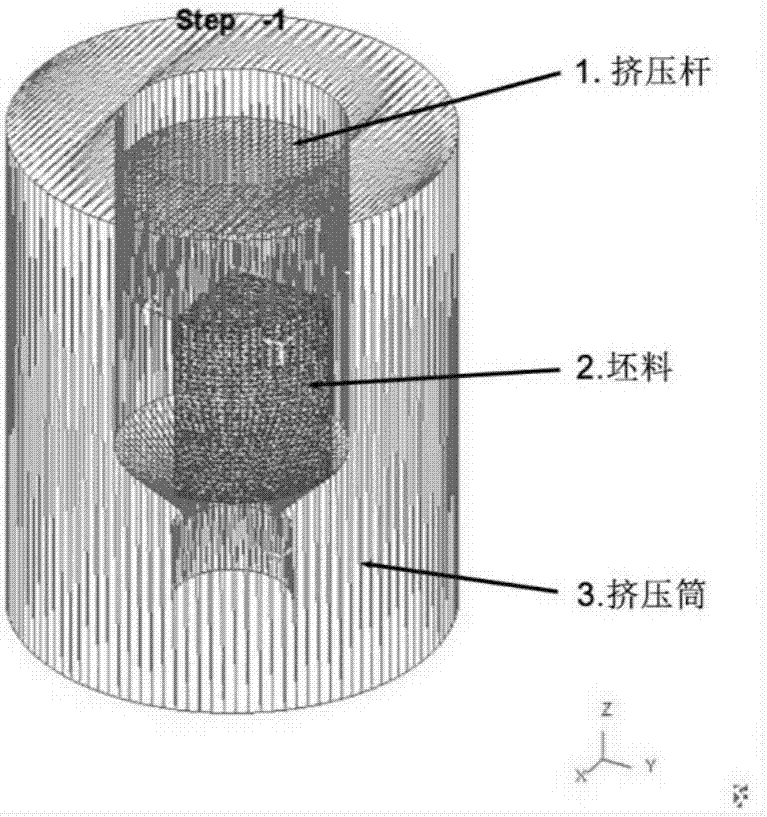
本發(fā)明涉及一種優(yōu)化合金擠壓工藝的方法,具體涉及一種粉末冶金合金的熱擠壓工藝的優(yōu)化方法,屬于塑性加工領(lǐng)域。
背景技術(shù):
:粉末鎳基高溫合金具有組織均勻、無(wú)宏觀偏析、合金化程度高、屈服強(qiáng)度高、抗氧化性能和疲勞性能好等優(yōu)點(diǎn),因此是熱結(jié)構(gòu)部件的常用材料之一。通過(guò)擠壓細(xì)化晶粒,不僅為后續(xù)的等溫鍛造和超塑性鍛造提供組織基礎(chǔ),也是提高合金的力學(xué)性能的有效手段。粉末鎳基高溫合金的熱擠壓工藝參數(shù)主要涉及擠壓比,擠壓速率,擠壓溫度、摩擦因子、工作帶長(zhǎng)度以及模具溫度、模具錐角等,以上參數(shù)均會(huì)影響擠壓過(guò)程。由于參數(shù)選擇的不合適,會(huì)使得擠壓出現(xiàn)“悶車”(無(wú)法順利擠出)、表面開裂、組織不均勻等現(xiàn)象,其中“悶車”現(xiàn)象往往在鎳基高溫合金中屬于常見(jiàn)現(xiàn)象。傳統(tǒng)的方法是通過(guò)大量的“試錯(cuò)”實(shí)驗(yàn)研究不同參數(shù)下的擠壓情況,然后不斷調(diào)整參數(shù),力圖尋求較好的擠壓效果:即既能最大限度地發(fā)揮設(shè)備的能力,又能順利地將試件擠出,獲得理想的組織和性能。但是,如上所述,影響擠壓的參數(shù)眾多,且存在相互影響,無(wú)法通過(guò)有限次的實(shí)驗(yàn)去達(dá)到所需的效果,且會(huì)導(dǎo)致很多實(shí)驗(yàn)的失??;或者沒(méi)能發(fā)揮設(shè)備的最大能力而造成資源的浪費(fèi);所以,存在為追求擠壓的順利而不得不選擇比較安全的擠壓工藝而致使擠壓產(chǎn)品的性能不佳等等問(wèn)題。而通過(guò)實(shí)驗(yàn)的獲得加工窗口,往往運(yùn)用到實(shí)際擠壓過(guò)程中也需要進(jìn)一步的調(diào)整,以保證順利擠出。隨著計(jì)算機(jī)技術(shù)的發(fā)展和模擬方法的成熟,使得許多工程上的問(wèn)題能夠通過(guò)計(jì)算機(jī)的模擬。例如,deform有限元軟件近年來(lái)更多地被用于熱擠壓的模擬。而質(zhì)量管理的統(tǒng)計(jì)分析軟件如minitab可以依據(jù)試驗(yàn)結(jié)果將多個(gè)影響因素和結(jié)果的關(guān)系建立起來(lái)。這為過(guò)程復(fù)雜、成本昂貴的熱擠壓工藝優(yōu)化提供了基礎(chǔ)。技術(shù)實(shí)現(xiàn)要素:本發(fā)明針對(duì)現(xiàn)有合金擠壓工藝存在的不足之處,提供一種經(jīng)濟(jì)、快速、合理而有效的優(yōu)化合金擠壓工藝的方法;為確定實(shí)際擠壓工藝提供指導(dǎo)依據(jù)。