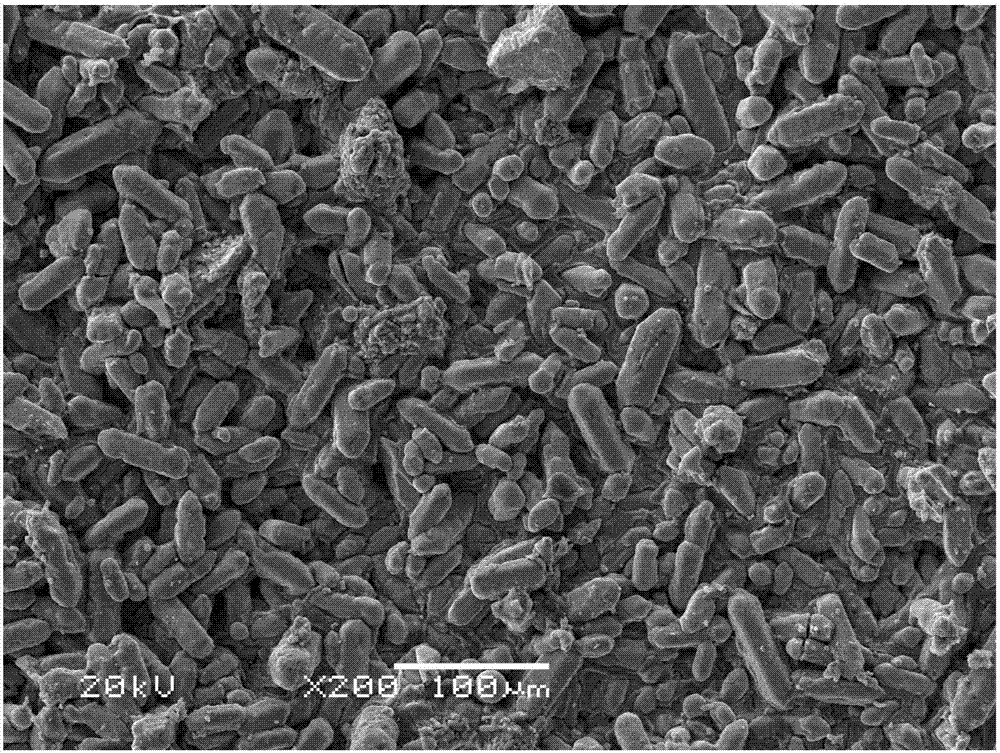
本發(fā)明涉及涂層
技術領域:
,尤其涉及一種鉬基復合涂層及其制備方法。
背景技術:
:鉬屬于難熔金屬,具有高熔點和高強度的優(yōu)點,應用于航空航天、化工、冶金、醫(yī)療器械等多個領域。但鉬及其合金在高溫有氧環(huán)境下會發(fā)生劇烈的破壞性氧化而失效破壞,嚴重限制了鉬及其合金在高溫環(huán)境下的使用。在鉬、鉬合金表面涂覆抗氧化涂層,可以最大程度保有合金力學性能,同時大幅提高鉬合金抗氧化溫度,是一種經(jīng)濟、有效的防護手段。目前,高溫抗氧化涂層包括硅化物涂層、鋁化物涂層以及耐熱合金涂層等,均能一定程度提高鉬的工作溫度和抗氧化性能。申請?zhí)枮?01110383828.6的中國專利介紹了三步原位反應合成法生成涂層的方法,首先在高溫下對基材通氮氣使其氮化,再經(jīng)過高溫包埋滲硅,最后再高溫包埋滲硼,制得一種Mo-N-Si-B系的抗氧化涂層。申請?zhí)枮?01310180081.3的中國專利先對預處理的鉬基材表面進行滲鎢處理,然后進行氮化處理,最后高溫滲硅,得到一種Mo-W-N-Si系硅化物涂層。申請?zhí)枮?01410733680.8的中國專利介紹了一種主要組成為:Al為15~20wt%,Ni為3~5wt%,W為2~3wt%,MoSi2為1.5~3wt%,Cr為0.5~0.8wt%,余量為Si的抗氧化涂層材料,采用真空料漿法制備。申請?zhí)枮?01410208597.9的中國專利公開了一種Hf-Y氧化物涂層,使用氯氧化鉿與氯化釔以適量的比例混合溶于正丙醇溶液,刷涂在鉬基材表面,然后置于馬弗爐中在400℃左右焙燒,經(jīng)15~30次刷涂-燒結后形成涂層。申請?zhí)枮?01510441949.X的中國專利公開了采用摻鉀鉬作為發(fā)熱體基體材料,對發(fā)熱體基體表面包埋于硅10~30wt%,硼、鋁、鉻、鎢粉末中的至少一種粉末5~10wt%,余量為氧化鋁的反應粉末中進行元素擴散反應制備出涂層鉬發(fā)熱體。此外,賈中華等使用料漿熔燒法,在鉬表面熔燒制備硅化物防護涂層。肖來榮等通過真空燒結法,在鉬表面燒結出MoSi2-ZrB2涂層。湯德志使用磁控濺射技術,在鉬表面制備硅鋁涂層。汪異采用大氣等離子噴涂法和原位化學氣相沉積法在鉬表面制備二硅化鉬涂層和二硅化鉬/硼化鉬復合涂層。馬小沖等采用料漿法在鉬基體上制備ZrO2和SnO2玻璃基抗氧化涂層。此外,王亮兵使用雙輝離子鍍法在鉬基體上制備Ir涂層。上述專利與文獻所記載的涂層材料中,包埋法制備涂層對過程要求苛刻,控制難度大;磁控濺射對設備要求較高,經(jīng)濟性差;刷涂-燒結法簡單易行,容易控制,但制備的Hf-Y氧化物涂層對基體的保護時間短。雙輝離子鍍法目前仍處于研究階段,所制備的Ir涂層成本昂貴,且目前測試壽命僅有60s(2000℃)。如上所述,目前仍缺乏一種可以使用在1600℃以上,具有長壽命、低成本、便于實施和控制的涂層材料及其制備方法。技術實現(xiàn)要素:本發(fā)明解決的技術問題在于提供一種鉬基復合涂層,本申請?zhí)峁┑膹秃贤繉邮广f基材的工作溫度與抗氧化效果大幅度提高。有鑒于此,本申請?zhí)峁┝艘环N鉬基復合涂層,包括:鉬基材,復合于鉬基材表面的硅化物底層;復合于所述硅化物底層表面的硅酸鹽外層;所述硅化物底層由以下組分制備得到:5~12wt%的W,2~7wt%的Cr,0.3~6wt%的B、B2O3或B4C,0.5~7wt%的HfO2;下述組分中的至少一種:1~5wt%的Mo,0.5~1.5wt%的Ta,1~4wt%的Fe,0.5~1.5wt%的S,0.2~0.5wt%的TiB2,1~5wt%的SiC,1~5wt%的ZrO2或Zr,1~5wt%的MoSi2;余量的Si;所述硅酸鹽外層由以下組分制備得到:3~18wt%的Mo,0.5~5wt%的W,0.5~3wt%的Nb,1~5wt%的HfO2;下述組分中的至少一種:0.2~2wt%的Ta或其氧化物,0.2~1.5wt%的V,0.7~1.5wt%的La或其氧化物,0.3~2.2wt%的Y或其氧化物,0.2~1wt%的BaO,0.7~4wt%的Ge或其氧化物,1~7wt%的Zr或其氧化物,1~5wt%的B或其氧化物;余量的Si。