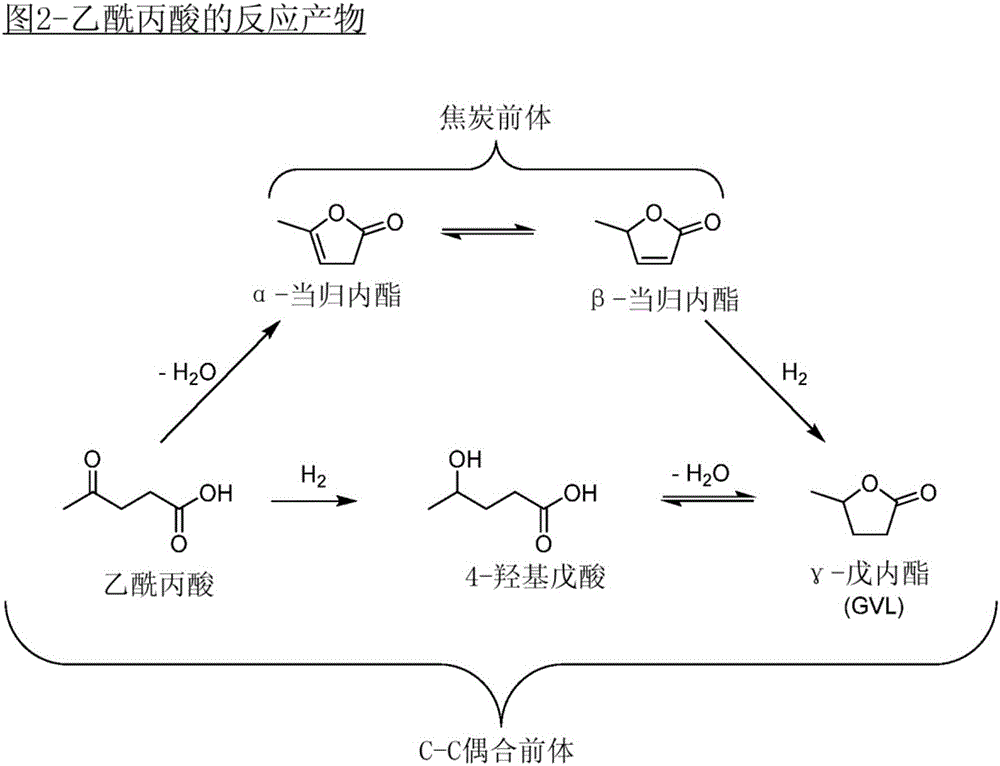
本發(fā)明涉及酮酸的催化轉(zhuǎn)化,包括用于增加酮酸分子量的方法、通過這樣的方法可得到的產(chǎn)物和這樣的產(chǎn)物用于生產(chǎn)液體烴和/或汽油或柴油機(jī)燃料或基礎(chǔ)油組分的用途。
背景技術(shù):
:由生物質(zhì)生產(chǎn)用作燃料或基礎(chǔ)油組分和化學(xué)品的烴受到越來越多的關(guān)注,因?yàn)樗鼈兪怯煽沙掷m(xù)的有機(jī)化合物源生產(chǎn)的。酮酸乙酰丙酸(LA,4-氧代戊酸)是許多可源自生物質(zhì)的平臺分子(platformmolecules)中的一種。其可由木質(zhì)纖維素材料的戊糖和己糖二者以相對低的成本生產(chǎn)(參見圖1)。使用乙酰丙酸作為平臺分子的一些優(yōu)點(diǎn)和缺點(diǎn)涉及由于它的酮基和酸官能團(tuán)二者其被認(rèn)為是活性分子的事實(shí)。乙酰丙酸的酯已被建議作為燃料組分以及柴油機(jī)燃料中的冷流添加劑,且特別地甲基和乙基酯已被用作柴油機(jī)燃料中的添加劑。γ-戊內(nèi)酯(GVL),其可通過乙酰丙酸的還原得到,已被用作汽油中的燃料添加劑。GVL進(jìn)一步還原為2甲基四氫呋喃(MTHF)提供了可與高達(dá)60%汽油混合的產(chǎn)品。由乙酰丙酸生產(chǎn)的戊酸烷基酯也已被建議作為生物燃料。通過多個催化路線,包括產(chǎn)生烯烴分布的方法,所述分布以C12為中心,涉及在第一反應(yīng)器系統(tǒng)中將水性GVL轉(zhuǎn)化為丁烯然后在第二反應(yīng)器中經(jīng)過酸性催化劑(例如70)進(jìn)行低聚反應(yīng),乙酰丙酸也已被用于液體烴燃料的生產(chǎn)SerranoRuiz等人(Appl.Catal.,B,2010,100,184)通過在一個反應(yīng)器中經(jīng)過Ru/C催化劑將乙酰丙酸還原為GVL,然后在另一個反應(yīng)器中在325-425℃,14bar,WHSV=0.8-0.5h-1下在Pd/Nb2O5+二氧化鈰-氧化鋯雙床配置中在水和0.02MH2SO4中使40重量%GVL反應(yīng)制備了C9-酮(5-壬酮)。使用多個反應(yīng)器可能是有利的,因?yàn)槠湎啾容^于使用單個反應(yīng)器可提供對工藝的更多控制。然而,多個反應(yīng)器增加了過程步驟的數(shù)目,這增加了過程的資本支出。US2006/0135793A1(屬于Blessing和Petrus)公開了乙酰丙酸在氫的存在下使用包含氫化金屬的強(qiáng)酸多相催化劑例如離子交換樹脂催化劑在60-170℃的溫度范圍內(nèi)和1-200bar壓力下(絕對壓力)二聚為C10單元。該實(shí)例表明作為主要產(chǎn)物的乙酰丙酸二聚物(26%)和未反應(yīng)的乙酰丙酸(70%)。由于離子交換樹脂在大于150℃的溫度下的熱不穩(wěn)定性,相對低的反應(yīng)溫度是優(yōu)選的。技術(shù)實(shí)現(xiàn)要素:相比較于多個反應(yīng)器,使用單個反應(yīng)器可能有利的方面在于它們降低了反應(yīng)步驟的數(shù)目并因此增加過程經(jīng)濟(jì)性。與升級的直接路線例如使用單個反應(yīng)器相關(guān)的一些缺點(diǎn)為這些反應(yīng)產(chǎn)生具有多于一個官能團(tuán)的高度活性的中間體,其可進(jìn)一步與其他不需要的分子反應(yīng)。通過升級的直接路線降低不需要的分子通常引起所需產(chǎn)物組合物的更低收率。通常通過使用稀釋的乙酰丙酸水溶液作為原料來實(shí)現(xiàn)抑制產(chǎn)生不需要的分子的副反應(yīng)。因此,相比較于升級的直接路線,使用多個反應(yīng)器或在單個反應(yīng)器中的多個催化劑床的升級進(jìn)料的間接路線在一些情況下可以是優(yōu)選的。因此,存在對用于將乙酰丙酸和其他酮酸升級為較高分子量化合物的額外工藝的需要,所述較高分子量化合物適合用作例如燃料或基礎(chǔ)油組分或化學(xué)品或作為在燃料或基礎(chǔ)油組分或化學(xué)品的生產(chǎn)中的組分。特別地,存在對通過特別是(i.a.)提高所需組分或化學(xué)品的收率來降低過程成本和/或通過提高催化劑的壽命來降低整個催化劑的消耗這樣的額外工藝的需要。本發(fā)明是考慮到上述現(xiàn)有技術(shù)做出的,且本發(fā)明的一個目的是提供能夠?qū)⑼崂缫阴1嵘墳檩^高分子量化合物的方法。本發(fā)明的另一個目的是以良好收率和低的過程成本提供酮酸至較高分子量化合物的升級。為了解決該問題,本發(fā)明提供一種用于增加酮酸的分子量的方法,該方法包括在反應(yīng)器中提供包含至少一種酮酸的原料;和使原料經(jīng)受一個或多個的C-C偶合反應(yīng)的步驟,其中該C-C偶合反應(yīng)在包含第一金屬氧化物和第二金屬氧化物的固體酸催化劑體系的存在下進(jìn)行且其中在原料中所述至少一種酮酸的含量為至少30重量%。