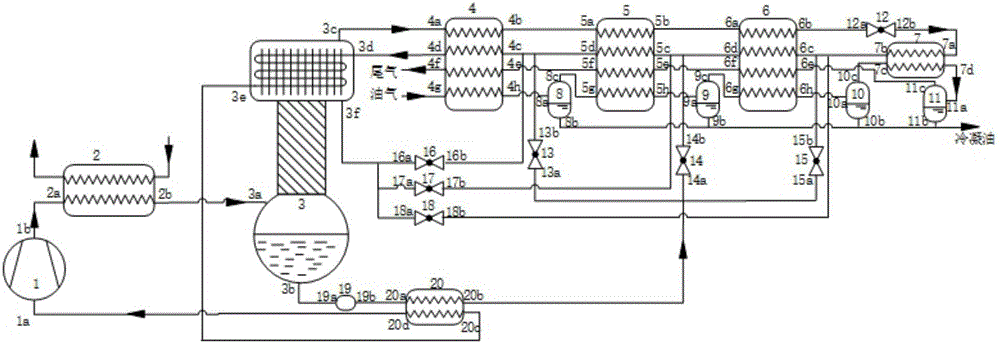
本發(fā)明涉及油氣分離
技術領域:
,尤其涉及一種精餾型自復疊低溫冷凝的油氣分離系統(tǒng)。
背景技術:
:油庫、加油站、石化加工等場所中儲存的一些油品中含有大量易揮發(fā)的輕烴組分,易在儲運過程中揮發(fā)并混合在空氣中,造成油品損耗、環(huán)境污染和安全隱患。所以有必要對這些場所中的含油空氣進行處理。國標GB20950-2007《儲油庫大氣污染物排放標準》和GB20952-2007《加油站大氣污染物排放標準》等規(guī)范中,均明確規(guī)定排放的油氣中非甲烷總烴含量應不大于25g/cm3。在油氣分離領域中,冷凝法由于其可分離出較純凈的產(chǎn)品,適合于較高濃度烴蒸汽的分離回收,受到人們的關注。最初人們普遍采用復疊制冷循環(huán)來營造低溫冷凝油氣,即采用不同制冷劑運行在多個制冷循環(huán)中獲得不同的溫度位以冷凝不同沸點的烴組分。但是復疊制冷系統(tǒng)所需設備多,逐漸被混合制冷劑制冷循環(huán)而替代。通常,混合制冷劑油氣分離系統(tǒng)采用了自復疊制冷循環(huán)的思想,制冷劑的循環(huán)中采用了多級分離,以便高低沸點的制冷劑分離更完全;同時,一般的中小型系統(tǒng)因成本考慮會使用普通的油潤滑壓縮機,多級分離可將制冷劑帶出的潤滑油冷凝下來,避免其進入低溫段堵塞節(jié)流裝置。但是分離級的增多導致系統(tǒng)的結構復雜化,變工況性能變差。特別是對于小型、微型規(guī)模的油氣分離系統(tǒng),結構簡單非常重要。中國專利ZL02110664.9提出一種精餾型混合制冷劑深度制冷裝置,采用一個精餾裝置來替代多個氣液分離器,以實現(xiàn)傳統(tǒng)混合制冷劑制冷裝置中分離高低沸點制冷劑和冷凝壓縮機潤滑油的目的,減小了系統(tǒng)的復雜度,也具有較高的效率。但是,該裝置能達到的制冷溫度并不是很低,裝置結構比較復雜。公告號為CN102141317A的中國專利文獻公開了一種精餾型自復疊氣體液化系統(tǒng),包括壓縮機、冷凝器、精餾裝置以及原料氣液化回路;壓縮機出料口與冷凝器進料口相連,冷凝器的出料口與精餾裝置釜中進料口相連,精餾裝置包括精餾塔以及與精餾塔精餾段頂部連通的塔頂換熱器,塔頂換熱器頂部的出料口與原料氣液化回路相連,原料氣穿過原料氣液化回路得到最終液化產(chǎn)品。該發(fā)明利用精餾裝置代替?zhèn)鹘y(tǒng)混合工質氣體液化系統(tǒng)的多級分離過程,并利用從精餾裝置底部和頂部引出的不同成分的高壓液體分別減壓進入原料氣液化回路中,優(yōu)化匹配原料氣降溫液化過程中的水當量變化,來逐段冷卻原料氣,具有結構簡單、運行可靠和系統(tǒng)液化效率高等優(yōu)點,特別適用于各種小型和微型氣體液化系統(tǒng)。然而,該裝置適用范圍有限,只適用于需要將原料氣全部液化的場合;而在處理含油空氣的場合中,只需要將油盡可能冷凝液化下來,而空氣是不需要被液化的,所以該裝置不適用于油氣分離領域。技術實現(xiàn)要素:針對現(xiàn)有技術存在的不足,本發(fā)明提供了一種精餾型自復疊低溫冷凝的油氣分離系統(tǒng),該系統(tǒng)結構簡單,運行可靠,用一臺普通的油潤滑壓縮機即能完成分離尾氣中的烴組分,使排放物濃度滿足國標要求,特別適合油庫、加油站、石化工廠等場所的揮發(fā)性油氣的處理。本發(fā)明的技術方案如下:一種精餾型自復疊低溫冷凝的油氣分離系統(tǒng),包括壓縮機、冷凝器、精餾裝置、以及油氣冷凝分離回路;所述的壓縮機出口與冷凝器進口相連;所述的冷凝器出口與精餾裝置進口相連;所述的精餾裝置包括精餾柱以及與精餾柱頂部相連的柱頂換熱器,柱頂換熱器頂部出口與油氣冷凝分離回路相連,所述的油氣冷凝分離回路包括第一換熱器單元、第二換熱器單元、第一節(jié)流元件和分離器單元;所述的第一換熱器單元包括第一換熱器、第二換熱器和第三換熱器中的一者或幾者的組合;所述的第一節(jié)流元件設置于第一換熱器單元和第二換熱器單元之間;所述的第二換熱器單元包含蒸發(fā)器;所述的分離器單元包括第一分離器、第二分離器、第三分離器和第四分離器中的一者或幾者的組合;所述的第一換熱器、第二換熱器、第三換熱器內均設有一個正流制冷劑管道、一個返流制冷劑管道、一個油氣管道和一個尾氣管道;所述的蒸發(fā)器內設有一個制冷劑管道和一個油氣管道;所述的精餾裝置的柱頂換熱器內設有冷卻管道;所述的第一分離器、第二分離器、第三分離器和第四分離器均設有氣相出口和液相出