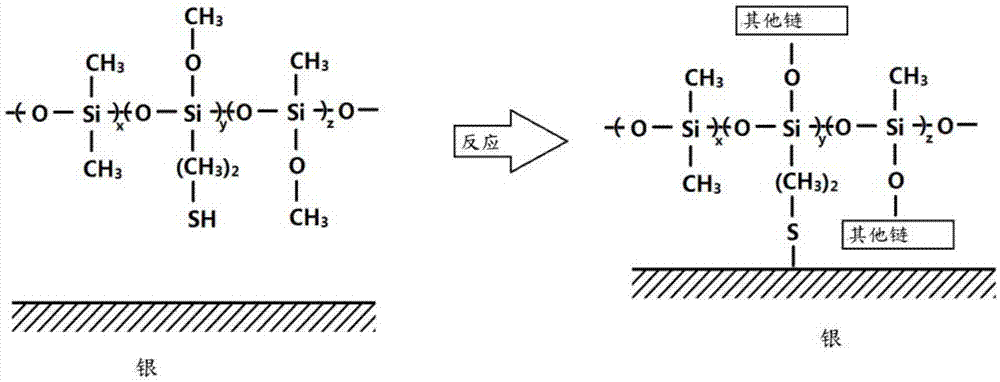
本發(fā)明涉及在基底上涂布多層涂層,尤其是多層涂層是通過無電鍍方式沉積在基底表面。
背景技術(shù):
:一種常用金屬表面的處理方式是電鍍。然而,電鍍因生成大量毒性副產(chǎn)物和廢物對地球環(huán)境造成危害。而且電鍍的成本很高。這些限制了電鍍工業(yè)的發(fā)展。技術(shù)實現(xiàn)要素:本發(fā)明提供一種具有無電鍍涂層的基底,包括一個在所述基底表面上的粘附涂層,所述粘附涂層包含第一硅基礎(chǔ)偶聯(lián)劑;一個在所述粘附涂層上的光滑涂層,所述光滑涂層包含環(huán)氧樹脂;一個在所述光滑涂層上的銀涂層,所述銀涂層包含銀納米顆粒;以及一個在所述銀涂層上的抗刮涂層,所述抗刮涂層包含第二個硅基礎(chǔ)偶聯(lián)劑。本發(fā)明的另一個方法提供了一種在基底上無電鍍涂布多涂層的方法,包括a.將包含第一硅基礎(chǔ)偶聯(lián)劑的粘附涂層涂布于所述基底的表面;b.將包含環(huán)氧樹脂的光滑涂層涂布于所述粘附涂層上;c.將包含銀納米顆粒的銀涂層涂布于所述光滑涂層上;d.將包含第二硅基礎(chǔ)偶聯(lián)劑的抗刮涂層涂布于所述銀涂層上。本發(fā)明另一個方面提供一個用于在基底上無電鍍涂層的套裝,包括含第一硅基礎(chǔ)偶聯(lián)劑的粘附涂層溶液、含環(huán)氧樹脂的光滑涂層溶液、含硝酸銀基礎(chǔ)溶液和葡萄糖基礎(chǔ)溶液的無電鍍涂層溶液、及含第二硅基礎(chǔ)偶聯(lián)劑的抗刮涂層溶液。附圖說明附圖1顯示了根據(jù)本發(fā)明一個實施例γ-氨丙基三乙氧基硅烷 (a1100)與環(huán)氧樹脂基礎(chǔ)的粘附涂層的相互作用。附圖2顯示了本發(fā)明同一個實施例(3-巰基丙基)三甲氧基硅烷(a189)與銀涂層的相互作用。附圖3顯示了本發(fā)明同一個實施例裝飾測試的結(jié)果。附圖4顯示了本發(fā)明同一個實施例樣品粘附測試的結(jié)果。附圖5顯示了本發(fā)明同一個實施例樣品抗腐蝕測試的結(jié)果。附圖6顯示了本發(fā)明同一個實施例樣品沖擊測試的結(jié)果。附圖7顯示了本發(fā)明同一個實施例樣品硬度測試的結(jié)果。附圖8顯示了本發(fā)明同一個實施例樣品uv照射測試的結(jié)果。附圖9顯示了本發(fā)明同一個實施例樣品防水測試的結(jié)果。附圖10顯示了本發(fā)明同一個實施例樣品抗酸測試的結(jié)果。附圖11顯示了本發(fā)明同一個實施例樣品抗堿測試的結(jié)果。具體實施方式本發(fā)明提供了一種具有無電鍍多涂層的裝飾性產(chǎn)品(即無需使用電鍍即可獲得多涂層)。本發(fā)明的一個實施例中,整個無電鍍涂層方法涉及三個主要步驟:基涂層涂布步驟、銀涂層涂布步驟和抗刮涂層涂布步驟。在一個實施例中,基涂層的厚度為17.5μm。在另一個實施例中,銀涂層的厚度為90nm。在另一個實施例中,抗刮涂層的厚度為2μm。下文將介紹每個步驟及所使用的材料。1.