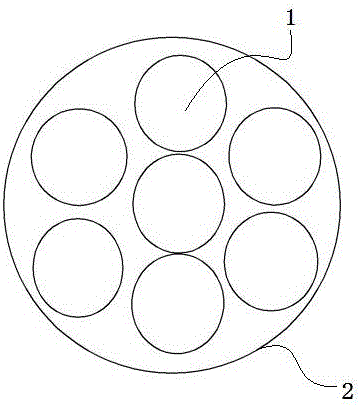
本發(fā)明涉及一種在海上使用的水中構(gòu)件裝置系留纜繩及其制作方法。
背景技術(shù):海上水中構(gòu)件裝置主要指海面浮筒泊位、浮標(biāo)、潛標(biāo)、航標(biāo)燈、水中兵器(水雷)等。過去這些水中構(gòu)件裝置在使用時(shí)的系留纜繩都采用鋼絲纜繩或錨鏈。現(xiàn)在隨著系留纜繩系統(tǒng)裝置使用范圍的擴(kuò)大和水深的增加,系留纜繩加長,重量隨之增加,浮體浮力無法支承。根據(jù)我國海區(qū)情況和海軍、海事(航管)部門的要求,不可能再用鋼絲纜繩或錨鏈作為系留索,需要替代材料。在實(shí)際使用中發(fā)現(xiàn)單層8股、12股結(jié)構(gòu)纜繩容易被海上風(fēng)力割斷和磨損,并不適合海上深水系泊。國內(nèi)外10多年海上系泊系統(tǒng)纜繩使用證明,超高分子量聚乙烯(UHMWPE)纖維是目前世界上強(qiáng)度最高的商業(yè)化高性能纖維。等直徑時(shí),其強(qiáng)度及伸長率與相應(yīng)的鋼纜相近,但重量僅為鋼纜的15%;等重量時(shí),其強(qiáng)度比鋼纜高15倍之多;其使用壽命比普通化纖纜繩一般高出2~3倍。用其纖維材料制成的系泊纜繩具有高強(qiáng)、高模、輕質(zhì)、低延伸、低蠕變,斷裂伸長率只有3%左右、耐海水腐蝕、耐紫外線輻射、漂浮于水、操作方便、經(jīng)久耐用、安全性高等特點(diǎn),所以超高分子量聚乙烯纜繩最適合長時(shí)間深水海上系泊的應(yīng)用。但在實(shí)際使用中發(fā)現(xiàn),超高分子量聚乙烯系泊纜繩如在高溫和持久強(qiáng)力下使用會(huì)發(fā)生蠕變性能不太好之弱點(diǎn),而蠕變的發(fā)展可導(dǎo)致纖維材料的破損和老化失效,限制其在海上系泊中的長期應(yīng)用。如作為長久性海上水中構(gòu)件裝置系留纜繩選用基材必須對(duì)其蠕變性能加以改善與提高,確保長久性海上水中構(gòu)件裝置系留纜繩在實(shí)際使用條件下的可靠性、耐久性、安全性。
技術(shù)實(shí)現(xiàn)要素:本發(fā)明要解決的技術(shù)問題是提供一種內(nèi)層纜芯由超高分子量聚乙烯制成8股形態(tài)結(jié)構(gòu),外層由耐磨高強(qiáng)型滌綸纖維編織成固定護(hù)套,具有更輕、更安全、更耐久性能的纜繩及其制作方法;為克服現(xiàn)有系留纜繩索扣存在的不耐磨和容易打滑松脫的現(xiàn)象,并保證纜繩及索扣綜合性能的利用。為了解決上述技術(shù)問題,本發(fā)明提供了一種海上用水中構(gòu)件裝置系留纜繩,為皮芯復(fù)合雙層結(jié)構(gòu);內(nèi)層纜芯由DM20超高分子量聚乙烯制成的8股形態(tài)結(jié)構(gòu),外層為耐磨高強(qiáng)型滌綸的固定護(hù)套。本發(fā)明一種海上用水中構(gòu)件裝置系留纜繩制作方法如下:步驟一:8股形態(tài)結(jié)構(gòu)的纜芯制備方法如下:a、制粗紗,選取纖度DM20超高分子量聚乙烯纖維3根通過拼線機(jī)捻合成粗紗;b、制繩紗,將7根合成的粗紗通過加捻機(jī)捻合成繩紗;c、制繩股,將3根合成的繩紗通過制股機(jī)捻合成繩股;d、編繩,將8根合成的繩股經(jīng)制繩機(jī)編織成8股纜芯;e、浸樹脂,將8股纜芯經(jīng)自動(dòng)浸膠機(jī)多次重復(fù)浸漬、涂覆LAG045樹脂,并通過擠膠裝置,擠出多余的樹脂;f、預(yù)拉處理,采用特制拉力機(jī)對(duì)纜芯進(jìn)行預(yù)拉,拉力為纜繩設(shè)計(jì)的實(shí)際使用拉力的2~3倍,預(yù)拉時(shí)間50~60秒,通過預(yù)拉處理,使纜芯形態(tài)相對(duì)固定,蠕變減?。