯化鈉溶液,返回步驟(2)中使用,得到的濾渣漿化后通入空氣氧化,氧化至濾渣中的錳完全轉(zhuǎn)化成四價態(tài),然后加入硫酸調(diào)節(jié)漿料的ph為1.35,過濾,濾渣為錳含量大于30%的錳渣,濾液經(jīng)過濃縮結(jié)晶得到純度>95%的硫酸鎂晶體。所述步驟(4)中磷酸二氫銨溶液的濃度為0.28mol/l,離心分離得到的濾液靜置20min分層,然后再外加超聲波進行分層,超聲波的功率密度為0.33w/cm2,超聲時間為12.5min,分層后進行有機相和水相的分離,得到的有機相返回步驟(1)使用,得到的水相為氯化銨溶液,離心分離得到的固體與碳酸氫鈉溶液的質(zhì)量比為1:5.8進行洗滌,洗滌后得到的濾液加入鹽酸調(diào)節(jié)溶液的ph為5.8,然后靜置分層,得到的有機相返回步驟(1)使用,含鐵有機相加入磷酸二氫銨溶液混合時采用的反應(yīng)釜高與直徑之比為1:0.725,分散盤攪拌槳的直徑為反應(yīng)釜直徑的0.18倍,分散盤攪拌槳的齒高為其直徑的0.13倍,分散盤攪拌槳距離反應(yīng)釜底部的高度為反應(yīng)釜高度的0.08倍。所述步驟(5)漿化料升溫過程采用的反應(yīng)釜高與直徑之比為1:0.724,攪拌器采用折葉渦輪攪拌器,攪拌器的寬度為反應(yīng)釜直徑的0.21倍,攪拌器為四葉,每葉傾角為38°,每葉寬度為其長度的0.225倍,反應(yīng)釜內(nèi)設(shè)置有三個均勻分布的擋板,擋板的寬度為反應(yīng)釜直徑的0.08倍,擋板與反應(yīng)釜壁之間的間隙為擋板寬度的0.12倍,高溫反應(yīng)后得到的母液為磷酸溶液。步驟(4)中離心固液分離之后,液體靜置分層得到的水相加入氫氧化鈉調(diào)節(jié)溶液的ph為9.35,再進行蒸氨,蒸發(fā)的氨經(jīng)過步驟(5)得到的母液吸收,按照氨與磷酸的摩爾比1:1混合,得到磷酸二氫銨溶液,返回步驟(4)使用,蒸氨后的溶液為氯化鈉溶液,返回步驟(2)使用。步驟(5)中洗滌磷酸鐵得到的洗滌水加入步驟(1)得到的萃取劑混合攪拌,按照有機相與水相的體積比1:4.2混合,混合時間為18min,將磷酸萃取到有機相中,加入氨水反萃得到磷酸二氫銨溶液返回步驟(4)使用,萃余液中的磷酸含量低于10ppm,萃余液體積的65%返回做磷酸鐵洗滌水使用,剩余35%外排。最終得到的磷酸鐵指標(biāo)如下:指標(biāo)鐵含量磷鐵摩爾比d10d50d90數(shù)值29.2%1.005363nm460nm595nmd100camgnanico740nm2.5ppm4.2ppm2.5ppm1.3ppm0.35ppmmnzncutialsi2.1ppm2.5ppm0.35ppm0.25ppm1.3ppm1.3ppm振實密度硫酸根氯離子betph1.15g/ml1.2ppm2.3ppm7.2m2/g3.21實施例2一種利用鈦白粉副產(chǎn)物制備磷酸鐵的方法,為以下步驟:(1)萃取劑的制備,將異壬烷、正丁醇鈉、氨氣、氫氣在催化劑的存在下反應(yīng)得到萃取劑,得到的萃取劑與乙酸丁酯和磺化煤油按照體積比28:42:30攪拌混合均勻,再加入質(zhì)量分數(shù)為14%的次氯酸溶液,按照萃取劑與次氯酸溶液質(zhì)量比為1:3.1混合,在溫度為25℃攪拌混合68min,靜置分層,得到有機相和水相;(2)將鈦白粉副產(chǎn)物加水溶解后,溶解至溶液中總鐵含量為0.68mol/l,加入鐵粉調(diào)節(jié)溶液的ph為5.3,過濾得到第一濾液和第一濾渣,第一濾液加入鹽酸調(diào)節(jié)溶液的ph為1.75,然后加入氯化鈉使得溶液中的氯離子與總鐵的摩爾比為4.65:1,得到調(diào)配后的鐵溶液;(3)將步驟(1)得到的有機相和步驟(2)得到的調(diào)配后的鐵溶液在溫度為38.5℃下混合,經(jīng)過4級逆流萃取和3級逆流洗滌,萃取過程有機相與水相的體積比為4.5:1,每一級萃取混合時間為23min,萃取溫度為38℃,澄清時間為48min,洗滌過程的洗滌劑為0.17mol/l的鹽酸溶液,洗滌過程有機相與水相的體積比為4.6:1,洗滌水并入調(diào)配后的鐵溶液中,得到含鐵有機相;(4)將步驟(3)得到的含鐵有機相加入磷酸二氫銨溶液混合,含鐵有機相中的鐵與磷酸二氫銨溶液中的磷酸根摩爾比為1:2.991,混合采用分散盤攪拌槳,混合時的溫度為39℃,攪拌至有機物液滴的粒徑為0.15mm,攪拌時間為42min,攪拌速度為600r/min,然后再離心機中高速離心分離,固液分離,將得到固體經(jīng)過用0.006mol/l的碳酸氫鈉溶液在33.5℃下洗滌,過濾,將濾渣加入純水漿化得到漿化料;(5)將步驟(4)得到的漿化料按照升溫速度4.1℃/min升溫,升溫至溫度為88℃,然后在此溫度下反應(yīng)40min,待物料由灰色變成白色為止,然后過濾,得到母液和磷酸鐵,將磷酸鐵繼續(xù)加入82.5℃的熱水洗滌,洗滌至溶液的ph為5.35,然后得到洗滌后的磷酸鐵,經(jīng)過烘干、篩分和除鐵后得到磷酸鐵。所述催化劑為將氫氧化鐵與鈦酸混合,氫氧化鐵與鈦酸的摩爾比為1:5.35,在壓力為5.55個大氣壓下,溫度為217℃反應(yīng),得到的固體經(jīng)過洗滌之后,在還原性氣氛下高溫還原,得到催化劑,碳酸鎳與鈦酸的摩爾比1:1.13,還原性氣氛為氫氣氣氛,還原溫度為271℃,每小時通入還原性氣體的摩爾數(shù)與鎳摩爾數(shù)之比為5.35:1,還原時間為4.28小時,即得催化劑,所述催化劑的組分為四氧化三鐵和二氧化鈦的混合物,四氧化三鐵均勻分散在二氧化鈦上,四氧化三鐵的粒徑為18nm,四氧化三鐵中的亞鐵與三價鐵的比例為0.5012:1,二氧化鈦的粒徑為42nm。所述步驟(1)中異壬烷、正丁醇鈉、氨氣、氫氣的摩爾比為2.15:1.13:1.25:0.35,萃取劑制備的反應(yīng)條件為溫度為130℃,壓力為2.15個大氣壓,反應(yīng)時間為2.25小時,反應(yīng)完畢,收集142℃的餾分,得到純度為99.25%的萃取劑,蒸餾后剩余的物質(zhì)返回繼續(xù)制備萃取劑,催化劑的加入量為異壬烷、正丁醇鈉、氨氣和氫氣總質(zhì)量的0.013%,得到的水相搭配高濃度的次氯酸溶液返回繼續(xù)使用。所述步驟(2)中第一濾渣加入氫氧化鈉溶液,在ph為13.25下、溫度為99℃下反應(yīng),過濾,得到的濾液加入鹽酸調(diào)節(jié)溶液的ph為8.1,過濾,得到鈦酸,返回步驟(1)制備催化劑。所述步驟(3)中萃取過程中,拌時將有機相的液滴分散為粒徑為0.325mm的直徑,水相為連續(xù)相,在鹽酸溶液洗滌過程中,攪拌時將有機相的液滴分散為粒徑為0.02mm的直徑,水相為連續(xù)相,萃取過程得到的萃余液加入氫氧化鈉溶液調(diào)節(jié)溶液的ph為9.25,然后過濾,得到的濾液為氯化鈉溶液,返回步驟(2)中使用,得到的濾渣漿化后通入空氣氧化,氧化至濾渣中的錳完全轉(zhuǎn)化成四價態(tài),然后加入硫酸調(diào)節(jié)漿料的ph為1.35,過濾,濾渣為錳含量大于30%的錳渣,濾液經(jīng)過濃縮結(jié)晶得到純度>95%的硫酸鎂晶體。所述步驟(4)中磷酸二氫銨溶液的濃度為0.25mol/l,離心分離得到的濾液靜置25min分層,然后再外加超聲波進行分層,超聲波的功率密度為0.325w/cm2,超聲時間為13min,分層后進行有機相和水相的分離,得到的有機相返回步驟(1)使用,得到的水相為氯化銨溶液,離心分離得到的固體與碳酸氫鈉溶液的質(zhì)量比為1:5.2進行洗滌,洗滌后得到的濾液加入鹽酸調(diào)節(jié)溶液的ph為5.6,然后靜置分層,得到的有機相返回步驟(1)使用,含鐵有機相加入磷酸二氫銨溶液混合時采用的反應(yīng)釜高與直徑之比為1:0.725,分散盤攪拌槳的直徑為反應(yīng)釜直徑的0.18倍,分散盤攪拌槳的齒高為其直徑的0.135倍,分散盤攪拌槳距離反應(yīng)釜底部的高度為反應(yīng)釜高度的0.09倍。所述步驟(5)漿化料升溫過程采用的反應(yīng)釜高與直徑之比為1:0.725,攪拌器采用折葉渦輪攪拌器,攪拌器的寬度為反應(yīng)釜直徑的0.225倍,攪拌器為四葉,每葉傾角為42°,每葉寬度為其長度的0.225倍,反應(yīng)釜內(nèi)設(shè)置有三個均勻分布的擋板,擋板的寬度為反應(yīng)釜直徑的0.075倍,擋板與反應(yīng)釜壁之間的間隙為擋板寬度的0.125倍,高溫反應(yīng)后得到的母液為磷酸溶液。步驟(4)中離心固液分離之后,液體靜置分層得到的水相加入氫氧化鈉調(diào)節(jié)溶液的ph為9.35,再進行蒸氨,蒸發(fā)的氨經(jīng)過步驟(5)得到的母液吸收,按照氨與磷酸的摩爾比1:1混合,得到磷酸二氫銨溶液,返回步驟(4)使用,蒸氨后的溶液為氯化鈉溶液,返回步驟(2)使用。步驟(5)中洗滌磷酸鐵得到的洗滌水加入步驟(1)得到的萃取劑混合攪拌,按照有機相與水相的體積比1:4.2混合,混合時間為13min,將磷酸萃取到有機相中,加入氨水反萃得到磷酸二氫銨溶液返回步驟(4)使用,萃余液中的磷酸含量低于10ppm,萃余液體積的60%返回做磷酸鐵洗滌水使用,剩余40%外排。最終得到的磷酸鐵指標(biāo)如下:指標(biāo)鐵含量磷鐵摩爾比d10d50d90數(shù)值28.951.004361nm456nm588nmd100camgnanico792nm2.1ppm4.9ppm2.6ppm1.5ppm0.3ppmmnzncutialsi2.1ppm1.9ppm0.35ppm0.27ppm1.9ppm1.6ppm振實密度硫酸根氯離子betph1.17g/ml1.3ppm2.6ppm6.9m2/g3.21實施例3一種利用鈦白粉副產(chǎn)物制備磷酸鐵的方法,為以下步驟:(1)萃取劑的制備,將異壬烷、正丁醇鈉、氨氣、氫氣在催化劑的存在下反應(yīng)得到萃取劑,得到的萃取劑與乙酸丁酯和磺化煤油按照體積比23:48:29攪拌混合均勻,再加入質(zhì)量分數(shù)為18%的次氯酸溶液,按照萃取劑與次氯酸溶液質(zhì)量比為1:3.3混合,在溫度為28℃攪拌混合72.5min,靜置分層,得到有機相和水相;(2)將鈦白粉副產(chǎn)物加水溶解后,溶解至溶液中總鐵含量為0.78mol/l,加入鐵粉調(diào)節(jié)溶液的ph為5.6,過濾得到第一濾液和第一濾渣,第一濾液加入鹽酸調(diào)節(jié)溶液的ph為1.75,然后加入氯化鈉使得溶液中的氯離子與總鐵的摩爾比為4.67:1,得到調(diào)配后的鐵溶液;(3)將步驟(1)得到的有機相和步驟(2)得到的調(diào)配后的鐵溶液在溫度為38.5℃下混合,經(jīng)過3級逆流萃取和2級逆流洗滌,萃取過程有機相與水相的體積比為4.3:1,每一級萃取混合時間為23min,萃取溫度為38℃,澄清時間為44min,洗滌過程的洗滌劑為0.18mol/l的鹽酸溶液,洗滌過程有機相與水相的體積比為4.25:1,洗滌水并入調(diào)配后的鐵溶液中,得到含鐵有機相;(4)將步驟(3)得到的含鐵有機相加入磷酸二氫銨溶液混合,含鐵有機相中的鐵與磷酸二氫銨溶液中的磷酸根摩爾比為1:2.990,混合采用分散盤攪拌槳,混合時的溫度為38℃,攪拌至有機物液滴的粒徑為0.18mm,攪拌時間為42.5min,攪拌速度為550r/min,然后再離心機中高速離心分離,固液分離,將得到固體經(jīng)過用0.008mol/l的碳酸氫鈉溶液在32.5℃下洗滌,過濾,將濾渣加入純水漿化得到漿化料;(5)將步驟(4)得到的漿化料按照升溫速度3.5℃/min升溫,升溫至溫度為88℃,然后在此溫度下反應(yīng)40min,待物料由灰色變成白色為止,然后過濾,得到母液和磷酸鐵,將磷酸鐵繼續(xù)加入82.5℃的熱水洗滌,洗滌至溶液的ph為5.25,然后得到洗滌后的磷酸鐵,經(jīng)過烘干、篩分和除鐵后得到磷酸鐵。所述催化劑為將氫氧化鐵與鈦酸混合,氫氧化鐵與鈦酸的摩爾比為1:5.5,在壓力為5.75個大氣壓下,溫度為213℃反應(yīng),得到的固體經(jīng)過洗滌之后,在還原性氣氛下高溫還原,得到催化劑,碳酸鎳與鈦酸的摩爾比1:1.18,還原性氣氛為一氧化碳氣氛,還原溫度為255℃,每小時通入還原性氣體的摩爾數(shù)與鎳摩爾數(shù)之比為5.2:1,還原時間為4.3小時,即得催化劑,所述催化劑的組分為四氧化三鐵和二氧化鈦的混合物,四氧化三鐵均勻分散在二氧化鈦上,四氧化三鐵的粒徑為12nm,四氧化三鐵中的亞鐵與三價鐵的比例為0.5001:1,二氧化鈦的粒徑為45nm。所述步驟(1)中異壬烷、正丁醇鈉、氨氣、氫氣的摩爾比為2.15:1.13:1.25:0.44,萃取劑制備的反應(yīng)條件為溫度為135℃,壓力為2.12個大氣壓,反應(yīng)時間為2.25小時,反應(yīng)完畢,收集139℃的餾分,得到純度為99.14%的萃取劑,蒸餾后剩余的物質(zhì)返回繼續(xù)制備萃取劑,催化劑的加入量為異壬烷、正丁醇鈉、氨氣和氫氣總質(zhì)量的0.015%,得到的水相搭配高濃度的次氯酸溶液返回繼續(xù)使用。所述步驟(2)中第一濾渣加入氫氧化鈉溶液,在ph為13.25下、溫度為103℃下反應(yīng),過濾,得到的濾液加入鹽酸調(diào)節(jié)溶液的ph為6.85,過濾,得到鈦酸,返回步驟(1)制備催化劑。所述步驟(3)中萃取過程中,拌時將有機相的液滴分散為粒徑為0.33mm的直徑,水相為連續(xù)相,在鹽酸溶液洗滌過程中,攪拌時將有機相的液滴分散為粒徑為0.019mm的直徑,水相為連續(xù)相,萃取過程得到的萃余液加入氫氧化鈉溶液調(diào)節(jié)溶液的ph為9.25,然后過濾,得到的濾液為氯化鈉溶液,返回步驟(2)中使用,得到的濾渣漿化后通入空氣氧化,氧化至濾渣中的錳完全轉(zhuǎn)化成四價態(tài),然后加入硫酸調(diào)節(jié)漿料的ph為1.29,過濾,濾渣為錳含量大于30%的錳渣,濾液經(jīng)過濃縮結(jié)晶得到純度>95%的硫酸鎂晶體。