本發(fā)明一種優(yōu)化合金擠壓工藝的方法,包括下述步驟:步驟一建立待擠壓合金的本構(gòu)方程在a-b之間選取至少3個(gè)點(diǎn)值、優(yōu)選為3-10個(gè)值,進(jìn)一步優(yōu)選為3-5個(gè)值;所述a為待擠壓合金的動(dòng)態(tài)再結(jié)晶溫度,所述b為待擠壓合金熔點(diǎn)的0.85倍;在應(yīng)變速率為0.0001-100s-1之間選取至少3個(gè)點(diǎn)值;優(yōu)選為4-10個(gè)值,進(jìn)一步優(yōu)選為4-6個(gè)值;在選定的溫度和應(yīng)變速率的限定下,進(jìn)行壓縮實(shí)驗(yàn);收集應(yīng)力-應(yīng)變數(shù)據(jù),并根據(jù)所收集的應(yīng)力-應(yīng)變數(shù)據(jù)構(gòu)建合金的本構(gòu)方程;步驟二根據(jù)要求設(shè)定合金擠壓坯尺寸,建立坯料、擠壓桿和擠壓筒的三維幾何模型,三維模型中,擠壓桿和擠壓筒的實(shí)際尺寸參數(shù)根據(jù)實(shí)際參數(shù)確定;將步驟一所設(shè)定并求解的本構(gòu)方程導(dǎo)入固體力學(xué)有限元分析軟件的材料數(shù)據(jù)庫(kù)中作為熱擠壓坯料的材料參數(shù),并且用該軟件模擬分析擠壓過(guò)程,并且得到擠壓過(guò)程多個(gè)工藝參數(shù)在不同工藝參數(shù)水平下的擠壓過(guò)程模擬分析結(jié)果,然后通過(guò)統(tǒng)計(jì)分析或統(tǒng)計(jì)分析軟件分析,量化這些擠壓工藝參數(shù)對(duì)擠壓坯料的影響;步驟三根據(jù)操作時(shí),所用擠壓設(shè)備所能提供的最大施工條件和待加工材料要求,并以此為限制條件,優(yōu)化擠壓工藝參數(shù);從而形成在滿足設(shè)備條件和材料要求的限制條件下,待擠壓合金的合理擠壓工藝。本發(fā)明一種優(yōu)化合金擠壓工藝的方法,所述本構(gòu)方程建立了應(yīng)變、應(yīng)力、溫度和材料參數(shù)的相互關(guān)系,可以合理預(yù)測(cè)不同實(shí)驗(yàn)條件下材料應(yīng)力-應(yīng)變的相互關(guān)系;所述本構(gòu)方程可以是雙曲正弦型arrhenius方程,所述雙曲正弦型arrhenius方程的表達(dá)式為:式(1)中,為應(yīng)變速率,其單位為s-1;q為變形激活能,其單位為j/mol,σp為流變應(yīng)力,其單位為mpa;n為應(yīng)力指數(shù);t為擠壓坯體的平均溫度,其單位為k;r為摩爾氣體常數(shù),取值為8.314j/mol·k;a和α為與材料有關(guān)的常數(shù);本發(fā)明一種優(yōu)化合金擠壓工藝的方法,所述固體力學(xué)有限元模擬分析軟件為可以采用材料的本構(gòu)方程以及相應(yīng)的邊界和初始條件對(duì)材料的固體變形行為進(jìn)行模擬分析的軟件。優(yōu)選為deform、ansys等商用或非商用軟件或執(zhí)行程序。本發(fā)明一種優(yōu)化合金擠壓工藝的方法,步驟二中,將步驟一所設(shè)定并求解的本構(gòu)方程導(dǎo)入固體力學(xué)有限元分析軟件的材料數(shù)據(jù)庫(kù)中作為熱擠壓坯料的材料參數(shù),并且用該軟件模擬分析擠壓過(guò)程,并且得到擠壓過(guò)程多個(gè)工藝參數(shù)在不同工藝參數(shù)水平下的擠壓過(guò)程模擬分析結(jié)果,然后通過(guò)統(tǒng)計(jì)分析或統(tǒng)計(jì)分析軟件分析,量化這些擠壓工藝參數(shù)對(duì)擠壓坯料內(nèi)部溫度,擠壓力、等效應(yīng)力的影響。