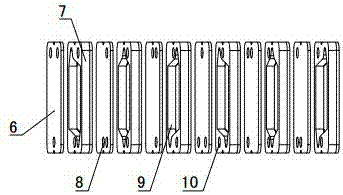
一種三介質編織式金屬絲網材料換熱器及制作方法,屬于換熱設備技術領域。
背景技術:換熱器是工業(yè)生產重要的能量交換設備,在石油化工、核能、航空航天等領域占有重要地位。目前主要以管殼式換熱器為主,體積大、換熱效率低,不符合科學發(fā)展的要求。不少人針對換熱器的優(yōu)化設計方法提出了方案,但由于優(yōu)化設計目標的不明確性及換熱器種類的多樣性,換熱器的優(yōu)化設計目前還不完善。隨著科學技術的發(fā)展和現實工藝的需要,三介質復合換熱器的應用也越來越受到了重視?,F有的三介質換熱器主要是在管殼式換熱器的基礎進行改進,具有承載壓力小、占地空間大、傳熱不均勻、傳熱效率低等缺點,因此有待于探索一種新型的三介質換熱器。管殼式換熱器是石油工業(yè)領域應用較為廣泛的一種換熱器,而以板翅結構作為基本散熱單元,制造的板翅式換熱器,與傳統(tǒng)管殼式換熱器相比,換熱效率提高10倍左右,而重量降低5-10倍,被認為是新一代能源系統(tǒng)的使能技術,如高溫氣冷堆、新一代航空發(fā)動機、微型燃氣輪機以及核動力潛艇等高端裝備均以回熱系統(tǒng)作為提高效率的關鍵。核反應堆,操作溫度達到850℃,冷卻介質的壓力達到9MPa,這需要換熱器除了具有高效的換熱效率之外,還應具有較高的強度,可以在高壓情況下正常工作。我國相關技術發(fā)展緩慢,加上西方國家的封鎖,尚未掌握核心制造技術和設計理論。板式換熱器由于其結構緊湊、傳熱系數高、清洗或維修方便、節(jié)省投資等優(yōu)點,被廣泛地應用于石油工業(yè)生產領域中。因此以板式換熱器為基礎,開發(fā)緊湊、節(jié)能高效的三介質換熱技術與設備,對換熱器的工業(yè)應用具有重要意義。但目前應用廣泛的板式換熱器,在實際使用時仍存在幾個缺陷:其換熱板片是由具有一定波紋形狀的金屬片疊裝而成的,剛度較低,承載能力差;工作壓力在2.5MPa以下的板式換熱器是靠墊片進行密封的,密封周邊較長,而且角孔的兩道密封處支承情況較差,墊片得不到足夠的壓緊力,容易引起泄漏;另外板式換熱器受到換熱面積的限制,使得其換熱效率并不高。中國發(fā)明專利ZL201110309135.2公開了一種點陣材料換熱器,相比常規(guī)板式換熱器,該換熱器的承載能力和換熱效率有所提高,但制作工藝較為復雜,需經過多次焊接工藝才能最終成型,上下面板與擴流板之間、上下面板與封條之間、擴流板與封條之間,均需焊接連接,可能會引起泄漏問題,密封性能并不能得到有效地保障;其次,點陣材料金屬網芯體在沖壓成型時,尤其對于大多數航材,容易產生回彈現象,使得金屬網芯體尺寸發(fā)生變化或金屬網芯體內部存在較大的殘余應力,并不能滿足使用要求,難以應用在對尺寸精度要求較高的領域。綜上所述,該點陣材料換熱器在工程應用時具有一定的局限性。
技術實現要素:本發(fā)明要解決的技術問題是:克服現有技術的不足,提供一種空隙大、傳熱面積大、換熱效率高而且承載能力好的三介質編織式金屬絲網材料換熱器及制作方法。本發(fā)明解決其技術問題所采用的技術方案是:該三介質編織式金屬絲網材料換熱器,包括壓緊板、導桿以及接管,其特征在于:在兩壓緊板之間設有多片金屬網換熱單元,多片金屬網換熱單元疊加并由導桿和壓緊板壓緊固定;所述的金屬網換熱單元包括換熱板、換熱板兩側的密封板以及金屬網芯體,換熱板中部設有換熱腔體,金屬網芯體設置在換熱腔體內,并通過兩側的密封板密封;所述金屬網換熱單元的換熱腔體外側設有三個介質流道,一個介質流道與換熱腔體連通,另外兩個介質流道分別與沿介質流向相鄰的兩金屬網換熱單元的換熱腔體連通。