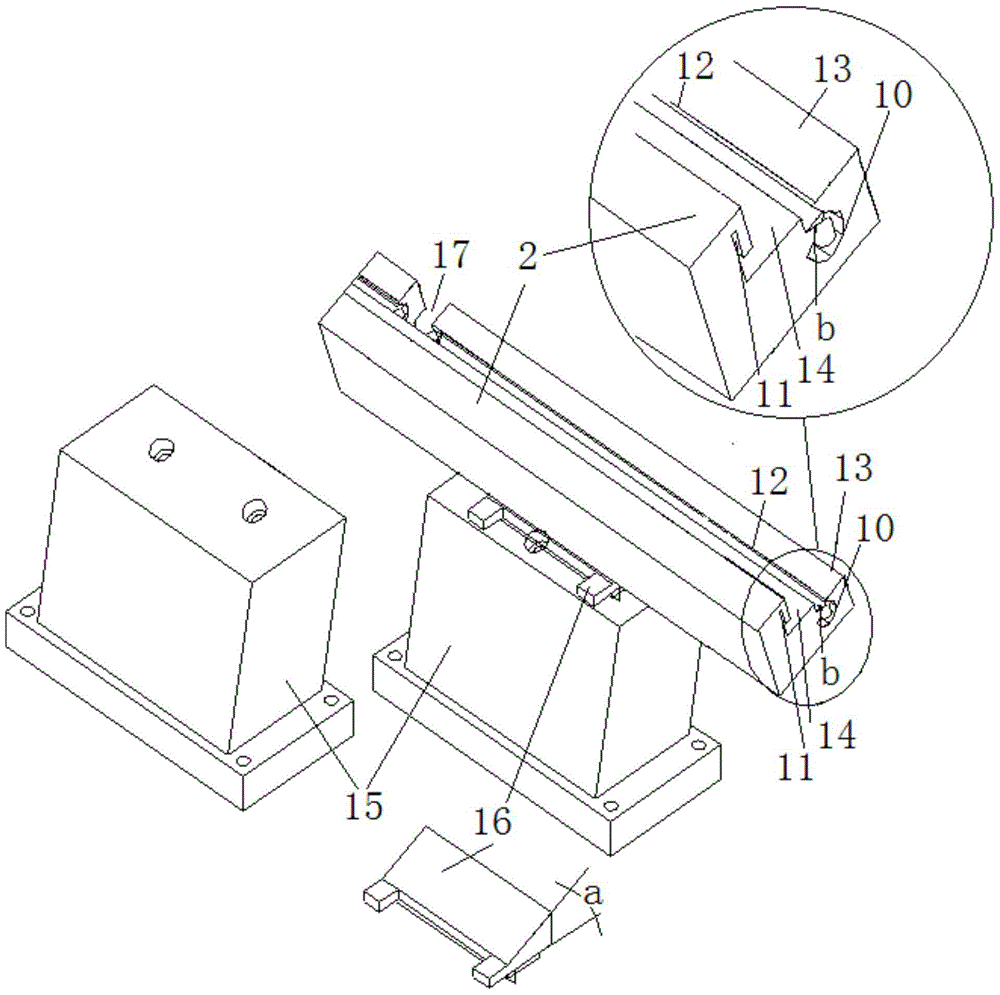
本發(fā)明屬于低壓電器加工設(shè)備技術(shù)領(lǐng)域,涉及一種小型斷路器線圈支架加工檢測系統(tǒng)。
背景技術(shù):支架作為靜觸頭支撐件,與線圈是斷路器過電流脫扣器中的關(guān)鍵核心部件,目前在線圈與支架的焊接過程中,由于線圈支架形狀的不規(guī)則,僅采用手工操作及簡單的定位夾具,手工調(diào)整夾緊螺釘,手動夾緊支架與弧角后將夾具中的產(chǎn)品送入焊接位置,焊接完后將產(chǎn)品從焊接位置取出,并手工松開夾緊螺釘,將焊接成品放入檢具中,對其支架端面到弧角上觸點中心面的高度尺寸,利用夾具百分表進(jìn)行人工全檢,檢測尺寸是否合格,合格后再重復(fù)前面工序,進(jìn)行下一個產(chǎn)品的焊接循環(huán),不合格則進(jìn)行返修處理。由于支架端面到弧角上觸點中心面的高度尺寸,是影響觸頭四大主要結(jié)構(gòu)參數(shù)(開距、超行程、觸頭壓力、接觸電阻)的關(guān)鍵尺寸,測量和焊接加工效率低、勞動強(qiáng)度大,加工質(zhì)量不一致,可靠性差外,該工序目前手工加工技術(shù)存在以下缺點:1)熟練工人的培養(yǎng)周期長:培訓(xùn)專職點焊工周期較長,一般需要2個月的培訓(xùn);2)單工位效率偏低:焊接件較小,形狀不規(guī)則,焊件的固定和尺寸檢測方面,耗時較多;3)手工操作產(chǎn)品的可靠性差,員工勞動強(qiáng)度大,作業(yè)環(huán)境差,需要人員和設(shè)備多,工序多,工序間隔時間長,占用場地大,生產(chǎn)效率低成本高。4)焊接一致性較差:如圖6所示的焊接成型尺寸7.5±0.1mm以及斜角20°±1°難以控制,手工操作難以控制焊接時間等條件。這種制作過程中,存在關(guān)鍵的性能尺寸、裝配尺寸難以完全保證,使斷路器的質(zhì)量經(jīng)常波動大,支架弧角與塑殼的卡位、線圈支架與靜觸頭組焊中心和前后偏移、偏移錯位,脫焊,難以裝配等質(zhì)量問題,經(jīng)常引發(fā)斷路器的超程、溫升等性能指標(biāo)大幅波動,甚至不合格。因此,對于U型帶斜角架的線圈支架與C型帶斜角架的靜觸頭組焊加工及焊接件的檢測,由于其零件形狀的復(fù)雜和不規(guī)則,焊接尺寸和角度要求高,目前為止,本行業(yè)一直采用手動操作手工全檢測的工藝技術(shù),未見有開發(fā)成功的用于U型帶斜角架的線圈支架與C型帶斜角架自動化焊接的設(shè)備。
技術(shù)實現(xiàn)要素:本發(fā)明的目的是提供一種小型斷路器線圈支架加工檢測系統(tǒng),解決了現(xiàn)有技術(shù)中沒有自動加工檢測設(shè)備,采用手工作業(yè)和人工檢測尺寸,產(chǎn)品質(zhì)量不可靠,工作效率低,制作成本高的問題。