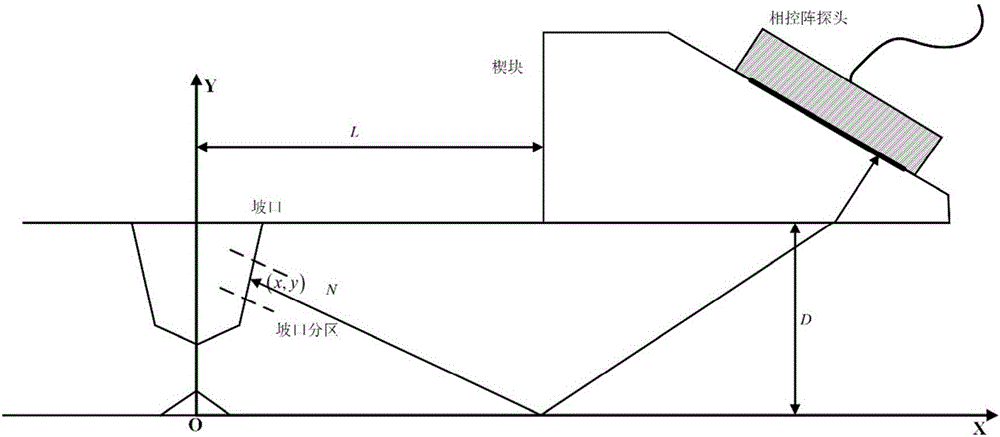
本發(fā)明屬于工業(yè)超聲無(wú)損檢測(cè)
技術(shù)領(lǐng)域:
,涉及一種基于支持向量機(jī)的環(huán)焊縫超聲相控陣自動(dòng)聚焦方法。
背景技術(shù):
:焊接連接是管道工程中最重要而且應(yīng)用最廣泛的連接方式,尤其是環(huán)形焊接的方式。在國(guó)內(nèi)外各種大型管道工程項(xiàng)目中,管道敷設(shè)工作絕大部分依靠環(huán)形焊接工藝來(lái)完成。但是,在采用焊接實(shí)現(xiàn)連接和鋪設(shè)的管道中,焊接過(guò)程中不可避免會(huì)產(chǎn)生各種缺陷,管線在服役或超期服役過(guò)程中運(yùn)行在高溫、高壓和腐蝕的環(huán)境下以及承受疲勞和沖擊等惡劣工況條件下,將極大地加速焊縫缺陷的發(fā)展,引發(fā)管線使用性能的惡化失效,導(dǎo)致事故的發(fā)生。因此,環(huán)焊縫作為管道線路中最薄弱的環(huán)節(jié),是決定管線建成后能否安全、可靠運(yùn)行的關(guān)鍵因素。管道的環(huán)焊縫焊接缺陷通常會(huì)根據(jù)焊縫坡口形式及焊接填充次數(shù)來(lái)實(shí)施分區(qū)檢測(cè)。超聲相控陣檢測(cè)技術(shù)作為一種先進(jìn)的超聲無(wú)損檢測(cè)技術(shù),可以通過(guò)控制各陣元發(fā)射/接收信號(hào)的時(shí)間延遲,達(dá)到波束的聚焦、偏轉(zhuǎn)等多種情況,在環(huán)焊縫焊接缺陷的檢測(cè)上具有無(wú)可比擬的優(yōu)勢(shì)。而由于實(shí)際檢測(cè)中,不同坡口角度、缺陷所在的分區(qū)以及楔塊的裝備位置都需要選擇最合適的聚焦方式,才能精確高效的檢測(cè)出環(huán)焊縫焊接缺陷,現(xiàn)有技術(shù)中缺少針對(duì)不同坡口角度、缺陷所在的分區(qū)以及楔塊的裝備位置進(jìn)行合適聚焦并能精確高效的檢測(cè)環(huán)焊縫焊接缺陷的方式。技術(shù)實(shí)現(xiàn)要素:鑒于超聲波相控陣檢測(cè)過(guò)程中不同裝配情況下對(duì)各坡口各分區(qū)的聲束路徑規(guī)劃比較繁瑣以及現(xiàn)有技術(shù)中的檢測(cè)精度等其他方面的不足,本發(fā)明提供了一種基于支持向量機(jī)的環(huán)焊縫超聲相控陣自動(dòng)聚焦方法。本發(fā)明可以針對(duì)不同的楔塊安裝位置、環(huán)焊縫坡口分區(qū)及鋼管厚度自動(dòng)預(yù)測(cè)出聲束路徑,實(shí)現(xiàn)智能化的環(huán)焊縫缺陷檢測(cè),有效提升檢測(cè)精度和效率。如圖1所示,本發(fā)明的技術(shù)問(wèn)題通過(guò)以下的技術(shù)方案予以解決:步驟一:楔塊裝配在管道上,楔塊的楔面上設(shè)置相控陣探頭,確定楔塊的裝配位置和管道厚度,將管道的環(huán)焊縫坡口進(jìn)行分區(qū),以內(nèi)管壁方向?yàn)閄軸、以環(huán)焊縫中心線方向?yàn)閅軸,建立直角坐標(biāo)系;步驟二:建立楔塊的裝配位置、管道厚度和檢測(cè)的環(huán)焊縫坡口分區(qū)與對(duì)應(yīng)分區(qū)的聲束路徑規(guī)劃之間的預(yù)測(cè)模型:具體是將最