所述步驟(4)中磷酸二氫銨溶液的濃度為0.25mol/l,離心分離得到的濾液靜置19min分層,然后再外加超聲波進行分層,超聲波的功率密度為0.33w/cm2,超聲時間為12min,分層后進行有機相和水相的分離,得到的有機相返回步驟(1)使用,得到的水相為氯化銨溶液,離心分離得到的固體與碳酸氫鈉溶液的質(zhì)量比為1:5.8進行洗滌,洗滌后得到的濾液加入鹽酸調(diào)節(jié)溶液的ph為5.98,然后靜置分層,得到的有機相返回步驟(1)使用,含鐵有機相加入磷酸二氫銨溶液混合時采用的反應(yīng)釜高與直徑之比為1:0.725,分散盤攪拌槳的直徑為反應(yīng)釜直徑的0.195倍,分散盤攪拌槳的齒高為其直徑的0.135倍,分散盤攪拌槳距離反應(yīng)釜底部的高度為反應(yīng)釜高度的0.068倍。所述步驟(5)漿化料升溫過程采用的反應(yīng)釜高與直徑之比為1:0.729,攪拌器采用折葉渦輪攪拌器,攪拌器的寬度為反應(yīng)釜直徑的0.239倍,攪拌器為四葉,每葉傾角為40°,每葉寬度為其長度的0.238倍,反應(yīng)釜內(nèi)設(shè)置有三個均勻分布的擋板,擋板的寬度為反應(yīng)釜直徑的0.068倍,擋板與反應(yīng)釜壁之間的間隙為擋板寬度的0.139倍,高溫反應(yīng)后得到的母液為磷酸溶液。步驟(4)中離心固液分離之后,液體靜置分層得到的水相加入氫氧化鈉調(diào)節(jié)溶液的ph為9.8,再進行蒸氨,蒸發(fā)的氨經(jīng)過步驟(5)得到的母液吸收,按照氨與磷酸的摩爾比1:1混合,得到磷酸二氫銨溶液,返回步驟(4)使用,蒸氨后的溶液為氯化鈉溶液,返回步驟(2)使用。步驟(5)中洗滌磷酸鐵得到的洗滌水加入步驟(1)得到的萃取劑混合攪拌,按照有機相與水相的體積比1:4.25混合,混合時間為19min,將磷酸萃取到有機相中,加入氨水反萃得到磷酸二氫銨溶液返回步驟(4)使用,萃余液中的磷酸含量低于10ppm,萃余液體積的68%返回做磷酸鐵洗滌水使用,剩余32%外排。最終得到的磷酸鐵指標(biāo)如下:指標(biāo)鐵含量磷鐵摩爾比d10d50d90數(shù)值29.15%1.003351nm484nm588nmd100camgnanico810nm2.3ppm4.5ppm3.8ppm1.6ppm0.28ppmmnzncutialsi1.9ppm1.2ppm0.4ppm0.45ppm1.8ppm1.3ppm振實密度硫酸根氯離子betph1.14g/ml1.39ppm2.5ppm9.5m2/g3.15附圖1、2和3分別為本發(fā)明實施例1、2、3的激光粒度分布圖,從粒度部分圖看來,粒度分布非常窄。從圖4來看,其剖面圖內(nèi)部基本無空心、氣孔和疏松多孔結(jié)構(gòu),生長密實。采用自己制備的萃取劑,來萃取鐵,鐵的萃取率高且其他雜質(zhì)的共萃少最終得到的產(chǎn)品雜質(zhì)含量低且最終鐵的回收率高。將實施例1、2、3與常規(guī)的液相法合成的磷酸鐵做比較,數(shù)據(jù)如下:噸產(chǎn)品廢水排放量每噸生產(chǎn)成本鐵的回收率實施例120.2噸5500元99.01%實施例223.1噸5800元98.95%實施例319.2噸5700元98.76%常規(guī)的磷酸鐵80-100噸9000-10000元92.5%最后說明的是,以上實施例僅用以說明本發(fā)明的技術(shù)方案而非限制,盡管參照較佳實施例對本發(fā)明進行了詳細說明,本領(lǐng)域的普通技術(shù)人員應(yīng)當(dāng)理解,可以對本發(fā)明的技術(shù)方案進行修改或者等同替換,而不脫離本發(fā)明技術(shù)方案的宗旨和范圍,其均應(yīng)涵蓋在本發(fā)明的權(quán)利要求范圍當(dāng)中。當(dāng)前第1頁12