在使原料經(jīng)受一個或多個C-C偶合反應(yīng)的步驟中,所述至少一種酮酸經(jīng)受與在原料中存在的另一種酮酸或酮酸衍生物的至少一次C-C偶合反應(yīng)以增加所述酮酸的分子量。參與C-C-偶合反應(yīng)的酮酸可為具有相同化學(xué)式的相同類型或不同類型。所述酮酸衍生物包括通過C-C-偶合反應(yīng)或其他反應(yīng)直接可從酮酸得到的所有化合物。所述酮酸衍生物可選自由酮酸的內(nèi)酯和內(nèi)酯衍生物,和戊酸組成的組。在C-C偶合反應(yīng)中,所述至少一種酮酸與另一種反應(yīng)物反應(yīng),在產(chǎn)物中形成新的碳-碳鍵。換句話說,使用酮酸作為直接前體(一步反應(yīng))且在單個反應(yīng)器或單個催化劑床內(nèi)增加酮酸的分子量。自然地,可發(fā)生進(jìn)一步的C-C-偶合反應(yīng)以進(jìn)一步增加C-C-偶合反應(yīng)產(chǎn)物的分子量。這些進(jìn)一步的反應(yīng)在相同(單個)反應(yīng)器或催化劑床中進(jìn)行。即,在本發(fā)明的第一方面,本發(fā)明的發(fā)明人發(fā)現(xiàn),包含第一金屬氧化物和第二金屬氧化物的固體酸催化劑可在酮酸的強(qiáng)溶液(至少30重量%)中催化多種類型的酮酸的C-C-偶合反應(yīng),能夠以良好的收率和在反應(yīng)器中生產(chǎn)出酮酸的更高分子量化合物。使用酮酸的強(qiáng)溶液允許兩種酮酸之間的C-C-偶合反應(yīng)的高可能性,因此提供了所需產(chǎn)物的高收率和副產(chǎn)物低的量。所述(強(qiáng))溶液的溶劑可為任何酮酸,優(yōu)選所述“至少一種酮酸”。此外,也可使用水和/或有機(jī)溶劑。優(yōu)選地,所述至少一種酮酸用作溶劑。所述催化劑體系的比表面積優(yōu)選為10-500m2/g。通常通過測量氮的等溫吸附線的BET方法測定比表面積(ASTMD-3663)。優(yōu)選地,所述催化劑體系的酸位點(diǎn)總量為30-500μmol/g??梢允褂肗H3-TPD方法測量酸位點(diǎn)總數(shù),它是一種用于確定酸位點(diǎn)數(shù)的常用方法并且已經(jīng)公開于例如M.Lashdaf等人的MicroporousandMesoporousMaterials75(2004)149-158中。在NH3-TPD方法中,使用200℃的NH3的吸附溫度。在本發(fā)明中,所述至少一種酮酸優(yōu)選為γ-酮酸,最優(yōu)選乙酰丙酸。除了所述至少一種酮酸,也可以使用一種或多種其他酮酸。在本發(fā)明的方法中使用的反應(yīng)器可為流動反應(yīng)器,優(yōu)選連續(xù)流動反應(yīng)器或間歇反應(yīng)器,優(yōu)選在攪拌下。從生產(chǎn)效率的觀點(diǎn)看,流動反應(yīng)器類型是優(yōu)選的。當(dāng)使用流動反應(yīng)器時,催化劑體系優(yōu)選固定在反應(yīng)器中。本發(fā)明提供了用于工業(yè)規(guī)模生產(chǎn)更高分子量酮酸產(chǎn)物的方法,和因此,優(yōu)選使用具有高濃度酮酸的原料進(jìn)行所述C-C偶合反應(yīng)。優(yōu)選所述至少一種酮酸在原料中的含量為至少40重量%,優(yōu)選至少50重量%,更優(yōu)選至少70重量%,甚至更優(yōu)選至少90重量%,和甚至更優(yōu)選至少95重量%。如果原料中存在多種酮酸,“所述至少一種酮酸的含量”指所有酮酸的總含量。在該方面,應(yīng)注意的是,本發(fā)明中的術(shù)語“原料”包括供應(yīng)至反應(yīng)器的所有材料,除了構(gòu)成催化劑體系的材料外。因此,原料中所述至少一種酮酸的含量的計(jì)算不考慮催化劑的量。已發(fā)現(xiàn)水可以減少C-C偶合反應(yīng)期間焦炭前體的形成,但是也已發(fā)現(xiàn)它會降低催化劑體系的活性。原料中水的含量為少于5.0重量%,更優(yōu)選少于2.0重量%,甚至更優(yōu)選少于1.0重量%。原料中水含量的計(jì)算不考慮催化劑的量。有多種金屬氧化物可用在所述催化劑體系中以催化酮酸的C-C-偶合反應(yīng)。優(yōu)選地,所述第一金屬氧化物包含W、Be、B、Mg、Si、Ca、Sc、Ti、V、Cr、Mn、Fe、Co、Ni、Cu、Zn、Ga、Sr、Y、Zr、Nb、Mo、Cd、Sn、Sb、Bi、La、Ce、Th之一的氧化物,且所述第二金屬氧化物包含Zr、Ti、Si、Al、V、Cr之一的氧化物或它們的組合,第一金屬氧化物不同于第二金屬氧化物。金屬氧化物的組合包括單個金屬氧化物(固體溶液),混合的金屬氧化物和負(fù)載的金屬氧化物的混合物。優(yōu)選地,催化劑體系包含第一金屬氧化物和第二金屬氧化物的混合物,其中第二金屬氧化物是選自氧化鋯、二氧化鈦、二氧化硅、氧化釩、氧化鉻的至少一種,優(yōu)選氧化鋯或二氧化鈦。