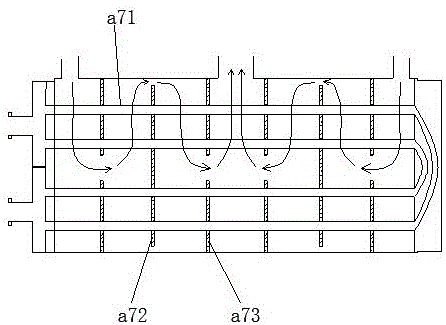
本發(fā)明涉及軸承裝置領域,尤其涉及及發(fā)電機或電動機軸承。
背景技術:
:軸承是當代機械設備中一種重要零部件。它的主要功能是支撐機械旋轉體,降低其運動過程中的摩擦系數,并保證其回轉精度。按運動元件摩擦性質的不同,軸承可分為滾動軸承和滑動軸承兩大類。滾動軸承一般由內圈、外圈、滾動體和保持架四部分組成,內圈的作用是與軸相配合并與軸一起旋轉;外圈作用是與軸承座相配合,起支撐作用;滾動體是借助于保持架均勻的將滾動體分布在內圈和外圈之間,其形狀大小和數量直接影響著滾動軸承的使用性能和壽命;保持架能使?jié)L動體均勻分布,防止?jié)L動體脫落,引導滾動體旋轉起潤滑作用?;瑒虞S承,是在滑動摩擦下工作的軸承,其軸承支承的軸部分稱為軸頸,與軸頸相配的零件稱為軸瓦?;瑒虞S承具有工作平穩(wěn)、可靠、無噪聲的優(yōu)點,但由于摩擦較大,其軸頸與軸瓦之間通過潤滑油分開而不發(fā)生直接接觸。在液體潤滑條件下,可以大大減小摩擦損失和表面磨損,同時,油膜還具有一定的吸振能力。另外,為了改善軸瓦表面的摩擦性質而在其內表面上澆鑄的減摩材料層稱為軸承襯。軸瓦和軸承襯的材料統(tǒng)稱為滑動軸承材料?;瑒虞S承應用場合一般在低速重載工況條件下,或者是維護保養(yǎng)及加注潤滑油困難的運轉部位。軸承是用于支撐發(fā)電機、電動機、轉輪、飛輪等的必不可少的部件,在用于大型發(fā)電機時,如水輪發(fā)電機,由于水輪發(fā)電機軸承所承接的徑向力和軸向力非常大,其摩擦產熱也非常大,需要特定的冷卻結構對其摩擦面進行降熱?,F有水輪發(fā)電機采用的軸承,如圖1所示,包括軸承座a1、軸承蓋a2、軸瓦a3、油泵a4、第一油腔a5、第二油腔a6和冷卻器a7;所述軸承蓋a2蓋合在軸承座a1上,所述軸瓦a3固定在軸承座a1上,所述軸瓦a3內徑側設有軸向方向的冷卻油槽a31,所述冷卻油槽a31的中部設有注油孔a32,所述冷卻油槽a31的兩側設置為排油孔a33;所述第一油腔a5為軸承蓋a2與軸承座a1蓋合形成的密封腔;所述第二油腔a6位于第一油腔a5下方,所述第二油腔a6的上腔壁設有進油道a61和出油道a62,所述第二油腔a6通過進油道a61連通第一油腔a5,所述第二油腔a6內安裝冷卻器a7,所述第二油腔a6的冷卻油通過出油道a62由油泵a5導入到注油孔a32,冷卻油流經軸瓦a3內徑面和冷卻油槽a31,流入排油孔a33,并排出到第一油腔a5?,F有水輪發(fā)電機軸承中常用的冷卻器a7,如圖2所示,包括冷卻銅管a71、邊環(huán)流道隔板a72和中心流道隔板a73,冷卻銅管a71貫穿邊環(huán)流道隔板a72和中心流道隔板a73;如圖3所示,所述邊環(huán)流道隔板a72的環(huán)邊與第二油腔a6的腔壁之間為用于流過冷卻油的邊環(huán)流道a74,如圖4所示,中心流道隔板a73的中心為用于流過冷卻油的中心流道a75。上述現有技術中采用的軸承冷卻器結構,存在如下不足:冷卻油只在第二油腔a6上半部流通,第二油腔a6下半部的冷卻油滯留,導致冷卻器a7與冷卻油的熱交換效率偏低,冷卻油的循環(huán)油溫偏高。目前水電站均采用上述現有的軸承冷卻器結構,在水輪發(fā)電機軸承的軸瓦和油溫運行三小時后,如表1所示,軸瓦溫度均在58℃以上,油溫在55℃以上。瓦編號12345油溫初始溫度31.229.630.430.830.229.61h溫度(℃)44.142.343.242.543.138.42h溫度(℃)56.354.253.254.752.749.83h溫度(℃)61.259.158.460.058.155.5表1由于現有的冷卻油主要采用46號汽輪機油或32號汽輪機油,46號汽輪機油在40℃下的運動粘黏度為45.8,其較佳運行溫度范圍為44-46℃;32號汽輪機油在40℃下的運動粘黏度為32,其較佳運行溫度范圍為38-40℃;現有的冷卻油運行過程中需控制在65℃以下,當冷卻油溫度過高,粘黏度變小,會導致潤滑不良,摩擦系數變大,摩擦產熱加劇,油溫迅速升高,且油溫居高不下,加劇滑動摩擦面的磨損;現有軸承采用此冷卻結構,為了防止油溫過高造成磨瓦,需對軸承中油溫進行監(jiān)控,當溫度偏高時,需增大需加大冷卻體的進水流量,當溫度過高時,進行報警,并停止運行。由于現有的水輪發(fā)電機軸承普遍存在熱交換效率偏低的問題,發(fā)電機容易出現報警停機,該問題不僅影響電站的輸出效能和經濟效益,且電站的停機和啟動過程對電站其它設備的使用壽命影響較大。存在的上述問題的原因主要是:由于冷卻油的密度和粘黏度受到油溫變化的影響較大,冷卻油溫越高,密度和粘黏度越小,冷卻油經冷卻銅管a71冷卻降溫后,其降溫量較大的冷卻油下沉,且流速變小,其降溫量較小的冷卻油上浮,導致第二油腔a6的下部區(qū)降溫量較大的冷卻油滯留,而上部區(qū)的降溫量較小的冷卻油流速變快,并從出油道a62流出,導致出油道a62流出的冷卻油處于高溫狀態(tài)。另外,現有技術中的軸承,還存在如下問題:1.