優(yōu)選的,所述硅化物底層中,所述Cr的含量為5.5~7wt%;所述B、B2O3或B4C的含量為3~6wt%;所述HfO2的含量為5.5~7wt%。優(yōu)選的,所述硅酸鹽外層中,所述Mo的含量為16~18wt%,所述W的含量為3.5~4wt%。優(yōu)選的,所述復合涂層的厚度為80~130μm。優(yōu)選的,鉬基材的材質為純鉬或鉬合金。本申請還提供了所述的鉬基復合涂層的制備方法,包括以下步驟:A),將權利要求1中硅化物底層中的各種組分混合,得到第一抗氧化材料;將權利要求1中硅酸鹽外層中的各種組分混合,得到第二抗氧化材料;將所述第一抗氧化材料、有機溶劑、粘結劑與反應催化劑混合,球磨后得到第一涂層漿料;將所述第二抗氧化材料、有機溶劑、粘結劑與反應催化劑混合,球磨后得到第二涂層漿料;B),將所述第一涂層漿料涂覆于預處理后的鉬基材表面,熔燒后保溫,得到硅化物底層;C),將第二涂層漿料涂覆于所述硅化物底層表面,熔燒后保溫,得到硅酸鹽外層。優(yōu)選的,得到第一涂層漿料的步驟中,所述有機溶劑為乙酸乙酯或無水乙醇,所述粘結劑為硝基清漆或聚乙二醇,所述反應催化劑為鹵化物;得到第二涂層漿料的步驟中,所述有機溶劑為乙酸乙酯或無水乙醇,所述粘結劑為硝基清漆或聚乙二醇,所述反應催化劑為鹵化物。優(yōu)選的,所述第一抗氧化材料與所述有機溶劑的體積比為1:(1~2),所述第一抗氧化材料與所述硝基清漆的質量比為1:(0.5~2),所述第一抗氧化材料與所述聚乙二醇的質量比為1:(0.01~0.06),所述第一抗氧化材料與所述鹵化物的質量比為1:(0.003~0.03);所述第二抗氧化材料與所述有機溶劑的體積比為1:(1~2),所述第二抗氧化材料與所述硝基清漆的質量比為1:(0.5~2),所述第二抗氧化材料與所述聚乙二醇的質量比為1:(0.01~0.06),所述第二抗氧化材料與所述鹵化物的質量比為1:(0.003~0.03)。優(yōu)選的,步驟B)中,所述熔燒的溫度為1300~1550℃,真空度大于0.1Pa;保溫時間為15~60min。優(yōu)選的,步驟C)中,所述熔燒的溫度為1350~1550℃,真空度大于0.1Pa,保溫時間為15~60min。本申請?zhí)峁┝艘环N鉬基復合涂層,所述鉬基復合涂層中包括硅化合物底層與硅酸鹽外層,本申請通過采用兩組配比不同的涂層材料,得到了高熔點、高致密度的陶瓷-玻璃相外層,其使鉬基材工作溫度與抗氧化效果大幅度提升;進一步的,硅化物底層與硅酸鹽外層的不同成分使形成的涂層的熱脹系數(shù)呈現(xiàn)梯度變化,使硅化物底層與鉬基材產生了冶金結合,確保涂層與基材結合牢固,使涂層在急冷急熱環(huán)境下工作。實驗結果表明,本申請的復合涂層可在1700℃下提供100h以上的抗氧化防護,在1800~室溫熱震性能可達1000次以上。附圖說明圖1為本發(fā)明復合涂層制備過程流程圖;圖2為本發(fā)明實施例1制備的復合涂層的表面微觀形貌圖;圖3為本發(fā)明實施例1制備的復合涂層的截面微觀形貌圖;圖4為本發(fā)明實施例1制備的復合涂層在1800℃靜態(tài)測試50h后涂層的EDS分析;圖5為本發(fā)明實施例1制備的復合涂層在1800℃測試50h后表面形成的陶瓷-玻璃相照片;圖6為本發(fā)明實施例3制備的復合涂層1800℃下靜態(tài)測試30h后的截面形貌照片。具體實施方式為了進一步理解本發(fā)明,下面結合實施例對本發(fā)明優(yōu)選實施方案進行描述,但是應當理解,這些描述只是為進一步說明本發(fā)明的特征和優(yōu)點,而不是對本發(fā)明權利要求的限制。