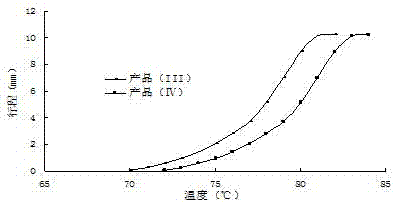
一種以F-T合成產(chǎn)物生產(chǎn)節(jié)溫器用蠟介質(zhì)的方法技術(shù)領(lǐng)域本發(fā)明屬于特種蠟生產(chǎn)技術(shù)領(lǐng)域,特別是涉及一種以F-T合成產(chǎn)物生產(chǎn)節(jié)溫器用蠟介質(zhì)的方法。
背景技術(shù):蠟質(zhì)溫控閥以蠟類物質(zhì)作為感應(yīng)溫度變化的介質(zhì),當(dāng)環(huán)境溫度變化時(shí),蠟類物質(zhì)的體積產(chǎn)生變化,進(jìn)而控制閥門開度,從而調(diào)節(jié)物流流量,達(dá)到調(diào)整、控制溫度的目的。蠟質(zhì)溫控閥所用蠟類物質(zhì)稱作蠟介質(zhì)。節(jié)溫器又稱調(diào)溫器,其作用是根據(jù)冷卻水溫度的高低自動(dòng)調(diào)節(jié)進(jìn)入散熱器的水量,改變水的循環(huán)范圍,以調(diào)節(jié)冷卻系統(tǒng)的散熱能力,保證發(fā)動(dòng)機(jī)在合適的溫度范圍內(nèi)工作。常用的節(jié)溫器是蠟式節(jié)溫器,屬蠟質(zhì)溫控閥。蠟式節(jié)溫器一般采用套管式結(jié)構(gòu),控溫范圍10~12℃,根據(jù)發(fā)動(dòng)機(jī)的最佳工作溫度區(qū)域,又按標(biāo)稱溫度分成70、72、76、80、82等規(guī)格,標(biāo)稱溫度為70℃的節(jié)溫器的控溫區(qū)間為70℃~80℃。對(duì)節(jié)溫器行程要求為:常溫~標(biāo)稱溫度+2℃的行程小于1mm,控溫范圍內(nèi)(標(biāo)稱溫度~標(biāo)稱溫度+10℃或標(biāo)稱溫度+12℃)行程大于8mm。蠟式節(jié)溫器是依靠其所用的蠟介質(zhì)隨溫度變化產(chǎn)生體積變化作為輸出動(dòng)作的原動(dòng)力。當(dāng)冷卻水溫度低于規(guī)定值時(shí),節(jié)溫器感溫體內(nèi)的蠟介質(zhì)呈固態(tài),節(jié)溫器閥在彈簧的作用下關(guān)閉發(fā)動(dòng)機(jī)與散熱器之間的通道,冷卻水經(jīng)水泵返回發(fā)動(dòng)機(jī),進(jìn)行發(fā)動(dòng)機(jī)內(nèi)小循環(huán);當(dāng)冷卻水溫度達(dá)到規(guī)定值后,蠟介質(zhì)產(chǎn)生固→液相變,體積膨脹,并壓迫橡膠管使其收縮。在橡膠管收縮的同時(shí)對(duì)推桿作用以向上的推力,推桿對(duì)閥門有向下的反推力使閥門開啟。這時(shí)冷卻水經(jīng)由散熱器和節(jié)溫器閥,再經(jīng)水泵流回發(fā)動(dòng)機(jī),進(jìn)行大循環(huán)。這樣蠟式節(jié)溫器就能根據(jù)冷卻水溫度的變化自動(dòng)調(diào)節(jié)進(jìn)入散熱器的水量,從而保證發(fā)動(dòng)機(jī)在合適的溫度范圍內(nèi)工作。從蠟式節(jié)溫器的工作原理可以看出,蠟介質(zhì)是其接收環(huán)境溫度變化進(jìn)而輸出相應(yīng)動(dòng)作的主體,因而蠟介質(zhì)的性質(zhì)是蠟式節(jié)溫器性能的決定因素。一般蠟介質(zhì)處于液體狀態(tài)時(shí),其膨脹系數(shù)約為6.7×10-4,固態(tài)時(shí)的膨脹系數(shù)比液態(tài)時(shí)稍大,而在固←→液相變范圍內(nèi)膨脹系數(shù)遠(yuǎn)大于此值。對(duì)節(jié)溫器用蠟介質(zhì)的要求就是相變過程的體積膨脹應(yīng)與節(jié)溫器的控溫范圍一致,反映在推桿行程上就是要在節(jié)溫器的控溫范圍內(nèi)大于8mm,而在控溫范圍以外行程要很小。石油蠟是原油經(jīng)過煉制加工后從含蠟餾分油中制得的各類蠟產(chǎn)品的總稱,包括液體石蠟、石蠟和微晶蠟。商品石油蠟是多種碳數(shù)的正構(gòu)烷烴、異構(gòu)烷烴、環(huán)烷烴等的烴類混合物,其碳數(shù)分布較寬,正構(gòu)烷烴含量較低。商品石油蠟直接用作節(jié)溫器的蠟介質(zhì)時(shí),會(huì)導(dǎo)致大循環(huán)開啟過早(常溫~標(biāo)稱溫度+2℃范圍內(nèi)推桿的行程大于1mm),使發(fā)動(dòng)機(jī)預(yù)熱時(shí)間延長(zhǎng);同時(shí)由于推桿行程較?。?biāo)稱溫度~標(biāo)稱溫度+10℃或標(biāo)稱溫度+12℃的行程小于8mm),會(huì)導(dǎo)致發(fā)動(dòng)機(jī)正常工作時(shí)大循環(huán)的水量不足,引起發(fā)動(dòng)機(jī)過熱。所以商品石油蠟必須經(jīng)分離提純才能用作節(jié)溫器的蠟介質(zhì)。這些提純過程工藝復(fù)雜,不僅生產(chǎn)成本高,而且對(duì)于節(jié)溫器用蠟介質(zhì)來說仍存在一定數(shù)量的非適宜組分,如油類等,這些非適宜組分的存在影響了使用性能。費(fèi)-托(F-T)合成技術(shù)是1923年發(fā)明的,1936年在德國(guó)實(shí)現(xiàn)工業(yè)化。