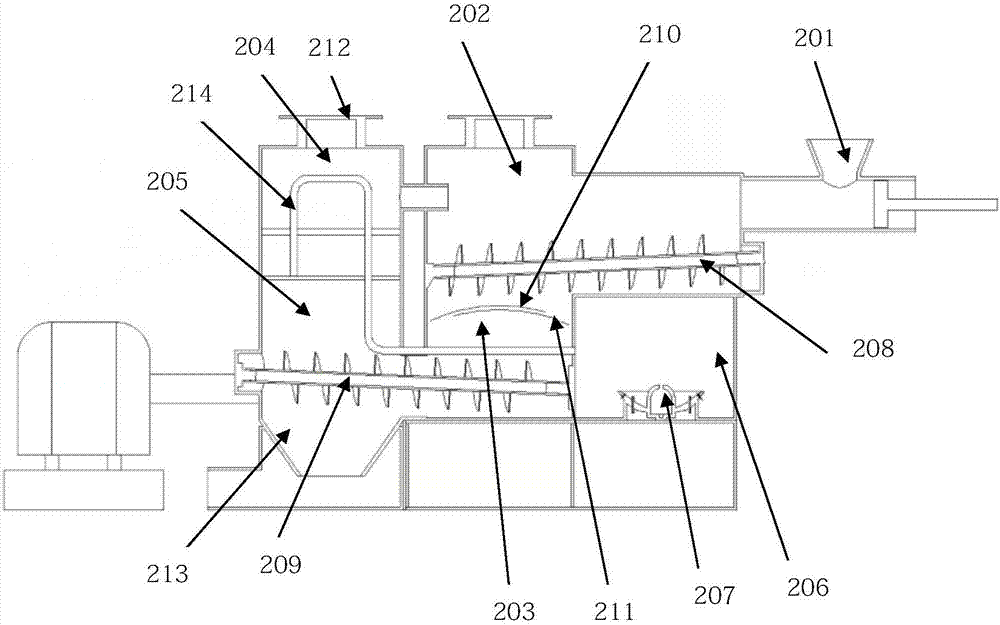
本發(fā)明涉及危險廢物無害化處理
技術(shù)領(lǐng)域:
,尤其涉及一種危險廢物無害化處理方法及裝置。
背景技術(shù):
:近年來,我國每年產(chǎn)生的工業(yè)廢物高達24億噸,其中一般工業(yè)固體廢物為23.52億噸,危險廢物為4800萬噸,并且每年還以12%的增長率快速增長。盡管國家加強了對工業(yè)固體廢物、特別是危險廢物的管理,但仍有40%左右的固體廢物沒有得到妥善處理,只是在企業(yè)內(nèi)部臨時貯存。據(jù)國家環(huán)境保護部統(tǒng)計,全國累計堆積的工業(yè)固體廢物已達到66億噸,占地約5.5萬傾,且每年呈不斷遞增的趨勢。有些大型企業(yè)雖然建起了填埋場,但由于沒有采取嚴(yán)格的防滲措施和缺乏科學(xué)的管理,仍存在污染地下水的情況。根據(jù)我國相關(guān)法律對危險廢物的定義,其是指具有腐蝕性、毒性、易燃性、反應(yīng)性或者感染性等一種或者幾種危險特性的;或者不排除具有危險特征,可能對環(huán)境或者人體健康造成有害影響,需要按照危險廢物進行管理的固體廢物。傳統(tǒng)的固廢處理方法包括填滿法、焚燒法、固化法和化學(xué)法。然而,四種處理方式均存在明顯缺陷。第一,填埋場占用土地量大、釋放腐臭有毒的氣體、產(chǎn)生易燃、易爆或毒性氣體;重金屬等致癌物在土壤申蓄積,造成土壤的永久性污染。第二,焚燒法會產(chǎn)生飛灰、煙塵、霧霾、pm2.5顆粒物和二噁英類劇毒污染物,還產(chǎn)生大量的酸性氣體和未完全燃燒的有機組分及爐渣。第三,固化法的固化體的浸出率較高,需作涂覆處理;由于油類、有機酸類、金屬氧化物等會妨礙凝結(jié)劑水化反應(yīng),需加大凝結(jié)劑的配比量,造成固化體增溶;固化體耐老化性能差,易破裂。第四,化學(xué)法只能處理少量例如是餐廚垃圾的有機物垃圾,絕大部分危險廢物都不能處理。中國專利(公告號cn101880538b)公開了一種新型生活垃圾熱解氣化焚燒處理方法,該方法以碎玻璃或硅酸鈉為原料,加入玻璃電熔爐中,啟動玻璃電熔爐,在1250~1500℃高溫下充分熔化成為玻璃液,經(jīng)過4~10小時穩(wěn)定化后,將城市生活垃圾連續(xù)從玻璃電熔爐的頂部加入到高溫玻璃液表面,經(jīng)過干燥、缺氧熱解和氣化,生活垃圾被轉(zhuǎn)化為小分子的可燃?xì)怏w,剩余的固體殘渣進入高溫玻璃液中被熔融轉(zhuǎn)化為玻璃液,新產(chǎn)生的玻璃液從玻璃電熔爐的溢流口流出,經(jīng)冷水水淬后成為惰性的玻璃渣。該專利提供的方法可將垃圾中的有機物全部轉(zhuǎn)化為高濃度的可燃?xì)怏w,熱解、氣化過程產(chǎn)生的煙氣量非常小,可燃?xì)怏w的含量超過70%,可以直接用于汽輪機發(fā)電。不產(chǎn)生焚燒飛灰和新的固體廢物。然而,該專利提供的方法至少還存在如下缺陷:(1)該專利僅對城市生活垃圾進行缺氧熱解和氣化,難以對組分復(fù)雜的工業(yè)固廢垃圾進行徹底處理,(2)該專利利用在1250~1500℃高溫下融化的玻璃液作為城市生活垃圾熱解和氣化的熱源,形成玻璃液所需的溫度高,使得該方法能量消耗大。另一方面,現(xiàn)有技術(shù)的危險廢物處理裝置還存在易堵塞、無法實現(xiàn)連續(xù)式生產(chǎn)、熱量和分解產(chǎn)生的氣體易噴出、對周圍環(huán)境影響大等諸多缺陷。技術(shù)實現(xiàn)要素:針對現(xiàn)有技術(shù)之不足,本發(fā)明提供了一種危險廢物無害化處理裝置。所述裝置至少包括熱解氣化裝置,所述熱解氣化裝置為至少具有無氧熱解倉、缺氧熱解倉、催化還原倉和熔融室的熱解氣化爐,其中,所述無氧熱解倉內(nèi)設(shè)有用于破碎所述危險廢物的第一攪拌器,所述熔融室在其下方的灰渣輸送管道中設(shè)有用于攪拌灰渣的第二攪拌器。優(yōu)選地,所述無氧熱解倉、所述缺氧熱解倉、所述催化還原倉和所述熔融室是按照一體且對外界環(huán)境隔離的方式設(shè)置的。其中,所述無氧熱解倉和所述缺氧熱解倉通過彼此貼合并能夠在沿垂直于所述第一攪拌器的軸向的方向上相對移動的第一分料盤和第二分料盤彼此分隔開,且所述第一分料盤靠近第一攪拌器的螺旋葉片端部,耐高溫的所述第一分料盤和所述第二分料盤均按照位置彼此對應(yīng)的方式設(shè)有在第一位置閉合但在第二位置敞開的通孔,其中,所述第一分料盤和所述第二分料盤沿所述第一攪拌器的軸向上觀察呈至少部分隆起的板狀件,所述第一分料盤和所述第二分料盤沿其自身縱向觀察呈中心隆起的弧形條狀件,使得所述第一分料盤僅在局部靠近所述第一攪拌器的螺旋葉片端部。優(yōu)選地,所述第一分料盤和所述第二分料盤由氮化物或碳化物中的一種制得。本發(fā)明的無氧熱解倉和缺氧熱解倉通過分料盤分隔開,使得所述無氧熱解倉內(nèi)分解產(chǎn)生的半焦化物能夠通過所述分料盤上的通道進入所述缺氧熱解倉并使得所述半焦化物在所述缺氧熱解倉內(nèi)分解產(chǎn)生的第二混合氣體能夠通過所述分料盤上的通道向上噴射入所述無氧熱解倉,所述第二混合氣體與在所述無氧熱解倉分解后產(chǎn)生的第一混合氣體混合后輸送至所述催化還原倉以使所述熱解氣化爐內(nèi)始終保持較穩(wěn)定的壓力環(huán)境。優(yōu)選地,所述熱解氣化爐內(nèi)始終保持非正壓的環(huán)境。更優(yōu)選地,所述熱解氣化爐內(nèi)的非正壓為-2000~-500pa。非正壓的環(huán)境避免了正壓操作導(dǎo)致的熱解氣化爐中熱量和分解的氣體向外噴出,從而不僅有利于氣體的生成,還可以解決現(xiàn)有技術(shù)中能量浪費,操作不安全的問題,也可以改善危險廢物處理的環(huán)境,實現(xiàn)綠色、環(huán)保、安全處理。