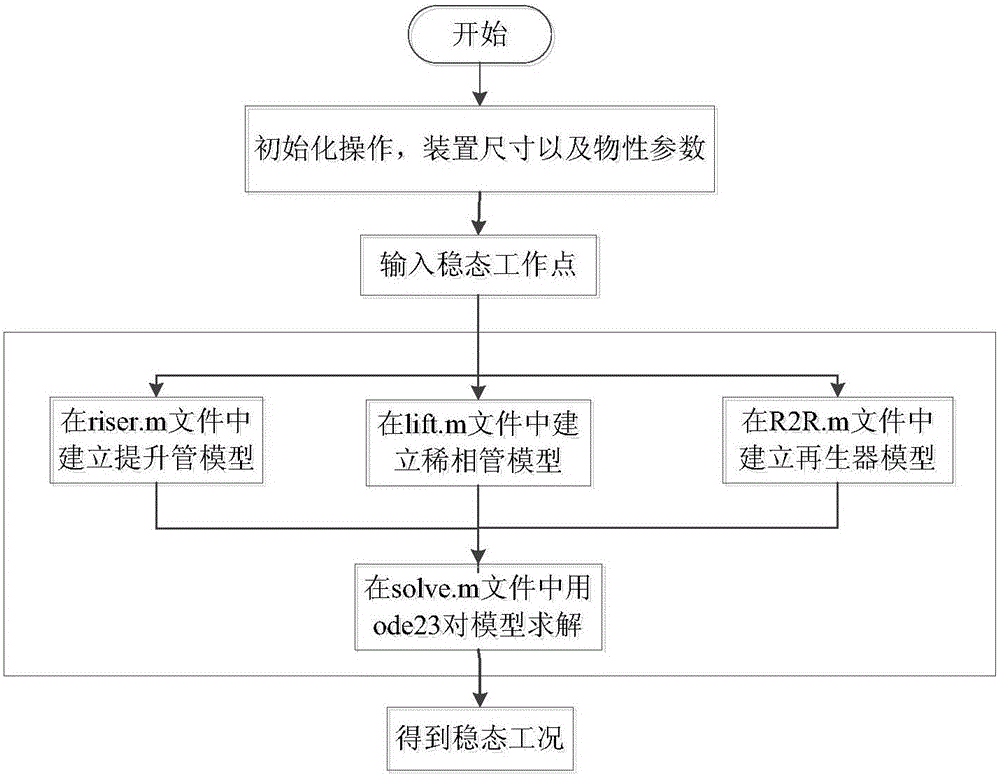
本發(fā)明涉及工業(yè)過程監(jiān)控領(lǐng)域,具體涉及一種雙段式催化裂化反再系統(tǒng)故障動態(tài)模擬方法及系統(tǒng)。
背景技術(shù):
:隨著經(jīng)濟發(fā)展,石化產(chǎn)品需求與日俱增,煉油工業(yè)發(fā)展十分迅速。催化裂化日益成為石油深度加工的重要手段,在煉油工業(yè)中占有舉足輕重的地位。在我國,催化裂化裝置生產(chǎn)的汽油和柴油組分分別占全國汽油和柴油成品總量的80%和30%,催化裂化的經(jīng)濟效益約占各煉廠總經(jīng)濟效益的2/3。因此催化裂化已經(jīng)成為我國煉油工業(yè)的核心技術(shù)。催化裂化是在熱和催化劑的作用下使重質(zhì)油發(fā)生裂化反應(yīng),轉(zhuǎn)變?yōu)榱鸦瘹?、汽油和柴油等的過程。催化裂化包括反應(yīng)再生系統(tǒng)(簡稱反再系統(tǒng))和分餾吸收穩(wěn)定系統(tǒng)兩大部分。催化裂化裝置(FluidCatalyticCrackingUnit,簡稱FCCU)作為約占總汽油產(chǎn)量的40%的生產(chǎn)單元,催化裂化反應(yīng)-再生系統(tǒng)是催化裂化的核心,直接影響產(chǎn)品產(chǎn)量分布和整個裝置的平穩(wěn)操作。隨著催化裂化工藝、技術(shù)的提高和裝置大型化發(fā)展,催化裂化裝置的安全、平穩(wěn)、長周期運行成為煉油企業(yè)日常管理的重點,也是實現(xiàn)煉油企業(yè)效益最大化的有效途徑。重油催化裂化裝置投產(chǎn)后會因各種原因造成非計劃停車、泄漏、火災(zāi)爆炸等事故。造成非計劃停工的原因是多方面的,有外界的影響,如因外電網(wǎng)晃電造成停工,如加工原油品種越來越多,催化裂化摻煉重油比例越來越高,生產(chǎn)技術(shù)難度也越來越大,也有主觀的原因,如工藝管理不嚴(yán),管理和操作人員素質(zhì)不高等。由于重油催化裂化裝置是石化煉油廠最主要和最關(guān)鍵的裝置,保持其安全平穩(wěn)長周期運行是提高催化裂化裝置的經(jīng)濟效益、避免各類停車、火災(zāi)、爆炸等事故的關(guān)鍵所在。然而實際生產(chǎn)裝置無法進行相關(guān)故障實驗測試研究,而且一般故障分析方法給出的多為模糊、定性的結(jié)果,無法滿足現(xiàn)實分析要求。催化裂化是重油輕質(zhì)化的主要手段之一,主要包括:反應(yīng)再生系統(tǒng)、分餾系統(tǒng)、吸收穩(wěn)定系統(tǒng)。建立過程動態(tài)模型的重點和難點在于建立反應(yīng)再生系統(tǒng)數(shù)學(xué)模型。催化裂化裝置反再系統(tǒng)的動態(tài)模型發(fā)展?fàn)顩r大致為:McFarlane等在1993年提出了包括大部分ModelIV型催化裂化裝置。然而,此反再模型過于簡化裂化反應(yīng)動力學(xué)模型,缺少對燒焦反應(yīng)的描述。Arbel等針對提升管反應(yīng)器假設(shè)為擬穩(wěn)態(tài)模型。1986年,鄭遠揚等為同軸式提升管催化裂化裝置建立動態(tài)模型,具有一定的理論基礎(chǔ)但沒有充分進行動態(tài)仿真研究。1998年,羅雄麟等為前置燒焦罐式高效再生器催化裂化裝置建立反再系統(tǒng)動態(tài)機理模型。目前國內(nèi)關(guān)于催化裂化裝置的動態(tài)仿真多基于這兩種動態(tài)機理模型。公開號為CN202352224U的中國專利文獻公開了一種多功能精餾實訓(xùn)裝置,采用化工技術(shù)及自動化控制技術(shù)相結(jié)合,能夠?qū)崿F(xiàn)工廠情景化、故障模擬化及操作實際化。