在本發(fā)明中,金屬氧化物的混合物包括如下物質(zhì)的混合物:單個金屬氧化物材料,例如以粉末形式,混合的金屬氧化物,其中所述金屬氧化物形成共同的基質(zhì),和負(fù)載的金屬氧化物,其中更加活性的金屬氧化物沉積在作為載體的金屬氧化物上。多種方法可用于制備金屬氧化物的混合物。在混合的金屬氧化物制備中,金屬氧化物前體在轉(zhuǎn)化成氧化物形式前從氣相或液相溶液匯集。在負(fù)載的金屬氧化物制備中,在金屬氧化物前體轉(zhuǎn)化成氧化物形式前,將金屬氧化物前體以氧化物(或氫氧化物)形式從氣相或液相溶液帶到固體載體上。優(yōu)選地,所述第一金屬氧化物負(fù)載在第二金屬氧化物載體上,其中所述第二金屬氧化物優(yōu)選選自由氧化鋯、二氧化鈦、二氧化硅、氧化釩、氧化鉻組成的組,優(yōu)選氧化鋯或二氧化鈦。優(yōu)選地,負(fù)載在第二金屬氧化物上的第一金屬氧化物的金屬原子的表面密度為0.5-20金屬原子/nm2。以催化劑中金屬氧化物的含量和催化劑體系的比表面積為基礎(chǔ)計(jì)算催化劑體系中第一金屬氧化物的金屬原子的表面密度。優(yōu)選地,所述催化劑體系包含負(fù)載在金屬氧化物載體上的氧化鎢、二氧化鈰或二氧化硅,其中所述載體優(yōu)選選自由氧化鋯、二氧化鈦、二氧化硅、氧化釩、氧化鉻組成的組,優(yōu)選氧化鋯或二氧化鈦。也可以使用選自上述第二金屬氧化物的由多元氧化物構(gòu)成的載體。優(yōu)選地,第一金屬氧化物是氧化鎢、二氧化鈰或二氧化硅,以金屬氧化物重量相對于催化劑總質(zhì)量計(jì)算,催化劑體系中第一金屬氧化物的含量為1.0-40.0重量%,優(yōu)選2.0-30.0重量%,進(jìn)一步優(yōu)選13.0-30.0重量%。通過測量催化劑中的金屬含量并計(jì)算金屬氧化物的含量來確定所述金屬氧化物含量,其中如果一種金屬存在多種(穩(wěn)定的)氧化物,那么計(jì)算金屬以最高的氧化值存在的金屬氧化物的含量。優(yōu)選地,以液相,與例如氣相相反將所述原料引入反應(yīng)器中。以液相將原料引入反應(yīng)器中的一個優(yōu)點(diǎn)是其不需要加熱原料以制備氣態(tài)流。此外,原料中固體組分的存在可導(dǎo)致催化劑的堵塞。因此,優(yōu)選所述原料為液相且不包括相當(dāng)大量的固體材料,例如,少于4.0重量%,優(yōu)選少于1.0重量%,更優(yōu)選少于0.2重量%的固體材料。在此,固體材料包括懸浮或分散在液相中的固體材料??赏ㄟ^調(diào)節(jié)多個參數(shù)來控制C-C-偶合反應(yīng),包括通過選擇反應(yīng)條件例如:溫度、壓力和重時空速(WHSV)(kg原料/kg催化劑每小時)C-C-偶合反應(yīng)優(yōu)選在200-350℃,優(yōu)選210-300℃,更優(yōu)選220-280℃且甚至更優(yōu)選220-260℃的溫度下進(jìn)行。發(fā)現(xiàn)該溫度范圍特別適用于得到高程度的中等分子量(C8-C25)反應(yīng)產(chǎn)物,同時避免了過多聚合和催化劑焦化。優(yōu)選地,C-C-偶合反應(yīng)在0.5-100bar,優(yōu)選1.0-50bar,更優(yōu)選1.0-20bar的壓力下進(jìn)行。C-C-偶合反應(yīng)優(yōu)選在0.05h-1-2.0h-1,優(yōu)選0.1h-1-1.8h-1,更優(yōu)選0.2h-1-1.5h-1,最優(yōu)選0.25h-1-1.25h-1的重時空速下進(jìn)行。WHSV對所得材料的組成有影響,因?yàn)樗鼪Q定反應(yīng)物和催化劑的有效接觸時間。已顯示上述范圍提供高程度的有利產(chǎn)物。C-C-偶合反應(yīng)可在氫氣存在下進(jìn)行。在此情況下,將氫氣作為原料的一部分供應(yīng)至反應(yīng)器,與剩余原料一起同時供應(yīng)或者是經(jīng)過反應(yīng)器內(nèi)的單獨(dú)入口引入。也可能在無氫氣的情況下進(jìn)行C-C-偶合反應(yīng)并通過不時將氫氣添加至反應(yīng)中或在洗滌步驟中加到混合物中回收催化劑。C-C-偶合反應(yīng)可在100-3000Nl/l,優(yōu)選200-2000Nl/l,更優(yōu)選500-1800Nl/l且最優(yōu)選500-1500Nl/l的進(jìn)料比(H2/液體原料)下進(jìn)行。在此,液體原料指在反應(yīng)條件下主要以液體形式存在的原料。如果在氫氣存在下進(jìn)行C-C-偶合反應(yīng),所述催化劑體系也可包含至少一種選自元素周期表第VIII族,優(yōu)選選自Co、Ni、Ru、Rh、Pd和Pt的氫化金屬。在本發(fā)明的另一方面,提供了通過根據(jù)本發(fā)明的方法可得到的C-C偶合反應(yīng)產(chǎn)物。在本發(fā)明的另一方面,提供了用于由含至少一種酮酸的原料制備烴的方法。在本發(fā)明的又一方面,提供了由根據(jù)本發(fā)明的方法可得到的烴組合物。附圖說明圖1示出了說明木質(zhì)纖維素材料至乙酰丙酸轉(zhuǎn)化的方案。圖2示出了說明乙酰丙酸的一些反應(yīng)產(chǎn)物,包括潛在的焦炭前體和潛在的C-C偶合前體的方案。