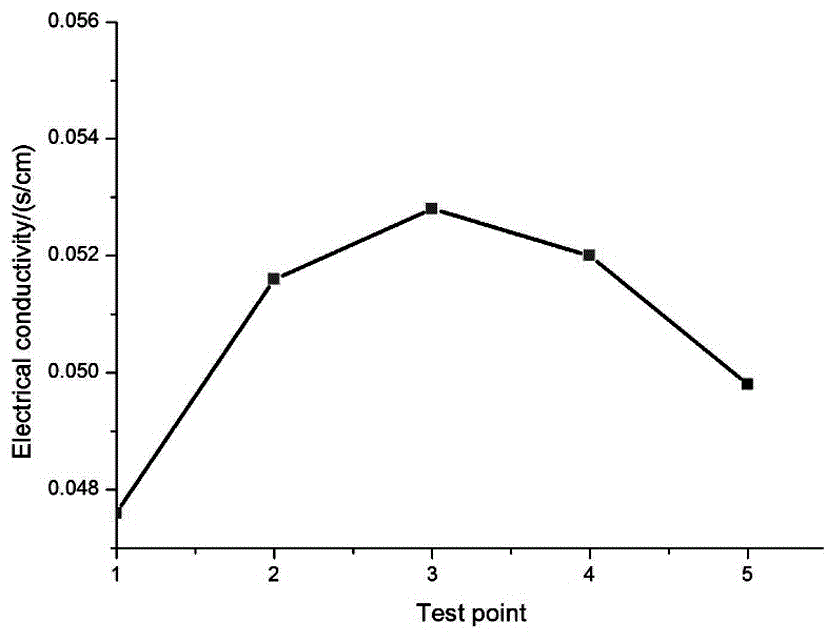
本發(fā)明涉及含有炭系導(dǎo)電填料的導(dǎo)電薄膜,特別是涉及一種納米石墨片導(dǎo)電薄膜及其制作方法。
背景技術(shù):導(dǎo)電薄膜主要用于傳導(dǎo)電流和排除靜電,厚度一般為0.1~1mm,在抗靜電、電磁屏蔽、電加熱、防腐導(dǎo)電、電子電路等許多方面都有著很重要的應(yīng)用。導(dǎo)電薄膜按照其內(nèi)部組成和導(dǎo)電機(jī)理的不同有結(jié)構(gòu)型導(dǎo)電薄膜和復(fù)合型導(dǎo)電薄膜之分。結(jié)構(gòu)型導(dǎo)電薄膜,因其制備工藝比較復(fù)雜,不易制取所以在實(shí)際應(yīng)用中較為廣泛的是復(fù)合型導(dǎo)電薄膜;復(fù)合型導(dǎo)電薄膜,是將具有導(dǎo)電功能的有機(jī)或者無機(jī)的導(dǎo)電填料通過一定的工藝方法混入不具有導(dǎo)電功能的基體樹脂,然后利用所得到的漿料制備得到。因此,復(fù)合型導(dǎo)電薄膜的性能受到多種因素的影響,主要有包括導(dǎo)電填料、成膜樹脂、相關(guān)助劑的選擇,成膜方法等。導(dǎo)電填料對導(dǎo)電薄膜的導(dǎo)電性能影響重大,填料含量的多少、填料種類、填料粒徑大小、填料形狀等因素都會影響導(dǎo)電薄膜的導(dǎo)電性。通常所用的導(dǎo)電填料有金、銀、銅粉及氧化物等,但是存在著價(jià)格較高、比較笨重的缺點(diǎn),后來又引入了碳系填料碳黑、碳纖維和石墨,碳系填料的優(yōu)點(diǎn)是價(jià)格較低,易于得到,但是又存在著均一性較差、易團(tuán)聚,所得到的導(dǎo)電薄膜強(qiáng)度低,易破損等缺點(diǎn)。我國制備的導(dǎo)電薄膜也以無機(jī)填料為主,如碳系填料等。然而,以碳系填料制備導(dǎo)電薄膜時(shí)因?yàn)槠涔に嚢ɑ炝虾统尚蝺纱箨P(guān)鍵工藝環(huán)節(jié),混料和成形效果的好壞直接影響涂層性能及其穩(wěn)定性?;炝瞎に嚪譃楦苫旌蜐窕靸煞N,干混是將納米石墨片與有機(jī)物通過直接混合或者熔融混合的方式混合在一起,其主要缺點(diǎn)是納米石墨片容易團(tuán)聚、混合不均勻且耗時(shí)較長;濕混是將納米石墨片混入有機(jī)溶劑中制成相應(yīng)的涂料,其主要缺點(diǎn)是溶劑較易揮發(fā),對環(huán)境污染嚴(yán)重且耗時(shí)耗能;成形工藝則分為共擠擠壓法和流延成型法,這兩種方法均對成形漿料的流動(dòng)性能有著特殊要求,即漿料的流動(dòng)性要好。因此,針對現(xiàn)在技術(shù)的不足,有必要選用一種新的碳系填料,并針對現(xiàn)有導(dǎo)電薄膜成型工藝的不足,提出一種新的導(dǎo)電薄膜及其制備方法。有效解決碳系填料易團(tuán)聚、不易分散、均一性差、分散范圍和分散效果不可控的問題。
