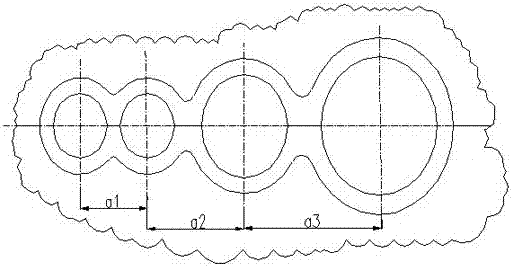
本發(fā)明屬于齒輪箱箱體裝置的領(lǐng)域,尤其是涉及一種用于提高大型齒輪箱箱體裝置形位精度的加工方法。
背景技術(shù):齒輪箱傳動(dòng)技術(shù)應(yīng)用十分廣泛,多數(shù)使用工況特別惡劣,要求在連續(xù)承受沖擊、振動(dòng)、過載的情況下運(yùn)行,而且使用壽命要求15年以上,同時(shí)隨著經(jīng)濟(jì)的發(fā)展和科技進(jìn)步,工業(yè)企業(yè)向著環(huán)境美好型、資源節(jié)約型、節(jié)能增效型、大型超大型化發(fā)展,工業(yè)企業(yè)裝備同時(shí)朝著大型化發(fā)展,尤其是冶金、礦山、水電等行業(yè)上所用傳動(dòng)齒輪箱傳遞功率由幾百千瓦發(fā)展到目前的上萬千瓦,設(shè)備規(guī)格越來越大,精度是越來越高。這樣對(duì)傳動(dòng)齒輪箱的可靠性提出了更高要求,因而對(duì)齒輪箱設(shè)計(jì)和制造提出了更高的要求。傳動(dòng)齒輪箱由傳遞運(yùn)動(dòng)和扭矩的齒輪及承載齒輪的箱體裝置組成,傳動(dòng)齒輪箱的設(shè)計(jì)和制造質(zhì)量高低直接影響齒輪箱整機(jī)的使用壽命,一旦設(shè)計(jì)定型,其主要矛盾就轉(zhuǎn)化為零件的制造上。傳遞運(yùn)動(dòng)和扭矩的齒輪制造由高精密的數(shù)控成型磨齒機(jī)磨削精加工已替代傳統(tǒng)的滾齒和展成磨削精加工,齒輪制造精度已達(dá)到3-5級(jí);而承載齒輪的箱體裝置(圖1和圖2)仍由傳統(tǒng)工藝流程加工,即:龍門刨床或龍門銑床等對(duì)箱體裝置剖分面和基準(zhǔn)面A實(shí)施粗加工——鏜床對(duì)箱體裝置軸孔實(shí)施粗加工——去應(yīng)力時(shí)效處理——龍門刨床或龍門銑床等對(duì)箱體裝置剖分面和基準(zhǔn)面A實(shí)施精加工——鏜床對(duì)箱體裝置軸孔實(shí)施精加工。結(jié)合示意圖1~7簡述其工藝流程如下:步驟1、劃線檢查箱體裝置(圖1和圖2)組件箱體1、箱蓋2各加工面余量,保證各部余量均勻。步驟2、將箱體裝置(圖1和圖2)組件箱體1、箱蓋2依次置于普通龍門刨床(圖3)或龍門銑床(圖4)上的等高墊鐵3上,對(duì)箱體1剖分面和基準(zhǔn)面A、箱蓋2剖分面粗加工,粗加工時(shí)各面以等高墊鐵3為基準(zhǔn),按工藝規(guī)范留取余量。步驟3、將箱體裝置(圖1和圖2)組件箱體1、箱蓋2依次置于普通鏜床上的等高墊鐵3上(圖5),對(duì)箱體裝置組件箱體1、箱蓋2半軸孔及其端面的粗加工,按工藝規(guī)范留取余量。步驟4、將步驟3所得進(jìn)行人工去應(yīng)力時(shí)效處理,以釋放毛坯殘余應(yīng)力和粗加工應(yīng)力,使內(nèi)部組織達(dá)到平衡和穩(wěn)定狀態(tài)。步驟5、將步驟4所得置于劃線平臺(tái)上,劃十字中心對(duì)稱線,劃各剖分面和基準(zhǔn)面A加工線。步驟6、將步驟5所得依次置于普通龍門刨床(圖3)或龍門銑床(圖4)上的等高墊鐵3上,找正壓緊后依次對(duì)箱體1剖分面和基準(zhǔn)面A、箱蓋2剖分面精加工。步驟7、劃箱體1、箱蓋2剖分面上聯(lián)接孔線;由鉆床加工箱體剖分面聯(lián)接孔;鉗工將箱體1、箱蓋2按對(duì)應(yīng)關(guān)系用聯(lián)接件把合組裝成箱體裝置(圖1和圖2);劃箱體裝置(圖1和圖2)十字中心對(duì)稱線及各軸孔位置線。步驟8、將步驟7所得箱體裝置(圖1和圖2)基準(zhǔn)面A置于鏜床等高墊鐵3上(圖6),軸孔端面對(duì)鏜床主軸18,找正軸孔中心線與鏜床主軸18軸線在同一平面內(nèi),誤差不大于0.3mm,按所劃十字中心對(duì)稱線找正箱體裝置,選定好切削用量(主軸轉(zhuǎn)速、鏜削深度、進(jìn)給速度)后,鏜床主軸18旋轉(zhuǎn)加水平橫向進(jìn)給運(yùn)動(dòng)和鏜床立柱17縱向運(yùn)動(dòng),一次裝卡粗鏜、半精鏜、精鏜箱體裝置各軸線上兩側(cè)軸孔及其一側(cè)軸孔端面,或箱體裝置一側(cè)軸孔及其端面,同時(shí)工藝要求在箱體裝置一端剖分面處全長銑一調(diào)裝找正基準(zhǔn);調(diào)裝,按已加工成軸孔圈圓鏜桿找正同心,找正箱體裝置一端工藝基準(zhǔn),以保證軸孔中心線垂直于軸孔端面,粗鏜、半精鏜、精鏜箱體裝置另一側(cè)軸孔端面,或另一側(cè)軸孔及其端面。步驟9最終測(cè)量。軸孔的形位精度在機(jī)床上用千分表在線檢測(cè),軸孔幾何精度由專業(yè)檢測(cè)人員利用量具測(cè)量。上述箱體裝置的加工是選用不同的設(shè)備機(jī)床、分工序加工,且鏜床加工軸孔時(shí)鏜床主軸18旋出很長,剛性差,加工精度較低,其加工精度一般7級(jí)或更低,軸孔粗糙度為Ra3.2~Ra6.3。再之傳統(tǒng)加工方法的設(shè)備能力有限,只適用于小型、中型齒輪箱體裝置的加工要求。目前最大鏜床的軸向最大旋出長度(主軸+滑枕)3800mm,而如圖5~10所示,鏜床工作臺(tái)16的邊沿距鏜床立柱17的距離L1約500mm,再加上箱體裝置的邊沿距鏜床工作臺(tái)16邊沿距離L2(便于裝卡,其距離根據(jù)箱體尺寸大小而定)約300mm,再加上箱體裝置(圖8~10)邊沿到軸孔端面的距離L3約為400mm及軸孔的深度300mm,鏜銑床要完成齒輪箱箱體裝置(圖8~10)一側(cè)軸孔的加工,鏜床主軸18軸向水平旋出長度大于1500mm(L1+L2+L3+軸孔深度),再加上圖8所示箱體裝置同一軸線上軸孔跨距3550mm,無法實(shí)現(xiàn)一次裝卡完成如圖8~10所示的大型、超大型、高精度齒輪箱箱體裝置同一軸心線上兩側(cè)軸孔的加工;若一次裝卡加工一側(cè)軸孔,調(diào)裝加工另一側(cè)軸孔,由于箱體裝置(圖8~10)規(guī)格超大,調(diào)裝非常困難,找正困難,存在調(diào)裝變形和二次找正誤差,找正和加工精度難以保證;而采用精密數(shù)控鏜銑床的旋轉(zhuǎn)移動(dòng)工作臺(tái),其旋轉(zhuǎn)精度8″,若完成一側(cè)軸孔加工,旋轉(zhuǎn)180°加工另一側(cè)軸孔,則另一側(cè)軸孔相對(duì)于一側(cè)軸孔位置精度為tan(8/3600)×(3550/2)=0.069mm,已超出(圖8~10)所要求0.03mm的一倍多;再加上鏜床主軸18軸向水平旋出越長,剛性越差,很難滿足大型、超大型、高精度箱體裝置(圖8~10)加工要求。