小二乘支持向量回歸機(jī)(LSSVR)作為支持向量機(jī)的回歸模型,高斯徑向基核函數(shù)作為L(zhǎng)SSVR的核函數(shù),將楔塊的裝配位置、管道厚度及檢測(cè)的環(huán)焊縫坡口分區(qū)進(jìn)行規(guī)范化處理后作為輸入量,對(duì)應(yīng)分區(qū)的聲束路徑規(guī)劃進(jìn)行規(guī)范化處理后作為輸出量,以規(guī)范化處理后的輸入量和輸出量作為樣本數(shù)據(jù)進(jìn)行訓(xùn)練,得到LSSVR初始函數(shù);楔塊的裝配位置指的是楔塊與環(huán)焊縫中心線的距離L,管道厚度指的是管道鋼管厚度D,檢測(cè)的環(huán)焊縫坡口分區(qū)指的是坡口分區(qū)號(hào)N,坡口分區(qū)的數(shù)量和相控探頭聚焦的陣元數(shù)量相同。將通過(guò)實(shí)驗(yàn)采集獲得的楔塊與環(huán)焊縫中心線的距離L、鋼管厚度D,坡口分區(qū)號(hào)N作為輸入量,將對(duì)應(yīng)坡口分區(qū)的聲束路徑規(guī)劃作為輸出量,輸入到支持向量機(jī)中訓(xùn)練獲得LSSVR初始函數(shù)。步驟三:以k重交叉驗(yàn)證法所計(jì)算出的泛化誤差作為目標(biāo)函數(shù),采用耦合模擬退火算法與網(wǎng)格搜索法相結(jié)合的優(yōu)化方法,對(duì)LSSVR初始函數(shù)進(jìn)行優(yōu)化得到最優(yōu)超參數(shù),由最優(yōu)超參數(shù)獲得LSSVR優(yōu)化模型;步驟四:將楔塊的裝配位置、鋼管厚度和需要檢測(cè)的環(huán)焊縫坡口分區(qū)進(jìn)行規(guī)范化處理后作為輸入量,通過(guò)LSSVR優(yōu)化模型預(yù)測(cè)獲得相應(yīng)的輸出量,對(duì)輸出量進(jìn)行逆規(guī)范化處理,得到對(duì)應(yīng)分區(qū)最優(yōu)的聲束路徑規(guī)劃;步驟五:根據(jù)費(fèi)馬定理由聲束路徑規(guī)劃根據(jù)管道幾何關(guān)系計(jì)算得到相控陣探頭上對(duì)應(yīng)發(fā)射/接收陣元的絕對(duì)延時(shí)量,再計(jì)算對(duì)應(yīng)發(fā)射/接收陣元的延時(shí)量,根據(jù)延時(shí)量控制相控陣探頭發(fā)射與延時(shí)量對(duì)應(yīng)的超聲信號(hào)對(duì)環(huán)焊縫缺陷進(jìn)行聚焦檢測(cè)。所述步驟一中,環(huán)焊縫坡口進(jìn)行分區(qū)具體是在焊縫掃查區(qū)域沿坡口高度方向上劃為若干層,每層的厚度為2~3mm。所述步驟二中,最小二乘支持向量回歸(LeastSquareSVR,LSSVR)采用等式約束條件,以誤差變量εk描述各項(xiàng)訓(xùn)練誤差,以平方損失函數(shù)作為函數(shù)回歸的訓(xùn)練誤差,其預(yù)測(cè)模型表示為:其中,w為高維空間的權(quán)向量,w∈Rm,Rm表示m維的高維空間,m表示維數(shù),C為懲罰因子,C>0,εk為誤差變量,表示為把輸入量xk投影到高維空間Rm上的映射函數(shù),B為L(zhǎng)SSVR初始函數(shù)的偏置項(xiàng),yk表示預(yù)測(cè)模型的目標(biāo)函數(shù),T表示轉(zhuǎn)置,k為輸入量的序數(shù),N為輸入量的總數(shù);將預(yù)測(cè)模型求解得到LSSVR初始函數(shù):其中,αk為L(zhǎng)agrange乘子向量,K(xk,xl)為核函數(shù),k,l=1,..,N,B為L(zhǎng)SSVR初始函數(shù)的偏置項(xiàng)。