公開號為CN102736619A的中國專利文獻公開了一種飛輪故障模擬系統(tǒng),可實現(xiàn)機械系統(tǒng)的故障、電氣系統(tǒng)的故障和潤滑系統(tǒng)故障的模擬。技術(shù)實現(xiàn)要素:本發(fā)明提供了一種雙段式催化裂化反再系統(tǒng)故障動態(tài)模擬方法及系統(tǒng),通過合理設(shè)置異常工況的動態(tài)模擬,分析在異常擾動下整個系統(tǒng)的故障動態(tài)特性,獲得有效故障數(shù)據(jù),解決在實際生產(chǎn)裝置上無法進行故障實驗研究獲取系統(tǒng)故障信息的難題。一種雙段式催化裂化反再系統(tǒng)故障動態(tài)模擬方法,包括:(1)建立知識數(shù)據(jù)庫,整合故障數(shù)據(jù)庫;(2)基于工業(yè)雙段式催化裂化裝置的DCS數(shù)據(jù)和工藝模型資料,構(gòu)建雙段式催化裂化反再系統(tǒng)動態(tài)模型,建立雙段式催化裂化反再系統(tǒng)動態(tài)模型庫;(3)根據(jù)知識數(shù)據(jù)庫,得到不同工況下的基礎(chǔ)輸入數(shù)據(jù),求得動態(tài)模擬的穩(wěn)態(tài)工作點;(4)從故障數(shù)據(jù)庫選擇特定故障類型,轉(zhuǎn)換為動態(tài)模型的輸入偏差,進行故障動態(tài)模擬;(5)運用故障智能分析模塊,驗證故障類型,將模擬結(jié)果錄入故障數(shù)據(jù)庫,完善數(shù)據(jù)庫。一種雙段式催化裂化反再系統(tǒng)故障動態(tài)模擬系統(tǒng),包括:DCS數(shù)據(jù)采集模塊、雙段式催化裂化反再系統(tǒng)動態(tài)模型庫、知識數(shù)據(jù)庫、故障數(shù)據(jù)庫以及故障智能分析模塊?;诠I(yè)雙段式催化裂化裝置的DCS數(shù)據(jù)和工藝模型資料,在對工業(yè)雙段式催化裂化裝置的簡化基礎(chǔ)上得到機理模型,所述雙段式催化裂化反再系統(tǒng)動態(tài)模型庫的模型分為反應(yīng)分離部分和再生部分;所述反應(yīng)分離部分包括提升管部分和氣提分離部分;所述再生部分包括一段二段再生部分和稀相管部分。所述提升管部分的建模采用六集總反應(yīng)動力學(xué)模型,建立擬穩(wěn)態(tài)模型;所述氣提分離部分建立物料平衡和能量平衡模型。提升管部分的機理模型從反應(yīng)的機理出發(fā),把原料組成及反應(yīng)條件對反應(yīng)速度及反應(yīng)結(jié)果的影響,定量的關(guān)聯(lián)起來,得到反應(yīng)動力學(xué)模型,此處所用的反應(yīng)動力學(xué)模型為六集總反應(yīng)動力學(xué)模型。所述六集總反應(yīng)動力學(xué)模型把裂化原料和產(chǎn)品歸納成6個集總,它們分別為:蠟油(VGO)、汽油(GLN)、柴油(LCO)、液化石油氣(LPG)、可燃燒氣體(FG)和焦炭(CK)。提升管內(nèi)裂化反應(yīng)時間相對再生器燒焦反應(yīng)時間很短,因此可以建立擬穩(wěn)態(tài)模型。根據(jù)牛頓定律建立固相與氣相沿管長的速度分布模型,根據(jù)熱量平衡的假設(shè),氣固兩相的溫度相同,建立沿管長的壓力分布模型。