F-T合成技術(shù)主要包括高溫合成技術(shù)和低溫合成技術(shù)。二十世紀(jì)九十年代以來,F(xiàn)-T合成工藝及催化劑都取得了突破性的進(jìn)展,F(xiàn)-T合成產(chǎn)品日益豐富,為生產(chǎn)節(jié)溫器用蠟介質(zhì)提供了新的原料。在石油蠟生產(chǎn)工藝方面,常用的分離加工手段主要有蒸餾、溶劑脫油、發(fā)汗脫油等。蒸餾是利用不同烴類的沸點(diǎn)不同達(dá)到分離提純的目的,減小蒸餾的沸程可以有效降低產(chǎn)物碳分布的寬度,但對(duì)提高正構(gòu)烷烴含量影響不大,并且由于蒸餾過程需要將石油蠟加熱到沸點(diǎn)以上,消耗大量的能量。同時(shí)熔點(diǎn)在70℃以上的烴類的沸點(diǎn)在500℃(常壓)以上,采用蒸餾進(jìn)行分離時(shí)效率大大下降。溶劑脫油方法是利用正構(gòu)烷烴與異構(gòu)烷烴在溶劑中的溶解度不同達(dá)到分離提純的目的,可以有效提高產(chǎn)物中的正構(gòu)烷烴含量,但對(duì)碳分布寬窄的影響不大,同時(shí)溶劑脫油生產(chǎn)設(shè)備投資大;生產(chǎn)過程中需要大量使用溶劑,回收溶劑需要消耗大量的能量;溶劑中含有苯系物,會(huì)對(duì)環(huán)境造成影響;溶劑易燃,容易造成生產(chǎn)事故。發(fā)汗脫油方法是利用蠟中各種烴類組分熔點(diǎn)不同的性質(zhì)進(jìn)行分離提純的。石油蠟中各種組分的分子量和結(jié)構(gòu)的不同都會(huì)使其熔點(diǎn)不同。同為正構(gòu)烷烴時(shí),分子量較大的正構(gòu)烷烴的熔點(diǎn)較高,而分子量較小的正構(gòu)烷烴的熔點(diǎn)較低;分子量相同時(shí),異構(gòu)烷烴和環(huán)烷烴的熔點(diǎn)要低于正構(gòu)烷烴,且異構(gòu)程度越高熔點(diǎn)就越低。所以發(fā)汗脫油即能降低產(chǎn)物碳分布的寬度又能提高正構(gòu)烷烴含量。與蒸餾分離方法相比,由于各種烴類的熔點(diǎn)溫度遠(yuǎn)低于沸點(diǎn)溫度,所以發(fā)汗分離過程的能耗遠(yuǎn)低于蒸餾分離,同時(shí)產(chǎn)物的熔點(diǎn)也可以提高;與溶劑分離方法相比,發(fā)汗分離過程不使用溶劑,所以發(fā)汗分離過程對(duì)環(huán)境無影響。而且發(fā)汗法即能降低產(chǎn)物碳分布的寬度又能提高正構(gòu)烷烴含量,所以對(duì)生產(chǎn)節(jié)溫器用蠟介質(zhì)而言,發(fā)汗脫油分離過程在生產(chǎn)過程和產(chǎn)品性能兩方面都有優(yōu)勢(shì)。普通的發(fā)汗脫油過程主要包括以下步驟:(1)準(zhǔn)備工作:墊水,用水充滿發(fā)汗裝置皿板下部空間;(2)裝料:原料加熱至熔點(diǎn)以上呈液態(tài)時(shí)裝入發(fā)汗裝置;(3)降溫結(jié)晶:將原料以不大于4℃/h的降溫速率緩慢冷卻到其熔點(diǎn)以下10~20℃。在冷卻過程中,熔點(diǎn)最高的組分先以粗的纖維狀晶體形態(tài)結(jié)晶出來,隨著蠟層溫度繼續(xù)降低,其它組分按熔點(diǎn)由高到低的順序依次結(jié)晶形成固體;(4)升溫發(fā)汗:當(dāng)蠟層溫度達(dá)到預(yù)設(shè)的降溫終止溫度之后,放掉墊水;再將原料緩慢地加熱到預(yù)設(shè)的發(fā)汗終止溫度。在升溫發(fā)汗過程中,各種組分按熔點(diǎn)由低到高的順序先后熔化成液態(tài)并流出(蠟下),最后得到的蠟層剩余物(蠟上)就是高熔點(diǎn)、低含油的蠟;(5)粗產(chǎn)品收集:升溫發(fā)汗過程結(jié)束后繼續(xù)升高溫度,以熔化取出蠟上,即為粗產(chǎn)品;(6)產(chǎn)品精制、成型、包裝:精制過程通常采用白土精制:將粗產(chǎn)品熔化后升溫至預(yù)定溫度,加入白土并恒溫?cái)嚢柚令A(yù)定時(shí)間后過濾;再經(jīng)成型、包裝即為目的產(chǎn)品。普通發(fā)汗工藝可以生產(chǎn)熔點(diǎn)在40℃~60℃的皂蠟和低熔點(diǎn)石蠟,不適宜生產(chǎn)熔點(diǎn)在70℃以上的高熔點(diǎn)蠟產(chǎn)品。有試驗(yàn)表明,普通發(fā)汗脫油工藝生產(chǎn)熔點(diǎn)在70℃以上的高熔點(diǎn)蠟產(chǎn)品時(shí),發(fā)汗后期蠟上的碳分布寬度和正構(gòu)烷烴含量與收率無關(guān),即蠟上的碳分布寬度不隨收率的下降而下降,正構(gòu)烷烴含量也不隨收率的下降而提高,所以普通發(fā)汗分離工藝不適宜生產(chǎn)熔點(diǎn)在70℃以上的節(jié)溫器用蠟介質(zhì)。目前僅有部分廠家使用發(fā)汗脫油工藝生產(chǎn)皂蠟和低熔點(diǎn)的石蠟等普通產(chǎn)品。多年來,發(fā)汗脫油工藝在生產(chǎn)設(shè)備和工藝方面得到了一些發(fā)展,如CN89214332(立式方形多段隔板發(fā)汗罐)、CN98233254.8(石蠟發(fā)汗罐)、CN201320127680.4(管式石蠟脫油裝置)等,在發(fā)汗脫油生產(chǎn)設(shè)備上作了改進(jìn);CN91206202(一種高效石蠟發(fā)汗罐)在發(fā)汗脫油工藝上作了改進(jìn)。