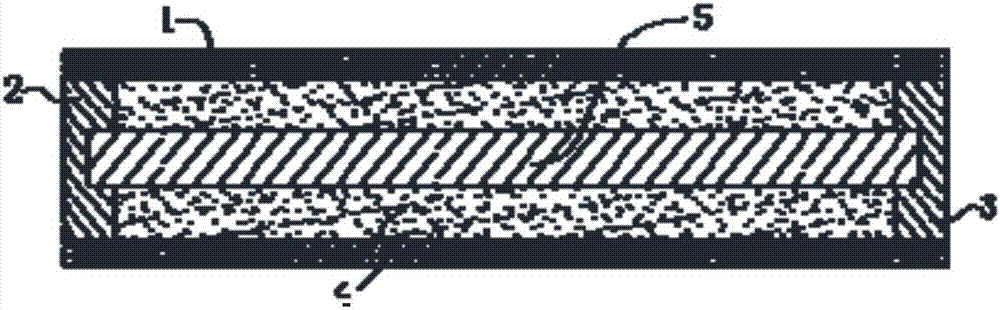
本發(fā)明涉及注塑擠出、抽粒機(jī)筒生產(chǎn)
技術(shù)領(lǐng)域:
,特指一種具有三元硼化物基金屬(mo2feb2)陶瓷成分的雙金屬合金機(jī)筒材料及其生產(chǎn)工藝。
背景技術(shù):
:現(xiàn)有塑膠成型擠出機(jī)筒生產(chǎn)領(lǐng)域中,在對塑膠綜合性能要求越來越高的前提下,在特種注塑擠出越發(fā)普及的情況下,注塑擠出成型在機(jī)筒塑化過程中,工程塑膠、粉末冶金注射、陶瓷注射成型、磁鐵鐵粉、電木、bmc等嚴(yán)重磨損腐蝕領(lǐng)域,對機(jī)筒造成了劇烈的磨損及劇烈的腐蝕,如磁鐵粉90%、加纖65%、pps+65%加纖、高環(huán)保、高阻燃條件下的塑膠成型,機(jī)筒的使用壽命經(jīng)常只有2-6個月的生產(chǎn)穩(wěn)定周期,對此造成大量的塑膠材料及資源浪費(fèi),嚴(yán)重制約了生產(chǎn)成型企業(yè)的正常運(yùn)轉(zhuǎn);因?yàn)槌湍ツ透g材料的缺失,致使國內(nèi)在這一領(lǐng)域目前還是空白。就國外而言,早期機(jī)筒制作的工藝步驟一般是采用38crmoal(sacm645)調(diào)質(zhì)定型后加工并經(jīng)72小時的氮化處理后制得,此類機(jī)筒的表面具氮化層僅有0.3~0.7mm,耐磨性差,無法應(yīng)對現(xiàn)今高玻璃纖維、礦纖維、碳纖維、高阻燃、高磨料磨損場合,僅有1~2個月左右的生產(chǎn)穩(wěn)定周期,便無法生產(chǎn)成型。后來隨著離心澆鑄工藝的成熟及自熔合金材料應(yīng)用普及使得氮化機(jī)筒逐漸淡出人們的視野,其中的鐵基合金、鎳基合金、鉆基合金三大合金材料的離心澆鑄最為廣泛。該工藝簡介為:將粉末加入預(yù)先加工好的孔內(nèi),將筒體加熱到自熔合金融化的溫度,再進(jìn)行高速旋轉(zhuǎn)產(chǎn)生較大離心力,從而獲得了一合金層,經(jīng)過后續(xù)加工制得成品。國外通常用電加熱爐或中頻加熱爐將加入粉末的機(jī)筒坯預(yù)先抽真空并封孔,在真空狀態(tài)下合金獲得了較低的氧化,另外通過添加一定的量包覆型碳化鎢粉末,也獲得較好的雙金屬合金機(jī)筒的材料產(chǎn)品。國內(nèi)的雙金屬因澆鑄粉末質(zhì)量上的差異,加熱爐及中頻加熱控溫的準(zhǔn)確性差異,使得合金層產(chǎn)生稀釋擴(kuò)散與底材產(chǎn)生侵蝕效應(yīng),使得澆鑄出來的合金達(dá)不到原來合金設(shè)計的耐磨性及耐腐蝕性。加入碳化鎢在合金融化后,因比重較合金大很多(碳化鎢比重為13以上)在高速旋轉(zhuǎn)離心澆鑄過程中會產(chǎn)生沉底效應(yīng),故合金層往往要加工得很薄才會獲得碳化物合金層,以增加其耐磨。但因合金層厚度的變薄及隨著碳化鎢的加入脆性變大問題使得在使用過程中大打折扣。故國內(nèi)國外合金機(jī)筒現(xiàn)狀不能同時很好解決合金機(jī)筒的高韌性、高耐磨性、高耐腐蝕性,生產(chǎn)出的機(jī)筒都會有各類問題出現(xiàn)。國內(nèi)三大合金材料在澆鑄過程中雖然獲得相應(yīng)硬度的合金,但大部分不是以硬質(zhì)相支撐而形成的硬度,而是由脆相形成的。與由真正全部硬質(zhì)相生成而形成的合金在耐磨性方面有很大的差別。