其支撐瓦內側的注油槽設計在頂部,并需對支撐瓦內側進行刮瓦處理,用于生成儲油小凹點,改善潤滑,由于其支撐瓦內的冷卻油是從注油槽通過主軸旋轉帶入滑動摩擦面的儲油小凹點,其冷卻油的帶入量較少,冷卻油交換速率低,造成支撐瓦底部區(qū)域熱交換速率較小,且由于刮瓦的標準一般是每平方厘米有兩到三個接觸點,其刮瓦過程較為費時費工;2.由于現有的排油孔普遍是設計在支撐瓦的一端,導致支撐瓦的另一端油路不通,其支撐瓦的兩端存在較大的溫差,容易導致支撐瓦形變,并導致磨瓦的現象;3.現有推力軸承的推力瓦與推力盤間的冷卻油直接通過油泵從推力瓦的外徑側壓入,該種方式結構簡單,但由于受到離心力的阻礙,其冷卻油較難壓入到推力瓦的內徑側,容易導致推力瓦內徑側高溫燒瓦;4.經人工刮瓦后,刮瓦品質存在較大差異,刮瓦品質差的瓦面,其觸點的面積和儲油點的深度均存在較大的分布差異,導致其支撐瓦滑動摩擦面存在油膜厚度不均、以及油膜流速不均的問題,滑動摩擦面存在高溫點,容易產生雜質,造成摩擦系數不穩(wěn)定;5.軸承的大部件采用鑄造工藝,國標鑄造工藝允許2%缺陷,其部件的使用壽命較短,極大影響了整機安裝后的穩(wěn)定性;6.軸瓦安裝架通過左右兩個螺絲進行固定,在水輪發(fā)電機出現故障時會產生徑向振動,導致軸瓦松動,主軸易出現偏振,導致主軸形變;7.軸瓦瓦座是環(huán)形實心體,厚度大,不易散熱,體積笨重,在安裝時通常需要用吊機進行吊裝上半邊,然后旋轉取出另半邊,由于重量較大,取出非常不便;8.現有的組合軸承中,包含用于徑向受力的支撐瓦和用于軸向受力的推力瓦,支撐瓦和推力瓦均需有油路通過,用于實現熱交換,但由于油路油阻受溫度影響較大,油阻易發(fā)生變化,容易造成其中油路供油不穩(wěn)定,影響熱交換效率的穩(wěn)定性,導致瓦體溫度升高。技術實現要素:本發(fā)明的主要目的在于提供一種油道平衡式軸承,旨在提高軸承的熱交換效率,降低軸瓦和冷卻油的溫度,避免軸瓦磨損或燒毀,增長軸承的使用壽命。為了實現上述目的,本發(fā)明提供了一種油道平衡式軸承,特征在于,包括軸承座、軸承蓋、瓦座、支撐瓦、正推力瓦、反推力瓦、正推力盤、反推力盤、第一油腔、第二油腔、冷卻器和帶油罩,所述軸承蓋用于蓋合在軸承座上方,所述瓦座固定在軸承座上,支撐瓦固定在所述瓦座的內徑側,所述瓦座的軸向兩端分別為前端和后端,所述正推力瓦固定在瓦座的前端,所述反推力瓦固定在瓦座的后端,正推力盤貼合在正推力瓦的前端,反推力瓦貼合在反推力瓦的后端,正推力盤和反推力盤同軸固定在主軸;所述支撐瓦內徑側中部設有注油槽,支撐瓦內徑側軸向兩端設有排油槽,所述注油槽設有徑向貫通支撐瓦的注油孔;所述正推力瓦的內徑側與瓦座間的環(huán)形間隙空腔為甩油腔;所述第一油腔為軸承蓋與軸承座蓋合形成的密封腔;所述第二油腔為設置在軸承座下部的腔體,所述第二油腔位于第一油腔下方,所述第二油腔包含熱油進油口和冷油出油口;所述冷卻器設置在第二油腔內;所述帶油罩設置在正推力盤的外徑側,所述正推力盤的徑向外側壁為帶油面,所述帶油罩與帶油面之間形成帶油腔,所述帶油腔呈環(huán)形,帶油腔內設有擋油片,所述擋油片的一端固定在所述帶油罩的內壁上,所述擋油片的另一端滑動接觸帶油面;所述帶油腔的頂部設有高壓出油口,所述帶油腔的底部設有抽油口;所述排油槽與第一油腔連通,第一油腔通過熱油進油口連通第二油腔,第二油腔的冷油出油口連通帶油腔的抽油口,帶油腔的高壓出油口分兩路油道分別連通注油槽和甩油腔;所述高壓出油口與注油槽的連通油道為第一油道,用于對支撐瓦滑動接觸面的冷卻,所述高壓出油口與甩油腔的連通油道為第二油道,所述第一油道和第二油道中分別設置有用于穩(wěn)定流量的第一流量調節(jié)閥與第二流量調節(jié)閥。以上技術方案中,所述高壓出油口的其中一路油道連通到注油槽,用于對支撐瓦滑動接觸面的冷卻,并從排油槽排出到第一油腔,所述高壓出油口的另一路油道連通到甩油腔,用于對正推力瓦滑動接觸面的冷卻,并從正推力瓦的外徑側甩出到第一油腔。由于第一油道的連接終端和第二油道的連接終端具有不同的油阻,且其油阻受溫度影響較大,當油阻差異發(fā)生變化時,容易導致第一油道和第二油道的流量發(fā)生變化,出現少油或斷油的現象;采用該結構,設置第一流量調節(jié)閥與第二流量調節(jié)閥,能有效防止其中的一個油道斷油或流速減小較大,從而有效防止燒瓦,保持較高的熱交換效率。優(yōu)選地,所述第一流量調節(jié)閥包括閥座、流孔、閥體和彈性部件,流孔貫穿閥座,流孔包括進液端流孔和出液端,閥體設置在出液端,閥體通過彈性部件連接在閥座上,閥體與出液端之間為液流道。采用該結構,根據伯努利效應,其液流道的寬度隨流速的增大而變小,從而實現自動平衡調節(jié),使第一油道和第二油道均能保持穩(wěn)定的流速,避免第一油道與第二油道中冷卻油分流不穩(wěn)定,避免因第一油道或第二油道的流量過小而燒瓦。優(yōu)選地,所述第二流量調節(jié)閥與第一流量調節(jié)閥具有相同結構,優(yōu)選地,所述第一流量調節(jié)閥包括閥座、流孔、閥體和彈性部件,所述流孔貫穿閥座,所述閥座中部設有閥腔,閥腔與流孔垂直,閥腔底部連通流孔,閥腔的底部端為腔底端,閥腔的開口端為腔口端,閥體設置在腔底端,所述彈性部件的一端固定連接在腔口端,另一端連接閥體;所述腔底端呈球面狀,所述閥體呈球狀;所述閥體與腔底端之間為液流道。