核函數(shù)的選擇和使用對(duì)決策函數(shù)的優(yōu)化起到?jīng)Q定性的作用,】核函數(shù)K(xk,xl)選擇高斯徑向基核函數(shù),表示為:其中,σ為核寬,xk,xl分別為兩個(gè)不同的輸入量,k,l=1,..,N。由于高斯徑向基核函數(shù)只有核寬一個(gè)核參數(shù),核參數(shù)優(yōu)化過(guò)程效率高。同時(shí),高斯徑向基核函數(shù)還具有插值能力強(qiáng)、善于提取樣本的局部性質(zhì)的能力,只要核寬σ取值合理,訓(xùn)練樣本在高維空間中幾乎總能夠被線性近似。所述步驟三具體為:k重交叉驗(yàn)證法對(duì)泛化誤差的估值非常有效,用所計(jì)算出的泛化誤差作為其目標(biāo)函數(shù),采用耦合模擬退火算法與網(wǎng)格搜索算法相結(jié)合的優(yōu)化方法,確保求解過(guò)程的全局收斂性與計(jì)算速度最優(yōu)性。簡(jiǎn)要步驟如下所示:(1)隨機(jī)生成q組超參數(shù)[Cs,σs],s=1,2,…,q;(2)以這q組超參數(shù)為初始值,將針對(duì)已知樣本數(shù)據(jù)用k重交叉驗(yàn)證法所計(jì)算出的泛化誤差作為優(yōu)化目標(biāo)函數(shù),通過(guò)耦合模擬退火算法求出最優(yōu)的一組超參數(shù)[Cm,σm],使得泛化誤差達(dá)到極小值或滿足收斂條件;(3)以超參數(shù)[Cm,σm]為網(wǎng)格中心,將針對(duì)已知樣本數(shù)據(jù)用k重交叉驗(yàn)證法所計(jì)算出的泛化誤差作為優(yōu)化目標(biāo)函數(shù),通過(guò)網(wǎng)格搜索算法進(jìn)一步優(yōu)化求解出最優(yōu)的超參數(shù)[Cε,σε],作為最終超參數(shù)。如圖3所示,為L(zhǎng)SSVR的決策變量?jī)?yōu)化流程圖,根據(jù)該流程計(jì)算得到LSSVR的優(yōu)化模型,用于對(duì)環(huán)焊縫各分區(qū)檢測(cè)的超聲相控陣聚焦方式預(yù)測(cè)。所述步驟三中的LSSVR優(yōu)化模型為:其中,αk為L(zhǎng)agrange乘子向量,K(xk,xl)為核函數(shù),k,l=1,..,N,B為L(zhǎng)SSVR初始函數(shù)的偏置項(xiàng)。本優(yōu)化模型具有泛化能力,針對(duì)不同的楔塊的裝配位置、管道厚度及檢測(cè)的環(huán)焊縫坡口分區(qū),可以快速精確的預(yù)測(cè)出待檢分區(qū)的聲束路徑規(guī)劃。LSSVR優(yōu)化模型中,決策變量為L(zhǎng)agrange乘子向量αk與偏移項(xiàng)B,而懲罰因子C及核參數(shù)σ對(duì)支持向量回歸擬合效果及泛化性能起到了決定性作用,這兩個(gè)參數(shù)也被稱為超參數(shù)。因此LSSVR優(yōu)化問(wèn)題實(shí)際上是在最優(yōu)超參數(shù)下的決策變量?jī)?yōu)化求解。