技術(shù)實(shí)現(xiàn)要素:本發(fā)明的目的在于克服現(xiàn)有技術(shù)中的不足之處而提供一種合金機(jī)筒材料,該材料硬度適中,高溫性能優(yōu)異,抗彎強(qiáng)度好,密度和鋼基體接近,斷裂韌性高,耐磨性優(yōu)異,耐腐蝕性能優(yōu)良,并進(jìn)一步提供了一種采用前述合金機(jī)筒材料制成合金機(jī)筒的生產(chǎn)工藝,通過該生產(chǎn)工藝使得塑膠成型更為穩(wěn)定,大大提高了合金機(jī)筒的使用壽命,使注塑擠出雙金屬合金機(jī)筒的耐磨性耐腐蝕性及耐高溫性方面產(chǎn)生了質(zhì)的飛躍。一種雙金屬合金機(jī)筒材料,所述合金機(jī)筒材料按以下原料粉末的質(zhì)量分?jǐn)?shù)比配比而成:鉬mo:25~50%,硼b:2~10%,鉻cr:5~15%,鎳ni:2~10%,錳mn:1~5%,碳c:0.1~1%,碳化鉻:0.8~3%,鐵fe:余量;其中,硼b以硼化鐵的合金形式加入。所述各原料粉末的粉度如下:鉬mo:1~8μm,硼b:1~15μm,鉻cr:1~20μm,鎳ni:2~10μm;錳mn:1~15μm,鐵fe:2~10μm,碳c:2~10μm,碳化鉻cr3c2:1~10μm。所述各原料粉末的純度如下:鉬mo:99.8%以上,硼b:99.7%以上,鉻cr:99.8%以上,鎳ni:99.5%以上,錳mn:99.5%以上,鐵fe:99.5%以上,碳化鉻cr3c2:99%以上,碳c:99.7%以上。一種上述雙金屬合金機(jī)筒材料制作合金機(jī)筒的生產(chǎn)工藝,該生產(chǎn)工藝步驟如下:1)球磨原始粉末:按配比重量取原始粉末,并將較粗的粉末預(yù)先進(jìn)行球磨,獲得液態(tài)混合體;2)混合干燥粉末:將其它的未加入的原始粉末加入步驟1)的液態(tài)混合體中,并配比一定量的液體介質(zhì)及硬質(zhì)球體介質(zhì)混合均勻后,進(jìn)行球液分離并真空干燥,獲得塊狀粉體,再將塊狀粉體進(jìn)行粉碎處理,獲得混合物粉末;3)粉末壓制坯體:將步驟2)的混合物粉末裝入預(yù)先設(shè)計好的坯體模具中,經(jīng)過冷等靜壓工藝、模壓或機(jī)壓,制得毛坯體;4)坯體加工整形:將步驟3)的毛坯體經(jīng)過機(jī)床加工整形,制得毛坯料;5)真空脫脂燒結(jié):將步驟4)的毛坯料放入燒結(jié)爐內(nèi)進(jìn)行燒結(jié)處理,制得合金坯體之半成品;6)整形加工半成品:對步驟5)的半成品并進(jìn)行機(jī)械整形及加工,制得合金機(jī)筒坯體;7)坯體熱套處理:取基體管并高溫加熱,再將預(yù)先計算好過盈量的合金機(jī)筒坯體鑲?cè)肭笆龌w管中,待兩者冷卻后,獲得了雙金屬合金機(jī)筒坯體;8)內(nèi)孔加工處理:對步驟7)的雙金屬合金機(jī)筒坯體進(jìn)行內(nèi)孔精度加工,制得雙金屬合金機(jī)筒。進(jìn)一步地,所述步驟1)球磨時采用丙酮或無水乙醇及特制的硬質(zhì)圓球作為球磨介質(zhì),其球磨時間為24~72小時,球磨所獲得的液態(tài)混合體為平均2~5μm粒度號的混合體。進(jìn)一步地,所述步驟2)的液體介質(zhì)采用為無水乙醇或者丙酮且純度為95%以上,硬質(zhì)球體為直徑為φ8~φ15的硬質(zhì)合金球,球體在混碎時的比值為大約2~4:1~2,球體在混合時的比值為大約1~2:2~4,其中,液體介質(zhì)的加料比為固液體積比3~5,混合時間通常為24~72小時,按以上比值所獲得的球磨粉碎效果最佳為2~5μm。