該圖不旨在覆蓋乙酰丙酸的所有反應(yīng)產(chǎn)物,也不旨在顯示所有類型的焦炭前體。圖2示出一種用于通過氫化反應(yīng)減少當(dāng)歸內(nèi)酯焦炭前體的可能機(jī)理,并且還示出了4-羥基戊酸的分子間酯,GVL,可以與4-羥基戊酸本身平衡。圖3示出了進(jìn)一步升級來自C-C-偶合反應(yīng)的產(chǎn)物的可能工藝方案的概觀。圖4示出了制備和升級來自C-C-偶合反應(yīng)的產(chǎn)物的可能工藝方案的概觀。具體實(shí)施方案通過C-C-偶合反應(yīng)增加酮酸分子量的挑戰(zhàn)之一是產(chǎn)物中間體的高活性,這導(dǎo)致起始組分太高程度的低聚作用。本發(fā)明人已發(fā)現(xiàn),在固體堿催化劑例如K2O/TiO2的存在下,酮酸特別地乙酰丙酸的低聚作用導(dǎo)致高的焦炭和焦油的形成,其通過抑制催化劑表面上的活性位點(diǎn)使催化劑中毒并最終導(dǎo)致反應(yīng)器的堵塞。不束縛于任何理論,建議這是由于乙酰丙酸至更活性的前體例如當(dāng)歸內(nèi)酯的反應(yīng)而發(fā)生的,所述前體已知在大于200℃的溫度下高度傾向于聚合。試圖通過在稀的水溶液中進(jìn)行反應(yīng)以減少不希望的聚合反應(yīng)并控制低聚反應(yīng)和焦化。然而,發(fā)現(xiàn)加入水以抑制焦化反應(yīng)會降低堿催化劑的性能,造成所希望的低聚反應(yīng)產(chǎn)物的低收率。本發(fā)明是基于這樣一個意外發(fā)現(xiàn):可以通過在包含第一金屬氧化物和第二金屬氧化物的固體酸催化劑體系的存在下使酮酸經(jīng)受C-C偶合反應(yīng),選擇性地增加酮酸的分子量。已發(fā)現(xiàn)使用包含第一和第二金屬氧化物的固體酸催化劑體系抑制反應(yīng)中間體的焦化傾向并同時催化多種類型的C-C偶合反應(yīng),導(dǎo)致在溶液中在反應(yīng)物之間形成新的碳-碳鍵。因此,本發(fā)明的一個方面是用于增加酮酸的分子量的方法,該方法包括在反應(yīng)器中提供包含至少一種酮酸的原料;和使原料經(jīng)受一個或多個的C-C偶合反應(yīng)的步驟,其中該C-C偶合反應(yīng)在包含第一金屬氧化物和第二金屬氧化物的固體酸催化劑體系的存在下進(jìn)行且其中在原料中所述至少一種酮酸的含量為至少30重量%。本發(fā)明還涉及用于增加酮酸分子量的方法。酮酸是具有酮官能(>C=O)和羧酸(COOH)或羧酸酯(COO–)官能二者的有機(jī)分子。在本說明書中,特殊形式的酮酸包括其中酮官能為醛(CH=O)的實(shí)施方案。在本發(fā)明中,所述酮酸可例如為α-酮酸(如丙酮酸、草酰乙酸和α-酮戊二酸)、β-酮酸(如乙酰乙酸)、γ-酮酸(如乙酰丙酸)或δ-酮酸。所述酮酸可具有多于一個的酮官能團(tuán)和多于一個的羧酸官能。優(yōu)選地,所述酮酸僅具有一個酮官能團(tuán)和一個羧酸官能團(tuán)。圖示1示出了根據(jù)本發(fā)明的示例性酮酸,例如其中n和m為整數(shù),各自彼此獨(dú)立地選自由0、1、2、3、4、5、6、7、8、9、10組成的組。優(yōu)選地,所述酮酸是γ-酮酸,更優(yōu)選乙酰丙酸(m=2,n=0)。優(yōu)選地,原料中酮酸的分子量增加至少40%或更多。優(yōu)選地,分子量增加為150-1000g/mol,例如160-500g/mol。當(dāng)所述酮酸為C4-C7-酮酸時,分子量可增加至具有C8-C35碳鏈,例如C8-C30碳鏈的相應(yīng)分子。例如,優(yōu)選的是,超過50重量%的反應(yīng)產(chǎn)物屬于含酮酸的二聚、三聚、四聚、五聚和六聚產(chǎn)物的組。二聚、三聚、四聚、五聚和六聚產(chǎn)物指與一種或多種酮酸的二、三、四、五和六個分子偶合在一起相關(guān)的反應(yīng)產(chǎn)物。在原料除酮酸還包含酮酸衍生物的情況下,所述二聚、三聚、四聚、五聚和六聚產(chǎn)物可額外地包含含一種或多種酮酸和/或其衍生物的混合的C-C偶合產(chǎn)物。二聚、三聚、四聚、五聚和六聚產(chǎn)物從至少一種酮酸衍生,例如至少兩種酮酸、至少三種酮酸、至少四種酮酸、至少五種酮酸、至少六種酮酸。在本發(fā)明中,通過一個或多個C-C-偶合反應(yīng)增加酮酸的分子量。許多C-C-偶合反應(yīng)是本領(lǐng)域中已知的,且技術(shù)人員基于所提供的反應(yīng)條件將能夠鑒定這樣的C-C-偶合反應(yīng)。特別地,所述C-C-偶合反應(yīng)可為酮基化反應(yīng)或通過烯醇或烯醇化物中間體進(jìn)行的反應(yīng)。在本發(fā)明中,所述C-C-偶合反應(yīng)可以選自含羥醛型反應(yīng)和縮合反應(yīng)、酮基化作用、其中C-C-偶合涉及烯烴的反應(yīng)和其他低聚合反應(yīng)的組。可使用兩個相同類型的分子(即相同化合物)進(jìn)行所述C-C偶合反應(yīng),或所述C-C偶合反應(yīng)可為兩個不同類型分子之間(即不同化合物之間)的交叉反應(yīng)。