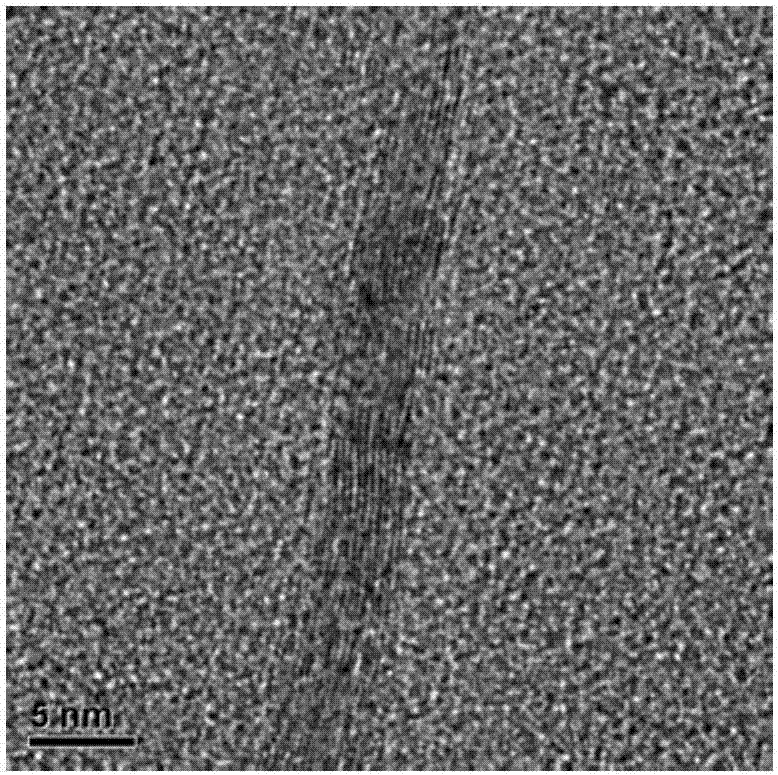
本發(fā)明屬于材料領(lǐng)域,具體涉及一種石墨烯/氰酸酯復(fù)合材料及其制備方法和用途,尤其涉及一種具有導(dǎo)電、導(dǎo)熱、低熱膨脹系數(shù)的石墨烯/氰酸酯復(fù)合材料及其制備方法和用途。
背景技術(shù):
:目前,衛(wèi)星等航天器結(jié)構(gòu)要長期經(jīng)受太陽、地球以及其它天體的輻射和空間低溫的交替加熱和冷卻,從而引起結(jié)構(gòu)內(nèi)部高低溫的劇烈變化,變化的幅度可達(dá)-200℃~200℃。對于大型的星載可展開天線來說,由于尺寸大、結(jié)構(gòu)柔度大,所以對熱的敏感性能較高,熱穩(wěn)定性較差。主要的不利影響有:1)不均勻的溫度梯度會引起熱變形以及熱-結(jié)構(gòu)響應(yīng),不僅會導(dǎo)致展開天線結(jié)構(gòu)的形狀尺寸變化,還可能會引起航天器的在軌姿態(tài)變化;2)劇烈的溫度變化引起的熱變形使得反射面形面精度降低,影響天線的電性能。在碳纖維復(fù)合材料中,由于碳纖維熱膨脹系數(shù)極低,因此熱固性樹脂的熱膨脹系數(shù)是影響復(fù)合材料熱變形的關(guān)鍵因素。在衛(wèi)星用碳纖維結(jié)構(gòu)復(fù)合材料中,通過鋪設(shè)熱管的形式傳導(dǎo)熱量,但是熱管很細(xì),可以理解為一維導(dǎo)熱體,即熱管近端的熱量可以快速傳導(dǎo),熱管遠(yuǎn)端的熱量傳導(dǎo)很慢,整個復(fù)合材料板溫度不均勻性仍然很大,需要提高碳纖維復(fù)合材料本身的熱導(dǎo)率以使得碳纖維結(jié)構(gòu)溫度更均勻。另外,在有些衛(wèi)星用碳纖維結(jié)構(gòu)件中,是不適合鋪設(shè)熱管的,在此類結(jié)構(gòu)材料中,提高材料本身的熱導(dǎo)率尤為重要。隨著航天技術(shù)的發(fā)展,我國航天器需要向“質(zhì)、量并重”發(fā)展,高穩(wěn)定性、長使用壽命是未來航天器的發(fā)展方向,這就對航天器材料提出了更高的要求。碳纖維復(fù)合材料在滿足力學(xué)性能的同時,需要具有導(dǎo)熱、導(dǎo)電、低熱膨脹系數(shù)等功能,即功能性碳纖維環(huán)氧樹脂復(fù)合材料。目前,針對石墨烯改性氰酸酯樹脂的研究主要集中在提高氰酸酯的導(dǎo)熱性能方面。CN105061760A中公開了將氧化石墨烯、六氯環(huán)三磷腈及超支化聚硅氧烷反應(yīng),得到相互之間通過化學(xué)鍵作用構(gòu)成的含磷雜化氧化石墨烯;再將熔融態(tài)的氰酸酯樹脂與含磷雜化氧化石墨烯均勻混合,經(jīng)固化處理后,即得到一種含磷雜化氧化石墨烯改性氰酸酯,具有良好的介電性能和阻燃性能;CN102796373A中公開了采用超支化聚硅氧烷修飾的石墨烯,其表面引入含有能與樹脂進(jìn)行化學(xué)反應(yīng)的活性官能團(tuán)環(huán)氧基,對雙酚A型氰酸酯樹脂進(jìn)行增韌改性。上述文獻(xiàn)中均以氧化石墨烯為原料,通過接枝方法提高氧化石墨烯與氰酸酯的相容性,力學(xué)性能得到了提高,但卻破壞了石墨烯的結(jié)構(gòu),使得導(dǎo)電、導(dǎo)熱性能必然下降。