本發(fā)明所采用的技術(shù)方案是,一種小型斷路器線圈支架加工檢測系統(tǒng),包括料道部分,沿料道部分設(shè)置有電極組件和送料機(jī)構(gòu)、料道部分末端設(shè)置有推料機(jī)構(gòu)和檢測機(jī)構(gòu),各個部分均支撐在工作臺上,所述的料道部分的結(jié)構(gòu)是,在工作臺上固定安裝有平振,在平振的上端面固定有支撐板,在支撐板的斜面上固定有復(fù)合料道;復(fù)合料道的橫截面近似為L型,復(fù)合料道的最右端為進(jìn)料端,復(fù)合料道的長邊固定在支撐板斜面上,該長邊上表面設(shè)置有兩層臺階,即靠內(nèi)側(cè)的高臺階與靠外側(cè)的低臺階,復(fù)合料道的短邊縱向開有倒置的深槽,深槽的槽口垂直對向高臺階,在低臺階靠近高臺階的位置縱向開有C型槽,C型槽截面形狀與觸頭支架的形狀一致,C型槽與低臺階表面相通,C型槽朝向高臺階的口沿設(shè)置有高棱邊,高棱邊位置高于高臺階;復(fù)合料道的最左端設(shè)置有出料槽,作為出料端,在復(fù)合料道的出料槽一端靠里開有缺口。本發(fā)明的小型斷路器線圈支架加工檢測系統(tǒng),其特征還在于:出料槽的結(jié)構(gòu)是,包括與復(fù)合料道下斜面對接的底板,底板左端安裝有側(cè)立板,在側(cè)立板下部開有通槽,在底板低位安裝有下立板,下立板開有矩形孔。缺口是從低臺階外沿直至高臺階外沿切出的U型通透空間,該部位的C型槽和低臺階被切除通透,缺口的開口尺寸與一個線圈支架的寬度尺寸相同。低臺階與高臺階的夾角b為20°,或者說高棱邊與高臺階的夾角b為20°。推料機(jī)構(gòu)的結(jié)構(gòu)是,包括固定在工作臺上的三角支撐板,在三角支撐板上傾斜安裝有滑臺氣缸,滑臺氣缸的滑桿上固定有推料板,推料板前端設(shè)置為L型槽口,該推料板前端穿過矩形孔與線圈支架被推的側(cè)面形狀對應(yīng)。檢測機(jī)構(gòu)的結(jié)構(gòu)是,包括設(shè)置在工作臺上的U型支撐架,在U型支撐架的外側(cè)立板上設(shè)置有CCD攝像機(jī),在U型支撐架的內(nèi)側(cè)立板上設(shè)置有傘狀的聚光燈,CCD攝像機(jī)的前端與聚光燈的后端同心等高設(shè)置,CCD攝像機(jī)與計算機(jī)連接。送料機(jī)構(gòu)的結(jié)構(gòu)是,包括運(yùn)動控制組件和壓緊松開組件兩部分。運(yùn)動控制組件結(jié)構(gòu)是,包括支撐架,在支撐架背面固定有雙滑桿氣缸,雙滑桿氣缸傳動連接有L型滑板;在支撐架上端面的前端固定安裝有L型板,L型板緊鄰雙限位螺釘?shù)墓潭ò?;L型板水平方向設(shè)置有限位螺釘,限位螺釘固定端套裝在L型板中。壓緊松開組件包括上壓板、L型雙槽板和下壓板,其中上壓板包括厚板和薄板一體水平相接,厚板中水平開有雙螺紋孔,薄板前端設(shè)置有雙臺階,上部臺階稱為臺階板,下部臺階稱為壓舌,厚板后端橫向固定有后端橫板,后端橫板中部開有側(cè)開口,側(cè)開口中連接有壓緊氣缸,壓緊氣缸缸體固定在L型滑板上;L型雙槽板的底板上表面設(shè)置有底槽,L型雙槽板的立板內(nèi)側(cè)面設(shè)置有淺槽,并且