優(yōu)選的,所述的金屬網芯體包括加強板以及金屬網,所述加強板有間隔設置的多片,每相鄰的兩加強板之間設有金屬網;加強板上間隔設有多個引流孔。一種上述三介質編織式金屬絲網材料換熱器的制作方法,其特征在于:包括如下步驟:a、將退火后的金屬絲進行拉直處理,將部分金屬絲制成波浪狀的預彎金屬絲,并進行表面處理;b、將直金屬絲從預彎金屬絲中間穿過,然后在預彎金屬絲和直金屬絲的連接處涂抹氮化硼,完成金屬網的裝配;c、將金屬網和加強板放入焊接成形裝置中,且相鄰兩加強板之間放入金屬網,進行擴散焊焊接,再向焊接成形裝置中充入氣體超塑成形,形成金屬網芯體;d、將金屬網芯體進行深冷處理和反淬火處理;e、切割金屬網芯體,并在金屬網芯體上設置引流孔和導流板;f、將金屬網芯體放入換熱板的換熱腔體內,并在換熱板兩側焊接密封板,形成金屬網換熱單元;g、對金屬網換熱單元檢驗,并對多片金屬網換熱單元進行組裝。優(yōu)選的,步驟b中所述的金屬網的金屬絲半徑與金屬絲間距之間滿足如下關系:;其中:為編織結構的相對密度,其值為0.07~0.1;d為相鄰金屬絲的間距;r為金屬絲的半徑。優(yōu)選的,步驟c中所述的焊接成形裝置包括承載板、承載板上方的上蓋板、兩側的側支撐板以及定位板,兩側支撐板間隔設置,承載板和上蓋板分別位于兩側支撐板的下方和上方,并分別與兩側支撐板的兩端固定連接,形成兩側開口的方形筒狀,定位板有兩塊,分別可滑動的安裝在兩側開口處并將開口封閉,從而形成一個容積可變的封閉內腔;兩側的側支撐板上分別連接有進氣管和排氣管。優(yōu)選的,步驟c中所述的擴散焊焊接的溫度為880~930℃,擴散焊保溫時間為120min。優(yōu)選的,步驟c中所述的氣體為氮氣,所述超塑成形的壓力源為氮氣。優(yōu)選的,步驟d中所述的金屬網芯體在-196℃的液氮中并處理180min,完成深冷處理。優(yōu)選的,步驟d中所述的金屬網芯體在175℃的有機介質中保溫120min后空冷至室溫,完成反淬火處理。與現有技術相比,本發(fā)明的三介質編織式金屬絲網材料換熱器及制作方法所具有的有益效果是:1、本三介質編織式金屬絲網材料換熱器的金屬網換熱單元通過金屬網芯體實現換熱,增大了孔隙率,增大了傳熱面積,使得換熱效率大大提高,金屬網換熱單元可以作為板式換熱器波紋板的替代材料;金屬網換熱單元對流體擾動形成渦流,提高了傳熱效率,金屬網相比目前已有的蜂窩結構、泡沫結構,具有質量輕、強度高的優(yōu)點;金屬網芯體還對兩側的密封板起到連接作用,大大提高了本換熱器的承載能力;金屬網換熱單元上設有三個介質流道,可實現三種介質的逆流換熱,也能對兩種介質進行換熱,應用范圍廣,有效地提高了傳熱效率。2、加強板提高了金屬網芯體的承載能力,進而提高了本三介質編織式金屬絲網材料換熱器的承載能力,提高本換熱器的使用范圍,也大大提高了本換熱器的使用壽命;加強板上設有引流孔,能夠避免加強板阻礙流體流動的問題,保證了流體的流動,從而保證了本換熱器的換熱效率。3、加強板上設有導流板,導流板能夠對金屬網換熱單元內的流體進行導流,使流體能夠更順暢的流入金屬網芯體內,并能更順暢的從金屬網芯體內流出。4、本三介質編織式金屬絲網材料換熱器的制作方法工藝簡單,金屬網通過金屬絲編織而成,相比于目前應用較為前沿的點陣結構,編織式金屬網結構具有制作工藝簡單、強度高、傳熱效率高的優(yōu)點;且在制作編織式金屬絲網時,通過制作一部分的預彎金屬絲,并夾持固定,讓直金屬絲從中間穿過,簡化了常規(guī)經緯編織法中繁瑣的挑壓工序,操作簡單、方法可靠,縮短了制造周期。