技術(shù)實(shí)現(xiàn)要素:為了克服上述現(xiàn)有技術(shù)的不足,本發(fā)明提供了一種納米石墨片導(dǎo)電薄膜及其制作方法。本發(fā)明通過下述技術(shù)方案來實(shí)現(xiàn):一種納米石墨片導(dǎo)電薄膜,其特征在于:該導(dǎo)電薄膜以納米石墨片為導(dǎo)電填料,成膜物質(zhì)為基體膜材。所述的納米石墨片厚度為1-20nm,高度為0.05-100um,寬度為0.01-5um,相鄰納米片間距為0.01-5um。所述的成膜物質(zhì)為酚醛樹脂、環(huán)氧樹脂和聚氨酯樹脂中的一種。一種納米石墨片導(dǎo)電薄膜的制備方法,至少包括以下步驟:a.將納米石墨片在60℃烘箱內(nèi)烘干24小時(shí),然后取出密封保存待用;b.按所需制備導(dǎo)電薄膜的大小,準(zhǔn)備合適尺寸的耐高溫分離膜,并用膠帶固定于基帶上;c.將成膜物質(zhì)、稀釋劑和助劑按照一定的比例混合,在100-200r/min攪拌速度下,將混合漿料攪拌50-120min以保證其充分混合,然后將混合漿料轉(zhuǎn)移至真空攪拌罐中,并添加除泡劑,在攪拌速度為150-250r/min時(shí)繼續(xù)攪拌30-90min,同時(shí)輔以真空除氣,此時(shí),真空攪拌罐內(nèi)的真空度為-0.5~-2MPa,最終得到混合基體膜材漿料;d.利用得到的混合基體膜材漿料,裝入流延成型裝置的料斗中,采用流延成型的方法,在準(zhǔn)備的耐高溫分離膜上按照所設(shè)計(jì)的導(dǎo)電薄膜形狀制成一厚度為0.2mm的基體膜材薄膜;e.將基體膜材薄膜連同耐高溫分離膜一起置于烘箱內(nèi),在60-90℃溫度條件下,加熱干燥5-20min,以調(diào)整基體膜材薄膜的固化程度,取出待用;f.將基體膜材薄膜連同耐高溫分離膜一起轉(zhuǎn)移、固定于微噴射成型的實(shí)驗(yàn)臺上,采用微粉噴射打印成形的方法,對所產(chǎn)生的高壓、高速氣流進(jìn)行精確控制,最終納米石墨片顆粒在高壓氣流的作用下將納米石墨片加速,達(dá)到其臨界速度,同時(shí),通過對打印噴頭X/Y方向運(yùn)動(dòng)的精確控制,實(shí)現(xiàn)納米石墨片在基體膜材上按照所需的形狀精確分散、嵌入到基體膜材中,形成一層致密的導(dǎo)電薄膜;g.將基體膜材薄膜連同耐高溫分離膜一起取出,在60-90℃溫度條件下,加熱固化30-60min。h.去除固定膠帶、并將導(dǎo)電薄膜從耐高溫分離膜上剝離,得到納米石墨片導(dǎo)電薄膜。所述的稀釋劑為丙酮、無水乙醇的一種。所述的助劑有偶聯(lián)劑、消泡劑、流平劑。所述的偶聯(lián)劑為γ-縮水甘油醚氧丙基三甲氧基硅烷(KH560),消泡劑為有機(jī)硅氧烷,流平劑為聚醚硅氧烷共聚物。所述的納米石墨片導(dǎo)電薄膜的制作方法,其特征在于:按質(zhì)量分?jǐn)?shù)計(jì),酚醛樹脂20-40份、聚醚硅氧烷共聚物1.5-3.0份、γ-縮水甘油醚氧丙基三甲氧基硅烷(KH560)0.6-3.2份、無水乙醇40-60份。所述基體膜材薄膜的成型方法為流延法。所述微粉噴射打印成形的方法,噴射壓力0.4-1MPa,送粉量0.0001-0.005kg/s,噴射距離10-30mm,所要求達(dá)到的最低速度為300m/s。與現(xiàn)有技術(shù)相比,本發(fā)明的有益效果是:1)選用的導(dǎo)電填料為納米石墨片,其具有著超高的比表積和良好的導(dǎo)電性能、機(jī)械強(qiáng)度高,而且制備成本低,生產(chǎn)量大,是制備導(dǎo)電薄膜的理想功能材料。