采用該結構,根據伯努利效應,其液流道的寬度隨流速的增大而變小,從而實現自動平衡調節(jié),使第一油道和第二油道均能保持穩(wěn)定的流速,避免第一油道與第二油道中冷卻油分流不穩(wěn)定,避免因第一油道或第二油道的流量過小而燒瓦。優(yōu)選的,所述第一流量調節(jié)閥和第二流量調節(jié)閥均為電控流量調節(jié)閥,瓦座上分別安裝有貼近支撐瓦和正推力瓦的溫度傳感器,第一流量調節(jié)閥和第二流量調節(jié)閥根據溫度傳感器的溫度感應值控制其流量。該種結構發(fā)生能實現自動穩(wěn)定支撐瓦和正推力瓦的溫度。優(yōu)選地,所述瓦座的內徑側中部設有第一環(huán)形儲油腔,瓦座前端外徑側設有第二環(huán)形儲油腔,第一環(huán)形儲油腔通過注油孔與注油槽連通,第二環(huán)形儲油腔連通甩油腔,第一環(huán)形儲油腔和第二環(huán)形儲油腔共同連通所述帶油腔的高壓出油口。采用該種結構方式,能有效防止注油槽和甩油腔斷油。優(yōu)選地,所述瓦座通過至少兩組固定螺絲固定在軸承座上。采用該種固定方式,能有效防止瓦座發(fā)生翹動。優(yōu)選地,所述瓦座外徑側設有環(huán)形散熱槽,所述環(huán)形散熱槽內設有軸向支撐件,所述軸向支撐件的兩端分別連接環(huán)形散熱槽的兩端。采用該種結構,環(huán)形散熱槽的軸向兩端部增大了徑向槽面,有利于環(huán)形散熱槽軸向兩端部的散熱。由于支撐瓦內的冷卻油是由中部向兩側流動,冷卻油沿流動路徑逐漸升溫,導致支撐瓦的兩端與中部存在較大的溫差,支撐瓦的兩端與中部的溫差會導致支撐瓦發(fā)生微小形變,支撐瓦中部內徑變大,支撐瓦兩端部內徑變小,支撐瓦的受力面變小,容易引發(fā)兩端溫度偏高;通過設置環(huán)形散熱槽,支撐瓦的兩端部溫度通過徑向槽面?zhèn)鲗У降谝挥颓?,有利于減小支撐瓦的兩端與中部的溫差,同時也較大程度的減小了瓦座的重量。優(yōu)選地,所述環(huán)形散熱槽內還設有徑向散熱片。優(yōu)選地,所述支撐瓦為分立式瓦體,包括上支撐瓦和下支撐瓦。優(yōu)選地,所述正推力瓦為分立式瓦體,包括至少兩個環(huán)形分布的扇形瓦體,所述扇形瓦體的前側面為推力接觸面,相鄰扇形瓦體之間的間隙為甩油槽。優(yōu)選地,所述注油槽沿支撐瓦的軸向方向開設,所述注油槽的軸向寬度小于支撐瓦的寬度。優(yōu)選地,所述支撐瓦的內側面包含至少兩條注油槽,所述注油槽沿軸向方向開設,所述注油槽均勻環(huán)形分布在支撐瓦的內側面。優(yōu)選地,所述支撐瓦的內側面包含至少兩條注油槽,所述注油槽螺旋分布在支撐瓦的內側面。采用常規(guī)的油槽結構,其遠離油槽區(qū)域容易出現油膜斷裂,油膜斷裂帶的滑動摩擦產熱大,導熱速度慢,容易造成燒瓦,該種方式能有效防止軸瓦與軸體間油膜的斷裂。優(yōu)選地,所述排油槽環(huán)繞支撐瓦開設。優(yōu)選地,所述排油槽設置有排油孔,排油孔連通第一油腔。優(yōu)選地,所述排油槽設有至少兩個排油孔,排油孔均勻環(huán)形分布。優(yōu)選地,所述排油槽包括第一排油槽和第二排油槽,第一排油槽和第二排油槽分別位于注油槽的兩端,所述第一排油槽與注油槽的間距小于30mm,所述第二排油槽與注油槽的間距小于30mm。優(yōu)選地,所述帶油面設有環(huán)形的帶油槽,所述帶油槽中環(huán)形分布有葉片。優(yōu)選地,所述帶油面設有用于密封的第一密封滑槽,所述帶油罩的后側端通過第一密封滑槽與所述帶油面密封接觸,主軸設有第二密封滑槽,帶油罩的前側端通過第二密封滑槽與主軸密封接觸。優(yōu)選地,所述熱油進油口和冷油出油口均位于第二油腔的邊端部。采用該種結構,第二油腔內的油路路徑增長,有利于降低冷卻油的溫度,從而提高熱交換效率;另外,冷油出油口位于位于第二油腔端部,可延長高壓出油口與抽油口之間的路徑長度,由于高壓出油口與抽油口之間的路徑長度越大,其高壓出油口與抽油口之間的壓差也越大,因此,上述結構方式,能提高高壓出油口的油壓,從而提高冷卻油流動速度。優(yōu)選地,所述第二油腔包含至少兩個分腔,所述各分腔串聯(lián)連通,各個分腔內安裝有冷卻器,所述各冷卻器的流道通過串聯(lián)連通。優(yōu)選地,所述第二油腔包含至少兩個分腔,所述各分腔串聯(lián)連通,各個分腔內安裝有冷卻器,所述各冷卻器的流道通過串聯(lián)連通,所述各冷卻器的液流方向與各分腔內油流方向相反。優(yōu)選地,所述冷卻器包括冷卻管、底孔流道隔板和頂孔流道隔板,所述冷卻管包含進水端和出水端,冷卻管的進水端和出水端分別連接有連接法蘭;所述底孔流道隔板和頂孔流道隔板間隔分布,所述底孔流道隔板的底部設有第一通道孔,所述頂孔流道隔板的頂部設有第二通道孔,所述底孔流道隔板和頂孔流道隔板的板面分布有用于穿插冷卻管的穿孔,冷卻管通過穿孔穿插在底孔流道隔板和頂孔流道隔板上。優(yōu)選地,所述冷卻器包含至少兩根冷卻管,各冷卻管并聯(lián),各冷卻管的進水端共同連接一個連接法蘭,各冷卻管的出水端共同連接到另一個連接法蘭。優(yōu)選地,所述底孔流道隔板和頂孔流道隔板垂直于冷卻管優(yōu)選地,所述冷卻器中的底孔流道隔板和頂孔流道隔板的總數為三至八片。