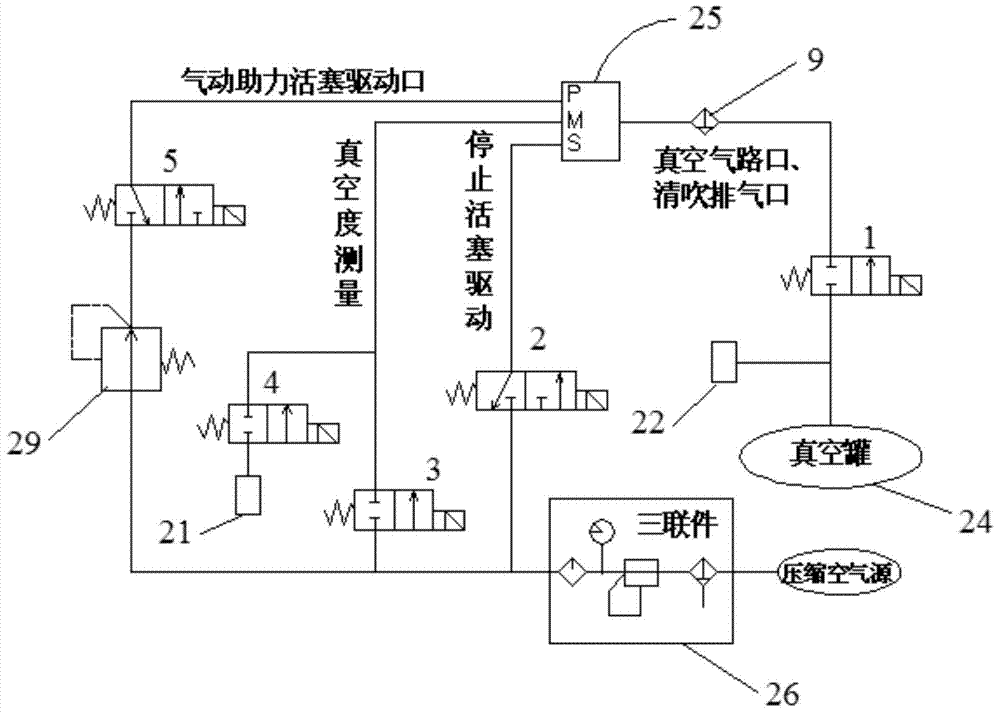
本發(fā)明涉及一種真空壓鑄輔助成型系統(tǒng),尤其涉及一種利用真空壓鑄技術(shù)的成型系統(tǒng)。
背景技術(shù):伴隨著全世界能源供應(yīng)越來越緊張,并且全球溫室效應(yīng)的氣體排放日益嚴重,再加上諸如汽車制造業(yè)的競爭越來越激烈的現(xiàn)狀,“低能低排低成本”的汽車先進制造技術(shù)便成為了汽車制造行業(yè)的一個可持續(xù)發(fā)展趨勢。而將轎車輕量化處理便是一種非常有效的節(jié)能減排的方法。在這個發(fā)展過程中,現(xiàn)階段的措施主要利用了鋁合金來代替以往鐵或著鋼等材料,如德國轎車型號AUDI--A8的全鋁合金制造的車身。隨著技術(shù)水平的日益發(fā)展,日本和德國等國家在制造高強韌鋁合金的成型技術(shù)方面都有相當大的發(fā)展,能制造出具有壁薄質(zhì)量輕、形狀復(fù)雜、高強度高韌性等優(yōu)點的零件。壓鑄是成型鋁合金鑄件的主要方法之一,在汽車零部件生產(chǎn)中占有相當大的比例。但是傳統(tǒng)壓鑄方法所制造出的壓鑄件內(nèi)部氣孔多,無法焊接或熱處理等原因,目前最先進的技術(shù)為采用真空壓鑄,真空壓鑄的原理是抽走或者抽走模具型腔里其中一部分的的氣體,使得減小型腔中的氣壓,從而讓沖型和合金熔體中氣體更容易排出,于是在壓力作用下熔融鋁液充滿型腔,并在壓強作用下凝固而得到壓鑄件結(jié)構(gòu)致密的一種成型工藝。但目前的真空壓鑄普遍存在如下問題,在模具調(diào)試、慢壓射和非正常生產(chǎn)時,由于現(xiàn)有的真空壓鑄輔助成型系統(tǒng)采用真空壓鑄,所以,導(dǎo)致了金屬液堵塞真空閥的問題。
技術(shù)實現(xiàn)要素:為解決上述技術(shù)問題,本發(fā)明的目的是提供一種具有兩種不同的工作模式,避免金屬液堵塞真空閥,也有助于改善產(chǎn)品質(zhì)量,提高生產(chǎn)效率的真空壓鑄輔助成型系統(tǒng)。本發(fā)明的一種真空壓鑄輔助成型系統(tǒng),包括壓室和型腔、連接在壓室和型腔之間的真空閥和氣路真空系統(tǒng)及控制所述氣路真空系統(tǒng)的電氣真空系統(tǒng),所述氣路真空系統(tǒng)包括第一壓力變送器、第二壓力變送器及依次串接的真空泵、真空罐、分流芯片和氣動三聯(lián)件,所述真空罐的出口端連接所述第二壓力變送器,所述分流芯片具有進口、P端出口、M端出口和S端出口,所述分流芯片的進口與真空罐連接,所述氣動三聯(lián)件分別連接至分流芯片的P端出口、M端出口、S端出口,所述分流芯片的M端出口還連接至第一壓力變送器,所述分流芯片的進口與真空罐之間設(shè)有使兩者導(dǎo)通或者斷開的第一開關(guān)裝置,所述氣動三聯(lián)件與分流芯片的P端出口之間設(shè)有使兩者導(dǎo)通或者斷開的第二開關(guān)裝置,所述氣動三聯(lián)件與分流芯片的M端出口之間設(shè)有使兩者導(dǎo)通或者斷開的第三開關(guān)裝置,所述氣動三聯(lián)件與分流芯片的S端出口之間設(shè)有使兩者導(dǎo)通或者斷開的第四開關(guān)裝置,所述分流芯片的M端出口與第二壓力變送器之間設(shè)有使兩者導(dǎo)通或者斷開的第五開關(guān)裝置。進一步的,所述分流芯片的P端出口與氣動三聯(lián)件之間還串接有調(diào)壓閥。