2)針對碳系填料在樹脂基體內(nèi)易團(tuán)聚、分散性不好,工藝復(fù)雜的問題,首次將微粉噴射成型的方法引入到導(dǎo)電薄膜的制備中,首先,酚醛樹脂、稀釋劑、固化劑和助劑按照一定的比例配制成基體膜材漿料,然后利用微粉噴射成型的方法將納米石墨片加速,納米石墨片沖擊精確嵌入到基體膜材薄膜中,在基體膜材薄膜中形成一層致密的導(dǎo)電薄膜薄膜,可以實(shí)現(xiàn)對納米石墨片的分散效果的控制,有效的解決了碳系填料在基體膜材內(nèi)易團(tuán)聚,分散性不好的問題。3)微粉噴射打印成型的方法,具有成型效率高、成膜效果好、對導(dǎo)電填料的分散范圍和分散效果精確可控的優(yōu)點(diǎn),相對于傳統(tǒng)的成膜工藝來說,有效的簡化了工藝步驟。附圖說明圖1為實(shí)施例1的“蜂窩狀”導(dǎo)電薄膜示意圖。圖2為實(shí)施例1的“蜂窩狀”導(dǎo)電薄膜不同測試點(diǎn)電導(dǎo)率。圖3“中國結(jié)狀”導(dǎo)電薄膜不同打印方案。圖4為實(shí)施例3的“心形”導(dǎo)電薄膜示意圖。具體實(shí)施方式實(shí)施例1一)納米石墨片前處理配制100ml的無水乙醇,將納米石墨片放入其中,用超聲波分散的方式分散40分鐘,然后在常溫下攪拌24小時(shí),過濾懸濁液,并用無水乙醇反復(fù)洗滌4-6次,然后將所得到的產(chǎn)物置于烘箱內(nèi)在60℃條件下干燥24小時(shí),取出密封待用。二)耐高溫分離膜準(zhǔn)備按所需要制備的“蜂窩狀”導(dǎo)電薄膜的形狀,準(zhǔn)備一大小為50×50mm的耐高溫分離膜,然后用乙醇擦洗干凈,置于室溫下風(fēng)干,然后將其用膠帶固定于流延成型裝置的基帶之上。三)基體膜材漿料的配制按質(zhì)量分?jǐn)?shù)計(jì),稱取酚醛樹脂34份、聚醚硅氧烷共聚物3.0份、γ-縮水甘油醚氧丙基三甲氧基硅烷(KH560)2.0份、無水乙醇60份、有機(jī)硅氧烷1.0份。按照上述比例,在200r/min的攪拌速度下,加酚醛樹脂加入無水乙醇中,攪拌20min,然后加入聚醚硅氧烷共聚物、γ-縮水甘油醚氧丙基三甲氧基硅烷(KH560)繼續(xù)攪拌10min,以利于基體膜材各組分之間的充分混合,最后加入有機(jī)硅氧烷在真空度為-0.6MPa的真空攪拌罐中進(jìn)行攪拌,攪拌速度為200r/min,以去除基體膜材漿料中的空氣,攪拌30min,最終得到基體膜材漿料。四)導(dǎo)電薄膜微粉噴射打印成型將所得到的基體膜材漿料采用流延成型的方法,在耐高溫分離膜上,按照所需要的導(dǎo)電薄膜的“蜂窩狀”形成0.2mm厚的薄膜,刮平,將耐高溫分離膜和所得到的基體膜材薄膜一起置于烘箱內(nèi)在60℃條件下烘干30分鐘,以調(diào)整薄膜的干燥程度,取出待用;將耐高溫分離膜和所得到的基體膜材薄膜一起固定在微噴射成型的實(shí)驗(yàn)臺之上,采用微粉噴射打印成形的方法在噴射壓力0.6MPa,溫度為300K,送粉量0.0001kg/s,噴射距離10mm的條件下,對所產(chǎn)生的高壓、高速氣流進(jìn)行精確控制,最終納米石墨片顆粒在高壓氣流的作用下將納米石墨片加速,達(dá)到其臨界速度,同時(shí),通過對打印噴頭X/Y方向運(yùn)動(dòng)的精確控制,實(shí)現(xiàn)納米石墨片在基體膜材上按照所需的“蜂窩狀”形狀精確分散、嵌入到基體膜材中,在基體膜材中形成一層致密的薄膜;然后將耐高溫分離膜連同所得到的導(dǎo)電薄膜一起置于烘箱內(nèi)在60℃溫度條件下,加熱固化60min,冷卻后去除固定膠帶,將導(dǎo)電薄膜從耐高溫分離膜上輕輕剝離,得到導(dǎo)電薄膜成品,該導(dǎo)電薄膜為“蜂窩狀”。