進一步地,為了使所述熱解氣化爐內(nèi)保持較穩(wěn)定的壓力環(huán)境,分料盤包括能夠在沿垂直于所述第一攪拌器的軸向的方向上相對移動的第一分料盤和第二分料盤。優(yōu)選地,所述第一分料盤和所述第二分料盤均按照位置彼此對應(yīng)的方式設(shè)有在第一位置閉合但在第二位置敞開的通孔。所述第一分料盤和所述第二分料盤起初為彼此貼合的狀態(tài),通過使其執(zhí)行錯位運動,可以調(diào)整所述第一分料盤和所述第二分料盤上通孔的孔徑和數(shù)量。例如,在所述無氧熱解倉內(nèi)的半焦化物過多時,可使所述第一分料盤和所述第二分料盤執(zhí)行錯位運動來增大通孔的孔徑和/或數(shù)量,半焦化物從所述通孔中向下流入缺氧熱解倉中,缺氧熱解倉中的第二混合氣體可通過所述第一分料盤和所述第二分料盤執(zhí)行錯位運動后的縱向兩側(cè)的通孔和/或縫隙中向上進入所述無氧反應(yīng)倉。又例如,在爐內(nèi)熱解產(chǎn)生的危險氣體(例如易燃易爆氣體、有毒氣體等)過多時,可通過將所述第一分料盤和所述第二分料盤錯位運動至合適位置,從而使所述第一分料盤和所述第二分料盤上的通孔完全閉合,中斷熱解反應(yīng)的進行,提高設(shè)備的安全性。由于所述無氧熱解倉內(nèi)產(chǎn)生的為半焦化物,其黏度較大,容易積聚在所述第一分料盤上而造成通孔堵塞,本發(fā)明將所述第一分料盤和所述第二分料盤設(shè)置成沿所述第一攪拌器的軸向上觀察呈至少部分隆起的板狀件,沿其自身縱向觀察呈中心隆起的弧形條狀件,通過第一攪拌器的螺旋葉片的擠壓、刮擦和/或剪切作用從而有利于半焦化物的流動。同時,所述第一分料盤和所述第二分料盤在執(zhí)行錯位運動后,第一分料盤和所述第二分料盤的邊緣處形成寬度可變的第一臺階結(jié)構(gòu),所述第一分料盤和所述第二分料盤的通孔間還形成第二臺階,加之所述第一攪拌器的螺旋葉片端部靠近所述第一分料盤,螺旋葉片的旋動和所述第一分料盤和所述第二分料盤的錯位運動可以更好刮除積聚在所述第一分料盤和所述第二分料盤上的半焦化物。另一方面,熱解氣化爐長時間使用后,爐壁上不可避免地會因為半焦化物的積聚而加厚,本發(fā)明可通過中央控制機構(gòu)基于所述熱解氣化爐的工作時間和/或所述無氧熱解倉爐壁的厚度來控制所述第一分料盤和所述第二分料盤錯位運動行程。例如,在所述熱解氣化爐長時間工作后,可通過中央控制機構(gòu)控制所述第一分料盤和所述第二分料盤執(zhí)行大幅度的錯位運動,從而清除積聚在爐壁以及分料盤上的半焦化物。如此不僅可以避免氣孔堵塞,還能延長所述熱解氣化爐的清洗周期。本發(fā)明的第一分料盤和第二分料盤為隆起結(jié)構(gòu),相較于現(xiàn)有技術(shù)的隔板,具有更大的承重量,不易被壓垮。根據(jù)一個優(yōu)選實施方式,分布于所述第一分料盤和所述第二分料盤邊緣上的通孔孔徑大于分布于所述第一分料盤和所述第二分料盤弧形隆起中心處的通孔孔徑,并且所述第一分料盤和所述第二分料盤靠近所述催化還原倉一側(cè)到遠(yuǎn)離所述催化還原倉一側(cè)的通孔孔徑呈先減小后增大的趨勢,且通孔排布密度呈逐漸增大的趨勢。本發(fā)明的通孔孔徑在中心小,在邊緣大,在靠近所述催化還原倉一側(cè)小,在遠(yuǎn)離所述催化還原倉一側(cè)大,更有利于半焦化物向下流入缺氧熱解倉中。另一方面,與第一攪拌器臨近的區(qū)域相比,通孔在遠(yuǎn)離第一攪拌器的區(qū)域具有更小的排布密度,進一步避免半焦化物在爐壁附近積聚,有利于實現(xiàn)危險廢物的連續(xù)式處理。根據(jù)一個優(yōu)選實施方式,所述第一分料盤和所述第二分料盤是由同一個驅(qū)動機構(gòu)來驅(qū)動并由位于中央的控制裝置來調(diào)節(jié)的,并且所述驅(qū)動機構(gòu)能夠在至少兩個方向上驅(qū)動所述第一分料盤和所述第二分料盤執(zhí)行錯位運動,以調(diào)節(jié)通孔的孔徑并補償長時間工作后與所述第一分料盤和所述第二分料盤抵接的爐壁的厚度變化。優(yōu)選地,所述第一分料盤和所述第二分料盤可以通過外設(shè)的驅(qū)動機構(gòu)而彼此錯位;不僅在軸向上,而且在徑向上進行移位,改變通孔的孔徑,進而可以適應(yīng)處理不同的危險廢棄物。熱解氣化爐長時間使用后,爐壁上不可避免地會因為半焦化物的積聚而加厚,通過中央控制機構(gòu)控制所述第一分料盤和所述第二分料盤執(zhí)行錯位運動,可以清除積聚在爐壁以及分料盤上的半焦化物,從而補償長時間工作后與所述第一分料盤和所述第二分料盤抵接的爐壁的厚度變化。根據(jù)一個優(yōu)選實施方式,所述第一分料盤和所述第二分料盤在所述驅(qū)動機構(gòu)的驅(qū)動下執(zhí)行沿著所述危險廢物輸送方向的錯位運動并在遠(yuǎn)離所述催化還原倉的一側(cè)形成至少兩個寬度可變的臺階結(jié)構(gòu),并且所述熱解氣化爐通過靠近所述第一分料盤的螺旋葉片的擠壓、刮擦和/或剪切作用而使所述無氧熱解倉內(nèi)產(chǎn)生的半焦化物從所述第一分料盤和所述第二分料盤上中心區(qū)域的通孔中落入所述缺氧熱解倉內(nèi),并使得所述缺氧熱解倉內(nèi)產(chǎn)生的第二混合氣體從所述第一分料盤和所述第二分料盤縱向兩側(cè)的孔徑可調(diào)的通孔向上進入所述無氧熱解倉內(nèi)。優(yōu)選的,至少兩個寬度可變的臺階結(jié)構(gòu)為第一分料盤和第二分料盤邊緣處形成的第一臺階和第一分料盤和第二分料盤上的通孔形成的多個第二臺階。