在L型雙槽板的立板外側(cè)面開有雙通孔;下壓板后端厚板上設(shè)有兩過孔,通過該兩過孔將下壓板固定在L型滑板外立面,前端薄板設(shè)有上棱邊和下棱邊的型面,下壓板前端設(shè)置有卡位槽,卡位槽上端露出開口,開口前端設(shè)有高臺階板,并且高臺階板上表面低于上壓板的壓舌的臺階高度;下壓板的下棱邊卡裝在L型雙槽板的底槽中,上壓板的厚板卡裝在L型雙槽板的淺槽中;厚板的雙螺紋孔和L型雙槽板的雙通孔通過兩組螺釘對應(yīng)連接。電極組件設(shè)置在與線圈支架與觸頭支架搭接端面的垂直方向,電極組件包括上電極和下電極,下電極為固定電極,上電極是移動電極。支撐板的上表面為斜面,該斜面的斜角a為20°。本發(fā)明的有益效果是,替代現(xiàn)有的手工加工方式,一次完成自動上料、分料、定位、夾緊、自動焊接、自動檢測,實現(xiàn)合格品和不合格品的自動分選,實現(xiàn)高速、方便、準(zhǔn)確對線圈支架與觸頭組焊接成型的自動加工與檢測,工作環(huán)境改善、人員操作危險性降低、焊接質(zhì)量穩(wěn)定,成本降低;操作夾夾具和檢具尺寸控制精度高,合格率高,使得小型斷路器觸頭和線圈單元的裝配標(biāo)準(zhǔn),電流承載能力、觸頭合分的同步性、極限分?jǐn)嗄芰褪褂脡勖⒊?、溫升、影響動熱穩(wěn)定性及使用的安全和性能均明顯提高。附圖說明圖1是本發(fā)明加工檢測系統(tǒng)的結(jié)構(gòu)示意圖;圖2是本發(fā)明中的復(fù)合料道2的爆炸示意圖;圖3是本發(fā)明中的電極組件1在焊接狀態(tài)位置示意圖;圖4是本發(fā)明中的送料機(jī)構(gòu)5的爆炸示意圖一;圖5是本發(fā)明中的送料機(jī)構(gòu)5的爆炸示意圖二;圖6是本發(fā)明焊接好的焊接件7的結(jié)構(gòu)示意圖。圖中,1.電極組件,2.復(fù)合料道,3.出口通道,4.推料機(jī)構(gòu),5.送料機(jī)構(gòu),6.檢測機(jī)構(gòu),7.焊接件,10.C型槽,11.深槽,12.高棱邊,13.低臺階,14.高臺階,15.平振,16.支撐板,17.缺口,18.出料槽,19.通槽,20.矩形孔,21.滑臺氣缸,22.推料板,23.三角支撐板,24.U型支撐架,25.CCD攝像機(jī),26.聚光燈,27.支撐架,28.雙滑桿氣缸,29.L型板,30.壓緊氣缸,31.L型滑板,32.限位螺釘,33.L型端板,34.雙限位螺釘,35.上壓板,36.L型雙槽板,37.下壓板,38.下棱邊,39.卡位槽,40.高臺階板,41.上棱邊,42.壓舌,43.薄板,44.厚板,45.雙螺紋孔,46.側(cè)開口,47.后端橫板,48.底槽,49.淺槽,50.雙通孔,51.臺階板,70.觸頭支架,71.線圈支架,72.上電極,73.下電極,74.伸板,75.觸板,a表示支撐板16的上表面斜角;b表示低臺階13和高臺階14的夾角。具體實施方式下面結(jié)合附圖和具體實施方式對本發(fā)明進(jìn)行詳細(xì)說明。