基涂層涂布步驟在將基涂層涂布在基底之前,準(zhǔn)備步驟可以任選地實施于基底上,即可于基底上實施表面拋光、表面清潔和/或表面預(yù)處理。在一個實施例中,所述基底可以是金屬基底。1.1表面預(yù)處理在一個特定實施例中,基底用預(yù)處理溶液進行預(yù)處理,預(yù)處理溶液由8.64ga1100、750ml乙醇和31.52g去離子水在室溫混合10分鐘而制 成。首先,基底和預(yù)處理溶液接觸,在室溫進行超聲10分鐘。然后,基底在烘箱100℃中干燥20分鐘,冷卻至室溫得到預(yù)處理基底。1.2.粘附涂層溶液和光滑涂層溶液的組成基涂層包括兩個原涂層:粘附涂層和光滑涂層。粘附涂層首先應(yīng)用于基底表面上用于增強基涂層與基底的粘性并且為被涂布的基底提供防腐蝕的性能。然后將光滑涂層應(yīng)用于粘附涂層上以提高基涂層光滑性從而增強基涂層與銀涂層的粘性。粘附涂層溶液和光滑涂層溶液的組成范圍分別列于表1a和2a。表1a粘附涂層溶液的組成范圍組成重量%范圍環(huán)氧樹脂(epoxy)e-5128.99%-32.04%byk-361n0.23%-0.26%乙醇6.96%-7.69%丙酮54.46%-60.19%tz-5504.36%-4.81%表2a光滑涂層溶液的組成范圍在一個特定實施例中,粘附涂層溶液和光滑涂層溶液的組成分別列于表1b和2b中。表1b粘附涂層溶液的組成表2b光滑涂層溶液的組成組成重量%環(huán)氧樹脂e-5144.17%byk-361n0.40%cge5.80%丙酮4.66%二丙酮醇24.98%正丁醇12.49%tz-5507.50%在一個實施例中,粘附涂層溶液或光滑涂層溶液中的丙酮充當(dāng)溶劑并可增加至粘附涂層溶液或光滑涂層溶液體積的90%。另外,在粘附涂層溶液和光滑涂層溶液中的溶劑(即丙酮)的不同重量比會導(dǎo)致兩種涂層溶液的不同蒸發(fā)速度。1.2.1粘附涂層溶液的制備在一個特定實施例中,粘附涂層溶液包括粘附原溶液和固化劑溶液。首先,粘附原溶液(1kg)通過將713.05g環(huán)氧樹脂e-51、171.15g丙酮和115.8g乙醇在室溫混合至形成均勻溶液而制成。固化劑溶液(1kg)由33.90gbyk-361n、636.80gtz-550和329.30g乙醇在室溫混合至形成均勻溶液而制成。之后,342.4g粘附原溶液、400.0g丙酮和57.6g固化劑溶液在室溫混合3分鐘,然后在水浴進行超聲波10分鐘,從而得到粘附涂層溶液。1.2.2光滑涂層溶液的制備在一個特定實施例中,光滑涂層溶液包括光滑原溶液和tz-500。首先,光滑原溶液(1kg)由477.55g環(huán)氧樹脂e-51、135.05g正丁醇、270.10g二丙酮醇、50.35g丙酮、62.65gcge和4.30gbyk-361n在室溫混合至形成均勻溶液而制成。之后,925.0g光滑原溶液與75.0gtz-550在室溫混合3分鐘,然后在水浴進行超聲波10分鐘,從而得到光滑涂層溶液。1.3偶聯(lián)劑a1100偶聯(lián)劑a1100被加到粘附涂層溶液中以增強環(huán)氧樹脂基礎(chǔ)的粘附涂層于基底表面之間的粘合。