優(yōu)選地,所述的縱向兩側(cè)為與所述第一分料盤和所述第二分料盤錯位運動方向相垂直的兩側(cè)。根據(jù)一個優(yōu)選實施方式,所述驅(qū)動機構(gòu)也用于調(diào)節(jié)設(shè)置于所述催化還原倉頂端的活動風(fēng)門、所述第一攪拌器和設(shè)置于所述熔融室下方的灰渣輸送管道中的第二攪拌器,其中,所述驅(qū)動機構(gòu)的中央控制機構(gòu)根據(jù)對所述無氧熱解倉的第一參數(shù)集的分析結(jié)果并參考所述第一攪拌器的轉(zhuǎn)速和轉(zhuǎn)動方向來調(diào)節(jié)所述活動風(fēng)門的開合度和所述第二攪拌器的轉(zhuǎn)動模式,并根據(jù)所述無氧熱解倉和所述催化還原倉內(nèi)的氣體壓力和/或一種或多種氣體的濃度來調(diào)整所述第一分料盤和所述第二分料盤的錯位運動行程。優(yōu)選地,所述第一參數(shù)集為所述無氧熱解倉、所述缺氧熱解倉、所述催化還原倉、所述熔融室內(nèi)的壓力、溫度、氣體濃度中的一種或多種,通過分析結(jié)果并參考第一攪拌器的轉(zhuǎn)速和轉(zhuǎn)動方向來調(diào)節(jié)所述活動風(fēng)門的開合度和所述第二攪拌器的轉(zhuǎn)動模式,以及根據(jù)所述無氧熱解倉和所述催化還原倉內(nèi)的氣體壓力和/或一種或多種氣體的濃度來調(diào)整所述第一分料盤和所述第二分料盤的錯位運動,不僅可使熱解氣化爐內(nèi)保持穩(wěn)定的壓力,還能避免可燃?xì)怏w濃度過大造成的爆炸和/或有害氣體濃度過大造成的外噴。根據(jù)一個優(yōu)選實施方式,所述驅(qū)動機構(gòu)包括分別與所述無氧熱解倉、所述缺氧熱解倉、所述催化還原倉、所述熔融室機械連接的第一至第四驅(qū)動馬達以及分別用于控制所述第一至第四驅(qū)動馬達的第一至第四控制器,其中,所述中央控制機構(gòu)分別用于控制所述第一至第四控制器的第一至第四控制電路分別集成到所述第一至第四控制器中,并且所述第一至第四控制電路基于所述第一至第四驅(qū)動馬達的驅(qū)動狀態(tài)以及所述熱解氣化爐內(nèi)的壓力和/或溫度并按照就所述無氧熱解倉、所述缺氧熱解倉、所述催化還原倉和/或所述熔融室而言最佳的反應(yīng)參數(shù)來向所述第一至第四馬達控制器發(fā)送控制指令。其中,所述控制指令為所述第一至第四驅(qū)動馬達的轉(zhuǎn)速設(shè)定值和/或最大電流設(shè)定值。優(yōu)選地,就所述無氧熱解倉、所述缺氧熱解倉、所述催化還原倉和/或所述熔融室而言最佳的反應(yīng)參數(shù)可以是指各部件的使用壽命或各部件的狀態(tài),如轉(zhuǎn)速、功率等。本發(fā)明的所述驅(qū)動機構(gòu)設(shè)置在所述熱解氣化爐外,且多個部件共用一個驅(qū)動機構(gòu),可避免其受高溫影響,且易于實現(xiàn)多功能的協(xié)調(diào)一致控制。另一方面,本發(fā)明采用一體式且唯一的驅(qū)動機構(gòu),易于維護,提高了爆炸環(huán)境下的安全性。根據(jù)一個優(yōu)選實施方式,所述驅(qū)動控制機構(gòu)基于所述無氧熱解倉、所述缺氧熱解倉、所述催化還原倉、所述熔融室內(nèi)熱解得到的氣體壓力和/或一種或多種氣體的濃度并通過與所述缺氧熱解倉機械連接的第二驅(qū)動馬達來協(xié)調(diào)控制所述第一分料盤和所述第二分料盤執(zhí)行錯位運動的行程以增大或減小氣體通道的供氣體流過的孔徑,和/或通過與所述催化還原倉機械連接的第三驅(qū)動馬達來協(xié)調(diào)控制所述活動風(fēng)門的最大允許排風(fēng)量和/或最小允許排風(fēng)量,和/或通過與所述無氧熱解倉和所述熔融室分別機械連接的第一驅(qū)動馬達和第四驅(qū)動馬達來協(xié)調(diào)控制所述第一攪拌器和所述第二攪拌器的攪拌方向、攪拌速度和攪拌時間。根據(jù)一個優(yōu)選實施方式,所述第一攪拌器按照其靠近所述第一分料盤的一端更靠下的方式傾斜布置,并且所述第一攪拌器按照左旋方式設(shè)置的第一螺旋葉片在所述第一分料盤與所述第二分料盤彼此相向運動之時以反向于工作方向的方向旋轉(zhuǎn)。本發(fā)明的第一攪拌器以推進所述危險廢物的方向旋轉(zhuǎn),在需要清理所述第一分料盤和所述第二分料盤上積聚的半焦化物時,通過反向于工作方向的方向旋轉(zhuǎn),有助于將所述第一分料盤和所述第二分料盤上的積聚物刮除。根據(jù)一個優(yōu)選實施方式,所述第一攪拌器沿著靠近所述第一分料盤的方向傾斜向下并使所述第一攪拌器上按照左旋方式設(shè)置的第一螺旋葉片的端部靠近所述第一分料盤,所述第二攪拌器沿著所述灰渣出口方向傾斜向下設(shè)置并使所述第二攪拌器上第二螺旋葉片按照與所述第一螺旋葉片相反的方向設(shè)置,從而使得第一攪拌器和所述第二攪拌器之間具有多種轉(zhuǎn)動模式來適應(yīng)不同的工況。本發(fā)明的第一攪拌器和第二攪拌器設(shè)置于所述無氧熱解倉內(nèi)和所述灰渣輸送管道內(nèi)較低的位置,不僅可以對輸送物料進行破碎和混合,其螺旋葉片還能對生成的半焦化物或灰渣進行剪切,有利于物料的連續(xù)輸送,另一方面,本發(fā)明第二攪拌器的攪拌棒傾斜方向以及第二螺旋葉片旋轉(zhuǎn)方式按照與第一攪拌器相反的方式設(shè)置,有利于參考第一攪拌器的轉(zhuǎn)速和轉(zhuǎn)動方向來按照有利于保持爐內(nèi)穩(wěn)定壓力的方式調(diào)節(jié)所述第二攪拌器的轉(zhuǎn)動模式,并且所述第一攪拌器和所述第二攪拌器具有多種轉(zhuǎn)動模式,有利于適應(yīng)不同的工況。