本發(fā)明一種優(yōu)化合金擠壓工藝的方法,步驟二中,通過(guò)實(shí)驗(yàn)設(shè)計(jì)的方法系統(tǒng)地分析五個(gè)或五個(gè)以上的工藝參數(shù)包括但不限于擠壓溫度、擠壓速度、擠壓比、模具溫度、模具錐角,并且通過(guò)統(tǒng)計(jì)分析量化這些工藝參數(shù)對(duì)擠壓坯料內(nèi)部溫度,擠壓力、等效應(yīng)力的影響;所述實(shí)驗(yàn)設(shè)計(jì)的方法優(yōu)選為正交實(shí)驗(yàn)設(shè)計(jì)。優(yōu)選為將步驟一所設(shè)定并求解的本構(gòu)方程導(dǎo)入固體力學(xué)有限元軟件包括商用軟件如deform與ansys和非商用軟件材料數(shù)據(jù)庫(kù)中作為熱擠壓坯料的材料參數(shù),按試驗(yàn)設(shè)計(jì)方法所設(shè)計(jì)的方案進(jìn)行有限元數(shù)值模擬試驗(yàn);所述按試驗(yàn)設(shè)計(jì)方法所設(shè)計(jì)的方案為七個(gè)工藝參數(shù)和每個(gè)參數(shù)三個(gè)水平的一共18組的模擬試驗(yàn)方案;所述七工藝參數(shù)分別為:坯料擠壓的平均溫度t、擠壓速度v、擠壓比r、模具溫度t、模具錐角摩擦因子f和工作帶長(zhǎng)度l;通過(guò)模擬實(shí)驗(yàn),得出七個(gè)工藝參數(shù)對(duì)坯料擠壓時(shí)坯料內(nèi)部最高溫度的影響,并通過(guò)相關(guān)性分析得出七個(gè)工藝參數(shù)對(duì)擠壓時(shí)坯料內(nèi)部最高溫度影響的順序;得出七個(gè)工藝參數(shù)對(duì)擠壓時(shí)坯料所受最大擠壓力的影響、并通過(guò)相關(guān)性分析得出七個(gè)工藝參數(shù)對(duì)擠壓時(shí)坯料所受最大擠壓力影響的順序;得出七個(gè)工藝參數(shù)對(duì)坯料擠壓時(shí)的等效應(yīng)力的影響;并通過(guò)相關(guān)性分析得出七個(gè)工藝參數(shù)對(duì)坯料擠壓時(shí)的等效應(yīng)力影響的順序。本發(fā)明一種優(yōu)化合金擠壓工藝的方法,步驟三,所用擠壓設(shè)備所能提供的最大施工條件中,定義其所能提供的最大擠壓力為p設(shè)備,p設(shè)備是最常規(guī)的限制條件。本發(fā)明一種優(yōu)化合金擠壓工藝的方法,步驟三中根據(jù)操作時(shí),所用擠壓設(shè)備所能提供的 最大壓力p設(shè)備,在統(tǒng)計(jì)分析軟件或參數(shù)優(yōu)化分析軟件包括商用軟件如minitab的響應(yīng)優(yōu)化器中設(shè)定擠壓力的目標(biāo)值為p設(shè)備;根據(jù)所制備材料在擠壓后應(yīng)力允許的最大值rmax,在統(tǒng)計(jì)分析軟件或參數(shù)優(yōu)化分析軟件包括商用軟件如minitab的響應(yīng)優(yōu)化器中設(shè)定最大應(yīng)力的目標(biāo)值為rmax;按照(擠壓坯的最高溫度-擠壓坯的平均溫度)|取值最小的原則,在統(tǒng)計(jì)分析軟件或參數(shù)優(yōu)化分析軟件包括商用軟件如minitab的響應(yīng)優(yōu)化器中設(shè)定溫差目標(biāo)最小化;按照上述設(shè)定進(jìn)行優(yōu)化,得出待擠壓合金的合理擠壓工藝。本發(fā)明一種優(yōu)化合金擠壓工藝的方法,建立待擠壓合金的本構(gòu)方程的同時(shí),通過(guò)在選定的溫度和應(yīng)變速率的限定下進(jìn)行的擠壓實(shí)驗(yàn);得出待擠壓合金的組織演化圖。