技術(shù)實(shí)現(xiàn)要素:本發(fā)明的目的是為解決現(xiàn)有技術(shù)中調(diào)裝非常困難,找正困難,存在調(diào)裝變形和二次找正誤差,找正和加工精度難以保證的問題,提供一種用于提高大型齒輪箱箱體裝置形位精度的加工方法。本發(fā)明為解決上述技術(shù)問題的不足,所采用的技術(shù)方案是:一種用于提高大型齒輪箱箱體裝置形位精度的加工方法,包括如下步驟:步驟1劃線:取箱體的分箱體鑄組件依次為下箱體、下中箱體、上中箱體和上箱體,將下箱體、下中箱體、上中箱體和上箱體放在劃線平臺(tái)上,檢查下箱體、下中箱體、上中箱體和上箱體的毛坯余量,通過劃線確定下箱體、下中箱體、上中箱體和上箱體的加工余量,然后分別以下箱體、下中箱體、上中箱體和上箱體的內(nèi)腔非加工面為基準(zhǔn)劃線:分別確定下箱體十字中心對(duì)稱線,下箱體上剖分面T和基準(zhǔn)面B的加工線,下箱體上的半軸孔L1和半軸孔L2的中心位置線及其圓線;下中箱體十字中心對(duì)稱線,下中箱體上剖分面T和剖分面S的加工線,下中箱體上的半軸孔L1、半軸孔L2、半軸孔M1、半軸孔M2、半軸孔N1和半軸孔N2的中心位置線及其圓線;上中箱體十字中心對(duì)稱線,上中箱體上的剖分面S和剖分面R的加工線,上中箱體上的半軸孔M1、半軸孔M2、半軸孔N1、半軸孔N2、半軸孔K1、半軸孔K2的中心位置線及其圓線;上箱體十字中心對(duì)稱線,上箱體上的剖分面R、剖分面P的加工線,上箱體上的半軸孔K1、半軸孔K2的中心位置線和半軸孔圓線;步驟2對(duì)各分箱體剖分面及半軸孔的粗加工:取用數(shù)個(gè)等高墊鐵并將等高墊鐵均勻分布于鏜銑床的工作臺(tái)上,將步驟1所得下箱體放于等高墊鐵上,使下箱體的剖分面T與等高墊鐵頂部平面重合,按步驟1所劃線進(jìn)行找正,使找正精度不大于0.5mm,然后用工藝螺栓壓板將下箱體固定于鏜銑床的工作臺(tái)上,選裝外圓直徑為φ200mm的面銑刀對(duì)下箱體基準(zhǔn)面B進(jìn)行粗加工,并使基準(zhǔn)面B單面留取余量10mm,重新調(diào)裝下箱體,將下箱體轉(zhuǎn)動(dòng)后置于等高墊鐵上,使已加工基準(zhǔn)面B與等高墊鐵頂部平面重合,已加工基準(zhǔn)面B與等高墊鐵頂部平面的不重合精度不大于0.05mm,重新找正下箱體的十字中心對(duì)稱線,使找正精度不大于0.5mm,然后用工藝螺栓壓板將下箱體固定于鏜銑床的工作臺(tái)上,采用加工基準(zhǔn)面B同樣的銑刀和參數(shù),啟動(dòng)機(jī)床對(duì)下箱體剖分面T進(jìn)行粗加工,使單面留取余量10mm,工件同工位,重新調(diào)整機(jī)床,拆去外圓直徑φ200mm面銑刀,換裝可調(diào)鏜銑刀并調(diào)整機(jī)床工位,使鏜軸對(duì)應(yīng)半軸孔L2,并按線找正半軸孔L2,使找正精度不大于0.5mm,啟動(dòng)機(jī)床,對(duì)下箱體半軸孔L2進(jìn)行粗加工,使半軸孔L2直徑留取余量25mm;重新調(diào)裝下箱體,下箱體的半軸孔L1對(duì)應(yīng)鏜軸,采用同半軸孔L2同樣方法對(duì)半軸孔L1進(jìn)行粗加工,利用所述下箱體加工其上的剖分面T半軸孔L2、半軸孔L1粗加工的方法,對(duì)下中箱體的剖分面T和剖分面S及其半軸孔L2、半軸孔L1、半軸孔M2、半軸孔M1、半軸孔N2、半軸孔N1進(jìn)行粗加工;利用所述下箱體加工其上的剖分面T半軸孔L2、半軸孔L1粗加工的方法,對(duì)上中箱體剖分面S和剖分面R及其半軸孔M2、半軸孔M1、半軸孔N2、半軸孔N1、半軸孔K2、半軸孔K1進(jìn)行粗加工;利用所述下箱體加工其上的剖分面T半軸孔L2、半軸孔L1粗加工的方法,對(duì)上箱體的剖分面R和剖分面P及其半軸孔K2和半軸孔K1進(jìn)行粗加工;步驟3人工時(shí)效:將步驟2所得下箱體、下中箱體、上中箱體和上箱體進(jìn)行人工時(shí)效,釋放毛坯殘余應(yīng)力和粗加工應(yīng)力,使步驟2所得下箱體、下中箱體、上中箱體和上箱體的內(nèi)部組織趨于穩(wěn)定,從而保證步驟2所得下箱體、下中箱體、上中箱體和上箱體結(jié)構(gòu)穩(wěn)定;步驟4二次劃線:取步驟3中時(shí)效后的下箱體、下中箱體、上中箱體和上箱體并放上劃線平臺(tái),檢查步驟3所得下箱體、下中箱體、上中箱體、上箱體變形量,以確定各部余量,來確定并劃下箱體剖分面T和基準(zhǔn)面B加工線,劃下中箱體剖分面T和剖分面S加工線,劃上中箱體剖分面S和剖分面R加工線,劃上箱體剖分面R和剖分面P加工線,同時(shí)以各分箱體內(nèi)腔非加工面為基準(zhǔn)劃:下箱體十字中心對(duì)稱線,及其半軸孔L1和半軸孔L2中心位置線及其圓線;下中箱體十字中心對(duì)稱線,及其半軸孔L1、半軸孔L2、半軸孔M1、半軸孔M2、半軸孔N1和半軸孔N2中心位置線及其圓線;上中箱體十字中心對(duì)稱線,及其各半軸孔M1、半軸孔M2、半軸孔N1、半軸孔N2,半軸孔K1和半軸孔K2的中心位置線及其圓線;上箱體十字中心對(duì)稱線,及其上半軸孔K1和半軸孔K2中心位置線及其圓線;步驟5對(duì)分箱體剖分面及半軸孔進(jìn)行半精加工:將數(shù)個(gè)等高墊鐵均勻分布于數(shù)控龍門銑鏜床的工作臺(tái)上,然后取步驟4中劃線后的下箱體并放于等高墊鐵上,使下箱體的剖分面T與等高墊鐵頂面重合,按步驟4所劃十字中心對(duì)稱線對(duì)下箱體進(jìn)行找正,找正精度不大于0.5mm,找正后用工藝螺栓壓板將下箱體固定于工作臺(tái)上,調(diào)整機(jī)床,選用外圓直徑φ200mm面銑刀裝于機(jī)床銑鏜主軸上,取銑刀切削參數(shù)是轉(zhuǎn)速200r/min、切削深度3~3.5mm、直線進(jìn)給速度1000mm/min并編寫程序并輸入程序,調(diào)試程序合格后啟動(dòng)機(jī)床,對(duì)下箱體基準(zhǔn)面B進(jìn)行半精加工,加工時(shí)留取精加工余量1mm;然后調(diào)裝下箱體,將下箱體轉(zhuǎn)動(dòng)后置于等高墊鐵上,使下箱體已加工的基準(zhǔn)面B與等高墊鐵頂面重合,使不重合精度不大于0.05mm,按步驟4所劃十字中心對(duì)稱線找正下箱體,使找正精度不大于0.5mm,找正后用工藝螺栓壓板將下箱體固定于工作臺(tái)上,調(diào)整機(jī)床采用相同刀具和加工參數(shù)對(duì)下箱體剖分面T進(jìn)行半精加工并留取精加工余量1mm;工件同工位,重新調(diào)整機(jī)床,拆去外圓直徑φ200mm面銑刀,換直角鏜銑裝置和外圓直徑φ200mm插補(bǔ)鏜銑刀,調(diào)整機(jī)床工位,按步驟4所劃半軸孔L2中心位置線找正半軸孔L2,找正精度不大于0.5mm,取插補(bǔ)鏜銑刀切削參數(shù)是轉(zhuǎn)速200r/min、切削深度6mm、圓周進(jìn)給速度1000mm/min,步長5mm,編寫并輸入程序,調(diào)試程序合格后啟動(dòng)機(jī)床,對(duì)下箱體半軸孔L2進(jìn)行半精加工,留取余量13mm;重新調(diào)整機(jī)床工位采用同樣刀具和加工參數(shù)對(duì)下箱體半軸孔L1進(jìn)行半精加工,留取余量13mm;利用所述下箱體加工其上的剖分面T半軸孔L2、半軸孔L1半精加工的方法,對(duì)下中箱體剖分面T和剖分面S及其半軸孔L2、半軸孔L1、半軸孔M2、半軸孔M1、半軸孔N2和半軸孔N1進(jìn)行半精加工,利用所述下箱體加工其上的剖分面T半軸孔L2、半軸孔L1半精加工的方法,對(duì)上中箱體剖分面S和剖分面R及其半軸孔M2、半軸孔M1、半軸孔N2、半軸孔N1、半軸孔K2和半軸孔K1進(jìn)行半精加工,利用所述下箱體加工其上的剖分面T半軸孔L2、半軸孔L1半精加工的方法,對(duì)上箱體剖分面R和剖分面P及其半軸孔K2和半軸孔K1進(jìn)行半精加工;步驟6自然時(shí)效:將步驟5所得下箱體、下中箱體、上中箱體和上箱體放置于工件存儲(chǔ)區(qū),進(jìn)行16-48小時(shí)的自然時(shí)效,以充分釋放毛坯殘余應(yīng)力、熱處理應(yīng)力及加工應(yīng)力,保證各分箱體結(jié)構(gòu)穩(wěn)定性,為保證精加工精度奠定良好基礎(chǔ);步驟7各分箱體剖分面的精加工:將數(shù)個(gè)等高墊鐵均勻分布于精密數(shù)控龍門銑鏜床的工作臺(tái)上,銑等高墊鐵上端面,使所有等高墊鐵的上端面處于同一平面內(nèi)且與數(shù)控龍門銑鏜床銑鏜軸回轉(zhuǎn)中心垂直,所述垂直精度不大于0.05mm,取經(jīng)過步驟6時(