例如,在反應(yīng)起始階段,熱解氣化爐內(nèi)的灰渣較少,所述第二攪拌器可具有較小的攪拌速度。反應(yīng)中后期,熱解氣化爐內(nèi)的灰渣較多且灰渣中易夾帶未完全燃燒的焦化物,此時所述第二攪拌器需要較大的攪拌速度,并且需要正方向攪拌與逆方向攪拌交替進行以使焦化物完全燃燒后再排出熔融室。基于本發(fā)明提供的危險廢物無害化處理裝置,本發(fā)明的另一方面還提供了一種危險廢物無害化處理方法。所述方法至少包括預(yù)處理過程、熱解氣化過程和凈化過程,其中,所述預(yù)處理過程是對所述危險廢物進行降塵和除臭后進行分選并將選出的物質(zhì)分別輸送至熱解氣化爐中;所述熱解氣化過程是將經(jīng)過預(yù)處理的危險廢物在高溫、無氧和負(fù)壓環(huán)境下進行裂解生成第一混合氣體和半焦化物,并將所述半焦化物在高溫、缺氧和負(fù)壓環(huán)境下再次進行一次或多次熱解氣化反應(yīng)以生成第二混合氣體和焦化物,將所述第一混合氣體和所述第二混合氣體在還原性環(huán)境下進行催化還原以生成可燃?xì)怏w,將所述焦化物在高溫、負(fù)壓環(huán)境下熔融以生成灰渣;所述凈化過程是將所述可燃?xì)怏w冷卻、分離后的氣體依次經(jīng)過脫氯脫酸凈化塔凈化后再通過過濾塔濾除灰塵和焦油以作為燃料輸送至所述加熱室為所述熱解氣化爐供熱。所述熱解氣化過程是在具有如下結(jié)構(gòu)的熱解氣化爐中完成的:所述熱解氣化爐具有無氧熱解倉、缺氧熱解倉、催化還原倉和熔融室,其中,所述無氧熱解倉內(nèi)設(shè)有用于破碎所述危險廢物的第一攪拌器,所述熔融室在其下方的灰渣輸送管道中設(shè)有用于攪拌灰渣的第二攪拌器,所述無氧熱解倉、所述缺氧熱解倉、所述催化還原倉和所述熔融室是按照一體且對外界環(huán)境隔離的方式設(shè)置的,其中,所述無氧熱解倉和所述缺氧熱解倉通過彼此貼合并能夠在沿垂直于所述第一攪拌器的軸向的方向上相對移動的第一分料盤和第二分料盤彼此分隔開,耐高溫的所述第一分料盤和所述第二分料盤均按照位置彼此對應(yīng)的方式設(shè)有在第一位置閉合但在第二位置敞開的通孔,其中,所述第一分料盤和所述第二分料盤沿所述第一攪拌器的軸向上觀察呈至少部分隆起的板狀件,所述第一分料盤和所述第二分料盤沿其自身縱向觀察呈中心隆起的弧形條狀件,使得所述第一分料盤僅在局部靠近所述第一攪拌器的螺旋葉片端部。本發(fā)明的危險廢物在處理過程中無臭氣、煙氣、粉塵、廢水、pm2.5顆粒物排放,不產(chǎn)生滲濾液和二噁英,能有效固化重金屬;危險廢物熱解后剩余的炭渣通過熔融燃燒后成為無害灰渣,可用于制作有機肥料或就地掩埋。另一方面,本發(fā)明的危廢減量率達到99%以上,可燃物體積由1立方減少至0.01立方;并且資源化利用率達到99%,處理1噸有機可燃物,可獲得400立方米的燃料氣體。該燃料氣體經(jīng)凈化處理后,可作為熱解氣化爐的輔助燃料循環(huán)利用,實現(xiàn)能量自我循環(huán)。附圖說明圖1是本發(fā)明危險廢物無害化處理系統(tǒng)的模塊示意圖;圖2是本發(fā)明熱解氣化爐的結(jié)構(gòu)示意圖;圖3是本發(fā)明第一分料盤和第二分料盤執(zhí)行錯位運動后的結(jié)構(gòu)示意圖;圖4是本發(fā)明燃燒頭的剖面結(jié)構(gòu)示意圖;圖5是本發(fā)明燃燒頭的噴孔布置位置的一個優(yōu)選實施方式示意圖;圖6是本發(fā)明處理玻璃鋼廢料的一個優(yōu)選實施方式工藝流程圖;和圖7是本發(fā)明處理皮革廢料的一個優(yōu)選實施方式工藝流程圖。附圖標(biāo)記列表10:預(yù)處理裝置20:熱解氣化裝置30:凈化裝置40:能量回收裝置101:負(fù)氧除臭裝置102:分選裝置201:進料口202:無氧熱解倉203:缺氧熱解倉204:催化還原倉205:熔融室206:加熱室207:燃燒頭208:第一攪拌器209:第二攪拌器210:第一分料盤211:第二分料盤212:活動風(fēng)門213:出渣口214:輸送管207a:噴孔210a:第一臺階210b:第二臺階301:冷卻塔302:氣液分離設(shè)備303:凈化塔304:過濾塔具體實施方式下面結(jié)合附圖和實施例進行詳細(xì)說明。本發(fā)明的危險廢物無害化處理方法和裝置是在熱解技術(shù)原理基礎(chǔ)上,將催化技術(shù)、氣化技術(shù)、還原技術(shù)與熱解技術(shù)相結(jié)合的一種新技術(shù)。其原理是利用危險廢物中的有機物的熱不穩(wěn)定性,在無氧和缺氧條件下對其進行加熱分解,使有機物產(chǎn)生熱裂解以獲得混合氣體和半焦化物或焦化物?;旌蠚怏w中的二氧化碳、水蒸汽、有機化合物溶劑及焦油等,通過熱解氣化爐進行二次反應(yīng),轉(zhuǎn)化為可燃?xì)怏w。半焦化物或焦化物通過熔融后獲得無害的灰渣和高溫?zé)煔猓桓邷責(zé)煔庵械亩趸己退魵馔ㄟ^催化還原反應(yīng)生成一氧化碳和氫氣等燃料氣體循環(huán)使用。圖1示出了本發(fā)明危險廢物無害化處理系統(tǒng)的模塊示意圖。如圖1所示,危險廢物無害化處理裝置至少還包括預(yù)處理裝置10、熱解氣化裝置20、凈化裝30和能量回收裝置40。優(yōu)選地,預(yù)處理裝置10至少包括負(fù)氧除臭裝置101和分選裝置102,并且負(fù)氧除臭裝置101和分選裝置102用于對危險廢物降塵、除臭和分選。優(yōu)選地,熱解氣化裝置20為熱解氣化爐。優(yōu)選地,凈化裝置30至少包括冷卻塔301、氣液分離設(shè)備302、凈化塔303和過濾塔304。