所得組織演化圖結(jié)合步驟二所得的七個(gè)工藝參數(shù)對(duì)擠壓時(shí)坯料內(nèi)部最高溫度影響的順序、七個(gè)工藝參數(shù)對(duì)擠壓時(shí)坯料所受最大擠壓力影響的順序;七個(gè)工藝參數(shù)對(duì)坯料擠壓時(shí)的等效應(yīng)力影響的順序;可以幫助本領(lǐng)域技術(shù)人員根據(jù)實(shí)際需求在minitab的響應(yīng)優(yōu)化器中設(shè)定擠壓力的目標(biāo)值、設(shè)定最大應(yīng)力的目標(biāo)值;進(jìn)而可以縮短計(jì)算時(shí)間,提高工作效率。本發(fā)明一種優(yōu)化合金擠壓工藝的方法,公式(1)中q、σp、n、a、α通過(guò)公知的解法可以得出。本發(fā)明一種優(yōu)化合金擠壓工藝的方法,步驟一中所述待擠壓合金為鎳基高溫合金。本發(fā)明一種優(yōu)化合金擠壓工藝的方法,當(dāng)所述待擠壓合金優(yōu)選為鎳基高溫合金時(shí),步驟一中,800℃-1200℃、優(yōu)選900℃-1200℃選取至少3個(gè)點(diǎn)值;優(yōu)選為3-10個(gè)值,進(jìn)一步優(yōu)選為3-5個(gè)值。優(yōu)選取值均勻性好的值,所取的任意兩個(gè)點(diǎn)值之間的數(shù)值差大于等于10℃而且小于等于47℃;在應(yīng)變速率為0.0001-100s-1之間選取至少3個(gè)點(diǎn)值;優(yōu)選為4-10個(gè)值,進(jìn)一步優(yōu)選為4-6個(gè)值。優(yōu)選取值均勻性好的值,所取任意兩個(gè)所選的點(diǎn)值,按大值/小值進(jìn)行排列后,所得商大于等于3小于等于100。本發(fā)明一種優(yōu)化合金擠壓工藝的方法,當(dāng)所述待擠壓合金優(yōu)選為鎳基高溫合金時(shí),步驟一中,在1000℃-1200℃選取3-5個(gè)點(diǎn)值;在應(yīng)變速率為0.0001-10s-1之間選取4-10個(gè)值。本發(fā)明一種優(yōu)化合金擠壓工藝的方法,當(dāng)所述待擠壓合金為鎳基高溫合金時(shí),步驟二中;定義坯料擠壓的平均溫度t的三個(gè)水平優(yōu)選在1000-1160℃的范圍內(nèi)。本發(fā)明一種優(yōu)化合金擠壓工藝的方法,當(dāng)所述待擠壓合金為鎳基高溫合金時(shí),步驟二中;擠壓速度v的單位mm/s,定義擠壓速度的三個(gè)水平優(yōu)選在20-220mm/s的范圍內(nèi)。本發(fā)明一種優(yōu)化合金擠壓工藝的方法,當(dāng)所述待擠壓合金為鎳基高溫合金時(shí),步驟二中;定義擠壓比r的三個(gè)水平優(yōu)選在4-12的范圍內(nèi)。本發(fā)明一種優(yōu)化合金擠壓工藝的方法,當(dāng)所述待擠壓合金為鎳基高溫合金時(shí),步驟二中;定義模具溫度t的三個(gè)水平優(yōu)選在300-600℃的范圍內(nèi)。本發(fā)明一種優(yōu)化合金擠壓工藝的方法,當(dāng)所述待擠壓合金為鎳基高溫合金時(shí),步驟二中;定義模具錐角的三個(gè)水平優(yōu)選在20-80°的范圍內(nèi)。