以下文本描述中的上下左右位置均以附圖中的顯示為基準(zhǔn),實際裝配結(jié)構(gòu)空間位置以此類推。參照圖1,本發(fā)明的結(jié)構(gòu)是,包括料道部分,沿料道部分設(shè)置有電極組件1和送料機(jī)構(gòu)5、料道部分末端設(shè)置有推料機(jī)構(gòu)4和檢測機(jī)構(gòu)6,各個部分均支撐在工作臺上,參照圖2,料道部分的結(jié)構(gòu)是,在工作臺上固定安裝有平振15,在平振15的上端面固定有支撐板16,支撐板16的上表面為斜面,該斜面的斜角a為20°,在支撐板16的斜面上固定有復(fù)合料道2;復(fù)合料道2的橫截面近似為L型,復(fù)合料道2的最右端為進(jìn)料端,復(fù)合料道2的長邊固定在支撐板16斜面上,該長邊上表面設(shè)置有兩層臺階,即靠內(nèi)側(cè)的高臺階14與靠外側(cè)的低臺階13,復(fù)合料道2的短邊縱向開有倒置的深槽11,深槽11的槽口垂直對向高臺階14,在低臺階13靠近高臺階14的位置縱向開有C型槽10,C型槽10截面形狀與觸頭支架70的(彎鉤)形狀一致,C型槽10與低臺階13表面相通,C型槽10朝向高臺階14的口沿設(shè)置有高棱邊12,高棱邊12位置高于高臺階14;復(fù)合料道2的最左端設(shè)置有出料槽18,作為出料端,出料槽18的結(jié)構(gòu)是,包括與復(fù)合料道2下斜面對接的底板,底板左端安裝有側(cè)立板,在側(cè)立板下部開有通槽19,通槽19用于外側(cè)的CCD攝像機(jī)25檢測焊接線圈支架71與觸頭支架70的成型尺寸,在底板低位安裝有下立板,下立板開有矩形孔20;出料槽18的兩立板所圍成的槽用于放置線圈支架71與觸頭支架70的焊接件7;在復(fù)合料道2的出料槽18一端靠里開有缺口17,缺口17是從低臺階13外沿直至高臺階14外沿切出的U型通透空間,該部位的C型槽10和低臺階13被切除通透,缺口17的開口尺寸與一個線圈支架71的寬度尺寸相同。深槽11和高臺階14配合用于振送和支撐線圈支架71的底面和里面一個立板,低臺階13用于懸掛線圈支架71的焊接所用的搭接端面,高棱邊12一方面對線圈支架71的伸板74進(jìn)行支撐,另一方面對觸頭支架70的頂板進(jìn)行限位,保證觸頭支架70的觸板75豎直。低臺階13與高臺階14的夾角b為20°,或者說高棱邊12與高臺階14的夾角b為20°,保證線圈支架71與觸頭支架70的搭接面處于水平狀態(tài),高楞邊12的底邊與高臺階14底邊的高度差大于等于線圈支架71與觸頭支架70兩搭接端面的厚度之和,出料端的C型槽10的間隙大于觸頭支架70的外廓,便于線圈支架71與觸頭支架70焊接后焊接件快速出料。參照圖1,推料機(jī)構(gòu)4的結(jié)構(gòu)是,包括固定在工作臺上的三角支撐板23,在三角支撐板23上傾斜安裝有滑臺氣缸21,滑臺氣缸21的滑桿上固定有推料板22,推料板22前端設(shè)置為L型槽口,該推料板22前端穿過矩形孔20與線圈支架71被推的側(cè)面形狀對應(yīng)(吻合),并且矩形孔20能夠?qū)崿F(xiàn)卡位擋位功能。