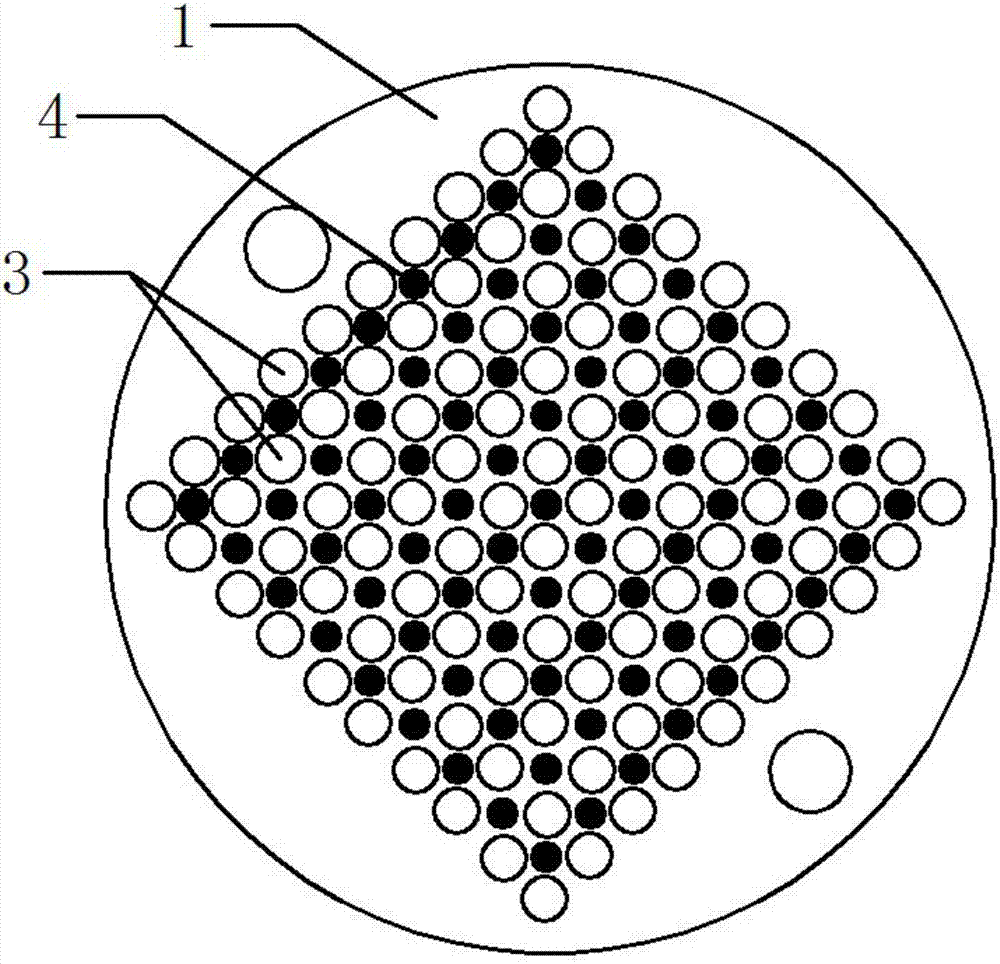
本發(fā)明涉及石油煉化行業(yè)所用的催化劑制造領(lǐng)域,具體的涉及一種用于汽油、煤焦油加氫精制脫硫、脫氮的催化劑及其制備方法。
背景技術(shù):
:隨著人類文明的進(jìn)步,對(duì)自然資源的索取也愈來愈烈,對(duì)環(huán)境的破壞也日益嚴(yán)重,而大多數(shù)資源是有限的,不可再生的,因此滿足人類對(duì)資源的長(zhǎng)期有效利用和保護(hù)自然環(huán)境是所有人刻不容緩的責(zé)任和義務(wù)。我們必須做到開源節(jié)流,采取開發(fā)新技術(shù),提高資源利用率等措施,旨在節(jié)約資源和減少或避免對(duì)環(huán)境的破壞,給子孫后代留下一片藍(lán)天。而石油煉化行業(yè)是自然資源開發(fā)利用和環(huán)境污染比較嚴(yán)重的行業(yè);目前多采用催化劑進(jìn)行污染物的脫除,以減弱對(duì)環(huán)境的污染;特別是用于汽油、煤焦油加氫精制脫硫,脫氮的催化劑,該類催化劑的構(gòu)成主要包括載體和活性物質(zhì),其中的載體結(jié)構(gòu)主要為當(dāng)量直徑0.5~3mm的條形實(shí)芯體,比如“三葉草”型,圓柱型等,該系列結(jié)構(gòu)的催化劑載體技術(shù)成熟,已工業(yè)化多年,有其優(yōu)勢(shì),也有其劣勢(shì),優(yōu)勢(shì)是技術(shù)成熟,生產(chǎn)工藝簡(jiǎn)單;劣勢(shì)是制造的催化劑堆積空隙率小,與同等反應(yīng)條件下的催化劑,所需要更多的活性組分。技術(shù)實(shí)現(xiàn)要素:本發(fā)明針對(duì)現(xiàn)有技術(shù)的上述不足,提供一種用于汽油、煤焦油加氫精制脫硫、脫氮的催化劑,該催化劑的空隙率是同當(dāng)量直徑的實(shí)芯催化劑載體的1.2~1.6倍,所使用的活性組分量也是同體積下的其它催化劑的50~80%,大幅度節(jié)約了催化劑活性組分的使用量,節(jié)約了資源。為了解決上述技術(shù)問題,本發(fā)明采用的技術(shù)方案為:一種用于汽油、煤焦油加氫精制脫硫、脫氮催化劑,包括催化劑載體和載體負(fù)載的活性物質(zhì),所述的催化劑為中心通孔、直徑1~2mm的圓柱狀,其空隙率是同當(dāng)量直徑的實(shí)芯催化劑載體的1.2~1.6倍,活性組分是同當(dāng)量直徑的其它結(jié)構(gòu)催化劑的0.2~0.5倍;所述的催化劑載體的材質(zhì)包括氧化鋁系列材料或氧化鋁系列材料和二氧化硅系列材料的混合物或氧化鋁系列材料和氧化鈦系列材料的混合物,負(fù)載的活性物質(zhì)含有鈷(Co),鎳(Ni),鉬(Mo),鋅(Zn),磷(P)等中的一種或者多種。