但這些改進(jìn)仍不能生產(chǎn)熔點(diǎn)在70℃以上的節(jié)溫器用蠟介質(zhì)?,F(xiàn)有技術(shù)中的蠟介質(zhì)制備手段,有采用溶劑法的,如:DD241,829、DD241,830等專利介紹以溶劑萃取的方法制備80~90℃范圍內(nèi)控溫的蠟介質(zhì)。DD247,572、SU1,084,289、RU2,009,171、US5,223,122等專利介紹的制備方式,均以溶劑萃取為主。這些專利介紹的制備方式對(duì)環(huán)境有污染?,F(xiàn)有技術(shù)中的蠟介質(zhì)制備手段,也有采用(多段)發(fā)汗或(與蒸餾方法)組合發(fā)汗的,如:CN02109670.8(淋浴自動(dòng)調(diào)溫閥用蠟質(zhì)感溫介質(zhì))等專利的目的產(chǎn)品的熔點(diǎn)都在50℃以下;CN201110353409.8(一種控溫閥用蠟質(zhì)感溫介質(zhì)的制備方法)等專利的目的產(chǎn)品熔點(diǎn)也在50℃以下,且控溫范圍寬,不適合用作節(jié)溫器用蠟介質(zhì)。發(fā)汗工藝具有投資少、生產(chǎn)過程簡(jiǎn)單、操作費(fèi)用低、處理量適中、產(chǎn)品質(zhì)量指標(biāo)易于調(diào)整等優(yōu)點(diǎn),更重要的是,發(fā)汗脫油工藝是目前已知用于工業(yè)規(guī)模生產(chǎn)石蠟產(chǎn)品的唯一無溶劑脫油方法,在提倡綠色低碳、環(huán)保節(jié)能的今天,采用發(fā)汗脫油工藝生產(chǎn)節(jié)溫器用蠟介質(zhì)的需求更加迫切。
技術(shù)實(shí)現(xiàn)要素:針對(duì)現(xiàn)有技術(shù)的不足,本發(fā)明提供一種以F-T合成產(chǎn)物生產(chǎn)節(jié)溫器用蠟介質(zhì)的方法,包括加氫轉(zhuǎn)化、蒸餾、發(fā)汗三部分。具體地說是以適宜的F-T合成產(chǎn)物為原料,在催化劑作用下進(jìn)行加氫轉(zhuǎn)化,將其中的烯烴和含氧化合物轉(zhuǎn)化為節(jié)溫器用蠟介質(zhì)的適宜組分;加氫產(chǎn)物經(jīng)蒸餾制取適當(dāng)餾程的組分;再采用發(fā)汗裝置,在普通發(fā)汗方法的基礎(chǔ)上,原料加熱熔化后優(yōu)選在壓力條件下?lián)饺氲头悬c(diǎn)液體;在冷卻降溫過程中的適當(dāng)溫度增加高溫恒溫階段,并增加在冷卻過程結(jié)束后的低溫恒溫階段和升溫發(fā)汗過程的恒溫階段;并在發(fā)汗過程中利用氣流通過蠟層攜帶出液態(tài)組分以強(qiáng)制分離固態(tài)組分與液態(tài)組分,增強(qiáng)了分離效果并加快了分離速度。降溫的低溫恒溫過程和升溫及恒溫的發(fā)汗過程中回收低沸點(diǎn)液體。本發(fā)明方法以F-T合成產(chǎn)物為原料使用發(fā)汗這種無溶劑分離方法生產(chǎn)出節(jié)溫器用蠟介質(zhì)。本發(fā)明的一種以F-T合成產(chǎn)物生產(chǎn)節(jié)溫器用蠟介質(zhì)的方法,包括以下內(nèi)容:(一)加氫轉(zhuǎn)化:F-T合成產(chǎn)物在催化劑作用下進(jìn)行加氫轉(zhuǎn)化,將其中的烯烴和含氧化合物轉(zhuǎn)化為正構(gòu)烷烴;(二)蒸餾:將上述經(jīng)加氫轉(zhuǎn)化所得產(chǎn)物在蒸餾裝置中制取初餾點(diǎn)為450~500℃、終餾點(diǎn)為510~540℃的餾分;(三)發(fā)汗,包括以下過程:(1)在發(fā)汗裝置中墊水;(2)以過程(二)蒸餾制取的餾分為原料,加熱熔化后裝入發(fā)汗裝置;(3)以1.0℃/h~3.0℃/h的速率將蠟層降溫至適當(dāng)溫度,高溫恒溫一段時(shí)間;再以0.5℃/h~2.5℃/h的速率降溫至原料熔點(diǎn)以下5℃~20℃的預(yù)定溫度,并低溫恒溫一段時(shí)間;(4)排出發(fā)汗裝置中的墊水;然后以0.5℃/h~2.5℃/h的速率升溫,蠟層達(dá)到預(yù)定溫度后恒溫一段時(shí)間,然后停止發(fā)汗;其中在發(fā)汗過程中強(qiáng)制氣流通過蠟層;(5)產(chǎn)品精制和成型、包裝后即得到節(jié)溫器用蠟介質(zhì)產(chǎn)品。本發(fā)明的方法中,所述的F-T合成產(chǎn)物,其正構(gòu)烷烴重量含量要求大于等于85%,優(yōu)選正構(gòu)烷烴含量大于等于95%的F-T合成產(chǎn)物作為原料。本發(fā)明的方法中,其中過程(三)的步驟(2)中,通常將發(fā)汗原料加熱至其熔點(diǎn)以上3℃~8℃,以使其盡快全部熔化。本發(fā)明的方法中,過程(一)所述的加氫轉(zhuǎn)化過程采用本領(lǐng)域的常規(guī)技術(shù)。加氫轉(zhuǎn)化操作條件為:反應(yīng)壓力3~10MPa、反應(yīng)溫度150~300℃、液時(shí)體積空速0.2~2.0h-1和氫液體積比100~1000:1,氫液體積比優(yōu)選為300~800:1。加氫轉(zhuǎn)化催化劑可以為Ni/Al2O3、W-Ni/Al2O3、Mo-Ni/Al2O3或W-Mo-Ni/Al2O3催化劑等。催化劑中活性金屬組分以氧化物計(jì)的重量含量為20%~70%。加氫轉(zhuǎn)化催化劑可以按本領(lǐng)域常規(guī)方法制備。