∂Fi∂z=ΩRS(1-ϵg)r^i---(1)]]>∂Fck∂z=ΩRSϵcr^ck---(2)]]>∂vc∂t=CD34ρg(vg-vc)2dclρcvc+(ρg-ρc)gρcvc---(3)]]>∂vg∂z=1-ϵgϵgCtΣir^iMw,i-vgCt∂Ct∂z-vgϵg∂ϵg∂z---(4)]]>∂Ct∂z=1RT∂PRS∂z-CtT∂TRS∂z---(5)]]>∂TRS∂z=ΩRSϵcΔHcrkr^DOFgCp,g+FcCp,c---(6)]]>∂PRS∂z=-ϵcρcg---(7)]]>式中,F(xiàn)i——集總i的質(zhì)量流量,kg/s;Fck——焦炭的質(zhì)量流量,kg/s;z——提升管長度微元,m;εg——提升管中氣體的空隙率,m3/m3;εc——提升管中催化劑的空隙率,m3/m3;ΩRS——提升管的截面積,m2;——集總i到集總j的反應(yīng)速率,mol/(m3·s);vg——空氣速率,m/s;vc——催化劑速率,m/s;t——反應(yīng)時間,s;CD——氣固兩相間的摩擦系數(shù);ρg——氣體的密度,kg/m3;ρc——催化劑的密度,kg/m3;dcl——催化劑團的直徑,m;g——重力加速度,9.18m/s2;Ci——集總i的摩爾濃度,mol/m3;Mw,I——集總i的摩爾質(zhì)量,kg/mol;R——理想氣體常數(shù),8.314J/(mol·K);PRS——提升管內(nèi)的壓力,Pa;TRS——提升管內(nèi)的溫度,K;T——反應(yīng)溫度,K;△Hcrk——每單位質(zhì)量VGO裂化為其他集總所吸收的熱量,J/kg;Fg——氣體的質(zhì)量流量,kg/s;Fc——催化劑的質(zhì)量流量,kg/s;Cp,g——氣體的平均比熱,J/(kg·K);Cp,c——催化劑的平均比熱,J/(kg·K);式(1)和式(2)為各集總和催化劑上的碳含量的質(zhì)量平衡方程,其中,式(3)和式(4)為固相與氣相沿管長的速度分布方程;式(5)為各集總沿管長的質(zhì)量濃度分布;式(6)為關(guān)于反應(yīng)溫度的熱量衡算方程;式(7)為沿管長的壓力分布。所述氣提分離部分不再進行裂化反應(yīng),主要目的是分離氣固兩相。因此建立物料平衡和能量平衡模型。∂Wi,ST∂t=Fi,RSout-Fi,STout,i=VGO,GLN,LCO,LPG,FG,CK,H2O---(8)]]>∂Wc,ST∂t=Fc,RSout-Fc,STout---(9)]]>∂LST∂t=Fc,RSout-Fc,SToutρcϵcΩST---(10)]]>∂(Wc,STCpcTST+Wg,STCpgTST)∂t=Fg,RSoutHg,RSout+Fs,STHs,ST+Fc,RSoutHc,RSout-Fg,SToutHg,STout-Fc,SToutHc,STout---(11)]]>Pg,ST=Wg,STRTg,STMwg,STVg,ST---(12)]]>式中,Wi,ST——各種產(chǎn)物在氣提分離部分中的質(zhì)量,kg;Wc,ST——催化劑在氣提分離部分中的質(zhì)量,kg;Fi,Rsout——進入氣提分離部分各產(chǎn)物的質(zhì)量流量,kg/s;Fi,STout——離開氣提分離部分各產(chǎn)物的質(zhì)量流量,kg/s;Fc,Rsout——進入氣提分離部分催化劑的質(zhì)量流量,kg/s;Fc,STout——離開氣提分離部分催化劑的質(zhì)量流量,kg/s;LST——氣提分離部分密相層的料位,m;ΩST——氣提分離部分分離器的截面積,m2;Fs,ST——進入氣提分離部分的氣提蒸汽質(zhì)量流量,kg/s;Hs,ST——進入氣提分離部分的氣提蒸汽的熱量,J/kg;Wg,ST——氣體在氣提分離部分中的質(zhì)量,kg;Pg,ST——氣提分離部分分離器的壓力,Pa;TST——氣提分離部分分離器內(nèi)的溫度,K;Fg,Rsout——進入氣提分離部分氣體的質(zhì)量流量,kg/s;Fg,STout——離開氣提分離部分氣體的質(zhì)量流量,kg/s;Hg,Rsout——進入氣提分離部分氣體的熱量,J/kg;Hg,STout——離開氣提分離部分氣體的熱量,J/kg;Hc,Rsout——進入氣提分離部分催化劑的熱量,J/kg;Hc,STout——離開氣提分離部分催化劑的熱量,J/kg;Wg,ST——氣體在氣提分離部分中的質(zhì)量,kg;Mwg,ST——氣提分離部分氣體的平均分子量,kg/mol;Tg,ST——氣提分離部分內(nèi)氣體的溫度,K;Vg,ST——氣提分離部分內(nèi)氣體的體積,m3。