所述的氧化鋁系列材料包括但不限于擬薄水鋁石、鋁溶膠等氧化鋁系列材料的一種或多種混合組成的粉料。所述的氧化硅系列材料是指包括但不限于硅溶膠,氣相二氧化硅等一種或多種混合組成的材料。本發(fā)明還提供一種上述用于汽油、煤焦油加氫精制脫硫、脫氮催化劑的制備方法,具體的步驟包括:(1)將氧化鋁和二氧化硅系列材料按照重量比為80~100:0~20的比例配成混合料,輔助于粘結(jié)劑為混合料重量的0.5~10%,加水為混合料重量的35~70%,膠溶劑為混合料重量的0.5~5%,糅合成泥料;(2)采用申請(qǐng)?zhí)枮?016109656335、發(fā)明名稱為《一種微型催化劑載體模具、該模具的制作工藝和利用該模具制備載體的方法》所述的模具,結(jié)合步驟(1)的泥料制備出直徑為1~2mm的米粒狀的催化劑載體坯體;(3)將步驟(2)制備的催化劑載體坯體切斷成長(zhǎng)2~12mm的短條;然后在室溫~200℃的溫度環(huán)境下干燥至坯體含水率不超過5%為止;最后將干燥后的坯體經(jīng)過窯爐450~1000℃溫度焙燒5~15小時(shí);(4)在步驟(3)獲得的載體上負(fù)載活性組分物質(zhì):配制Ni-Mo-P-Zn或Co-Mo-P-Zn的前驅(qū)體構(gòu)成的活性組分的雜多酸混合溶液,通過等體積、飽和浸漬等方式在步驟(3)的載體上負(fù)載上述的雜多酸混合溶液;(5)將步驟(4)獲得的催化劑放置于50~200℃下烘5~30小時(shí);(6)將步驟(5)完成的產(chǎn)品通過窯爐在350~750℃焙燒5~35小時(shí),完成催化劑產(chǎn)品制造。本發(fā)明步驟(1)所述的粘結(jié)劑為:甲基纖維素、纖維素醚、羥丙基甲基纖維、素羥乙基纖維素、羧甲基纖維素,田菁膠、阿拉伯樹膠等中的一種或多種混合物。本發(fā)明步驟(1)所述的膠溶劑為工業(yè)純硝酸、工業(yè)純乙酸、工業(yè)純草酸等中的一種或一種以上。本發(fā)明步驟(1)所述的氧化鋁系列材料包括但不限于擬薄水鋁石、鋁溶膠等氧化鋁系列材料的中的一種或多種混合組成的粉料。本發(fā)明步驟(1)所述的二氧化硅系列材料是指包括但不限于硅溶膠,氣相二氧化硅等一種或多種混合組成的材料。本發(fā)明上述步驟(4)中Ni(鎳)前驅(qū)體為催化劑級(jí)別的硝酸鎳,碳酸鎳或堿式碳酸鎳;Mo(鉬)前驅(qū)體為催化劑級(jí)別的氧化鉬,七鉬酸銨或其它鉬酸鹽;P(磷)前驅(qū)物為凈含量為85%的磷酸;Co(鈷)前驅(qū)體為催化劑級(jí)別的硝酸鈷,碳酸鈷或堿式碳酸鈷;Zn為工業(yè)純鋅鹽(如:ZnCl2、ZnSO4、Zn(NO3)2、Zn(ClO4)2)。