籫、烘干,預(yù)拉處理后,將纜芯放到繩架上晾干或送入烘房烘干,同時(shí)卷裝成形候用;步驟二、固定護(hù)套編制如下:a、拼線,選取纖度1118D耐磨高強(qiáng)型滌綸長絲3根,捻合成粗紗;b、加捻,將拼線后的7根粗紗,通過加捻機(jī)進(jìn)行加捻,制作繩紗;c、制股,將加捻后的3根繩紗,在制股機(jī)上制成符合雙層編繩機(jī)錠子大小的筒子繩股;d、編制,將32根繩股圍繞纜芯經(jīng)雙層編繩機(jī)一次性編織成固定護(hù)套。采用本發(fā)明后,其有益效果為:采用超高分子量聚乙烯纖維,其超高分子量聚乙烯(UHMWPE)纖維是目前世界上強(qiáng)度最高的商業(yè)化高性能纖維。等直徑時(shí),其強(qiáng)度及伸長率與相應(yīng)的鋼纜相近,但重量僅為鋼纜的15%;等重量時(shí),其強(qiáng)度比鋼纜高15倍之多;其使用壽命比普通化纖纜繩一般高出2~3倍。用其纖維材料制成的系泊纜繩具有高強(qiáng)、高模、輕質(zhì)、低延伸、低蠕變,斷裂伸長率只有3%左右、耐海水腐蝕、耐紫外線輻射、漂浮于水、操作方便、經(jīng)久耐用、安全性高等特點(diǎn),所以超高分子量聚乙烯纜繩最適合長時(shí)間深水海上系泊的應(yīng)用。但在實(shí)際使用中發(fā)現(xiàn),超高分子量聚乙烯系泊纜繩如在高溫和持久強(qiáng)力下使用會(huì)發(fā)生蠕變性能不太好之弱點(diǎn),而蠕變的發(fā)展可導(dǎo)致纖維材料的破損和老化失效,限制其在海上系泊中的長期應(yīng)用。如作為長久性海上水中構(gòu)件裝置系留纜繩選用基材必須對(duì)其蠕變性能加以改善與提高,確保長久性海上水中構(gòu)件裝置系留纜繩在實(shí)際使用條件下的可靠性、耐久性、安全性。超高分子量聚乙烯纜繩蠕變的程度取決于UHMWPE纖維的型號(hào)、工作溫度、平均載荷和加載時(shí)間。通過改善與提高UHMWPE蠕變性能后,使得Dyneema纖維既具有最高的拉伸強(qiáng)度和模量,又具有最好的抗蠕變性能。不同蠕變性能Dyneema等級(jí)纖維特性與應(yīng)用比較長久性海上水中構(gòu)件裝置系留纜繩繩體選用具有超低蠕變性能的超高分子量聚乙烯DM20等級(jí)纖維制成纜芯,經(jīng)實(shí)驗(yàn)室測試證明達(dá)到系留纜繩高強(qiáng)、超輕、低延展、耐疲勞、30年持久壽命的基本特性要求。為進(jìn)一步增強(qiáng)系留纜繩使用的耐磨性、耐久性、耐候性,控制磨損和老化程度,保持纜繩強(qiáng)度的最佳化,系留纜繩纜芯外層設(shè)有固定護(hù)套,選用耐磨高強(qiáng)型滌綸纖維(PET)制作。不僅耐磨性能好、高強(qiáng),而且低延展、耐疲勞性能良好,綜合性能媲美錦綸。同時(shí)由于滌綸纖維價(jià)格便宜,相比錦綸等纖維更具性價(jià)比,相比普通滌綸長絲,耐磨高強(qiáng)型滌綸具有更好的耐磨性,能完善纜繩對(duì)耐磨性要求較高產(chǎn)品的性能。不同纖維材料耐磨及基本性能比較超高分子量聚乙烯和耐磨高強(qiáng)型滌綸復(fù)合雙層結(jié)構(gòu)系留纜繩既能滿足水中構(gòu)件裝置在風(fēng)暴中定位時(shí)最大載荷對(duì)剛度的要求,又能保證具有足夠的彈性來削弱由波浪運(yùn)動(dòng)引起的最大峰值載荷。已經(jīng)證明UHMWPE-PET復(fù)合雙層結(jié)構(gòu)繩纜是最適合長時(shí)間固定深海水中構(gòu)件裝置海上系留的應(yīng)用。同時(shí)確認(rèn)這種復(fù)合雙層結(jié)構(gòu)纜繩在海上深水中的應(yīng)用比鋼纜和錨鏈系泊系統(tǒng)具有更輕、更安全、更耐久的優(yōu)勢。