進一步的,所述第一開關(guān)裝置、第二開關(guān)裝置、第三開關(guān)裝置、第四開關(guān)裝置和第五開關(guān)裝置均為電磁閥。進一步的,所述氣動三聯(lián)件包括串接的油霧器、減壓閥和過濾器。進一步的,所述氣路真空系統(tǒng)還包括設(shè)置在所述分流芯片的進口上的第一過濾器。進一步的,所述電氣真空系統(tǒng)包括控制器、與所述控制器信號連接的A/D轉(zhuǎn)換模塊、與所述A/D轉(zhuǎn)換模塊信號連接的壓力傳感器,所述壓力傳感器檢測真空閥、真空罐的數(shù)值,所述A/D轉(zhuǎn)換模塊接收真空閥、真空罐的數(shù)值并轉(zhuǎn)換成數(shù)字信號發(fā)送至控制器,所述控制器根據(jù)A/D轉(zhuǎn)換模塊所發(fā)送的數(shù)字信號及壓鑄信號控制真空泵、第一開關(guān)裝置、第二開關(guān)裝置、第三開關(guān)裝置、第四開關(guān)裝置和第五開關(guān)裝置。進一步的,所述電氣真空系統(tǒng)還包括與所述控制器信號連接的觸摸屏。進一步的,所述真空閥包括第一閥塊、相對設(shè)置在所述第一閥塊兩側(cè)的補償器和第二閥塊,所述第一閥塊與第二閥塊之間通過啟動氣缸連接,所述第一閥塊和第二閥塊之間還連接有從動氣缸,所述啟動氣缸具有啟動活塞,所述從動氣缸具有從動活塞,所述啟動活塞與從動活塞通過圓盤聯(lián)接。進一步的,所述第一閥塊和第二閥塊之間還連接有伺服氣缸,所述伺服氣缸具有固定在所述圓盤上的伺服活塞。進一步的,所述補償器背向所述第一閥塊的一側(cè)開設(shè)有凹腔,所述凹腔內(nèi)設(shè)置有補償器緩沖盤和補償導(dǎo)向盤,且所述補償導(dǎo)向盤位于所述補償器緩沖盤的外側(cè),所述補償器緩沖盤與補償導(dǎo)向盤之間通過螺栓連接,所述補償器緩沖盤和補償導(dǎo)向盤之間夾持有第一碟簧,所述第一閥塊和第二閥塊之間通過預(yù)緊栓連接,所述第二閥塊內(nèi)設(shè)置有碟簧槽,所述碟簧槽內(nèi)設(shè)置有碟簧,所述預(yù)緊栓的一端抵壓碟簧。本發(fā)明的有益效果如下:由于本發(fā)明的真空壓鑄輔助成型系統(tǒng)的氣路真空系統(tǒng)設(shè)置有第一壓力變送器、第二壓力變送器及依次串接的真空泵、真空罐、分流芯片和氣動三聯(lián)件,且上述部件連接中通過各開關(guān)實現(xiàn)相互之間的導(dǎo)通和斷開,從而使該真空壓鑄輔助成型系統(tǒng)具有兩種不同的工作模式,即普通壓鑄和真空壓鑄,以避免金屬液堵塞真空閥,也有助于改善產(chǎn)品質(zhì)量,提高生產(chǎn)效率。上述說明僅是本發(fā)明技術(shù)方案的概述,為了能夠更清楚了解本發(fā)明的技術(shù)手段,并可依照說明書的內(nèi)容予以實施,以下以本發(fā)明的較佳實施例并配合附圖詳細說明如后。附圖說明圖1是本發(fā)明所示的真空壓鑄輔助成型系統(tǒng)的結(jié)構(gòu)示意圖;圖2、圖3和圖4是用于本發(fā)明的真空壓鑄輔助成型系統(tǒng)的氣路真空系統(tǒng)在不同工作狀態(tài)時的原理圖;圖5是用于本發(fā)的真空壓鑄輔助成型系統(tǒng)的電氣真空系統(tǒng)的原理圖;圖6是用于本發(fā)明的真空壓鑄輔助成型系統(tǒng)的真空閥的剖視圖。