進(jìn)一步地,在所述步驟3)的過程中,需在坯體模具表面均勻加壓,單位面積壓力不低于100mpa~300mpa。進(jìn)一步地,所述步驟4)中的毛坯料的直線度為≤1000/0.2~0.5μm,毛坯料的圓度為≤0.2~0.5μm,經(jīng)過整形后的毛坯料在后續(xù)燒結(jié)過程中,減少了變形的產(chǎn)生,為最終機(jī)加工減少加工量,提高了合金坯體的加工效益。進(jìn)一步地,所述步驟5)采用保護(hù)氣氛燒結(jié)或者熱等靜壓燒結(jié),其極限真空為1.0×10-4pa以上。進(jìn)一步地,所述步驟5)的燒結(jié)工藝分為如下三個階段:第一階段:加溫0~550℃,加溫及保溫時間為5~6個小時左右,期間輔助充入一定流量的保護(hù)性氣體進(jìn)行脫脂,該氣體為氬氣、氮?dú)狻⒒驓錃?,其中,壓力?.2~0.8mpa,流量為10-40l/min;②第二階段:加溫550℃~1100℃以內(nèi),加溫及保溫時間5~7小時;③第三階段:加溫1100℃~1380℃以內(nèi),加溫及保溫時間為3~5小時,燒結(jié)完成后隨爐冷卻,完成燒結(jié)。所述步驟6)之合金機(jī)筒坯體的外圓圓度在0.005~0.01μm以內(nèi),合金機(jī)筒坯體的直線度在≤1000/0.02以內(nèi)。所述步驟7)的基體管加熱溫度為600℃~1000℃,其冷卻處理為在常溫常壓下空氣中自然冷卻或者風(fēng)扇冷卻。所述步驟8)的雙金屬合金機(jī)筒內(nèi)孔的圓度為0.005~0.01μm,雙金屬合金機(jī)筒內(nèi)孔的直線度為≤1000/0.01,該雙金屬合金機(jī)筒內(nèi)孔的表面光潔度為≥0.4~0.8。本發(fā)明的有益效果在于:1.采用前述材料制作的雙金屬合金機(jī)筒硬度適中,高溫性能優(yōu)異,抗彎強(qiáng)度好,密度和鋼基體接近,斷裂韌性高,耐磨性優(yōu)異,耐腐蝕性能優(yōu)良。2.采用前述生產(chǎn)工藝使得塑膠成型更為穩(wěn)定,大大提高了合金機(jī)筒的使用壽命,使注塑擠出雙金屬合金機(jī)筒的耐磨性耐腐蝕性及耐高溫性方面產(chǎn)生了質(zhì)的飛躍。附圖說明圖1是本發(fā)明的工藝流程圖。圖2是本發(fā)明工藝所需模具的結(jié)構(gòu)示意圖。圖3是本發(fā)明材料腐蝕前的金相組織圖。圖4是本發(fā)明材料腐蝕后的金相組織圖。具體實(shí)施方式以下結(jié)合說明書附圖對本發(fā)明作進(jìn)一步說明:如圖1-4所示,本發(fā)明關(guān)于一種雙金屬合金機(jī)筒材料,所述合金機(jī)筒材料按以下原料粉末的質(zhì)量分?jǐn)?shù)比配比而成:鉬mo:25~50%,硼b:2~10%,鉻cr:5~15%,鎳ni:2~10%,錳mn:1~5%,碳c:0.1~1%,碳化鉻:0.8~3%,鐵fe:余量;其中,硼b以硼化鐵的合金形式加入,優(yōu)選硼化鐵feb等。所述各原料粉末的粉度如下:鉬mo:1~8μm,硼b:1~15μm,鉻cr:1~20μm,鎳ni:2~10μm;錳mn:1~15μm,鐵fe:2~10μm,碳c:2~10μm,碳化鉻cr3c2:1~10μm。