本發(fā)明通過(guò)k重交叉驗(yàn)證法所計(jì)算出的泛化誤差作為其目標(biāo)函數(shù),采用模擬退火算法與網(wǎng)格搜索算法相結(jié)合的優(yōu)化方法,確保求解過(guò)程的全局收斂性與計(jì)算速度最優(yōu)性。如圖3所示,為L(zhǎng)SSVR的決策變量?jī)?yōu)化流程圖,根據(jù)該流程計(jì)算得到LSSVR的優(yōu)化模型,用于對(duì)環(huán)焊縫各分區(qū)檢測(cè)的超聲相控陣聚焦方式預(yù)測(cè)。由于樣本的輸入、輸出量為不同種類的物理量,而且數(shù)據(jù)間的量級(jí)也存在差異,因此在建立LSSVR初始函數(shù)前,需要對(duì)樣本數(shù)據(jù)進(jìn)行相應(yīng)的規(guī)范化處理。所述步驟二和步驟四中,針對(duì)楔塊的裝配位置、鋼管厚度和檢測(cè)的環(huán)焊縫坡口分區(qū)的三方面數(shù)據(jù),均采用以下方式進(jìn)行規(guī)范化處理:將采集數(shù)據(jù)分為非訓(xùn)練樣本數(shù)據(jù)和訓(xùn)練樣本數(shù)據(jù)兩部分,再采用以下公式計(jì)算:其中,z為非訓(xùn)練樣本數(shù)據(jù),為規(guī)范化前的訓(xùn)練樣本數(shù)據(jù),mean(*)與std(*)分別表示求均值和標(biāo)準(zhǔn)差,是規(guī)范化后的訓(xùn)練樣本數(shù)據(jù)。所述步驟四中輸出量按如下公式進(jìn)行逆規(guī)范化處理,獲得對(duì)應(yīng)分區(qū)最優(yōu)的聲束路徑規(guī)劃:其中,z為非訓(xùn)練樣本數(shù)據(jù),為規(guī)范化前的訓(xùn)練樣本數(shù)據(jù),mean(*)與std(*)分別表示求均值和標(biāo)準(zhǔn)差,是規(guī)范化后的訓(xùn)練樣本數(shù)據(jù)。由對(duì)應(yīng)分區(qū)最優(yōu)的聲束路徑規(guī)劃根據(jù)圖2的裝配及聲學(xué)特性,利用幾何關(guān)系可以計(jì)算得到聚焦發(fā)射的陣元序列和聲束偏轉(zhuǎn)角度。針對(duì)不同的坡口分區(qū),聲束的路徑規(guī)劃根據(jù)探測(cè)傾斜角度劃分主要有直接法、反射法和串接法。為了方便預(yù)測(cè),實(shí)施例用編號(hào)M來(lái)對(duì)聲束的路徑規(guī)劃進(jìn)行編號(hào),M=1為直接法,M=2為一次反射法,M=3為二次反射法,M=4為三次反射法,M=5為串接法。所述步驟五中用步驟四得到的聚焦發(fā)射的陣元序列以及聲束偏轉(zhuǎn)角度,根據(jù)費(fèi)馬定理計(jì)算得到每個(gè)陣元到坡口分區(qū)中心點(diǎn)的延時(shí)量,用所有陣元中最大延時(shí)量作為絕對(duì)延時(shí)基準(zhǔn)量,減去各陣元延時(shí)所得的結(jié)果作為延時(shí)偏移量,即采用以下公式計(jì)算:式中,為延時(shí)偏移量,為絕對(duì)延時(shí)量,為絕對(duì)延時(shí)基準(zhǔn)量,i表示陣元的序數(shù)。