本發(fā)明的優(yōu)點(diǎn)和有益效果:1.本方法生產(chǎn)的催化劑空隙率是同等當(dāng)量直徑的三葉或四葉草形催化劑的1.2~1.6倍,大的空隙率能提供更大的外表面積以增加催化劑與反應(yīng)物質(zhì)的接觸頻率,提高反應(yīng)效率,被反應(yīng)完成的物質(zhì)也能快速逸出以避免局部發(fā)熱使反應(yīng)器溫度上升而誘發(fā)事故;2.在保證使用的情況下,同等體積反應(yīng)器中使用本催化劑用量是同當(dāng)量直徑的其它結(jié)構(gòu)的催化劑的0.5~0.8倍,即同體積下裝填本催化劑能節(jié)省20~50%催化劑用量,節(jié)約了催化劑用量,節(jié)約成本非??捎^;3.使用本技術(shù)生產(chǎn)的催化劑所耗用的活性組分僅是同當(dāng)量直徑的其它結(jié)構(gòu)催化劑的0.2~0.5倍,節(jié)約資源所產(chǎn)生的經(jīng)濟(jì)和社會(huì)效應(yīng)非??捎^。此技術(shù)用于汽油,煤焦油加氫脫硫、脫氮等化學(xué)加工領(lǐng)域,能大幅度節(jié)約了資源,生產(chǎn)出的汽油能滿足國(guó)5標(biāo)準(zhǔn)。附圖說明圖1申請(qǐng)?zhí)枮?016109656335中的模具剖面示意圖。圖2申請(qǐng)?zhí)枮?016109656335中的陽(yáng)模俯視圖結(jié)構(gòu)示意圖。圖3申請(qǐng)?zhí)枮?016109656335中的陰模俯視圖結(jié)構(gòu)示意圖。圖4申請(qǐng)?zhí)枮?016109656335中的陽(yáng)模結(jié)構(gòu)示意圖。圖5申請(qǐng)?zhí)枮?016109656335中的陰模結(jié)構(gòu)示意圖。具體實(shí)施方式下面通過實(shí)施例進(jìn)一步詳細(xì)描述本發(fā)明,但本發(fā)明不僅僅局限于以下實(shí)施例。實(shí)施例(1)取擬薄水鋁石原粉1kg,甲基纖維素30g,一并投入混料機(jī)混料5分鐘后加水550g和20g硝酸,繼續(xù)混料直至粉料全部變成泥料為此;(2)將步驟(1)完成的泥料投入壓力擠出機(jī)中,通過申請(qǐng)?zhí)枮?016109656335、發(fā)明名稱為《一種微型催化劑載體模具、該模具的制作工藝和利用該模具制備載體的方法》中所述的模具擠出成型;具體的,如附圖1-5所示,申請(qǐng)?zhí)枮?016109656335中的微型催化劑載體模具,該模具包括陽(yáng)模1和陰模2,所述的陽(yáng)模和陰模的一端相互壓