式(8)和式(9)為產(chǎn)物與催化劑藏量的物料平衡;式(10)為氣提分離部分的料位方程;式(11)為能量平衡方程;式(12)為氣提分離部分內(nèi)氣體的壓力。所述再生部分再生器的燃燒反應(yīng),根據(jù)燒焦反應(yīng)動力學(xué),建立氣體、碳、氫元素的摩爾平衡,催化劑質(zhì)量平衡與能量平衡模型;所述稀相管部分建立擬穩(wěn)態(tài)模型。所述再生部分再生器中的燃燒主要包括兩種類型,一種是燃燒經(jīng)裂化反應(yīng)附著在催化劑上的焦炭,此為主要的燃燒反應(yīng),另一種是由待生催化劑夾帶而來的部分油氣及裂化產(chǎn)物,因為這種夾帶來的混合物的質(zhì)量相對較小,所以此為次要的燃燒反應(yīng)。所述再生部分對于再生器中燃燒反應(yīng),采用燒焦反應(yīng)動力學(xué)進行建模,主要包括燒炭和燒氫兩種反應(yīng),具體包含5種化學(xué)反應(yīng),可得到不同組分的反應(yīng)速率。根據(jù)燒焦反應(yīng)動力學(xué),建立氣體、碳、氫元素的摩爾平衡,催化劑質(zhì)量平衡與能量平衡模型。∂N^i,RG∂t=Ni,RGin-Ni,RGout+Vbed(ϵgΣj(rjgvjig)+ϵcρcΣj(rjsvjis)),i=O2,CO,CO2,H2O,N2,C,H---(13)]]>∂Wc,RG∂t=Fc,RGin-Fc,RGout---(14)]]>∂LRG∂t=Fc,RGin-Fc,RGoutρcϵcΩRG---(15)]]>∂(Wc,RGCpcTRG+Wg,RGCpgTRG)∂t=Fg,RGinHg,RGin+Fc,RGinHc,RGin+Qr0-Fg,RGoutHg,RGout-Fc,RGoutHc,RGout-Qloss---(16)]]>PRG=Wg,RGRTRGM‾w,RGgVg,RG---(17)]]>式中,——再生器氣體、碳、氫元素的摩爾總量,mol;——進入再生器氣體、碳、氫元素的摩爾流量,mol/s;——離開再生器氣體、碳、氫元素的摩爾流量,mol/s;Vbed——密相床層的體積,m3;j——反應(yīng)方程式的序號,1-4;vji——第j個化學(xué)反應(yīng)方程式中i組分的反應(yīng)式系數(shù),無因次量;Wc,RG——催化劑在再生器中的質(zhì)量,kg;Fc,RGin——進入再生器催化劑的質(zhì)量流量,kg/s;Fc,RGout——離開再生器催化劑的質(zhì)量流量,kg/s;LRG——再生器的料位,m;ΩRG——再生器的截面積,m2;TRG——再生器內(nèi)的溫度,K;Wg,RG——氣體在再生器中的質(zhì)量,kg;Fg,RGin——進入再生器氣體的質(zhì)量流量,kg/s;Fg,RGout——離開再生器氣體的質(zhì)量流量,kg/s;Hg,RGin——進入再生器氣體的熱量,J/kg;Hg,RGout——離開再生器氣體的熱量,J/kg;Hc,RGin——進入再生器催化劑的熱量,J/kg;Hc,RGout——離開再生器催化劑的熱量,J/kg;Qloss——再生器的熱量損失,J;PRG——再生器的壓力,Pa;——再生器氣體的平均分子量,kg/mol;Vg,RG——再生器內(nèi)氣體的體積,m3。