口;所述的柱頂換熱器頂部出口與第一換熱器的正流制冷劑管道進口相連;所述的第一換熱器的正流制冷劑管道出口與第二換熱器的正流制冷劑管道進口相連;所述的第二換熱器的正流制冷劑管道出口與第三換熱器的正流制冷劑管道進口相連;所述的第三換熱器的正流制冷劑管道出口與第一節(jié)流元件的進口相連,第一節(jié)流元件的出口與蒸發(fā)器的制冷劑管道進口相連;所述蒸發(fā)器的制冷劑管道出口與第三換熱器的返流制冷劑管道進口相連;所述的第三換熱器的返流制冷劑管道出口與第二換熱器的返流制冷劑管道進口相連;所述的第二換熱器的返流制冷劑管道出口與第一換熱器的返流制冷劑管道進口相連;所述的第一換熱器的返流制冷劑管道出口與精餾裝置的柱頂換熱器冷卻管道的進口相連;所述的柱頂換熱器冷卻管道的出口與壓縮機的吸氣口連通;所述的第一換熱器的油氣管道出口與第一分離器的進口相連;所述的第一分離器的氣相出口與第二換熱器的油氣管道進口相連;所述的第二換熱器的油氣管道出口與第二分離器的進口相連;所述的第二分離器的氣相出口與第三換熱器的油氣管道進口相連;所述的第三換熱器的油氣管道出口與第三分離器的進口相連;所述的第三分離器的氣相出口與蒸發(fā)器的油氣管道進口相連;所述的蒸發(fā)器的油氣管道出口與第四分離器的進口相連;所述的第四分離器的氣相出口與第三換熱器的尾氣管道進口相連;所述的第三換熱器的尾氣管道出口與第二換熱器的尾氣管道進口相連;所述的第二換熱器的尾氣管道出口與第一換熱器的尾氣管道進口相連;所述精餾裝置的底部出口通過三條支路分別與第一換熱器、第二換熱器和第三換熱器的返流制冷劑管道的進口相連;所述的三條支路上分別設有一個節(jié)流元件;所述柱頂換熱器的底部出口通過三條支路管道分別與第一換熱器、第二換熱器和第三換熱器的返流制冷劑管道的進口相連,所述的三條支路管道上分別設有一個節(jié)流元件。在上述油氣冷凝處理回路中,油氣首先從第一換熱器的油氣管道進口進入冷凝分離回路,第一換熱器的油氣管道出口與第一分離器的進口相連,經(jīng)過第一分離器的氣液分離過程,第一分離器的氣相出口與第二換熱器油氣管道進口相連,第二換熱器的油氣管道出口與第二分離器的進口相連,經(jīng)過第二分離器的氣液分離過程,第二分離器的氣相出口與第三換熱器油氣管道進口相連;第三換熱器的油氣管道出口與第三分離器的進口相連,經(jīng)過第三分離器的氣液分離過程,第三分離器的氣相出口與蒸發(fā)器的油氣管道進口相連;蒸發(fā)器的油氣管道出口與第四分離器的進口相連,經(jīng)過第四分離器的氣液分離過程,氣相部分即為符合排放濃度要求的低溫尾氣,該低溫尾氣經(jīng)第四分離器的氣相出口進入第三換熱器的尾氣管道進口,第三換熱器尾氣管道出口與第二換熱器的尾氣管道進口相連,第二換熱器尾氣管道出口與第一換熱器尾氣管道進口相連,最終符合要求的尾氣經(jīng)第一換熱器尾氣管道出口排放。經(jīng)過逐步冷凝并分離出來的冷凝油液體經(jīng)第一分離器的液相出口、第二分離器的液相出口、第三分離器的液相出口、第四分離器的液相出口排出,回收至儲罐或者以其他方式加以儲存和利用。上述技術方案中第一換熱器單元并不局限于由三個換熱器構成,可以根據(jù)實際情況調整第一換熱器單元內換熱器的個數(shù)。隨著第一換熱器單元內換熱器數(shù)目的調整,分離器單元內分離器的數(shù)目應作相應的調整,精餾裝置底部出口和柱頂換熱器底部出口連接的支路管道數(shù)目及支路上的節(jié)流元件數(shù)目也應作相應的調整。上述技術方案將需要處理的油氣依次通入油氣處理回路的換熱器單元中,由返流的低壓制冷劑提供主要的冷量,并且按照要處理的油氣成分的特點,利用精餾裝置底部和頂部不同成分的高壓液體分別節(jié)流后與低壓制冷劑混合,以優(yōu)化和匹配油氣降溫過程中的水當量變化,逐段冷卻油氣,減小不同溫度段換熱器內混合制冷劑與油氣之間的傳熱溫差,從而適應不同成分油氣的冷凝分離和減小系統(tǒng)的單位耗功。被逐級冷卻的油氣經(jīng)過多次氣液分離,最終形成符合排放濃度要求的低溫尾氣,可以再提供一部分冷量,復溫后排放;冷凝油液體可有多種儲存或利用方式。為保證整個油氣分離系統(tǒng)的穩(wěn)定性,同時實現(xiàn)能源的綜合利用,在優(yōu)選的技術方案中,可以在所述的精餾裝置的底部出口管道上設置一個或多個干燥過濾器,實現(xiàn)對底部流出液體制冷劑的干燥和過濾;同時還可以設置一個或多個釜底換熱器,對底部流出的制冷劑進行預冷處理。