催化劑使用時(shí)可以根據(jù)需要按本領(lǐng)域常規(guī)方法將活性金屬氧化物還原或硫化,以提高催化劑活性。本發(fā)明的方法中,過程(二)中所述的蒸餾裝置可以是具有接近2塊理論塔板的減壓蒸餾裝置。本發(fā)明的方法中,優(yōu)選在過程(三)的步驟(2)中原料(即過程(二)蒸餾制取的餾分)加熱熔化后在壓力條件下?lián)饺氲头悬c(diǎn)液體。所述的壓力(表壓)為0.5~20.0個(gè)大氣壓,優(yōu)選為1.0~10.0個(gè)大氣壓。所述的低沸點(diǎn)液體為有機(jī)物,其與原料有較好的互溶性,且在常壓下的沸點(diǎn)低于冷卻降溫的預(yù)定溫度,而在高壓下的沸點(diǎn)高于加料過程的最高溫度。所述的低沸點(diǎn)液體可以是烷烴、烯烴、炔烴、二烯烴、醇、醛、醚、酯、鹵代烴等沸點(diǎn)適宜的有機(jī)物中的一種或幾種,優(yōu)選為烷烴、醇、酯等與原料有較好的互溶性、無特殊氣味且無毒副作用的物質(zhì)。所述的低沸點(diǎn)液體的加入量占原料蠟膏的0.1%~5.0%(重量),優(yōu)選的比例為0.3%~2.0%。在降溫的低溫恒溫過程和升溫及恒溫的發(fā)汗過程中可以回收低沸點(diǎn)液體。本發(fā)明的方法中,所述的發(fā)汗裝置一般為發(fā)汗皿,并在蠟層以上增加可拆卸的密封系統(tǒng)及加壓裝置,以保證在加料和冷卻過程中保持低沸點(diǎn)液體處于液體狀態(tài),所述的壓力(表壓)為0.5~20.0個(gè)大氣壓,優(yōu)選為1.0~10.0個(gè)大氣壓。本發(fā)明的方法中,所述的發(fā)汗皿在蠟層以上增加加壓裝置和/或在蠟層以下增加真空裝置。所述的強(qiáng)制氣流通過蠟層采用在蠟層上方增加壓力(氣壓)和/或在蠟層下方降低壓力(氣壓),使蠟層上、下方形成壓力差實(shí)現(xiàn)。所述的壓力差一般為0.1~5.0個(gè)大氣壓,優(yōu)選為0.2~1.5個(gè)大氣壓,以強(qiáng)制氣流通過蠟層。本發(fā)明的方法中,步驟(3)中所述的降溫過程在高溫恒溫段之前的降溫速率優(yōu)選1.5℃/h~2.5℃/h。本發(fā)明的方法中,步驟(3)中所述的降溫過程的高溫恒溫段的適當(dāng)溫度為原料(過程(二)所得餾分)熔點(diǎn)-1.0℃~熔點(diǎn)+2.0℃,優(yōu)選為原料熔點(diǎn)~熔點(diǎn)+1.0℃。冷卻降溫過程的高溫恒溫段的時(shí)間為0~4.0小時(shí),優(yōu)選為0.1~4.0小時(shí),最優(yōu)選為1.0~4.0小時(shí)。本發(fā)明的方法中,步驟(3)中所述的降溫過程在高溫恒溫段之后的降溫速率優(yōu)選1.0℃/h~2.0℃/h。本發(fā)明的方法中,步驟(3)所述的預(yù)定溫度(即降溫終止溫度)優(yōu)選為原料熔點(diǎn)以下8℃~15℃。本發(fā)明的方法中,步驟(3)所述的冷卻降溫至預(yù)定溫度后,增加低溫恒溫階段以使固體結(jié)晶更充分,同時(shí)逐漸減低壓力至常壓。冷卻降溫過程的低溫恒溫階段的時(shí)間為0~3.0小時(shí),優(yōu)選為0.1~3.0小時(shí),最優(yōu)選為1.0~3.0小時(shí)。本發(fā)明的方法中,步驟(4)中所述升溫的速率優(yōu)選1.0℃/h~2.0℃/h。所述升溫的預(yù)定溫度(即終止溫度)為目的產(chǎn)品標(biāo)稱溫度~標(biāo)稱溫度+10℃。本發(fā)明的方法中,步驟(4)中升溫發(fā)汗至制取產(chǎn)品的預(yù)定溫度后,增加恒溫階段以使固態(tài)組分與液態(tài)組分分離更充分,恒溫階段的時(shí)間為0~5.0小時(shí),優(yōu)選為0.1~5.0小時(shí),最優(yōu)選為1.0~5.0小時(shí)。本發(fā)明的方法中,所述蠟層的升溫速度和降溫速度,可以通過空氣浴、水浴、油浴或者其他可行的方式進(jìn)行控制,優(yōu)選采用水浴或油浴進(jìn)行控制。采用水浴或油浴方式控制蠟層升溫速率和降溫速率時(shí),可在發(fā)汗皿外增加夾套,夾套與可移動(dòng)盤管及循環(huán)系統(tǒng)相連,循環(huán)系統(tǒng)具有程序降溫/加熱功能,以水或?qū)嵊偷任镔|(zhì)作為循環(huán)介質(zhì);增加盤管可使蠟層升/降溫過程更快、蠟層溫度更均勻。本發(fā)明的方法中,所述的強(qiáng)制氣流通過蠟層可以在發(fā)汗過程任意階段實(shí)施,優(yōu)選在升溫初期實(shí)施。本發(fā)明的方法中,所述的強(qiáng)制氣流通過蠟層是采用在蠟層上方增加壓力(氣壓)實(shí)現(xiàn)的,如在蠟層上方施加的壓力為0.2~1.5個(gè)大氣壓(表壓),而蠟層下方保持為常壓。本發(fā)明的方法中,所述的強(qiáng)制氣流通過蠟層是采用在蠟層下方降低壓力(氣壓)實(shí)現(xiàn)的,如在蠟層上方保持常壓,而在蠟層下方維持-0.2~-0.8個(gè)大氣壓(表壓)的壓力。本發(fā)明的方法中,所述的發(fā)汗裝置連接回收系統(tǒng),以回收低沸點(diǎn)液體。回收系統(tǒng)可以采用液體吸收或冷凍系統(tǒng)等多種可行的方式,優(yōu)選為液體吸收系統(tǒng)。