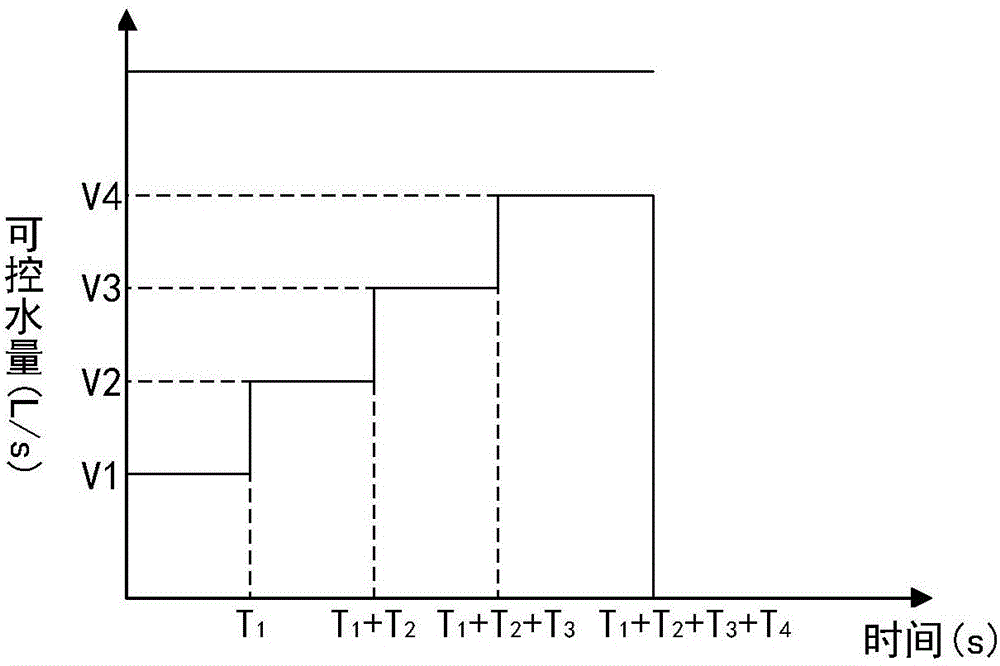
本發(fā)明總體來說涉及鐵路車輛車輪,具體而言,涉及一種鐵路車輛車輪的熱處理方法。
背景技術(shù):
:鐵路車輛車輪一般采用鑄造或鍛造,然后進(jìn)行熱處理的方法生產(chǎn),車輪1型式通常如圖1所示,車輪1的重量一般在500KG左右,材質(zhì)為碳素鋼,車輪1與軌道接觸的部位為輪輞11,接觸面即為踏面12。一直以來,鐵路車輪1的主要熱處理方式為車輪1整體加熱奧氏體化,然后踏面12進(jìn)行噴水冷卻淬火,該熱處理方法要求在車輪輪輞11區(qū)域?qū)崿F(xiàn)淬火,獲得優(yōu)異的細(xì)珠光體組織和非常重要的壓應(yīng)力,而在輻板和輪轂上實(shí)現(xiàn)正火處理,獲得較好的韌性。但是近年來,隨著鐵路重載運(yùn)輸?shù)男枰囕?的強(qiáng)硬度、耐磨性、承載量要求越來越高,車輪1的含碳量越來越高,采用傳統(tǒng)的低壓力、恒定大水量的淬火難以避免在車輪表層產(chǎn)生貝氏體,使車輪組織變脆,服役性能下降。在碳含量接近0.77%的情況下,采用水冷的同時不允許出現(xiàn)貝氏體,逐漸成為車輪設(shè)計的基本技術(shù)要求,這逐漸成為車輪制造技術(shù)的難題之一。因此,需要提供一種鐵路車輛車輪熱處理方法,以解決上述技術(shù)問題,制造符合技術(shù)要求的鐵路車輛車輪。技術(shù)實(shí)現(xiàn)要素:本發(fā)明的一個主要目的在于克服上述現(xiàn)有技術(shù)的至少一種缺陷,提供一種可以獲得較細(xì)珠光體組織、同時有效避免激冷淬火時在車輪踏面表層產(chǎn)生貝氏體等硬脆組織的鐵路車輛車輪熱處理方法。本發(fā)明的另一個主要目的在于克服上述現(xiàn)有技術(shù)的至少一種缺陷,提供一種通過可以獲得較細(xì)珠光體組織、同時有效避免激冷淬火時在車輪踏面表層產(chǎn)生貝氏體等硬脆組織的熱處理方法所獲得的鐵路車輛車輪。為實(shí)現(xiàn)上述發(fā)明目的,本發(fā)明采用如下技術(shù)方案:根據(jù)本發(fā)明的一個方面,提供了一種鐵路車輛車輪熱處理方法,包括以下步驟:(1)車輪經(jīng)整體加熱完全奧氏體化;(2)采用恒定壓力小流量噴水對所述車輪的踏面進(jìn)行短時間冷卻;(3)采用連續(xù)可控水量階梯式噴水對所述車輪的踏面進(jìn)行淬火,對所述車輪踏面以下形成均衡冷速,使整個車輪的輪輞區(qū)域獲得均衡的細(xì)珠光體組織。根據(jù)本發(fā)明的一實(shí)施方式,所述步驟(2)和所述步驟(3)的總和時間為3-5分鐘。根據(jù)本發(fā)明的一實(shí)施方式,所述步驟(2)的時間為30-50秒。根據(jù)本發(fā)明的一實(shí)施方式,所述步驟(2)中的所述恒定壓力為0.8-0.9MPa。根據(jù)本發(fā)明的一實(shí)施方式,所述步驟(3)包括依次連續(xù)的第一階段、第二階段、第三階段和第四階段,其中,所述第一階段的可控水量為V1,所述第二階段的可控水量為V2,所述第三階段的可控水量為V3,所述第四階段的可控水量為V4,且V1<V2<V3<V4。