所述各原料粉末的純度如下:鉬mo:99.8%以上,硼b:99.7%以上,鉻cr:99.8%以上,鎳ni:99.5%以上,錳mn:99.5%以上,鐵fe:99.5%以上,碳化鉻cr3c2:99%以上,碳c:99.7%以上。根據(jù)上述雙金屬合金機(jī)筒材料的配置要求,制得如下表1:表1進(jìn)一步地,本發(fā)明還揭示一種上述雙金屬合金機(jī)筒材料制成合金機(jī)筒的生產(chǎn)工藝,該生產(chǎn)工藝步驟如下:1)球磨原始粉末:按配比重量取原始粉末,并將較粗的粉末預(yù)先進(jìn)行球磨,獲得液態(tài)混合體;2)混合干燥粉末:將其它的未加入的原始粉末加入步驟1)的液態(tài)混合體中,并配比一定量的液體介質(zhì)及硬質(zhì)球體介質(zhì)混合均勻后,進(jìn)行球液分離并真空干燥,獲得塊狀粉體,再將塊狀粉體進(jìn)行粉碎處理,獲得混合物粉末;3)粉末壓制坯體:將步驟2)的混合物粉末裝入預(yù)先設(shè)計好的坯體模具中,該模具如圖2(其中,1-橡膠管;2、3-橡膠塞頭;4-粉末;5-鋼基體芯桿)所示,經(jīng)過冷等靜壓工藝、模壓或機(jī)壓,制得毛坯體;4)坯體加工整形:將步驟3)的毛坯體經(jīng)過機(jī)床加工整形,制得毛坯料;5)真空脫脂燒結(jié):將步驟4)的毛坯料放入燒結(jié)爐內(nèi)進(jìn)行燒結(jié)處理,制得合金坯體之半成品;6)整形加工半成品:對步驟5)的半成品并進(jìn)行機(jī)械整形及加工,制得合金機(jī)筒坯體;7)坯體熱套處理:取基體管并高溫加熱,再將預(yù)先計算好過盈量的合金機(jī)筒坯體鑲?cè)肭笆龌w管中,待兩者冷卻后,獲得了雙金屬合金機(jī)筒坯體;8)內(nèi)孔加工處理:對步驟7)的雙金屬合金機(jī)筒坯體進(jìn)行內(nèi)孔精度加工,制得雙金屬合金機(jī)筒。進(jìn)一步地,所述步驟1)球磨時采用丙酮或無水乙醇及特制的硬質(zhì)圓球作為球磨介質(zhì),其球磨時間為24~72小時,球磨所獲得的液態(tài)混合體為平均2~5μm粒度號的混合體,此液體混合體與步驟2)加入粉末的粒度號接近,為最終獲得綜合粒度號為1~3μm的平均粒質(zhì)號的原始材料粉末提供保證。經(jīng)實(shí)際驗(yàn)證測試,粉末的原始粒度控制在1-3μm之間所獲得的晶體組織,特別是耐磨相均在1~3μm之間,如圖3、4所示。進(jìn)一步地,步驟2)的液體介質(zhì)采用為無水乙醇或者丙酮且純度為95%以上,硬質(zhì)球體為直徑為φ8~φ15的硬質(zhì)合金球,球體在混碎時的比值為大約2~4:1~2,球體在混合時的比值為大約1~2:2~4,其中,液體介質(zhì)的加料比為固液體積比3~5,混合時間通常為24~72小時,按以上比值所獲得的球磨粉碎效果最佳為2~5μm。此粒度號的粉末在壓制坯料后容易在燒結(jié)過程中產(chǎn)生相互浸濕及擴(kuò)散的反應(yīng),從而獲得韌性強(qiáng)度較高的材料,同時因耐磨相較為細(xì)小(1~3μm),故其耐磨性能在同樣配方粉末里。細(xì)小的耐磨相可以獲得最好的耐磨性能,并配比一定量的液體介質(zhì)及球體介質(zhì),按以上比值所獲得的球磨粉碎效果最佳為2~5μm,混合效果最佳可以獲得混合均勻的懸浮狀的混合液體?;旌弦后w經(jīng)過真空固液分離裝置,在具有真空度(1~200pa)的條件下進(jìn)行較為快速的球液及固液分離(同時進(jìn)行)與空氣接觸時間可以控制在10-30分鐘之內(nèi),最大限度的減少材料的氧化及性能的改變,因該裝置為自行設(shè)計產(chǎn)品,故只說明其性能,不做結(jié)構(gòu)說明。