商品石油蠟直接用作節(jié)溫器用蠟介質(zhì)時(shí),會(huì)導(dǎo)致大循環(huán)開啟過早且控溫范圍內(nèi)推桿行程較小,這是由商品石油蠟的化學(xué)組成引起的,即商品石油蠟的碳數(shù)分布較寬且含有較多的異構(gòu)烷烴和環(huán)烷烴。由于商品石油蠟碳數(shù)分布較寬,即含有較多的低分子量的成分,低分子量成分的熔點(diǎn)低于節(jié)溫器的控溫范圍,這些成分會(huì)提前熔化而產(chǎn)生體積膨脹,導(dǎo)致大循環(huán)開啟過早;同時(shí)由于商品石油蠟含有較多的異構(gòu)烷烴和環(huán)烷烴(一般異構(gòu)烷烴和環(huán)烷烴的膨脹系數(shù)小于正構(gòu)烷烴),這就會(huì)使在節(jié)溫器控溫范圍內(nèi)推桿的行程較小,導(dǎo)致大循環(huán)的水量不足。低溫F-T合成產(chǎn)物的重組分主要為正構(gòu)烷烴,但是還含有一定量的烯烴和含氧化合物,而且碳數(shù)分布比商品石油蠟還要寬很多,該產(chǎn)物本身不適宜直接作為節(jié)溫器用蠟介質(zhì)。所以商品石油蠟和F-T合成產(chǎn)物都必須經(jīng)分離提純才能用作節(jié)溫器用蠟介質(zhì)。普通發(fā)汗工藝是利用蠟和油熔點(diǎn)不同的性質(zhì)進(jìn)行分離生產(chǎn)蠟產(chǎn)品的,但是對(duì)于熔點(diǎn)在70℃左右的蠟產(chǎn)品,由于原料化學(xué)組成復(fù)雜,導(dǎo)致結(jié)晶時(shí)晶體結(jié)構(gòu)更加細(xì)小致密,對(duì)液態(tài)組分的排出形成巨大的濾流阻力,這就造成僅靠重力自然分離的普通發(fā)汗過程中固態(tài)組分與液態(tài)組分難以完全分離。因此普通發(fā)汗脫油工藝不能生產(chǎn)熔點(diǎn)在70℃以上的節(jié)溫器用蠟介質(zhì)產(chǎn)品。本發(fā)明為了生產(chǎn)高性能的節(jié)溫器用蠟介質(zhì),通過對(duì)節(jié)溫器用蠟介質(zhì)使用性能與其化學(xué)組成的關(guān)系和F-T合成產(chǎn)物的組成的深入研究,針對(duì)低溫F-T合成產(chǎn)物含有一定量的烯烴和含氧化合物,且碳數(shù)分布非常寬是造成低溫F-T合成產(chǎn)物不能滿足節(jié)溫器用蠟介質(zhì)產(chǎn)品技術(shù)要求的原因,通過選擇適當(dāng)?shù)拇呋瘎┖头磻?yīng)條件,將低溫F-T合成產(chǎn)物中的烯烴和含氧化合物等非適宜組分轉(zhuǎn)化為正構(gòu)烷烴;并通過減壓蒸餾對(duì)目的組分富集;再通過發(fā)汗降低碳數(shù)分布寬度以使產(chǎn)物的性能滿足節(jié)溫器用蠟介質(zhì)的技術(shù)要求。本發(fā)明為了使發(fā)汗這種無溶劑分離方法可以生產(chǎn)熔點(diǎn)在70℃以上的節(jié)溫器用蠟介質(zhì),針對(duì)普通發(fā)汗過程中固態(tài)組分與液態(tài)組分難以分離原因,通過在發(fā)汗過程中采用強(qiáng)制氣流通過蠟層攜帶出液態(tài)組分的方法,同時(shí)還優(yōu)選原料加熱熔化后在壓力條件下?lián)饺氲头悬c(diǎn)液體,并在冷卻降溫過程中增加高溫恒溫階段、降溫過程的低溫恒溫階段和升溫發(fā)汗至預(yù)設(shè)溫度后的恒溫階段等過程。這些措施有效地降低了產(chǎn)物碳分布的寬度并提高正構(gòu)烷烴含量,使產(chǎn)物的性能能夠滿足節(jié)溫器用蠟介質(zhì)的技術(shù)要求。針對(duì)普通發(fā)汗過程的研究表明,在發(fā)汗過程中,液態(tài)組分是順著結(jié)晶部分逐漸排出的,類似于液體在毛細(xì)管中流動(dòng)的情況。由于熔點(diǎn)在70℃以上的蠟細(xì)小致密的結(jié)晶結(jié)構(gòu),會(huì)使對(duì)液態(tài)組分形成的濾流阻力急劇增大,這就導(dǎo)致僅靠重力自然分離過程的普通發(fā)汗過程不能生產(chǎn)熔點(diǎn)在70℃以上的節(jié)溫器用蠟介質(zhì)產(chǎn)品。在降溫過程中增加高溫恒溫階段可以使蠟的結(jié)晶更大,利于發(fā)汗過程中液態(tài)組分的排出。針對(duì)蠟結(jié)晶過程的研究表明,其化學(xué)組成是決定結(jié)晶形態(tài)的最主要因素,同時(shí)冷卻過程的條件也會(huì)影響結(jié)晶形態(tài),尤其是在熔點(diǎn)附近的溫度下的冷卻條件對(duì)結(jié)晶形態(tài)的影響最明顯。熔點(diǎn)在70℃以上的蠟在冷卻到熔點(diǎn)附近時(shí),較大分子量的正構(gòu)烷烴已形成結(jié)晶析出,這部分結(jié)晶體可以作為后續(xù)形成結(jié)晶的晶核,此時(shí)增加高溫恒溫階段,可以使晶核能夠充分增長(zhǎng),形成更大尺寸的晶體,這種更大尺寸的晶體雖然不如低熔點(diǎn)石蠟的結(jié)晶那樣粗大,但這種增大的晶體結(jié)構(gòu)對(duì)發(fā)汗階段排出液態(tài)組分也是十分有利的。原料加熱熔化后在壓力條件下?lián)饺氲头悬c(diǎn)液體,同時(shí)在發(fā)汗過程中強(qiáng)制氣流通過蠟層也有利于發(fā)汗過程中液態(tài)組分的排出。