當干燥過濾器和釜底換熱器個數(shù)均為一個時,所述的精餾裝置的底部出口首先依次連接干燥過濾器和釜底換熱器,然后再與所述的三條支路相連;所述的釜底換熱器內設有釜底換熱器高壓制冷劑管道和釜底換熱器低壓制冷劑管道;所述的干燥過濾器進口與精餾裝置底部出口相連,出口與釜底換熱器高壓制冷劑管道進口相連;所述的釜底換熱器高壓制冷劑管道出口再分別與支路上的節(jié)流元件進口相連;所述的釜底換熱器低壓制冷劑管道進口與精餾裝置柱頂換熱器出口相連,出口與壓縮機的吸氣口相連。利用低壓制冷劑對精餾裝置底部的液體制冷劑進行預冷,實現(xiàn)能量的綜合利用;所述的釜底換熱器內的高壓制冷劑管道和低壓制冷劑管道的進口分別位于釜底換熱器的兩側,以實現(xiàn)逆流換熱。若待處理的油氣中含水量較高,或者是待處理的油氣在冷凝處理之前沒有經(jīng)過其他干燥處理,在另一種優(yōu)選的技術方案中,可以將返流經(jīng)過第一換熱器單元的仍處于-10℃~-20℃的尾氣與進入第一換熱器單元之前的待處理油氣在第三換熱器單元中進行回熱,使得待處理油氣降溫至-1℃~4℃以基本除盡水汽。所述的第三換熱器單元包括第四換熱器、第五換熱器、第一截止閥、第二截止閥、第三截止閥、第四截止閥、第五截止閥、第六截止閥、第七截止閥和第八截止閥;所述的第四換熱器和第五換熱器并聯(lián)設置。所述的第四換熱器和第五換熱器內部均設有一個油氣管道和一個尾氣管道;油氣首先分兩支路分別與第一截止閥和第三截止閥進口相連;第一換熱器的尾氣管道出口分別與第五截止閥和第七截止閥進口相連,使得尾氣分為兩條支路;所述的第四換熱器的油氣管道進口與第一截止閥出口相連,油氣管道出口與第二截止閥進口相連,尾氣管道進口和第五截止閥出口相連,尾氣管道出口與第六截止閥進口相連;所述的第五換熱器的油氣管道進口與第三截止閥出口相連,油氣管道出口與第四截止閥進口相連,尾氣管道進口與第七截止閥出口相連,尾氣管道出口與第八截止閥進口相連;所述的第二截止閥出口和第四截止閥出口相連,匯聚成一個管道后與第一換熱器的油氣管道進口相連;所述的第六截止閥出口和第八截止閥出口相連,匯聚成一個管道后作為尾氣的出口。第四換熱器、第五換熱器以及與各自相連的各截止閥一并切換運行。所述的第四換熱器和第五換熱器的油氣管道和尾氣管道的進口均位于各自換熱器的兩側,以實現(xiàn)逆流換熱。在第三換熱器單元中,利用尾氣的剩余冷量為油氣提供預冷,使得油氣中的大部分水分凝結,實現(xiàn)能量的綜合利用;并采用兩換熱器切換運行的模式,使一個換熱器運行時,另一個換熱器排水或除霜,增加裝置連續(xù)運行的穩(wěn)定性。若待處理的油氣中含低沸點組分較多時,要將其處理到可排放的濃度標準,所需的制冷溫度也要求更低,制冷劑回路中需采用低沸點組分濃度較高的多元混合制冷劑。這將導致油氣分離系統(tǒng)中制冷劑回路的壓縮機在開始降溫階段的壓比和排氣溫度過高,大大降低壓縮機壽命,甚至導致壓縮機因壓力保護而不能開啟,使整個油氣分離系統(tǒng)不能正常運行,冷卻效率低。為解決這些問題,在另一種優(yōu)選的技術方案中,可以在所述的精餾裝置與壓縮機吸氣口之間設置并聯(lián)的第一變濃度回路和第二變濃度回路。第一變濃度回路包括依次串聯(lián)的第九截止閥、儲液罐、第十截止閥,第二變濃度回路由依次串聯(lián)的第十一截止閥、第一儲氣罐、第十二截止閥構成;在該優(yōu)選的技術方案中,所述第九截止閥的進口與精餾裝置的底部出口相連,所述第十一截止閥的進口與精餾裝置的柱頂換熱器頂部出口相連;所述第十截止閥的出口和所述第十二截止閥的出口均與壓縮機的吸氣口相連。通過第一變濃度回路以及第二變濃度回路在不同過程的啟用和停用,來調節(jié)參與循環(huán)的混合制冷劑中低沸點組分的濃度,可以改善開機過程,或是達到更低的制冷溫度。為進一步便于調節(jié)制冷劑回路中低沸點制冷劑的含量,優(yōu)選的技術方案中,可以在所述的第一節(jié)流元件的進口和第三換熱器的高壓制冷劑管道出口之間的管路上設置第五分離器;所述的第五分離器與壓縮機的吸氣口之間設置第三變濃度回路;所述的第三變濃度回路由依次串聯(lián)連接的第十三截止閥、第二儲氣罐和第十四截止閥構成,第十三截止閥進口與第五分離器的氣相出口連通。所述的冷凝器、精餾裝置的柱頂換熱器、第一換熱器、第二換熱器、第三換熱器、蒸發(fā)器、釜底換熱器、第四換熱器、第五換熱器可選用常見的套管式換熱器、噴淋式換熱器、殼管式換熱器或板翅式換熱器。根據(jù)實際需要連接的管路和具體場合選擇不同類型的換熱器。本發(fā)明中優(yōu)選板翅式換熱器。