參照圖1,檢測機(jī)構(gòu)6的結(jié)構(gòu)是,包括設(shè)置在工作臺上的U型支撐架24,在U型支撐架24的外側(cè)立板上設(shè)置有CCD攝像機(jī)25,在U型支撐架24的內(nèi)側(cè)立板上設(shè)置有傘狀的聚光燈26,CCD攝像機(jī)25的前端與聚光燈26的后端同心等高設(shè)置,并通過出料槽18的通槽19正對觸頭支架70上觸板75的基準(zhǔn)面與線圈支架71的側(cè)面進(jìn)行攝像,得到實測尺寸,CCD攝像機(jī)25與計算機(jī)連接,將實測尺寸與檢驗標(biāo)準(zhǔn)尺寸7.5±0.1mm比對(見圖6),判斷焊接件7合格或不合格,便于下一步分別處理。參照圖3,電極組件1設(shè)置在與線圈支架71與觸頭支架70搭接端面的垂直方向,電極組件1包括上電極72和下電極73,下電極73為固定電極,上電極72是移動電極,即由氣缸控制下移,(氣缸在各圖中均未顯示),將線圈支架71的伸板74垂直對壓在下電極73上支撐的觸頭支架70的頂板上。參照圖4、圖5,送料機(jī)構(gòu)5的結(jié)構(gòu)是,包括運(yùn)動控制組件和壓緊松開組件兩部分,運(yùn)動控制組件結(jié)構(gòu)是,包括支撐架27,在支撐架27背面固定有雙滑桿氣缸28,雙滑桿氣缸28傳動連接有L型滑板31,L型滑板31的上端豎直方向設(shè)置雙限位螺釘34用于調(diào)整厚板44的運(yùn)動高度(雙限位螺釘34固定端套裝在L型滑板31中);在支撐架27上端面的前端固定安裝有L型板29,L型板29緊鄰雙限位螺釘34的固定板;L型板29水平方向設(shè)置有限位螺釘32,限位螺釘32固定端套裝在L型板29中,雙滑桿氣缸28上的雙滑桿與L型端板33固定連接,限位螺釘32用于對L型端板33運(yùn)動限位,也就限定了L型滑板31的向上移動位置;壓緊松開組件包括上壓板35、L型雙槽板36和下壓板37,其中上壓板35包括厚板44和薄板43一體水平相接,厚板44中水平開有雙螺紋孔45,薄板43前端設(shè)置有雙臺階,上部臺階稱為臺階板51,下部臺階稱為壓舌42,厚板44后端橫向固定有后端橫板47,后端橫板47中部開有側(cè)開口46,側(cè)開口46中連接有壓緊氣缸30,壓緊氣缸30缸體固定在L型滑板31上;L型雙槽板36的(短邊)底板上表面設(shè)置有底槽48,L型雙槽板36的(長邊)立板內(nèi)側(cè)面設(shè)置有淺槽49,并且在L型雙槽板36的立板外側(cè)面開有雙通孔50;下壓板37后端厚板上設(shè)有兩過孔,通過該兩過孔將下壓板37固定在L型滑板31外立面,實現(xiàn)雙滑桿氣缸28控制下壓板37的上下移動,前端薄板設(shè)有上棱邊41和下棱邊38的型面,下壓板37前端設(shè)置有卡位槽39,卡位槽39上端露出開口,開口前端設(shè)有高臺階板40,高臺階板40的高度至少為觸頭支架70搭接端面厚度2倍,并且高臺階板40上表面低于上壓板35的壓