根據(jù)本發(fā)明的一實(shí)施方式,所述第一階段的時間為T1,所述第二階段的時間為T2,所述第三階段的時間為T3,所述第四階段的時間為T4,T1<T2<T3<T4。根據(jù)本發(fā)明的一實(shí)施方式,V2-V1=A1,V3-V2=A2,V4-V3=A3,且A1<A2<A3。根據(jù)本發(fā)明的一實(shí)施方式,所述步驟(2)和所述步驟(3)中,所述車輪處于轉(zhuǎn)動狀態(tài)。根據(jù)本發(fā)明的一實(shí)施方式,所述車輪水平轉(zhuǎn)動,噴水方向?yàn)樗匠蛩鲕囕喌奶っ?。為?shí)現(xiàn)上述發(fā)明目的,本發(fā)明還采用如下技術(shù)方案:根據(jù)本發(fā)明的一個方面,提供了一種鐵路車輛車輪,所述車輪采用如上所述的熱處理方法形成。由上述技術(shù)方案可知,本發(fā)明的鐵路車輛車輪熱處理方法的優(yōu)點(diǎn)和積極效果在于:本發(fā)明中通過較高水壓下小流量用于消除薄膜沸騰或縮短薄膜沸騰階段,同時避免較高冷速形成貝氏體,此后采用連續(xù)可控水量階梯式噴水淬火,對車輪踏面以下形成均衡冷速,使整個輪輞區(qū)域獲得均衡的細(xì)珠光體組織,從而獲得均衡的力學(xué)性能,即較高的強(qiáng)硬度和塑韌性,減小在車輪磨耗方向上的硬度梯度。附圖說明通過結(jié)合附圖考慮以下對本發(fā)明的優(yōu)選實(shí)施例的詳細(xì)說明,本發(fā)明的各種目標(biāo)、特征和優(yōu)點(diǎn)將變得更加顯而易見。附圖僅為本發(fā)明的示范性圖解,并非一定是按比例繪制。在附圖中,同樣的附圖標(biāo)記始終表示相同或類似的部件。其中:圖1是鐵路車輛車輪的結(jié)構(gòu)示意圖。圖2是根據(jù)一示例性實(shí)施方式示出的本發(fā)明鐵路車輛車輪熱處理方法中步驟(3)示意圖。圖3是根據(jù)一示例性實(shí)施方式示出的本發(fā)明鐵路車輛車輪熱處理方法中對車輪進(jìn)行淬火的狀態(tài)示意圖。圖4是本發(fā)明鐵路車輛車輪輪輞截面硬度及梯度圖。圖5是本發(fā)明鐵路車輛車輪踏面以下的微觀組織測試圖。圖6是圖5中1#樣微觀組織的金相照片。圖7是圖5中2#樣微觀組織的金相照片。圖8是圖5中3#樣微觀組織的金相照片。其中,附圖標(biāo)記說明如下:1、車輪;11、輪輞;12、踏面;2、噴頭;R、車輪轉(zhuǎn)動方向;V1、V2、V3、V4、可控水量;T1、T2、T3、T4、時間。具體實(shí)施方式現(xiàn)在將參考附圖更全面地描述示例實(shí)施方式。然而,示例實(shí)施方式能夠以多種形式實(shí)施,且不應(yīng)被理解為限于在此闡述的實(shí)施方式;相反,提供這些實(shí)施方式使得本發(fā)明將全面和完整,并將示例實(shí)施方式的構(gòu)思全面地傳達(dá)給本領(lǐng)域的技術(shù)人員。