shí)效后的下箱體放置在等高墊鐵上并使其剖分面T與等高墊鐵頂面重合,按步驟4所劃十字中心對(duì)稱線找正,找正精度不大于0.5mm,找正后用工藝螺栓壓板將下箱體固定于工作臺(tái)上,調(diào)整機(jī)床,選用外圓直徑φ200mm面銑刀,加工切削參數(shù)是轉(zhuǎn)速300r/min、切削深度0.15mm、直線進(jìn)給速度500mm/min,編制并輸入程序,調(diào)試程序合格后啟動(dòng)機(jī)床,對(duì)下箱體基準(zhǔn)面B進(jìn)行精加工;轉(zhuǎn)動(dòng)下箱體并置于等高墊鐵上,使下箱體已加工基準(zhǔn)面B與等高墊鐵頂面重合,不重合精度不大于0.05mm,按步驟4所劃十字中心對(duì)稱線找正,找正精度不大于0.5mm,滿足找正精度后用工藝螺栓壓板將下箱體固定于工作臺(tái)上,調(diào)整機(jī)床后采用相同刀具及加工參數(shù)對(duì)下箱體剖分面T進(jìn)行精加工,加工后對(duì)下箱體進(jìn)行重新劃線,以下箱體內(nèi)腔非加工面為基準(zhǔn)劃十字中心對(duì)稱線,以十字中心對(duì)稱線為基準(zhǔn)劃剖分面T上把合聯(lián)接孔位置線,調(diào)整機(jī)床,拆去外圓直徑φ200mm面銑刀,換裝鉆鏜孔刀具,鉆鏜剖分面T上把合聯(lián)接孔;采用加工下箱體的方法,依次對(duì)下中箱體的剖分面T和剖分面S進(jìn)行精加工及其把合聯(lián)接孔加工;對(duì)上中箱體的剖分面和剖分面R進(jìn)行精加工及其把合聯(lián)接孔加工;對(duì)上箱體的剖分面R和剖分面P進(jìn)行精加工及其把合聯(lián)接孔加工;步驟8箱體裝置組裝:取步驟7中加工過的下箱體、下中箱體、上中箱體和上箱體以及取工藝聯(lián)接件,將各件去除毛刺,清理干凈,備用,將等高墊鐵均布放置于工作臺(tái)并找正上,等高墊鐵找正精度不大于0.05mm,將下箱體置于等高墊鐵上,使下箱體B基準(zhǔn)面與等高墊鐵頂面重合,不重合精度不大于0.05mm,依次將下中箱體相配剖分面T相對(duì)疊加于下箱體上,兩箱體十字中心對(duì)稱線對(duì)齊,把合聯(lián)接孔對(duì)正,內(nèi)腔和外形對(duì)正,對(duì)正后再將上中箱體相配剖分面S相對(duì)疊加于下中箱體上,兩箱體十字中心對(duì)稱線對(duì)齊,把合聯(lián)接孔對(duì)正,內(nèi)腔和外形對(duì)正,對(duì)正后再將上箱體相配剖分面R相對(duì)疊加于上中箱體上,兩箱體十字中心對(duì)稱線對(duì)齊,把合聯(lián)接孔對(duì)正,內(nèi)腔和外形對(duì)正,對(duì)正后,穿入工藝聯(lián)接件將下箱體、下中箱體、上中箱體和上箱體把緊組裝成箱體裝置,各箱體相對(duì)剖分面R、剖分面S和剖分面T重合,重合精度不大于0.05mm,以十字中心對(duì)稱線為基準(zhǔn)劃各軸孔位置線及軸孔圓線;步驟9箱體裝置軸孔精加工:①將數(shù)個(gè)等高墊鐵均布放置于工作臺(tái)上,銑平所有等高墊鐵上端面等高墊鐵的上端面使其處于同一平面內(nèi)且與銑鏜主軸回轉(zhuǎn)中心垂直,所述平面精度不大于0.05mm;將步驟8所得箱體裝置放置于等高墊鐵上,使箱體裝置內(nèi)的B基準(zhǔn)面與等高墊鐵頂面重合,所述重合精度不大于0.05mm;按步驟8中劃線確定的箱體裝置十字中心對(duì)稱線找正,找正精度不大于0.5mm;按步驟8所劃各軸孔位置線及圓線找正各軸孔圓心,保證水平各軸孔中心在剖分平面內(nèi)、垂直各軸孔中心在垂直于剖分面的平面內(nèi),找正精度不大于0.3mm;找正后用工藝螺栓壓板將箱體裝置固定于工作臺(tái)上,復(fù)查所述找正精度,不滿足找正精度要求時(shí)重復(fù)找正,滿足找正精度要求后待用;②編制數(shù)控程序,將箱體裝置的軸孔圖紙參數(shù)和所選擇的切削參數(shù)編制數(shù)控程序,選插補(bǔ)銑刀的切削參數(shù)為轉(zhuǎn)速200r/min,切削深度5mm,圓周進(jìn)給速度1000mm/min,步長5mm;③將數(shù)控龍門銑鏜床直角鏜銑裝置裝于銑鏜床銑鏜主軸上,且移到軸孔K2的中心,再將外圓直徑φ200mm插補(bǔ)銑刀裝于數(shù)控龍門銑鏜床直角鏜銑裝置上,輸入②中編制的程序并調(diào)試,調(diào)試合格后啟動(dòng)機(jī)床,通過數(shù)控龍門銑鏜床直角鏜銑裝置,按②中編制的程序半精加工一側(cè)軸孔K2及其端面,按工藝規(guī)范各加工面單面均留余量1.5mm;通過調(diào)整機(jī)床,按程序保證孔距,同加工軸孔K2原理加工同側(cè)軸孔M2及其端面;再通過調(diào)整機(jī)床,按程序保證孔距,同加工軸孔K2原理加工同側(cè)軸孔N2及其端面;再通過調(diào)整機(jī)床,按程序保證孔距,同加工軸孔K2原理加工同側(cè)軸孔L2及其端面,然后調(diào)整機(jī)床復(fù)位到加工軸孔K2位置,插補(bǔ)銑刀每完成一次插補(bǔ)過程沿軸孔軸向方向進(jìn)給步長5mm,重復(fù)進(jìn)給前的加工過程,直至完成所有軸孔加工;④工件同工位,調(diào)整機(jī)床,同③所述插補(bǔ)粗加工箱體裝置另一側(cè)的軸孔K1、軸孔M1、軸孔N1、軸孔L1及各軸孔的端面;完成后在箱體裝置一端上中箱體和下中箱體結(jié)合面處全長銑一精加工找正工藝基準(zhǔn),該基準(zhǔn)的粗糙度Ra3.2,加工完成后松開工藝螺栓壓板,充分釋放加工應(yīng)力,待工件冷至室溫后重新找正;⑤箱體裝置軸孔鏜銑半精加工,按①所述找正要求找正,同時(shí)將①按十字中心對(duì)稱線找正替換成按③~④工步所銑上中箱體、下中箱體結(jié)合面處工藝找正基準(zhǔn)找正,找正精度不大于0.05mm,而后重新將箱體裝置用工藝螺栓壓板固定于工作臺(tái)上,調(diào)整機(jī)床,將調(diào)整范圍為φ800~φ900mm或φ1000~φ1100mm可調(diào)鏜銑刀裝于數(shù)控龍門銑鏜床直角鏜銑裝置上,選取切削參數(shù)轉(zhuǎn)速為25~30r/min、橫向進(jìn)給0.1mm/r、切削深度0.25mm,按③~④所述加工順序加工各軸孔,各軸孔直徑留取精加工余量0.6mm;⑥激光跟蹤儀配合機(jī)床檢測(cè)形位精度;⑦箱體裝置軸孔精加工:將可調(diào)鏜銑刀復(fù)位到初始孔位,校正軸孔圓心,所述精度不大于0.02mm,然后根據(jù)⑥檢測(cè)結(jié)果,微調(diào)程序,按⑤所述對(duì)箱體裝置軸孔鏜銑半精加工的方法對(duì)其軸孔和端面進(jìn)行精加工;步驟10最終檢查:采用激光檢測(cè)儀配合檢測(cè)箱體裝置各軸孔的形位精度,粗糙度檢測(cè)儀檢測(cè)各軸承孔的表面粗糙度Ra,箱體裝置的幾何尺寸由專業(yè)檢測(cè)人員利用專用測(cè)量工具在機(jī)床上進(jìn)行檢測(cè),檢測(cè)不合格重復(fù)步驟9,檢測(cè)合格后加工完成。本發(fā)明的有益效果是:①由于各分箱體和箱體裝置的半精、精加工所有加工內(nèi)容采用同一機(jī)床,且同一定位基準(zhǔn),加工精度大大提高。②一次裝卡找正后完成了箱體裝置所有軸孔及其端面的精加工,減小了傳統(tǒng)工藝二次調(diào)裝找正誤差和大型工件調(diào)裝變形誤差,加工精度大大提高。③利用精密數(shù)控龍門銑鏜床上垂直銑鏜軸25裝上數(shù)控龍門銑鏜床直角鏜銑裝置24加工超大型齒輪箱箱體裝置軸孔,系統(tǒng)剛性大大優(yōu)于鏜銑床,加工精度高,軸孔表面粗糙度低,達(dá)到Ra1.5,滿足圖紙要求的Ra1.6。④本發(fā)明工序間合理安排去應(yīng)力處理,使各分箱體內(nèi)部組織更加穩(wěn)定,有利于提高加工精度。⑤采用了模擬加工技術(shù)和數(shù)控補(bǔ)償技術(shù),大大提高加工精度。⑥采用最先進(jìn)激光檢測(cè)技術(shù)配合機(jī)床對(duì)加工過程實(shí)時(shí)檢測(cè),提高了加工精度。⑦本發(fā)明各分箱體剖分面、半軸孔及把合聯(lián)接孔均在一機(jī)床組合加工,不但提高了加工精度,而且大大減少了中間轉(zhuǎn)序環(huán)節(jié),再之?dāng)?shù)控機(jī)床的精加工效率大大高于傳統(tǒng)機(jī)床,提高了加工效率。⑧本發(fā)明易操作,銑鏜工即可實(shí)施。⑨本發(fā)明經(jīng)濟(jì)。本發(fā)明粗加工和半精、精加工工序分機(jī)床實(shí)施,充分發(fā)揮粗、精機(jī)床的效能,同時(shí)工序集中,不需要特殊工裝刀具,靠機(jī)床自帶附件即可實(shí)施,且無污染,環(huán)保。⑩本發(fā)明還適應(yīng)于其它空間孔系、高精度、大型零部件的加工。附圖說明圖1是傳統(tǒng)箱體裝置示意圖。圖2是圖1的K向示意圖。圖3是龍門刨床對(duì)箱體剖分面和基準(zhǔn)面A刨削加工示意圖。圖4是龍門銑床對(duì)箱體剖分面和基準(zhǔn)面A銑削加工示意圖。圖5是鏜床對(duì)箱體半軸孔及其端面鏜銑加工示意圖。圖6是鏜床對(duì)箱體裝置軸孔及其端面鏜銑加工示意圖。圖7是圖6中K向示意圖。圖8是本發(fā)明的齒輪箱箱體裝置示意圖。圖9是圖8示意圖中A-A剖視圖。圖10是圖8示意圖中B-B剖視圖。圖11是普通大型鏜銑床對(duì)各分箱體粗加工示意圖。圖12普通大型鏜銑床對(duì)各分箱體粗加工另一狀態(tài)示意圖。圖13是本發(fā)明的下箱體20基準(zhǔn)面B加工示意圖。圖14是本發(fā)明的下箱體20剖分面T、半軸孔(L1、L2)加工示意圖。圖15是本發(fā)明的下中箱體21剖分面S、半軸孔(M1、N1、M2、N2)加工示意圖。圖16是本發(fā)明的下中箱體21剖分面T、半軸孔(L1、L2)加工示意圖。圖17是本發(fā)明的上中箱體22剖分面R、半軸孔(K1、K2)加工示意圖。圖18是本發(fā)明的上中箱體22剖分面S、半軸孔(M1、N1、M2、N2)加工示意圖。圖19是本發(fā)明的上箱體23剖分面P加工示意圖。圖20是本發(fā)明的上箱體23剖分面R、半軸孔(K1、K2)加工示意圖。圖21是本發(fā)明的鉆鏜各單箱體剖分面P(或R、S、T)聯(lián)接把合螺孔示意圖。圖22是本發(fā)明插補(bǔ)加工箱體裝置軸孔及軸孔端面的加工示意圖。圖23是本發(fā)明的箱體裝置軸孔及軸孔端面的加工示意圖。圖24是圖21~22工位1鏜銑一側(cè)軸孔順序示意圖。圖25是圖21~22工位2鏜銑另一側(cè)軸孔順序示意圖。圖示標(biāo)記:1、箱體2、箱蓋3、等高墊鐵4、龍門刨床移動(dòng)工作臺(tái)5、龍門刨床水平刀架(2個(gè))6、龍門刨床立柱7、龍門刨床橫梁8、龍門刨床垂直刀架(2個(gè))9、刨刀10、龍門銑床移動(dòng)工作臺(tái)11、龍門銑床水平銑軸(2個(gè))12、龍門銑床立柱13、龍門銑床橫梁14、龍門銑床垂直銑軸(1個(gè))15、端面盤銑刀16、鏜床工作臺(tái)17、鏜床立柱18、鏜床主軸19、鏜銑刀20、下箱體21、下中箱體22、上中箱體23、上箱體24、數(shù)控龍門銑鏜床直角鏜銑裝置25、數(shù)控龍門銑鏜床銑鏜主軸26、移動(dòng)龍門立柱27、龍門橫梁28、滑枕29、面銑刀30、插補(bǔ)銑刀31、數(shù)控龍門銑鏜床固定式工作臺(tái)32、工藝聯(lián)接件33、鉆鏜孔刀具34、可調(diào)鏜銑刀。具體實(shí)施方式圖中所示,具體實(shí)施方式如下:本發(fā)明的幾何參數(shù)是:本發(fā)明(如圖8~10所示)不同于以往齒輪箱箱體裝置,其由下箱體20、下中箱體21、上中箱體22、上箱體23四層分箱體組成,軸孔成空間分布,軸孔尺寸4-Φ880H7(M1、M2、N1、N2)和4-Φ1090H7(K1、K2、L1、L2),同一軸線方向上軸孔最大跨距3550mm,同一側(cè)軸孔中心距2486.97~2487.22mm,箱體剖分面最大幾何尺寸:長×寬=7000×4150mm。本發(fā)明精度要求:剖分面的形位精度為4~6級(jí),軸孔的形位精度高為3~6級(jí),其具體要求剖分面的平面度公差是0.12mm,剖分面相對(duì)于基準(zhǔn)B的平行度公差是0.08mm,軸孔圓度公差是0.03mm,同一軸線上軸孔同心度公差0.03mm,軸孔軸線相對(duì)于基準(zhǔn)面B的平行度公差0.04mm,軸孔的粗糙度是Ra1.6。本發(fā)明所選用刀具:加工各單箱體剖分面(P、R、S、T)及基準(zhǔn)面B選用刀盤直徑φ200mm面銑刀29,根據(jù)不同加工工步配備粗加工刀片、精刀片和修光刀片;加工軸孔時(shí),根據(jù)不同工步選用不同刀具,粗加工選用刀盤直徑φ200mm插補(bǔ)銑刀30,精加工選用鏜孔直徑尺寸可調(diào)(可調(diào)范圍一種φ800~φ900mm,一種φ1000~φ1100mm)的可調(diào)鏜銑刀34。本發(fā)明是在大型進(jìn)口PT6500AG-S2精密數(shù)控龍門銑鏜床上實(shí)施。結(jié)合圖8~25闡述本發(fā)明如下:依次將箱體裝置圖8組件下箱體20、下中箱體21、上中箱體22、上箱體23吊放于劃線平臺(tái)上,劃線檢查下箱體20、下中箱體21、上中箱體22、上箱體23各加工面余量,并借均各部余量,以下箱體20、下中箱體21、上中箱體22、上箱體23不加工內(nèi)腔為基準(zhǔn)分別劃十字中心對(duì)稱線,劃各剖分面P、R、S、T及基準(zhǔn)面B加工線,劃各軸孔位置中心線及其圓線。先將等高墊鐵3均勻的放置于普通大型鏜銑床固定式工作臺(tái)16上(圖11),找正等高墊鐵3,找正精度不大于0.05mm,將箱體裝置(圖8~10)組件下箱體20剖分面T置放于等高墊鐵3上(圖11),使剖分面T與等高墊鐵3所在平面重合,以下箱體20的不加工內(nèi)腔為基準(zhǔn)所劃十字中心對(duì)稱線找正,保證下箱體的軸孔中心線垂直或平行于箱體內(nèi)腔側(cè)面,要求所述精度不大于0.50mm,滿足所述精度后通過工藝螺栓壓板(圖中未標(biāo)出)將下箱體20固定于普通大型鏜銑床固定式工作臺(tái)16上(圖11),選裝刀盤直徑φ200mm面銑刀29,根據(jù)圖紙參數(shù)和選取的大切削參數(shù),啟動(dòng)機(jī)床,多次調(diào)裝(定位基面不變),由圖11工位1粗加工下箱體20基準(zhǔn)面B,按工藝規(guī)范留取余量。重新調(diào)裝工件,下箱體20已加工基準(zhǔn)面B置于等高墊鐵3上(圖12),已加工基準(zhǔn)面B與等高墊鐵3所在平面緊密重合,不重合精度不大于0.05mm(0.05mm塞尺檢查不入),找正下箱體20十字中心對(duì)稱線,找正精度不大于0.5mm,保證下箱體的軸孔中心線垂直或平行于箱體內(nèi)腔側(cè)面,滿足找正精度后通過工藝螺栓壓板(圖中未標(biāo)出)將下箱體20固定于普通大型鏜銑床固定式工作臺(tái)16上(圖12),同前所述由圖12工位1粗加工下箱體20剖分面T;工件同工位,重新調(diào)整機(jī)床,拆去刀盤直徑φ200mm面銑刀29,換裝可調(diào)鏜銑刀34,根據(jù)圖紙參數(shù)和選取的大切削參數(shù),啟動(dòng)機(jī)床,由圖12工位2粗加工一側(cè)半軸孔(L2),按工藝規(guī)范留取余量;重新調(diào)裝工件,同上所述由圖12工位2粗加工另一側(cè)半軸孔(L1)。