本發(fā)明實施例公開了一種鉬基復合涂層,包括:鉬基材,復合于鉬基材表面的硅化物底層;復合于所述硅化物底層表面的硅酸鹽外層;所述硅化物底層由以下組分制備得到:5~12wt%的W,2~7wt%的Cr,0.3~6wt%的B、B2O3或B4C,0.5~7wt%的HfO2;下述組分中的至少一種:1~5wt%的Mo,0.5~1.5wt%的Ta,1~4wt%的Fe,0.5~1.5wt%的S,0.2~0.5wt%的TiB2,1~5wt%的SiC,1~5wt%的ZrO2或Zr,1~5wt%的MoSi2;余量的Si;所述硅酸鹽外層由以下組分制備得到:3~18wt%的Mo,0.5~5wt%的W,0.5~3wt%的Nb,1~5wt%的HfO2;下述組分中的至少一種:0.2~2wt%的Ta或其氧化物,0.2~1.5wt%的V,0.7~1.5wt%的La或其氧化物,0.3~2.2wt%的Y或其氧化物,0.2~1wt%的BaO,0.7~4wt%的Ge或其氧化物,1~7wt%的Zr或其氧化物,1~5wt%的B或其氧化物;余量的Si。本申請?zhí)峁┝艘环N鉬基復合涂層,其包括依次復合的硅酸鹽外層、硅化物底層與鉬基材,本申請通過調整鉬基材外層與底層組分及其含量,使底層與鉬基材能夠形成良好的冶金結合,保證復合涂層不脫落,同時形成的復合涂層形成高熔點、高致密的陶瓷-玻璃相外層,使鉬基材的工作溫度與抗氧化效果大幅度提升。在形成的硅化物底層中,所述W的含量為5~12wt%,在某些實施例中,所述W的含量為7~12wt%,示例的,所述W的含量為7wt%、7.8wt%、8.1wt%、8.5wt%、9.0wt%、9.8wt%、10.0wt%、10.7wt%、11.2wt%或11.6wt%。所述Cr的含量為2~7wt%,在實施例中,所述Cr的含量為5.5~7wt%,示例的,所述Cr的含量可為6.0wt%、6.2wt%、6.5wt%、6.8wt%或7wt%。所述B、B2O3或B4C的含量為0.3~6wt%,在實施例中,所述B、B2O3或B4C的含量為2.5~6wt%,示例的,所述B、B2O3或B4C的含量為2.5wt%、3.2wt%、3.7wt%、4.3wt%、4.7wt%、5.0wt%、5.4wt%或6wt%。所述HfO2的含量為0.5~7wt%,在實施例中,所述HfO2的含量為2~7wt%,示例的,所述HfO2的含量為2.6wt%、3.0wt%、3.2wt%、3.8wt%、4.5wt%、5.2wt%、6.8wt%或7.0wt%。在所述硅化物底層中,所述W、Cr、B或其化合物、HfO2與Si為主要必要添加元素,除此之外,可根據(jù)具體形成的硅化物底層選擇添加1~5wt%的Mo,0.5~1.5wt%的Ta,1~4wt%的Fe,0.5~1.5wt%的S,0.2~0.5wt%的TiB2,1~5wt%的SiC,1~5wt%的ZrO2或Zr與1~5wt%的MoSi2中的至少一種。在上述元素中,可添加其中的一種組分,或添加多種組分,可根據(jù)具體的形成的硅化物底層的性質進行選擇。在具體的實施例中,所述Mo的含量為1.5~4.0wt%,更具體的,所述Mo的含量為1.8wt%、2.4wt%、3.0wt%、3.2wt%、3.5wt%或4.0wt%。在具體實施例中,所述Ta的含量為0.8wt%~1.2wt%。在具體實施例中,所述Fe的含量為1.5~3.0wt%。在具體實施例中,所述S的含量為1~1.5wt%。在具體實施例中,所述TiB2的含量為0.2wt%、0.3wt%、0.4wt%或0.5wt%。在具體實施例中,所述SiC的含量為2.5~4.0wt%,具體的,所述SiC的含量為2.8wt%、3.2wt%、3.5wt%或3.8wt%。在具體實施例中,所述ZrO2的含量為1.8~4.2wt%,具體的,所述ZrO2的含量為2.0wt%、2.2wt%、2.8wt%、3.4wt%、3.8wt%或4.0wt%。在具體實施例中,所述MoSi2的含量為1.6wt%~4.2wt%,具體的,所述MoSi2的含量為2.0wt%、2.4wt%、2.8wt%、3.4wt%或4.0wt%。涂層底層中添加了較多的活化元素,其作用是形成高硅化物,在高溫下分解形成單質硅和低硅化合物,硅元素向表層躍遷,為表層提供抗氧化元素,從而起到“儲備層”的作用;部分非金屬元素的作用是在高溫下腐蝕鉬及鉬合金基材表面,提高基材比表面積,用以提高涂層與合金的反應程度,提升涂層與合金的結合力。