固液分離完成后再放入特殊訂制的真空干燥箱中(真空度為0.1pa~100pa),此設(shè)備為特殊訂制及改制產(chǎn)品在此不作特殊結(jié)構(gòu)說明。設(shè)定干燥溫度為25℃~75℃之間,連續(xù)干燥時間為12~36h,干燥冷卻后獲得干燥粉末固體(塊狀形狀),最后將塊狀固體經(jīng)過粉碎為粒度號為20~500μm的混合粉末,選取此粒度號是為了增加裝粉的流動性為下一道工序提供便利。此處粉碎設(shè)備為跨行業(yè)選用件,不作結(jié)構(gòu)說明。進(jìn)一步地,在所述步驟3)的過程中,需在坯體模具表面均勻加壓,單位面積壓力不低于100mpa~300mpa,在此壓力范圍內(nèi)可以獲得較為致密的合金機(jī)筒坯體,為后續(xù)加工合金機(jī)筒坯體提供強(qiáng)度保證,以及為后續(xù)的燒結(jié)過程致密化縮短了時間,加速了粘結(jié)相與耐磨相的快速位移反應(yīng)。進(jìn)一步地,步驟4)中的毛坯料的直線度為≤1000/0.2~0.5μm,毛坯料的圓度為≤0.2~0.5μm。進(jìn)一步地,步驟5)采用保護(hù)氣氛燒結(jié)或者熱等靜壓燒結(jié),其極限真空為1.0×10-4pa以上。進(jìn)一步地,步驟5)的燒結(jié)工藝分為如下三個階段:第一階段:加溫0~550℃,加溫及保溫時間為5~6個小時左右,期間輔助充入一定流量的保護(hù)性氣體進(jìn)行脫脂,該氣體為氬氣、氮?dú)?、或氫氣,其中,壓力?.2~0.8mpa,流量為10-40l/min,以該壓力及流量充入氣體進(jìn)行脫脂,在該材料脫脂過程中,可以獲得最優(yōu)的脫脂效果及最優(yōu)的材料保護(hù)(不被氧化),當(dāng)然該脫脂氣體可優(yōu)選為氫氣或者氬氣,最后是氮?dú)狻?yōu)先氫氣的原因是在脫脂過程中會對部分氧化材料有一個還原的過程效應(yīng),大大提升了后續(xù)材料的品質(zhì)性能;第二階段:加溫550℃~1100℃以內(nèi),加溫及保溫時間5~7小時;第三階段:加溫1100℃~1380℃以內(nèi),加溫及保溫時間為3~5小時,燒結(jié)完成后隨爐冷卻,完成燒結(jié)。進(jìn)一步地,步驟6)之合金機(jī)筒坯體的外圓經(jīng)車制磨削加工后所獲得的圓度在0.005~0.01μm以內(nèi),合金機(jī)筒坯體的直線度在≤1000/0.02以內(nèi),直線度及圓度控制在此范圍之內(nèi),可以為后續(xù)熱套工序提供保證。進(jìn)一步地,步驟7)的基體管加熱溫度為600℃~1000℃,其冷卻處理為在常溫常壓下空氣中自然冷卻或者風(fēng)扇冷卻,因選取了特殊的鋼基體材料,所以該過程不會對鋼基體的硬度及晶粒大小造成顯著的影響(該鋼基體為與特鋼廠共同生產(chǎn)的技術(shù)協(xié)議產(chǎn)品,命名牌號為jy26)。再進(jìn)一步地,步驟8)的雙金屬合金機(jī)筒內(nèi)孔的圓度為0.005~0.01μm,雙金屬合金機(jī)筒內(nèi)孔的直線度為≤1000/0.01,該雙金屬合金機(jī)筒內(nèi)孔的表面光潔度為≥0.4~0.8,該精度完全滿足雙金屬合金機(jī)筒的使用生產(chǎn)要求。