本發(fā)明一種優(yōu)化合金擠壓工藝的方法,當(dāng)所述待擠壓合金為鎳基高溫合金時(shí),步驟二中;定義摩擦因子f的三個(gè)水平優(yōu)選在0.05-0.6的范圍內(nèi)。本發(fā)明一種優(yōu)化合金擠壓工藝的方法,當(dāng)所述待擠壓合金為鎳基高溫合金時(shí),步驟二中;所述工作帶的單位mm,定義工作帶長(zhǎng)度l的三個(gè)水平優(yōu)選在2-30mm的范圍內(nèi)。原理和優(yōu)勢(shì)本發(fā)明先通過(guò)有限次實(shí)驗(yàn)收集數(shù)據(jù)后,即可建立本構(gòu)方程,再依據(jù)本構(gòu)方程,依托固體力學(xué)有限元軟件,通過(guò)試驗(yàn)設(shè)計(jì)的方案以及有限元模擬分析得出不同工藝參數(shù)組合下的響應(yīng)結(jié)果,然后將模擬結(jié)果導(dǎo)入到統(tǒng)計(jì)分析軟件中分析,得出各因子對(duì)產(chǎn)品性能的影響大小順序,最后借用參數(shù)優(yōu)化分析軟件的分析優(yōu)化,實(shí)現(xiàn)對(duì)多個(gè)擠壓工藝參數(shù)的優(yōu)化。本發(fā)明通過(guò)物理試驗(yàn)建立材料應(yīng)力-應(yīng)變的本構(gòu)方程,結(jié)合固體力學(xué)有限元軟件進(jìn)行系統(tǒng)的模擬分析,將模擬結(jié)果與統(tǒng)計(jì)分析軟件結(jié)合對(duì)工藝參數(shù)的影響進(jìn)行統(tǒng)計(jì)分析,通過(guò)這些不同試驗(yàn)-模擬-分析的結(jié)合,提出了對(duì)多個(gè)擠壓工藝參數(shù)進(jìn)行優(yōu)化的快速、高效并且低成本的方法。采用本發(fā)明方法,獲得了擠壓比,擠壓速率,擠壓溫度、摩擦因子、工作帶長(zhǎng)度以及模具溫度、模具錐角等擠壓工藝對(duì)擠壓力、擠壓坯料溫度分布及等效應(yīng)力的影響大小,優(yōu)化確定并實(shí)驗(yàn)驗(yàn)證了合理的擠壓工藝參數(shù)。附圖說(shuō)明附圖1為實(shí)施例1步驟一所得不同變形條件下的組織演化圖;附圖2為實(shí)施例1步驟二中坯料、擠壓桿和擠壓筒的三維幾何模型;附圖3為實(shí)施例1步驟二中通過(guò)相關(guān)性分析得出七個(gè)工藝參數(shù)對(duì)擠壓時(shí)坯料內(nèi)部最高溫度影響的主效應(yīng)圖;附圖4為實(shí)施例1步驟二中通過(guò)相關(guān)性分析得出七個(gè)工藝參數(shù)對(duì)擠壓后坯料的等效應(yīng)力的主效應(yīng)圖;附圖5為實(shí)施例1步驟二中通過(guò)相關(guān)性分析得出七個(gè)工藝參數(shù)對(duì)擠壓時(shí)坯料所受最大擠壓力的主效應(yīng)圖;附圖6為實(shí)施例1步驟三中,按照(擠壓坯的最高溫度-擠壓坯的平均溫度)取值最小的 原則,在的響應(yīng)優(yōu)化器中設(shè)定溫差目標(biāo)最小化;參數(shù)設(shè)計(jì)對(duì)話框的截圖;附圖7為實(shí)施例1步驟三中,通過(guò)minitab的優(yōu)化求解后所得求解界面圖;附圖8為按照實(shí)施例1所得最優(yōu)參數(shù)進(jìn)行實(shí)驗(yàn)驗(yàn)證所得樣品的宏觀形貌圖;附圖9為附圖8中的1號(hào)樣品樣品的截面不同位置的金相圖。