原料加熱熔化后摻入的低沸點(diǎn)液體,在壓力條件下的沸點(diǎn)高于此時(shí)原料的溫度而呈液體狀態(tài),并且由于與原料有較好的互溶性而均勻分散在原料中;保持壓力下原料冷卻至熔點(diǎn)以下8℃~15℃并恒溫0.1~3.0h以使蠟層結(jié)晶更充分;同時(shí)在恒溫過程中逐漸降低壓力至常壓,此時(shí)原料處于較軟的固體狀態(tài),并且溫度高于低沸點(diǎn)液體常壓下的沸點(diǎn)(或泡點(diǎn)),低沸點(diǎn)液體隨壓力緩慢下降而逐漸汽化(或在其后的升溫發(fā)汗過程中逐漸汽化),會(huì)在蠟層內(nèi)形成均勻分散的微小氣泡,這些微小氣泡形成的空間在發(fā)汗過程中易于在蠟層中形成若干細(xì)小的通道,從而有利于發(fā)汗過程中液態(tài)組分的排出。同時(shí)在升溫及恒溫的發(fā)汗過程中利用氣流通過蠟層攜帶出液態(tài)組分的方法強(qiáng)制液態(tài)組分與固態(tài)組分分離,增強(qiáng)了分離效果并加快了分離速度。再輔以冷卻過程的低溫恒溫階段使固體結(jié)晶更充分,以及發(fā)汗過程的恒溫階段使固態(tài)組分與液態(tài)組分分離更充分等方法,使得發(fā)汗工藝可以生產(chǎn)碳數(shù)分布范圍窄且正構(gòu)烷烴含量高的節(jié)溫器用蠟介質(zhì)。本發(fā)明的優(yōu)點(diǎn)是:通過選擇適當(dāng)?shù)拇呋瘎┖头磻?yīng)條件,將原料中的烯烴及含氧化合物通過加氫方法轉(zhuǎn)化為節(jié)溫器用蠟介質(zhì)的適宜組分(正構(gòu)烷烴),同時(shí)不產(chǎn)生其它雜質(zhì)。然后通過蒸餾富集目的組分。在發(fā)汗過程中采用氣流通過蠟層攜帶出液態(tài)組分的方法,增強(qiáng)了固態(tài)組分與液態(tài)組分的分離效果并加快了分離速度;而利用低沸點(diǎn)液體汽化在蠟層中形成均勻分散的微小氣泡,更加有利于液態(tài)組分的快速排出。從而以F-T合成產(chǎn)物為原料采用發(fā)汗工藝可以生產(chǎn)碳數(shù)分布范圍較窄且正構(gòu)烷烴含量高的蠟產(chǎn)品,這些產(chǎn)品可以用作節(jié)溫器用蠟介質(zhì)。本發(fā)明方法裝置投資低、生產(chǎn)過程無溶劑污染環(huán)境。附圖說明圖1是利用本發(fā)明實(shí)施例1制備的節(jié)溫器用蠟介質(zhì)(Ⅰ)、(Ⅱ)制備的節(jié)溫器推桿的行程性能曲線。圖2利用本發(fā)明實(shí)施例2制備的節(jié)溫器用蠟介質(zhì)(Ⅲ)、(Ⅳ)制備的節(jié)溫器推桿的行程性能曲線。圖中橫坐標(biāo)為溫度,縱坐標(biāo)為行程。具體實(shí)施方式本發(fā)明通過選用適宜的低溫F-T合成產(chǎn)物為原料,經(jīng)加氫轉(zhuǎn)化、減壓蒸餾、發(fā)汗等工藝過程生產(chǎn)熔點(diǎn)在70℃以上的節(jié)溫器用蠟介質(zhì)。具體為低溫F-T合成產(chǎn)物在催化劑作用下進(jìn)行加氫轉(zhuǎn)化;加氫產(chǎn)物在蒸餾裝置中制取適宜餾程的餾分;發(fā)汗皿上部連接可拆卸的密封裝置并與加壓緩沖罐和壓縮機(jī)連接,和/或在發(fā)汗皿下部連接減壓緩沖罐和真空泵;以水浴或油浴控制蠟層升、降溫速度;發(fā)汗皿外增加夾套,夾套與可移動(dòng)盤管和循環(huán)系統(tǒng)相連,循環(huán)系統(tǒng)具有程序降溫/加熱功能;以蒸餾制備的餾分為原料,加熱熔化并優(yōu)選在壓力條件下?lián)饺氲头悬c(diǎn)液體后裝入發(fā)汗皿;保持壓力下使蠟層溫度降至原料熔點(diǎn)溫度附近并高溫恒溫一段時(shí)間;繼續(xù)降低蠟層溫度至設(shè)定溫度并低溫恒溫一段時(shí)間,恒溫過程中逐漸降低原料蠟層以上的壓力至常壓;在發(fā)汗過程中,啟動(dòng)壓縮機(jī)以在蠟層以上形成正壓,和/或啟動(dòng)真空泵以在蠟層以下形成負(fù)壓,用以強(qiáng)制氣流通過蠟層;蠟層溫度達(dá)到預(yù)設(shè)溫度并恒溫一段時(shí)間后停止發(fā)汗過程;蠟上經(jīng)精制、成型、包裝后即為節(jié)溫器用蠟介質(zhì)產(chǎn)品。以下通過實(shí)施例1-2具體說明本發(fā)明的以F-T合成產(chǎn)物生產(chǎn)節(jié)溫器用蠟介質(zhì)的方法。實(shí)施例1本實(shí)施例包括:(一)加氫轉(zhuǎn)化、(二)蒸餾、(三)發(fā)汗三部分。(一)加氫轉(zhuǎn)化以中國(guó)石油化工股份有限公司低溫F-T合成實(shí)驗(yàn)裝置的蠟油產(chǎn)物(正構(gòu)烷烴重量含量為95.0%)為原料,在FHJ-2催化劑(一種Ni/Al2O3商業(yè)催化劑,撫順石油化工研究院研制生產(chǎn),以氧化物計(jì)活性金屬鎳含量為40%,催化劑在使用前進(jìn)行常規(guī)還原處理)作用下在反應(yīng)壓力5.0MPa、反應(yīng)溫度200℃、體積空速1.0h-1和氫液體積比500:1的條件下進(jìn)行加氫以轉(zhuǎn)化其中的烯烴和含氧化合物,加氫產(chǎn)物中正構(gòu)烷烴重量含量97.36%。(二)蒸餾將上述經(jīng)加氫轉(zhuǎn)化所得產(chǎn)物在接近2塊理論塔板的減壓蒸餾裝置中,在13.3Pa~133Pa之間壓力條件下,制備470℃~530℃的餾分。