催化劑的活性取決于催化劑表面上的活性位點(diǎn)數(shù)和催化劑的比表面積。優(yōu)選地,所述催化劑體系的比表面積為10-500m2/g。具有該范圍內(nèi)的比表面積的催化劑體系已顯示提供足夠的反應(yīng)性以得到高收率的所需的C-C-偶合反應(yīng)產(chǎn)物,例如酮酸的二聚物、三聚物、四聚物、五聚物和六聚物,但同時使酮酸至焦炭前體的反應(yīng)最小化。固體酸催化劑的活性還取決于酸位點(diǎn)的總量,其優(yōu)選為30-500μmol/g的范圍內(nèi)。優(yōu)選地,原料包含作為主要組分的一種或多種酮酸。例如,所述至少一種酮酸在原料中的含量為至少40重量%,例如至少50重量%,至少70重量%,更優(yōu)選至少90重量%,或至少95重量%。優(yōu)選地,原料中水的含量為少于5.0重量%,優(yōu)選少于2.0重量%,更優(yōu)選少于1.0重量%。優(yōu)選地,原料中沒有水。然而,在一些縮合反應(yīng)中可以產(chǎn)生內(nèi)部水。發(fā)現(xiàn)酮酸至所需C-C-偶合反應(yīng)產(chǎn)物的轉(zhuǎn)化隨著原料中酮酸含量的增加而增加。發(fā)現(xiàn)水的存在降低乙酰丙酸至焦炭前體的反應(yīng),但水的添加也降低催化劑活性且降低所需C-C-偶合反應(yīng)產(chǎn)物的收率。C-C-偶合反應(yīng)產(chǎn)物的收率必須足夠高以使經(jīng)濟(jì)可行的用于由酮酸生產(chǎn)燃料組分和化學(xué)品的工藝成為可能。所述原料可通過處理木質(zhì)纖維素材料獲得,且在本發(fā)明的方法中可直接使用這樣處理的材料,或在用作原料之前將其純化不同的程度。所述乙酰丙酸可例如使用US5608105中公開的生物精煉(Biofine)方法制備。優(yōu)選地,原料包含乙酰丙酸,并且乙酰丙酸可與一種或多種其他酮酸或酮酸衍生物組合。所述酮酸衍生物可選自由酮酸的內(nèi)酯和內(nèi)酯衍生物,和戊酸組成的組。所述原料可包含乙酰丙酸與酮酸衍生物組合的混合物,例如基于原料總質(zhì)量至少30重量%的乙酰丙酸和至少10重量%的乙酰丙酸衍生物。除酮酸和酮酸衍生物外,所述原料還可包含醛類,例如糠醛或羥甲基糠醛。優(yōu)選地,本發(fā)明中使用的催化劑體系的第一金屬氧化物包含W、Be、B、Mg、Si、Ca、Sc、Ti、V、Cr、Mn、Fe、Co、Ni、Cu、Zn、Ga、Sr、Y、Zr、Nb、Mo、Cd、Sn、Sb、Bi、La、Ce、Th之一的氧化物,且所述第二金屬氧化物包含Zr、Ti、Si、Al、V、Cr之一的氧化物或它們的組合,第一金屬氧化物不同于第二金屬氧化物。金屬氧化物的組合包括金屬氧化物材料、混合的金屬氧化物和負(fù)載的金屬氧化物的固體混合物。更優(yōu)選地,催化劑體系包含第一金屬氧化物和第二金屬氧化物的混合物,其中第二金屬氧化物是選自氧化鋯、二氧化鈦、二氧化硅、氧化釩、氧化鉻的至少一種,優(yōu)選氧化鋯或二氧化鈦。催化劑體系可包含氧化鎢、二氧化鈰或二氧化硅和至少一種由氧化鋯、二氧化鈦、二氧化硅、氧化釩、氧化鉻,優(yōu)選氧化鋯或二氧化鈦中選擇的氧化物的混合物。優(yōu)選地,所述催化劑體系包含負(fù)載在金屬氧化物載體上的氧化鎢、二氧化鈰或二氧化硅,其中所述載體選自由氧化鋯、二氧化鈦、二氧化硅、氧化釩、氧化鉻組成的組,優(yōu)選氧化鋯或二氧化鈦。這里,鎢、鈰或硅的氧化物代表具有更高活性的金屬氧化物。已表明這些氧化物提供了良好的反應(yīng)性質(zhì)。此外,已顯示上面提到的載體提供了良好的負(fù)載性能而不影響更活性部分的功能,包括協(xié)同交互作用。此外,上面提到的組合允許在酸性反應(yīng)介質(zhì)中長時間使用催化劑而不劣化和/或分解并因此允許降低的總催化劑消耗。優(yōu)選地,以金屬氧化物的重量相對于催化劑的總質(zhì)量計(jì)算,催化劑體系中第一金屬氧化物的含量為1.0-40.0重量%,優(yōu)選2.0-30.0重量%,進(jìn)一步優(yōu)選13.0-30.0重量%。優(yōu)選地,將原料提供至單個反應(yīng)器中,或單個反應(yīng)器床中。所述反應(yīng)器應(yīng)能夠被加壓和容納原料和催化劑體系。所述反應(yīng)器應(yīng)具有用于供應(yīng)氣體和添加/取出原料的裝置,例如一個或多個入口和/或出口。此外,優(yōu)選存在用于控制壓力和溫度的裝置。優(yōu)選地,以液相,與例如氣相相反將所述原料引入反應(yīng)器中。以液相將原料引入反應(yīng)器中的一個優(yōu)點(diǎn)是其不需要加熱原料以制備氣態(tài)流。此外,原料中固體組分的存在可導(dǎo)致催化劑的堵塞。因此,優(yōu)選所述原料為液相且不包括相當(dāng)大量的固體材料,例如,少于4.0重量%,優(yōu)選少于1.0重量%,更優(yōu)選少于0.2重量%的固體材料。在此,固體材料包括懸浮或分散在液相中的固體材料。C-C偶合反應(yīng)主要在液相進(jìn)行,而不是氣相,這意味著該反應(yīng)是至少主要發(fā)生在液相中的催化劑上。