優(yōu)選的,所述軸承座、軸承蓋和瓦座采用焊接工藝制作成型。現有的軸承座、軸承蓋和瓦座采用鑄造成型,鑄造成型工藝,容易出現澆注缺陷,根據工藝標準,缺陷占比允許2%以內,其缺陷通過補焊方式修補,鑄造成型的工件存在質量不穩(wěn)定的缺點;采用焊接工藝制作成型,其工藝簡單,加工方便,且能提高軸承座、軸承蓋和瓦座的質量穩(wěn)定性,杜絕鑄造缺陷。本發(fā)明的工作原理是:本發(fā)明所述的油道平衡式軸承,由于所述帶油腔的內徑面為帶油面,帶油面在旋轉過程中帶動冷卻油從抽油口流到高壓出油口,并導致抽油口與高壓出油口存在壓差,高壓出油口為相對高壓,抽油口為相對負壓,從而抽油口不斷從外部向帶油腔進油,高壓出油口不斷向外部出油。由于所述抽油口連通第二油腔,高壓出油口分兩路分別連通注油槽和甩油腔,所述第二油腔內的冷卻油從抽油口抽入帶油腔,并從高壓出油口壓入到注油槽和甩油腔;所述注油槽內的冷卻油在正壓壓強作用下進入主軸與支撐瓦的滑動摩擦面上,將摩擦熱吸入到冷卻油中,吸熱后的冷卻油從排油槽排出到第一油腔中;所述甩油腔內的冷卻油在正壓壓強和離心力作用下進入到正推力瓦與正推力盤的滑動摩擦面上,將摩擦熱吸入到冷卻油中,并從正推力瓦的外徑側排出到第一油腔中。由于所述第一油腔通過熱油進油口連通第二油腔,所述第一油腔內的高溫冷卻油通過熱油進油口進入第二油腔,并在第二油腔內與冷卻器發(fā)生熱交換。另外,本發(fā)明所述的油道平衡式軸承,在其優(yōu)化技術方案中,所述第二油腔包含至少兩個分腔,所述各分腔串聯(lián)連通,各個分腔內安裝有冷卻器,所述各冷卻器的流道通過串聯(lián)連通,所述各冷卻器的冷卻管內液流方向與各分腔內油流方向相反;該種結構方式,其油腔出液端可冷卻至冷卻器內的進液溫度,其冷卻器內冷卻液可較大程度地吸收冷卻油內的熱能,增大冷卻油與冷卻器的熱交換效率。此外,本發(fā)明所述的油道平衡式軸承,在其優(yōu)化技術方案中,其冷卻器包括冷卻管、底孔流道隔板和頂孔流道隔板,底孔流道隔板的底部設有第一通道孔,頂孔流道隔板的頂部設有第二通道孔,冷卻管穿插在底孔流道隔板和頂孔流道隔板上;該種結構方式,分腔內的冷卻油依次流經第一通道孔和第二通道孔;由于第一通道孔和第二通道孔分別位于冷卻腔內的底部和頂部,冷卻腔內的冷卻油反復從底部流到上部,其底部的冷卻油不存在滯留的問題,能防止降溫量較大的冷卻油下沉,降溫量較小的冷卻油上浮,避免冷卻油上下分層,從而提高冷卻油與冷卻器的熱交換效率。相對于現有技術的技術效果:現有技術中的軸承,熱交換油的循環(huán)通過油泵驅動。本發(fā)明所述的油道平衡式軸承,設置有帶油腔,熱交換油無需采用液泵驅動,能實現自驅動熱交換油的循環(huán)?,F有技術中的軸承,推力瓦與推力盤間的冷卻油直接通過油泵從推力瓦的外徑側壓入,該種方式結構簡單,但由于受到離心力的阻礙,其冷卻油較難壓入到推力瓦的內徑側,容易導致推力瓦內徑側高溫燒瓦。本發(fā)明所述的油道平衡式軸承,設置有甩油腔,并將甩油腔設置在正推力瓦的內徑側,其冷卻油由內向外流動,甩油腔內的冷卻油可同時受到油壓壓強和離心力的驅動作用,正推力瓦與正推力盤之間的油膜的流速是常規(guī)結構方式流速的三至五倍,能較大程度的降低推力瓦的溫度?,F有技術中的軸承,其支撐瓦滑動摩擦面的油膜流速較小,油膜的吸熱速率較低,導致滑動摩擦面和油膜溫度偏高,容易燒瓦。本發(fā)明所述的油道平衡式軸承,所述注油槽與排油槽的間距較小,其滑動摩擦面內油膜流速能得到較大程度地增大,滑動摩擦面和油膜的溫度能維持較低的水平。現有技術中的軸承,其支撐瓦內側的注油槽設計在頂部,并需對支撐瓦內側進行刮瓦處理,用于生成儲油小凹點,改善潤滑,由于其支撐瓦內的冷卻油是從注油槽通過主軸旋轉帶入滑動摩擦面的儲油小凹點,其冷卻油的帶入量較少,冷卻油交換速率低,造成支撐瓦底部區(qū)域熱交換速率較小;且由于刮瓦的標準一般是每平方厘米有兩到三個接觸點,其刮瓦過程較為費時費工;另外,由于現有的排油孔普遍是設計在支撐瓦的一端,導致支撐瓦的另一端油路不通,其支撐瓦的兩端存在較大的溫差,容易導致支撐瓦形變,并導致磨瓦的現象。本發(fā)明所述的油道平衡式軸承,其支撐瓦內側面均勻分布有注油槽,且在兩端設置有排油槽;該種結構方式,可省去刮瓦過程,其相鄰兩注油槽間能形成較厚的油膜,潤滑效果好,摩擦面摩擦產熱小,且其摩擦面的冷卻油流速較快,能較快地從兩端的排油槽排出,具有較高的熱交換效率,支撐瓦體兩端溫度能保持平衡狀態(tài),摩擦面內冷卻油的油溫能維持較低水平,同時,該結構對冷卻水的需求量較少?,F有技術中的軸承,經人工刮瓦后,刮瓦品質存在較大差異,刮瓦品質差的瓦面,其觸點的面積和儲油點的深度均存在較大的分布差異,導致其支撐瓦滑動摩擦面存在油膜厚度不均、以及油膜流速不均的問題,滑動摩擦面存在高溫點,容易產生雜質,造成摩擦系數不穩(wěn)定。本發(fā)明所述的軸承,其支撐瓦滑動摩擦面采用機械打磨的光面,并均勻分布注油槽,油膜厚度以及油膜流速較均勻,無特別的高溫點?,F有技術中的軸承,其用于冷卻油熱交換的第二油腔為單腔形式,油道路徑短,不便于擴充,無法進行后期熱效率改造。