這種增強的粘合是由于a1100的nh基團與環(huán)氧樹脂的o基團相互作用導(dǎo)致這兩個功能基團很強的結(jié)合,如圖1所示。1.4粘附涂層涂布于基底由上述所制備的粘附涂層溶液首先經(jīng)過超聲波脫氣超過5分鐘。粘附涂層溶液通過刷、浸入或噴涂方式涂布于基底上。被涂布的基底經(jīng)150℃加熱硬化15分鐘。在一個特定實施例中,按下述方式將粘附涂層溶液噴涂在基底上。首先,將去離子水以22ml/min的速率、3bar的壓力噴涂于基底上。然后,在基底上噴涂丙酮,之后在基底上噴涂粘附涂層溶液30秒且噴槍距離基底約15cm。被涂布的基底經(jīng)150℃加熱硬化15分鐘。1.5光滑涂層涂布于被粘附涂層涂布的基底由上述所制備的光滑涂層溶液首先經(jīng)過超聲波脫氣超過10分鐘。光滑涂層溶液通過刷、浸入或噴涂方式涂布于粘附涂層上。被涂布的基底經(jīng)80℃涂布3-6小時。在一個特定實施例中,按下述方式將光滑涂層溶液噴涂在基底上。首先,將去離子水以55ml/min的速率、3bar的壓力噴涂于基底上。然后,在基底上噴涂丙酮,之后在基底上噴涂光滑涂層溶液30秒且噴槍距離基底約15cm。被涂布的基底經(jīng)80℃加熱硬化處理3-6小時。2銀涂層涂布步驟在這步驟中,通過氧化還原反應(yīng)銀被無電鍍涂布在基涂層上,其中銀銨復(fù)合物[ag(nh3)2]+與作為還原劑的葡萄糖反應(yīng)。2.1無電鍍涂層溶液無電鍍涂層溶液包括兩個溶液,硝酸銀基礎(chǔ)溶液和葡萄糖基礎(chǔ)溶液,其組合物的范圍如表3所示。表3硝酸銀基礎(chǔ)溶液和葡萄糖基礎(chǔ)溶液的組成在一個實施例中,硝酸銀在硝酸銀基礎(chǔ)溶液中的濃度范圍為7.5-20g/l。在另一個實施例中,葡萄糖在葡萄糖基礎(chǔ)溶液中的濃度范圍為5-20g/l。2.1.1硝酸銀基礎(chǔ)溶液的制備在一個特定的實施例中,硝酸銀基礎(chǔ)溶液由下述方式制備。6.00g氫氧化鈉和20ml去離子水在室溫混合直至所有固體溶解,從而獲得氫氧化鈉溶液。10g硝酸銀和100ml去離子水在室溫混合至所有固體溶解從而獲得硝酸銀溶液。氫氧化鈉溶液被加到硝酸銀溶液中直到棕色沉淀生成。30ml28%的氨水與60ml去離子水混合而得到氨水溶液。氨水溶液被滴加至氫氧化鈉和硝酸銀混合物直至所有棕色沉淀恰好再溶解從而獲得澄清溶液。澄清溶液最后被去離子水稀釋至1l從而得到硝酸銀基礎(chǔ)溶液。2.1.2葡萄糖基礎(chǔ)溶液的制備在一個特定的實施例中,葡萄糖基礎(chǔ)溶液通過將8.00g葡萄糖、0.54g檸檬酸、20ml乙醇和980ml水在室溫下混合直到形成均勻溶液而制備。2.1.3敏化液的制備在一個特定的實施例中,混合4.00gsncl2(氯化亞錫)和4ml37%鹽酸,然后將混合物在60℃加熱10分鐘直至形成澄清溶液。在室溫將800ml去離子水加入至澄清溶液中而獲得敏化液。2.2銀涂層涂布于有基涂層的基底上2.2.1清潔涂布有基涂層的基底用流動的丙酮和乙醇(體積比1:1)進行洗滌1分鐘,然后用去離子水洗滌1分鐘。