所述的低溫冷凝油氣分離系統(tǒng)所用的制冷劑為二元或二元以上的非共沸混合制冷劑,常見的組分主要有:氮氣、惰性氣體、烴類、烴的鹵化物、二氧化碳等等。所述的各節(jié)流元件可選用常規(guī)的手動節(jié)流閥、自動節(jié)流閥或毛細管,以起到節(jié)流降溫的作用。所述的各截止閥可選用常見的手動或自動雙向截止閥,以實現(xiàn)截止閥的自動或手動控制,其中第一與第二截止閥聯(lián)動,第三與第四截止閥聯(lián)動,第五與第六截止閥聯(lián)動,第七與第八截止閥聯(lián)動。所述的精餾裝置可選用常規(guī)的填料塔或者板式塔。與現(xiàn)有技術相比,本發(fā)明的有益效果為:(1)本發(fā)明的油氣分離系統(tǒng)中制冷系統(tǒng)的結構簡化,運行可靠。對于含低沸點成分較多的油氣,所需的最低制冷溫度較低,如-110℃--130℃。要達到如此低的制冷溫度,傳統(tǒng)的混合制冷劑自復疊制冷系統(tǒng)一般需要2-5級分離過程。采用精餾裝置來替代多級分離過程,可以使系統(tǒng)結構大大簡化,并且使得進入到低溫段的制冷劑中攜帶的潤滑油有效去除,保證系統(tǒng)的可靠運行。(2)本發(fā)明的油氣分離系統(tǒng)可提高油氣冷凝系統(tǒng)的熱力學效率。針對不同成分的油氣,根據(jù)其降溫過程中的水當量分布特點和流量不同,可以調節(jié)精餾裝置底部、頂部兩個地方引出的不同成分的高壓混合制冷劑液體的流量以及混合位置,優(yōu)化換熱器內的溫度分布,減小傳熱溫差,從而提高系統(tǒng)的熱力學效率,減小系統(tǒng)耗功。(3)本發(fā)明的油氣分離系統(tǒng)充分利用尾氣的余冷。若油氣中含水量多或者在進行冷凝處理前沒有進行過干燥,則可以利用尾氣中的余冷對油氣進行預冷,使得大部分水冷凝下來,減小在后續(xù)低溫段結霜的可能性。同時預冷換熱器單元采用切換運行的方式,增加裝置的連續(xù)運行穩(wěn)定性。(4)本發(fā)明的油氣分離系統(tǒng)能優(yōu)化油氣分離系統(tǒng)的開始降溫階段,提高降溫速率。開始降溫階段內,混合制冷劑中高沸點組分濃度增加能降低系統(tǒng)的開機壓力,改善該階段內壓縮機排氣溫度過高和壓比偏大的問題,改善系統(tǒng)的動態(tài)運行特性。(5)本發(fā)明的油氣分離系統(tǒng)能優(yōu)化油氣分離系統(tǒng)的最終降溫階段,使得系統(tǒng)達到更低的制冷溫度,提高系統(tǒng)的熱力學效率。降溫最終階段內,混合制冷劑中低沸點組分濃度增加能改善換熱器中高低壓側混合制冷劑的水當量匹配,從而降低系統(tǒng)能達到的最低溫度,提高系統(tǒng)的熱力學性能。(6)本發(fā)明的油氣分離系統(tǒng)中三個變濃度回路均結構簡單,調節(jié)能力強,操作方便。在系統(tǒng)設計時就可以根據(jù)所需要實現(xiàn)的最低制冷溫度設置若干個變濃度回路,也可以在系統(tǒng)運行時根據(jù)需要啟用若干個變濃度回路。附圖說明圖1為本發(fā)明的精餾型自復疊低溫冷凝油氣分離系統(tǒng)的第一種實施方式的結構示意圖;圖2為本發(fā)明的精餾型自復疊低溫冷凝油氣分離系統(tǒng)的第二種實施方式的結構示意圖;圖3為本發(fā)明的精餾型自復疊低溫冷凝油氣分離系統(tǒng)的第三種實施方式的結構示意圖;圖4為本發(fā)明的精餾型自復疊低溫冷凝油氣分離系統(tǒng)的第四種實施方式的結構示意圖;圖5為本發(fā)明的變濃度精餾型自復疊低溫冷凝油氣分離系統(tǒng)的第五種實施方式的結構示意圖。具體實施方式下面結合附圖和具體實施方式對本發(fā)明一種精餾型自復疊低溫冷凝的油氣分離系統(tǒng)作進一步詳細說明。實施例1如圖1所示,一種精餾型自復疊低溫冷凝油氣分離系統(tǒng),包括壓縮機1、冷凝器2、精餾裝置3、第一換熱器4、第二換熱器5、第三換熱器6、蒸發(fā)器7、第一分離器8、第二分離器9、第三分離器10、第四分離器11、第一節(jié)流元件12、第二節(jié)流元件13、第三節(jié)流元件14、第四節(jié)流元件15、第五節(jié)流元件16、第六節(jié)流元件17和第七節(jié)流元件18。精餾裝置3中包括精餾柱以及與精餾柱頂部相連的柱頂換熱器,柱頂換熱器內設有冷卻管道。第一換熱器4、第二換熱器5、第三換熱器6中均設有一個正流制冷劑管道、一個返流制冷劑管道、一個油氣管道和一個尾氣管道,外壁上均設有與管道連通的進口或出口。蒸發(fā)器7中設有一個制冷劑管道和一個油氣管道,外壁上設有與管道連通的進口或出口。