凈化裝置30通過冷卻塔301對可燃?xì)怏w冷卻后再通過氣液分離設(shè)備302分離出液體油和氣體,并且依次通過凈化塔303和過濾塔304對分離出的氣體凈化。優(yōu)選地,能量回收裝置40為熱交換器。熱交換器將可燃?xì)怏w在加熱室206中充分燃燒后產(chǎn)生的煙氣中的熱能回收。本發(fā)明的危險廢物處理裝置預(yù)處理裝置10、熱解氣化裝置20、凈化裝30和能量回收裝置40設(shè)置成一體化系統(tǒng),從而使得整個設(shè)備占地面積較小,無需龐大的尾氣處理裝置,在一個系統(tǒng)內(nèi)實現(xiàn)了熱解、氣化、還原和凈化處理,從而實現(xiàn)危險廢物的無害化處理。實施例1圖2示出了本發(fā)明熱解氣化爐的結(jié)構(gòu)示意圖。如圖2所示,熱解氣化爐至少具有進料口201、無氧熱解倉202、缺氧熱解倉203、催化還原倉204、熔融室205、加熱室206和出渣口213。無氧熱解倉202內(nèi)設(shè)有用于破碎危險廢物的第一攪拌器208。熔融室205在其下方的灰渣輸送管道中設(shè)有用于攪拌灰渣的第二攪拌器209。無氧熱解倉202、缺氧熱解倉203、催化還原倉204和熔融室205是按照一體且對外界環(huán)境隔離的方式設(shè)置的。無氧熱解倉202設(shè)置于缺氧熱解倉203上方并通過彼此貼合并能夠在沿垂直于第一攪拌器208的軸向的方向上相對移動的第一分料盤210和第二分料盤211彼此分隔開。催化還原倉204設(shè)置于無氧熱解倉的一側(cè)并通過氣體輸送管道與之連通。熔融室205設(shè)置于催化還原倉204的下方并通過半焦化物輸送管道與缺氧熱解倉203連通。出渣口213設(shè)置于熔融室205下方。根據(jù)一個優(yōu)選實施方式,熱解氣化爐一端的上部設(shè)有連續(xù)上料密封裝置,連續(xù)上料密封裝置與無氧熱解倉202一端的進料口通道連接。無氧熱解倉202的另一端連接缺氧熱解倉203。優(yōu)選地,連續(xù)上料密封裝置包括壓縮式密封筒、活塞式推料筒、進料口201、進料口壓蓋。其中,壓縮式密封筒上方的開口為進料口201?;钊酵屏贤苍O(shè)在壓縮式密封筒遠(yuǎn)離無氧熱解倉202的一端,活塞式推料筒設(shè)有推料活塞,壓縮式密封筒內(nèi)設(shè)有密封塞,密封塞包括分別設(shè)在壓縮式密封筒內(nèi)壁上方及左右兩側(cè)的密封條。進料口201一側(cè)的壓縮式密封筒上向外設(shè)有進料口壓蓋。連續(xù)上料密封裝置的作用是通過物料壓縮的方式將危險廢物推入一體式熱解氣化爐內(nèi)并堵塞進料通道,隔絕爐內(nèi)和爐外氣體流通,保障一體式熱解氣化爐連續(xù)工作上料時,爐內(nèi)的氣體不外泄,爐外的空氣進不來,保證危險廢物無氧熱解。根據(jù)一個優(yōu)選實施方式,無氧熱解倉202為臥式圓筒或長方體,其設(shè)置于加熱室206上方。缺氧熱解倉203中下部設(shè)有加熱管。缺氧熱解倉203與加熱室206由隔板隔開。缺氧熱解倉203底部橫設(shè)有輸送管214。輸送管214一端外側(cè)為加熱室206,另一端與熔融室205連接。熔融室205設(shè)置于催化還原倉204下方并與催化還原倉204和缺氧熱解倉203通過網(wǎng)狀隔料板彼此分隔開。催化還原倉204底部設(shè)有燃?xì)馐占瘋},下部設(shè)有網(wǎng)狀隔料板,中部設(shè)有加熱管,上部設(shè)有活動風(fēng)門212。無氧熱解倉202、缺氧熱解倉203及熔融室205分別由管道與催化還原倉204連接。在熔融室205內(nèi)產(chǎn)生的高溫?zé)煔庀蛏蠂娚淙氪呋€原倉204。熔融室205內(nèi)產(chǎn)生的灰渣經(jīng)輸送管道輸送至出渣口213并通過呈傾斜設(shè)置的出渣口213輸送至水封式灰渣箱中。熔融室205另一端與水封式灰渣箱連接,熔融室205產(chǎn)生的灰渣進入水封式灰渣箱。熔融室205焚燒產(chǎn)生的高溫?zé)煔馔ㄟ^管道提供給缺氧熱解倉203,作為缺氧熱解倉203熱能來源的一部分。在連續(xù)出渣時,水封式灰渣箱不僅可防止?fàn)t外空氣通過灰渣排出口進入熱解氣化爐內(nèi),還可保障熱解氣化爐內(nèi)出現(xiàn)一定壓力時自動泄壓,保障熱解氣化爐的運行安全。如圖3所示,第一分料盤210和第二分料盤211均按照位置彼此對應(yīng)的方式設(shè)有在第一位置閉合但在第二位置敞開的通孔,其中,第一分料盤210和第二分料盤211沿第一攪拌器208的軸向上觀察呈至少部分隆起的板狀件,第一分料盤210和第二分料盤211沿其自身縱向觀察呈中心隆起的弧形條狀件。優(yōu)選地,分布于第一分料盤210和第二分料盤211邊緣上的通孔孔徑大于分布于第一分料盤210和第二分料盤211弧形隆起中心處的通孔孔徑,并且第一分料盤210和第二分料盤211靠近催化還原倉204一側(cè)到遠(yuǎn)離催化還原倉204一側(cè)的通孔孔徑呈先減小后增大的趨勢,且通孔排布密度呈逐漸增大的趨勢。根據(jù)一個優(yōu)選實施方式,第一分料盤210和第二分料盤211在驅(qū)動機構(gòu)的驅(qū)動下執(zhí)行沿著危險廢物輸送方向的錯位運動并在遠(yuǎn)離催化還原倉204的一側(cè)形成寬度可變的第一臺階210a,第一分料盤210和第二分料盤211的通孔間還形成第二臺階210b。形成的臺階結(jié)構(gòu)如圖3所示。優(yōu)選地,第一分料盤210和第二分料盤211執(zhí)行錯位運動后形成的第二臺階210b有多個。