此外,添加了部分的強化元素或化合物,以提升涂層強度,調整涂層彈性模量,提升涂層抗熱震能力,提高涂層的環(huán)境適應能力。在形成的硅酸鹽外層中,所述Mo的含量為3~18wt%,在具體實施例中,所述Mo的含量為6~18wt%,在某些具體實施例中,所述Mo的含量為10~17wt%,具體的,所述Mo的含量為12wt%、15wt%、16.2wt%、17wt%或18wt%。所述W的含量為0.5~5wt%,在某些實施例中,所述W的含量為2~5wt%,在某些實施例中,所述W的含量為3.5~5wt%,具體的,所述W的含量為3.5wt%、3.8wt%、4.0wt%、4.2wt%或4.8wt%。所述Nb的含量為0.5~3wt%,在某些實施例中,所述Nb的含量為1~2.5wt%,具體的,所述Nb的含量為1.2wt%、1.5wt%、2.0wt%或2.2wt%。所述HfO2的含量為1~5wt%,在某些實施例中,所述HfO2的含量為1.2~3.8wt%,在某些實施例中,所述HfO2的含量為1.8~2.5wt%。在所述硅酸鹽外層中,所述W、Mo、Nb、HfO2與Si為主要必要添加元素,除此之外,可根據(jù)具體形成的硅酸鹽外層選擇添加0.2~2wt%的Ta或其氧化物,0.2~1.5wt%的V,0.7~1.5wt%的La或其氧化物,0.3~2.2wt%的Y或其氧化物,0.2~1wt%的BaO,0.7~4wt%的Ge或其氧化物,1~7wt%的Zr或其氧化物與1~5wt%的B或其氧化物中的至少一種;在上述元素中,可添加其中的一種組分,或添加多種組分,可根據(jù)具體的形成的硅酸鹽外層的性質進行選擇。在具體實施例中,所述Ta或氧化物的含量為2wt%~2.8wt%。在具體實施例中,所述V的含量為1.2~1.5wt%。在具體的實施例中,所述La或其氧化物的含量為0.8~1.5wt%,更具體的,所述La或其氧化物的含量為0.9wt%、1.2wt%、1.4wt%或1.5wt%。在具體實施例中,所述Y或其氧化物的含量為0.8~2.2wt%,具體的,所述Y或其氧化物的含量為1.0wt%、1.2wt%、1.8wt%或2.0wt%。在具體實施例中,所述BaO的含量為0.4~0.9wt%。在具體實施例中,所述Ge或其氧化物的含量為1.2~3.6wt%,在具體實施例中,所述Ge或其氧化物的含量為2.0~3.0wt%。在具體實施例中,所述Zr或其氧化物的含量為3~6.8wt%,具體的,所述ZrO2的含量為3.2wt%、4.5wt%、4.8wt%、5.6wt%、6.5wt%或6.8wt%。在具體實施例中,所述B或其氧化物的含量為1.2wt%~4.5wt%,具體的,所述B或其氧化物的含量為1.4wt%、1.6wt%、2.8wt%、3.4wt%或4.2wt%。復合涂層在大氣下遭遇高溫環(huán)境,外層升溫氧化的過程中部分金屬元素的硅化物氧化后,可以形成高熔點的金屬硅酸鹽,與SiO2形成陶瓷-玻璃相,提升面層的高溫穩(wěn)定性;部分非金屬、金屬氧化物可以降低SiO2的軟化溫度,提高面層抗熱沖擊的能力。此外,部分金屬元素的添加及硅化物的形成,起到調整面層熱膨脹系數(shù)的作用。本申請還提供了上述鉬基復合涂層的制備方法,制備流程如圖1所示,具體的,所述鉬基復合涂層的制備包括以下步驟:A),將權利要求1中硅化物底層中的各種組分混合,得到第一抗氧化材料;將權利要求1中硅酸鹽外層中的各種組分混合,得到第二抗氧化材料;將所述第一抗氧化材料、有機溶劑、粘結劑與反應催化劑混合,球磨后得到第一涂層漿料;將所述第二抗氧化材料、有機溶劑、粘結劑與反應催化劑混合,球磨后得到第二涂層漿料;B),將所述第一涂層漿料涂覆于預處理后的鉬基材表面,熔燒后保溫,得到硅化物底層;C),將第二抗氧化漿料涂覆于所述硅化物底層表面,熔燒后保溫,得到硅酸鹽外層。