壓縮機1的出口1b和冷凝器2的制冷劑進口2a相連,冷凝器2的制冷劑出口2b和精餾裝置3中精餾柱的中部進料口3a相連,精餾裝置3的精餾柱底部出液口3b分別與第二節(jié)流元件13的進口13a、第三節(jié)流元件14的進口14a、第四節(jié)流元件15的進口15a相連。精餾裝置3的柱頂換熱器頂部的出口3c和第一換熱器4的正流制冷劑管道進口4a相連;精餾裝置3的柱頂換熱器底部的出口3f和分別與第五節(jié)流元件16的進口16a、第六節(jié)流元件17的進口17a、第七節(jié)流元件18的進口18a相連。第一換熱器4的正流制冷劑管道出口4b與第二換熱器5的正流制冷劑管道進口5a相連;第一換熱器4的返流制冷劑管道進口4c與第二換熱器5的返流制冷劑管道出口5d相連,第一換熱器4的返流制冷劑管道出口4d則與精餾裝置3柱頂換熱器內的冷卻管道的進口3d相連;第一換熱器4中的待處理油氣管道進口為4g,尾氣管道出口為4f;第一換熱器4中的油氣管道出口4h與第一分離器8的進口8a相連,尾氣管道進口4e與第二換熱器5的尾氣管道出口5f相連。第一換熱器4中的正流制冷劑管道進口4a、返流制冷劑管道出口4d、尾氣管道出口4f、油氣管道進口4g在同一側,而第一換熱器4中的正流制冷劑管道出口4b、返流制冷劑管道進口4c、尾氣管道進口4e、油氣管道出口4h在另一側,以實現(xiàn)冷熱流體的逆向換熱。第二換熱器5的正流制冷劑管道出口5b與第三換熱器6的正流制冷劑管道進口6a相連,第二換熱器5的返流制冷劑管道進口5c和第三換熱器6的返流制冷劑管道出口6d相連;第二換熱器5的尾氣管道進口5e與第三換熱器6的尾氣管道出口6f相連,油氣管道進口5g與第一分離器8的氣相出口8c相連,油氣管道出口5h與第二分離器9的進口9a相連。第二換熱器5中正流制冷劑管道進口5a、返流制冷劑管道出口5d、尾氣管道出口5f、油氣管道進口5g在同一側,而第二換熱器5的正流制冷劑管道出口5b、返流制冷劑管道進口5c、尾氣管道進口5e、油氣管道出口5h在另一側,以實現(xiàn)冷熱流體的逆向換熱。第三換熱器6的正流制冷劑管道出口6b與第一節(jié)流元件11的進口11a相連,第一節(jié)流元件11的出口11b則與蒸發(fā)器7的制冷劑管道進口7a相連;第三換熱器6的返流制冷劑管道進口6c與蒸發(fā)器7的制冷劑管道出口7b相連;第三換熱器6的尾氣管道進口6e與第四分離器11的氣相出口11c相連,油氣管道進口6g與第二分離器9的氣相出口9c相連,油氣管道出口6h與第三分離器10的進口10a相連。第三換熱器6中正流制冷劑管道進口6a、返流制冷劑管道出口6d、尾氣管道出口6f、油氣管道進口6g在同一側,而第三換熱器6中正流制冷劑管道出口6b、返流制冷劑管道進口6c、尾氣管道進口6e、油氣管道出口6h在另一側,以實現(xiàn)冷熱流體的逆向換熱。蒸發(fā)器7的尾氣管道進口7c與第三分離器10的氣相出口10c相連,尾氣管道出口7d與第四分離器11的進口11a相連;蒸發(fā)器7中的制冷劑管道出口7b和尾氣管道進口7c在同一側,制冷劑管道進口7a和尾氣管道出口7d在另一側,以實現(xiàn)冷熱流體的逆向換熱。第一分離器8的液相出口8b、第二分離器9的液相出口9b、第三分離器10的液相出口10b以及第四分離器11的液相出口11b最終匯聚成一股,作為冷凝油被收集或者送回到儲罐。第二節(jié)流元件13的出口13b、第五節(jié)流元件6的出口16b均與第一換熱器4的返流制冷劑管道進口4c相連,或與第二換熱器5的返流制冷劑管道出口5d相連;第三節(jié)流元件14的出口14b、第六節(jié)流元件17的出口17b均與第二換熱器5的返流制冷劑管道進口5c相連,或與第三換熱器6的返流制冷劑管道出口6d相連;第四節(jié)流元件的出口15b、第七節(jié)流元件的出口18b均與第三換熱器6的返流制冷劑管道進口6c相連,或與蒸發(fā)器7的制冷劑管道出口7b相連。上述實施方式中的冷凝器2、精餾裝置3的柱頂換熱器、第一換熱器4、第二換熱器5、第三換熱器6、蒸發(fā)器7為板翅式換熱器。第一節(jié)流元件12、第二節(jié)流元件13、第三節(jié)流元件14、第四節(jié)流元件15、第五節(jié)流元件16、第六節(jié)流元件17、第七節(jié)流元件18可選用常規(guī)的手動節(jié)流閥、自動節(jié)流閥或毛細管,以起到節(jié)流降溫的作用。精餾裝置3與普通制冷裝置中的精餾裝置類似,精餾柱可以選用常規(guī)的塔板式精餾柱或者填料式精餾柱。