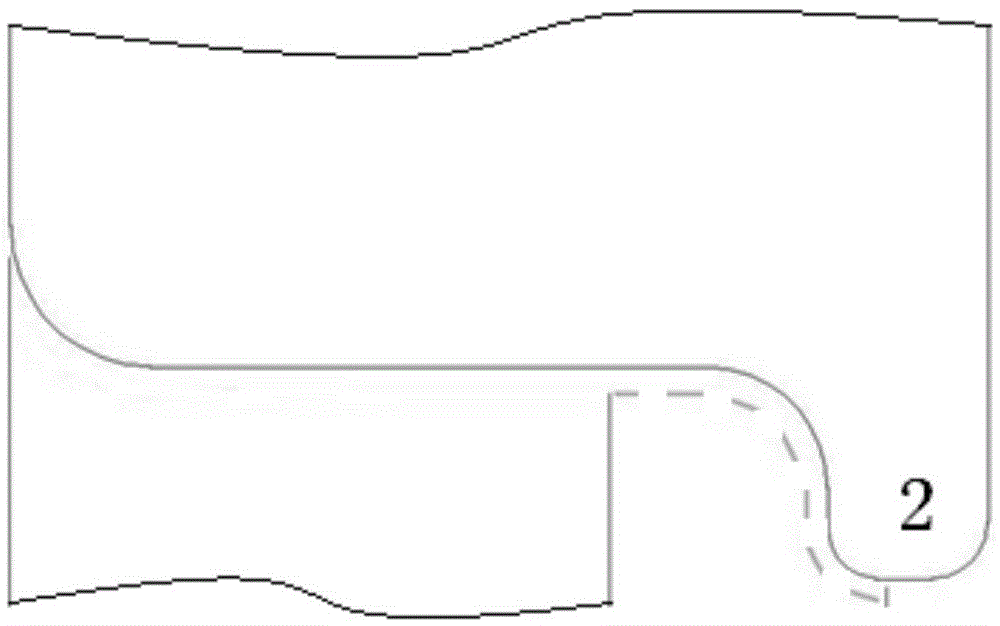
本發(fā)明涉及一種提高機車車輪耐磨性的超聲加工方法及應用,屬于超聲金屬表面加工的
技術領域:
。
背景技術:
:眾所周知,鐵路運輸是基于輪軌相互作用產(chǎn)生的黏著牽引力和黏著制動力以實現(xiàn)列車運行的,輪軌間因摩擦磨損在鐵路運輸中消耗的能量和能源很多,耗資也很大。隨著鐵路運輸向高速、重載發(fā)展,因摩擦磨損所致的事故風險也在增加。輪軌接觸面形成的各種損傷,不但縮短了輪軌的使用壽命,在嚴重磨損后還會導致輪對和鋼軌失效,危及行車安全。車輪是鐵路機車車輛的重要走行部件。在列車運行中,車輪滾動會使車輪踏面和輪緣發(fā)生磨耗,而車輪在鋼軌上滑動也會造成踏面損傷。據(jù)失效分析統(tǒng)計,鐵道機車車輛車輪損傷的主要類型有輪緣磨耗、輪輞疲勞裂紋、熱損傷、車輪踏面剝離和崩裂等。輪緣是車輪上的重要組成部分,使車輪能可靠地通過曲線和道岔,對列車行駛的安全性及穩(wěn)定性具有重要作用,輪緣的異常磨耗往往會使正常的輪軌關系發(fā)生改變,降低車輛動力性能和乘車舒適度?;疖囋诮?jīng)過曲線和道岔時,鋼軌對輪對的作用力一部分在車輪的踏面處,另一部分作用于輪對的輪緣部,此時,輪緣部的磨損最快。機車輪對的鏇修依據(jù),是通過檢測輪緣的厚度來判斷,當輪緣的厚度減小到一個確定值時,就需要對輪對進行鏇修,否則會影響列車的運行安全。機車輪對鏇修加工現(xiàn)采用的加工方式為數(shù)控車削,即當輪對輪緣厚度減小到一定值時,通過數(shù)控車削,將車輪直徑減小,使車削后的輪緣厚度恢復到要求的數(shù)值。經(jīng)過車削后,不再進行其它的表面處理。經(jīng)車削后的輪緣部表面粗糙度值一般在Ra值6.3左右。經(jīng)車削后的輪緣表面處于拉應力狀態(tài),拉應力的存在使得輪對初期磨損非???,從而使輪對的使用壽命大大降低。技術實現(xiàn)要素:針對現(xiàn)有技術的不足,本發(fā)明提供一種提高機車車輪耐磨性的超聲加工方法。本發(fā)明還提供上述加工方法的應用。本發(fā)明的技術方案如下:一種提高機車車輪耐磨性的超聲加工方法,包括:對機車車輪的輪緣進行超聲加工,即利用超聲加工工具頭對沿主軸旋轉的輪緣的表面進行超聲加工。根據(jù)本發(fā)明優(yōu)選的,所述機車車輪是新出廠的機車車輪或是磨損后的機車車輪。根據(jù)本發(fā)明優(yōu)選的,當所述機車車輪是磨損后的機車車輪時,對經(jīng)半精加工后的機車車輪的輪緣進行超聲加工。根據(jù)本發(fā)明優(yōu)選的,對機車車輪的輪緣進行車削半精加工,即使所述輪緣的表面粗糙度為3.2-10μm。根據(jù)本發(fā)明優(yōu)選的,所述超聲加工的參數(shù)為:主軸的轉速為5-45r/min;進給量為0.03-0.2mm/r;超聲加工工具頭對待加工表面的壓力為300-3000N。