圖中相同的附圖標(biāo)記表示相同或類似的結(jié)構(gòu),因而將省略它們的詳細(xì)描述。在對本發(fā)明的不同示例的下面描述中,參照附圖進(jìn)行,所述附圖形成本發(fā)明的一部分,并且其中以示例方式顯示了可實(shí)現(xiàn)本發(fā)明的多個方面的不同示例性結(jié)構(gòu)、系統(tǒng)和步驟。應(yīng)理解,可以使用部件、結(jié)構(gòu)、示例性裝置、系統(tǒng)和步驟的其他特定方案,并且可在不偏離本發(fā)明范圍的情況下進(jìn)行結(jié)構(gòu)和功能性修改。而且,雖然本說明書中可使用術(shù)語“頂部”、“底部”、“前部”、“后部”、“側(cè)部”等來描述本發(fā)明的不同示例性特征和元件,但是這些術(shù)語用于本文中僅出于方便,例如根據(jù)附圖中所述的示例的方向。本說明書中的任何內(nèi)容都不應(yīng)理解為需要結(jié)構(gòu)的特定三維方向才落入本發(fā)明的范圍內(nèi)。本發(fā)明提供了一種鐵路車輛車輪,該車輪通過本發(fā)明的熱處理方法形成。本發(fā)明的鐵路車輛車輪熱處理方法,包括以下步驟:(1)車輪經(jīng)整體加熱完全奧氏體化;(2)采用恒定壓力小流量噴水對所述車輪的踏面進(jìn)行短時間冷卻;(3)采用連續(xù)可控水量階梯式噴水對所述車輪的踏面進(jìn)行淬火,對所述車輪踏面以下形成均衡冷速,使整個車輪的輪輞區(qū)域獲得均衡的細(xì)珠光體組織。其中,所述步驟(2)和所述步驟(3)的總和時間為3-5分鐘,所述步驟(2)的時間為30-50秒,但本發(fā)明并不以此為限,能夠?qū)崿F(xiàn)本發(fā)明目的時間取值,均屬于本發(fā)明的上述時間的取值范圍。所述步驟(2)中的所述恒定壓力為0.8-0.9MPa,但本發(fā)明并不以此為限,能夠?qū)崿F(xiàn)本發(fā)明目的的恒定壓力值,均屬于本發(fā)明的恒定壓力取值范圍。而且本發(fā)明中,如圖2所示,圖2是根據(jù)一示例性實(shí)施方式示出的本發(fā)明鐵路車輛車輪熱處理方法中步驟(3)示意圖。所述步驟(3)包括依次連續(xù)的第一階段、第二階段、第三階段和第四階段,其中,所述第一階段的可控水量為V1,所述第二階段的可控水量為V2,所述第三階段的可控水量為V3,所述第四階段的可控水量為V4,且V1<V2<V3<V4,也即在這四個階段中,可控水量是在不斷上升的。另外,所述第一階段的時間為T1,所述第二階段的時間為T2,所述第三階段的時間為T3,所述第四階段的時間為T4,且T1<T2<T3<T4),也就是說這四個階段的用時是不斷增加的。而對于相鄰兩階段間的可控水量增量而言,其中,V2-V1=A1,V3-V2=A2,V4-V3=A3,且A1<A2<A3,也就是說水量的增量仍然是遞增的。本發(fā)明的一實(shí)施例如圖3所示,圖3是根據(jù)一示例性實(shí)施方式示出的本發(fā)明鐵路車輛車輪熱處理方法中對車輪進(jìn)行淬火的狀態(tài)示意圖。