本發(fā)明所述的軸承,其第二油腔包含至少兩個分腔,該結構可根據熱效率要求匹配適當數量的冷卻器,便于電站的后期熱效率改造,并且冷卻器能被通用;且能較大程度增長冷卻油流道路徑,并便于將冷卻油流道與冷卻器內水流流道設計成對流形式,能較大程度增大冷卻器的熱交換效率。現有技術中的軸承,其瓦座具有較大的厚度,重量大,不易散熱,不便于安裝和拆卸。本發(fā)明所述的軸承通過設置環(huán)形散熱槽,支撐瓦的兩端部溫度通過徑向槽面?zhèn)鲗У降谝挥颓唬欣跍p小支撐瓦的兩端與中部的溫差,同時也較大程度地減小了瓦座的重量。本發(fā)明的優(yōu)點是:本發(fā)明所述的油道平衡式軸承,可降低油溫和軸瓦溫度達8-20℃,具有較高的熱交換效率,油溫可控制在38-45℃,軸承能保持良好的潤滑效果,維持軸瓦摩擦系數穩(wěn)定,軸承摩擦產熱小,冷卻器供水量少,能有效避免油溫過高導致的發(fā)電機報警停機,能有效避免軸瓦和冷卻油溫度過高而導致磨瓦或燒瓦的現象。附圖說明此處所說明的附圖用來提供對本發(fā)明的進一步理解,構成本申請的一部分,本發(fā)明的示意性實施例及其說明用于解釋本發(fā)明,并不構成對本發(fā)明的不當限定。在附圖中:圖1為現有的軸承的結構示意圖;圖2為現有冷卻器a7的結構示意圖;圖3為現有邊環(huán)流道隔板a72的結構示意圖;圖4為現有中心流道隔板a73的結構示意圖;圖5為本發(fā)明實施例一中整體側邊剖視結構示意圖;圖6為本發(fā)明實施例一中正推力盤51橫截面結構示意圖;圖7為本發(fā)明實施例一中A-A截面示意圖;圖8為本發(fā)明實施例一中軸承座1俯視結構示意圖;圖9為本發(fā)明實施例一中支撐瓦41結構示意圖;圖10為本發(fā)明實施例一中正推力瓦42結構示意圖;圖11為本發(fā)明實施例一中支撐瓦41軸向剖視結構示意圖;圖12為本發(fā)明實施例一中支撐瓦41中柱油槽截面剖視結構示意圖;圖13為本發(fā)明實施例一中支撐瓦41中排油槽截面剖視結構示意圖;圖14為本發(fā)明實施例一中帶油罩9截面剖視結構示意圖;圖15為本發(fā)明實施例一中冷卻器8和分腔73的垂直截面結構示意圖;圖16為本發(fā)明實施例一中冷卻器8和分腔73的水平截面結構示意圖;圖17為本發(fā)明實施例一中頂孔流道隔板83的結構示意圖;圖18為本發(fā)明實施例一中底孔流道隔板82的結構示意圖;圖19為本發(fā)明實施例二中支撐瓦41結構示意圖;圖20為本發(fā)明實施例三中支撐瓦41軸向剖視結構示意圖;圖21為本發(fā)明實施例五中支撐瓦軸向剖視結構示意圖;圖22為本發(fā)明實施例六中正推力盤51軸向剖視結構示意圖;圖23為本發(fā)明實施例六中正推力盤51徑向剖視結構示意圖;圖24為本發(fā)明實施例八中整體側邊剖視結構示意圖;圖25為本發(fā)明實施例八中第一流量調節(jié)閥915結構示意圖;圖26為本發(fā)明實施例九中第一流量調節(jié)閥915結構示意圖;圖27為本發(fā)明實施例十中整體側邊剖視結構示意圖;圖中:a1為軸承座,a2為軸承蓋,a3為軸瓦,a31為冷卻油槽,a32為注油孔,a33為排油孔,a4為油泵,a5為第一油腔,a6為第二油腔,a61為進油道,a62為出油道,a7為冷卻器,a71為冷卻銅管,a72為邊環(huán)流道隔板,a73為中心流道隔板,a74為邊環(huán)流道,a75為中心流道;1為軸承座,2為軸承蓋,3為瓦座,31為甩油腔,32為第一環(huán)形儲油腔,33為第二環(huán)形儲油腔,34為固定螺絲,41為支撐瓦,41a為上支撐瓦,41b為下支撐瓦,411為注油槽,412為排油槽,413為注油孔,414為排油孔,42為正推力瓦,42a為扇形瓦體,421為推力接觸面,422為甩油槽,43為反推力瓦,51為正推力盤,511為帶油面,512為帶油槽,513為葉片,52為反推力盤,6為第一油腔,7為第二油腔,71為熱油進油口,72為冷油出油口,73為分腔,8為冷卻器,81為冷卻管,82為底孔流道隔板,83為頂孔流道隔板,84為連接法蘭,821為第一通道孔,831為第二通道孔,c1為穿孔,9為帶油罩,91為帶油腔,911為高壓出油口,912為抽油口,913為第一油道,914為第二油道,915為第一流量調節(jié)閥,916為第一流量調節(jié)閥,s1為第一密封滑槽,s2為第二密封滑槽,10為主軸,f11為閥座,f12為流孔,f13為閥體,f14為彈性部件,f15為進液端,f16為出液端,f17為液流道,f18為閥腔,f181為腔底端,f182為腔口端。具體實施方式下面可以參照附圖1以及文字內容理解本發(fā)明的內容以及本發(fā)明與現有技術之間的區(qū)別點。下文通過附圖以及列舉本發(fā)明的一些可選實施例的方式,對本發(fā)明的技術方案(包括優(yōu)選技術方案)做進一步的詳細描述。需要說明的是:本實施例中的任何技術特征、任何技術方案均是多種可選的技術特征或可選的技術方案中的一種或幾種,為了描述簡潔的需要本文件中無法窮舉本發(fā)明的所有可替代的技術特征以及可替代的技術方案,也不便于每個技術特征的實施方式均強調其為可選的多種實施方式之一,所以本領域技術人員應該知曉:可以將本發(fā)明提供的任意技術手段進行替換或將本發(fā)明提供的任意兩個或更多個技術手段或技術特征互相進行組合而得到新的技術方案。