熱解氣化爐通過靠近第一分料盤210的螺旋葉片的擠壓、刮擦和/或剪切作用而使無氧熱解倉202內(nèi)產(chǎn)生的半焦化物從第一分料盤210和第二分料盤211上中心區(qū)域的通孔中落入缺氧熱解倉203內(nèi),同時,缺氧熱解倉203內(nèi)產(chǎn)生的第二混合氣體從第一分料盤210和第二分料盤211縱向兩側(cè)的縫隙向上進入無氧熱解倉202內(nèi)。第一分料盤210和第二分料盤211執(zhí)行錯位運動并形成寬度可變的臺階結(jié)構(gòu),不僅可以調(diào)整通孔的孔徑和數(shù)量,更重要的是能夠強化第一攪拌器208的螺旋葉片在旋動時對積聚在第一分料盤210和第二分料盤211上的半焦化物的刮擦作用。根據(jù)一個優(yōu)選實施方式,無氧熱解倉202、缺氧熱解倉203、熔融室205和/或催化還原倉204為立式和/或臥式的圓筒形結(jié)構(gòu)或長條結(jié)構(gòu)且圓筒形外殼是由多個弧形受熱管拼接而成。弧形受熱管的弧度為60~90°且弧形受熱管的內(nèi)徑為無氧熱解倉202、缺氧熱解倉203、熔融室205和/或催化還原倉204內(nèi)徑的0.1%~1%。由多個弧形受熱管拼接而成,有利于無氧熱解倉202、缺氧熱解倉203、熔融室205和/或催化還原倉204的受熱。根據(jù)一個優(yōu)選實施方式,加熱室206為立式形。加熱室206下部設(shè)有爐排和供風(fēng)管,兩側(cè)壁設(shè)有二次供風(fēng)噴嘴,其中一側(cè)壁還設(shè)有維修觀察孔。加熱室206向無氧熱解倉202、缺氧熱解倉203、催化還原倉204和熔融室205提供熱能。加熱室206使用的燃料為危險廢物有機物產(chǎn)生的熱解氣體,初次加熱升溫時,加熱室206使用的燃料為柴油或煤炭、焦炭、農(nóng)業(yè)廢棄物秸稈,將其置于爐排上。根據(jù)一個優(yōu)選實施方式,供風(fēng)管為加熱室206提供的空氣通過呈45~75°傾斜設(shè)置的爐排分散后進入加熱室206。加熱室206還通過設(shè)置于燃燒頭207兩側(cè)的供風(fēng)噴嘴為加熱室206提供空氣。供風(fēng)噴嘴上方還配有至少一個探測口,探測口用于監(jiān)測加熱室206的燃燒狀態(tài)。如圖4和圖5所示,由高溫耐火材料制成的燃燒頭207呈半圓形結(jié)構(gòu),并且半圓形結(jié)構(gòu)的燃燒頭207的弧面上按經(jīng)、緯線方向間隔布置有多個直徑為15~30mm的噴孔207a。為了避免加熱室內(nèi)的燃料氣體燃燒不充分,本發(fā)明通過在加熱室內(nèi)增設(shè)供風(fēng)噴嘴,可以確保燃料氣體的充分燃燒。另一方面,本發(fā)明通過設(shè)置的探測口可監(jiān)測加熱室內(nèi)的燃燒狀態(tài),避免溫度過低或過高。本發(fā)明的熱解氣化爐實現(xiàn)多功能裝置一體化,提高熱能利用率和工作效率;該熱解氣化爐將無氧熱解、缺氧分解、熔融焚燒、催化還原反應(yīng)等集中于一個處理裝置內(nèi),實現(xiàn)裝置內(nèi)熱能共享及實現(xiàn)裝置能源自我循環(huán)利用,提高熱能利用率;熱解處理裝置可做到連續(xù)進料和連續(xù)出渣,實現(xiàn)自動化控制,保障設(shè)備穩(wěn)定運行和提高工作效率;減少輔助燃料的使用,降低處理成本,實現(xiàn)資源化綜合效益。實施例2本實施例在實施例1的基礎(chǔ)上,詳細(xì)說明本發(fā)明提供的危險廢物無害化處理方法。本發(fā)明的危險廢物無害化處理方法至少包括預(yù)處理過程、熱解氣化過程和凈化過程。其中,預(yù)處理過程是對危險廢物進行降塵和除臭后進行分選并將選出的物質(zhì)分別輸送至熱解氣化爐中。熱解氣化過程是將經(jīng)過預(yù)處理的危險廢物在高溫、無氧和負(fù)壓環(huán)境下進行裂解生成第一混合氣體和半焦化物,并將半焦化物在高溫、缺氧和負(fù)壓環(huán)境下再次進行一次或多次熱解氣化反應(yīng)以生成第二混合氣體和焦化物,將第一混合氣體和第二混合氣體在還原性環(huán)境下進行催化還原以生成可燃?xì)怏w。焦化物通過燃燒生成無害灰渣。凈化過程是將可燃?xì)怏w經(jīng)冷卻、分離后再依次經(jīng)過脫氯脫酸凈化塔凈化后再通過過濾塔濾除灰塵和焦油以作為燃料輸送至加熱室為熱解氣化爐供熱。根據(jù)一個優(yōu)選實施方式,危險廢物的預(yù)處理過程至少包括如下步驟:利用負(fù)氧除臭系統(tǒng)對危險廢物進行降塵和除臭。通過分選系統(tǒng)對危險廢物進行分選并將選出的篩上物輸送至熱解氣化爐中。其中,分選過程至少包括對危險廢物破碎、風(fēng)選、磁選和旋流分選。根據(jù)一個優(yōu)選實施方式,第一混合氣體至少包括二氧化碳、水蒸汽、一氧化碳和、甲烷、有機化合物溶劑和焦油。第二混合氣體至少包括二氧化碳和水蒸汽,沼氣至少包括甲烷、二氧化碳和水蒸汽。第一混合氣體、第二混合氣體和沼氣經(jīng)催化還原生成的可燃?xì)怏w至少包括一氧化碳、氫氣和甲烷。根據(jù)一個優(yōu)選實施方式,危險廢物的熱解氣化過程至少包括如下步驟:將危險廢物輸送至熱解氣化爐的無氧熱解倉202中。通過熱解氣化爐的加熱室206內(nèi)的燃料充分燃燒產(chǎn)生的高溫氣體對無氧熱解倉202中的物料加熱以使危險廢物的有機物分子鏈在高溫、無氧環(huán)境下進行裂解后生成第一混合氣體和半焦化物。將半焦化物輸送至熱解反應(yīng)爐的無氧熱解倉202或缺氧熱解倉203中進行第二次熱解氣化以產(chǎn)生第二混合氣體和焦化物。將無氧熱解倉202或缺氧熱解倉203中未完全分解的半焦化物或焦化物輸送至無氧熱解倉202或缺氧熱解倉203中進行第三次熱解氣化以產(chǎn)生第三混合氣體和焦化物,如此循環(huán),直至半焦化物完全分解為氣體和焦化物。