環(huán)氧樹脂基礎(chǔ)的基涂層的清潔不僅去除未反應(yīng)的環(huán)氧樹脂殘基,而且使環(huán)氧樹脂表面變粗糙從而改善sn離子和銀的機械互鎖而可以在后面的步驟中粘附于環(huán)氧樹脂表面。2.2.2敏化在這步驟中,清潔后和干燥后的基底與氯化亞錫溶液接觸,然后用流動的去離子水洗滌基底,在烘箱90℃干燥,在空氣中冷卻至室溫。氯化亞錫作為敏化劑增強銀和基涂層的環(huán)氧樹脂表面的粘附。在一個實施例中,氯化亞錫在應(yīng)用在基底前先被氧化(例如被空氣氧化1天)。發(fā)明者發(fā)現(xiàn)一旦經(jīng)過氧化(或老化),一些sn2+將會氧化成sn4+,所產(chǎn)生的sn2+和sn4+的混合物對銀和環(huán)氧樹脂的粘附比只含有sn2+的“新鮮氯化亞錫”有更好的增強效果。在一個特定實施例中,按下述方式將敏化液噴涂在基底上。首先,將去離子水以10ml/min的速率、3bar的壓力噴涂于基底上。然后,敏化液在基底上噴涂30秒且噴槍在距離基底約5cm。2.2.3銀涂層涂布于基底敏化后,硝酸銀基礎(chǔ)溶液和葡萄糖基礎(chǔ)溶液在室溫同時交叉噴涂在敏化后的基底上0.5分鐘。交叉噴涂時,硝酸銀基礎(chǔ)溶液和葡萄糖基礎(chǔ)溶液的顆粒在接觸敏化的基底的表面前將形成精細的蒸發(fā)形式。因此,銀納米顆粒均勻?qū)?大約30-150nm的顆粒大小)可以通過交叉噴涂在基底上,所產(chǎn)生的產(chǎn)物比電鍍涂布銀的產(chǎn)物有相同或更好的光亮效果。之后,基底用去離子水洗滌,然后在100℃烘箱中干燥至少15分鐘。在一個實施例中,硝酸銀基礎(chǔ)溶液和葡萄糖基礎(chǔ)溶液的噴涂速率為3:2至1:3(例如12ml/min:8ml/min,8ml/min:8ml/min,8ml/min:12ml/min,8ml/min:16ml/min,or8ml/min:24ml/min等)。在另一個實施例中,硝酸銀基礎(chǔ)溶液的濃度是10g/l;葡萄糖基礎(chǔ)溶液的濃度是8g/l;硝酸銀基礎(chǔ)溶液的噴涂速率是10ml/min;葡萄糖基礎(chǔ)溶液的噴涂速率是20ml/min。在另一個特定實施例中,硝酸銀基礎(chǔ)溶液和葡萄糖基礎(chǔ)溶液以下述方法噴涂在基底上。首先敏化的基底用去離子水沖洗1分鐘,然后使用雙頭噴槍,去離子水通過第一個噴頭以10ml/min的速率噴涂基底,去離子水通過第二個噴頭以20ml/min的速率噴涂基底,雙噴槍距離基底約40cm。之后硝酸銀基礎(chǔ)溶液和葡萄糖基礎(chǔ)溶液分別通過第一和第二個噴頭同時噴涂在基底上60秒,第一個噴頭以10ml/min的速率噴涂基底,第二個噴頭以20ml/min的速率噴涂基底,雙噴槍距離基底約40cm。涂布的基底用去離子水清洗1分鐘,在壓縮空氣中干燥30秒,在100℃加熱硬化15分鐘,再冷卻至室溫。2.2.4抗氧化處理銀涂布的基底可以任選地被處理以增強抗氧化效果。在這步驟中,基底與抗氧化溶液在40℃相接觸5分鐘,基底然后用去離子水洗滌超過3次并在室溫干燥。