超高分子量聚乙烯和耐磨高強(qiáng)型滌綸皮芯復(fù)合雙層結(jié)構(gòu)系留纜繩不僅具備超高分子量聚乙烯纜繩強(qiáng)度大、重量輕、低延展、低蠕變、耐老化、浮于水、易操作的特點(diǎn),而且具有和滌綸相當(dāng)?shù)哪Σ料禂?shù)及耐磨性能,從而極大地延長纜繩的使用壽命。附圖說明圖1為本發(fā)明海上用水中構(gòu)件裝置系留纜繩皮芯復(fù)合雙層結(jié)構(gòu)示意圖。圖2為本發(fā)明海上用水中構(gòu)件裝置系留纜繩截面結(jié)構(gòu)示意圖。具體實(shí)施方式如圖1和圖2所示,一種海上用水中構(gòu)件裝置系留纜繩,為皮芯復(fù)合雙層結(jié)構(gòu);內(nèi)層纜芯1由DM20超高分子量聚乙烯制成的8股形態(tài)結(jié)構(gòu),外層為耐磨高強(qiáng)型滌綸纖維編織的固定護(hù)套2。本發(fā)明一種海上用水中構(gòu)件裝置系留纜繩制作方法,其制作過程如下:步驟一:8股形態(tài)結(jié)構(gòu)的纜芯制備方法如下:a、制粗紗,選取纖度DM20超高分子量聚乙烯纖維3根通過拼線機(jī)捻合成粗紗;b、制繩紗,將7根合成的粗紗通過加捻機(jī)捻合成繩紗;c、制繩股,將3根合成的繩紗通過制股機(jī)捻合成繩股;d、編繩,將8根合成的繩股經(jīng)制繩機(jī)編織成8股纜芯;e、浸樹脂,將8股纜芯經(jīng)自動(dòng)浸膠機(jī)多次重復(fù)浸漬、涂覆LAG045樹脂,并通過擠膠裝置,擠出多余的樹脂;f、預(yù)拉處理,采用特制拉力機(jī)對(duì)纜芯進(jìn)行預(yù)拉,拉力為纜繩設(shè)計(jì)的實(shí)際使用拉力的2~3倍,預(yù)拉時(shí)間50~60秒,通過預(yù)拉處理,使纜芯形態(tài)相對(duì)固定,蠕變減小;g、烘干,預(yù)拉處理后,將纜芯放到繩架上晾干或送入烘房烘干,同時(shí)卷裝成形候用;編織工藝的關(guān)鍵在于控制纜芯的直徑,提高強(qiáng)力和力求粗細(xì)均勻??刂浦睆街饕谟谶m當(dāng)配置纖維的根數(shù)并合理組合,而纜芯的強(qiáng)度除與纖維材料的強(qiáng)度有關(guān)外,還與纖維纖度和編織時(shí)的密度大小有關(guān)。一般來說,纖度大有利于強(qiáng)度利用率的發(fā)揮。另外,隨著編織密度的減小,則纜芯的強(qiáng)度就增大。編織密度不能過大,否則纜芯不僅強(qiáng)度低而且手感較硬。編織密度適當(dāng)調(diào)節(jié),不僅有利于強(qiáng)度的提高,而且還能獲得良好的手感,纜芯的粗細(xì)均勻性與編織時(shí)的張力有關(guān)。在制粗紗、制繩紗、制繩股和編繩過程中,保持每根纖維所受張力基本一樣,捻距控制在20~30cm。在制粗紗、繩紗、繩股時(shí),均具有一定的捻度,這樣可以確保單絲的斷裂不會(huì)將強(qiáng)度的損失傳遞很遠(yuǎn),一般在幾個(gè)捻距后就沒有影響了。同樣單股繩紗的強(qiáng)力損失也不會(huì)傳遞很遠(yuǎn)。這樣提高了纜繩的整體耐磨性能,即便纜繩表面磨起毛,也不會(huì)對(duì)強(qiáng)度產(chǎn)生大的影響。實(shí)際使用證明,這種編織工藝與普通編織工藝相比纜繩強(qiáng)力能夠提高8~10%。步驟二、固定護(hù)套的編制如下:a、拼線,選取纖度1118D耐磨高強(qiáng)型滌綸長絲3根,捻合成粗紗;b、加捻,將拼線后的7根粗紗,通過加捻機(jī)進(jìn)行加捻,制作繩紗;c、制股,將加捻后的3根繩紗,在制股機(jī)上制成符合雙層編繩機(jī)錠子大小的筒子繩股;d、編制,將32根繩股圍繞纜芯經(jīng)雙層編繩機(jī)一次性編織成固定護(hù)套。上述工藝流程為: