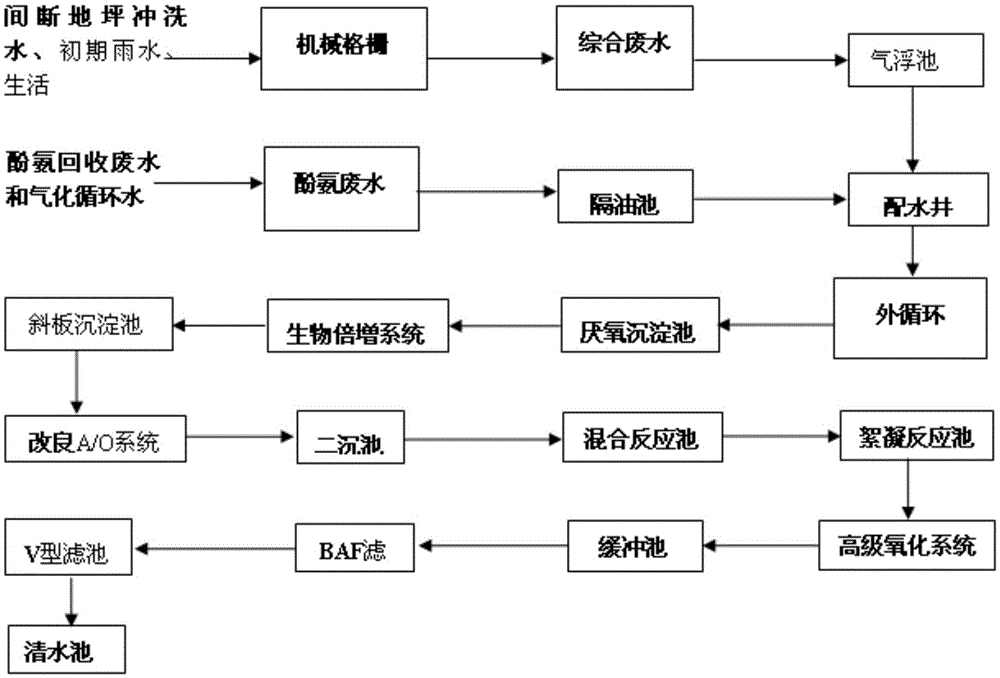
本發(fā)明涉及工業(yè)污水處理領(lǐng)域,具體涉及一種煤化工廢水的處理工藝。
背景技術(shù):
:隨著近年來能源工業(yè)的迅速發(fā)展,煤化工廢水已經(jīng)成為重要的污染源之一。煤化工行業(yè)既是用水大戶也是排污大戶,單位產(chǎn)品廢水產(chǎn)生量在1t/t以上,年產(chǎn)20萬噸的甲醇裝置每小時(shí)排放廢水達(dá)上百噸;而且廢水中含有難降解的焦油、酚等物質(zhì),成分復(fù)雜。采用一般的生化工藝很難處理,煤化工行業(yè)的廢水污染控制的難度大。但是隨著經(jīng)濟(jì)社會的可持續(xù)發(fā)展和人們對環(huán)保要求的提高,對煤化工廢水處理的要求也隨之越來越嚴(yán)格。煤化工企業(yè)廢水按照含鹽量可分為兩類:一類是有機(jī)廢水,主要來源于煤氣化工藝廢水等,其特點(diǎn)是含鹽量低、污染物以COD為主。二類是含鹽廢水,主要來源于循環(huán)水系統(tǒng)排污水、除鹽水系統(tǒng)排水、回用系統(tǒng)反滲透排放的濃鹽水等,及有機(jī)廢水處理過程添加的藥劑等,也包括生化處理后的有機(jī)廢水,其特點(diǎn)是含鹽量高,主要成分包括氨、硫酸鹽、及硫氰化物等。據(jù)調(diào)查,神華集團(tuán)某煤制天然氣項(xiàng)目補(bǔ)充新鮮水(以黃河為水源)帶入的鹽量超過整個(gè)系統(tǒng)鹽量的57%,其次是生產(chǎn)過程和水系統(tǒng)添加化學(xué)藥劑產(chǎn)生的鹽量,分別為29%和13.6%。新鮮水來源和生產(chǎn)工藝確定后,主要通過合理選擇循環(huán)冷卻系統(tǒng)的循環(huán)倍數(shù)和水處理藥劑的品種來降低廢水含鹽量,然而煤化工含鹽廢水的總含鹽量(TDS)通常在500~5000mg/L,甚至更高。煤化工企業(yè)的正常運(yùn)轉(zhuǎn)需要有環(huán)境容量足夠大的納污水體。然而,我國煤化工企業(yè)大多分布在煤炭資源豐富的西北地區(qū),這些地區(qū)水環(huán)境容量不足,甚至缺乏納污水體?!?011年中國環(huán)境狀況公報(bào)》顯示,2011年我國地表水水質(zhì)總體為輕度污染。為此一些地方也相繼頒布了嚴(yán)格的廢水排放標(biāo)準(zhǔn),黃河、淮河等水污染嚴(yán)重的敏感流域、區(qū)域和省份甚至不允許工業(yè)企業(yè)廢水排放到地表水體。國家對新建煤化工項(xiàng)目的用水和水污染物的排放也提出了嚴(yán)格的指標(biāo)要求。然而煤化工廢水的復(fù)雜性、高污染性和難降解性導(dǎo)致了采用常規(guī)處理手段很難對其進(jìn)行有效降解,目前已經(jīng)投產(chǎn)的國內(nèi)煤化工廢水處理項(xiàng)目能夠穩(wěn)定達(dá)標(biāo)排放的實(shí)例很少,絕大多數(shù)處于不穩(wěn)定運(yùn)行或故障狀態(tài),煤化工廢水處理問題已成為制約煤化工產(chǎn)業(yè)發(fā)展的瓶頸。因而,如何得到一種處理效果好和工藝穩(wěn)定性強(qiáng)的廢水處理工藝,提高水資源的重復(fù)利用率,更好實(shí)現(xiàn)節(jié)約用水,已成為行業(yè)內(nèi)的各前沿企業(yè)亟待解決的技術(shù)問題。技術(shù)實(shí)現(xiàn)要素:有鑒于此,本發(fā)明解決的技術(shù)問題在于提供一種煤化工廢水的處理工藝,使用本發(fā)明提供處理工藝,能夠更好提高水資源的重復(fù)利用率,節(jié)約用水,具有處理效果好和工藝穩(wěn)定性強(qiáng)的特點(diǎn)。本發(fā)明公開了一種煤化工廢水的處理工藝,包括以下步驟:a)將煤化工廢水中的有機(jī)廢水經(jīng)過脫氨酚處理工藝后,得到處理后廢液;b)將上述步驟得到的處理后廢液經(jīng)過生化處理工藝后,得到生化處理水;c)將步驟b)得到的生化處理水和含鹽廢水經(jīng)過提濃處理工藝后,得到回用水和高鹽廢水;d)將上述步驟得到的高鹽廢水經(jīng)過濃鹽水處理工藝后,得到含鹽物料;所述脫氨酚處理工藝包括脫酸脫氨工序、萃取工序、溶劑脫除工序、溶劑回收工序、廢液分離系統(tǒng)、溶劑貯存工序和堿液制備工序。優(yōu)選的,所述生化處理工藝依次包括預(yù)處理工序、生化處理工序和深度處理工序。優(yōu)選的,所述煤化工廢水還包括其他廢水;所述其他廢水包括地面沖洗水、雨水、氣化爐廢水、低溫甲醇洗廢水、生產(chǎn)性廢水和生活化驗(yàn)廢水中的一種或多種;所述預(yù)處理工序具體為:將處理后廢液經(jīng)過生化污泥繼續(xù)回收氨酚后,進(jìn)行配水處理;同時(shí)將上述其他廢水經(jīng)過除雜、均質(zhì)均量和除油除泥后,進(jìn)行配水處理;所述配水處理后的混合廢水進(jìn)入生化處理工序。優(yōu)選的,所述生化處理工序依次包括外循環(huán)厭氧系統(tǒng)、生物倍增系統(tǒng)、改良A/O處理工序和二沉池系統(tǒng)。優(yōu)選的,所述深度處理工序依次包括混合反應(yīng)預(yù)吸附工序、臭氧催化氧化工序、BAF曝氣生物濾池工序和濾池系統(tǒng);所述混合反應(yīng)預(yù)吸附工序?yàn)椴捎没钚怨柙逋梁吞挤鄣倪M(jìn)行吸附。優(yōu)選的,所述提濃處理工藝依次包括生化水處理工序、中水處理工序和濃水深度處理工序。優(yōu)選的,所述生化水處理工序包括活性炭處理步驟和除氟過濾步驟。優(yōu)選的,所述中水處理工序依次包括攪拌澄清步驟、多介質(zhì)過濾步驟、超濾步驟和反滲透步驟。優(yōu)選的,所述濃水深度處理工序依次包括鈉離子交換步驟、多介質(zhì)過濾步驟、超濾步驟和反滲透步驟。優(yōu)選的,所述濃鹽水處理工藝依次包括高效反滲透工序和蒸發(fā)工序;所述濃鹽水處理工藝后還包括高濃鹽水固化結(jié)晶處理工藝。本發(fā)明公開了一種煤化工廢水的處理工藝,包括以下步驟:首先將煤化工廢水中的有機(jī)廢水經(jīng)過脫氨酚處理工藝后,得到處理后廢液;然后將上述步驟得到的處理后廢液經(jīng)過生化處理工藝后,得到生化處理水;再將上述步驟得到的生化處理水和含鹽廢水經(jīng)過提濃處理工藝后,得到回用水和高鹽廢水;最后將上述步驟得到的高鹽廢水經(jīng)過濃鹽水處理工藝后,得到含鹽物料;所述脫氨酚處理工藝包括脫酸脫氨工序、萃取工序、溶劑脫除工序、溶劑回收工序、廢液分離系統(tǒng)、溶劑貯存工序和堿液制備工序。與現(xiàn)有技術(shù)相比,本發(fā)明創(chuàng)造性的選取了廢水處理工藝,構(gòu)建了由煤化工廢水無害化水與煤化工廢水資源化、減量化兩個(gè)子系統(tǒng)組成的煤化工廢水零排放系統(tǒng),是一套適用于水資源匱乏地區(qū)的煤化工廢水處理與零排放整體解決方案,并且穩(wěn)定連續(xù)運(yùn)行,本發(fā)明通過工藝創(chuàng)造性的組合與優(yōu)化,使得各工藝系統(tǒng)良好銜接與過度,尤其是各級別處理系統(tǒng)的穩(wěn)定運(yùn)行,避免了廢水在系統(tǒng)中的滯留現(xiàn)象,確保了下一級處理的正常運(yùn)轉(zhuǎn)。本發(fā)明提供的煤化工廢水處理方案,通過廢水梯級利用及重復(fù)利用,最大限度的減少了新鮮水資源的使用,能夠充分降低項(xiàng)目水耗,同時(shí)減少排污量,有效的開拓了區(qū)域水資源協(xié)同整合的新模式。附圖說明圖1為本發(fā)明脫氨酚處理工藝的出水中主要污染物指標(biāo)情況;圖2為本發(fā)明生化處理工藝的流程概圖;圖3為本發(fā)明有機(jī)廢水生化處理后出水的COD檢測情況;圖4為本發(fā)明有機(jī)廢水生化處理后出水的氨氮檢測情況;圖5為本發(fā)明生化水處理工序的工藝流程概圖;圖6為本發(fā)明中水處理工序的工藝流程概圖;圖7為本發(fā)明濃水深度處理工序的工藝流程概圖。具體實(shí)施方式為了進(jìn)一步理解本發(fā)明,下面結(jié)合實(shí)施例對本發(fā)明優(yōu)選實(shí)施方案進(jìn)行描述,但是應(yīng)當(dāng)理解,這些描述只是為了進(jìn)一步說明本發(fā)明的特征和優(yōu)點(diǎn),而不是對發(fā)明權(quán)利要求的限制。本發(fā)明所有原料,對其來源沒有特別限制,在市場上購買的或按照本領(lǐng)域技術(shù)人員熟知的常規(guī)方法制備的即可。本發(fā)明所有原料,對其純度沒有特別限制,本發(fā)明優(yōu)選采用工業(yè)純或化學(xué)純。本發(fā)明公開了一種煤化工廢水的處理工藝,包括以下步驟:a)將煤化工廢水中的有機(jī)廢水經(jīng)過脫氨酚處理工藝后,得到處理后廢液;b)將上述步驟得到的處理后廢液經(jīng)過生化處理工藝后,得到生化處理水;c)將步驟b)得到的生化處理水和含鹽廢水經(jīng)過提濃處理工藝后,得到回用水和高鹽廢水;d)將上述步驟得到的高鹽廢水經(jīng)過濃鹽水處理工藝后,得到含鹽物料;所述脫氨酚處理工藝包括脫酸脫氨工序、萃取工序、溶劑脫除工序、溶劑回收工序、廢液分離系統(tǒng)、溶劑貯存工序和堿液制備工序。本發(fā)明首先將煤化工廢水中的有機(jī)廢水經(jīng)過脫氨酚處理工藝后,得到處理后廢液。本發(fā)明所述煤化工廢水包括有機(jī)廢水和含鹽廢水,其中有機(jī)廢水是指煤制氣過程中對粗煤氣進(jìn)行冷卻洗滌產(chǎn)生的工藝廢水,該類廢水是一種有毒的高濃度含酚有機(jī)廢水,具有水量大、多元酚含量高、COD值高,難生化、凈化等特點(diǎn),煤氣化廢水處理難題已經(jīng)成為制約煤氣化發(fā)展的一個(gè)重要因素。含鹽廢水是指循環(huán)水系統(tǒng)排污水、除鹽水系統(tǒng)排水、回用系統(tǒng)反滲透排放的濃鹽水等,及有機(jī)廢水處理過程添加的藥劑等,也包括生化處理后的有機(jī)廢水,其特點(diǎn)是含鹽量高,主要成分包括氨、硫酸鹽、及硫氰化物等。本發(fā)明所述脫氨酚處理工藝優(yōu)選包括脫酸脫氨工序、萃取工序、溶劑脫除工序、溶劑回收工序、廢液分離系統(tǒng)、溶劑貯存工序和堿液制備工序。本發(fā)明對所述脫酸脫氨工序、萃取工序、溶劑脫除工序、溶劑回收工序、廢液分離系統(tǒng)、溶劑貯存工序和堿液制備工序的定義沒有特別限制,以本領(lǐng)域技術(shù)人員熟知的上述概念即可,本領(lǐng)域技術(shù)人員可以根據(jù)實(shí)際生產(chǎn)情況、水處理情況和水處理要求進(jìn)行調(diào)整。本發(fā)明所述脫氨酚處理工藝具體為,有機(jī)廢水經(jīng)過單塔脫氨、脫酸,廢水分冷、熱兩股分別從上部和中上部進(jìn)入污水汽提塔,冷進(jìn)料的目的是降低塔頂溫度,減少酸氣中的氨和水含量。汽提出的CO2、H2S等酸性氣體及少量氨、水蒸汽進(jìn)入后續(xù)處理裝置或火炬焚燒;從側(cè)線采出的氨水汽進(jìn)入三級分凝,冷凝回部分水和少量氨、CO2,富氨氣進(jìn)入氨精制工段加工成液氨。脫酸氣后的污水汽提塔的釜液冷卻到40℃左右后從上部進(jìn)入萃取塔,與萃取劑MIBK進(jìn)行逆流萃取。萃取相泵入酚塔中,精餾分離粗酚與MIBK,MIBK回用。萃取塔的萃余相加入水塔,從頂部采出溶解和夾帶的溶劑,冷凝、分相后回用。萃取劑再生流股回送至溶劑回收罐循環(huán)使用。水塔的釜液(處理后廢液)進(jìn)入后續(xù)的生化段生化處理。本發(fā)明所述脫氨酚處理工藝在回收溶劑的同時(shí)可利用側(cè)提將水中氨氣提出來,并制成稀氨水送出界區(qū),使流程更為簡化,即脫酚蒸氨在同一裝置進(jìn)行,降低了投資和運(yùn)行費(fèi)用。產(chǎn)品為粗酚和11%的氨水。本發(fā)明所述脫氨酚處理工藝中,總酚萃取效率能夠達(dá)到93%,使得廢水總酚降低到300mg/l以下,COD含量降至1500mg/l以下,使后續(xù)生化處理得以順利進(jìn)行,解決了長期困擾煤氣化廢水處理的技術(shù)難題。本發(fā)明然后將上述步驟得到的處理后廢液經(jīng)過生化處理工藝后,得到生化處理水。本發(fā)明所述生化處理工藝優(yōu)選依次包括預(yù)處理工序、生化處理工序和深度處理工序。本發(fā)明所述煤化工廢水優(yōu)選還包括其他廢水,所述其他廢水優(yōu)選包括地面沖洗水、雨水、氣化爐廢水、低溫甲醇洗廢水、生產(chǎn)性廢水和生活化驗(yàn)廢水中的一種或多種。本發(fā)明所述預(yù)處理工序優(yōu)選具體為,將處理后廢液經(jīng)過生化污泥繼續(xù)回收氨酚后,進(jìn)行配水處理;同時(shí)將上述其他廢水經(jīng)過除雜、均質(zhì)均量和除油除泥后,進(jìn)行配水處理;所述配水處理后的混合廢水進(jìn)入生化處理工序。本發(fā)明預(yù)處理工序,首先將處理后廢液經(jīng)過生化污泥繼續(xù)回收氨酚后,進(jìn)行配水處理,即送入?yún)捬跖渌{(diào)節(jié)池。本發(fā)明對所述生化污泥沒有特別限制,以本領(lǐng)域技術(shù)人員熟知的用于處理廢水的生化污泥即可,本發(fā)明優(yōu)選將后續(xù)生化處理工段產(chǎn)生的富余生物污泥返回厭氧配水調(diào)節(jié)池,形成泥床,通過污泥的混凝沉淀與水解酸化作用,消除油類物質(zhì)及懸浮物,可獲得良好的處理效果。本發(fā)明優(yōu)選同時(shí)將所述其他廢水,如地坪沖洗水、生活污水、低溫甲醇洗廢水和生活化驗(yàn)廢水等先經(jīng)過格柵進(jìn)行除雜過濾,再在廢水綜合調(diào)節(jié)池進(jìn)行水質(zhì)、水量調(diào)節(jié),然后優(yōu)選經(jīng)過刮油刮泥機(jī)處理后,最后也送入?yún)捬跖渌{(diào)節(jié)池,與之前的處理后廢液一起混合后形成混合廢水。本發(fā)明對所述生化處理工序的定義沒有特別限制,以本領(lǐng)域技術(shù)人員熟知的上述概念即可,本領(lǐng)域技術(shù)人員可以根據(jù)實(shí)際生產(chǎn)情況、水處理情況和水處理要求進(jìn)行調(diào)整和選擇。本發(fā)明所述生化處理工序具體優(yōu)選依次包括外循環(huán)厭氧系統(tǒng)、生物倍增系統(tǒng)、改良A/O處理工序和二沉池系統(tǒng)。本發(fā)明對上述具體工序和系統(tǒng)及其工藝參數(shù)沒有特別限制,以本領(lǐng)域技術(shù)人員熟知的上述工序和系統(tǒng)及其工藝參數(shù)即可,本領(lǐng)域技術(shù)人員可以根據(jù)實(shí)際生產(chǎn)情況、水處理情況和水處理要求進(jìn)行調(diào)整和選擇。本發(fā)明所述外循環(huán)厭氧系統(tǒng)、生物倍增系統(tǒng)、改良A/O處理工序和二沉池系統(tǒng)具體是指,混合廢液在外循環(huán)(EC)厭氧工藝中通過羧化、苯?;?、開環(huán)、斷鏈和產(chǎn)甲烷等五個(gè)階段完成厭氧共代謝過程從而消除多元酚,改善了酚氨回收廢水水質(zhì)的同時(shí),實(shí)現(xiàn)部分有機(jī)物的羧化和苯?;D(zhuǎn)變過程,避免多元酚向醌類物質(zhì)的轉(zhuǎn)化。并利用厭氧細(xì)菌將部分酚氨回收廢水污染物轉(zhuǎn)化為甲烷,同時(shí)將部分難降解的有機(jī)物轉(zhuǎn)為易降解的有機(jī)物,為后續(xù)好氧生物工藝降低處理難度和減輕運(yùn)行負(fù)擔(dān),是整個(gè)工藝中污染物去除的主體工藝。再經(jīng)過生物倍增系統(tǒng),即生物增濃同步脫氮工藝是投加一定量的碳粉增加污泥濃度,控制特定的水力條件、高污泥濃度、低溶解氧等參數(shù)來實(shí)現(xiàn)在低氧條件下去除有機(jī)物、氨氮短程硝化反硝化和脫氮過程相結(jié)合的工藝。該工藝是在亞硝酸鹽和氨氮同時(shí)存在的條件下,通過控制溶解氧,利用自養(yǎng)型細(xì)菌將氨和亞硝酸鹽同時(shí)去除,產(chǎn)物為氮?dú)夂蜕倭肯跛猁},由于參加反應(yīng)的微生物屬于自養(yǎng)型微生物,因此不需要碳源。另外由于該工藝只需要硝化50%左右的氨氮,硝化步驟只需要控制亞硝化階段,因此可以節(jié)約堿度約50%,節(jié)約供氧量約62.5%,低氧曝氣避免了運(yùn)行中泡沫增加的問題,是組合工藝中最主要的污染物去除工藝。再通過改良A/O工藝,本發(fā)明對所述A/O工藝沒有特別限制,以本領(lǐng)域技術(shù)人員熟知的A/O工藝即可;本發(fā)明所述改良A/O工藝,是指AOAOO,底部都有曝氣管,根據(jù)實(shí)際運(yùn)行工況可以調(diào)整曝氣AOAOO,利用多級厭氧和好氧的交替作用,進(jìn)一步去除污水中難降解的COD,以及利用多級厭氧和好氧的交替作用,利用生物水解作用提高廢水的可生化性,利用硝化菌和反硝化菌的作用,進(jìn)一步降解廢水中的氨氮。本發(fā)明所述改良A/O工藝,回流比可以根據(jù)需要隨意變動,針對酚氨回收廢水剩余氨氮和有機(jī)物的降解需要調(diào)整回流比,對氨氮消化和反硝化脫氮進(jìn)行強(qiáng)化處理,其中兼氧微生物系利用周邊地區(qū)污水處理廠污泥培養(yǎng),非常適應(yīng)本系統(tǒng)排放的有機(jī)廢水,處理效果較優(yōu)。最后經(jīng)過二沉池則是進(jìn)行再次的沉淀,從而進(jìn)一步得到分離。本發(fā)明對所述深度處理工序的定義沒有特別限制,以本領(lǐng)域技術(shù)人員熟知的上述概念即可,本領(lǐng)域技術(shù)人員可以根據(jù)實(shí)際生產(chǎn)情況、水處理情況和水處理要求進(jìn)行調(diào)整和選擇,本發(fā)明所述深度處理工序優(yōu)選依次包括混合反應(yīng)預(yù)吸附工序、臭氧催化氧化工序、BAF曝氣生物濾池工序和濾池系統(tǒng)。本發(fā)明對上述具體工序和系統(tǒng)及其工藝參數(shù)沒有特別限制,以本領(lǐng)域技術(shù)人員熟知的上述工序和系統(tǒng)及其工藝參數(shù)即可,本領(lǐng)域技術(shù)人員可以根據(jù)實(shí)際生產(chǎn)情況、水處理情況和水處理要求進(jìn)行調(diào)整和選擇。本發(fā)明所述混合反應(yīng)預(yù)吸附工序、臭氧催化氧化工序、BAF曝氣生物濾池工序和濾池系統(tǒng)具體是指,經(jīng)過上述步驟處理的混合廢水經(jīng)過混合反應(yīng)吸附工藝,通過活性硅藻土和碳粉的物理化學(xué)吸附功能,進(jìn)一步吸附去除污水中難降解的CODcr,提高水體的可生化性;吸附方式采用廊道式高效動態(tài)方式,吸附CODcr去除率在40%以上;吸附后的出水經(jīng)沉淀后進(jìn)入后續(xù)的BAF曝氣生物濾池工序或其它低負(fù)荷生物處理裝置進(jìn)行處理。再經(jīng)過臭氧催化氧化工序,該高級氧化工藝采用多項(xiàng)催化臭氧氧化技術(shù),多項(xiàng)催化臭氧氧化技術(shù)是以產(chǎn)生·OH自由基等強(qiáng)活性自由基為目的的臭氧高級氧化過程,它遵循羥基自由基反應(yīng)機(jī)理的多項(xiàng)催化臭氧氧化技術(shù)具有更廣闊的應(yīng)用前景和使用范圍。然后再通過BAF曝氣生物濾池工序,最后經(jīng)過的濾池系統(tǒng)是一種去除水中SS的深度處理技術(shù),作為廢水的回用深度處理手段,確保出水水質(zhì)達(dá)到設(shè)計(jì)要求,得到生化處理水。本發(fā)明創(chuàng)造性的將脫除酚氨的有機(jī)廢水直接進(jìn)入生化處理工段的污水生化預(yù)處理系統(tǒng),也解決了后續(xù)生化處理系統(tǒng)剩余污泥處理的問題;并且以外循環(huán)厭氧(EC)多段生化組合工藝為核心煤氣化污水處理技術(shù),具有容積負(fù)荷高、啟動快、剩余污泥少、動力消耗少和代謝難以降解的有機(jī)物能力高等優(yōu)點(diǎn)。本發(fā)明將占煤化工項(xiàng)目廢水總量1/3的有機(jī)廢水進(jìn)行上述處理,有機(jī)廢水處理效果好,廢水在系統(tǒng)中平穩(wěn)運(yùn)行,沒有滯留現(xiàn)象,充分發(fā)揮裝置效能,出水COD可達(dá)30~100mg/l、NH3≤1mg/l,為中水回用奠定了堅(jiān)實(shí)的基礎(chǔ);而且利用富余生物污泥進(jìn)行預(yù)處理,大大增加了系統(tǒng)中生物處理的比重,無需啟動隔油、氣浮等處理設(shè)備該,減少了化學(xué)藥劑的添加量,大大降低了預(yù)處理成本,每年可節(jié)約處理費(fèi)用幾百萬元;在生化處理階段培養(yǎng)馴化菌種,實(shí)現(xiàn)無縫銜接達(dá)標(biāo)處理生產(chǎn)、生活污水。通過優(yōu)化菌種、科學(xué)調(diào)配污泥菌種,使用“污泥減量技術(shù)”,充分發(fā)揮裝置效能;而且.煤氣化廢水中有機(jī)污染物在厭氧微生物作用下實(shí)現(xiàn)脫毒和環(huán)結(jié)構(gòu)斷裂等,去處顯色物、醌、萘等長鏈芳烴,從而提高了廢水的可生化性,為后續(xù)的好氧生物處理創(chuàng)造了良好的條件;生物曾濃同步脫氮兼具有水解酸化作用,對難降解的COD和多元酚有較好的適應(yīng)性,去除效果優(yōu)于其他耗氧工藝,與此同時(shí)低溶氧又創(chuàng)造了同步硝化反硝化脫氮的條件,在生化池實(shí)現(xiàn)了脫氮過程;改良的A/O氧化工藝兼氧與好氧交替運(yùn)行可以改善難降解污染物的性質(zhì),強(qiáng)化降解水中剩余的有機(jī)污染物。本發(fā)明然后將上述步驟得到的生化處理水和含鹽廢水經(jīng)過提濃處理工藝后,得到回用水和高鹽廢水。本發(fā)明所述煤化工含鹽廢水具體優(yōu)選包括凈化合成系統(tǒng)的廢鹽水、凈化空分系統(tǒng)的廢鹽水、尿素循環(huán)水系統(tǒng)的排污廢鹽水、原水凈化站的排污廢鹽水、除鹽水站的排污廢鹽水和鍋爐排污廢鹽水中的一種或多種。本發(fā)明對所述提濃處理工藝的定義沒有特別限制,以本領(lǐng)域技術(shù)人員熟知的上述概念即可,本領(lǐng)域技術(shù)人員可以根據(jù)實(shí)際生產(chǎn)情況、水處理情況和水處理要求進(jìn)行調(diào)整和選擇。本發(fā)明所提濃處理工藝具體優(yōu)選依次包括生化水處理工序、中水處理工序和濃水深度處理工序。本發(fā)明對所述生化水處理工序的定義沒有特別限制,以本領(lǐng)域技術(shù)人員熟知的上述概念即可,本領(lǐng)域技術(shù)人員可以根據(jù)實(shí)際生產(chǎn)情況、水處理情況和水處理要求進(jìn)行調(diào)整和選擇。本發(fā)明所述生化水處理工序具體優(yōu)選包括活性炭處理步驟和除氟過濾步驟。本發(fā)明對上述具體工序和系統(tǒng)及其工藝參數(shù)沒有特別限制,以本領(lǐng)域技術(shù)人員熟知的上述工序和系統(tǒng)及其工藝參數(shù)即可,本領(lǐng)域技術(shù)人員可以根據(jù)實(shí)際生產(chǎn)情況、水處理情況和水處理要求進(jìn)行調(diào)整和選擇。本發(fā)明所述活性炭處理步驟和除氟過濾步驟具體是指采用活性炭降低生化進(jìn)水中的COD和有機(jī)物,同時(shí)通過除氟過濾器降低進(jìn)水的氟離子含量,避免反滲透膜表面因氟化鈣結(jié)垢,影響處理效率。主要裝置優(yōu)選為活性炭過濾器(360m3/h)和除氟過濾器(360m3/h)。本發(fā)明對所述中處理工序的定義沒有特別限制,以本領(lǐng)域技術(shù)人員熟知的上述概念即可,本領(lǐng)域技術(shù)人員可以根據(jù)實(shí)際生產(chǎn)情況、水處理情況和水處理要求進(jìn)行調(diào)整和選擇。本發(fā)明所述中水處理工序具體優(yōu)選依次包括攪拌澄清步驟、多介質(zhì)過濾步驟、超濾步驟和反滲透步驟。本發(fā)明對上述具體工序和系統(tǒng)及其工藝參數(shù)沒有特別限制,以本領(lǐng)域技術(shù)人員熟知的上述工序和系統(tǒng)及其工藝參數(shù)即可,本領(lǐng)域技術(shù)人員可以根據(jù)實(shí)際生產(chǎn)情況、水處理情況和水處理要求進(jìn)行調(diào)整和選擇。本發(fā)明所述攪拌澄清步驟、多介質(zhì)過濾步驟、超濾步驟和反滲透步驟具體是指,中水處理工藝包括機(jī)械攪拌澄清池,多介質(zhì)過濾器,超濾裝置,中水反滲透裝置。經(jīng)過生化水處理工序的來水,先進(jìn)入中水調(diào)節(jié)池經(jīng)過計(jì)息攪拌澄清池降低濁度;考慮中水的硬度和堿度較高,采用石灰乳投加裝置去除鈣鎂硬度,并添加Na2CO3,調(diào)節(jié)pH以達(dá)到去除鈣鎂硬度的目的,再加酸調(diào)節(jié)pH值滿足反滲透進(jìn)水要求;進(jìn)入公用回用水池加壓過多介質(zhì)過濾器去除水中懸浮物及油類,使油脂含量滿足超濾及反滲透運(yùn)行要求(<1.0mg/l);出水進(jìn)入濾后水箱,濾后水進(jìn)入管道混合器,調(diào)整pH值、還原多余的氧化劑及進(jìn)行阻垢劑穩(wěn)定處理,出水進(jìn)入5微米保安過濾器,除去5微米及以上直徑顆粒,出水壓送至反滲透設(shè)備。反滲透處理后的淡水即為回用水,可回用于生產(chǎn)系統(tǒng),而濃水則進(jìn)入后續(xù)濃水深度處理。本發(fā)明對所述濃水深度處理工序的定義沒有特別限制,以本領(lǐng)域技術(shù)人員熟知的上述概念即可,本領(lǐng)域技術(shù)人員可以根據(jù)實(shí)際生產(chǎn)情況、水處理情況和水處理要求進(jìn)行調(diào)整和選擇。本發(fā)明所述濃水深度處理工序具體優(yōu)選依次包括鈉離子交換步驟、多介質(zhì)過濾步驟、超濾步驟和反滲透步驟。本發(fā)明對上述具體工序和系統(tǒng)及其工藝參數(shù)沒有特別限制,以本領(lǐng)域技術(shù)人員熟知的上述工序和系統(tǒng)及其工藝參數(shù)即可,本領(lǐng)域技術(shù)人員可以根據(jù)實(shí)際生產(chǎn)情況、水處理情況和水處理要求進(jìn)行調(diào)整和選擇。本發(fā)明所述鈉離子交換步驟、多介質(zhì)過濾步驟、超濾步驟和反滲透步驟具體是指上述步驟得到的濃水經(jīng)過鈉離子交換裝置,多介質(zhì)過濾器,超濾裝置和濃水反滲等裝置。中水處理后的濃水硬度和含鹽量經(jīng)過濃縮已經(jīng)很高,不利于直接用反滲透除鹽,因此為了更多的回收清靜水,采用鈉離子裝置去除鈣鎂硬度,再加酸調(diào)價(jià)PH值滿足反滲透進(jìn)水要求,在經(jīng)多介質(zhì)過濾器去除懸浮物后,進(jìn)超濾和反滲透裝置。本發(fā)明上述工藝得到的淡水即為回用水,回用到生產(chǎn)系統(tǒng),濃水(高鹽廢水)量已經(jīng)很少,進(jìn)入后續(xù)濃鹽水處理工藝。本發(fā)明由于含鹽水提濃工藝前端生化處理出水水質(zhì)高,保障了回用水處理系統(tǒng)的運(yùn)轉(zhuǎn)效率,回用水產(chǎn)率提高,回用于生產(chǎn)的中水量增加,從而減少了新鮮水用量;且前端廢水產(chǎn)生量小于設(shè)計(jì)值,系統(tǒng)處理量降低,從而運(yùn)行維護(hù)成本降低。本發(fā)明最后將上述步驟得到的高鹽廢水經(jīng)過濃鹽水處理工藝后,得到含鹽物料。本發(fā)明對所述濃鹽水處理工藝的定義沒有特別限制,以本領(lǐng)域技術(shù)人員熟知的上述概念即可,本領(lǐng)域技術(shù)人員可以根據(jù)實(shí)際生產(chǎn)情況、水處理情況和水處理要求進(jìn)行調(diào)整和選擇。本發(fā)明所濃鹽水處理工藝具體優(yōu)選包括高效反滲透工序和蒸發(fā)工序。本發(fā)明對上述具體工序和系統(tǒng)及其工藝參數(shù)沒有特別限制,以本領(lǐng)域技術(shù)人員熟知的上述工序和系統(tǒng)及其工藝參數(shù)即可,本領(lǐng)域技術(shù)人員可以根據(jù)實(shí)際生產(chǎn)情況、水處理情況和水處理要求進(jìn)行調(diào)整和選擇。本發(fā)明所述經(jīng)含鹽水提濃處理后高鹽廢水送入濃鹽水處理工藝做進(jìn)一步處理,該多效蒸發(fā)工序優(yōu)選包括高效反滲透和蒸發(fā)器系統(tǒng),為提高處理效果,本發(fā)明還優(yōu)選在進(jìn)行高效反滲透工序前,先進(jìn)行過濾、軟化、除氣和調(diào)節(jié)pH值等工序;本發(fā)明對上述工序的順序、組合和參數(shù)沒有特別限制,本領(lǐng)域技術(shù)人員可以根據(jù)實(shí)際生產(chǎn)情況、水處理情況和水處理要求進(jìn)行調(diào)整和選擇,本發(fā)明優(yōu)選過濾和軟化出來的淡水,可以作為回用水返回系統(tǒng)。本發(fā)明所述高效反滲透工序具體是指,首先來水進(jìn)行原水池后進(jìn)行水量和水質(zhì)的調(diào)節(jié)。根據(jù)廢水的特點(diǎn),硬度含量很高,設(shè)置石灰處理。向原水中投加石灰以去除水中的硬度,經(jīng)澄清池去除懸浮物后送入硬度去除系統(tǒng)中的硬度,硬度采用兩級離子交換,一般采用強(qiáng)酸鈉離子交換器,在此將大部分的硬度,二級硬度去除采用弱酸陽離子交換器,取出剩余所有的硬度,脫除硬度后的軟水送至脫氣塔以脫除水中大部分的CO2。脫碳后產(chǎn)水有反滲透進(jìn)水泵預(yù)提升并經(jīng)精密過濾器中除水中可能存在的直徑大于5μm的顆粒,以免大顆粒物質(zhì)進(jìn)入RO系統(tǒng)損傷膜元件,然后由反滲透高壓泵增壓后送入一級反滲透系統(tǒng);反滲透是脫鹽的核心部分,可脫除97%以上的鹽分;一級反滲透的產(chǎn)水送至反滲透水箱,作為循環(huán)冷卻水補(bǔ)水回用,經(jīng)濃縮后的濃水儲存于濃水箱中,可作為后續(xù)處理系統(tǒng)的進(jìn)水;RO的產(chǎn)水送至反滲透產(chǎn)水箱中外送至循環(huán)水站作為循環(huán)水補(bǔ)充水。RO濃水送至濃水箱,鈉離子交換器和弱酸陽離子交換器送至再生廢水箱,單獨(dú)預(yù)處理后進(jìn)行濃縮處理。最后濃縮的濃鹽水送至蒸發(fā)工序。本發(fā)明所述蒸發(fā)工序具體是指,高效反滲透后的濃鹽水在板式換熱器中使用蒸發(fā)器產(chǎn)生的高溫蒸餾水作為熱源加熱。預(yù)熱后的濃鹽水然后進(jìn)入各自的脫氧罐中使用蒸發(fā)器中產(chǎn)生的二次蒸汽脫氧。預(yù)熱脫氧后的濃鹽水進(jìn)入蒸發(fā)器的底部物料罐。蒸發(fā)器是立式降膜設(shè)計(jì)。濃鹽水從底部物料罐循環(huán)至頂部物料罐,通過物料分配系統(tǒng)進(jìn)入換熱管,并在管壁上形成物料膜,在濃鹽水物料通過換熱管的過程中蒸發(fā),濃鹽水和二次蒸汽從換熱管底部進(jìn)入底部物料罐與循環(huán)鹽水混合,濃鹽水完成少量的濃縮。二次蒸汽從底部物料罐水平進(jìn)入折板消霧器。夾帶的鹽水滴在通過消霧器的過程中被去除,重新回到底部物料罐。消霧后的二次蒸汽,幾乎不含任何液滴,進(jìn)入機(jī)械蒸汽壓縮機(jī)。壓縮機(jī)提高二次蒸汽的壓力,增強(qiáng)后的二次蒸汽的冷凝點(diǎn)高于換熱管中鹽水的沸點(diǎn),通過管道進(jìn)入蒸發(fā)器的殼程,并在換熱管外壁冷凝。本發(fā)明采用高效反滲透技術(shù)來處理廢水,克服了單純離子交換和反滲透各自的缺點(diǎn),結(jié)合了離子交換和反滲透各自的優(yōu)點(diǎn),是目前最先進(jìn)的反滲透技術(shù)。其核心的工藝原理是:采用離子交換將水中的硬度去除,大部分的鹽分靠反滲透去除。同時(shí),反滲透在高pH條件下運(yùn)行,硅主要是以離子形式存在,不會污染反滲透膜并可通過反滲透去除;而水中的有機(jī)物在高pH條件下皂化或弱電離,不會造成膜的有機(jī)物和生物污染,可節(jié)省了大量的酸堿。本發(fā)明優(yōu)選還包括將上述步驟得到的高濃鹽水送入固化結(jié)晶處理工藝,得到含鹽物料。本發(fā)明對所述固化結(jié)晶處理工藝沒有特別限制,本領(lǐng)域技術(shù)人員可以根據(jù)實(shí)際生產(chǎn)情況、水處理情況和水處理要求進(jìn)行調(diào)整和選擇,本發(fā)明優(yōu)選為將排出的高濃鹽水做蒸發(fā)結(jié)晶處理,將高濃鹽水中的鹽分結(jié)晶為固體鹽進(jìn)行處理。根據(jù)物料的處理量及蒸發(fā)過程中的結(jié)晶情況,采用雙效順流蒸發(fā)裝置,最后得到的混鹽濾餅固體(含鹽物料)。本發(fā)明經(jīng)過上述步驟處理了煤化工廢水中的含鹽廢水,有效的解決了由于高含鹽量(含鹽量高達(dá)10000~50000mg/L,主要含Na+、K+、Ca2+、Mg2+、Al3+、Mn2+、Cl-、等離子,其中Na+的濃度達(dá)到10000~40000mg/L,Cl-濃度可達(dá)到10000~20000mg/L,SO42-濃度為10000~20000mg/L,而且COD含量較高,為500~2000mg/L。)而導(dǎo)致其無法直接進(jìn)入生化系統(tǒng)處理,同時(shí)高COD對膜有腐蝕和損害作用,也使其無法利用常規(guī)膜系統(tǒng)進(jìn)行除鹽處理,COD過高給蒸發(fā)結(jié)晶運(yùn)行帶來困難,造成了煤化工濃鹽水難處理的現(xiàn)狀。含鹽水處理是煤化工廢水實(shí)現(xiàn)“零排放”的又一重要環(huán)節(jié)。本發(fā)明提供的上述含鹽廢水處理步驟由含鹽水提濃處理工藝與濃鹽水處理工藝兩部分組成,具有系統(tǒng)銜接性好,鑒于生化處理的穩(wěn)定與高效,含鹽水提濃系統(tǒng)的設(shè)備并未受到廢水中COD與氨氮對膜系統(tǒng)的不良影響,順利過渡,并良好運(yùn)行;回用水得率、脫鹽率均較高,分別到90%及92%以上,且由于前端水質(zhì)優(yōu)化到位,處理維護(hù)成本降低;濃鹽水處理階段反滲透、超濾得率均達(dá)到同類系統(tǒng)先進(jìn)水平;濃鹽水蒸發(fā)系統(tǒng)正常穩(wěn)定運(yùn)行,濃鹽水蒸發(fā)濃縮效果好,濃水含鹽量200000~250000mg/L,鹽水濃度達(dá)到20~30%,且濃水產(chǎn)水量小,濃水排放量僅僅6~7m3/h。本發(fā)明經(jīng)過上述步驟有效的處理煤化工廢水,得到了回用水和含鹽物料,并且實(shí)現(xiàn)了煤化工廢水的零排放。本發(fā)明構(gòu)建了一套適用于水資源匱乏地區(qū)的煤化工廢水處理與零排放整體解決方案,并穩(wěn)定連續(xù)運(yùn)行,構(gòu)建了由煤化工廢水無害化水與煤化工廢水資源化、減量化兩個(gè)子系統(tǒng)組成的煤化工廢水零排放系統(tǒng)。而且系統(tǒng)各環(huán)節(jié)銜接良好流暢。該系統(tǒng)通過工藝的創(chuàng)造性優(yōu)化與改進(jìn),使得各工藝系統(tǒng)良好銜接與過度,尤其是生化處理系統(tǒng)的穩(wěn)定運(yùn)行,避免了廢水在系統(tǒng)中的滯留現(xiàn)象,確保了下一級處理的正常運(yùn)轉(zhuǎn);通過煤氣化廢水循環(huán)利用、凝結(jié)水清清分流實(shí)現(xiàn)了水資源的分質(zhì)、梯級利用,提高了水資源的利用效率;廢水在逐級處理的過程不斷得到減量化處置。各級處理工藝注重回用水產(chǎn)量的提高,從而逐步減少了廢水的產(chǎn)出量,降低了整個(gè)系統(tǒng)運(yùn)行負(fù)荷,為系統(tǒng)的穩(wěn)定運(yùn)行打下了良好基礎(chǔ);優(yōu)化脫鹽水與循環(huán)水平衡。系統(tǒng)創(chuàng)新性的將回用水用作脫鹽水補(bǔ)水,減少新鮮水制脫鹽水量,降低脫鹽水成本,也大大減少脫鹽水排污水;同時(shí)利用生產(chǎn)水補(bǔ)充循環(huán)水,從而改善了循環(huán)水質(zhì)量,提升了換熱能力,減輕了腐蝕和結(jié)垢現(xiàn)象。從而為回用水、脫鹽水、循環(huán)水優(yōu)化操作發(fā)揮效能提供了先決條件;改良有機(jī)廢水預(yù)處理系統(tǒng)。在廢水生化預(yù)處理階段利用后續(xù)生化段富余生物污泥進(jìn)行預(yù)處理,大大增加了系統(tǒng)中生物處理的比重,無需啟動隔油、氣浮等處理設(shè)備該,減少了化學(xué)藥劑的添加量,大大降低了預(yù)處理成本;高濃鹽水出水濃度高,有利后續(xù)結(jié)晶處理。通過精細(xì)操作嚴(yán)控工藝指標(biāo),使?jié)恹}水裝置操作效能達(dá)到國內(nèi)領(lǐng)先水平。出水含鹽量20%以上,水量僅6~7m3/h。為了進(jìn)一步理解本發(fā)明,下面結(jié)合實(shí)施例對本發(fā)明提供的一種煤化工廢水的處理工藝進(jìn)行說明,本發(fā)明的保護(hù)范圍不受以下實(shí)施例的限制。實(shí)施例1本發(fā)明煤化工廢水的處理工藝12個(gè)月內(nèi)運(yùn)行情況首先,將煤化工廢水中的有機(jī)廢水經(jīng)過單塔脫氨、脫酸,廢水分冷、熱兩股分別從上部和中上部進(jìn)入污水汽提塔,汽提出的CO2、H2S等酸性氣體及少量氨、水蒸汽進(jìn)入后續(xù)處理裝置或火炬焚燒;從側(cè)線采出的氨水汽進(jìn)入三級分凝,冷凝回部分水和少量氨、CO2,富氨氣進(jìn)入氨精制工段加工成液氨。脫酸氣后的污水汽提塔的釜液冷卻到40℃左右后從上部進(jìn)入萃取塔,與萃取劑MIBK進(jìn)行逆流萃取。萃取相泵入酚塔中,精餾分離粗酚與MIBK,MIBK回用。萃取塔的萃余相加入水塔,從頂部采出溶解和夾帶的溶劑,冷凝、分相后回用。萃取劑再生流股回送至溶劑回收罐循環(huán)使用。水塔的釜液(處理后廢液)進(jìn)入后續(xù)的生化段生化處理。有機(jī)廢水量為100m3/h,經(jīng)酚氨處理進(jìn)出水水質(zhì)及其控制指標(biāo)見表1-1。表1-1有機(jī)廢水脫除酚氨處理進(jìn)出水水質(zhì)對比主要污染物進(jìn)水實(shí)測值出水實(shí)測值總酚mg/L4329707總氨mg/L15000300油mg/L76090CODmg/L162582800pH98塵mg/L12070單元酚mg/L2653265游離氨mg/L13000140本發(fā)明上述有機(jī)廢水經(jīng)過脫氨酚處理工藝后,得到處理后廢液,去除率分別為總酚84%、總氨98%,COD83%。本發(fā)明上述脫氨酚處理工藝中總酚、總氨、COD等污染物指標(biāo)的實(shí)際檢測情況,參見圖1,圖1為本發(fā)明脫氨酚處理工藝的出水中主要污染物指標(biāo)情況。如圖1所示,脫氨酚處理工藝處理出水效果滿足工藝控制要求且運(yùn)行穩(wěn)定,在年7~9月間出現(xiàn)波動,主要原因是7月供電系統(tǒng)出現(xiàn)問題,生產(chǎn)及水處理系統(tǒng)停止運(yùn)行,8月恢復(fù)生產(chǎn),各污染物出現(xiàn)一段峰值,后逐步回落。然后將上述步驟得到的處理后廢液,以及地面沖洗水、雨水、氣化爐廢水、低溫甲醇洗廢水、生產(chǎn)性廢水和生活化驗(yàn)廢水等其他廢水,送入生化處理工藝,具體為預(yù)處理-生化處理-深度處理三段式處理工藝,規(guī)模為360m3/h,脫除酚氨廢水進(jìn)入調(diào)節(jié)池→外循環(huán)(EC)厭氧系統(tǒng)→沉淀池→生物增濃同步脫氮系統(tǒng)→改良A/O氧化系統(tǒng)→二沉池→絮凝沉淀池→高級氧化→BAF曝氣生物濾池→濾池→消毒池→出水。參見圖2,圖2為本發(fā)明生化處理工藝的流程概圖。本發(fā)明生化處理工藝總處理水量約為250m3/h,其中處理后廢液約為80~100m3/h,生活污水50m3/h、氣化循環(huán)水排污約30m3/h、低溫甲醇洗廢水15m3/h、地坪沖洗水等其他生產(chǎn)性廢水約30m3/h。污水水質(zhì)見表1-2。表1-2有機(jī)廢水生化處理工藝來水水質(zhì)情況本發(fā)明生化處理工藝過程中,出水水質(zhì)參見表1-3。表1-3有機(jī)廢水生化處理出水水質(zhì)參見圖3,圖3為本發(fā)明有機(jī)廢水生化處理后出水的COD檢測情況。參見圖4,圖4為本發(fā)明有機(jī)廢水生化處理后出水的氨氮檢測情況。本發(fā)明經(jīng)過上生化處理工藝過程后,得到生化處理水,然后將其送入提濃處理工藝,與含鹽廢水一同進(jìn)行提濃處理。含鹽廢水包括凈化合成系統(tǒng)的廢鹽水、凈化空分系統(tǒng)的廢鹽水、尿素循環(huán)水系統(tǒng)的排污廢鹽水、原水凈化站的排污廢鹽水、除鹽水站的排污廢鹽水和鍋爐排污廢鹽水。