具體實(shí)施方式在本發(fā)明實(shí)施例1中所采用的擠壓設(shè)備的的最大加壓壓力為1800kn;且擠壓設(shè)備的摩擦因子可調(diào)。目標(biāo)產(chǎn)物的擠壓后應(yīng)力標(biāo)準(zhǔn)為小于均值860mpa;實(shí)施例1以鎳基高溫合金為例,按下述步驟進(jìn)行步驟一建立待擠壓合金(鎳基高溫合金)的本構(gòu)方程在1040-1160℃之間選取5個(gè)值;這五個(gè)值分別為1040℃、1070℃、1100℃、1130℃、1160℃;在應(yīng)變速率為0.0001-100s-1之間選取5個(gè)點(diǎn)值;5個(gè)點(diǎn)值分別為0.001s-1、0.01s-1、0.1s-1、1s-1、10s-1;在選定的溫度和應(yīng)變速率的限定下,進(jìn)行擠壓實(shí)驗(yàn);收集應(yīng)力-應(yīng)變數(shù)據(jù),并根據(jù)所收集的應(yīng)力-應(yīng)變數(shù)據(jù)構(gòu)建雙曲正弦型arrhenius方程;所述雙曲正弦型arrhenius方程的表達(dá)式為:式(1.1)中,為應(yīng)變速率,其單位為s-1;t為擠壓坯體的平均溫度,其單位為k;r為摩爾氣體常數(shù),取值為8.314j/mol·k;同時(shí),通過(guò)實(shí)驗(yàn)獲得了不同變形條件下的組織演化圖(如圖1所示),作為初步選取工藝參數(shù)的依據(jù);步驟二根據(jù)實(shí)際需求,設(shè)定擠壓坯料尺寸,建立坯料、擠壓桿和擠壓筒的三維幾何模型,三維模型中,擠壓桿和擠壓筒的實(shí)際尺寸參數(shù)根據(jù)實(shí)際參數(shù)確定;坯料、擠壓桿和擠壓筒的三維幾何模型如圖2所示;將步驟一所設(shè)定并求解的本構(gòu)方程導(dǎo)入deform-3d材料數(shù)據(jù)庫(kù)中作為熱擠壓坯料的材 料參數(shù),按doe所設(shè)計(jì)的實(shí)驗(yàn)方案進(jìn)行有限元數(shù)值模擬試驗(yàn);所述按doe所設(shè)計(jì)的實(shí)驗(yàn)方案為七因素三水平的一共18組的模擬實(shí)驗(yàn)方案如表2所示;所述七因素分別為:坯料擠壓的平均溫度t、擠壓速度v、擠壓比r、模具溫度t、模具錐角摩擦因子f和工作帶長(zhǎng)度l;鎳基高溫合金熱擠壓關(guān)鍵工藝參數(shù)因子及水平如表1所示表1鎳基高溫合金熱擠壓工藝的關(guān)鍵工藝參數(shù)及水平表2鎳基高溫合金熱擠壓有限元數(shù)值模擬的實(shí)驗(yàn)方案通過(guò)模擬實(shí)驗(yàn):得出七個(gè)因子對(duì)坯料擠壓時(shí)坯料內(nèi)部最高溫度的影響,并通過(guò)相關(guān)性分析得出七個(gè)因子對(duì)擠壓時(shí)坯料內(nèi)部最高溫度影響的主效應(yīng)圖(如圖3所示);通過(guò)圖3可以看出,擠壓溫度和擠壓比與坯料內(nèi)部溫度的成正相關(guān)關(guān)系,而擠壓速度、模具溫度、模具錐角、摩擦因子以及工作帶長(zhǎng)度與坯料內(nèi)部溫度不存在明顯的線性關(guān)系。