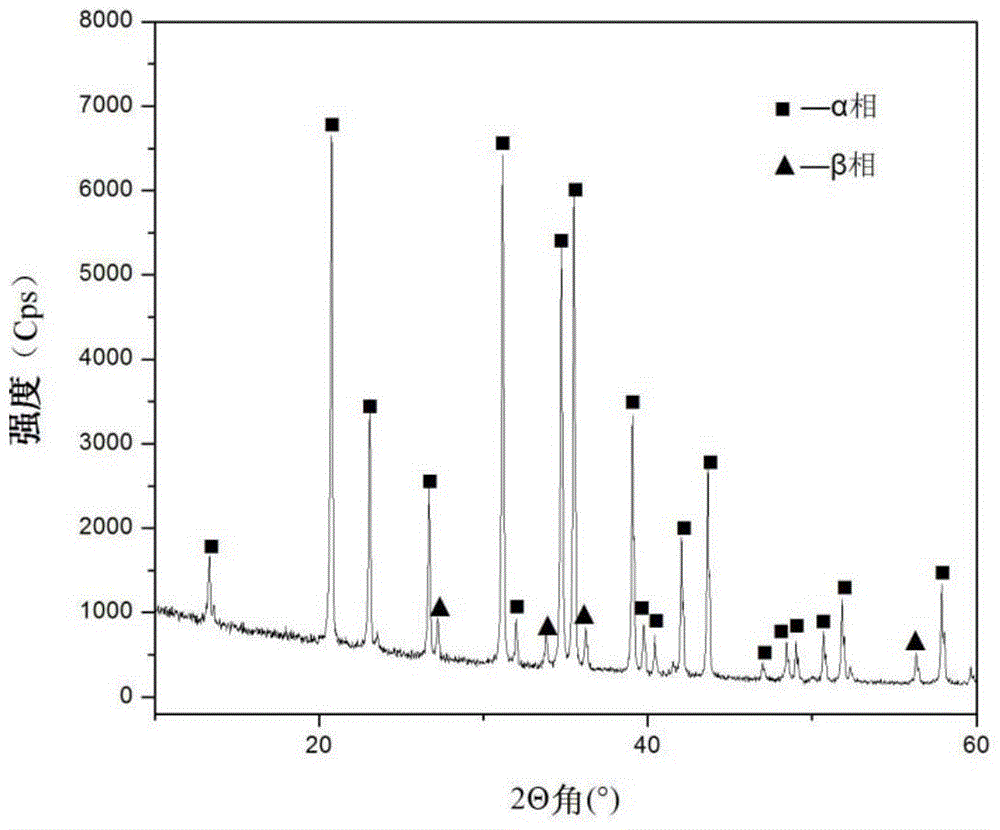
本發(fā)明涉及氮化硅的制備領(lǐng)域,尤其涉及一種利用多孔硅制備高α相氮化硅的方法。
背景技術(shù):氮化硅是一種應(yīng)用廣泛的特種陶瓷材料。之所以應(yīng)用廣泛,是因?yàn)榈杈哂性S多優(yōu)異的性能。首先,氮化硅是一種強(qiáng)結(jié)合力的共價(jià)鍵化合物,要到1800℃左右,它才會(huì)發(fā)生分解,所以氮化硅具有很好的高溫穩(wěn)定性;然后,氮化硅不與大多數(shù)熔融金屬發(fā)生反應(yīng),也不會(huì)和除氫氟酸以外的所有無機(jī)酸反應(yīng),所以氮化硅具有非常好的抗化學(xué)腐蝕的能力;此外,氮化硅還有比重輕、強(qiáng)度高、硬度大、耐磨損等優(yōu)點(diǎn)。因此,在冶金、汽車、航天、醫(yī)療等廣大領(lǐng)域都有氮化硅的身影。除了反應(yīng)燒結(jié)氮化硅外,大多數(shù)氮化硅陶瓷都是使用氮化硅陶瓷粉為原料進(jìn)行高溫高壓燒結(jié)而成。因而氮化硅陶瓷粉的品質(zhì),對氮化硅陶瓷的燒結(jié)和質(zhì)量都有重大的影響。為了得到高強(qiáng)度、高硬度的氮化硅陶瓷,往往希望氮化硅陶瓷粉具有α相含量高、粒度分布均勻等特點(diǎn)。這是由于在氮化硅高溫?zé)Y(jié)過程中,α相可以轉(zhuǎn)變?yōu)榘魻罨蛘哚槧畹摩孪?,這種具有一定長寬比的β相將會(huì)像增韌纖維一樣,有助于氮化硅陶瓷強(qiáng)度、硬度等性能的提高。而粒度分布均勻的氮化硅粉末更容易燒結(jié)出組織均勻而且致密的氮化硅陶瓷。因此,制備α相含量高、粒度分布均勻的氮化硅粉末具有實(shí)際的科研意義和應(yīng)用價(jià)值。氮化硅陶瓷粉的制備有直接氮化法、碳熱還原法、硅酰亞胺分解法、等離子合成法等方法。其中,直接氮化法,即硅粉與氮?dú)庠诟邷叵路磻?yīng)生成氮化硅的方法,由于其具有生產(chǎn)工藝簡單易行,生產(chǎn)設(shè)備操作容易,生產(chǎn)成本較低等優(yōu)點(diǎn),得到了產(chǎn)業(yè)界和科研工作者廣泛的認(rèn)同和采納。但是, 由于氮?dú)庠诠滔嘀袛U(kuò)散系數(shù)小,硅粉氮化速率慢,使得硅粉完全氮化所需的時(shí)間非常長。而且硅粉氮化是一個(gè)強(qiáng)放熱反應(yīng),反應(yīng)放出的熱量將在硅粉中聚集,使得反應(yīng)體系很容易產(chǎn)生過熱,體系的過熱常常使得高溫下亞穩(wěn)定的α相轉(zhuǎn)變?yōu)榉€(wěn)定的β相,造成產(chǎn)物中α相含量降低。于是,針對直接氮化法生產(chǎn)周期長、體系容易過熱等問題,本領(lǐng)域的科研工作者和生產(chǎn)技術(shù)人員做了許多的努力和改進(jìn)。