根據(jù)一個優(yōu)選實施方式,加熱室206以可燃?xì)怏w氣體為燃料,并且可燃?xì)怏w充分燃燒產(chǎn)生的高溫氣體通過熱傳導(dǎo)或熱輻射的方式將熱能傳輸至無氧熱解倉202內(nèi)的物料層并按照危險廢物種類使物料層的溫度升高至500~1000℃,并使物料層的危險廢物在該溫度下反應(yīng)1~1.5h。根據(jù)一個優(yōu)選實施方式,可燃?xì)怏w的凈化過程至少包括如下步驟:將可燃?xì)怏w通過冷卻塔進行冷卻。將冷卻后的可燃?xì)怏w通過氣液分離設(shè)備分離出液體油和氣體。其中,分離出的液體油通過過濾裝置過濾后回收利用,分離出的氣體經(jīng)過脫氯脫酸凈化塔凈化后再通過過濾塔濾除灰塵和焦油以作為燃料輸送至加熱室206為熱解氣化爐供熱。本發(fā)明為防止后期二噁英再合成,設(shè)置脫氯凈化和尾氣急冷降溫裝置,從源頭上切斷二噁英形成的條件。根據(jù)一個優(yōu)選實施方式,該方法還包括能量回收過程,能量回收過程至少包括如下步驟:可燃?xì)怏w在熱解氣化爐的加熱室206充分燃燒后產(chǎn)生的煙氣通過熱交換器回收熱能,并且回收熱能后的煙氣再依次進入冷卻塔和過濾塔進行凈化處理后再進行排放??扇?xì)怏w產(chǎn)生的煙氣溫度高達800~1000℃,通過熱交換器回收熱能后,可用于為工廠供熱或發(fā)電。本發(fā)明的危險廢物無害化處理方法與焚燒相比,其產(chǎn)生的二氧化碳溫室氣體可減少70%,可節(jié)約電能60%,節(jié)約輔助燃料80%,節(jié)約用水60%,節(jié)省運行費用50~70%。有利于對大氣污染、pm2.5的控制,特別是對減輕霧霾產(chǎn)生與影響有著重大的意義,而且本發(fā)明提供的危險廢物無害化處理方法及裝置適用于《國家危險廢物名錄2016版》中的危險廢物的處理。本發(fā)明的危險廢物無害化處理方法的具體工藝路線如下所述:s1:將經(jīng)過磁選、破碎、除塵的危險廢物輸送至熱解氣化爐接收斗內(nèi),通過擠壓的方式進入到無氧熱解倉202內(nèi),堵塞進料通道,阻塞爐內(nèi)和爐外氣體流通,保障熱解氣化爐連續(xù)工作上料時,爐內(nèi)的氣體不外泄。s2:危險廢物中的有機可燃物在無氧熱解倉202內(nèi)800℃以上高溫、無氧條件下進行干燥脫水和熱分解。危險廢物表面的水分、一氧化碳、二氧化碳、氫、甲烷等析出;此時危險廢物轉(zhuǎn)化為半焦化狀。s3:半焦化物進入到缺氧熱解倉203進一步熱解,分解出甲烷、氫氣、一氧化碳等,同時,危險廢物轉(zhuǎn)化為焦化狀。s4:焦化狀危險廢物進入熔融室205焚燒,產(chǎn)生高溫?zé)煔夂突以?;灰渣通過排渣口213排出熱解氣化爐,綜合利用或填埋。s5:危險廢物在熱解氣化爐內(nèi)產(chǎn)生的各種氣體和在熔融室205焚燒產(chǎn)生的高溫?zé)煔膺M入到催化還原倉204進行催化還原為可燃?xì)怏w。水蒸氣在此還原為氫氣,二氧化碳還原為一氧化碳。s6:在催化還原倉204內(nèi)轉(zhuǎn)化的可燃?xì)怏w排出爐外,進入到燃?xì)鈨艋?nèi)進行凈化處理。燃?xì)庵械乃嵝詺怏w與堿性物質(zhì)中和,燃?xì)庵械碾s質(zhì)被凈化處理。s7:經(jīng)凈化后的可燃?xì)怏w一部分返回到熱解氣化爐的加熱室206,通過燃燒為后續(xù)危險廢物熱解提供熱能。另一部分輸送到燃?xì)鈨Υ婀迌?nèi),通過燃?xì)廨斔蜋C輸送給燃?xì)獍l(fā)電機組進行發(fā)電。s8:可燃?xì)怏w在熱解氣化爐加熱室燃燒后產(chǎn)生的煙氣,排出熱解氣化爐后直接進入到水下曝氣急冷塔急速降溫至200℃以內(nèi),之后再通過過濾后排入大氣。根據(jù)一個優(yōu)選實施方式,本發(fā)明熱解氣化爐工作溫度即加熱室溫度900~980℃,無氧熱解倉202工作溫度850~930℃,缺氧熱解倉203工作溫度800~880℃。加熱室206產(chǎn)生的高溫首先提供給無氧熱解倉202,之后再提供給缺氧熱解倉203。根據(jù)熱動力學(xué)理論,在900℃高溫條件下,危險廢物每分鐘提高10℃,達到900℃高溫時需要1.5小時。下表1列出了不同類型危險廢物開始熱解時的溫度以及最大失重時溫度區(qū)間。表1不同類型危險廢物開始熱解時的溫度以及最大失重時溫度區(qū)間表從上表可知,危險廢物從進入無氧熱解倉202至熱解完成需要1~1.5小時,此時大約有80%的揮發(fā)組分易被析出。本發(fā)明的危險廢物無害化處理方法將無氧干餾、缺氧分解與熔融焚燒有機結(jié)合,有效的解決了無氧干餾外加熱耗能高,不能連續(xù)進料與出渣,處理能力小,炭渣需二次處理的缺陷以及缺氧分解產(chǎn)生的燃?xì)鉄嶂档?,不能作為單一燃料使用和焚燒產(chǎn)生二次污染,尾氣處理設(shè)備復(fù)雜,處理費用高等缺陷。采用本發(fā)明的危險廢物無害化處理方法及裝置排放的污染物濃度限制均在控制標(biāo)準(zhǔn)以內(nèi),具體如下表2所示。表2主要污染物排放濃度限制以及控制標(biāo)準(zhǔn)另一方面,采用光譜分析法對本發(fā)明的可燃?xì)怏w組分進行分析,結(jié)果如下表3所示。表3可燃?xì)怏w組分分析組分名稱氫氣丙烷丙烯異丁烷正丁烷正丁烯二氧化碳分析數(shù)據(jù)(v/v)22.90%0.17%0.28%0.01%0.01%0.03%4.73%組分名稱乙烯乙烷氧氣氮氣甲烷一氧化碳——分析數(shù)據(jù)(v/v)1.33%1.02%6.98%40.35%10.25%11.94%——本發(fā)明提供的危險廢物無害化處理方法用到的熱解氣化工藝與焚燒工藝完全不同。