本發(fā)明通過(guò)支持向量機(jī)的應(yīng)用,通過(guò)機(jī)器學(xué)習(xí)的方式,方便通過(guò)已有的檢測(cè)數(shù)據(jù),實(shí)現(xiàn)對(duì)不同位置的環(huán)焊縫缺陷實(shí)現(xiàn)最優(yōu)的相控陣陣列時(shí)間延遲,讓檢測(cè)自動(dòng)選擇最優(yōu)的聚焦方式,提升信噪比,實(shí)現(xiàn)對(duì)環(huán)焊縫缺陷的精確檢測(cè)。本發(fā)明的有益效果主要表現(xiàn)在:(1)利用LSSVR建立楔塊與環(huán)焊縫坡口中心距離、環(huán)焊縫坡口檢測(cè)分區(qū)及鋼管厚度與各分區(qū)最優(yōu)聲束路徑的預(yù)測(cè)模型,可以針對(duì)不同的裝配情況,鋼管厚度及各坡口分區(qū)實(shí)現(xiàn)智能的環(huán)焊縫缺陷檢測(cè)。(2)利用耦合模擬退火算法及網(wǎng)格搜索法相結(jié)合的優(yōu)化方法,可以快速高效的得到LSSVR優(yōu)化模型,提升模型的泛化能力及精確度,智能化的適應(yīng)各種不同的工況。(3)通過(guò)對(duì)不同規(guī)格及類型的環(huán)焊縫各分區(qū)最優(yōu)聲束路徑學(xué)習(xí)計(jì)算,實(shí)現(xiàn)環(huán)焊縫坡口各分區(qū)的智能最優(yōu)聲束路徑規(guī)劃,完成動(dòng)態(tài)的聚焦檢測(cè),不需要像傳統(tǒng)方法,稍有變化就需要重新計(jì)算,減少許多重復(fù)低效計(jì)算,提升全自動(dòng)環(huán)焊縫檢測(cè)的效率。(4)基于支持向量基的特點(diǎn),會(huì)隨著檢測(cè)樣本的增加繼續(xù)提高模型精度,從而提高檢測(cè)精度。附圖說(shuō)明圖1是本發(fā)明方法流程圖。圖2是實(shí)施例的楔塊幾何參數(shù)和探頭裝配位置的示意圖。圖3是對(duì)LSSVR初始函數(shù)優(yōu)化獲得LSSVR優(yōu)化模型流程圖。圖4是實(shí)施例時(shí)坡口各分區(qū)用LSSVR預(yù)測(cè)的聲束路徑規(guī)劃結(jié)果誤差示意圖。具體實(shí)施方式以下結(jié)合附圖對(duì)本發(fā)明作進(jìn)一步說(shuō)明。本發(fā)明的實(shí)施例如下:如圖1所示,本發(fā)明利用利用支持向量機(jī)實(shí)現(xiàn)超聲相控陣智能動(dòng)態(tài)聚焦的操作流程可以分為以下幾個(gè)步驟:步驟一,楔塊裝配在管道上,楔塊的楔面上設(shè)置相控陣探頭。各參數(shù)如圖2所示,根據(jù)儀器檢測(cè)獲得確定楔塊與環(huán)焊縫中心線的距離為L(zhǎng),鋼管厚度為D。并根據(jù)坡口形式及壁厚,焊縫掃查區(qū)域在坡口高度方向上劃為若干層,每個(gè)分層的高度一般為2~3mm,坡口分區(qū)從下至上依次編號(hào)N(N=1,2,3,…),選取內(nèi)管軸向?yàn)閄軸,環(huán)焊縫中心線為Y軸,建立直角坐標(biāo)系。這里選用D=5.6mm,D=8mm,D=11mm三種厚度規(guī)格的管道,按照分區(qū)標(biāo)準(zhǔn),分成3層、4層和5層,移動(dòng)楔塊的裝配位置,使楔塊與環(huán)焊縫中心線的距離為L(zhǎng)=26mm,L=28mm,L=30mm,L=32mm,L=34mm,L=36mm,分別實(shí)驗(yàn)獲得各分區(qū)的最優(yōu)聲束路徑規(guī)劃,將共計(jì)67個(gè)結(jié)果作為訓(xùn)練樣本。