本實施例內的任何技術特征以及任何技術方案均不限制本發(fā)明的保護范圍,本發(fā)明的保護范圍應該包括本領域技術人員不付出創(chuàng)造性勞動所能想到的任何替代技術方案以及本領域技術人員將本發(fā)明提供的任意兩個或更多個技術手段或技術特征互相進行組合而得到的新的技術方案。需要說明的是,以下描述中的“前側”、“后側”、“上部”、“下部”或“中部”的方位描述,是參照圖的方位描述,其方位描述只是為了更清楚地描述實施方式,并非實現本發(fā)明的絕對方位,不限制本發(fā)明的保護范圍。實施例一一種油道平衡式軸承,如圖5、圖6和圖7所示,包括軸承座1、軸承蓋2、瓦座3、支撐瓦41、正推力瓦42、反推力瓦43、正推力盤51、反推力盤52、第一油腔6、第二油腔7、冷卻器8和帶油罩9;所述軸承蓋2用于蓋合在軸承座1上方,所述瓦座3固定在軸承座1上,支撐瓦41固定在所述瓦座3的內徑側,所述瓦座3的軸向兩端分別為前端和后端,所述正推力瓦42固定在瓦座3的前端,所述反推力瓦43固定在瓦座3的后端,正推力盤51貼合在正推力瓦42的前端,反推力瓦43貼合在反推力瓦43的后端,正推力盤51和反推力盤52同軸固定在主軸10;所述支撐瓦41內徑側中部設有注油槽411,支撐瓦41內徑側軸向兩端設有排油槽412,所述注油槽411設有徑向貫通支撐瓦41的注油孔413,所述正推力瓦42的內徑側與瓦座3間的環(huán)形間隙空腔為甩油腔31;所述第一油腔6為軸承蓋2與軸承座1蓋合形成的密封腔;所述第二油腔7為設置在軸承座1下部的腔體,所述第二油腔7位于第一油腔6下方,所述第二油腔7包含熱油進油口71和冷油出油口72;所述冷卻器8設置在第二油腔7內;所述帶油罩9設置在正推力盤51的外徑側;所述正推力盤51的徑向外側壁為帶油面511,所述帶油罩9與帶油面511之間形成帶油腔91,所述帶油腔91呈環(huán)形,帶油腔91內設有擋油片92,所述擋油片92的一端固定在所述帶油罩9的內壁上,所述擋油片92的另一端滑動接觸帶油面511;所述帶油腔91的頂部設有高壓出油口911,所述帶油腔91的底部設有抽油口912;所述排油槽412與第一油腔6連通,第一油腔6通過熱油進油口71連通所述第二油腔7,所述帶油腔91的抽油口912連通第二油腔7的冷油出油口72,所述帶油腔91的高壓出油口911分兩路油道分別連通注油槽411和甩油腔31。作為上述實施方式的進一步具體說明,如圖5所示,所述瓦座3的內徑側中部設有第一環(huán)形儲油腔32,瓦座3前端外徑側設有第二環(huán)形儲油腔33,第一環(huán)形儲油腔32通過注油孔413與注油槽411連通,第二環(huán)形儲油腔33連通甩油腔31,第一環(huán)形儲油腔32和第二環(huán)形儲油腔33共同連通所述帶油腔91的高壓出油口911。作為上述實施方式的進一步具體說明,如圖8所示,所述瓦座3通過三組固定螺絲34固定在軸承座1上。采用該種固定方式,能有效防止瓦座3發(fā)生翹動。作為上述實施方式的進一步具體說明,如圖9所示,所述支撐瓦41為分立式瓦體,包括上支撐瓦41a和下支撐瓦41b。作為上述實施方式的進一步具體說明,如圖10所示,所述正推力瓦42為分立式瓦體,包括至少兩個環(huán)形分布的扇形瓦體42a,所述扇形瓦體42a的前側面為推力接觸面421,相鄰扇形瓦體42a之間的間隙為甩油槽422。作為上述實施方式的進一步具體說明,如圖11、圖12和圖13所示,所述注油槽411沿支撐瓦41的軸向方向開設,所述注油槽411的軸向寬度小于支撐瓦41的寬度。所述支撐瓦41的內側面包含四條注油槽411,所述注油槽411沿軸向方向開設,所述注油槽411均勻環(huán)形分布在支撐瓦41的內側面。所述排油槽412環(huán)繞支撐瓦41開設;所述排油槽412設置有排油孔414,排油孔414連通第一油腔6。所述排油槽412設有至少兩個排油孔414,排油孔414均勻環(huán)形分布。作為上述實施方式的進一步具體說明,如圖14所示,所述帶油面511設有用于密封的第一密封滑槽s1,所述帶油罩9的后側端通過第一密封滑槽s1與所述帶油面511密封接觸,主軸10設有第二密封滑槽s2,帶油罩9的前側端通過第二密封滑槽s2與主軸密封接觸。作為上述實施方式的進一步具體說明,所述熱油進油口71和冷油出油口72均位于第二油腔7的邊端部。作為上述實施方式的進一步具體說明,如圖15和圖16所示,所述第二油腔7包含八個分腔73,所述各分腔73串聯(lián)連通,各個分腔73內安裝有冷卻器8,所述各冷卻器8的流道通過串聯(lián)連通,所述各冷卻器8內的液流方向與各分腔73內油流方向相反;所述冷卻器8包括冷卻管81、底孔流道隔板82和頂孔流道隔板83,所述冷卻管81的兩端分別連接有連接法蘭84;所述底孔流道隔板82和頂孔流道隔板83垂直于冷卻管81,所述所述底孔流道隔板82和頂孔流道隔板83間隔分布,如圖17和圖18所示,所述底孔流道隔板82的底部設有第一通道孔821,所述頂孔流道隔板83的頂部設有第二通道孔831,所述底孔流道隔板82和頂孔流道隔板83的板面均分布有用于穿插冷卻管81的穿孔c1;所述冷卻器8包含多根冷卻管81,各冷卻管81并聯(lián),各冷卻管81的進水端共同連接一個連接法蘭84,各冷卻管81的出水端共同連接到另一個連接法蘭84;所述冷卻器8中的底孔流道隔板82和頂孔流道隔板83的總數為三片。