擠壓后坯料內(nèi)部溫度的大小主要受擠壓溫度、擠壓比、模具錐角和摩擦因子的影響,相關(guān)性分析結(jié)果如下表所示:因子p值擠壓溫度(℃)0.019擠壓速度(mm/s)0.757擠壓比0.332模具溫度(℃)0.772模具錐角(°)0.201摩擦因子0.610工作帶長(zhǎng)度(mm)0.905p值的大小代表相關(guān)性的弱強(qiáng),p值越小,代表相關(guān)性越大,p<<0.05表示強(qiáng)相關(guān),則它們影響擠壓坯料內(nèi)部溫度的主次關(guān)系為:擠壓溫度>模具錐角>擠壓比>摩擦因子,其中擠壓溫度為強(qiáng)相關(guān)因子。擠壓溫度根據(jù)材料的流變行為進(jìn)行確定,選擇適當(dāng)?shù)臄D壓溫度。擠壓比主要決定了坯料的變形程度,擠壓比越大對(duì)擠壓設(shè)備的能量要求也就越大,因此擠壓比不宜過(guò)大。模具錐角決定了材料瞬時(shí)變形量的大小以及與擠壓筒作用的時(shí)間,模具錐角通常選擇適中的大小。摩擦因子決定了坯料與擠壓筒接觸的摩擦的大小,通常應(yīng)盡量減小坯料與擠壓筒之間的摩擦因子。擠壓速度、模具溫度和工作帶長(zhǎng)度對(duì)坯料內(nèi)部溫度影響較小,不同條件 下的坯料內(nèi)部溫度均在均值附近。通過(guò)模擬實(shí)驗(yàn):同時(shí)也得出七個(gè)因子對(duì)擠壓后坯料的等效應(yīng)力的影響,并通過(guò)相關(guān)性分析得出七個(gè)因子對(duì)擠壓后坯料的等效應(yīng)力的主效應(yīng)圖(見(jiàn)圖4)。通過(guò)圖4可以看出,擠壓后坯料的最大等效應(yīng)力與擠壓溫度、擠壓速度、模具溫度和模具錐角成相負(fù)相關(guān),與擠壓比成正相關(guān)關(guān)系。摩擦因子和工作帶長(zhǎng)度與最大等效應(yīng)力不存在明顯的線性關(guān)系,最大等效應(yīng)力在摩擦因子為0.3時(shí)取最小值,在工作帶長(zhǎng)度為10mm時(shí)取最小值。擠壓后坯料的最大等效應(yīng)力值主要受擠壓溫度、擠壓速度、擠壓比、模具溫度和摩擦因子的影響,相關(guān)性分析結(jié)果如下表所示:因子p值擠壓溫度(℃)0.048擠壓速度(mm/s)0.006擠壓比0.374模具溫度(℃)0.026模具錐角(°)0.864摩擦因子0.211工作帶長(zhǎng)度(mm)0.899則它們影響擠壓后坯料最大等效應(yīng)力的主次關(guān)系為:擠壓速度>模具溫度>擠壓溫度>擠壓比>摩擦因子,其中擠壓速度及模具溫度為強(qiáng)相關(guān)因子。因此,在確定工藝參數(shù)的過(guò)程中,應(yīng)該盡量增大擠壓速度(擠壓速率是個(gè)綜合影響因素,一方面擠壓速率快會(huì)使得材料變形過(guò)程的抗力增大,另一方面,擠壓速度慢,會(huì)使得坯錠的溫降增大,從而使得材料變形過(guò)程的抗力增大),提高擠壓溫度和模具溫度,減小擠壓比和摩擦因子。而模具錐角和工作帶長(zhǎng)度對(duì)擠壓后坯料的最大等效應(yīng)力的影響小。通過(guò)模擬實(shí)驗(yàn):同時(shí)也得出七個(gè)因子對(duì)擠壓時(shí)坯料所受最大擠壓力的影響、并通過(guò)相關(guān)性分析得出七個(gè)因子對(duì)擠壓時(shí)坯料所受最大擠壓力的主效應(yīng)圖(見(jiàn)圖5)通過(guò)圖5可以看出,在熱擠壓過(guò)程中的最大擠壓力與擠壓比、模具錐角、摩擦因子和工作帶長(zhǎng)度成正相關(guān)關(guān)系,與擠壓溫度成負(fù)相關(guān)關(guān)系。擠壓速度和模具溫度與最大擠壓力不存在明顯的線性關(guān)系,最大擠壓力在擠壓比為8:1時(shí)取最小值,在模具溫度為450℃時(shí)取最大值??梢钥闯鲈跓釘D壓過(guò)程中的最大擠壓力主要受擠壓溫度、擠壓速度、擠壓比、模具錐角、摩擦因子和工作帶長(zhǎng)度的影響,相關(guān)性分析結(jié)果如下表所示:因子p值擠壓溫度(℃)0.003擠壓速度(mm/s)0.092擠壓比0.005模具溫度(℃)0.577模具錐角(°)0.016摩擦因子0.041工作帶長(zhǎng)度(mm)0.04它們影響最大擠壓力的主次關(guān)系為:擠壓溫度>擠壓比>模具錐角>摩擦因子>工作帶長(zhǎng)度>擠壓速度,表明擠壓溫度、擠壓比、模具錐角為主要影響因素。因此,為了減小在擠壓過(guò)程中擠壓力的大小,在選擇熱擠壓工藝參數(shù)時(shí)應(yīng)該盡量提高擠壓溫度,減小擠壓比、模具錐角、摩擦因子、工作帶長(zhǎng)度等工藝參數(shù),選擇適中的擠壓速度和模具溫度,模具溫度對(duì)最大擠壓力的影響小,故在擠壓工藝的選擇,主要是根據(jù)模具材料的承溫情況及坯料的擠壓溫度而定。步驟三優(yōu)化求解根據(jù)實(shí)際操作時(shí),所用擠壓設(shè)備所能提供的最大壓力p設(shè)備=1800kn,在minitab的響應(yīng)優(yōu)化器中設(shè)定擠壓力的目標(biāo)值為p設(shè)備;根據(jù)所制備材料在應(yīng)用時(shí),對(duì)擠壓后應(yīng)力允許的最大值rmax=860mpa,在minitab的響應(yīng)優(yōu)化器中設(shè)定最大應(yīng)力的目標(biāo)值為rmax;按照|擠壓坯的平均溫度-擠壓坯的最高溫度|取值最小的原則,在minitab的響應(yīng)優(yōu)化器中設(shè)定溫差目標(biāo)最小化;參數(shù)設(shè)計(jì)對(duì)話框見(jiàn)圖6;按照上述設(shè)定進(jìn)行優(yōu)化,通過(guò)響應(yīng)優(yōu)化器求解,根據(jù)以上分析進(jìn)行優(yōu)化求解,得出滿足以上設(shè)定的要求的最優(yōu)解。其求解優(yōu)化圖如圖7所示。所得合理優(yōu)化工藝為:擠壓溫度:1120.3℃;擠壓速度197.53mm/s;擠壓比:8.3:1;擠壓模具錐角44°及工作帶長(zhǎng)度設(shè)計(jì)為8.0mm;擠壓模具的預(yù)熱溫度505℃,摩擦方式采用雙重摩擦、控制摩擦因子為0.1469,其一是坯料采用玻璃粉潤(rùn)滑,擠壓筒采用特制的潤(rùn)滑劑,以盡量減小摩擦力擠壓過(guò)程的摩擦力。其擠壓的外觀如圖8所示,可以看出,擠壓外觀完整度較好,表明所制定擠壓工藝參數(shù)能順利安全地將坯料擠出。對(duì)擠壓后的材料進(jìn)行顯微組織分析,如圖9所示。abc為橫截面上不同位置的顯微組織。其中圖9a表示試棒邊緣的顯微組織圖(金相圖)、圖9b表示試棒1/2半徑處的顯微組織 圖(金相圖)、圖9c表示試棒中心處的顯微組織圖(金相圖)從圖中可以看出,材料經(jīng)過(guò)擠壓后,其組織均勻細(xì)小,且不同位置下的組織差別不大,表明設(shè)定的擠壓參數(shù)不僅能將其順利擠出,且表面質(zhì)量良好,無(wú)脫皮、開裂現(xiàn)象,內(nèi)部組織均勻細(xì)小。當(dāng)前第1頁(yè)12