其中,F(xiàn)ukuhira等人在公開號為US5441694A的美國專利文獻(xiàn)中公開了一種制備高α相氮化硅的方法,即在硅粉氮化體系中添加Cu或者Cu的化合物作為催化劑,使得反應(yīng)溫度降低,反應(yīng)時(shí)間縮短。此外,Cu良好的導(dǎo)熱能力可以幫助體系更順利的將熱量導(dǎo)出,從而降低體系過熱的可能性,提高α相的含量。但是,由于Cu和Si的密度相差很大,反應(yīng)前難以將兩者混合均勻,而且反應(yīng)后Cu作為雜質(zhì)殘留在氮化硅中,將影響氮化硅燒結(jié)的性能。James.P等人在公開號為US25519124的美國專利中也提出一種硅粉氮化的前處理工藝,即在高溫氮化前,先在一定的溫度和氫氣氣氛下對硅粉進(jìn)行預(yù)先的熱處理,其中,溫度為200~800℃,氣氛中氫氣含量為25~100%(V%)。這是由于低溫下氫氣可以將硅表面的氧化層還原去除,有助于后續(xù)的氮化反應(yīng)的進(jìn)行。雖然此方案可以有效縮短反應(yīng)時(shí)間,但是,200~800℃高溫下使用氫氣濃度較高的混合氣是有一定的危險(xiǎn)性的,不符合工業(yè)化的安全生產(chǎn)的要求。公開號為CN102173396A的中國專利中提出了使用旋轉(zhuǎn)爐制備高α相氮化硅的辦法。在硅粉氮化反應(yīng)期間,轉(zhuǎn)動(dòng)爐管,使得反應(yīng)物在爐管中翻轉(zhuǎn),這有利于硅粉和氮?dú)獬浞值慕佑|,并有利體系的散熱,可以有效的提高產(chǎn)物中α相的含量。但是,高溫下旋轉(zhuǎn)的爐管很容易變形和斷裂,這也不符合穩(wěn)定安全的生產(chǎn)要求。此外,公開號為CN102245503A的中國專利中提出了使用兩步法硅粉氮化的方案,此方案中,硅粉先在圓柱形回轉(zhuǎn)爐的1150~1250℃的溫區(qū)中部分氮化,然后轉(zhuǎn)移到1250~1350℃的溫區(qū)中完全氮化。雖然此方案也可以在一定程度上提高α相的含量,但是對設(shè)備要求很高,而且操作過程復(fù) 雜,第一步氮化的程度難以控制,重復(fù)性較差,也不適合工業(yè)化生產(chǎn)。
技術(shù)實(shí)現(xiàn)要素:本發(fā)明提供了一種利用多孔硅制備高α相氮化硅的方法,高效制備得到了高α相含量、粒徑分布均勻的氮化硅,本制備方法工藝簡單、性能可控,且生產(chǎn)周期短、極大地降低了生產(chǎn)能耗,成本低廉,適合于大規(guī)模的工業(yè)化生產(chǎn)。一種利用多孔硅制備高α相氮化硅的方法,步驟如下:以多孔硅為原料,在氮?dú)鈿夥障?,依次?jīng)高溫煅燒、研磨處理,得到所述的高α相氮化硅。