式(13)為氣體、碳、氫元素的摩爾平衡方程;式(14)為催化劑的質(zhì)量平衡方程;式(15)再生器的料位方程;式(16)為能量平衡方程。式(17)為再生器稀相層的壓力。稀相管的作用是使一段再生器中的半再生催化劑由稀相管主風(fēng)吹入二段再生器中進行完全再生,即起到兩段再生器的連接作用。由于催化劑與氣體(主要為O2、CO2、CO、N2和水蒸汽)在稀相管停留的時間較短,與提升管反應(yīng)部分類似,因此可以建立擬穩(wěn)態(tài)模型。∂Ni,Lift∂z=ΩLift(ϵgΣj(rjgvjig)+ϵcρcΣj(rjsvjis))---(18)]]>∂Ni,Lift∂z=ΩLiftϵcρcΣj(rjsvjis)---(19)]]>ΣiFiCpi∂TLift∂z=-ΩLift(ϵgΣj(rjgΔHjig)+ϵcρcΣj(rjsΔHjis)),i=O2,CO,CO2,H2O,N2,C,H,Catalyst---(20)]]>∂PLift∂z=-(ϵcρc+ϵgρg)g---(21)]]>式中,Ni,Lift——稀相管中氣體及碳、氫元素的摩爾流量,mol/s;ΩLift——稀相管的截面積,m2;Cpi——i的平均比熱,J/(kg·K);TLift——稀相管內(nèi)的溫度,K;PLift——稀相管內(nèi)的壓力,Pa。式(18)和式(19)為氣體及碳、氫元素的摩爾平衡方程;式(20)為能量平衡方程;式(21)為壓力沿管長的分布。反再系統(tǒng)的模型不僅僅需要各個部分的模型,還要求把這些模型聯(lián)系起來綜合考慮,把各部分的流量、溫度、壓力等作為聯(lián)系的手段。其中,對于所述反應(yīng)分離部分,提升管出口處催化劑的流量、油氣和各產(chǎn)物的流量、催化劑上的含碳量以及氣固兩相的溫度作為氣提分離部分入口處的邊界條件。對于所述再生部分,一段再生部分進行燒焦反應(yīng),燒焦所產(chǎn)生的氣體以及半再生催化劑,由稀相管主風(fēng)帶入所述稀相管部分。稀相管主風(fēng)控制催化劑的流量,一段再生器內(nèi)的溫度,作為稀相管部分入口處的邊界條件。燒焦反應(yīng)繼續(xù)在稀相管中進行,稀相管出口處的溫度、催化劑的流量、氣體的流量又作為二段再生部分入口處的邊界條件。所述反應(yīng)分離部分與再生部分之間的聯(lián)系是通過催化劑的循環(huán)來完成的。氣提分離部分內(nèi)的待生催化劑通過待生斜管流入一段再生部分,即氣提分離部分密相層的溫度為待生催化劑的溫度,待生催化劑流入一段再生部分,所以待生催化劑的溫度可以作為一段再生部分入口邊界條件。而流出氣提分離部分催化劑的流量也就是流入一段再生部分催化劑的流量,一段再生部分入口處的催化劑上的含碳量也與分離氣提部分相同。二段再生部分的再生催化劑通過再生斜管流入提升管反應(yīng)器的底部,到達提升管反應(yīng)器的底部的催化劑的溫度與二段再生部分密相床層的溫度相同,即提升管反應(yīng)器入口條件為二段再生部分出口處的條件通過以上的分析,就可以得到反應(yīng)再生整個系統(tǒng)的數(shù)學(xué)模型,而不是孤立的各部分的數(shù)學(xué)模型。所述知識數(shù)據(jù)庫包括裝置專家知識和歷史采集數(shù)據(jù)。所述知識數(shù)據(jù)庫的建立包括:ⅰ)在建立初期,搜集生產(chǎn)設(shè)備、安全設(shè)備、危險源和生產(chǎn)活動的資料,完成基本的知識收集工作,得到故障總結(jié)情況;ⅱ)通過對工業(yè)雙段式催化裂化裝置DCS端采集在線測量信號的分析,得到設(shè)備運行實際工況。所述穩(wěn)態(tài)工作點初始輸入數(shù)據(jù)包括:新鮮油氣的溫度與流量、提升管汽化蒸汽的溫度與流量、汽提蒸汽的溫度與流量、主風(fēng)系統(tǒng)的溫度與風(fēng)量、分餾塔與廢氣的壓力和劑油比。