舌42的臺階高度(方便與上壓板35與下壓板37的運(yùn)動);下壓板37的下棱邊38卡裝在L型雙槽板36的底槽48中,上壓板35的厚板44卡裝在L型雙槽板36的淺槽49中;厚板44的雙螺紋孔45和L型雙槽板36的雙通孔50通過兩組螺釘對應(yīng)連接,將上壓板35與L型雙槽板36固定為一體;壓緊氣缸30帶動上壓板35和L型雙槽板36同步沿下壓板37縱向移動,一方面使上壓板35的壓舌42對下壓板37的卡位槽39實現(xiàn)打開或關(guān)閉,實現(xiàn)對觸頭支架70的壓緊或?qū)С黾皩?dǎo)入;另一方面上壓板35的臺階板51對線圈支架71的側(cè)面實現(xiàn)壓緊或松開。本發(fā)明的工作原理是,復(fù)合料道2的右端分別與線圈支架71與觸頭支架70的儲料分選輸送振盤連接(圖中未表達(dá)儲料分選輸送振盤),實現(xiàn)線圈支架71與觸頭支架70在復(fù)合料道2中的同時連續(xù)進(jìn)料;高棱邊12的高度大于線圈支架71與觸頭支架70兩搭接端面的厚度之和,適合在觸頭支架70沿C型槽10振動輸送時,線圈支架71的伸板74沿低臺階13表面同步振送,C型槽10將觸頭支架70振送到復(fù)合料道2缺口17,高臺階14同步振送的線圈支架71同時到達(dá)復(fù)合料道2缺口17,此時觸頭支架70的頂板剛好位于線圈支架71的伸板74下方(頂板和伸板74上下有間隙,但不接觸);然后,依靠送料機(jī)構(gòu)5的雙滑桿氣缸28上頂(雙滑桿氣缸28上L型板29上面的兩螺釘限位),使觸頭支架70的頂板與線圈支架71的伸板74底部搭接(處于水平位置)等待電極組件1垂直對壓焊接完成后,壓緊氣缸30帶動上壓板35的臺階板51和壓舌42后退松開線圈支架71和觸頭支架70,滑軌氣缸21下行復(fù)位,線圈支架71與觸頭支架70焊后的焊接件7繼續(xù)依靠高臺階14和深槽11振送到復(fù)合料道2左端的出料槽18(以此類推將焊接組件推到出料槽18),依次循環(huán)重復(fù)以上工作循環(huán)。當(dāng)線圈支架71與觸頭支架70搭接端面位于復(fù)合料道2的缺口17中時,觸頭支架70由設(shè)在復(fù)合料道2后端的C型槽10振送到卡位槽39支撐,觸頭支架70由設(shè)置在缺口17后方的送料機(jī)構(gòu)5夾緊;線圈支架71由高臺階14及深槽11限位;在缺口17中完成焊接的焊接件7繼續(xù)由平振15振送到復(fù)合料道2末端連接的出料槽18,出料槽18垂直復(fù)合料道2,出料槽18通過出口通道3連接有料箱實現(xiàn)產(chǎn)品的收集,與出料槽18對應(yīng)設(shè)置的推料機(jī)構(gòu)4通過矩形孔20將焊接成品推入出口通道3;出料槽18的左端外側(cè)設(shè)置檢測機(jī)構(gòu)6,檢測機(jī)構(gòu)6通過出料槽18內(nèi)的通槽19對焊接件7的焊接尺寸實施檢測。