C-C偶合反應(yīng)可以完全在液相中進(jìn)行。發(fā)明人發(fā)現(xiàn),可通過調(diào)節(jié)多個參數(shù)來控制C-C-偶合反應(yīng),包括適當(dāng)選擇反應(yīng)條件例如:溫度、壓力和重時空速(WHSV)和反應(yīng)時間/停留時間。已發(fā)現(xiàn)反應(yīng)溫度對產(chǎn)物分布具有顯著的影響。在低于200℃溫度下,酮酸的C-C-偶合產(chǎn)物的收率可能太低,且在400℃以上的溫度下由于形成焦炭和其他不需要的聚合產(chǎn)物,所述收率也可能減小。C-C-偶合反應(yīng)優(yōu)選在200-400℃,優(yōu)選210-300℃,更優(yōu)選220-280℃且最優(yōu)選220-260℃的溫度下進(jìn)行。發(fā)現(xiàn)上述溫度范圍特別適用于得到高程度的中等分子量(C8-C30)反應(yīng)產(chǎn)物,同時避免了過多聚合和催化劑焦化。由于大部分C-C偶合反應(yīng)發(fā)生在液相中,合適地選擇壓力和溫度以便保持反應(yīng)物在液相中。有利地,C-C-偶合反應(yīng)在0.5-100bar,優(yōu)選1.0-50bar,更優(yōu)選1.0-20bar的壓力下進(jìn)行。C-C-偶合反應(yīng)優(yōu)選在0.05h-1-2.0h-1,優(yōu)選0.1h-1-1.8h-1,更優(yōu)選0.2h-1-1.5h-1,最優(yōu)選0.25h=-1.25h-1的重時空速(kg原料/kg催化劑*小時)下進(jìn)行。WHSV對所得材料的組成有影響,因?yàn)樗鼪Q定反應(yīng)物和催化劑的有效接觸時間。已顯示上述范圍提供高程度的有利產(chǎn)物。C-C偶合反應(yīng)可以在作為原料的一部分供應(yīng)至反應(yīng)器中的氫氣存在下進(jìn)行。氫氣可以與一種或多種其他氣體,優(yōu)選惰性氣體如氮?dú)?、氬氣、氦氣或另一種惰性氣體,或者對本發(fā)明的反應(yīng)條件表現(xiàn)為惰性的氣體混合。表現(xiàn)惰性被認(rèn)為是該氣體不應(yīng)該在很大程度上參與作為反應(yīng)成員,并且優(yōu)選地惰性氣體應(yīng)當(dāng)盡可能少參與,例如根本不參與。發(fā)現(xiàn)催化劑體系的性能可以通過在原料中添加氫進(jìn)一步提高,減少低聚程度和酮酸向不希望組分的轉(zhuǎn)化。氫的添加不會引入氫化活性,除非該催化劑體系包含氫化金屬,但提出了修改催化劑體系一部分的可還原的金屬氧化物的表面性質(zhì)。C-C-偶合反應(yīng)可在100-3000Nl/l,優(yōu)選200-2000Nl/l,更優(yōu)選500-1800Nl/l且最優(yōu)選500-1500Nl/l的流量比(H2/液體原料)下進(jìn)行。當(dāng)在氫氣存在下反應(yīng)時,該催化劑體系除了第一和第二金屬氧化物外可以包含至少一種氫化金屬。氫化金屬優(yōu)選選自元素周期表第VIII族,優(yōu)選選自Co、Ni、Ru、Rh、Pd和Pt。發(fā)現(xiàn)包含氫化金屬的催化劑體系可以進(jìn)一步提高催化劑的穩(wěn)定性并抑制至不適合用作燃料組分或化學(xué)品的組分的低聚反應(yīng)。在本發(fā)明的另一方面,提供了通過根據(jù)本發(fā)明的方法可得到的C-C偶合反應(yīng)產(chǎn)物。該產(chǎn)物可直接用作燃料或基礎(chǔ)油組分或化學(xué)品或作為在燃料或基礎(chǔ)油組分或化學(xué)品生產(chǎn)中的中間體組分。如果需要的話,通過本發(fā)明的方法可得到的C-C偶合反應(yīng)產(chǎn)物可進(jìn)一步經(jīng)受加氫脫氧(HDO)步驟以移除氧,這優(yōu)選地產(chǎn)生完全脫氧的材料(即,不含氧原子的烴化合物)。所產(chǎn)生的烴可用作燃料或基礎(chǔ)油組分或化學(xué)品或作為在燃料或基礎(chǔ)油組分或化學(xué)品生產(chǎn)中的起始組分。所述加氫脫氧的產(chǎn)物也可進(jìn)一步被異構(gòu)化為異鏈烷烴。本發(fā)明的一個優(yōu)勢是由可再生材料制備的酮酸可被升級至更高分子量的烴和/或烴衍生物,其可被用作燃料或基礎(chǔ)油組分或化學(xué)品或作為在燃料或基礎(chǔ)油組分或化學(xué)品生產(chǎn)中的起始組分。C-C-偶合反應(yīng)產(chǎn)物可被分餾以移除潛在的未反應(yīng)的酮酸單體和其他低分子量組分例如來自反應(yīng)產(chǎn)物的在C-C-偶合反應(yīng)中形成的水和CO2,如在圖3中所示。可通過任何常規(guī)的方法例如蒸餾來進(jìn)行所述分餾。所述未反應(yīng)的酮酸單體可任選地被回收并與第一反應(yīng)器的進(jìn)料結(jié)合。本發(fā)明的另一個方面涉及一種用于生產(chǎn)烴的方法,所述方法包括使用本發(fā)明的方法增加酮酸分子量以得到C-C偶合反應(yīng)產(chǎn)物和使所述C-C偶合反應(yīng)產(chǎn)物經(jīng)受加氫脫氧步驟和任選地經(jīng)受異構(gòu)化步驟的步驟。