采用上述實施例實施方式,用于在軸承的支撐瓦41、正推力瓦42和油溫測試中,如下表2所示,運行三小時后,支撐瓦41溫度趨于穩(wěn)定在44℃以內,支撐瓦41內的油溫趨于穩(wěn)定在38℃左右;正推力瓦42溫度趨于穩(wěn)定在41℃以內,正推力瓦42內的油溫趨于穩(wěn)定在36℃左右;相對于現有常規(guī)的軸承,其軸瓦可降低達14℃,油溫可降低達19℃。支撐瓦編號12345油溫初始溫度(℃)26.526.326.426.526.726.21h(℃)32.332.732.531.831.932.52h(℃)40.341.340.641.242.237.63h(℃)41.742.441.942.543.138.1正推力瓦編號12345油溫初始溫度(℃)26.626.426.526.726.626.31h(℃)30.731.130.431.330.830.62h(℃)37.938.238.838.939.335.83h(℃)39.340.139.240.840.536.2表2實施例二與實施例一不同之處在于:如圖19所示,所述支撐瓦41的內側面包含至少兩條注油槽411,所述注油槽411螺旋分布在支撐瓦41的內側面。采用常規(guī)的油槽結構,其遠離油槽區(qū)域容易出現油膜斷裂,油膜斷裂帶的滑動摩擦產熱大,導熱速度慢,容易造成燒瓦;該種方式能有效防止軸瓦與軸體間油膜的斷裂。采用上述實施例實施方式,用于在軸承的支撐瓦41和油溫測試中,運行三小時后,支撐瓦41溫度趨于穩(wěn)定在44.5℃以內,油溫趨于穩(wěn)定在35℃左右。實施例三與實施例一不同之處在于:如圖20所示,所述排油槽412包括第一排油槽412a和第二排油槽412b,第一排油槽412a和第二排油槽412b分別位于注油槽411的兩端,所述第一排油槽412a與注油槽411的間距為30mm,所述第二排油槽412b與注油槽411的間距為30mm,所述第一排油槽412a設有排油孔414,所述第一排油槽412a通過排油孔414與第一油腔6連通,所述第二排油槽412b為半開放槽,直接與第一油腔6連通。采用上述實施例實施方式,用于在軸承的支撐瓦41和油溫測試中,運行三小時后,支撐瓦41溫度趨于穩(wěn)定在44.5℃以內,油溫趨于穩(wěn)定在36.5℃左右。實施例四與實施例三不同之處在于:所述排油槽412包括第一排油槽412a和第二排油槽412b,第一排油槽412a和第二排油槽412b分別位于注油槽411的兩端,所述第一排油槽412a與注油槽411的間距為15mm,所述第二排油槽412b與注油槽411的間距為15mm,所述第一排油槽412a設有排油孔414,所述第一排油槽412a通過排油孔414與第一油腔6連通,所述第二排油槽412b為半開放槽,直接與第一油腔6連通。采用上述實施例實施方式,用于在軸承的支撐瓦41和油溫測試中,運行三小時后,支撐瓦41溫度趨于穩(wěn)定在44℃以內,油溫趨于穩(wěn)定在35.5℃左右。實施例五與實施例一不同之處在于:如圖21所示,所述排油槽412包括第一排油槽412a和第二排油槽412b,第一排油槽412a和第二排油槽412b分別位于注油槽411的兩端,所述第一排油槽412a與注油槽411的間距為0mm,也即第一排油槽412a與注油槽411直接聯(lián)通,所述第二排油槽412b與注油槽411的間距為0mm,也即第二排油槽412b與注油槽411直接聯(lián)通,所述第一排油槽412a設有排油孔414,所述第一排油槽412a通過排油孔414與第一油腔6連通,所述第二排油槽412b為半開放槽,直接與第一油腔6連通。采用上述實施例實施方式,用于在軸承的支撐瓦41和油溫測試中,運行三小時后,支撐瓦41溫度趨于穩(wěn)定在46.5℃以內,油溫趨于穩(wěn)定在33.5℃左右。實施例六與實施例一不同之處在于:如圖22和圖23所示,所述帶油面511設有環(huán)形的帶油槽512,所述帶油槽512中環(huán)形分布有葉片513。采取該種結構,能提高高壓出油口911的油壓,從而增大冷卻油的循環(huán)流速;在油溫測試中,油溫趨于穩(wěn)定時的溫度。采用上述實施例實施方式,用于在軸承的支撐瓦41和油溫測試中,運行三小時后,支撐瓦41溫度趨于穩(wěn)定在43.5℃以內,油溫趨于穩(wěn)定在36.5℃左右。實施例七與實施例一不同之處在于:所述第二油腔7包含兩個水平并列的分腔73,所述各分腔73串聯(lián)連通,各個分腔73內安裝有冷卻器8,所述各冷卻器8的流道通過串聯(lián)連通。所述各冷卻器8的液流方向與各分腔73內冷卻油液流方向相同。所述冷卻器8包含多根冷卻管81,各冷卻管81并聯(lián),各冷卻管81的進水端共同連接一個連接法蘭84,各冷卻管81的出水端共同連接到另一個連接法蘭84;所述冷卻器8中的底孔流道隔板82和頂孔流道隔板83的總數為八片。