以下結(jié)合實(shí)際,對表1做進(jìn)一步解釋:首先,合金機(jī)筒材料成份中的鉬mo、硼b(以硼化鐵的形式加入),鉻cr、鐵fe元素的加入,是形成陶瓷硬質(zhì)相的基本元素,此中合金機(jī)筒材料的硬度特性主要是由陶瓷硬質(zhì)相生成的多少來決定的,實(shí)驗(yàn)證明:當(dāng)加入鉬mo的含量為25%、硼b含量為2%時,所得材料的硬度最低,即陶瓷硬質(zhì)相生成含量最少為40%以下,當(dāng)加入鉬mo的含量為50%以上、硼b含量為40%時,所得材料的陶瓷硬質(zhì)相生成含量為80%以上,硬度最高,材料特性太脆,無直接使用性能,故鉬mo、硼b的含量應(yīng)控制在上述范圍之內(nèi);其中,鐵fe元素的加入,主要以鐵基粘結(jié)相的結(jié)構(gòu)存在于材料體系中,并與其他cr、ni元素形成綜合性能優(yōu)越的鉻鎳不銹鋼鐵基粘結(jié)相,但其不參與陶瓷硬質(zhì)相的生成。其次,成分中的鉻cr、鎳ni、碳c元素的加入,使材料具有較好的硬度和強(qiáng)度,且對鐵基粘結(jié)相起到顯著的合金強(qiáng)化作用,提高了粘結(jié)相的硬度,又進(jìn)一步提高的材料的強(qiáng)度。實(shí)驗(yàn)證明,當(dāng)鉻cr的含量為5%、鎳ni的含量為2.5%、碳c的含量為0.1%時,所起的強(qiáng)化作用不明顯;當(dāng)鉻cr的含量為15%、鎳ni的含量為10%、碳c的含量為1%時,則出現(xiàn)了明顯的脆性傾向,故鉻cr、鎳ni、碳c的含量控制在上述范圍之內(nèi)。最后碳化鉻(cr3c2)的加入在此材料燒結(jié)過程中起到明顯抑制晶粒長大的作用,將晶??刂埔欢ǚ秶畠?nèi)加入量為小于0.8%時所起的抑制晶粒作用不明顯,加入量過3%時會產(chǎn)生明顯的硬度增加傾向。特別說明的是,通過實(shí)驗(yàn)測試觀察可知:材料中錳mn元素的加入,明顯改變了材料的顯微組織,特別是陶瓷硬質(zhì)相的晶粒增大,可見,錳mn元素的加入,改善了材料的強(qiáng)度和硬度,具有增大材料強(qiáng)度和硬度的作用;實(shí)驗(yàn)證明,當(dāng)錳mn含量小于1%時,材料不能獲得機(jī)械性能的充分改善;當(dāng)錳mn含量超過7%時,陶瓷硬質(zhì)相組織粗化,橫向斷裂強(qiáng)度和斷裂韌性降低,機(jī)械性能得到改善,錳mn的含量控制在上述范圍,可獲得機(jī)械性能符合實(shí)際需要的材料;而且,加入錳mn之后,材料獲得的燒結(jié)范圍擴(kuò)大。因此,為了改善機(jī)械性能,需加入在材料中加入mn,并將mn的含量控制在1~7%之間。緊接著,結(jié)合耐磨、耐腐蝕性能實(shí)驗(yàn),對上述各具體實(shí)施例所制得的合金機(jī)筒性能做進(jìn)一步說明:首先,將取合金機(jī)筒的硼化物試樣,進(jìn)行耐磨性能測試,其各測試結(jié)果如下:①在不同轉(zhuǎn)速下進(jìn)行yg6磨環(huán),實(shí)驗(yàn)載荷100n,硼化物試樣對應(yīng)的平均摩擦系數(shù)如表2:表2②在不同轉(zhuǎn)速下進(jìn)行yg6磨環(huán),實(shí)驗(yàn)載荷100n,與硬質(zhì)合金yg8相比,硼化物試樣對應(yīng)的磨損失重如表3:表3③不同摩擦配副下,以實(shí)驗(yàn)載荷100n,轉(zhuǎn)速800