在加氫脫氧步驟中使用的HDO催化劑可包含在支撐物上的氫化金屬,諸如例如選自由Pd、Pt、Ni、Co、Mo、Ru、Rh、W或它們?nèi)魏谓M合組成的組的HDO催化劑。所述加氫脫氧步驟可例如在100-500℃的溫度和10-150bar的壓力下進(jìn)行??墒褂萌魏纬R?guī)的方法例如蒸餾將水和輕氣體從HDO產(chǎn)物中分離。在移除水和輕氣體后,HDO產(chǎn)物可被分餾至一種或多種適合作為汽油、航空燃料、柴油或基礎(chǔ)油組分的餾分??赏ㄟ^任何常規(guī)的方法例如蒸餾來進(jìn)行所述分餾。任選地,部分HDO步驟的產(chǎn)物可被再循環(huán)和與HDO反應(yīng)器的進(jìn)料結(jié)合。本發(fā)明的另一方面涉及通過根據(jù)本發(fā)明的方法可得到的烴組合物。該產(chǎn)物可用作燃料或基礎(chǔ)油組分或化學(xué)品或在燃料或基礎(chǔ)油組分或化學(xué)品的生產(chǎn)中作為中間體組分。本發(fā)明的另一個方面涉及一種烴組合物,其包含至少30重量%的鏈烷烴,至少50重量%的環(huán)烷,少于10重量%的芳族化合物,并且其中該烴中的至少70重量%具有的碳原子數(shù)為8-10。這種烴組合物可以由根據(jù)本發(fā)明的方法得到。優(yōu)選地,這種烴組合物被用作汽油燃料或汽油燃料組分。本發(fā)明的另一個方面涉及一種烴組合物,其包含至少60重量%的脂族烴,至少30wt%的芳族化合物,并且其中該烴中的至少70重量%具有碳原子數(shù)為9-24。這種烴組合物可以由根據(jù)本發(fā)明的方法得到。優(yōu)選地,這種烴組合物被用作柴油燃料或柴油燃料組分。加氫脫氧步驟的產(chǎn)物也可在氫和異構(gòu)化催化劑存在下經(jīng)受異構(gòu)化步驟。加氫脫氧步驟和異構(gòu)化步驟二者可在同一反應(yīng)器中進(jìn)行。所述異構(gòu)化催化劑可為貴金屬雙功能催化劑,例如Pt-SAPO或Pt-ZSM-催化劑。所述加氫脫氧步驟可例如在200-400℃的溫度和20-150bar的壓力下進(jìn)行。優(yōu)選僅部分HDO產(chǎn)物經(jīng)受異構(gòu)化步驟,特別地所述經(jīng)受異構(gòu)化的部分HDO產(chǎn)物可為在300℃或以上的溫度下沸騰的重餾分。由加氫脫氧和/或異構(gòu)化步驟可得到的烴產(chǎn)物可用作燃料或基礎(chǔ)油組分或化學(xué)品或用作在燃料或基礎(chǔ)油組分或化學(xué)品的生產(chǎn)中的中間體組分。通常使HDO產(chǎn)物經(jīng)受異構(gòu)化的選擇高度依賴于最終產(chǎn)品所需的性能。在HDO產(chǎn)物包含大量的正鏈烷烴的情況下,HDO產(chǎn)物可經(jīng)受異構(gòu)化步驟以將至少部分的正鏈烷烴轉(zhuǎn)化為異鏈烷烴以改善最終產(chǎn)品的冷性能。實(shí)施例材料作為催化劑例子,在乙酰丙酸的C-C偶合反應(yīng)中可以使用具有表1所示組成的WO3/ZrO2、CeO2/ZrO2和SiO2/ZrO2。這些催化劑可以得自Saint-GobainNORPRO。表1.催化劑的組成WO3/ZrO2CeO2/ZrO2SiO2/ZrO2類型SZ6*143SZ6*191SZ6*152表面積,m2/g130110140WO3,重量%18CeO2,重量%18SiO2,重量%3.3原子密度3.6W/nm25.7Ce/nm22.4Si/nm2各自的氧化物的重量百分比通過催化劑的總質(zhì)量來計(jì)算。第一金屬氧化物的金屬的原子密度已基于催化劑的比表面積和催化劑中各金屬氧化物的含量被計(jì)算。通過催化劑生產(chǎn)商提供的比表面積已經(jīng)通過測量氮的等溫吸附線的BET方法測定(ASTMD-3663)。實(shí)施例1通過使用WO3/ZrO2-催化劑體系的C-C偶合反應(yīng)增加乙酰丙酸的分子量WO3/ZrO2-催化劑(樣品SZ6*143)的性能在連續(xù)的管式流動反應(yīng)器測試運(yùn)行中使用商用級乙酰丙酸(97%,Sigma-Aldrich)作為原料進(jìn)行評估。C-C-偶合反應(yīng)在約200℃至約240℃的溫度和約20bar的壓力下使用0.25、0.5和1.0h-1的重時空速(WHSV)進(jìn)行。所述反應(yīng)在氮?dú)饣驓錃饬?50ml/min)中進(jìn)行以研究添加至進(jìn)料中的氫氣的影響。根據(jù)進(jìn)料至容器中乙酰丙酸的量計(jì)算WHSV。對于不同條件下的反應(yīng),由液體收率確定所形成氣體的量(氣體=100-液體產(chǎn)物)。所述液體產(chǎn)物由包含在反應(yīng)中形成的水的有機(jī)相組成。通過熱重分析(TGA)獲得對液體產(chǎn)物中水量的大致評估。通過HPLC分析確定LA(乙酰丙酸)和GVL(γ-戊內(nèi)酯)在液體產(chǎn)物中的定量量。