具體實施方式下面結(jié)合附圖和實施例,對本發(fā)明的具體實施方式作進一步詳細描述。以下實施例用于說明本發(fā)明,但不用來限制本發(fā)明的范圍。請參見圖1和圖2,本發(fā)明一較佳實施例所述的一種真空壓鑄輔助成型系統(tǒng)包括殼體10、設(shè)置在所述殼體10內(nèi)的壓室(未圖示)和型腔(未圖示)、連接在壓室和型腔之間的真空閥(未圖示)和氣路真空系統(tǒng)20及控制所述氣路真空系統(tǒng)20的電氣真空系統(tǒng)。所述殼體10設(shè)置有第一控制箱30和第二控制箱40。所述氣路真空系統(tǒng)20包括第一壓力變送器21、第二壓力變送器22及依次串接的真空泵(未圖示)、真空罐24、分流芯片25和氣動三聯(lián)件26。上述第一壓力變送器21、第二壓力變送器22、分流芯片25和氣動三聯(lián)件26設(shè)置在第一控制箱30內(nèi),真空泵、真空罐24設(shè)置在第一控制箱30的外部。根據(jù)瑞士方達瑞真空系統(tǒng)及相關(guān)理論計算,真空壓鑄輔助成型系統(tǒng)的真空罐24的體積需大于100L,現(xiàn)有真空罐24形狀一般為方形罐體、腰型管體和柱形罐體,在本實施例中,該真空罐24選擇方形罐體,其原因為:方形罐體空間體積上達到了最大利用率,結(jié)構(gòu)緊湊,外觀上一體化,協(xié)調(diào)合理便于第一控制箱30的安放和真空泵的安裝。本實施例中的真空泵采用的型號為TX-25,該真空泵的技術(shù)參數(shù)如表1-1所示。表1-1真空泵技術(shù)參數(shù)表所述真空罐24的出口端連接所述第二壓力變送器22,所述分流芯片25具有進口、P端出口、M端出口和S端出口,所述分流芯片25的進口與真空罐24連接,所述氣動三聯(lián)件26分別連接至分流芯片25的P端出口、M端出口、S端出口,所述分流芯片25的M端出口還連接至第一壓力變送器21,所述分流芯片25的進口與真空罐24之間設(shè)有使兩者導(dǎo)通或者斷開的第一開關(guān)裝置,所述氣動三聯(lián)件26與分流芯片25的P端出口之間設(shè)有使兩者導(dǎo)通或者斷開的第二開關(guān)裝置,所述氣動三聯(lián)件26與分流芯片25的M端出口之間設(shè)有使兩者導(dǎo)通或者斷開的第三開關(guān)裝置,所述氣動三聯(lián)件26與分流芯片25的S端出口之間設(shè)有使兩者導(dǎo)通或者斷開的第四開關(guān)裝置,所述分流芯片25的M端出口與第第一壓力變送器21之間設(shè)有使兩者導(dǎo)通或者斷開的第五開關(guān)裝置。在本實施例中,上述第一開關(guān)裝置、第二開關(guān)裝置、第三開關(guān)裝置、第四開關(guān)裝置和第五開關(guān)裝置均為電磁閥,所述第一開關(guān)裝置為使真空罐24與分流芯片25的進口導(dǎo)通或者斷開的兩位兩通閥,該兩位兩通閥命名為閥1,所述第二開關(guān)裝置包括一個兩位三通閥(命名為閥5),所述分流芯片25的P端出口與氣動三聯(lián)件26之間還串接有調(diào)壓閥29,該調(diào)壓閥29串接在位于閥5與氣動三聯(lián)件26之間。所述第三開關(guān)裝置為一個兩位兩通閥(命名為閥3),所述第四開關(guān)裝置為一個兩位三通閥(命名為閥2),所述第五開關(guān)裝置為一個兩位兩通閥(命名為閥4)。