采用上述實施例實施方式,用于在軸承的支撐瓦41和油溫測試中,運行三小時后,支撐瓦41溫度趨于穩(wěn)定在48.5℃以內,油溫趨于穩(wěn)定在41℃左右。實施例八與實施例一不同之處在于:如圖24所示,所述高壓出油口911與注油槽411的連通油道為第一油道913,用于對支撐瓦41滑動接觸面的冷卻,所述高壓出油口911與甩油腔31的連通油道為第二油道914,所述第一油道913和第二油道914中分別設有用于穩(wěn)定流量的第一流量調節(jié)閥915與第二流量調節(jié)閥916。由于第一油道913的連接終端和第二油道914的連接終端具有不同的油阻,且其油阻受溫度影響較大,當油阻差異發(fā)生變化時,容易導致第一油道913和第二油道914的流量發(fā)生變化,出現少油或斷油的現象;采用該結構,能有效防止其中的一個油道斷油或流速減小較大,從而有效防止燒瓦,保持較高的熱交換效率。作為上述實施方式的進一步具體說明,如圖25所示,所述第一流量調節(jié)閥915與第二流量調節(jié)閥916具有相同結構,所述第一流量調節(jié)閥915包括閥座f11、流孔f12、閥體f13和彈性部件f14,流孔f12貫穿閥座f11,流孔f12包括進液端流孔f15和出液端f16,閥體f13設置在出液端f16,閥體f13通過彈性部件f14連接在閥座f11上,閥體f13與出液端f16之間為液流道f17。采用該結構,根據伯努利效應,其液流道f17的寬度隨流速的增大而變小,從而實現自動平衡調節(jié),使第一油道913和第二油道914均能保持穩(wěn)定的流速,避免第一油道913與第二油道914中冷卻油分流不穩(wěn)定,避免因第一油道913或第二油道914的流量過小而燒瓦。采用上述實施例實施方式,用于在軸承的支撐瓦41、正推力瓦42和油溫測試中,運行三小時后,支撐瓦41溫度趨于穩(wěn)定在42.5℃以內,支撐瓦41內的油溫趨于穩(wěn)定在37℃左右;正推力瓦42溫度趨于穩(wěn)定在42℃以內,正推力瓦42內的油溫趨于穩(wěn)定在36.5℃左右。實施例九與實施例八不同之處在于:如圖26所示,所述第一流量調節(jié)閥915與第二流量調節(jié)閥916具有相同結構,所述第一流量調節(jié)閥915包括閥座f11、流孔f12、閥體f13和彈性部件f14,所述流孔f12貫穿閥座f11,所述閥座f11中部設有閥腔f18,閥腔f18與流孔f12垂直,閥腔f18底部連通流孔f12,閥腔f18的底部端為腔底端f181,閥腔f18的開口端為腔口端f182,閥體f13設置在閥腔f18內,所述彈性部件f14的一端固定連接在腔口端f182,另一端連接閥體f13;所述腔底端f181呈球面狀,所述閥體f13呈球狀,所述腔底端f181與閥體f13之間為液流道f17。采用該結構,根據伯努利效應,其液流道f17的寬度隨流速的增大而變小,從而實現自動平衡調節(jié),使第一油道913和第二油道914均能保持穩(wěn)定的流速,避免第一油道913與第二油道914中冷卻油分流不穩(wěn)定,避免因第一油道913或第二油道914的流量過小而燒瓦。采用上述實施例實施方式,用于在軸承的支撐瓦41、正推力瓦42和油溫測試中,運行三小時后,支撐瓦41溫度趨于穩(wěn)定在42℃以內,支撐瓦41內的油溫趨于穩(wěn)定在36.5℃左右;正推力瓦42溫度趨于穩(wěn)定在41.5℃以內,正推力瓦42內的油溫趨于穩(wěn)定在36.5℃左右。實施例十與實施例一不同之處在于:如圖27所示,所述瓦座3外徑側設有環(huán)形散熱槽35,所述環(huán)形散熱槽35內設有軸向支撐件36,所述軸向支撐件36的兩端分別連接環(huán)形散熱槽35的兩端,所述環(huán)形散熱槽35內還設有徑向散熱片37。上述本發(fā)明所公開的任意技術方案除另有聲明外,如果其公開了數值范圍,那么公開的數值范圍均為優(yōu)選的數值范圍,任何本領域的技術人員應該理解:優(yōu)選的數值范圍僅僅是諸多可實施的數值中技術效果比較明顯或具有代表性的數值。由于數值較多,無法窮舉,所以本發(fā)明才公開部分數值以舉例說明本發(fā)明的技術方案,并且,上述列舉的數值不應構成對本發(fā)明創(chuàng)造保護范圍的限制。如果本文中使用了“第一”、“第二”等詞語來限定零部件的話,本領域技術人員應該知曉:“第一”、“第二”的使用僅僅是為了便于描述上對零部件進行區(qū)別如沒有另行聲明外,上述詞語并沒有特殊的含義。另外,上述本發(fā)明公開的任意技術方案中所應用的用于表示位置關系或形狀的術語除另有聲明外其含義包括與其近似、類似或接近的狀態(tài)或形狀。本發(fā)明提供的任意部件既可以是由多個單獨的組成部分組裝而成,也可以為一體成形工藝制造出來的單獨部件。最后應當說明的是:以上實施例僅用以說明本發(fā)明的技術方案而非對其限制;盡管參照較佳實施例對本發(fā)明進行了詳細的說明,所屬領域的普通技術人員應當理解:依然可以對本發(fā)明的具體實施方式進行修改或者對部分技術特征進行等同替換;而不脫離本發(fā)明技術方案的精神,其均應涵蓋在本發(fā)明請求保護的技術方案范圍當中。當前第1頁1 2 3