在制備鉬基復合涂層的過程中,本申請首先進行復合涂層中原料組分的配制,即首先將硅化物底層與硅酸鹽外層中的各種組分按照上述比例分別進行混合,分別得到第一抗氧化材料與第二抗氧化材料;再將得到的第一抗氧化材料與第二抗氧化材料均分別與有機溶劑、粘結劑、反應催化劑混合,球磨后,分別得到第一涂層漿料與第二涂層漿料。在上述過程中,所述有機溶劑作為載體,用于調整涂層漿料的粘度和流動性,從而提升漿料的涂覆均勻性,并且可實現(xiàn)快速干燥固化。所述有機溶劑優(yōu)選為無水乙醇或乙酸乙酯。所述粘結劑優(yōu)選為硝基清漆或聚乙二醇,所述反應催化劑優(yōu)選為鹵化物,具體的,所述鹵化物為NH4Cl、NaF、NaCl、KF、KCl中的一種或多種。所述第一抗氧化材料與所述有機溶劑的體積比為1:(1~2),所述第一抗氧化材料與所述硝基清漆的質量比為1:(0.5~2),優(yōu)選為1:(0.8~1.2),所述第一抗氧化材料與所述聚乙二醇的質量比為1:(0.01~0.06),所述第一抗氧化材料與所述鹵化物的質量比為1:(0.003~0.03);所述第二抗氧化材料與上述添加劑的比例與第一抗氧化材料的范圍相同,在具體實施例中,所述第一抗氧化材料與第二抗氧化材料分別與上述添加劑的比例可以相同,也可以不同,對此本申請沒有特別的限制。所述球磨的轉速為150~400r/min,球磨的時間為3~12h;在具體實施例中,在制備第一涂層漿料的過程中,所述球磨的轉速為150~300r/min,球磨的時間為8~10h,在制備第一涂層漿料的過程中,所述球磨的轉速為180~320r/min,球磨的時間為8~10h。在涂覆第一涂層漿料之前,本申請優(yōu)選將鉬基材進行了預處理,所述預處理為本領域技術人員熟知的技術手段,此處不進行特別的限制,示例的,所述預處理可以為打磨、噴砂、酸洗或真空退火。本申請所述鉬基材的材質為純鉬或鉬合金,其中,所述鉬合金為本領域技術人員熟知的鉬合金,對此本申請沒有特別的限制。按照本發(fā)明,首先將所述第一涂層漿料涂覆于鉬基材表面,熔燒后保溫,得到硅化物底層。所述熔燒的溫度為1300~1550℃,真空度大于0.1Pa;保溫時間為15~60min;在具體實施例中,所述熔燒的溫度為1350~1500℃,所述保溫時間為45~60min。在得到硅化物底層之后,本申請則在其表面涂覆所述第二抗氧化涂層漿料,熔燒后保溫,得到硅化物底層。所述熔燒的溫度為1300~1550℃,真空度大于0.1Pa;保溫時間為15~60min;在具體實施例中,所述熔燒的溫度為1350~1500℃,所述保溫時間為45~50min。在熔燒過程中,底層、外層配料中的部分金屬與硅生成固溶體,部分金屬、金屬氧化物則與硅反應生成硅化物及硅酸鹽,從而形成固溶體、硅化物以及硅酸鹽的復雜混合體。有別于Ta、Nb等金屬,同為難熔金屬的Mo與其主要硅化物MoSi2的線膨脹系數(shù)(CET)相差極大(Mo為5.2×10-6/℃,MoSi2為8.1×10-6/K),因此與Nb、Ta金屬及合金抗氧化涂層不同,鉬及鉬合金對抗氧化涂層的改性成分和結構層設計(層數(shù)、結構層厚度)要求更高,否則很容易因熱脹系數(shù)匹配失當或是成分固溶不良導致涂層出現(xiàn)開裂、剝落或者表面凸起等質量缺陷。本申請所提供的鉬及鉬合金用高溫抗氧化涂層材料及其制備方法的特點和優(yōu)勢在于:使用兩組配比不同的涂層材料,采用二次疊加熔燒的方法,制備出一種復合涂層。這種復合涂層高溫下表面可以形成高度致密化和穩(wěn)定化的復雜陶瓷-玻璃膜層,解決了鉬及鉬合金硅化物涂層普遍存在的1500℃以上的快速揮發(fā)失效問題,有效提升涂層工作溫度;同時底層、面層的不同成分設計使涂層的熱脹系數(shù)呈現(xiàn)梯度變化,解決了鉬及鉬合金傳統(tǒng)硅化物涂層因涂層主體MoSi2與基體Mo熱脹系數(shù)相差過大導致的涂層起皮、剝落和開裂等致命缺陷,有效提升涂層性能;此外,在疊加熔燒的過程中,通過調整熔燒工藝,可以實現(xiàn)面層與底層、底層與合金的輕度熱擴散,從而形成冶金級結合,提升涂層層間結構、涂層與合金間的結合力,避免涂層在冷熱交變工況下的開裂甚至剝落,進一步提升涂層的實際工作能力。