除本實施例外,該第一開關(guān)裝置、第二開關(guān)裝置、第三開關(guān)裝置、第四開關(guān)裝置和第五開關(guān)裝置可以不為電磁閥,如可以為行程開關(guān)等。所述氣路真空系統(tǒng)20還包括設(shè)置在所述分流芯片25的進口上的第一過濾器27,該第一過濾器27的具體位置為:串接在第一開關(guān)裝置與分流芯片25的進口之間。所述氣動三聯(lián)件26包括依次串接的油霧器、減壓閥和過濾器,所述油霧器的進口分別與分流芯片25的P端出口、M端出口、S端出口連接,所述過濾器輸出壓縮空氣。上述氣路真空系統(tǒng)20可實現(xiàn)普通壓鑄和真空壓鑄兩種工作模式,如下:①普通壓鑄(即無抽真空壓鑄)在調(diào)試模具或慢壓射操作正常生產(chǎn)工作之前,因模具和真空閥溫度偏低,金屬的流動充型能力較差,此時,就選擇普通壓鑄模式。在該模式下,真空閥在合模狀態(tài)下始終處于關(guān)閉狀態(tài),即型腔中并沒有抽真空而直接進行壓鑄。當調(diào)試或模具溫度達到預(yù)定要求,金屬液能很好地充滿至真空閥的所有部位,即可切換到真空壓鑄模式。因此,在模具調(diào)試、慢壓射和非正常生產(chǎn)時使用此模式,否則,將會導(dǎo)致金屬液堵塞真空閥。該模式下電磁閥動作狀態(tài)如表1-2所示:表1-2普通壓鑄模式時電磁閥狀態(tài)表“-”標示斷電、“+”標示通電。②真空壓鑄真空壓鑄是指依靠金屬液的金屬動能來產(chǎn)生慣性沖擊力從而關(guān)閉閥芯的工作模式。在該模式下,型腔中的氣體邊抽出,金屬液邊充型,在金屬液到達真空閥排氣道末端之前,真空閥就依靠金屬液的沖擊力觸動使真空口與型腔隔絕,從面防止金屬液進入真空管道。其電磁閥動作狀態(tài)如表1-3所示:表1-3真空壓鑄模式下的電磁閥狀態(tài)表“-”標示斷電、“+”標示通電。請結(jié)合圖2至圖4,上述氣路真空系統(tǒng)20原理具體如下:該氣路真空系統(tǒng)20有兩個方面構(gòu)成,一個是真空通道,另一個是壓縮空氣通道。壓鑄機正常工作時,模具合模,當接收到?jīng)_頭封閉外澆口信號,經(jīng)過T1秒后閥1、閥4、閥5通電(閥1開啟抽真空功能,閥4開啟測量型腔真空度功能,閥5開啟氣動助力功能),啟動抽真空,同時開始測量型腔真空度(T2時間內(nèi)測量真空度,需保證壓射結(jié)束前測得),T2秒后閥4斷電(真空度測量完成),經(jīng)過T3秒后真空結(jié)束,此時閥1、閥5斷電(真空結(jié)束)。當接收到開模信號時閥3通電(開始吹氣),T5秒后閥3斷電(結(jié)束吹氣,噴吹時長T5秒,需保證噴吹時長大于噴脫模劑和涂料時間以防止脫模劑、涂料進入真空管道),等待下一個沖頭信號,經(jīng)T6秒延遲后若無動作則自動關(guān)機。請參見圖5,所述電氣真空系統(tǒng)包括設(shè)置在第二控制箱40內(nèi)的控制器31、與所述控制器31信號連接的A/D轉(zhuǎn)換模塊32、與所述A/D轉(zhuǎn)換模塊32信號連接的壓力傳感器33和觸摸屏34。所述壓力傳感器33檢測真空罐24、真空閥50的數(shù)值,所述A/D轉(zhuǎn)換模塊32接收壓力傳感器33的數(shù)值并轉(zhuǎn)換成數(shù)字信號發(fā)送至控制器31,所述控制器31根據(jù)A/D轉(zhuǎn)換模塊32所發(fā)送的數(shù)字信號及鑄壓信號,控制真空泵23、觸摸屏34、第一開關(guān)裝置、第二開關(guān)裝置、第三開關(guān)裝置、第四開關(guān)裝置和第五開關(guān)裝置。