五)導(dǎo)電薄膜性能檢測利用四探針測試儀對所得到的導(dǎo)電薄膜進(jìn)行相應(yīng)的測試,測試其不同測試點(diǎn)的導(dǎo)電性能,測試結(jié)果表明導(dǎo)電薄膜整體厚度為0.38mm,其中酚醛樹脂厚度0.2mm,納米石墨片層厚度為0.18mm,五個(gè)不同測試點(diǎn)的電導(dǎo)率分別為0.0476S/cm、0.0516S/cm、0.0528S/cm、0.0520S/cm、0.0498S/cm.具體結(jié)果見圖2。實(shí)施例2一)納米石墨片前處理配制100ml的無水乙醇,將納米石墨片放入其中,用超聲波分散的方式分散40分鐘,然后在常溫下攪拌24小時(shí),過濾懸濁液,并用無水乙醇反復(fù)洗滌4-6次,然后將所得到的產(chǎn)物置于烘箱內(nèi)在60℃條件下干燥24小時(shí),取出密封待用。二)耐高溫分離膜準(zhǔn)備按所需要制備的“中國結(jié)狀”導(dǎo)電薄膜的形狀,準(zhǔn)備一大小為50×50mm的耐高溫分離膜,然后用乙醇擦洗干凈,置于室溫下風(fēng)干,然后將其用膠帶固定于流延成型裝置的基帶之上。三)基體膜材漿料的配制按質(zhì)量分?jǐn)?shù)計(jì),稱取環(huán)氧樹脂33份、聚醚硅氧烷共聚物3.0份、γ-縮水甘油醚氧丙基三甲氧基硅烷(KH560)3.0份、丙酮60份、有機(jī)硅氧烷1.0份。按照上述比例,在200r/min的攪拌速度下,加環(huán)氧樹脂加入丙酮中,攪拌20min,然后加入聚醚硅氧烷共聚物、γ-縮水甘油醚氧丙基三甲氧基硅烷(KH560)繼續(xù)攪拌10min,以利于基體膜材各組分之間的充分混合,最后加入有機(jī)硅氧烷在真空度為-0.6MPa的真空攪拌罐中進(jìn)行攪拌,攪拌速度為230r/min,以去除基體膜材漿料中的空氣,攪拌30min,最終得到基體膜材漿料。四)導(dǎo)電薄膜微粉噴射打印成型將所得到的基體膜材漿料采用流延成型的方法,在耐高溫分離膜上,按照所需要的導(dǎo)電薄膜的大小形成0.2mm厚的薄膜,刮平,將耐高溫分離膜和所得到的基體膜材薄膜一起置于烘箱內(nèi)在60℃條件下烘干30分鐘,以調(diào)整薄膜的干燥程度,取出待用;將耐高溫分離膜和所得到的基體膜材薄膜一起固定在微噴射成型的實(shí)驗(yàn)臺之上,采用微粉噴射打印成形的方法在噴射壓力0.8MPa,溫度為300K,送粉量0.0001kg/s,噴射距離10mm的條件下,對所產(chǎn)生的高壓、高速氣流進(jìn)行精確控制,最終納米石墨片顆粒在高壓氣流的作用下將納米石墨片加速,達(dá)到其臨界速度,同時(shí),通過對打印噴頭X/Y方向運(yùn)動(dòng)的精確控制,首先打印出不同形狀的導(dǎo)電通路,然后再重復(fù)打印,最終實(shí)現(xiàn)納米石墨片在基體膜材上按照所需的“中國結(jié)”形狀精確分散、嵌入到基體膜材中,在基體膜材中形成一層致密的導(dǎo)電薄膜;然后將耐高溫分離膜連同所得到的導(dǎo)電薄膜一起置于烘箱內(nèi)在60℃溫度條件下,加熱固化60min,冷卻后去除固定膠帶,將導(dǎo)電薄膜從耐高溫分離膜上輕輕剝離,得到導(dǎo)電薄膜成品,該導(dǎo)電薄膜為“中國結(jié)狀”。