2.3葡萄糖為還原劑us4,737,188(188專利)描述過還原劑在無電鍍涂層的使用中不穩(wěn)定,其中氫會釋放和/或還原糖被降解為沉淀物或其他副產(chǎn)物。另外,轉(zhuǎn)化糖作為還原劑需要更高的溫度來使銀有效的沉積。例如,188專利討論了銀沉積在43-54℃以下時效果不好而且成本高。本發(fā)明中,發(fā)明者成功利用葡萄糖作為還原劑有效地將銀納米顆粒均勻?qū)映练e在基底的環(huán)氧樹脂表面。而且銀層的沉積過程(即噴涂過程)是在室溫進行,比188專利所需要的溫度要低得多。3抗刮涂層涂布步驟在這步驟中,含硅的抗刮涂層涂布在銀涂層上以提高被涂布基底的抗刮性能。3.1抗刮涂層溶液的組成抗刮涂層溶液的組成范圍列于表4a。表4a抗刮涂層溶液的組成范圍在一個特定實施例中,抗刮涂層溶液的組成列于表4b中。表4b抗刮涂層溶液的組成組成重量%mtms34.57%a1894.00%正丁醇12.04%乙酸1.21%去離子水13.65%3%硅膠1.21%二丙酮醇33.32%結(jié)晶紫0.01%3.1.1抗刮涂層溶液的制備在一個特定實施例中,36.0ga189、311.2gmtms、122.9g去離子水、10.8g乙酸、108.3g正丁醇和10.8g3%硅膠在室溫混合15分鐘,所得溶液在水浴中超聲波45分鐘,在70℃加熱10小時并冷卻到室溫。然后在冷卻的溶液中加0.11g結(jié)晶紫和300g二丙酮醇從而得到抗刮涂層溶 液。3.2偶聯(lián)劑a189a189,(3-巰基丙基)三甲氧基硅烷的化學(xué)結(jié)構(gòu)如下式(i)所示(i)在將抗刮涂層應(yīng)用于銀涂層上時,偶聯(lián)劑a189與硅基礎(chǔ)抗刮涂層溶液混合應(yīng)用于銀涂層上以增強硅基礎(chǔ)抗刮涂層與銀涂層的粘附。這種增強的粘附是由于a189的sh基團和銀涂層的銀表面相互作用形成強的結(jié)合而形成,如圖2所示。3.3結(jié)晶紫如有需要,可將結(jié)晶紫加入抗刮涂層溶液中改善被涂布產(chǎn)物的外觀。尤其,加入結(jié)晶紫可除去銀涂層的銀表面的微黃的副效果。3.4抗刮涂層涂布于有銀涂層的基底涂布有銀涂層的基底與上述抗刮涂層溶液接觸超過1分鐘,基底在100℃加熱超過18小時,再在150℃處理3小時,從而得到具有多涂層的基底。在一特定實施例中,抗刮涂層溶液以下述方式噴涂在基底上。首先將去離子水以8ml/min的速率、3bar的壓力噴涂在基底上,然后在基底上噴涂抗刮涂層溶液35秒,噴槍距離基底約15cm,噴涂的基底在150℃加熱硬化3小時。4樣品測試由上述方法制備的裝飾產(chǎn)物(無電鍍樣品)與電鍍方式涂布銀的的產(chǎn)品(電鍍樣品)進行比較測試。金屬基底用于無電鍍樣品和電鍍樣品的是鋼q-195a和/或鋅合金#3。4.1裝飾測試無電鍍樣品和電鍍樣品在45度380-780nm的角反射用uv-vis分光光度計測量。如圖3所示,無電鍍樣品比電鍍樣品有更高的角反射。無電鍍樣品的反射面積是26,264而電鍍樣品的反射面積是17,911。因此無電鍍樣品比電鍍樣品具有更好的裝飾效果。