為了進一步理解本發(fā)明,下面結合實施例對本發(fā)明提供的復合涂層及其制備方法進行詳細說明,本發(fā)明的保護范圍不受以下實施例的限制。實施例11)兩組高溫抗氧化材料,分別為:①W為5wt%,Cr為2wt%,B為2wt%,Ta為1.2wt%,Mo為1wt%,HfO2為2wt%,ZrO2為3wt%,SiC為2.8wt%,余量為Si;②Mo為7.2wt%,W為2.2wt%,Nb為3wt%,Y為2.2wt%,HfO2為3wt%,BaO為1wt%,Ta為2wt%,B為3wt%,余量為Si;將上述兩組材料按比例混勻,分別使用行星式球磨機研磨成不大于300目的粉料,裝入不同的容器;2)用噴砂的方法清潔鉬基材表面(設備為長空牌GS-943型吸入式干噴砂機,80目白剛玉砂),然后浸入無水乙醇浸泡30min,晾干備用;3)在第①組抗氧化材料中分別加入粉末質量80wt%的硝基清漆(浙江油漆有限公司,寶塔牌硝基清漆)和3wt%的NaF分別作為粘結劑和催化劑,再加入粉末體積2倍的乙酸乙酯作為載體,混合均勻后用剛玉珠以150r/min轉速球磨12h后制成料漿;將料漿均勻涂覆在鉬基材表面,烘干后在溫度1380℃,真空度≥0.1Pa的條件下熔燒,保溫60min,制成抗氧化涂層底層,厚度約65~80μm;4)在第②組抗氧化材料中分別加入粉末質量120wt%的硝基清漆(浙江油漆有限公司,寶塔牌硝基清漆)和2wt%的KF分別作為粘結劑和催化劑,再加入粉末體積2倍的乙酸乙酯作為載體,混合均勻后用剛玉珠以200r/min轉速球磨10h后制成料漿;將料漿均勻涂覆在抗氧化涂層底層表面,烘干后在溫度1550℃,真空度≥0.1Pa的條件下熔燒,保溫50min,制成抗氧化涂層面層,厚度約25~35μm;最終成型的復合型抗氧化涂層,整體厚度在90~120μm。圖2為本發(fā)明實施例1制備的復合涂層的表面微觀形貌圖;圖3為本發(fā)明實施例1制備的復合涂層的截面微觀形貌圖;如圖2與圖3可知,使用兩種抗氧化材料制備的鉬涂層呈典型的蜂窩狀結構,整體結構致密,顆粒彌散;涂層呈典型的復合型三層結構,面層較為疏松,底層極為致密,并與合金有一定的互擴散,從而提高了涂層與合金的結合力。5)抗氧化涂層的抗氧化能力測試方法為:鉬試樣進行1800℃高溫測試,測試方法為:使用銅電極對試樣進行通電,利用其自身電阻產生熱量使試樣升溫;使用美國Raytek公司的B17MR1SBSF型雙色集成式測溫儀(測溫范圍600~2100℃,測溫精度±15.75℃)測定試樣溫度,使用日本SHIMADEN公司的FP23溫控表控制通過試樣的電流大小進而控制溫度(±10℃),測試至試樣表面出現(xiàn)黑色斑點時,涂層失效;對失效試片進行EDS分析,儀器型號ZeissSUPRA55,結果如4所示,圖4為本發(fā)明實施例1制備的復合涂層在1800℃靜態(tài)測試50h后涂層的EDS分析;由圖4可知,抗氧化涂層1800℃靜態(tài)測試50h以后,涂層中的氧元素升高,但基材中的氧元素含量很低,證明涂層對基材起到了很好的抗氧化效果。對涂層進行1700℃、1800℃高溫抗氧化性能測試,如圖5所示,測試結果顯示,涂層在高溫下表面能生成深黑色玻璃-陶瓷相保護層,可有效阻擋氧元素的侵入,使得涂層具有良好的靜態(tài)、熱震抗氧化能力較好,結果表1所示。表1抗氧化涂層綜合性能測試數(shù)據(jù)表實施例21)兩組高溫抗氧化材料,分別為:①W為7wt%,Cr為7wt%,B2O3為2.5wt%,F(xiàn)e為3wt%,S為1wt%,Mo為5wt%,HfO2為4wt%,SiC為3wt%,MoSi2為2.8wt%,余量為Si;②Mo為12wt%,W為3.5wt%,Nb為1wt%,Y2O3為0.8wt%,HfO2為3wt%,BaO為0.7wt%,V為1.2wt%,B為1wt%,余量為Si;將上述兩組材料按比例混勻,分別使用行星式球磨機研磨成不大于300目的粉料,裝入不同的容器;2)將TZM合金(鉬鋯鈦合金)基材表面用400#砂紙打磨至表面光亮無異物附著,再用無水乙醇浸泡30min,晾干后備用;