合;所述的陽(yáng)模沿軸向設(shè)置有若干進(jìn)泥孔3和棒針容置孔4,所述的棒針容置孔內(nèi)插接有導(dǎo)泥棒5;所述的陰模軸向設(shè)置有若干成型孔6,當(dāng)陽(yáng)模和陰模的一端相互壓合時(shí)、所述的成型孔和棒針容置孔同軸線、且所述的導(dǎo)泥棒貫穿成型孔和棒針容置孔;所述的陰模與陽(yáng)模壓合的端面向內(nèi)軸向設(shè)置有凹槽7、所述的凹槽與陽(yáng)模的端面形成夾層間隙8;所述的導(dǎo)泥棒的外徑小于成型孔的內(nèi)徑。采用上述結(jié)構(gòu),將陽(yáng)模和陰模的一端相互壓合,然后將導(dǎo)泥棒自棒針容置孔一端插入至成型孔內(nèi),并端頭突出于成型孔;然后將含有活性物質(zhì)的催化劑載體泥料通過壓機(jī)從進(jìn)泥孔壓入,進(jìn)入到凹槽形成夾層間隙內(nèi)充分混合,然后從成型孔擠出,得到空心的催化劑載體,這種結(jié)構(gòu)的載體由于內(nèi)部空心設(shè)置,可以使得催化面積變大,提高催化效率,降低成本,使得材料利用率更加充分。(3)將步驟(2)制造的坯體放至70℃烘箱內(nèi)恒溫干燥8小時(shí),至坯體含水率為0.83%;(4)取步驟(3)的坯體用馬弗爐580℃焙燒6小時(shí);(5)按照表1中的各個(gè)活性組分在催化劑中的含量,用硝酸鎳,鉬酸氨,硝酸鋅,磷酸配制多元素混合藥水,通過等體積方法(等體積法)浸漬活性組分溶液;具體見下表1所示:表1各個(gè)活性組分在催化劑中的含量項(xiàng)目米粒環(huán)催化劑活性物質(zhì)含量實(shí)芯三葉草型催化劑MoO3(%)713Co(%)0.81.5Zn(%)0.50.9Ni(%)0.20.2P(%)0.91.8(6)將步驟(5)的產(chǎn)品放至烘箱內(nèi),用60℃溫度烘24小時(shí)后,再將其放置馬弗爐內(nèi)500℃溫度焙燒4小時(shí)完成催化劑制造。在同等條件下,單位體積內(nèi)使用本專利制造的催化劑和傳統(tǒng)三葉草型載體使用效果對(duì)比見表2:表2本發(fā)明實(shí)施例樣品與現(xiàn)有技術(shù)樣品比較結(jié)果從上述的對(duì)比可知,本發(fā)明的催化劑具有大的空隙率能提供更大的外表面積以增加催化劑與反應(yīng)物質(zhì)的接觸頻率,提高反應(yīng)效率,被反應(yīng)完成的物質(zhì)也能快速逸出以避免局部發(fā)熱使反應(yīng)器溫度上升而誘發(fā)事故;而且與同當(dāng)量直徑的其它結(jié)構(gòu)催化劑相比活性物質(zhì)的用量更省,但是脫硫率和脫氮率更高。當(dāng)前第1頁(yè)1 2 3