所述故障數(shù)據(jù)庫的故障類型包括工藝類故障、操作類故障和設(shè)備類故障;所述工藝類故障包括進料原油帶水和催化劑失活故障;所述操作類故障包括主風(fēng)系統(tǒng)故障;所述設(shè)備類故障包括再生滑閥堵塞。所述故障數(shù)據(jù)庫的建立包括:Ⅰ)在建立初期,通過分析知識數(shù)據(jù)庫中的故障總結(jié)情況,得到設(shè)備的工藝失常狀態(tài)故障樹;Ⅱ)在得到故障動態(tài)模擬結(jié)果后,分析驗證故障類型,將模擬結(jié)果錄入故障數(shù)據(jù)庫,完善數(shù)據(jù)庫。工業(yè)過程中易發(fā)故障可分為三類:操作類故障、工藝類故障和設(shè)備類故障。其中,操作類故障是由于操作人員錯誤操作引起的,在實際發(fā)生的故障占有比例很大;工藝類故障是由于工藝條件隨時間或外部條件發(fā)生異常變化引起的;設(shè)備類故障包括設(shè)備老化失效、設(shè)備斷電、外物損壞等引起。本發(fā)明中可選取四種特定故障開展故障動態(tài)模擬研究,在反再系統(tǒng)過程動態(tài)模擬運行穩(wěn)定后的某一時刻,引入進料原油帶水(工藝類故障)、催化劑失活故障(工藝類故障)、主風(fēng)系統(tǒng)故障(操作類故障)、再生滑閥堵塞(設(shè)備類故障),分析不同故障動態(tài)擾動下系統(tǒng)特性。本發(fā)明的有益結(jié)果是:在對實際生產(chǎn)與模型計算過程簡化卻不失催化裂化反再系統(tǒng)重要特性的基礎(chǔ)上,建立了雙段式催化裂化反再部分的動態(tài)模擬系統(tǒng),并在動態(tài)模擬系統(tǒng)上合理設(shè)置引起異常工況的擾動因素,進行故障動態(tài)特性仿真研究,獲得有效的故障數(shù)據(jù),為進一步探索有效的故障診斷與容錯控制方法提供一種新思路。附圖說明:圖1為雙段式催化裂化反再系統(tǒng)故障動態(tài)模擬系統(tǒng)示意圖;圖2為本發(fā)明實施例穩(wěn)態(tài)工作點的求解流程圖;圖3a為本發(fā)明實施例中進料原油帶水故障系統(tǒng)動態(tài)響應(yīng)圖——裂化反應(yīng)產(chǎn)率;圖3b為本發(fā)明實施例中進料原油帶水故障系統(tǒng)動態(tài)響應(yīng)圖——溫度;圖3c為本發(fā)明實施例中進料原油帶水故障系統(tǒng)動態(tài)響應(yīng)圖——催化劑料位;圖3d為本發(fā)明實施例中進料原油帶水故障系統(tǒng)動態(tài)響應(yīng)圖——壓力;圖4a為本發(fā)明實施例中催化劑失活故障系統(tǒng)動態(tài)響應(yīng)圖——裂化反應(yīng)產(chǎn)率;圖4b為本發(fā)明實施例中催化劑失活故障系統(tǒng)動態(tài)響應(yīng)圖——溫度;圖4c為本發(fā)明實施例中催化劑失活故障系統(tǒng)動態(tài)響應(yīng)圖——催化劑料位;圖4d為本發(fā)明實施例中催化劑失活故障系統(tǒng)動態(tài)響應(yīng)圖——壓力;圖5a為本發(fā)明實施例中主風(fēng)系統(tǒng)故障系統(tǒng)動態(tài)響應(yīng)圖——裂化反應(yīng)產(chǎn)率;圖5b為本發(fā)明實施例中主風(fēng)系統(tǒng)故障系統(tǒng)動態(tài)響應(yīng)圖——溫度;圖5c為本發(fā)明實施例中主風(fēng)系統(tǒng)故障系統(tǒng)動態(tài)響應(yīng)圖——催化劑料位;圖5d為本發(fā)明實施例中主風(fēng)系統(tǒng)故障系統(tǒng)動態(tài)響應(yīng)圖——壓力;圖6a為本發(fā)明實施例中再生滑閥堵塞故障系統(tǒng)動態(tài)響應(yīng)圖——裂化反應(yīng)產(chǎn)率;圖6b為本發(fā)明實施例中再生滑閥堵塞故障系統(tǒng)動態(tài)響應(yīng)圖——溫度;圖6c為本發(fā)明實施例中再生滑閥堵塞故障系統(tǒng)動態(tài)響應(yīng)圖——催化劑料位;圖6d為本發(fā)明實施例中再生滑閥堵塞故障系統(tǒng)動態(tài)響應(yīng)圖——壓力。具體實施方式:以下將結(jié)合附圖和具體過程對本發(fā)明進行進一步的闡述和說明。如圖1所示,一種雙段式催化裂化反再系統(tǒng)故障動態(tài)模擬系統(tǒng),包括:DCS數(shù)據(jù)采集模塊、雙段式催化裂化反再系統(tǒng)動態(tài)模型庫、知識數(shù)據(jù)庫、故障數(shù)據(jù)庫以及故障智能分析模塊。一種雙段式催化裂化反再系統(tǒng)故障動態(tài)模擬方法,包括:(1)建立知識數(shù)據(jù)庫,整合故障數(shù)據(jù)庫;所述知識數(shù)據(jù)庫的建立包括:ⅰ)在建立初期,搜集生產(chǎn)設(shè)備、安全設(shè)備、危險源和生產(chǎn)活動的資料,完成基本的知識收集工作,得到故障總結(jié)情況,如表1所示;表1雙段式催化裂化反再系統(tǒng)故障總結(jié)情況表ⅱ)通過對工業(yè)雙段式催化裂化裝置DCS端采集在線測量信號的分析,得到設(shè)備運行實際工況。所述穩(wěn)態(tài)工作點初始輸入數(shù)據(jù)包括:新鮮油氣的溫度與流量、提升管汽化蒸汽的溫度與流量、汽提蒸汽的溫度與流量、主風(fēng)系統(tǒng)的溫度與風(fēng)量、分餾塔與廢氣的壓力和劑油比。所述故障數(shù)據(jù)庫的故障類型包括工藝類故障、操作類故障和設(shè)備類故障;所述工藝類故障包括進料原油帶水和催化劑失活故障;所述操作類故障包括主風(fēng)系統(tǒng)故障;所述設(shè)備類故障包括再生滑閥堵塞。所述故障數(shù)據(jù)庫的建立包括:Ⅰ)在建立初期,通過分析知識數(shù)據(jù)庫中的故障總結(jié)情況,得到設(shè)備的工藝失常狀態(tài)故障樹;Ⅱ)在得到故障動態(tài)模擬結(jié)果后,分析驗證故障類型,將模擬結(jié)果錄入故障數(shù)據(jù)庫,完善數(shù)據(jù)庫。(2)基于工業(yè)雙段式催化裂化裝置的DCS數(shù)據(jù)和工藝模型資料,在MATLAB平臺上搭建雙段式催化裂化反再系統(tǒng)動態(tài)模型,建立雙段式催化裂化反再系統(tǒng)動態(tài)模型庫;(3)根據(jù)知識數(shù)據(jù)庫,得到不同工況下的基礎(chǔ)輸入數(shù)據(jù),求得動態(tài)模擬的穩(wěn)態(tài)工作點;本實施例的穩(wěn)態(tài)工作點初始輸入數(shù)據(jù)如表2所示:表2雙段式催化裂化反再系統(tǒng)穩(wěn)態(tài)工作點初始輸入數(shù)據(jù)動態(tài)模擬的穩(wěn)態(tài)工作點的求解流程如圖2所示,運用MATLAB平臺上的ode23求解得到穩(wěn)態(tài)工作點。(4)從故障數(shù)據(jù)庫選擇特定故障類型,轉(zhuǎn)換為動態(tài)模型的輸入偏差,進行故障動態(tài)模擬;本實例中給出4種特定故障下的系統(tǒng)主要變量的動態(tài)模擬情況,分別為進料原油帶水、催化劑失活、主風(fēng)系統(tǒng)故障和再生滑閥堵塞故障。