出口通道3的下方布置人字型通道分別分流合格品和不合格品,人字型通道人字接點上裝有翻料板,電腦根據(jù)檢測機(jī)構(gòu)6的結(jié)果,判斷焊接尺寸的合格與不合格,由安裝在人字通道外的旋轉(zhuǎn)汽缸控制開閉接合格品箱子和不合格品箱子的對應(yīng)通道。上述的所有電氣部件均與控制系統(tǒng)連接,協(xié)調(diào)一致的實現(xiàn)各個部分的操作功能。本發(fā)明的工作過程是,手工將線圈支架71與觸頭支架70放入各自的振盤,并分別自動分選振送進(jìn)入平振15支撐的復(fù)合料道2進(jìn)料端,觸頭支架70由平振15自動振送存滿復(fù)合料道2中的C型槽10,線圈支架71由平振15自動振送存滿復(fù)合料道2中的深槽11及高臺階14,當(dāng)送料機(jī)構(gòu)5的下壓板37在原位時,且上壓板35處于松開下壓板37的高臺階板40時,觸頭支架70從C型槽10振送入下壓板37的卡位槽39,線圈支架71從深槽11及高臺階14振入缺口17中,線圈支架71位于觸頭支架70的上方;然后,雙滑桿氣缸28帶動送料機(jī)構(gòu)5上升到指定位置后(此時線圈支架71與觸頭支架70搭接端面接觸對齊),壓緊氣缸30啟動帶動上壓板35的壓舌42,對卡位槽39中的觸頭支架70和壓舌42實施定位壓緊,同時臺階板51對線圈支架71立板實施定位壓緊;接著,設(shè)置在電極組件1的上電極72垂直對壓在下電極73上的線圈支架71與觸頭支架70搭接端面指定面,實施焊接;焊接完成后,壓緊氣缸30后退松開觸頭支架70和壓舌42及線圈支架71立板,復(fù)合料道2前端的深槽11和高臺階14中的線圈支架71,再振送到復(fù)合料道2的左端的深槽11和高臺階14及C型槽10中(與此同時雙滑桿氣缸28帶動送料機(jī)構(gòu)5下降回到原位位置,下壓板37在原位時重復(fù)線圈支架71與觸頭支架70的進(jìn)料動作,重復(fù)前面的壓緊、焊接、松開、復(fù)位的循環(huán));缺口17焊接完成的焊接件7由平振15振送到復(fù)合料道2末端連接的出料槽18中,出料槽18外側(cè)設(shè)置的檢測機(jī)構(gòu)6通過利用CCD攝像機(jī)25對焊接件7進(jìn)行攝像,其圖像通過計算機(jī)進(jìn)行智能測算,依據(jù)檢驗標(biāo)準(zhǔn)判斷合格與不良,推料機(jī)構(gòu)4通過出料槽18的矩形孔20將焊接成品推入出口通道3,分料分別進(jìn)入良品或不良的料箱中(電腦根據(jù)檢測機(jī)構(gòu)6的結(jié)果,判斷焊接尺寸的合格與不合格,對應(yīng)處理合格品與不合格品咋分別處理收集),與出口通道3連接的料箱實現(xiàn)焊接成品的收集。由于采用上述結(jié)構(gòu),本發(fā)明徹底實現(xiàn)了小型斷路器線圈及支架的加工檢測,采用自動焊接和自動檢測焊接尺寸替代了手工操作焊接和手工檢測,上述實施例只是對本發(fā)明的說明,而不是對本發(fā)明的限制,任何不超出本發(fā)明實質(zhì)精神范圍內(nèi)的結(jié)構(gòu)設(shè)置,均落入本發(fā)明的保護(hù)范圍之內(nèi)。