5、編織結構的相對密度限定在0.07-0.1之間,各方面的性能表現為最優(yōu),通過金屬絲的半徑和金屬絲間距來調整編織結構的相對密度,能夠極大的提高換熱器的性能。6、成形焊接裝置既能夠進行擴散焊焊接,還能夠進行超塑成形,裝置結構簡單,操作方便,而且效果好。7、應用超塑成形擴散焊制作的編織結構,具有無回彈、無殘余應力、成形精度高、強度高等優(yōu)點,作為換熱器的芯體,可以承受更大的載荷,提高了結構的承載能力,另外,結構的整體性好,抗彎剛度大,編織結構在擴散連接后的界面完全消失,使整個結構成為一個整體,極大地提高了結構的抗疲勞和抗腐蝕特性;金屬網芯體的超塑成形以氮氣為壓力源,一方面氮氣的價格低,降低了生產成本,另一方面可以促使金屬絲表面滲氮,提高金屬絲的硬度、耐蝕性、疲勞強度及耐高溫性能。8、深冷處理降低了編織結構的熱應力,同時組織晶粒細化,提高了金屬網硬度、強度和抗沖擊性能,使用壽命和尺寸穩(wěn)定性也得以提高。9、反淬火處理能夠防止金屬網芯體發(fā)生變形,提高了金屬網芯體的精度,而且大大提高了金屬網芯體的使用壽命。附圖說明圖1為三介質編織式金屬絲網材料換熱器的爆炸示意圖。圖2為三介質編織式金屬絲網材料換熱器換熱單元的爆炸示意圖。圖3為換熱單元的立體結構示意圖。圖4為安裝金屬網芯體后的換熱板的主視示意圖。圖5為金屬網芯體的立體結構示意圖。圖6為金屬網的立體結構示意圖。圖7為三介質流向示意圖。圖8為金屬網芯體擴散焊的主視結構示意圖。圖9為金屬網芯體擴散焊的左視結構示意圖。圖10為金屬網芯體超塑成形主視剖視示意圖。圖中:1、壓緊板2、導桿孔3、接管4、螺栓孔5、法蘭6、密封板7、換熱板8、密封板流道9、換熱腔體10、換熱板流道11、金屬網芯體12、金屬網13、導流板14、加強板15、引流孔16、定位板17、進氣管18、排氣管19、上蓋板20、承載板21、側支撐板。具體實施方式圖1~10是本發(fā)明的最佳實施例,下面結合附圖1~10對本發(fā)明做進一步說明。一種三介質編織式金屬絲網材料換熱器,包括壓緊板1、導桿以及接管3,在兩壓緊板1之間設有多片金屬網換熱單元,多片金屬網換熱單元疊加并由導桿和壓緊板1壓緊固定;金屬網換熱單元包括換熱板7、換熱板7兩側的密封板6以及金屬網芯體11,換熱板7中部設有換熱腔體9,金屬網芯體11設置在換熱腔體9內,并通過兩側的密封板6密封;金屬網換熱單元的換熱腔體9外側設有三個介質流道,一個介質流道與換熱腔體9連通,另外兩個介質流道分別與沿介質流向相鄰的兩金屬網換熱單元的換熱腔體9連通。本三介質編織式金屬絲網材料換熱器的金屬網換熱單元通過金屬網芯體11實現換熱,增大了孔隙率,增大了傳熱面積,使得換熱效率大大提高,金屬網換熱單元可以作為板式換熱器波紋板的替代材料;金屬網換熱單元對流體擾動形成渦流,提高了傳熱效率,金屬網12相比目前已有的蜂窩結構、泡沫結構,具有質量輕、強度高的優(yōu)點;金屬網芯體11還對兩側的密封板6起到連接作用,大大提高了本換熱器的承載能力;金屬網換熱單元上設有三個介質流道,可實現三種介質的逆流換熱,也能對兩種介質進行換熱,應用范圍廣,有效地提高了傳熱效率。具體的:如圖1~2所示:壓緊板1有兩塊,兩塊壓緊板1均為長方形板,兩壓緊板1的下方均設有用于支撐的支撐腳。金屬網換熱單元有多個,金屬網換熱單元為長方形,且金屬網換熱單元的長和寬均小于壓緊板1的長和寬,多塊金屬網換熱單元均設置在兩塊壓緊板1之間。