470℃~530℃餾分熔點(diǎn)71.1℃,收率8.03%(相對(duì)于蠟油原料),針入度(25℃)12(0.1mm)。(三)發(fā)汗本部分包括:(1)準(zhǔn)備工作、(2)裝料、(3)降溫—高溫恒溫—降溫—低溫恒溫結(jié)晶、(4)升溫—恒溫發(fā)汗、(5)發(fā)汗裝置清理、(6)產(chǎn)品精制和成型、包裝等過程。(1)準(zhǔn)備工作將發(fā)汗皿夾套和可移動(dòng)盤管與具有程序制冷/加熱功能的循環(huán)系統(tǒng)連接,將盤管固定在發(fā)汗皿上;以水為介質(zhì);啟動(dòng)循環(huán)系統(tǒng)的加熱功能,使循環(huán)水介質(zhì)升溫至75℃。發(fā)汗皿皿板下部墊水;發(fā)汗皿下部連接減壓緩沖罐和真空泵。(2)裝料以(二)部分蒸餾制備的470℃~530℃餾分為原料,加熱至75℃熔化后加入發(fā)汗皿。安裝發(fā)汗皿上部的密封系統(tǒng)并與加壓緩沖罐和壓縮機(jī)連接好;啟動(dòng)壓縮機(jī)并保持加壓緩沖罐內(nèi)壓力穩(wěn)定在5.0~5.2個(gè)大氣壓(表壓)。(3)降溫—高溫恒溫—降溫—低溫恒溫結(jié)晶啟動(dòng)循環(huán)系統(tǒng)的制冷功能,以2.0℃/h的降溫速率使蠟層溫度下降至72.0℃并恒溫2.0小時(shí)進(jìn)行高溫恒溫,以使結(jié)晶充分增長(zhǎng);再以1.5℃/h的降溫速率使蠟層溫度下降至60.0℃以使蠟層結(jié)晶形成固體,并恒溫2.0小時(shí)進(jìn)行低溫恒溫,以使結(jié)晶更充分。低溫恒溫階段通過排空系統(tǒng)控制加壓緩沖罐內(nèi)壓力逐漸降低至常壓。關(guān)閉循環(huán)系統(tǒng)的制冷功能。(4)升溫—恒溫發(fā)汗排出發(fā)汗皿墊水。發(fā)汗皿出口連接蠟下儲(chǔ)罐;啟動(dòng)壓縮機(jī)并保持加壓緩沖罐內(nèi)壓力穩(wěn)定在1.0~1.2個(gè)大氣壓(表壓),而在蠟層下方保持為常壓;啟動(dòng)循環(huán)系統(tǒng)加熱功能,以1.5℃/h的升溫速率使蠟層溫度升高到73.0℃并恒溫4.0小時(shí)以使蠟層中的固態(tài)組分與液態(tài)組分充分分離。發(fā)汗皿出口換接粗產(chǎn)品儲(chǔ)罐(Ⅰ),并保持緩沖罐內(nèi)壓力穩(wěn)定在1.0~1.2個(gè)大氣壓(表壓),發(fā)汗皿皿板下方保持常壓;繼續(xù)以1.0℃/h的升溫速率使蠟層溫度升高到75.0℃并恒溫4.0小時(shí)以使蠟層中的固態(tài)組分與液態(tài)組分充分分離;停壓縮機(jī)。發(fā)汗皿出口換接粗產(chǎn)品儲(chǔ)罐(Ⅱ);開啟真空泵并保持緩沖罐內(nèi)壓力穩(wěn)定在-0.4~-0.6大氣壓(表壓),蠟層上方保持常壓;以1.0℃/h的升溫速率使蠟層溫度升高到77.0℃并恒溫4.0小時(shí)以使蠟層中的固態(tài)組分與液態(tài)組分充分分離。停真空泵,終止發(fā)汗過程。(5)發(fā)汗裝置清理發(fā)汗皿出口換接蠟上儲(chǔ)罐;繼續(xù)升高循環(huán)水的溫度到90℃熔化取出蠟上,以清理發(fā)汗裝置。(6)產(chǎn)品精制和成型、包裝粗產(chǎn)品(Ⅰ)、(Ⅱ)分別經(jīng)白土精制、成型和包裝后即為節(jié)溫器用蠟介質(zhì)產(chǎn)品(Ⅰ)和產(chǎn)品(Ⅱ)。節(jié)溫器用蠟介質(zhì)產(chǎn)品(Ⅰ)性質(zhì):熔點(diǎn)74.4℃。節(jié)溫器用蠟介質(zhì)產(chǎn)品(Ⅰ)的收率為11.25%(相對(duì)于原料470℃~530℃餾分)。由節(jié)溫器用蠟介質(zhì)產(chǎn)品(Ⅰ)制備的節(jié)溫器產(chǎn)品推桿的行程—溫度關(guān)系如圖1中曲線(Ⅰ)所示。從圖1中曲線(Ⅰ)可以看出,節(jié)溫器推桿行程在72℃時(shí)行程小于1mm,70℃~80℃間行程大于8mm,符合標(biāo)稱溫度為70℃節(jié)溫器的技術(shù)要求。節(jié)溫器用蠟介質(zhì)產(chǎn)品(Ⅱ)性質(zhì):熔點(diǎn)76.2℃。節(jié)溫器用蠟介質(zhì)產(chǎn)品(Ⅱ)的收率為12.28%(相對(duì)于原料470℃~530℃餾分)。由節(jié)溫器用蠟介質(zhì)產(chǎn)品(Ⅱ)制備的節(jié)溫器產(chǎn)品推桿的行程—溫度關(guān)系如圖1中曲線(Ⅱ)所示。從圖1中曲線(Ⅱ)可以看出,節(jié)溫器推桿行程在74℃時(shí)行程小于1mm,72℃~82℃間行程大于8mm,符合標(biāo)稱溫度為72℃節(jié)溫器的技術(shù)要求。實(shí)施例2本實(shí)施例包括:(一)加氫轉(zhuǎn)化、(二)蒸餾、(三)發(fā)汗三部分。(一)加氫轉(zhuǎn)化同實(shí)施例1。(二)蒸餾同實(shí)施例1。(三)發(fā)汗本部分包括:(1)準(zhǔn)備工作、(2)裝料、(3)降溫—高溫恒溫—降溫—低溫恒溫結(jié)晶、(4)升溫—恒溫發(fā)汗、(5)發(fā)汗裝置清理、(6)產(chǎn)品精制和成型、包裝等過程。(1)準(zhǔn)備工作將發(fā)汗皿夾套和可移動(dòng)盤管與具有程序制冷/加熱功能的循環(huán)系統(tǒng)連接,將盤管固定在發(fā)汗皿上;以水為介質(zhì);啟動(dòng)循環(huán)系統(tǒng)的加熱功能,使循環(huán)水介質(zhì)升溫至75℃。