各個部件之間的連接采用制冷劑管路連接,低溫管路外要包裹防水和保溫材料。低溫冷凝油氣分離系統(tǒng)所用的制冷劑為二元或二元以上的非共沸混合制冷劑,常見的組分主要有:氮氣、惰性氣體、烴類、烴的鹵化物、二氧化碳等等。為便于理解,上述精餾型自復疊低溫冷凝油氣分離系統(tǒng)可以分為制冷劑回路和油氣回路,以下是詳細的工作流程:在制冷劑回路中,非共沸混合制冷劑經(jīng)過壓縮機1加壓后,經(jīng)過冷凝器2被冷凝成氣液兩相的高壓流體,再進入精餾裝置3的釜中。氣態(tài)混合制冷劑從下到上通過精餾裝置3的精餾柱,與精餾裝置3頂部流下來的回流液進行傳熱傳質的過程;混合制冷劑中的高沸點組分、壓縮機潤滑油以及少量的低沸點組分被冷凝下來作為回流液的一部分;大部分低沸點組分構成的氣態(tài)混合制冷劑通過精餾裝置3頂部換熱器,從頂部出口3c流出。這股氣態(tài)混合制冷劑依次通過第一換熱器4、第二換熱器5、第三換熱器6,經(jīng)過第一節(jié)流元件12節(jié)流降溫,然后進入蒸發(fā)器7提供冷量,再依次返流經(jīng)過第三換熱器6、第二換熱器5、第一換熱器4、精餾裝置3的柱頂換熱器,分別為油氣和精餾過程提供冷量,最終返回壓縮機1的吸氣口。以高沸點組分為主的液態(tài)制冷劑從精餾裝置3的底部3b流出,可以分別進入第二節(jié)流元件13、第三節(jié)流元件14、第四節(jié)流元件15,經(jīng)過節(jié)流后和以低沸點為主的返流制冷劑在不同的位置混合。調節(jié)第二節(jié)流元件13或第三節(jié)流元件14或第四節(jié)流元件15的開度,可以使得這股液態(tài)制冷劑和返流制冷劑以不同的比例混合,以匹配換熱器中的水當量。以中間沸點組分為主的液態(tài)制冷劑從精餾裝置3的柱頂換熱器的底部出口3f流出,可以分別進入第五節(jié)流元件16、第六節(jié)流元件17、第八節(jié)流元件18,經(jīng)過節(jié)流后和以低沸點為主的返流制冷劑在不同的位置混合。調節(jié)第五節(jié)流元件16或第六節(jié)流元件17或第七節(jié)流元件18的開度,可以使得這股液態(tài)制冷劑和返流制冷劑以不同的比例混合,以匹配換熱器中的水當量。在油氣回路中,高溫或常溫油氣首先經(jīng)過第一換熱器4降溫,進入第一分離器8,將部分液化下來的油品分離出來;未液化的油氣繼續(xù)進入第二換熱器5被冷卻到更低的溫度,進入第二分離器9,將再次部分液化的油品分離出來;未液化的油氣再繼續(xù)進入第三換熱器6繼續(xù)降溫,進入第三分離器10,將再次部分液化的油品分離出來;最后,未液化的油氣進入蒸發(fā)器7降溫,進入第四分離器11,將液化的油品分離出來。經(jīng)過系統(tǒng)各參數(shù)的調節(jié),可以保證此時未液化的油氣已經(jīng)達到了國標中的排放標準。為利用這部分未液化油氣的冷量,將其依次返流通過第三換熱器6、第二換熱器5、第一換熱器4,復溫后以尾氣的形式排放。第一分離器8、第二分離器9、第三分離器10、第四分離器11的分離出來的油品分別從分離器液相出口流出,并匯集起來以冷凝油的形式返回儲罐或者以其他方式儲存起來。對某石化廠裝車油氣采用本發(fā)明方法進行低溫冷凝分離。油氣溫度為35℃,流量為30m3/h,油氣成分與濃度如表1所示:表1.油氣組成與各組分濃度采用某種多元混合制冷劑,制冷劑回路的工況為:低壓為200kPa,高壓為2000kPa,假設壓縮機絕熱效率為85%,忽略各換熱器壓降與漏熱。利用化工軟件HYSYS進行流程模擬,結果顯示:油氣可被冷凝至-130℃,正丁烷、異丁烷、正戊烷、異戊烷、正己烷均被冷凝,尾氣中只剩下甲烷、乙烷、丙烷這些烴類,具體濃度如表2所示:表2.尾氣組成與各組分濃度組分摩爾分數(shù)(%)甲烷0.56乙烷1.41丙烷0.11氮氣75.14氧氣22.77經(jīng)核算,在該算例中,尾氣中非甲烷總烴含量約為21.5g/m3,低于國標要求,每立方的油氣處理功耗約為0.27kW·h。實施例2如圖2所示,與實施例1連接方式與結構相同,不同之處在于在精餾裝置底部液體出口設有干燥過濾器19和釜底換熱器20。精餾裝置3的底部出口首先依次連接干燥過濾器19和釜底換熱器20,然后再與第二節(jié)流元件13、第三節(jié)流元件14以及第四節(jié)流元件15所在的三條支路相連;釜底換熱器19內設有一個高壓制冷劑管道和一個低壓制冷劑管道。