3)在第①組抗氧化材料中分別加入粉末質量150wt%的硝基清漆(浙江油漆有限公司,寶塔牌硝基清漆)和3wt%的NaF分別作為粘結劑和催化劑,再加入粉末體積2倍的乙酸乙酯作為載體,混合均勻后用剛玉珠以150r/min轉速球磨8h后制成料漿,將料漿均勻涂覆在TZM基材表面,烘干后在溫度1360℃,真空度≥0.1Pa的條件下熔燒,保溫60min,制成抗氧化涂層底層,厚度約75~85μm;4)在第②組抗氧化材料中分別加入粉末質量120wt%的硝基清漆(浙江油漆有限公司,寶塔牌硝基清漆)和3wt%的KF分別作為粘結劑和催化劑,再加入粉末體積2倍的乙酸乙酯作為載體,混合均勻后用剛玉珠以180r/min轉速球磨8h后制成料漿;將料漿均勻涂覆在抗氧化涂層底層表面,烘干后在溫度1500℃,真空度≥0.1Pa的條件下熔燒,保溫45min,制成抗氧化涂層面層,厚度約20~30μm。最終成型的復合型抗氧化涂層,整體厚度在95~115μm。實施例31)兩組高溫抗氧化材料,分別為:①W為10%wt%,Cr為4wt%,B4C為2wt%,HfO2為4wt%,Ta為1wt%,Mo為5wt%,S為1.2Wt%,TiB2為0.5wt%,ZrO2為3wt%,余量為Si;②Mo為15wt%,W為3.5wt%,Nb為0.5wt%,HfO2為5wt%,La2O3為1.2wt%,Y為1wt%,Zr2O3為7wt%,余量為Si;將上述兩組材料按比例混勻,分別使用行星式球磨機研磨成不大于300目的粉料,裝入不同的容器;2)使用干式噴砂機,使用300#白剛玉砂對鉬金屬基材進行噴砂,至表面光亮無異物附著,表面粗糙度不大于Ra6.3μm(樣板對比法),以20~30KHz頻率對試樣進行超聲波清洗,清洗時間15~20分鐘,清洗后將試片浸入無水乙醇備用。3)在第①組抗氧化材料中分別加入粉末質量5wt%的聚乙二醇和1wt%的KCl作為粘結劑和催化劑,再加入粉末體積2倍的無水乙醇作為載體,混合均勻后用剛玉珠以200r/min轉速球磨12h后制成料漿,將料漿用噴槍噴涂在鉬基材表面,噴涂厚度約為300μm,自然干燥后在溫度1500℃,真空度≥0.1Pa的條件下熔燒,保溫40min,制成抗氧化涂層底層,厚度約60~70μm;4)在第②組抗氧化材料中分別加入粉末質量5wt%的聚乙二醇和0.5wt%的KCl作為粘結劑和催化劑,再加入粉末體積2倍的無水乙醇作為載體,混合均勻后用剛玉珠以300r/min轉速球磨10h后制成料漿,將料漿用噴槍噴涂在底層涂層表面,噴涂厚度約為150μm,自然干燥后在溫度1500℃,真空度≥0.1Pa的條件下熔燒,保溫30min,制成抗氧化涂層面層,厚度約20~30μm。圖6為本發(fā)明實施例3制備的復合涂層1800℃下靜態(tài)測試30h后的截面形貌照片。表2為抗氧化復合涂層的抗氧化性能測試數(shù)據(jù)表。表2抗氧化涂層抗氧化性能測試數(shù)據(jù)表試片編號涂層厚度(μm)測試項目測試性能109871800℃靜態(tài)33h110891800℃熱震1120次111881800℃熱震1260次1161021800℃熱震1211次1171051800℃靜態(tài)30h1181071800℃熱震1151次1191041800℃靜態(tài)30h實施例41)兩組高溫抗氧化材料,分別為:①W為7wt%,Cr為5wt%,B4C為4wt%,HfO2為6wt%,Mo為3wt%,TiB2為0.5wt%,ZrO2為3wt%,MoSi2為4wt%,余量為Si;②Mo為16.2wt%,W為3.5wt%,Nb為1.2wt%,HfO2為2.5wt%,Ta為1wt%,V為1.2wt%,Y為2wt%,Ge為2.5wt%,B2O3為2wt%,ZrO2為3.2wt%,余量為Si;將上述兩組材料按比例混勻,分別使用行星式球磨機研磨成不大于300目的粉料,裝入不同的容器;2)使用240#、500#耐水砂紙對純鉬金屬基材進行打磨,至表面光亮無異物附著,表面粗糙度不大于Ra3.2μm(樣板對比),以20~30KHz頻率對試樣進行超聲波清洗,清洗時間15~20分鐘,清洗后將試片浸入無水乙醇備用。