本發(fā)明以多孔硅為原料,首先,其比表面積可以達(dá)到100m2/g以上,這樣大的比表面積可以大幅度增加氮?dú)馀c硅的接觸面積,提高反應(yīng)速率,縮短反應(yīng)所需的時(shí)間;其次,本發(fā)明采用的多孔硅的孔隙率很高,經(jīng)研究發(fā)現(xiàn),能夠很好地疏散反應(yīng)產(chǎn)生的熱量,有效的控制反應(yīng)體系的溫度,抑制硅粉的自燒結(jié),進(jìn)而獲得高α相含量的氮化硅;再次,本發(fā)明采用的多孔硅粒度分布均勻,因此制備得到的氮化硅的粒度分布也很均勻,利于其進(jìn)一步的應(yīng)用。作為優(yōu)選,所采用的多孔硅的粒徑為1~20μm,孔隙為30~500nm,比表面積大于100m2/g。進(jìn)一步優(yōu)選,所述的多孔硅的粒徑為1~10μm,比表面積大于100m2/g,多孔硅孔隙為50~200nm。最優(yōu)選,采用的多孔硅的粒徑為7.5~10μm,比表面積大于100m2/g,多孔硅孔隙為100~200nm。以其為原料,制備得到的氮化硅中α相含量最高。作為優(yōu)選,所述高溫煅燒的溫度為1250~1350℃,保溫時(shí)間為15~30h。作為優(yōu)選,所述的研磨在行星式球磨機(jī)中進(jìn)行。進(jìn)一步優(yōu)選,所述行星式球磨機(jī)的磨球采用熱壓燒結(jié)的氮化硅陶瓷球,磨球直徑為1~10mm,球料比為2~10,球磨介質(zhì)為無水乙醇,球磨時(shí)間為2~10h。作為優(yōu)選,本發(fā)明中所述的多孔硅可以通過熱降解硅化鎂制備得到,具體為:以硅化鎂為原料,在高溫?zé)崽幚頎t中,于氮?dú)饣蛘叨栊詺怏w和氧氣的混合氣氛下,經(jīng)300~800℃,15~35h熱分解得到多孔硅。作為優(yōu)選,所述混合氣氛中氧氣的含量為10~30%;進(jìn)一步優(yōu)選,所述熱分解的溫度為400~600℃。通過對氧氣分壓及分解溫度的精確調(diào)控,可以制備得到本發(fā)明中所需要的特定粒徑、孔隙和比表面積的多孔硅粉。與現(xiàn)有技術(shù)相比,本發(fā)明具有如下優(yōu)點(diǎn):本發(fā)明以多孔硅為原料,利用材料本身的性能,無需外加助劑,即可很好地疏散反應(yīng)產(chǎn)生的熱量,有效的控制反應(yīng)體系的溫度,抑制硅粉的自燒結(jié),進(jìn)而獲得高α相含量的氮化硅,α相氮化硅的含量高達(dá)92%以上。本發(fā)明的制備工藝簡單、性能可控,且生產(chǎn)周期短、極大地降低了生產(chǎn)能耗,成本低廉,適合于大規(guī)模的工業(yè)化生產(chǎn)。附圖說明圖1為實(shí)施例1中制備產(chǎn)物的XRD圖譜;圖2為實(shí)施例2中制備產(chǎn)物的XRD圖譜;圖3為實(shí)施例3中制備產(chǎn)物的XRD圖譜。具體實(shí)施方式下面通過具體實(shí)施例對本發(fā)明作進(jìn)一步說明,但本發(fā)明的保護(hù)范圍不局限于以下實(shí)施例。