在本實施例中,所述控制器31選用PLC(ProgrammableLogicController,可編程邏輯控制器),其作為系統(tǒng)的中央處理器統(tǒng)領(lǐng)整個系統(tǒng),既要讀取外部輸入信號,如沖頭的封閉倒料口信號、壓鑄機的開模信號或壓鑄機開模到位信號等;又要輸出信號控制真空泵23的啟動停止、真空閥50的動作、觸摸屏34的數(shù)據(jù)顯示等。A/D轉(zhuǎn)換模塊從壓力傳感器33讀取模擬信號轉(zhuǎn)換成數(shù)字信號,控制器31通過讀取指令把數(shù)據(jù)讀取并存儲到指定的數(shù)據(jù)寄存器。觸摸屏34與控制器31進行通信,能夠輕松實現(xiàn)人機之間的溝通,并能對控制器31的軟元件進行實時監(jiān)控和數(shù)據(jù)讀寫。請參見圖6,所述真空閥包括第一閥塊41、相對設(shè)置在所述第一閥塊41兩側(cè)的補償器42和第二閥塊43。所述第一閥塊41與第二閥塊43之間通過啟動氣缸44連接,所述第一閥塊41和第二閥塊43之間還連接有從動氣缸(未標號)和伺服氣缸46,所述啟動氣缸44具有固定在第一閥塊41上的啟動缸體和設(shè)置在所述第二閥塊43上的啟動活塞,所述從動氣缸具有固定在第一閥塊41上的從動缸體和設(shè)置在第二閥塊43上的從動活塞,所述伺服氣缸46具有固定在第一閥塊41上的伺服缸體和設(shè)置在所述第二閥塊43上的伺服活塞,所述啟動活塞、從動活塞、伺服活塞通過圓盤45聯(lián)接。所述補償器42背向所述第一閥塊41的一側(cè)開設(shè)有凹腔421,所述凹腔421內(nèi)設(shè)置有補償器緩沖盤471和補償導(dǎo)向盤472,且所述補償導(dǎo)向盤472位于所述補償器緩沖盤471的外側(cè),所述補償器緩沖盤471與補償導(dǎo)向盤472之間通過螺栓473連接,所述補償器緩沖盤471和補償導(dǎo)向盤472之間夾持有第一碟簧474,所述第一閥塊41和第二閥塊43之間通過預(yù)緊栓48連接,所述第二閥塊43內(nèi)設(shè)置有碟簧槽431,所述碟簧槽431內(nèi)設(shè)置有第二碟簧432,所述預(yù)緊栓48的一端抵壓第二碟簧432。該真空閥通過使用圓盤45聯(lián)接啟動氣缸44和從動氣缸,同時加入伺服氣缸46,提高傳動機構(gòu)的靈敏性;通過設(shè)置第一碟簧474預(yù)緊防止壓鑄過程中金屬液飛出;通過設(shè)置第二碟簧432鎖定復(fù)位。該真空閥的工件原理如下:①、一個壓鑄過程開始,壓鑄模具做合模動作,補償器42與模具動模一同移動,同時推動預(yù)緊栓48帶動補償器緩沖盤471移動使第一碟簧474壓縮讓真空閥處于解鎖狀態(tài);②、當壓鑄機沖頭動作時,壓室和模具型腔處于封密狀態(tài),此時開啟抽真空模式,使封密的壓室和型腔與通過真空閥與真空罐連通,實現(xiàn)壓鑄全過程處于真空狀態(tài);③、當金屬液充滿型腔通過進料口進入真空閥導(dǎo)入流道,其首先觸碰到啟動氣缸44,此時啟動氣缸44在金屬動能推動下通過圓盤45帶動排氣活塞51和伺服氣缸46產(chǎn)生約0.7mm的位移,伺服氣缸46在產(chǎn)生位移的過程中因受到壓縮空氣的受力面積突然變大,因而有足夠的力帶動圓盤45連同排氣活塞51繼續(xù)運動,從而使排氣活塞51關(guān)閉,抽真空結(jié)束(此時真空管路與型腔斷開,從而防止金屬液進入真空管路)。