根據(jù)本發(fā)明優(yōu)選的,所述超聲加工的參數(shù)為:主軸的轉速為19r/min;進給量為0.1mm/r;超聲加工工具頭對待加工表面的壓力為1200N。根據(jù)本發(fā)明優(yōu)選的,利用超聲加工工具頭對沿主軸旋轉的輪緣的表面進行超聲加工,所述超聲加工的往返次數(shù)為1-3次。根據(jù)本發(fā)明優(yōu)選的,利用超聲加工工具頭對沿主軸旋轉的輪緣的表面進行超聲加工,所述超聲加工的振幅為5-25μm。一種利用如上述超聲加工方法以提高機車車輪耐磨性的應用:針對機車車輪對應存在磨損的區(qū)域進行超聲加工,所述超聲加工的參數(shù)為:主軸的轉速為5-45r/min;進給量為0.03-0.2mm/r;超聲加工工具頭對待加工表面的壓力為300-3000N。根據(jù)本發(fā)明優(yōu)選的,在所述磨損的區(qū)域進行超聲加工之前,對其進行車削半精加工,即使其的表面粗糙度為3.2-10μm。根據(jù)本發(fā)明優(yōu)選的,所述超聲加工的參數(shù)為:主軸的轉速為19r/min;進給量為0.1mm/r;超聲加工工具頭對待加工表面的壓力為1200N。本發(fā)明的優(yōu)勢在于:本發(fā)明所述的超聲加工方法能夠解決目前機車車輛輪軌摩擦磨損嚴重、修理費用高的現(xiàn)象。本發(fā)明所述的超聲加工方法不但可以對剛出廠的機車車輪進行加工,還能對磨損后的機車車輪進行修復加工,其中,采用超聲加工方法對機車車輪輪緣部進行表面加工后,會使輪緣的金屬表面的拉應力變成壓應力,輪緣部表面粗糙度值會大大降低的同時,在其表面預置理想的壓應力,其表面的硬度得到了提高,晶粒得到了細化,耐磨性大幅提高,改善了輪軌接觸關系,減小輪對的滾動接觸疲勞損傷。減小車輪的磨耗速率,延長車輪的鏇修周期以及使用壽命。附圖說明圖1是本發(fā)明所述利用超聲加工方法對機車車輪的加工示意圖;圖2是機車車輪上待超聲加工的區(qū)域示意圖,其中虛線部分為待加工區(qū)域;圖3a、圖3b、圖3c、圖3d、圖3e、為本發(fā)明實施例4中,通過改變超聲加工壓力對輪緣超聲加工后,所述輪緣表面金相圖;在圖1和圖2中,1、超聲加工工具頭;2、輪緣。具體實施方式下面結合實施例和說明書附圖對本發(fā)明做詳細的說明,但不限于此。如圖1-2所示。實施例1、一種提高機車車輪耐磨性的超聲加工方法,包括:對機車車輪的輪緣2進行超聲加工,即利用超聲加工工具頭1對沿主軸旋轉的輪緣2的表面進行超聲加工。所述機車車輪是新出廠的機車車輪。實施例2、如實施例1所述的一種提高機車車輪耐磨性的超聲加工方法,其區(qū)別在于,所述超聲加工的參數(shù)為:主軸的轉速為5-45r/min;進給量為0.03-0.2mm/r;超聲加工工具頭對待加工表面的壓力為300-3000N。實施例3、如實施例1所述的一種提高機車車輪耐磨性的超聲加工方法,其區(qū)別在于,所述機車車輪是磨損后的機車車輪。當所述機車車輪是磨損后的機車車輪時,對經(jīng)半精加工后的機車車輪的輪緣進行超聲加工。