實(shí)施例1多孔硅原料的制備過程如下:將硅化鎂置于高溫?zé)崽幚頎t中進(jìn)行熱處理,反應(yīng)溫度為450℃,時(shí)間為35h,整個(gè)熱處理過程中通入氬氣和氧氣的混合氣,其中氧氣的含量為25%。分別使用1Mol/L的鹽酸和去離子水對上述得到的產(chǎn)物清洗三遍,然后離心,再在真空條件下烘干。取用上述自行制備的多孔硅原料,其粒度為1~5μm,比表面積大于 100m2/g,多孔硅孔隙大小為75~150nm。在氮?dú)鈿夥障?,?300℃保溫25h,即可得到疏松的高α相氮化硅。再使用行星式球磨機(jī)對得到的氮化硅進(jìn)行球磨。其磨球?yàn)闊釅簾Y(jié)的氮化硅陶瓷球,磨球直徑2mm,球料比7.5,球磨介質(zhì)為無水乙醇,球磨5h即可以得到α相含量高,粒度分布均勻的氮化硅陶瓷粉。將本實(shí)施例制備的產(chǎn)物進(jìn)行X射線能譜分析(XRD),結(jié)果如圖1所示,α相含量為93.8%。實(shí)施例2多孔硅原料的制備過程如下:將硅化鎂置于高溫?zé)崽幚頎t中進(jìn)行熱處理,反應(yīng)溫度為500℃,時(shí)間為30h,整個(gè)熱處理過程中通入氬氣和氧氣的混合氣,其中氧氣的含量為15%。分別使用1Mol/L的鹽酸和去離子水對上述得到的產(chǎn)物清洗三遍,然后離心,再在真空條件下烘干。取用上述自行制備的多孔硅原料,其粒度為7.5~10μm,比表面積大于100m2/g,多孔硅孔隙大小為100~200nm。在氮?dú)鈿夥障?,?320℃保溫20h,即可得到疏松的高α相氮化硅。再使用行星式球磨機(jī)對得到的氮化硅進(jìn)行球磨。其磨球?yàn)闊釅簾Y(jié)的氮化硅陶瓷球,磨球直徑5mm,球料比5,球磨介質(zhì)為無水乙醇,球磨7.5h即可以得到α相含量高,粒度分布均勻的氮化硅陶瓷粉。將本實(shí)施例制備的產(chǎn)物進(jìn)行X射線能譜分析(XRD),結(jié)果如圖2所示,α相含量為94.5%。實(shí)施例3多孔硅原料的制備過程如下:將硅化鎂置于高溫?zé)崽幚頎t中進(jìn)行熱處理,反應(yīng)溫度為600℃,時(shí)間為20h,整個(gè)熱處理過程中通入氬氣和氧氣的混合氣,其中氧氣的含量為10%。分別使用1Mol/L的鹽酸和去離子水對上述得到的產(chǎn)物清洗三遍,然 后離心,再在真空條件下烘干。取用上述自行制備的多孔硅原料,其粒度為10~20μm,比表面積大于100m2/g,多孔硅孔隙大小為150~500nm。在氮?dú)鈿夥障?,?350℃保溫15h,即可得到疏松的高α相氮化硅。再使用行星式球磨機(jī)對得到的氮化硅進(jìn)行球磨。其磨球?yàn)闊釅簾Y(jié)的氮化硅陶瓷球,磨球直徑7.5mm,球料比5,球磨介質(zhì)為無水乙醇,球磨5h即可以得到α相含量高,粒度分布均勻的氮化硅陶瓷粉。將本實(shí)施例制備的產(chǎn)物進(jìn)行X射線能譜分析(XRD),結(jié)果如圖3所示,α相含量為92.1%。