同上所述,如圖11、圖12換裝下中箱體21粗加工各剖分面(T、S)、半軸孔(L1、L2、M1、M2、N1、N2);再換裝上中箱體22粗加工各剖分面(S、R)、半軸孔(M1、M2、N1、N2、K1、K2);再換裝上箱體23粗加工各剖分面(R、P)、半軸孔(K1、K2)。注:本實(shí)例各分箱體單獨(dú)粗加工半軸孔時(shí),軸孔端面暫不加工,待組成箱體裝置后加工。對(duì)下箱體20、下中箱體21、上中箱體22、上箱體23各分箱體進(jìn)行人工去應(yīng)力時(shí)效處理,以釋放毛坯殘余應(yīng)力和粗加工應(yīng)力,使各分箱體內(nèi)部組織趨于穩(wěn)定。在劃線平臺(tái)上劃線檢查下箱體20、下中箱體21、上中箱體22、上箱體23各分箱體變形量,借均各部余量。以不加工內(nèi)腔為基準(zhǔn)分別劃下箱體20、下中箱體21、上中箱體22、上箱體23十字中心對(duì)稱線并引至側(cè)面打印,劃各分箱體剖分面P、R、S、T及基準(zhǔn)面B加工線,劃各軸孔中心位置線及其圓線并打印。將12件等高墊鐵3均勻的置放于大型進(jìn)口PT6500AG-S2精密數(shù)控龍門銑鏜床固定式工作臺(tái)31上(圖13~20),并進(jìn)行等高度銑削加工,使12件等高墊鐵3的相對(duì)高度保持在與數(shù)控龍門銑鏜床銑鏜主軸25回轉(zhuǎn)中心相垂直的同一平面內(nèi),12件等高墊鐵作為各分箱體及箱體裝置的加工基準(zhǔn),使加工基準(zhǔn)保持一致;再將下箱體20的剖分面T置放于等高墊鐵3上(圖13),找正基準(zhǔn)面B加工線、找正下箱體20十字中心對(duì)稱線,要求所述找正精度不大于0.50mm,滿足所述精度后通過工藝螺栓壓板(圖中未畫出)將下箱體20固定于大型進(jìn)口PT6500AG-S2精密數(shù)控龍門銑鏜床固定式工作臺(tái)31上(圖13);將刀盤直徑φ200mm面銑刀29裝于數(shù)控龍門銑鏜床銑鏜主軸25上,將圖紙參數(shù)和切削參數(shù)輸入程序,由圖13工位3半精銑、精銑下箱體20基準(zhǔn)面B;調(diào)裝,下箱體20已加工基準(zhǔn)面B置于12件等高墊鐵3上(圖14),使基準(zhǔn)面B與等高墊鐵3所在平面緊密重合,要求所述不重合精度不大于0.050mm(即0.05mm塞尺檢查不入),滿足所述精度后通過工藝螺栓壓板(圖中未畫出)將下箱體20固定于大型進(jìn)口PT6500AG-S2精密數(shù)控龍門銑鏜床固定式工作臺(tái)31上(圖14),由圖14工位3半精銑、精銑下箱體20剖分面T。要求:上述半精銑剖分面過程中,為滿足精加工圖紙精度要求,模擬加工選擇最佳精銑切削參數(shù)(精加工的切削參數(shù)選取很關(guān)鍵,直接影響加工精度);精銑剖分面時(shí),按半精銑模擬加工選取的最佳精銑切削參數(shù)實(shí)施;半精銑完成后,重新調(diào)整機(jī)床,拆去刀盤外圓直徑φ200mm面銑刀29,換裝數(shù)控龍門銑鏜床直角鏜銑裝置24和插補(bǔ)銑刀30,輸入圖紙參數(shù)和切削參數(shù),按插補(bǔ)程序由圖14工位1、2半精加工半軸孔(L1、L2),按工藝規(guī)范留余量;去應(yīng)力自然時(shí)效后再按本工步前述對(duì)下箱體20基準(zhǔn)面B和剖分面T進(jìn)行精加工。精銑完成后,劃線配合,以下箱體20的不加工內(nèi)腔為基準(zhǔn)劃十字中心對(duì)稱線,并引至側(cè)面打印,劃下箱體20剖分面T把合聯(lián)接孔位置線;按線找正,找正精度不大于0.50mm,拆去刀盤外圓直徑φ200mm面銑刀29,換裝鉆鏜孔刀具33,開坐標(biāo)保證孔距,鉆鏜剖分面T上把合聯(lián)接孔(圖21)。同理依次如圖15~16半精銑、精銑下中箱體21的各剖分面(T、S),半精加工各半軸孔,鉆鏜剖分面把合聯(lián)接孔(圖21);如圖17~18半精銑、精銑上中箱體22的各剖分面(S、R),半精加工各半軸孔,鉆鏜剖分面把合聯(lián)接孔(圖21);如圖19~20半精銑、精銑上箱體23的各剖分面(R、P),半精加工各半軸孔,鉆鏜剖分面把合聯(lián)接孔(圖21)。重新找正均勻布置于大型進(jìn)口PT6500AG-S2精密數(shù)控龍門銑鏜床固定式工作臺(tái)31上12件等高墊鐵3(圖22~23),所述找正精度不大于0.05mm,滿足所述精度后,將下箱體20的基準(zhǔn)面B置于等高墊鐵3上,使基準(zhǔn)面B與等高墊鐵3所在平面緊密重合,不重合精度不大于0.05mm(0.05mm塞尺檢查不入)。鉗工配合,鉗工根據(jù)機(jī)體裝置結(jié)構(gòu)示意圖8~10的組裝配合順序,依次將下中箱體21、上中箱體22、上箱體23相配剖分面(T、S、R)相對(duì)疊加,各剖分面緊密貼合,各分箱體剖分面在聯(lián)接件32未把緊狀態(tài)下用0.05mm的塞尺檢查不入,各分箱體十字中心對(duì)稱線對(duì)齊,兼顧不加工內(nèi)腔側(cè)面和外形對(duì)正,而后用工藝聯(lián)接件32把緊組裝成箱體裝置(圖8~10)。劃線配合,以箱體裝置十字中心對(duì)稱線為基準(zhǔn),劃各軸孔中心位置線及其圓線。按線找正,要求所述找正精度不大于0.50mm,滿足所述精度后通過工藝螺栓壓板(圖中未畫出)將箱體裝置固定于大型進(jìn)口PT6500AG-S2精密數(shù)控龍門銑鏜床固定式工作臺(tái)31上(圖22~23)。調(diào)整機(jī)床,將數(shù)控龍門銑鏜床直角鏜銑裝置24裝于數(shù)控龍門銑鏜床銑鏜主軸25上,插補(bǔ)銑刀30裝于數(shù)控龍門銑鏜床直角鏜銑裝置24上,編制插補(bǔ)程序,輸入圖紙參數(shù),合理選取切削參數(shù)后調(diào)試程序,合格后啟動(dòng)機(jī)床由圖22工位1、2實(shí)施軸孔及軸孔端面的半精加工(圖22),按工藝規(guī)范留余量;重新調(diào)整機(jī)床,拆掉插補(bǔ)銑刀30,將可調(diào)鏜銑刀34裝于數(shù)控龍門銑鏜床直角鏜銑裝置24上(圖23),重新編制程序并調(diào)試程序,程序調(diào)試合格后啟動(dòng)機(jī)床由圖23工位1、2實(shí)施軸孔及軸孔端面的半精加工,同時(shí)在半精加工過程中通過模擬加工選取滿足圖紙精度的最佳精加工切削參數(shù),按工藝規(guī)范留余量;激光跟蹤儀配合機(jī)床檢測(cè)形位精度,根據(jù)檢測(cè)結(jié)果微調(diào)程序,且根據(jù)半精加工模擬選擇最佳精加工切削參數(shù),由圖23工位1、2實(shí)施軸孔及軸孔端面精加工。軸孔加工順序示意圖24~25。具體包括如下步驟:步驟1劃線。上劃線平臺(tái),劃線檢查箱體裝置(圖8~10)中下箱體20、下中箱體21、上中箱體22、上箱體23各分箱體的毛坯余量,借均各部余量。以不加工箱體內(nèi)腔為基準(zhǔn)劃:下箱體20十字中心對(duì)稱線及剖分面T、基準(zhǔn)面B加工線,各半軸孔(L1、L2)中心位置線及其圓線;下中箱體21十字中心對(duì)中線及剖分面T、S加工線,各半軸孔(L1、L2,M1、M2,N1、N2)中心位置線及其圓線;上中箱體22十字中心對(duì)中線及剖分面S、R加工線、各半軸孔(M1、M2,N1、N2,K1、K2)中心位置線及其圓線;上箱體23十字中心對(duì)中線及剖分面R、P加工線、各半軸孔(K1、K2)中心位置線和半軸孔圓線。