焚燒是放熱和氧化過程,焚燒時需要足夠的氧氣,是在有氧狀態(tài)下燃燒;焚燒的主要產(chǎn)物是粉塵、二氧化碳和廢水;廢物中的硫、重金屬等有害成分混在粉塵當(dāng)中,廢氣中含有大量二噁英類污染物,均需要進行后續(xù)的嚴(yán)格處理;焚燒爐及尾氣處理裝備工藝復(fù)雜且體積龐大,難以實現(xiàn)移動化和小型化。熱解是一個吸收熱能和析出有機物表面物質(zhì)過程,是在無氧或缺氧條件下進行干餾和分解,主要產(chǎn)物是可燃的低分子化合物(如氣態(tài)的有氫氣、甲烷、一氧化碳,液態(tài)的有甲醇、丙烔、醋酸、乙醛、焦油、溶劑油等,固態(tài)的主要是焦炭或炭黑)等儲存性能源;熱解產(chǎn)生的廢氣少,相應(yīng)地排放的廢氣也少;廢物中的硫、重金屬等有害成分被固定在炭黑中,呈惰性狀態(tài),不需要再進行處理和處置;熱解后二噁英的含量低于國家和歐盟的排放標(biāo)準(zhǔn),甚至不產(chǎn)生二噁英。圖6示出了本發(fā)明處理玻璃鋼廢料的一個優(yōu)選實施方式工藝流程圖。如圖6所示,其工藝流程至少包括如下步驟:s101:廢料預(yù)處理。具體過程為玻璃鋼廢料卸入儲料池內(nèi)。通過抓斗機把廢料抓起后放入專用破碎機內(nèi)進行破碎,同時開啟破碎機上的除塵裝置,破碎后的廢料通過輸送機輸送進入到儲料池內(nèi)。再通過抓斗機將廢料送入密封倉內(nèi)。密封倉內(nèi)的廢料通過推料器進入熱解氣化爐的無氧熱解倉202內(nèi),用第一攪拌器208將廢料均勻分布。s102:廢料熱解氣化處理。具體過程為加熱室206開始加熱,通過熱傳導(dǎo)方式將熱能輸送到無氧熱解倉202。無氧熱解倉202內(nèi)的廢料在高溫、無氧條件下進行裂解,廢料中的有機物分子鏈開始斷裂和分解,其表面水分、二氧化碳、一氧化碳、甲烷析出,樹脂轉(zhuǎn)化為固體焦炭,并和玻璃鋼廢料中的無機物玻璃絲粘合在一起。通過輸送機將固體焦炭和玻璃絲一起送入缺氧熱解倉203進一步熱解氣化,產(chǎn)生一氧化碳、氫等可燃?xì)怏w和玻璃絲廢渣。無氧熱解倉202和缺氧熱解倉203內(nèi)產(chǎn)生的氣體輸送至催化還原倉204進行催化還原,生成可燃?xì)怏w。玻璃絲廢渣通過排渣系統(tǒng)排出爐外,收集作為耐火材料或保溫材料添加料綜合利用。s103:凈化處理。具體過程為玻璃鋼廢料中的有機物和樹脂經(jīng)過裂解和氣化后產(chǎn)生的混合可燃?xì)怏w排出熱解氣化爐,進入油氣分離塔進行油氣分離。分離出的液體油進入回收系統(tǒng)進行過濾處理。混合可燃?xì)怏w進入脫酸塔脫酸,再進入凈化過濾塔進一步凈化處理以脫除燃料氣體中的雜質(zhì)。經(jīng)凈化后的燃料氣體被送入到熱解氣化爐的加熱室206內(nèi)燃燒,為后續(xù)處理廢料提供熱能。燃料氣體在加熱室206燃燒后產(chǎn)生的煙氣排出爐外,進入到熱交換器,回收熱水,供廠區(qū)使用?;厥諢崮芎蟮臒煔庠俅芜M入到急冷塔進行冷卻,再到過濾塔進行過濾凈化處理后經(jīng)排氣筒排入大氣。圖7示出了本發(fā)明處理皮革廢物的一個優(yōu)選實施方式工藝流程圖。如圖7所示,其工藝流程至少包括如下步驟:s101:廢料預(yù)處理。具體過程為抓斗從儲存池中將皮革廢物抓起,倒入無氧熱解倉202的接收斗內(nèi)。通過擠壓的方式進入到熱解氣化爐,堵塞進料通道,阻塞爐內(nèi)和爐外氣體流通,保障熱解氣化爐連續(xù)工作上料時,爐內(nèi)的氣體不外泄。s102:廢料熱解氣化處理。具體過程為熱解氣化爐的加熱室206開始加熱,燃料在加熱室206內(nèi)充分燃燒產(chǎn)生高溫氣體,通過熱輻射的方式將高溫傳送給無氧熱解倉202內(nèi)的物料層。物料在無氧熱解倉202內(nèi)800~900℃高溫、無氧條件下進行干燥脫水和分解,產(chǎn)生可燃的第一混合氣體和焦化物(炭)。焦化物(炭)在第一攪拌器208作用下進入缺氧熱解倉203進一步分解產(chǎn)生可燃?xì)怏w。缺氧熱解倉203內(nèi)沒有完全分解的焦化物(炭)在輸送機的作用下再次進入無氧熱解倉202或缺氧氣化倉203內(nèi)再進行氣化分解,產(chǎn)生第二混合氣體和無機灰渣。無氧熱解倉202和缺氧熱解倉203內(nèi)產(chǎn)生的氣體輸送至催化還原倉204進行催化還原,生成可燃?xì)怏w。無機灰渣在熔融室205內(nèi)燃燒后排渣口213排出熱解氣化爐綜合處理。s103:凈化處理。具體過程為熱解氣化爐內(nèi)各階段產(chǎn)生的混合可燃?xì)怏w通過氣體輸送機排出爐外,進入到氣液分離塔。分離出的液體收集(可作原料)。分離出的氣體進入凈化塔內(nèi)進行凈化處理。凈化處理后的可燃?xì)怏w一部分作為清潔能源返回到熱解氣化爐內(nèi)燃為后續(xù)熱解處理廢物提供熱能;另一部分可燃?xì)怏w直接輸送給熱水鍋爐或發(fā)電機組使用。燃料氣體在加熱室燃燒后產(chǎn)生的煙氣排出爐外,進入到熱交換器,回收熱水,供廠區(qū)使用?;厥諢崮芎蟮臒煔庠俅芜M入到急冷塔進行冷卻,再到過濾塔進行過濾凈化處理后經(jīng)排氣筒排入大氣。需要注意的是,上述具體實施例是示例性的,本領(lǐng)域技術(shù)人員可以在本發(fā)明公開內(nèi)容的啟發(fā)下想出各種解決方案,而這些解決方案也都屬于本發(fā)明的公開范圍并落入本發(fā)明的保護范圍之內(nèi)。本領(lǐng)域技術(shù)人員應(yīng)該明白,本發(fā)明說明書及其附圖均為說明性而并非構(gòu)成對權(quán)利要求的限制。本發(fā)明的保護范圍由權(quán)利要求及其等同物限定。當(dāng)前第1頁12