壓緊板1上設有三個接管3,接管3上設有法蘭5,接管3用于換熱器與流體管道連接,法蘭5方便與流體管道的固定。金屬網換熱單元上設有三個介質流道,且每相鄰的兩個金屬網換熱單元的介質流道相連通,與兩個壓緊板1的金屬網換熱單元的三個介質流道分別與接管3連通,該換熱器可以在三種介質或兩種介質之間進行換熱,使用方便。兩塊壓緊板1的外沿均設有螺栓孔4,兩塊壓緊板1通過螺栓固定連接,兩壓緊板1的上下兩側分別設有一個導桿孔2,且每個金屬網換熱單元的上下兩側均設有與導桿孔2相配合的導桿槽,金屬網換熱單元通過兩壓緊板1和導桿壓緊固定。換熱板7和密封板6均為長方形板,換熱板7的厚度大于密封板6的厚度,換熱腔體9設置在換熱板7的中部,金屬網芯體11安裝在換熱板7的換熱腔體9內。換熱板7和兩側的密封板6密封連接,金屬網芯體11分別與換熱板7和密封板6相連,增大了金屬網換熱單元的承載能力,進而提高了該換熱器的承載能力,使該換熱器的適用范圍大大增加。每個密封板6上設有三個密封板流道8,每個換熱板7上設有兩個換熱板流道10,密封板6上的兩個密封板流道8與換熱板7上的換熱板流道10連通,密封板6上的第三個密封板流道8與換熱板7上的換熱腔體9連通,從而使兩兩介質之間形成逆流換熱,有效地提高了換熱效率。如圖3~4所示:金屬網芯體11包括加強板14以及金屬網12。加強板14有間隔設置的多塊,多塊加強板14均豎直設置。加強板14的寬度與換熱板7厚度相等,加強板14的長度小于換熱板7的長度。每相鄰的兩加強板14之間設有金屬網12,金屬網12與加強板14固定連接,從而形成金屬網芯體11。金屬網芯體11具有大孔隙率,增大了傳熱面積,使得換熱效率大大提高,而且又有良好的承載能力,可以作為板式換熱器波紋板的替代材料;而且金屬網12結構相比目前已有的蜂窩結構、泡沫結構,具有輕質、高強等優(yōu)點,而相比目前應用較為前沿的點陣結構,金屬網12的結構具有制作工藝簡單,強度高,傳熱效率高等優(yōu)點。如圖5所示:加強板14的兩端分別設有導流板13,導流板13的寬度與加強板14的寬度相等,導流板13一端與加強板14固定連接,另一端向與密封板6連通的密封板流道8傾斜,導流板13對進入換熱腔體9的流體和流出換熱腔體9的流體進行導向,從而使流體更好的流入和流出換熱腔體9。加強板14上間隔設有多個引流孔15,引流孔15能夠使整個換熱腔體9連通,方便流體在換熱腔體9內的流動,進而提高了流體的換熱效率。如圖6所示:金屬網12為采用類似經緯編織的方法編織而成,且每相鄰的兩金屬絲間的間距相等。在制作編織式金屬絲網時,通過制作一部分的預彎金屬絲,并夾持固定,讓直金屬絲從中間穿過,簡化了常規(guī)經緯編織法中繁瑣的挑壓工序,操作簡單、方法可靠,縮短了制造周期。如圖7所示:每個金屬網換熱單元上的三個介質流道中,有一個與該金屬網換熱單元的換熱腔體9連通,另兩個分別與沿介質流向相鄰的兩個金屬網換熱單元的換熱腔體9連通,使得每個介質流道均是回流型,增大了介質的流速和湍流程度,從而提高了傳熱效率。同時,每相鄰的兩金屬網換熱單元內介質流動方向相反,實現了三介質相互之間的逆流換熱,換熱效率高。上述三介質編織式金屬絲網材料換熱器的制作方法,包括如下步驟:1、將退火后的金屬絲進行拉直處理,將部分金屬絲制成波浪狀的預彎金屬絲,并進行表面處理。金屬網12的金屬絲半徑與金屬絲間距之間滿足如下關系:;其中:為編織結構的相對密度,其值為0.07~0.1;d為相鄰金屬絲的間距;r為金屬絲的半徑。