3)在第①組抗氧化材料中分別加入粉末質量3wt%的聚乙二醇和0.5wt%的NH4Cl作為粘結劑和催化劑,再加入粉末體積1.5倍的無水乙醇作為載體,混合均勻后用剛玉珠以300r/min轉速球磨8h后制成料漿,將料漿用噴槍噴涂在鉬基材表面,噴涂厚度約為300μm,自然干燥后在溫度1550℃,真空度≥0.1Pa的條件下熔燒,保溫20min,制成抗氧化涂層底層,厚度約50~60μm;4)在第②組抗氧化材料中分別加入粉末質量50wt%的硝基清漆和0.8wt%的NH4Cl作為粘結劑和催化劑,再加入粉末體積1.5倍的無水乙醇作為載體,混合均勻后用剛玉珠以300r/min轉速球磨10h后制成料漿,將料漿用噴槍噴涂在底層涂層表面,噴涂厚度約為200μm,自然干燥后在溫度1550℃,真空度≥0.1Pa的條件下熔燒,保溫20min,制成抗氧化涂層面層,厚度約30~50μm。表3為抗氧化復合涂層的抗氧化性能測試數(shù)據(jù)表。表3抗氧化涂層抗氧化性能測試數(shù)據(jù)表實施例51)兩組高溫抗氧化材料,分別為:①W為6wt%,Cr為7wt%,B2O3為3wt%,HfO2為5.5wt%,Mo為5wt%,Ta為1wt%,S為0.6wt%,ZrO2為2wt%,MoSi2為5wt%;②Mo為18wt%,W為4wt%,Nb為2wt%,HfO2為5wt%,Ta2O5為2wt%,V為1.5wt%,Y2O3為2.2wt%,Ge為3.4wt%,B為1wt%,ZrO2為5wt%;將上述兩組材料按比例混勻,分別使用行星式球磨機研磨成不大于300目的粉料,裝入不同的容器;2)使用240#、500#耐水砂紙對TZM合金基材進行打磨,至表面光亮無異物附著,表面粗糙度不大于Ra3.2μm(樣板對比),以20~30KHz頻率對試樣進行超聲波清洗,清洗時間10~20分鐘,清洗后將試片浸入無水乙醇備用。3)在第①組抗氧化材料中分別加入粉末質量6wt%的聚乙二醇和0.5wt%的NaF作為粘結劑和催化劑,再加入粉末體積2倍的乙酸乙酯作為載體,混合均勻后用剛玉珠以400r/min轉速球磨6h后制成料漿,將料漿用噴槍噴涂在鉬基材表面,噴涂厚度約為300μm,自然干燥后在溫度1530℃,真空度≥0.1Pa的條件下熔燒,保溫12min,制成抗氧化涂層底層,厚度約71~82μm;4)在第②組抗氧化材料中分別加入粉末質量6wt%的聚乙二醇和1wt%的KCl作為粘結劑和催化劑,再加入粉末體積1.5倍的無水乙醇作為載體,混合均勻后用剛玉珠以400r/min轉速球磨8h后制成料漿,將料漿用噴槍噴涂在底層涂層表面,噴涂厚度約為200μm,自然干燥后在溫度1550℃,真空度≥0.1Pa的條件下熔燒,保溫20min,制成抗氧化涂層面層,厚度約25~35μm。表4為抗氧化復合涂層的抗氧化性能測試數(shù)據(jù)表。表4抗氧化涂層抗氧化性能測試數(shù)據(jù)表試片編號涂層厚度(μm)測試項目測試性能1481091900℃靜態(tài)25min1491061700℃靜態(tài)142h1501031700℃靜態(tài)141h1511101900℃靜態(tài)15min1521011800℃熱震636次1531071800℃熱震722次1541081700℃靜態(tài)136h以上實施例的說明只是用于幫助理解本發(fā)明的方法及其核心思想。應當指出,對于本
技術領域:
的普通技術人員來說,在不脫離本發(fā)明原理的前提下,還可以對本發(fā)明進行若干改進和修飾,這些改進和修飾也落入本發(fā)明權利要求的保護范圍內。對所公開的實施例的上述說明,使本領域專業(yè)技術人員能夠實現(xiàn)或使用本發(fā)明。對這些實施例的多種修改對本領域的專業(yè)技術人員來說將是顯而易見的,本文中所定義的一般原理可以在不脫離本發(fā)明的精神或范圍的情況下,在其它實施例中實現(xiàn)。因此,本發(fā)明將不會被限制于本文所示的這些實施例,而是要符合與本文所公開的原理和新穎特點相一致的最寬的范圍。當前第1頁1 2 3