r/min對硼化物試樣進(jìn)行測試,其平均摩擦系數(shù)如表4:與yg6配副的摩擦系數(shù)與45#鋼配副的摩擦系數(shù)硼化物試樣0.400.55表4④不同摩擦配副下,以實(shí)驗(yàn)載荷100n,轉(zhuǎn)速800r/min對硼化物試樣進(jìn)行測試,其磨損失重(與硬質(zhì)合金yg8相比)如表5:45#鋼磨環(huán)時磨損減重yg6鋼磨環(huán)時磨損減重硼化物試樣1.261.96硬質(zhì)合金yg80.341.09表5由上述實(shí)驗(yàn)測試數(shù)據(jù)可見,通過本發(fā)明所生產(chǎn)制成的合金機(jī)筒材料的耐磨性僅次于硬質(zhì)合金。接著,取合金機(jī)筒的硼化物試樣與鋼基體材料,進(jìn)行不同條件的耐腐蝕性能的測試對比,其各測試結(jié)果如下:①在室溫條件下,將硼化物試樣與鋼基體材料分別在65%硝酸中腐蝕65h的情況對比如表6:表6②在室溫條件下,將硼化物試樣與鋼基體材料分別在硝酸-氫氟酸(按照“gb/t4334.4-2000”《不銹鋼硝酸-氫氟酸腐蝕試驗(yàn)方法》配置10%硝酸、3%氫氟酸腐蝕溶液)中,腐蝕24h的情況對比如表7:表7③在室溫條件下,將硼化物試樣與鋼基體材料分別在硫酸-硫酸銅溶液(按照“gb/t4334.5-2000”《不銹鋼硫酸-硫酸銅腐蝕試驗(yàn)方法》配置硫酸-硫酸銅腐蝕溶液)中,腐蝕30h的情況對比如表8:表8④在室溫條件下,將硼化物試樣與鋼基體材料分別在5%硫酸中腐蝕65h的情況對比如表9:表9⑤將硼化物試樣與鋼基體材料分別在天然海水中腐蝕60h的情況對比如表10:表10由上述實(shí)驗(yàn)測試數(shù)據(jù)可見,通過本發(fā)明所揭示的合金機(jī)筒材料的耐腐蝕性相當(dāng)于不銹鋼或優(yōu)于不銹鋼。本發(fā)明所揭示的一種雙金屬合金機(jī)筒材料及其生產(chǎn)工藝,在材料方面,通過對合金機(jī)筒材料中各原料配比的控制,以保證制作出來的材料的強(qiáng)度和硬度。于材料中加入含錳的原料粉末,以進(jìn)一步提高材料的強(qiáng)度和硬度,同時,還擴(kuò)大了材料的燒結(jié)溫度范圍;該合金機(jī)筒材料硬度選中,硬度高達(dá)hrc55~69,高溫性能優(yōu)異,可工作溫度為300~800℃,抗彎強(qiáng)度高達(dá)486.74~1128.39mpa,密度為7.8~8.2×103kg/m3,密度和鋼基體接近,斷裂韌性高,耐磨性優(yōu)異(如表2~5所示),耐腐蝕性能優(yōu)良(如表6~10所示),工藝方面,通過在生產(chǎn)工藝中運(yùn)用了還原氣氛脫脂真空燒結(jié)工藝技術(shù),使得材料性能更為穩(wěn)定,大大提高了制成合金機(jī)筒坯體的成品率,保證了注塑擠出機(jī)筒生產(chǎn)過程中的長期穩(wěn)定性,保證了合金機(jī)筒在惡劣的使用工況下,使用壽命大大超過現(xiàn)有各種類型合金機(jī)筒的使用壽命。以上所述僅是對本發(fā)明的較佳實(shí)施例,并非對本發(fā)明的范圍進(jìn)行限定,故在不脫離本發(fā)明設(shè)計精神的前提下,本領(lǐng)域普通工程技術(shù)人員對本發(fā)明所述的構(gòu)造、特征及原理所做的等效變化或裝飾,均應(yīng)落入本發(fā)明申請專利的保護(hù)范圍內(nèi)。當(dāng)前第1頁12