含鹽廢水水質(zhì)概總參見表1-4。表1-4含鹽廢水水質(zhì)概總提濃工藝流程主要分為生化水處理-中水處理-濃水深度處理三級工藝,其中生化水處理工序包括活性炭處理步驟和除氟過濾步驟,采用活性炭降低生化進(jìn)水中的COD和有機(jī)物,同時(shí)通過除氟過濾器降低進(jìn)水的氟例子含量,避免反滲透膜表面因氟化鈣結(jié)垢,影響處理效率。主要裝置活性炭過濾器(360m3/h)和除氟過濾器(360m3/h)。參見圖5,圖5為本發(fā)明生化水處理工序的工藝流程概圖。中水處理工序依次包括攪拌澄清步驟、多介質(zhì)過濾步驟、超濾步驟和反滲透步驟。具體裝置包括1350m3/h機(jī)械攪拌澄清池,1350m3/h多介質(zhì)過濾器,8*150m3/h超濾,8*113m3/h中水反滲透裝置。經(jīng)過過濾后的生化處理水和含鹽廢水先進(jìn)入中水調(diào)節(jié)池經(jīng)過計(jì)息攪拌澄清池降低濁度,考慮中水的硬度和堿度較高,采用石灰乳投加裝置去除鈣鎂硬度,并添加Na2CO3,調(diào)節(jié)PH以達(dá)到去除鈣鎂硬度的目的,再加酸調(diào)節(jié)PH值滿足反滲透進(jìn)水要求;進(jìn)入公用回用水池加壓過多介質(zhì)過濾器去除水中懸浮物及油類,使油脂含量滿足超濾及反滲透運(yùn)行要求(<1.0mg/l);出水進(jìn)入濾后水箱,濾后水進(jìn)入管道混合器,調(diào)整PH值、還原多余的氧化劑及進(jìn)行阻垢劑穩(wěn)定處理,出水進(jìn)入5微米保安過濾器,除去5微米及以上直徑顆粒,出水壓送至反滲透設(shè)備。反滲透處理的淡水回用于生產(chǎn)系統(tǒng),濃水進(jìn)入后續(xù)深度處理工序。參見圖6,圖6為本發(fā)明中水處理工序的工藝流程概圖。將上述步驟得到的濃水,濃水深度處理工序包括鈉離子交換步驟、多介質(zhì)過濾步驟、超濾步驟和反滲透步驟,具體裝置為300m3/h多介質(zhì)過濾器,2*150m3/h超濾,2*150m3/h鈉離子交換器和2*60m3/h濃水反滲等裝置。參見圖7,圖7為本發(fā)明濃水深度處理工序的工藝流程概圖。中水處理后的濃水采用鈉離子裝置去除鈣鎂硬度,再加酸調(diào)價(jià)PH值滿足反滲透進(jìn)水要求,在經(jīng)多介質(zhì)過濾器去除懸浮物后,進(jìn)超濾和反滲透裝置。該步驟出的淡水回用到生產(chǎn)系統(tǒng),反滲透的濃水進(jìn)入后續(xù)濃鹽水處理工藝。經(jīng)測試,上述回用水超濾裝置平均產(chǎn)水量150m3/h,濃水超濾裝置平均產(chǎn)水量150m3/h,回收率均超過90%;回用水反滲透裝置平均回收率76.6%,脫鹽率97.2%;濃水反滲透裝置回收率25%,脫鹽率92.6%。上述提濃工藝流程生化處理水和含鹽廢水的具體水質(zhì)參見表1-5。表1-5生化處理水和含鹽廢水具體水質(zhì)參見表1-6,表1-6為生產(chǎn)可用水指標(biāo)。表1-6生產(chǎn)可用水指標(biāo)參見表1-7,表1-7為提濃處理工藝出水水質(zhì)。表1-7提濃處理工藝出水水質(zhì)參見表1-8,表1-8為提濃處理工藝后高鹽廢水水質(zhì)。表1-8提濃處理工藝后高鹽廢水水質(zhì)項(xiàng)目水質(zhì)指標(biāo)項(xiàng)目水質(zhì)指標(biāo)氨氮7mg/L碳?xì)渌猁}350mg/L鉀40mg/L硝酸鹽133mg/L鈉1350mg/L氯化物2267mg/L鎂133mg/L氟化物10mg/L鈣200mg/L硫酸鹽2333mg/L鍶6.7mg/LTDS20000mg/L鋇1.5mg/LPH6-9mg/L鹽酸鹽30mg/LCOD300mg/L將上述步驟得到的高鹽廢水,即反滲透后的濃水,先進(jìn)入濃水均質(zhì)水池,經(jīng)濃水傳輸泵進(jìn)入快速反應(yīng)池,在快速反應(yīng)池中加入石灰乳、碳酸鈉、絮凝劑進(jìn)行快速反應(yīng),反應(yīng)后的水流入接觸澄清池,在接觸反應(yīng)池進(jìn)一步加入助凝劑進(jìn)行反應(yīng)使水進(jìn)一步澄清,污水排入污泥處理系統(tǒng),澄清水流入清水池,澄清水經(jīng)多介質(zhì)過濾器提升泵送入多介質(zhì)過濾器過濾降低濁度進(jìn)入弱酸陽床,經(jīng)弱酸陽床降低部分硬度然后進(jìn)入高效反滲透除去大部分硬度,高效反滲透產(chǎn)水硬度接近于零,反滲透產(chǎn)水收集在高效反滲透產(chǎn)水水池回用到循環(huán)水作為循環(huán)水補(bǔ)充水,高效反滲透濃水收集在濃水池,濃水經(jīng)過蒸發(fā)器給水泵進(jìn)入降膜式蒸發(fā)器進(jìn)行蒸發(fā)處理,蒸餾水收集到高效反滲透產(chǎn)水水池,蒸發(fā)器濃水到蒸發(fā)結(jié)晶處理。本發(fā)明經(jīng)過上述濃鹽酸處理工藝后,得到(高濃鹽水)濃水含鹽量200000~250000mg/L,鹽水濃度達(dá)到20~30%。且濃水排放量為6~7m3/h。然后再將高濃鹽水送入雙效順流蒸發(fā)裝置,最后得到的混鹽濾餅固體。以上對本發(fā)明所提供的一種煤化工廢水的處理工藝進(jìn)行了詳細(xì)介紹。本文中應(yīng)用了具體的個(gè)例對本發(fā)明的原理及實(shí)施方式進(jìn)行了闡述,以上實(shí)施例的說明只是用于幫助理解本發(fā)明的方法及其核心思想。應(yīng)當(dāng)指出,對于本
技術(shù)領(lǐng)域:
的普通技術(shù)人員來說,在不脫離本發(fā)明原理的前提下,還可以對本發(fā)明進(jìn)行若干改進(jìn)和修飾,這些改進(jìn)和修飾也落入本發(fā)明權(quán)利要求的保護(hù)范圍內(nèi)。當(dāng)前第1頁1 2 3