步驟二:建立楔塊的裝配位置、管道厚度和檢測(cè)的環(huán)焊縫坡口分區(qū)與對(duì)應(yīng)分區(qū)的聲束路徑規(guī)劃之間的預(yù)測(cè)模型:具體是將最小二乘支持向量回歸機(jī)(LSSVR)作為支持向量機(jī)的回歸模型,高斯徑向基核函數(shù)作為L(zhǎng)SSVR的核函數(shù),將楔塊與環(huán)焊縫中心線的距離L、鋼管厚度D和檢測(cè)的環(huán)焊縫坡口分區(qū)號(hào)N進(jìn)行規(guī)范化處理后作為輸入量,對(duì)應(yīng)分區(qū)的聲束路徑規(guī)劃根據(jù)探測(cè)傾斜角度劃分的類型編號(hào)進(jìn)行規(guī)范化處理后作為輸出量,以規(guī)范化處理后的輸入量和輸出量作為樣本數(shù)據(jù)進(jìn)行訓(xùn)練,得到LSSVR初始函數(shù)。為了方便預(yù)測(cè),實(shí)施例用編號(hào)M來(lái)對(duì)聲束的路徑規(guī)劃進(jìn)行編號(hào),M=1為直接法,M=2為一次反射法,M=3為二次反射法,M=4為三次反射法,M=5為串接法。具體實(shí)施是最小二乘支持向量回歸(LeastSquareSVR,LSSVR)采用等式約束條件,以誤差變量εk描述各項(xiàng)訓(xùn)練誤差,以平方損失函數(shù)作為函數(shù)回歸的訓(xùn)練誤差,其預(yù)測(cè)模型表示為:將預(yù)測(cè)模型求解得到LSSVR初始函數(shù):步驟三:以k重交叉驗(yàn)證法所計(jì)算出的泛化誤差作為目標(biāo)函數(shù),采用模擬退火算法與網(wǎng)格搜索法相結(jié)合的優(yōu)化方法,對(duì)LSSVR初始函數(shù)進(jìn)行優(yōu)化得到最優(yōu)超參數(shù),由最優(yōu)超參數(shù)獲得LSSVR優(yōu)化模型,具體是如圖3所示:(1)隨機(jī)生成q組超參數(shù)[Cs,σs],s=1,2,…,q;(2)以這q組超參數(shù)為初始值,將泛化誤差作為優(yōu)化目標(biāo)函數(shù),通過(guò)耦合模擬退火算法求出一組較優(yōu)超參數(shù)[Cm,σm],使得泛化誤差達(dá)到極小值或滿足收斂條件;(3)以[Cm,σm]為網(wǎng)格中心,仍將泛化誤差作為優(yōu)化目標(biāo)函數(shù),通過(guò)網(wǎng)格搜索算法進(jìn)一步優(yōu)化求解出最優(yōu)超參數(shù)[Cε,σε]。步驟三得到的LSSVR優(yōu)化模型為:用步驟一得到的實(shí)驗(yàn)樣本訓(xùn)練完成后,超參數(shù)分別為:C=1.5184×1012,σ=239.6029。由該組超參數(shù)求得的Lagrange乘子向量αi如下表所示,偏置向B=575.9694。表1Lagrange乘子向量數(shù)值iαiiαiiαiiαi17.91×107188.04×10735-3.94×10752-1.41×1082-1.65×10819-4.50×108367.13×10753-2.89×10838.19×107201.24×10937-1.47×107545.90×1084-8.92×10621-1.11×10938-9.17×10655-2.00×10854.21×107223.26×10839-3.26×10856-3.22×1086