步驟2各分箱體剖分面及半軸孔的粗加工。將等高墊鐵3均勻分布于普通大型鏜銑床固定式工作臺(tái)16上(圖11),將步驟1所得下箱體20的剖分面T放于等高墊鐵3上,保證剖分面與等高墊鐵3平面重合,按步驟1所劃線找正,找正精度不大于0.5mm,滿足所述精度要求后用工藝螺栓壓板(圖中未畫出)將下箱體20固定于普通大型鏜銑床固定式工作臺(tái)16上(圖11),調(diào)整機(jī)床,選裝外圓直徑φ200mm面銑刀29,根據(jù)圖紙參數(shù)和選取的大切削參數(shù)(粗加工主要是去除毛坯余量,不需保證圖紙精度,本發(fā)明所選面銑刀29切削參數(shù)按通用技術(shù)選取,即大切深、大進(jìn)給、低轉(zhuǎn)速),啟動(dòng)機(jī)床,由圖11工位1多次調(diào)裝對(duì)下箱體20基準(zhǔn)面B進(jìn)行粗加工,按工藝規(guī)范單面留取余量10mm,注:由于基準(zhǔn)面B或剖分面(T、S、R、P)屬超大平面,每一超大平面在定位基準(zhǔn)不變的情況下,需多次調(diào)裝才能完成粗加工;重新調(diào)裝下箱體20,下箱體20已加工基準(zhǔn)面B置于等高墊鐵3上(圖12),已加工基準(zhǔn)面B與等高墊鐵3緊密重合,不重合精度不大于0.05mm(0.05mm塞尺檢查不入),找正十字中心對(duì)稱線,找正精度不大于0.5mm,滿足所述精度后用工藝螺栓壓板(圖中未畫出)將下箱體20固定于普通大型鏜銑床固定式工作臺(tái)16上(圖12),啟動(dòng)機(jī)床同前所述由圖12工位1對(duì)下箱體20剖分面T進(jìn)行粗加工,按工藝規(guī)范單面留取余量10mm。工件同工位,重新調(diào)整機(jī)床,拆去外圓直徑φ200mm面銑刀29,換裝可調(diào)鏜銑刀34,機(jī)床調(diào)整至圖12工位2,按線找正半軸孔L2,找正精度不大于0.5mm,根據(jù)圖紙參數(shù)及所選取切削參數(shù)(粗加工主要是切除毛坯余量,不需保證圖紙精度,本發(fā)明所選可調(diào)鏜銑刀34切削參數(shù)按通用技術(shù)選取,即大切深、大進(jìn)給、低轉(zhuǎn)速),啟動(dòng)機(jī)床,由圖12工位2對(duì)下箱體20半軸孔(L2)進(jìn)行粗加工,按工藝規(guī)范直徑留取余量25mm;重新調(diào)裝下箱體20,下箱體20的半軸孔(L1)對(duì)鏜軸,同上所述由圖12工位2對(duì)下箱體20半軸孔(L1)進(jìn)行粗加工。同上所述如圖14、圖12依次調(diào)換對(duì)下中箱體21剖分面(T、S)、半軸孔(L2、L1、M2、M1、N2、N1)進(jìn)行粗加工,對(duì)上中箱體22剖分面(S、R)、半軸孔(M2、M1、N2、N1、K2、K1)進(jìn)行粗加工,對(duì)上箱體23剖分面(R、P)、半軸孔(K2、K1)進(jìn)行粗加工。注:工藝要求軸孔端面暫不加工(本發(fā)明中軸孔端面為劃平止口,箱體裝置軸孔外測(cè)面圖紙要求不加工)。步驟3人工時(shí)效。將步驟2所得各分箱體進(jìn)行人工時(shí)效,最大限度的釋放毛坯殘余應(yīng)力和粗加工應(yīng)力,使各分箱體內(nèi)部組織趨于穩(wěn)定,從而保證各分箱體結(jié)構(gòu)穩(wěn)定,為提高精加工精度奠定基礎(chǔ)。步驟4劃線。上劃線平臺(tái),劃線檢查步驟3所得下箱體20、下中箱體21、上中箱體22、上箱體23變形量,借均各部余量,且保證各加工尺寸,劃下箱體20剖分面T和基準(zhǔn)面B加工線,劃下中箱體21剖分面T、S加工線,劃上中箱體22剖分面S、R加工線,上箱體23剖分面R、P加工線;以各分箱體不加工內(nèi)腔為基準(zhǔn)劃:下箱體20十字中心對(duì)稱線,各半軸孔(L1、L2)中心位置線及其圓線;下中箱體21十字中心對(duì)稱線,各半軸孔(L1、L2,M1、M2,N1、N2)中心位置線及其圓線;上中箱體22十字中心對(duì)中線,各半軸孔(M1、M2,N1、N2,K1、K2)中心位置線及其圓線;上箱體23十字中心對(duì)稱線,各半軸孔(K1、K2)中心位置線及其圓線。要求各單箱體十字中心對(duì)稱線引至側(cè)面并打印。步驟5各分箱體剖分面及半軸孔的半精加工。將12件等高墊鐵3均勻分布于大型進(jìn)口PT6500AG-S2精密數(shù)控龍門銑鏜床固定式工作臺(tái)31上(圖13~20),將下箱體20的剖分面T放于等高墊鐵3上,保證剖分面T與等高墊鐵3平面重合,按步驟4所劃線找正,找正精度不大于0.5mm,滿足所述找正精度后用工藝螺栓壓板(圖中未畫出)將下箱體20固定于大型進(jìn)口PT6500AG-S2精密數(shù)控龍門銑鏜床固定式工作臺(tái)31上(圖13),調(diào)整機(jī)床,選用外圓直徑φ200mm面銑刀29裝于數(shù)控龍門銑鏜床銑鏜主軸25上,編制程序,將圖紙參數(shù)和選取的切削參數(shù)(注:半精加工主要還是去除毛坯余量,不需保證圖紙精度,本發(fā)明面銑刀29切削參數(shù)是轉(zhuǎn)速200r/min、切削深度3~3.5mm、直線進(jìn)給速度1000mm/min)輸入程序,調(diào)試程序合格后啟動(dòng)機(jī)床,由圖13工位3通過移動(dòng)龍門立柱26的縱向移動(dòng)(X軸)、滑枕28沿龍門橫梁27橫向移動(dòng)(Y軸)和數(shù)控龍門銑鏜床銑鏜主軸25上下運(yùn)動(dòng)(Z軸)及其旋轉(zhuǎn)運(yùn)動(dòng)(C軸)對(duì)下箱體20基準(zhǔn)面B進(jìn)行半精加,此時(shí)留取精加工余量1mm;調(diào)裝,下箱體20已加工基準(zhǔn)面B置于12個(gè)等高墊鐵3上,基準(zhǔn)面B與等高墊鐵3緊密重合,不重合精度不大于0.05mm(0.05mm塞尺檢查不入),按步驟4所劃十字中心對(duì)稱線找正,找正精度不大于0.5mm,滿足找正精度后用工藝螺栓壓板(圖中未畫出)將下箱體20固定于PT6500AG-S2精密數(shù)控龍門銑鏜床固定式工作臺(tái)31上(圖14),調(diào)整機(jī)床后同前所述對(duì)下箱體20剖分面T進(jìn)行半精加工留取精加工余量1mm;注:工藝要求,半精加工各分箱體剖分面(T、S、R、P)及下箱體20基準(zhǔn)面B時(shí),根據(jù)程序進(jìn)行模擬加工,以選取滿足圖紙精度要求的最佳精加工切削參數(shù)(精加工需保證圖紙精度,切削參數(shù)選取很關(guān)鍵,直接影響加工精度,本發(fā)明經(jīng)模擬加工所選精加工剖分面(T、S、R、P)及基準(zhǔn)面B最佳面銑刀29切削參數(shù)是轉(zhuǎn)速300r/min、切削深度0.15mm、直線進(jìn)給速度500mm/min)。工件同工位,重新調(diào)整機(jī)床,拆去外圓直徑φ200mm面銑刀29,換裝數(shù)控龍門銑鏜床直角鏜銑裝置24和外圓直徑φ200mm插補(bǔ)鏜銑刀30,滑枕28移位至圖14工位1,按線找正半軸孔L2,找正精度不大于0.5mm,將圖紙參數(shù)及所選取切削參數(shù)(半精加工主要是切除毛坯余量。