具體地,精餾裝置3的底部液體出口3b與干燥過濾器19的進口19a相連,干燥過濾器19的出口19b與釜底換熱器20的高壓制冷劑管道進口20a相連;所述的釜底換熱器20的高壓制冷劑管道出口20b分別與第二節(jié)流元件13的進口13a、第三節(jié)流元件14的進口14a、第四節(jié)流元件15的進口15a相連;精餾裝置3的柱頂換熱器冷卻管道出口3e與釜底換熱器20的低壓制冷劑管道進口20c相連;釜底換熱器20的低壓制冷劑管道出口20d與壓縮機1的吸氣口1a相連。在所述的釜底換熱器20中,高壓制冷劑管道進口20a和低壓制冷劑管道出口20d在同一側,高壓制冷劑管道出口20b和低壓制冷劑管道進口20c在另一側,以實現(xiàn)冷熱流體的逆向換熱。實施例3如圖3所示,與實施例1連接方式與結構相同,不同之處在于新增了第三換熱器單元。第三換熱器單元包括第四換熱器22、第五換熱器25、第一截止閥21、第二截止閥23、第三截止閥24、第四截止閥26、第五截止閥27、第六截止閥28、第七截止閥29和第八截止閥30,第四換熱器22和第五換熱器25并聯(lián)設置,其中第一截止閥21與第二截止閥23聯(lián)動,第三截止閥24與第四截止閥26聯(lián)動,第五截止閥27與第六截止閥28聯(lián)動,第七截止閥29與第八截止閥30聯(lián)動。具體地,油氣首先分別與第一截止閥21的進口21a和第三截止閥24進口24a相連;第一換熱器4的尾氣管道出口4f分別與第五截止閥27的進口27a和第七截止閥29的進口29a相連,使得尾氣分為兩條支路;第四換熱器22的油氣管道進口22a與第一截止閥21的出口21b相連,油氣管道出口22b與第二截止閥23的進口23a相連,尾氣管道進口22c和第五截止閥27的出口27a相連,尾氣管道出口22d與第六截止閥28的進口28a相連;第五換熱器25的油氣管道進口25a與第三截止閥24的出口24a相連,油氣管道出口25b與第四截止閥26的進口26a相連,尾氣管道進口25c與第七截止閥29的出口29b相連,尾氣管道出口25d與第八截止閥30的進口30a相連;第二截止閥出口23b和第四截止閥出口26b相連,匯聚成一個管道后與第一換熱器4的油氣管道進口4g相連;第六截止閥28的出口28b和第八截止閥30的出口30b相連,匯聚成一個管道后作為尾氣的出口。第四換熱器22的油氣管道進口22a和尾氣管道出口22d位于同一側,油氣管道出口22b和尾氣管道進口22c位于另一側,以實現(xiàn)逆流換熱;第五換熱器25的油氣管道進口25a和尾氣管道出口25d位于同一側,油氣管道出口25b和尾氣管道進口25c位于另一側,以實現(xiàn)逆流換熱。系統(tǒng)的工作流程于實施例1類似,不同之處在于剛開始運行時,同時打開第一截止閥21、第二截止閥23、第五截止閥27和第六截止閥28,同時關閉第三截止閥24、第四截止閥25、第七截止閥29和第八截止閥30,待處理油氣和尾氣在第四換熱器22中發(fā)生熱交換,利用尾氣的余冷來預冷油氣以冷凝大部分水汽,此時第五換熱器25實施排水或除霜過程;當系統(tǒng)運行一段時間后,同時關閉第一截止閥21、第二截止閥23、第五截止閥27、第六截止閥28,同時打開第三截止閥24、第四截止閥25、第七截止閥27、第八截止閥30,將油氣和尾氣的換熱過程切換到第五換熱器25中進行,此時第四換熱器22實施排水或除霜過程。實施例4如圖4所示,精餾型自復疊低溫冷凝油氣分離系統(tǒng)包括正常濃度回路、第一變濃度回路、第二變濃度回路。正常濃度回路與實施例1中油氣分離回路的連接方式與結構類似,但在精餾柱與壓縮機之間增加了第一變濃度回路和第二變濃度回路。下面對每個回路進行說明:(1)正常濃度回路:正常濃度回路的部件與連接與實施例1中類似,不同之處在于:精餾裝置3的柱頂換熱器頂部的出口3c分別與兩條并聯(lián)支路相連,其中一條支路與第一換熱器4的正流制冷劑管道進口4a相連,另一條支路與第十一截止閥34的進口34a相連;精餾裝置3的精餾柱底部出液口3b分別與四條并聯(lián)支路相連,即分別與第二節(jié)流元件13的進口13a、第三節(jié)流元件14的進口14a、第四節(jié)流元件15的進口15a以及第九截止閥31的進口31a相連。(2)第一變濃度回路:第一變濃度回路由依次串聯(lián)設置的第九截止閥31、儲液罐32和第十截止閥33組成。其中第九截止閥31的進口31a與精餾裝置3的底部出口3b相連,出口與儲液罐32的進口32a相連;第十截止閥33的進口33a與儲液罐32的出口32b相連,出口33b與壓縮機1的吸氣口1a相連。