五)導(dǎo)電薄膜成品檢測測試結(jié)果表明導(dǎo)電薄膜整體厚度為0.43mm,其中酚醛樹脂厚度0.2mm,納米石墨片層厚度為0.23mm,單個(gè)測試點(diǎn)的電導(dǎo)率為0.0657S/cm。實(shí)施例3一)納米石墨片前處理配制100ml的無水乙醇,將納米石墨片放入其中,用超聲波分散的方式分散40分鐘,然后在常溫下攪拌24小時(shí),過濾懸濁液,并用無水乙醇反復(fù)洗滌4-6次,然后將所得到的產(chǎn)物置于烘箱內(nèi)在60℃條件下干燥24小時(shí),取出密封待用。二)耐高溫分離膜準(zhǔn)備按所需要制備的“心形”導(dǎo)電薄膜的形狀,準(zhǔn)備一大小為50×50mm的耐高溫分離膜,然后用無水乙醇擦洗干凈,置于室溫下晾干,然后將其用膠帶固定于流延成型裝置的基帶之上。三)基體膜材漿料的配制按質(zhì)量分?jǐn)?shù)計(jì),稱取聚氨酯35份、聚醚硅氧烷共聚物2.0份、γ-縮水甘油醚氧丙基三甲氧基硅烷(KH560)3.0份、丙酮59份、有機(jī)硅氧烷1.0份。按照上述比例,在210r/min的攪拌速度下,將聚氨酯加入丙酮中,攪拌20min,然后加入聚醚硅氧烷共聚物、γ-縮水甘油醚氧丙基三甲氧基硅烷(KH560)繼續(xù)攪拌10min,以利于基體膜材各組分之間的充分混合,最后加入有機(jī)硅氧烷在真空度為-0.6MPa的真空攪拌罐中進(jìn)行攪拌,攪拌速度為230r/min,以去除基體膜材漿料中的空氣,攪拌30min,最終得到基體膜材漿料。四)導(dǎo)電薄膜微粉噴射打印成型將所得到的基體膜材漿料采用流延成型的方法,在耐高溫分離膜上,按照所需要的導(dǎo)電薄膜的大小形成0.2mm厚的薄膜,刮平,將耐高溫分離膜和所得到的基體膜材薄膜一起置于烘箱內(nèi)在60℃條件下烘干30分鐘,以調(diào)整薄膜的干燥程度,取出待用;將耐高溫分離膜和所得到的基體膜材薄膜一起固定在微噴射成型的實(shí)驗(yàn)臺之上,采用微粉噴射打印成形的方法在噴射壓力0.6MPa,溫度為300K,送粉量0.0001kg/s,噴射距離10mm的條件下,對所產(chǎn)生的高壓、高速氣流進(jìn)行精確控制,最終納米石墨片顆粒在高壓氣流的作用下將納米石墨片加速,達(dá)到其臨界速度,同時(shí),通過對打印噴頭X/Y方向運(yùn)動(dòng)的精確控制,首先打印出不同形狀的導(dǎo)電通路,然后再重復(fù)打印,最終實(shí)現(xiàn)納米石墨片在基體膜材上按照所需的“心形”形狀精確分散、嵌入到基體膜材中,在基體膜材中形成一層致密的導(dǎo)電薄膜;然后將耐高溫分離膜連同所得到的導(dǎo)電薄膜一起置于烘箱內(nèi)在60℃溫度條件下,加熱固化60min,冷卻后去除固定膠帶,將導(dǎo)電薄膜從耐高溫分離膜上輕輕剝離,得到導(dǎo)電薄膜成品,該導(dǎo)電薄膜為“心形”。五)導(dǎo)電薄膜成品檢測測試結(jié)果表明導(dǎo)電薄膜整體厚度為0.44mm,其中酚醛樹脂厚度0.2mm,納米石墨片層厚度為0.25mm,單個(gè)測試點(diǎn)的電導(dǎo)率為0.0568S/cm。