編織結構相對密度值越小時,特征表現為越細長,越容易發(fā)生屈曲變形,理論上相對密度最低值應在0.07左右。另外,實驗表明相關密度在0.1-0.3時,表現為高的摩擦因素,介質從其中穿過時可能引起動能的大量損失。而相對密度超過0.3時,編織結構孔隙率非常低,不利于介質在編織結構中的流動。因此,將編織結構的相對密度限定在0.07-0.1之間,各方面的性能表現為最優(yōu)。結構緊湊型板式換熱器,一般板間距為4-6mm。另外,考慮到金屬絲的制作成本,其直徑不應該過小,而且金屬絲直徑過小時,相應的金屬絲間距減小,介質通過時容易引起堵塞問題。綜合上述編織結構的相對密度、板間距以及金屬絲的制作成本等因素,將金屬絲直徑優(yōu)化為0.25mm,金屬絲間距為2mm,板間距為6mm,相對密度為0.098。根據金屬絲的直徑以及金屬絲的間距,制作預彎金屬絲模具。對金屬絲進行退火處理,并將退火處理后的金屬絲進行拉直處理,然后通過液壓機和模具將部分金屬絲制成預彎金屬絲,預彎金屬絲上間隔設有多個向同一側凸出的弧形,并根據需要對預彎金屬絲進行切割以及對切割面的打磨處理,預彎金屬絲兩端面的粗糙度達到3.2um,預彎金屬絲的曲率半徑為0.125mm。2、將直金屬絲從預彎金屬絲中間穿過,然后在預彎金屬絲和直金屬絲的連接處涂抹氮化硼,完成金屬網12的裝配。在制作編織式金屬絲網時,并夾持固定預彎金屬絲,讓直金屬絲從中間穿過,簡化了常規(guī)經緯編織法中繁瑣的挑壓工序,操作簡單、方法可靠,縮短了制造周期。3、將金屬網12和加強板14放入焊接成形裝置中,且相鄰兩加強板14之間放入金屬網12,進行擴散焊焊接,再向焊接成形裝置中充入氣體超塑成形,形成金屬網芯體11。如圖8~9所示:焊接成形裝置包括承載板20、承載板20上方的上蓋板19、兩側的側支撐板21以及定位板16,兩側支撐板21間隔設置,承載板20和上蓋板19分別位于兩側支撐板21的下方和上方,并分別與兩側支撐板21的兩端固定連接,形成兩側開口的方形筒狀,定位板16有兩塊,分別可滑動的安裝在兩側開口處并將開口封閉,從而形成一個容積可變的封閉內腔。兩側的側支撐板21上分別連接有進氣管17和排氣管18,且進氣管17和排氣管18可以單獨控制通斷。將裝配好的金屬網12放置在承載板20上,預彎金屬絲長度方向與水平面垂直,然后放置加強板14,并在金屬網12和加強板14的連接處涂抹氮化硼,注意保持連接處表面的清潔度。準確的在兩側的加強板14外側放置定位板16并加以固定,且兩側的加強板14與定位板16間隔設置,進氣管17和排氣管18均設有兩組,兩組進氣管17分別連接兩側的加強板14與定位板16間的空腔以及焊接成形裝置的內腔,兩組排氣管18也分別連接兩側的加強板14與定位板16間的空腔以及焊接成形裝置的內腔。通過對上蓋板19以及兩側支撐板21施加壓力實現整個裝配件的固定,繼而在擴散焊加熱爐中進行焊接。兩側的加強板14的厚度為中部加強板14厚度的一半。焊接過程為:首先將焊接成形裝置的內腔抽真空,然后以20℃/min的速度加熱到880~930℃。打開進氣管17向兩側的加強板14與定位板16之間充入氮氣,使得2MPa的壓力作用在兩側加強板14的外側,并保溫120min,完成擴散焊焊接過程。如圖10所示:焊接完成后繼續(xù)保持溫度不變,進行超塑成形處理。打開進氣管17,向相鄰加強板14之間的空腔內充入氮氣,兩側的加強板14在壓力作用下向定位板16移動,金屬網12在加強板14的帶動下拉伸,完成超塑成形,最終形成金屬網芯體11。