由GPC色譜圖得到有機(jī)相中二聚物和低聚物的相對量。相對于干液體產(chǎn)物(不含水)計(jì)算包括未反應(yīng)的LA的有機(jī)相的組成。表2和表3中示出了在氮?dú)夂蜌錃饬髦性赪O3/TiO2催化劑體系上用于乙酰丙酸轉(zhuǎn)化的有機(jī)相的產(chǎn)物收率和組成。表2.使用WO3/ZrO2-催化劑的工藝條件和產(chǎn)物收率。表3.使用WO3/ZrO2-催化劑的有機(jī)相中的產(chǎn)物分布在實(shí)驗(yàn)8中,在實(shí)驗(yàn)期間從反應(yīng)混合物連續(xù)除去水,因此產(chǎn)物中的水量低于其他實(shí)驗(yàn)。實(shí)驗(yàn)8的產(chǎn)物在實(shí)施例3中用作用于加氫脫氧實(shí)驗(yàn)的C-C偶合反應(yīng)產(chǎn)物原料。實(shí)施例2通過使用WO3/ZrO2-、CeO2/ZrO2-和SiO2/ZrO2-催化劑體系的C-C偶合反應(yīng)增加乙酰丙酸的分子量在間歇反應(yīng)器測試運(yùn)行中使用商用級乙酰丙酸(97%,SigmaAldrich)作為進(jìn)料對比WO3/ZrO2-、CeO2/ZrO2-和SiO2/ZrO2-催化劑的性能。在裝入反應(yīng)器之前將催化劑在120℃在氮?dú)饬髦懈稍镞^夜。反應(yīng)器中裝載5g催化劑和50g乙酰丙酸。在200℃和20bar在氮?dú)庀逻M(jìn)行測試運(yùn)行。通過GPC方法分析在200℃下2小時后取出的液體樣品的組成。表4.有機(jī)相中的產(chǎn)物分布表4中乙酰丙酸、二聚物和低聚物的含量是基于GPC色譜中的峰面積。實(shí)施例3C-C偶合反應(yīng)產(chǎn)物餾分加氫脫氧以生產(chǎn)烴在該實(shí)施例中,實(shí)施例1中實(shí)驗(yàn)8的C-C偶合反應(yīng)產(chǎn)物經(jīng)受加氫脫氧(HDO)步驟,以除去雜原子(特別是氧)和以穩(wěn)定油產(chǎn)物。用作HDO反應(yīng)器進(jìn)料的C-C偶合反應(yīng)產(chǎn)物含有24重量%的低聚物、35重量%的二聚物和41重量%的未反應(yīng)的乙酰丙酸,其在進(jìn)料到HDO步驟之前未被除去。在管式流動反應(yīng)器中在硫化的NiMo/Al2O3催化劑存在下,在310℃溫度和80bar壓力下使用3300Nl/l的氫/進(jìn)料(H2/進(jìn)料)比和0.3h-1的重時空速(WHSV)進(jìn)行加氫脫氧反應(yīng)。根據(jù)進(jìn)料到容器中的測試油的量計(jì)算WHSV和氫/烴比。表5中所示的HDO產(chǎn)物分布通過模擬GC-蒸餾確定和除氧的成功性由FTIR光譜進(jìn)行評估。該HDO產(chǎn)物蒸餾成汽油和柴油餾分。汽油餾分的化學(xué)組成通過GC-MS和PIONA分析測定。在PIONA分析中,存在于樣品中的化合物進(jìn)行定量和分組為鏈烷烴、烯烴,環(huán)烷、芳族化合物和含氧化物。組分分析是作為碳數(shù)的函數(shù)表示。對于柴油餾分,測定芳族化合物和極性化合物的量。表5.加氫處理產(chǎn)物收率。存在于HDO進(jìn)料中的未反應(yīng)的LA被部分轉(zhuǎn)化為戊烷,這是在氣相中相對高的C5-C9收率看出的。氧氣可以在脫水和HDO反應(yīng)中作為H2O被除去,在脫羧反應(yīng)中作為CO2被除去。除去的氧量(40重量%)與在LA中的氧含量(41重量%)對應(yīng)良好。汽油餾分的PIONA分析表明,它含有37.4重量%的鏈烷烴(主要是異鏈烷烴),58.2重量%的環(huán)烷(主要是石蠟環(huán)烷)和4.1重量%的芳族化合物。還觀察到少量的含氧化物(0.2重量%)。含氧化物被確定為是戊基醚(0.1重量%)和丙酮(0.1重量%)。汽油餾分的化合物主要分布在C8-C10范圍中。碳含量為85.3重量%,氫含量為14.6重量%,相應(yīng)于H/C-摩爾比為2.0。芳族化合物和極性化合物在柴油餾分中的含量通過HPLC方法進(jìn)行分析,它表明柴油含有37.6重量%的芳族化合物和0.1重量%的極性化合物。柴油餾分的剩余部分(62.3重量%)為脂族烴。這些實(shí)施例表明,可以通過在包含第一金屬氧化物和第二金屬氧化物的固體酸催化劑體系的存在下進(jìn)行的C-C偶合反應(yīng)增加乙酰丙酸的分子量。這些實(shí)施例還表明,乙酰丙酸的C-C-偶合反應(yīng)產(chǎn)物可以通過使乙酰丙酸的C-C-偶合反應(yīng)產(chǎn)物在典型的HDO催化劑和氫存在下經(jīng)受加氫脫氧反應(yīng)而被進(jìn)一步加工為具有典型的燃料組分例如汽油和柴油組分的沸點(diǎn)范圍的烴。本發(fā)明涉及酮酸的催化轉(zhuǎn)化,包括用于增加酮酸分子量的方法,所述方法包括在反應(yīng)器中提供含至少一種酮酸的原料的步驟。然后將原料在包含第一金屬氧化物和第二金屬氧化物的催化劑體系存在下經(jīng)受一個或多個C-C偶合反應(yīng)當(dāng)前第1頁1 2 3