本發(fā)明所選插補(bǔ)銑刀30切削參數(shù)是轉(zhuǎn)速200r/min、切削深度6mm、圓周進(jìn)給速度1000mm/min,步長5mm)輸入程序,調(diào)試程序合格后啟動(dòng)機(jī)床,通過大型進(jìn)口PT6500AG-S2精密數(shù)控龍門銑鏜床直角鏜銑裝置24鏜銑軸C1旋轉(zhuǎn)運(yùn)動(dòng),滑枕28沿龍門橫梁27橫向運(yùn)動(dòng)Y和鏜銑軸C1中心繞半軸孔L2中心圓周運(yùn)動(dòng),由圖14工位1利用插補(bǔ)程序?qū)ο孪潴w20半軸孔L2進(jìn)行半精加工,按工藝規(guī)范直徑留取余量13mm;通過滑枕28沿龍門橫梁27橫向運(yùn)動(dòng)Y,重新調(diào)整刀位至圖14工位2,同前所述由圖14工位2利用插補(bǔ)程序?qū)ο孪潴w20半軸孔L1進(jìn)行粗加工,按工藝規(guī)范直徑留取余量13mm。同上所述(如圖15~16)對(duì)下中箱體21剖分面(T、S)、半軸孔(L2、L1、M2、M1、N2、N1)進(jìn)行半精加工,(如圖17~18)對(duì)上中箱體22剖分面(S、R)、半軸孔(M2、M1、N2、N1、K2、K1)進(jìn)行半精加工,(如圖19~20)對(duì)上箱體23剖分面(R、P)、半軸孔(K2、K1)進(jìn)行半精加工;注:工藝要求,軸孔端面暫不加工(本發(fā)明中軸孔端面為劃平止口,箱體裝置軸孔外端面圖紙不要求加工)。步驟6自然時(shí)效。將步驟5所得各分箱體進(jìn)行自然時(shí)效,以充分釋放毛坯殘余應(yīng)力、熱處理應(yīng)力及加工應(yīng)力,保證各分箱體結(jié)構(gòu)穩(wěn)定性,為保證精加工精度奠定良好基礎(chǔ)。步驟7各分箱體剖分面精加工。將12件等高墊鐵3均勻分布于大型進(jìn)口PT6500AG-S2精密數(shù)控龍門銑鏜床固定式工作臺(tái)31上(圖13~20),銑12個(gè)等高墊鐵3上端面,使12件等高墊鐵3的上端面處于同一平面內(nèi)且與數(shù)控龍門銑鏜床銑鏜軸25回轉(zhuǎn)中心垂直,所述精度為不大于0.05mm,將下箱體20的剖分面T放于等高墊鐵3上,保證剖分面T與等高墊鐵3平面重合(如圖13),按步驟4所劃十字中心對(duì)稱線找正,找正精度不大于0.5mm,滿足所述找正精度后用工藝螺栓壓板(圖中未畫出)將下箱體20固定于大型進(jìn)口PT6500AG-S2精密數(shù)控龍門銑鏜床固定式工作臺(tái)31上(圖13),調(diào)整機(jī)床,選用外圓直徑φ200mm面銑刀29裝于數(shù)控龍門銑鏜床銑鏜主軸25上,輸入圖紙參數(shù)和半精加工過程中模擬加工選取的最佳精加工切削參數(shù)(本發(fā)明經(jīng)模擬加工所選面銑刀29最佳精加工切削參數(shù)是轉(zhuǎn)速300r/min、切削深度0.15mm、直線進(jìn)給速度500mm/min),編制程序,調(diào)試程序合格后啟動(dòng)機(jī)床,由圖13工位3通過移動(dòng)龍門立柱26的縱向移動(dòng)(X軸)、滑枕28沿龍門橫梁27橫向移動(dòng)(Y軸)和數(shù)控龍門銑鏜床銑鏜主軸25上下運(yùn)動(dòng)(Z軸)及其旋轉(zhuǎn)運(yùn)動(dòng)(C軸)對(duì)下箱體20基準(zhǔn)面B進(jìn)行精加工。調(diào)裝,下箱體20已加工基準(zhǔn)面B置于12件等高墊鐵3上,基準(zhǔn)面B與等高墊鐵3緊密重合(如圖14),不重合精度不大于0.05mm(0.05mm塞尺檢查不入),按步驟4所劃十字中心對(duì)中線找正,找正精度不大于0.5mm,滿足找正精度后用工藝螺栓壓板(圖中未畫出)將下箱體20固定于大型進(jìn)口PT6500AG-S2精密數(shù)控龍門銑鏜床固定式工作臺(tái)31上(圖14),調(diào)整機(jī)床后同前所述對(duì)下箱體20剖分面T進(jìn)行精加工。劃線工配合,以下箱體20不加工內(nèi)腔為基準(zhǔn)劃十字中心對(duì)稱線、并引至側(cè)面打印,以此為基準(zhǔn)劃剖分面T上把合聯(lián)接孔位置線。調(diào)整機(jī)床,拆去外圓直徑φ200mm面銑刀29,換裝鉆鏜孔刀具33,開坐標(biāo)保證孔距,鉆鏜剖分面T上把合聯(lián)接孔(圖21)。同上下箱體20所述,對(duì)下中箱體21的剖分面(T、S)進(jìn)行精加工(圖15~16)及其把合聯(lián)接孔加工(圖21);對(duì)上中箱體22的剖分面(S、R)進(jìn)行精加工(圖17~18)及其把合聯(lián)接孔加工(圖21);對(duì)上箱體23的剖分面(R、P)進(jìn)行精加工(圖19~20)及其把合聯(lián)接孔加工(圖21)。注:半軸孔及其端面暫不加工,待組裝把合成箱體裝置后進(jìn)行精加工。步驟8箱體裝置(圖8~10)組裝。鉗工領(lǐng)取下箱體20、下中箱體21、上中箱體22、上箱體23和工藝聯(lián)接件32,將各件去除毛刺,清理干凈。與步驟9配合,12件等高墊鐵3均布放置于大型進(jìn)口PT6500AG-S2精密數(shù)控龍門銑鏜床固定式工作臺(tái)31上(圖22),12件等高墊鐵找正精度不大于0.05mm,將下箱體20的B基準(zhǔn)面置于等高墊鐵3上,B基準(zhǔn)面與等高墊鐵3緊密重合,不重合精度不大于0.05mm(0.05mm塞尺檢查不入),按示意圖8~10依次將下中箱體21相配剖分面T相對(duì)疊加于下箱體20上,各分箱體十字中心對(duì)稱線對(duì)齊,把合聯(lián)接孔對(duì)正,兼顧內(nèi)腔、外形對(duì)正,再將上中箱體22相配剖分面S相對(duì)疊加于下中箱體21上,各分箱體十字中心對(duì)稱線對(duì)齊,把合聯(lián)接孔對(duì)正,兼顧內(nèi)腔、外形對(duì)正,再將上箱體23相配剖分面R相對(duì)疊加于上中箱體22上,各分箱體十字中心對(duì)稱線對(duì)齊,把合聯(lián)接孔對(duì)正,兼顧內(nèi)腔、外形對(duì)正,穿入工藝聯(lián)接件32把緊組裝成箱體裝置(圖8~10)。要求:各分箱體相對(duì)剖分面(R、S、T)緊密貼合,在工藝聯(lián)接件32未把緊狀態(tài)下0.05mm塞尺檢查不入。劃線配合,以十字中心對(duì)稱線為基準(zhǔn)劃各軸孔位置線及軸孔圓線。步驟9箱體裝置軸孔精加工。步驟8所得箱體裝置(圖8~10)的軸孔精加工與步驟8配合,結(jié)合示意圖22~25進(jìn)行敘述:①配合步驟8找正。12件等高墊鐵3均布放置于大型進(jìn)口PT6500AG-S2精密數(shù)控龍門銑鏜床固定式工作臺(tái)31上(圖22~23),銑平12件等高墊鐵3上端面,使12件等高墊鐵3的上端面處于同一平面內(nèi)且與數(shù)控龍門銑鏜床銑鏜主軸25回轉(zhuǎn)中心垂直,所述精度為不大于0.05mm;將步驟8所得箱體裝置(圖8~10)的下箱體20的B基準(zhǔn)面置放于等高墊鐵3上,使B基準(zhǔn)面與等高墊鐵3所在平面緊密貼合,所述精度不大于0.05mm(0.05mm塞尺檢查不入);按箱體裝置十字中心對(duì)稱線找正,以保證軸孔中心線與箱體內(nèi)腔壁垂直或平行,同時(shí)保證軸孔處壁厚均勻,找正精度不大于0.5mm;將大型進(jìn)口PT6500AG-S2精密數(shù)控龍門銑鏜床滑枕28依次橫向移動(dòng)到圖22~23工位1、2,按所劃各軸孔位置線及圓線找正各軸孔圓心,保證水平各軸孔中心在剖分平面內(nèi)、垂直各軸孔中心在垂直于剖分面的平面內(nèi),找正精度不大于0.3mm;滿足所述精度后用工藝螺栓壓板(圖中未畫出)將箱體裝置固定于大型進(jìn)口PT6500AG-S2精密數(shù)控龍門銑鏜床固定式工作臺(tái)31上(圖22~23),復(fù)查所述精度并滿足所述精度要求。②編制數(shù)控程序,將箱體裝置的軸孔圖紙參數(shù)和所選擇的切削參數(shù)輸入程序中,按③~⑦所述要求分別調(diào)試程序,實(shí)施加工。