(3)第二變濃度回路:第二變濃度回路由依次串聯(lián)設置的第十一截止閥34、第一儲氣罐35和第十二截止閥36組成。其中第十一截止閥34的進口34a與精餾裝置3的頂部出口3c相連,出口34b與第一儲氣罐35的進口35a相連;第十二截止閥36的進口36a與第一儲氣罐35的出口35b相連,出口36b與壓縮機1的吸氣口1a相連。該實施方式中的第九截止閥31、第十截止閥33、第十一截止閥34、第十二截止閥36為手動或者自動雙向截止閥。為便于理解,以下是詳細的工作流程:制冷劑的正常濃度回路、油氣分離回路工作流程與實施例1中所述相同,不同之處在于開機前要確認第九截止閥31、第十截止閥33、第十一截止閥34、第十二截止閥36都處于關閉狀態(tài)。隨著時間延續(xù),油氣分離系統(tǒng)的制冷溫度不斷下降,在足夠長的時間之后,在環(huán)境溫度以及油氣熱負荷不變的情況下,系統(tǒng)達到穩(wěn)定運行狀態(tài),制冷溫度在混合制冷劑的正常濃度下達到了最低極限。此時,分別啟動第一變濃度回路和第二變濃度回路就可以實現(xiàn)更低的制冷溫度。啟用第一變濃度回路:打開第九截止閥31,將富含高沸點組分的混合制冷從精餾柱底部引入儲液罐32中,一段時間后關閉第九截止閥31,使得正常濃度回路中高沸點組分制冷劑減少,提高了參與循環(huán)的制冷劑中低沸點組分的濃度,能比正常濃度制冷實現(xiàn)更低的制冷溫度,可以將油氣中的輕烴類處理得更徹底。啟用第二變濃度回路:打開第十二截止閥36,將富含低沸點組分的混合制冷劑從第一儲氣罐35中放出,一段時間后關閉第十二截止閥36,使得正常濃度回路中參與循環(huán)的低沸點制冷劑增加,因此提高了參與循環(huán)的低沸點組分濃度,可以比正常濃度和啟用第一變濃度回路后的制冷實現(xiàn)更低的制冷溫度。經(jīng)過足夠長時間運行后,在環(huán)境溫度和熱負荷不變的情況下,系統(tǒng)再次達到穩(wěn)定狀態(tài),制冷溫度在改變后的制冷劑濃度下達到了新的最低極限。關機前,依次停用第二變濃度回路和第一變濃度回路,可以逐步減小停機時混合制冷劑中的低沸點組分濃度。停用第二變濃度回路:打開第十一截止閥34,將富含低沸點組分的混合制冷劑儲存到第一儲氣罐35中,一段時間后關閉第十一截止閥34,使得參與循環(huán)的制冷劑低沸點組分濃度繼續(xù)減小。停用第一變濃度回路:打開第十截止閥33,將儲液罐32中富含高沸點組分的混合制冷劑放出,一段時間后關閉第十截止閥33,使得參與循環(huán)的制冷劑低沸點組分濃度繼續(xù)減小。在停用兩個變濃度回路后即可停機,這兩個變濃度回路可在下一次開機運行中繼續(xù)啟用單個或者兩個同時啟用。實施例5如圖5所示,與實施例4的結構及連接方式相同,不同之處在于:在第一節(jié)流元件12的進口12a和第三換熱器6的正流制冷劑管道出口6b之間設有第五分離器40,所述的第五分離器40與壓縮機1的吸氣口1a之間設有第三變濃度回路;第三變濃度回路由依次串聯(lián)的第十三截止閥37、第二儲氣罐38和第十四截止閥39組成;其中,第十三截止閥37的進口37a與第五分離器40的氣相出口40c相連,出口37b與第二儲氣罐38的進口38a相連;第十四截止閥39的進口39a與第二儲氣罐38的出口38b相連,出口39b與壓縮機1的吸氣口1a相連。啟用第一和第二變濃度回路的方法和實施例4相同。啟用第三變濃度回路:打開第十四截止閥39,將低沸點組分比例更高的混合制冷劑從第二儲氣罐38中放出,一段時間后關閉第十四截止閥39,使得參與循環(huán)的制冷劑低沸點組分濃度提高,可以比正常濃度制冷、啟用第一變濃度回路制冷、啟用第二變濃度回路制冷實現(xiàn)更低的制冷溫度。經(jīng)過足夠長時間運行后,在環(huán)境溫度和熱負荷不變的情況下,系統(tǒng)再次達到穩(wěn)定狀態(tài),制冷溫度在改變后的制冷劑濃度下達到了新的最低極限。關機前,依次停用第三變濃度回路、第二變濃度回路和第一變濃度回路,可以逐步減小停機時混合制冷劑中的低沸點組分濃度。停用第三變濃度回路:打開第十三截止閥37,將低沸點組分含量最多的混合制冷劑儲存到第二儲氣罐38中,一段時間后關閉第十三截止閥37,使得參與循環(huán)的制冷劑低沸點濃度繼續(xù)減小。停用第二變濃度回路和停用第一變濃度回路方法與實施例4相同。以上所述僅為本發(fā)明的較佳實施舉例,并不用于限制本發(fā)明,凡在本發(fā)明精神和原則之內,所作的任何修改、等同替換、改進等,均應包含在本發(fā)明的保護范圍之內。當前第1頁1 2 3