4.2粘附測試參考iso2409:2007漆畫和清畫用膠帶測試測量粘附的astmd3359-08標(biāo)準(zhǔn)測試方法被采用(劃格測試)。如圖4所示結(jié)果表明,無電鍍樣品沒有碎片脫落,達到5b標(biāo)準(zhǔn)(0%的測試面積脫落),表明測試面積沒有脫落,比4b標(biāo)準(zhǔn)更好(有少于5%的測試面積脫落)。因此這些涂層,尤其是銀涂層不容易從無電鍍樣品脫落。4.3抗腐蝕測試參考iso9227:2006在人工調(diào)節(jié)空氣中腐蝕測試,操作鹽噴(fog)儀器的astmb117-07標(biāo)準(zhǔn)方法被采用(鹽噴測試-72小時無腐蝕)。如圖5所示結(jié)果表明無電鍍樣品沒有可視變化。因此無電鍍樣品表現(xiàn)出抗腐蝕性。4.4沖擊測試用于有機涂層抗快速變形的astmd2794-93(2004)標(biāo)準(zhǔn)測試方法被采用(鋼球沖擊-無可見裂痕)。如圖6所示,無電鍍樣品無可見裂痕。因此表明無電鍍樣品不易變形。4.5硬度測試參考iso15184:1998漆畫和清畫用鉛筆測試涂膜硬度的astmd3363-05標(biāo)準(zhǔn)測試方法被采用(鉛筆測試-≥2小時)。如圖7所示結(jié)果表明無電鍍樣品可持續(xù)此測試3-4小時。因此表明無電鍍樣品表面能抗刮。4.6rohs指令測試這個測試參考香港通用檢測認(rèn)證有限公司iec62321:2008執(zhí)行。如表5所示,無電鍍樣品沒有檢測到cd,pb,hg,cr(vi),pbbs,pbde。無電鍍樣品也沒有檢測出毒性重金屬或碳氫物,因此是環(huán)保的。表5無電鍍樣品的rohs指令測試4.7uv照射測試參考iso4892-3,用于非金屬材料的uv照射的熒光燈儀器的astmg154-04標(biāo)準(zhǔn)方法并且暴露模式1/2被采用。如圖8所示無電鍍樣品無可見顏色變化。因此無電鍍樣品的涂層表現(xiàn)有抗uv光保護作用。4.8防水測試在這個測試中,無電鍍樣品浸泡在40℃水中24小時。如圖9所示無電鍍樣品無可見顏色變化。因此表明無電鍍樣品是防水的。4.9抗酸測試在這個測試中,無電鍍樣品浸泡在室溫0.1n硫酸中24小時。如圖10所示無電鍍樣品無可見顏色變化。因此表明無電鍍樣品是抗酸的。4.10抗堿測試在這個測試中,無電鍍樣品浸泡在室溫0.1n氫氧化鈉中24小時。如圖11所示無電鍍樣品無可見顏色變化。因此表明無電鍍樣品是抗堿的。因此本發(fā)明的示例性實施方案已被完整地描述了。盡管說明書提到具體實施方案,但本領(lǐng)域技術(shù)人員清楚,可以用這些具體細節(jié)的變化來實施本發(fā)明。因此本發(fā)明不應(yīng)被解釋為限于這里闡述的實施方案。例如,丙酮可用在本發(fā)明的方法中作為溶劑,但本領(lǐng)域人員知曉其他化學(xué)試劑例如甲醇、苯、三乙胺、乙酸、氯苯、苯酚和喹諾酮也可以使用。而且,本領(lǐng)域人員可以理解噴涂時間可以根據(jù)不同因素變化而變化,例如被噴涂的基底和噴涂環(huán)境等。當(dāng)前第1頁12