對機車車輪的輪緣進行車削半精加工,即使所述輪緣的表面粗糙度為3.2-10μm。實施例4、如實施例2、3所述的一種提高機車車輪耐磨性的超聲加工方法,其區(qū)別在于,所述超聲加工的參數(shù)為:主軸的轉速為19r/min;進給量為0.1mm/r;超聲加工工具頭1對待加工表面的壓力為1200N。如本實施例,改變超聲加工工具頭對待加工表面的壓力分別為:100N、300N、1200N、3000N、3500N,經(jīng)加工后所述車輪輪緣的殘余應力均值如下:試樣/試樣處理參數(shù)殘余應力均值未經(jīng)超聲加工處理的車輪輪緣-17.68超聲波加工壓力100N-55.21超聲波加工壓力300N-98.7超聲波加工壓力1200N-176.07超聲波加工壓力3000N-212.93超聲波加工壓力3500N-277.04其中圖3a為超聲加工工具頭對待加工表面的壓力為100N時,所加工出的輪緣表面的金相圖;其中圖3b為超聲加工工具頭對待加工表面的壓力為300N時,所加工出的輪緣表面的金相圖;其中圖3c為超聲加工工具頭對待加工表面的壓力為1200N時,所加工出的輪緣表面的金相圖;其中圖3d為超聲加工工具頭對待加工表面的壓力為3000N時,所加工出的輪緣表面的金相圖;其中圖3e為超聲加工工具頭對待加工表面的壓力為3500N時,所加工出的輪緣表面的金相圖。實施例5、如實施例2、3所述的一種提高機車車輪耐磨性的超聲加工方法,其區(qū)別在于,利用超聲加工工具頭1對沿主軸旋轉的輪緣2的表面進行超聲加工,所述超聲加工的往返次數(shù)為1-3次。實施例6、如實施例2、3所述的一種提高機車車輪耐磨性的超聲加工方法,其區(qū)別在于,利用超聲加工工具頭1對沿主軸旋轉的輪緣2的表面進行超聲加工,所述超聲加工的振幅為5-25μm。實施例7、一種利用如實施例1-6所述超聲加工方法以提高機車車輪耐磨性的應用:針對機車車輪對應存在磨損的區(qū)域進行超聲加工,所述超聲加工的參數(shù)為:主軸的轉速為5-45r/min;進給量為0.03-0.2mm/r;超聲加工工具頭對待加工表面的壓力為300-3000N。實施例8、一種利用如實施例7所述提高機車車輪耐磨性的應用,其區(qū)別在于,在所述磨損的區(qū)域進行超聲加工之前,對其進行車削半精加工,即使其的表面粗糙度為3.2-10μm。實施例9、一種利用如實施例7所述提高機車車輪耐磨性的應用,其區(qū)別在于,所述超聲加工的參數(shù)為:主軸的轉速為19r/min;進給量為0.1mm/r;超聲加工工具頭1對待加工表面的壓力為1200N。試驗對比例:對實施例3和實施例4中加工后的機車車輪進行試驗對比如下:在機車車輪的表面進行超聲加工的過程中,影響加工效果的因素有主軸轉速、進給量和壓力,本試驗將上述三個因素作為試驗因素,分別記作A(對應主軸轉速)、B(對應進給量)和C(對應壓力)。