這一過程在金屬液到達從動氣缸前完成(這一過程可在1ms內(nèi)完成)。④、當充填過程完成并冷卻后,壓鑄模具打開,被壓縮的第二碟簧432彈力釋放,推動導(dǎo)向盤52,從而帶動圓盤45和啟動氣缸44,排氣活塞51,伺服氣缸46復(fù)位鎖定,在復(fù)位的同時排氣活塞51還具有將真空閥內(nèi)的迷宮槽金屬凝料推出作用,保證其留在動模一側(cè)。當模具開模到位后,真空壓鑄輔助成型系統(tǒng)接收到信號啟動反吹功能,經(jīng)過濾后的壓縮空氣從排氣活塞51底部吹出,實現(xiàn)自動清潔功能,提高真空閥的在線工作時長。根據(jù)上述真空閥的動作要求和真空壓鑄輔助成型系統(tǒng)所處的現(xiàn)場工作環(huán)境,真空壓鑄輔助成型系統(tǒng)需要滿足的要求有以下幾點:①系統(tǒng)必須要保證現(xiàn)場使用的可靠性和穩(wěn)定性;②盡可能地選擇耐高溫、耐腐蝕、抗震性好、使用壽命長的元件;③對需要檢測的物理量進行實時監(jiān)控,如真空罐真空度、型腔真空度、污染度以及油缸壓力等,當檢測到壓力超過預(yù)設(shè)的上限或者下限時,真空壓鑄輔助成型系統(tǒng)能夠及時報警停機;④真空壓鑄輔助成型系統(tǒng)參數(shù)可修改。根據(jù)壓鑄生產(chǎn)的實際情況,該真空壓鑄輔助成型系統(tǒng)通過采用PLC控制,從而適用于各種壓鑄機。該真空壓鑄輔助成型系統(tǒng)有普通壓鑄(無抽真空壓鑄)和真空壓鑄兩種工作模式,以及可進行模具密封性能測試、對不同模具或壓鑄機的可調(diào)節(jié)性、真空管路堵塞狀態(tài)測試等功能,同時還可具有報警、數(shù)據(jù)顯示等多種功能。該真空壓鑄輔助成型系統(tǒng)工作過程如下:當真空壓鑄輔助成型系統(tǒng)檢測到壓鑄機的沖頭封閉壓室的澆注口(即接受到真空啟動信號)時,PLC發(fā)出打開真空管路的信號,開始抽真空,并實時測量型腔中的真空度。當金屬液觸動主動活塞,真空閥關(guān)閉,抽真空結(jié)束,當檢測到開?;蜷_模到位信號(即真空停止信號)時,PLC開啟真空閥反吹功能。壓鑄完畢,壓鑄模打開時,在壓鑄機取件、噴涂等工序期間,真空壓鑄輔助成型系統(tǒng)則完成真空閥復(fù)位、真空閥清洗、真空管路測試等動作。當檢測到壓鑄模合模信號時,真空閥自鎖解除,為下一壓鑄循環(huán)做好準備。綜上所述,上述真空壓鑄輔助成型系統(tǒng)的氣路真空系統(tǒng)20設(shè)置有第一壓力變送器21、第二壓力變送器22及依次串接的真空泵23、真空罐24、分流芯片25和氣動三聯(lián)件26,且上述部件連接中通過各開關(guān)實現(xiàn)相互之間的導(dǎo)通和斷開,從而使該真空壓鑄輔助成型系統(tǒng)具有兩種不同的工作模式,即普通壓鑄和真空壓鑄,避免金屬液堵塞真空閥,也有助于改善產(chǎn)品質(zhì)量,提高生產(chǎn)效率。以上所述僅是本發(fā)明的優(yōu)選實施方式,并不用于限制本發(fā)明,應(yīng)當指出,對于本技術(shù)領(lǐng)域的普通技術(shù)人員來說,在不脫離本發(fā)明技術(shù)原理的前提下,還可以做出若干改進和變型,這些改進和變型也應(yīng)視為本發(fā)明的保護范圍。