發(fā)汗皿皿板下部墊水。安裝發(fā)汗皿上部的密封系統(tǒng)并與加壓緩沖罐和壓縮機(jī)連接好,將加壓緩沖罐排空系統(tǒng)和發(fā)汗皿下部排氣口分別與回收系統(tǒng)連接好,以液體石蠟為吸收介質(zhì)。在發(fā)汗皿下部連接減壓緩沖罐和真空泵。(2)裝料以實(shí)施例1中第(二)部分蒸餾制備的470℃~530℃餾分為原料,加熱至75℃熔化后在5.0~5.2個(gè)大氣壓(表壓)下?lián)饺?.0%的甲酸乙酯,再加入發(fā)汗皿;保持加壓緩沖罐內(nèi)壓力穩(wěn)定在5.0~5.2個(gè)大氣壓(表壓)。(3)降溫—高溫恒溫—降溫—低溫恒溫結(jié)晶啟動(dòng)循環(huán)系統(tǒng)的制冷功能,以2.0℃/h的降溫速率使蠟層溫度下降至72.0℃并恒溫2.0小時(shí)進(jìn)行高溫恒溫,以使結(jié)晶充分增長(zhǎng);再以1.5℃/h的降溫速率使蠟層溫度下降至60.0℃以使蠟層結(jié)晶形成固體,并恒溫2.0小時(shí)進(jìn)行低溫恒溫,以使結(jié)晶更充分。低溫恒溫階段通過排空系統(tǒng)控制加壓緩沖罐內(nèi)壓力逐漸降低至常壓。排出的氣體通過液體石蠟以回收低沸點(diǎn)液體甲酸乙酯。關(guān)閉循環(huán)系統(tǒng)的制冷功能。(4)升溫—恒溫發(fā)汗排出發(fā)汗皿墊水。發(fā)汗皿出口連接蠟下儲(chǔ)罐;啟動(dòng)壓縮機(jī)并保持加壓緩沖罐內(nèi)壓力穩(wěn)定在1.0~1.2個(gè)大氣壓(表壓),而在蠟層下方保持為常壓;啟動(dòng)循環(huán)系統(tǒng)加熱功能,以1.5℃/h的升溫速率使蠟層溫度升高到73.0℃并恒溫4.0小時(shí)以使蠟層中的固態(tài)組分與液態(tài)組分充分分離。發(fā)汗皿出口換接粗產(chǎn)品儲(chǔ)罐(Ⅲ),并保持緩沖罐內(nèi)壓力穩(wěn)定在1.0~1.2個(gè)大氣壓(表壓),發(fā)汗皿皿板下方保持常壓;繼續(xù)以1.0℃/h的升溫速率使蠟層溫度升高到75.0℃并恒溫4.0小時(shí)以使蠟層中的固態(tài)組分與液態(tài)組分充分分離;停壓縮機(jī)。發(fā)汗皿出口換接粗產(chǎn)品儲(chǔ)罐(Ⅳ);開啟真空泵并保持緩沖罐內(nèi)壓力穩(wěn)定在-0.4~-0.6大氣壓(表壓),蠟層上方保持常壓;以1.0℃/h的升溫速率使蠟層溫度升高到77.0℃并恒溫4.0小時(shí)以使蠟層中的固態(tài)組分與液態(tài)組分充分分離。停真空泵,終止發(fā)汗過程。升溫及恒溫的發(fā)汗過程中排出的氣體通過液體石蠟以回收低沸點(diǎn)液體甲酸乙酯。(5)發(fā)汗裝置清理發(fā)汗皿出口換接蠟上儲(chǔ)罐;繼續(xù)升高循環(huán)水的溫度到90℃熔化取出蠟上,以清理發(fā)汗裝置。(6)產(chǎn)品精制和成型、包裝。粗產(chǎn)品(Ⅲ)、(Ⅳ)分別經(jīng)白土精制、成型和包裝后即為節(jié)溫器用蠟介質(zhì)產(chǎn)品(Ⅲ)和產(chǎn)品(Ⅳ)。節(jié)溫器用蠟介質(zhì)產(chǎn)品(Ⅲ)性質(zhì):熔點(diǎn)74.6℃。節(jié)溫器用蠟介質(zhì)產(chǎn)品(Ⅲ)的收率為12.61%(相對(duì)于原料470℃~530℃餾分)。由節(jié)溫器用蠟介質(zhì)產(chǎn)品(Ⅲ)制備的節(jié)溫器產(chǎn)品推桿的行程—溫度關(guān)系如圖2中曲線(Ⅲ)所示。從圖2中曲線(Ⅲ)可以看出,節(jié)溫器推桿行程在72℃時(shí)行程小于1mm,70℃~80℃間行程大于8mm,符合標(biāo)稱溫度為70℃節(jié)溫器的技術(shù)要求。節(jié)溫器用蠟介質(zhì)產(chǎn)品(Ⅳ)性質(zhì):熔點(diǎn)76.7℃。節(jié)溫器用蠟介質(zhì)產(chǎn)品(Ⅳ)的收率為13.15%(相對(duì)于原料470℃~530℃餾分)。由節(jié)溫器用蠟介質(zhì)產(chǎn)品(Ⅳ)制備的節(jié)溫器產(chǎn)品推桿的行程—溫度關(guān)系如圖2中曲線(Ⅳ)所示。從圖2中曲線(Ⅳ)可以看出,節(jié)溫器推桿行程在74℃時(shí)行程小于1mm,72℃~82℃間行程大于8mm,符合標(biāo)稱溫度為72℃節(jié)溫器的技術(shù)要求。通過實(shí)施例1-2可以看出,本發(fā)明以F-T合成產(chǎn)物生產(chǎn)節(jié)溫器用蠟介質(zhì)的方法,通過選擇適當(dāng)?shù)拇呋瘎┖头磻?yīng)條件,將原料中的烯烴及含氧化合物轉(zhuǎn)化為節(jié)溫器用蠟介質(zhì)的適宜組分;再通過蒸餾富集目的組分;通過在發(fā)汗過程中采用氣流通過蠟層攜帶出液態(tài)組分的方法強(qiáng)制液態(tài)組分與固態(tài)組分分離,增強(qiáng)了分離效果;利用低沸點(diǎn)液體汽化在蠟層中形成均勻分散的微小氣泡也有利于液態(tài)組分的快速排出,從而以F-T合成產(chǎn)物為原料,使用發(fā)汗這種無溶劑分離方法生產(chǎn)出碳數(shù)分布范圍較窄且正構(gòu)烷烴含量較高的蠟產(chǎn)品,可以用作節(jié)溫器用蠟介質(zhì)。