③將數(shù)控龍門銑鏜床直角鏜銑裝置24裝于大型進(jìn)口PT6500AG-S2精密數(shù)控龍門銑鏜床銑鏜主軸25上,且移到圖22工位1初始位置即其中一軸孔中心(如圖22中K2孔中心),再將外圓直徑φ200mm插補(bǔ)銑刀30裝于數(shù)控龍門銑鏜床直角鏜銑裝置24上,啟動(dòng)機(jī)床和程序,通過數(shù)控龍門銑鏜床直角鏜銑裝置24旋轉(zhuǎn)運(yùn)動(dòng)C1及其繞軸孔中心圓周運(yùn)動(dòng)和滑枕28沿龍門橫梁27水平橫向運(yùn)動(dòng)Y,按插補(bǔ)程序半精加工一側(cè)K2軸孔及其端面,按工藝規(guī)范各加工面單面均留余量1.5mm,注:本工步所選插補(bǔ)銑刀30切削參數(shù)為轉(zhuǎn)速200r/min,切削深度5mm,圓周進(jìn)給速度1000mm/min,步長5mm。再通過大型進(jìn)口PT6500AG-S2精密數(shù)控龍門銑鏜床的移動(dòng)龍門立柱26的縱向運(yùn)動(dòng)X,數(shù)控龍門銑鏜床銑鏜主軸25上下運(yùn)動(dòng)Z,按程序保證孔距,同加工K2孔原理加工同側(cè)M2軸孔及其端面。再通過大型進(jìn)口PT6500AG-S2精密數(shù)控龍門銑鏜床的移動(dòng)龍門立柱26的縱向運(yùn)動(dòng)X,按程序保證孔距,同加工K2孔原理加工同側(cè)N2軸孔及其端面。再通過PT6500AG-S2精密數(shù)控龍門銑鏜床的移動(dòng)龍門立柱26的縱向運(yùn)動(dòng)X,數(shù)控龍門銑鏜床銑鏜主軸25上下運(yùn)動(dòng)Z,按程序保證孔距,同加工K2孔原理加工同側(cè)L2軸孔及其端面,再通過PT6500AG-S2數(shù)控龍門銑鏜床銑鏜主軸25上下運(yùn)動(dòng)Z回到原位K2軸孔。工位1加工軸孔順序圖24。本發(fā)明插補(bǔ)半精加工軸孔過程是插補(bǔ)銑刀30以200r/min旋轉(zhuǎn),同時(shí)根據(jù)插補(bǔ)程序計(jì)算的坐標(biāo)點(diǎn)(x,z)繞軸孔中心以1000mm/min圓周進(jìn)給速度回轉(zhuǎn)一周后,插補(bǔ)銑刀30返回切入位置,而后插補(bǔ)銑刀30沿軸孔軸向方向進(jìn)給一個(gè)步長5mm,重復(fù)上一插補(bǔ)過程,直至完成軸孔插補(bǔ)加工。④工件同工位,將大型進(jìn)口PT6500AG-S2精密數(shù)控龍門銑鏜床滑枕28橫向移動(dòng)Y到工位2(圖22),同③所述插補(bǔ)粗加工另一側(cè)各軸孔(K1、M1、N1、L1)及其端面。工位2加工軸孔順序圖25。注:待③~④各軸孔插補(bǔ)半精加工完成后在箱體裝置一端上、下中箱體結(jié)合面處全長銑一精加工找正工藝基準(zhǔn),粗糙度Ra3.2。半精加工后松壓板,充分釋放加工應(yīng)力,待工件冷至室溫后重新找正。⑤箱體裝置軸孔鏜銑半精加工。按①所述找正要求找正,同時(shí)將①按十字中心對(duì)稱線找正替換成按③~④工步所銑上、下中箱體結(jié)合面處工藝找正基準(zhǔn)找正,找正精度不大于0.05mm,而后重新將箱體裝置用工藝螺栓壓板(圖中未畫出)固定于大型進(jìn)口PT6500AG-S2精密數(shù)控龍門銑鏜床固定式工作臺(tái)31上(圖23),調(diào)整機(jī)床,將調(diào)整范圍φ800~φ900mm或φ1000~φ1100mm可調(diào)鏜銑刀34裝于數(shù)控龍門銑鏜床直角鏜銑裝置24上,選取不同切削參數(shù)(C1軸轉(zhuǎn)速、切削深度、Y軸進(jìn)給速度),按③~④所述加工順序模擬加工各軸孔,各軸孔直徑留取精加工余量0.6mm;通過多次模擬加工選取滿足圖紙精度要求的最佳精鏜孔切削參數(shù)。本發(fā)明模擬所選最佳精鏜軸孔切削參數(shù)為可調(diào)鏜銑刀34轉(zhuǎn)速為25~30r/min、橫向進(jìn)給0.1mm/r、切削深度0.25mm。注:加工φ880H7(M1、M2、N1、N2)軸孔采用調(diào)整范圍φ800~φ900mm可調(diào)鏜銑刀34,加工φ1090H7(K1、K2、L1、L2)軸孔采用調(diào)整范圍φ1000~φ1100mm可調(diào)鏜銑刀34。⑥激光跟蹤儀配合機(jī)床檢測(cè)形位精度(略)。⑦箱體裝置軸孔精加工。將可調(diào)鏜銑刀34復(fù)位到初始孔位,校正軸孔圓心,所述精度不大于0.02mm,根據(jù)⑥檢測(cè)結(jié)果,微調(diào)程序,按模擬加工選取的最佳切削參數(shù),按⑤所述實(shí)施軸孔及其端面精加工。步驟10最終檢查。激光檢測(cè)儀配合檢測(cè)箱體裝置各軸孔的形位精度,粗糙度檢測(cè)儀檢測(cè)各軸承孔的表面粗糙度Ra,箱體裝置的幾何尺寸由專業(yè)檢測(cè)人員利用專用測(cè)量工具和大型進(jìn)口PT6500AG-S2精密數(shù)控龍門銑鏜床配合檢測(cè)。注:圖8中垂直方向上的上軸孔標(biāo)記K1-K2、下軸孔標(biāo)記L1-L2,水平方向上的左軸孔標(biāo)記M1-M2、右軸孔標(biāo)記N1-N2。箱體裝置同一側(cè)軸承孔標(biāo)記K1、L1、M1、N1,一側(cè)軸承孔標(biāo)記K2、L2、M2、N2注:激光檢測(cè)儀配合檢查屬檢測(cè)技術(shù)領(lǐng)域。示意圖中固定用工藝螺栓壓板未畫出。上述所述12件等高墊鐵3的作用主要是加工各分箱體及箱體裝置加工基準(zhǔn),保證加工基準(zhǔn)同一。箱體裝置設(shè)計(jì)基準(zhǔn)B置于12件等高墊鐵3上,使加工基準(zhǔn)與設(shè)計(jì)基準(zhǔn)及裝配基準(zhǔn)重合,保證加工基準(zhǔn)與設(shè)計(jì)、裝配基準(zhǔn)統(tǒng)一,提高加工裝配精度。本發(fā)明實(shí)施效果:精度檢測(cè)記錄見上表,各項(xiàng)檢測(cè)結(jié)果均達(dá)到或超過圖紙要求。與傳統(tǒng)加工方法比較:1、提高加工精度。本發(fā)明全部半精、精加工內(nèi)容采用同一機(jī)床,且機(jī)床精度高;同一定位基準(zhǔn)(等高墊鐵3),且工藝基準(zhǔn)與設(shè)計(jì)基準(zhǔn)統(tǒng)一;一次裝卡完成箱體裝置軸孔及其軸孔端面的加工,減小了傳統(tǒng)加工二次調(diào)裝找正誤差和大型工件調(diào)裝變形誤差,大大提高了加工精度,其形位精度達(dá)到了4級(jí),表面粗糙度達(dá)到Ra1.5,相對(duì)于傳統(tǒng)加工方法采取分工序選用不同加工機(jī)床加工(形位精度一般為7級(jí)、加工面粗糙度大于等于Ra3.2),形位精度提高2~3等級(jí),表面粗糙度提高1~2等級(jí),同時(shí)箱體裝置的幾何精度使用本發(fā)明的加工方法得到了大幅度提高,幾何精度達(dá)到6級(jí),經(jīng)過裝配試車,整機(jī)的震動(dòng)和噪音降低,整機(jī)性能得到提高。2、提高效率。本發(fā)明同一機(jī)床完成,減少了許多轉(zhuǎn)序、調(diào)裝和找正時(shí)間;同時(shí)由于提高了加工精度,大大減少了整機(jī)裝配的調(diào)整和返修時(shí)間。同時(shí)粗加工、精加工合理選用不同精度機(jī)床,充分發(fā)揮粗、精機(jī)床的效能,既保證了加工質(zhì)量,又提高了效率,且也保護(hù)了精密機(jī)床的精度。3、本發(fā)明的加工方法不僅適用于大型、超大型齒輪箱箱體裝置的加工,還可適用于其它空間分布的多孔系、高精度、超大型零部件的加工。