本試驗對比例中確定各因素分別取三個水平,即:A(對應主軸轉速)對應的三個標準包括:A1=5r/min;A2=19r/min;A3=45r/min;B(對應進給量)對應的三個標準包括:B1=0.03mm/r;B2=0.1mm/r;B3=0.2mm/r;C(對應壓力)對應的三個標準包括:C1=300N;C2=1200N;C3=3000N。表1:超聲加工應用于機車車輪表面耐磨性能試驗參數(shù)由表1的試驗數(shù)據(jù)可知,當A(對應主軸轉速)對應A2=19r/min、B(對應進給量)對應B2=0.1mm/r、C(對應壓力)對應C2=1200N時,得到最佳的表面粗糙度、硬度、硬度提高均是最高。下面再結合正交試驗對上述數(shù)據(jù)進行分析,以驗證是否也是當A(對應主軸轉速)對應A2=19r/min、B(對應進給量)對應B2=0.1mm/r、C(對應壓力)對應C2=1200N時,得到最佳的表面粗糙度、硬度、硬度提高均是最高。正交試驗數(shù)據(jù)分析:A1=5r/min;A2=19r/min;A3=45r/min;B(對應進給量)對應的三個標準包括:B1=0.03mm/r;B2=0.1mm/r;B3=0.2mm/r;C(對應壓力)對應的三個標準包括:C1=300N;C2=1200N;C3=3000N。表2:三個試驗因素水平表按照正交試驗數(shù)據(jù)方法,可以選用L9(34)或L27(313);因本試驗僅考察三個因素對機車車輪表面加工效果的影響,不考察因素間的交互作用,故選用L9(34)正交表。在L9(34)正交表中填入各因素的水平值,便形成了正交試驗方案(表3):表3:正交試驗方案從表3中直觀可以看出,主軸轉速為19r/min,進給量為0.1mm/r,壓力為1200N時鋼軌與車輪的總磨損率最小,其水平組合為A2B2C2。對試驗的結果進行分析1.從滑動磨損的總磨損率進行分析,表4對于因素A主軸轉速來說,可以看出k1>k3>k2。由于結果指標為磨損率,期望得到磨損率的最小值,所以可以判斷A2為A因素的優(yōu)水平。同理可以得到因素B和因素C的優(yōu)水平分別為B2和C2。因此優(yōu)組合為A2B2C2。另外從極差R的大小可以看出,在三個實驗因素中,因素B進給量對滑動磨損率的影響最大。2.從滾動磨損的總磨損率進行分析,表5對于因素A主軸轉速來說,可以看出k1>k3>k2。由于結果指標為磨損率,期望得到磨損率的最小值,所以可以判斷A2為A因素的優(yōu)水平。同理可以得到因素B和因素C的優(yōu)水平分別為B2和C2。因此優(yōu)組合為A2B2C2。另外從極差R的大小可以看出,在三個實驗因素中,因素B進給量對滾動磨損率的影響最大。由滑動磨損率的分析結果及滾動磨損率的結果可知,優(yōu)組合均為A2B2C2,因此選取A2B2C2對應的參數(shù)加工的工件進行摩擦磨損試驗。試驗結果表明,經(jīng)表面處理后,在滾動磨損和滑動磨損試驗中車輪試樣的耐磨性均提高了50%以上,同時,經(jīng)表面處理后的車輪對鋼軌試樣的磨損率也明顯降低。當前第1頁1 2 3