所述步驟(2)和所述步驟(3)中,所述車輪處于轉(zhuǎn)動狀態(tài)。該實(shí)施例中,所述車輪1水平轉(zhuǎn)動,如箭頭R所示,噴頭2的噴水方向?yàn)樗匠蛩鲕囕?的踏面12。本發(fā)明中通過較高水壓下小流量用于消除薄膜沸騰或縮短薄膜沸騰階段,同時避免較高冷速形成貝氏體,此后采用連續(xù)可控水量階梯式噴水淬火,對車輪踏面以下形成均衡冷速,使整個輪輞區(qū)域獲得均衡的細(xì)珠光體組織,從而獲得均衡的力學(xué)性能,即較高的強(qiáng)硬度和塑韌性,減小在車輪磨耗方向上的硬度梯度。本發(fā)明的方法最顯著的優(yōu)點(diǎn)是避免恒定水量淬火時表層冷速過高形成貝氏體組織(一種硬脆相,為車輪制造標(biāo)準(zhǔn)中明確杜絕的組織),內(nèi)部冷速過緩導(dǎo)致硬度及淬硬深度不夠。而且,根據(jù)車輪鋼的CCT曲線,確定材料的臨界冷卻速度,通過設(shè)置幾個淬火步驟,控制每一步淬火的噴水流量與噴水時間,可在輪輞區(qū)域獲得一個恒定的冷卻速度。這種連續(xù)、階梯式遞增、可控水量的淬火方式可保證車輪輪輞冷速的一致,使車輪輪輞區(qū)域的硬度梯度極大的減小,在整個車輪的磨耗區(qū)組織及性能狀態(tài)趨于一致,可明顯改善車輪的使用性能。采用上述熱處理方法,對一種碳含量在0.67-0.77%、錳含量在0.60-0.90%、硅含量在0.15-1.0%的高碳鋼重載鐵路車輪進(jìn)行熱處理,熱處理后車輪磨耗部位的硬度及其梯度如下圖4所示,從圖4中可以看出,車輪硬度較高,梯度合理,符合該類型車輪的設(shè)計原理。并對車輪踏面以下的微觀組織進(jìn)行測試(如圖5所示),1#、2#、3#樣的測試結(jié)果如下表1所示,金相照片分別見圖6,圖7,圖8。從測試結(jié)果看,車輪微觀組織均滿足車輪使用要求,即車輪整體組織為有較好耐磨性,同時不存在貝氏體等硬脆相,保證車輪的使用安全。車輪踏面由表及里鐵素體含量增加,硬度降低,符合車輪制造原理。由于高碳鋼極易發(fā)生相變,一般淬火方法難免在車輪表層生成貝氏體等有害組織,采用本發(fā)明的熱處理方法,有效避免了該問題。表1試樣編號微觀組織鐵素體含量(%)1#細(xì)珠光體+少量鐵素體0.102#細(xì)珠光體+少量鐵素體0.243#細(xì)珠光體+少量鐵素體0.42以上結(jié)合附圖示例說明了本發(fā)明的一些優(yōu)選實(shí)施例式。本發(fā)明所屬
技術(shù)領(lǐng)域:
的普通技術(shù)人員應(yīng)當(dāng)理解,上述具體實(shí)施方式部分中所示出的具體結(jié)構(gòu)和工藝過程僅僅為示例性的,而非限制性的。而且,本發(fā)明所屬
技術(shù)領(lǐng)域:
的普通技術(shù)人員可對以上所述所示的各種技術(shù)特征按照各種可能的方式進(jìn)行組合以構(gòu)成新的技術(shù)方案,或者進(jìn)行其它改動,而都屬于本發(fā)明的范圍之內(nèi)。當(dāng)前第1頁1 2 3