應用超塑成形擴散焊制作的編織結構,具有無回彈、無殘余應力、成形精度高、強度高等優(yōu)點,作為換熱器的芯體,可以承受更大的載荷,提高了結構的承載能力。另外,結構的整體性好,抗彎剛度大,編織結構在擴散連接后的界面完全消失,使整個結構成為一個整體,極大地提高了結構的抗疲勞和抗腐蝕特性。金屬網芯體11的超塑成形以氮氣為壓力源,一方面氮氣的價格低,降低了生產成本,另一方面可以促使金屬絲表面滲氮,提高金屬絲的硬度、耐蝕性、疲勞強度及耐高溫性能。4、將金屬網芯體11進行深冷處理和反淬火處理。將金屬網芯體11從焊接成形裝置內取出,采用深冷處理工藝進行深冷處理。首先,放入深冷箱的液氮中,深冷處理溫度為-196℃,保溫180min后迅速取出并轉移到QCW-01型高溫有機介質中,進行反淬火處理,升溫至175℃,并保溫120min,然后空冷至室溫。進行深冷處理的目的是為了降低連接處的殘余應力,細化晶粒,并提高硬度、強度和抗沖擊性能。深冷處理是為了降低編織結構的熱應力,同時組織晶粒細化,提高了金屬網12的硬度、強度和抗沖擊性能,使用壽命和尺寸穩(wěn)定性也得以提高。反淬火處理能夠防止金屬網芯體11發(fā)生變形,提高了金屬網芯體11的精度,而且大大提高了金屬網芯體11的使用壽命。5、切割金屬網芯體11,并在金屬網芯體11上設置引流孔15和導流板13。通過線切割方式,對金屬網芯體11進行分割,并在加強板14上開設引流孔15,引流孔15的直徑為0.8mm。然后采用脈沖激光焊將導流板13焊接在加強板14上,并進行除油、除銹處理。6、將金屬網芯體11放入換熱板7的換熱腔體9內,并在換熱板7兩側焊接密封板6,形成金屬網換熱單元。在密封板6與換熱板7上分別開設密封板流道8和換熱板流道10,同時需對換熱板7和密封板6進行表面處理,達到平整且光滑,再用丙酮清洗去除表面油污。將金屬網芯體11放置在換熱板7的換熱腔體9內,分別在兩側的密封板6、金屬網芯體11和換熱板7的連接處涂抹一層氮化硼,完成金屬網換熱單元的裝配,再用與上述擴散焊相同的工藝,實現密封板6、金屬網芯體11以及換熱板7的固定連接,形成金屬網換熱單元。可能泄漏的部位僅在換熱板7與密封板6之間的連接處,換熱板7和密封板6通過擴散焊焊接,保證了該部位的密封,提高了整體的密封性能,有效的降低了泄漏的可能,金屬網芯體11也與密封板6和換熱板7焊接,提高了承載能力。7、對金屬網換熱單元檢驗,并對多片金屬網換熱單元進行組裝。采用X射線探傷檢測密封板6與換熱板7連接處的內部缺陷,并進行氣密性實驗,確保擴散焊的質量。然后將多個金屬網換熱單元通過壓緊板1固定,完成換熱器的制作。打開連接相鄰加強板14之間空腔的進氣管17,向其中充入氮氣作為超塑成形的壓力源。由于相鄰加強板14之間的空腔內壓力不同于加強板14與定位板16之間的空腔內壓力,因此兩側的加強板14在壓力作用下向定位板16移動,金屬網12在加強板14的帶動下,逐漸超塑成形。其中,采用微機控制超塑成形的壓力,保證超塑成形在最佳應變速率下進行。超塑成形處理一般采用氬氣作為壓力源,本實施例中的超塑成形采用氮氣的原因是一方面氮氣成本低,另一方面可以促使金屬絲表面滲氮,提高金屬絲的硬度、耐蝕性、疲勞強度及耐高溫性能。以上所述,僅是本發(fā)明的較佳實施例而已,并非是對本發(fā)明作其它形式的限制,任何熟悉本專業(yè)的技術人員可能利用上述揭示的技術內容加以變更或改型為等同變化的等效實施例。但是凡是未脫離本發(fā)明技術方案內容,依據本發(fā)明的技術實質對以上實施例所作的任何簡單修改、等同變化與改型,仍屬于本發(fā)明技術方案的保護范圍。