1)進料原油帶水故障動態(tài)模擬雙段式催化裂化裝置反再系統(tǒng)中干擾反應(yīng)器影響最大的操作是原料的特性變化。原油性質(zhì)是所有操作條件中最重要的,制定生產(chǎn)方案、選擇操作條件都應(yīng)先了解原油的性質(zhì)。正常工況下進料溫度為450.12K,不論是否存在相變,只要原油帶水都會引起進料溫度下降,且在有相變時引起進料溫度的大幅下降。因此在雙段式催化裂化反再裝置動態(tài)模擬系統(tǒng)穩(wěn)定運行后2ks后,引入進料原油溫度減小的故障擾動,系統(tǒng)的動態(tài)響應(yīng)模擬結(jié)果如圖3a、3b、3c和3d所示。從圖3b、3c看到,原料帶水會引起反應(yīng)器催化劑料位升高,一段二段再生器出口溫度降低,反應(yīng)溫度上升。因此,處理措施為控制反應(yīng)溫度,適當(dāng)提高再生溫度,這與實際工廠的處理措施相符合。2)催化劑失活故障動態(tài)模擬催化劑在生產(chǎn)過程中其活性隨著使用時間的增長而降低,催化劑的失活甚至可以導(dǎo)致雙段式催化裂化反再系統(tǒng)的非穩(wěn)態(tài)操作。催化劑失活類型很多,比如化學(xué)的、熱的、機械的。催化劑在裂化反應(yīng)過程中由于積碳的發(fā)生,活性組分被覆蓋,導(dǎo)致活性降低。催化劑失活是一個復(fù)雜過程,活性衰退時,反應(yīng)速率隨著活性的衰退而下降。本文通過模擬反應(yīng)動力學(xué)中各反應(yīng)的速率下降進行催化劑失活故障模擬,系統(tǒng)的動態(tài)響應(yīng)模擬結(jié)果如圖4a、4b、4c和4d所示。從圖4a可以看到,再生催化劑活性降低會引起原油轉(zhuǎn)化率的下降,這與實際工廠經(jīng)驗相符。同時,反應(yīng)器催化劑料位大幅下降,一段二段再生器溫度與壓力均上升。需及時恢復(fù)再生催化劑活性,一般通過燒焦的方法來恢復(fù)催化劑的活性,但有時燒焦溫度控制失誤會使再生催化劑失活。3)主風(fēng)系統(tǒng)故障動態(tài)模擬再生器的作用為燒去結(jié)焦劑上的焦炭以恢復(fù)催化劑活性,同時提供裂化反應(yīng)所需熱量。再生用主風(fēng)由主風(fēng)系統(tǒng)提供。主風(fēng)系統(tǒng)或可由于操作工的原因進行誤操作導(dǎo)致主風(fēng)量的改變,從而導(dǎo)致異常工況。通過模擬兩段再生器主風(fēng)量均在2ks后上升5%以模擬主風(fēng)故障,系統(tǒng)的動態(tài)響應(yīng)模擬結(jié)果如圖5a、5b、5c和5d所示。由于主風(fēng)量的變化對反應(yīng)器影響不大,因此對裂化反應(yīng)產(chǎn)率影響不大,與圖5a結(jié)果相符。主風(fēng)量上升,兩段再生器內(nèi)壓力、溫度均增大,與圖5b和5d結(jié)果相符。4)再生滑閥堵塞故障動態(tài)模擬再生滑閥是催化裂化裝置特殊滑閥之一,使用在高溫催化劑環(huán)境下,作為催化劑循環(huán)流程中的關(guān)鍵設(shè)備之一,對催化裂化反應(yīng)溫度控制、物料調(diào)節(jié)以及壓力控制起到關(guān)鍵作用。通過模擬再生滑閥在2ks后堵塞100s后恢復(fù)正常的運行異常情況以進行滑閥故障分析,系統(tǒng)的動態(tài)響應(yīng)模擬結(jié)果如圖6a、6b、6c和6d所示。再生滑閥堵塞后系統(tǒng)波動極大,反應(yīng)器催化劑料位急劇下降,反應(yīng)溫度上升,此與工業(yè)現(xiàn)場規(guī)程描述相符。(5)運用故障智能分析模塊,驗證故障類型,將模擬結(jié)果錄入故障數(shù)據(jù)庫,完善數(shù)據(jù)庫。當(dāng)前第1頁1 2 3