-1.54×107231.08×108408.76×108571.98×1087-6.23×10724-4.15×10841-7.72×10858-3.80×10889.73×107254.18×108422.22×108597.29×1089-6.12×10726-1.43×108431.72×10860-2.11×10710-4.88×107273.57×10844-4.25×10861-5.61×108111.03×10828-8.29×108452.65×108622.48×10812-3.77×107297.19×108464.35×107634.43×10813-8.35×10630-1.99×10847-5.91×10764-9.16×108142.60×107312.17×108481.44×108652.38×10815-2.17×10732-5.84×10849-2.17×108664.90×108167.54×107334.45×10850-8.65×10767-2.58×10817-1.56×10834-1.09×108513.15×108步驟四:將楔塊的裝配位置、鋼管厚度和需要檢測(cè)的環(huán)焊縫坡口分區(qū)進(jìn)行規(guī)范化處理后作為輸入量,通過(guò)LSSVR優(yōu)化模型預(yù)測(cè)獲得相應(yīng)的輸出量,對(duì)輸出量進(jìn)行逆規(guī)范化處理,得到對(duì)應(yīng)分區(qū)最優(yōu)的聲束路徑規(guī)劃。具體實(shí)施是:將D=11mm,L=36mm,N=1,2,3,4,5,規(guī)范后作為輸入量,通過(guò)步驟三得到的LSSVR優(yōu)化模型進(jìn)行預(yù)測(cè),預(yù)測(cè)得到的各分區(qū)聲路路徑分別為M=1,2,2,2,3,即從下往上的聲束路徑規(guī)劃方式分別為:直接法、一次反射法、一次反射法、一次反射法、二次反射法。將結(jié)果與實(shí)驗(yàn)數(shù)據(jù)比對(duì),可以發(fā)現(xiàn)這種情況下用LSSVR優(yōu)化模型預(yù)測(cè)得到的結(jié)果完全吻合實(shí)驗(yàn)數(shù)據(jù)。步驟五:用步驟四得到對(duì)應(yīng)分區(qū)最優(yōu)的聲束路徑規(guī)劃,根據(jù)圖2的裝配及聲學(xué)特性,利用幾何關(guān)系可以計(jì)算得到聚焦發(fā)射的陣元序列以及聲束偏轉(zhuǎn)角度,根據(jù)費(fèi)馬定理計(jì)算得到每個(gè)陣元到坡口分區(qū)中心點(diǎn)的延時(shí)量,用所有陣元中最大延時(shí)量作為絕對(duì)延時(shí)基準(zhǔn)量,減去各陣元延時(shí)所得的結(jié)果,從而獲得延時(shí)偏移量,即采用以下公式計(jì)算:式中,為延時(shí)偏移量,為絕對(duì)延時(shí)量,為絕對(duì)延時(shí)基準(zhǔn)量,i表示陣元的序數(shù)。以D=11mm,L=36mm,N=1為例,相控陣探頭的激勵(lì)陣元為16個(gè),計(jì)算得到的各陣元延時(shí)量為:單位為微秒。根據(jù)上面計(jì)算的延時(shí)時(shí)間就能通過(guò)相控陣探頭合成聲束,實(shí)現(xiàn)對(duì)環(huán)焊縫缺陷的自動(dòng)檢測(cè)。當(dāng)前第1頁(yè)1 2 3