CN105368046A中公開了采用單官能異氰酸酯處理的多壁碳納米管或采用單官能異氰酸酯處理的石墨烯中的一種或組合改性氰酸酯得到的復(fù)合物,其熱導(dǎo)率可達(dá)到0.759W·m-1k-1,其中未說明碳納米管或石墨烯改性氰酸脂后,樹脂的力學(xué)性能、電學(xué)性能、熱膨脹系數(shù)以及粘度等綜合性能,而作為一種多功能樹脂,需要滿足加工工藝性的同時,兼顧各種性能需求。完整的石墨烯結(jié)構(gòu)是其具備導(dǎo)電、導(dǎo)熱特性的基礎(chǔ),如何在不破壞石墨烯結(jié)構(gòu)的前提下,提高石墨烯、石墨烯微片在氰酸酯樹脂中的分散性和界面相容性,是同時提高石墨烯/氰酸酯復(fù)合材料力學(xué)性能、導(dǎo)電性能、導(dǎo)熱性能,降低熱膨脹系數(shù)的關(guān)鍵。技術(shù)實現(xiàn)要素:為解決現(xiàn)有技術(shù)的上述問題,本發(fā)明提供了一種石墨烯/氰酸酯復(fù)合材料及其制備方法和用途,本發(fā)明制備得到的復(fù)合材料具有高導(dǎo)電、高導(dǎo)熱、低熱膨脹系數(shù)的特點,并具有良好的加工工藝性(粘度低),力學(xué)性能得到了大幅提高。為了達(dá)到上述目的,本發(fā)明采用如下技術(shù)方案:第一方面,本發(fā)明提供了一種石墨烯/氰酸酯復(fù)合材料的制備方法,其包括以下步驟:(1)將石墨烯、石墨烯微片、π-π共軛小分子和水進(jìn)行混合,預(yù)分散;(2)將預(yù)分散后的水溶液置于冰浴環(huán)境中進(jìn)行再次分散,然后將得到的分散液置于液氮中冷卻,干燥后得到泡沫化預(yù)分散的石墨烯-石墨烯微片;(3)將泡沫化預(yù)分散的石墨烯-石墨烯微片與氰酸酯樹脂混合,通過攪拌、研磨,將石墨烯-石墨烯微片分散在氰酸酯樹脂中;(4)在泡沫化預(yù)分散的石墨烯-石墨烯微片與氰酸酯樹脂混合過程中抽真空脫氣,并澆注固化成型,得到所述石墨烯/氰酸酯復(fù)合材料。本發(fā)明所述制備方法中采用的石墨烯原料為石墨烯和石墨烯微片,其中的石墨烯可以采用先由石墨經(jīng)化學(xué)剝離制備氧化石墨烯,之后還原為石墨烯的方法進(jìn)行制備。本發(fā)明通過采用石墨烯為原料,其相比采用氧化石墨烯類,能增加石墨烯/氰酸酯復(fù)合材料的導(dǎo)電和導(dǎo)熱性能,并使其具有低熱膨脹系數(shù)。本發(fā)明在制備方法中采用了將預(yù)分散后的水溶液置于冰浴環(huán)境中進(jìn)行再次分散從而得到泡沫化預(yù)分散的石墨烯-石墨烯微片的步驟,其能夠使石墨烯-石墨烯微片在氰酸酯樹脂中分散良好,在低含量、低粘度下,電導(dǎo)率、熱導(dǎo)率和力學(xué)性能提高,熱膨脹系數(shù)降低。本領(lǐng)域技術(shù)人員應(yīng)當(dāng)明了,對于步驟(4)中涉及的混合過程中抽真空脫氣,以及澆注固化成型均為本領(lǐng)域制備樹脂材料所采用的常用手段,本發(fā)明在此不做贅述。根據(jù)本發(fā)明,步驟(1)中所述石墨烯的厚度為0.35nm~2nm,例如0.35nm、0.5nm、0.6nm、0.8nm、1nm、1.2nm、1.5nm、1.8nm或2nm等;直徑為200nm~1μm,例如200nm、300nm、400nm、600nm、800nm或1μm等。根據(jù)本發(fā)明,步驟(1)中所述石墨烯微片的厚度為5nm~20nm,例如5nm、8nm、10nm、12nm、15nm、18nm或20nm等;直徑為3μm~6μm,例如3μm、4μm、4.5μm、5μm、5.5μm或6μm等。根據(jù)本發(fā)明,步驟(1)中所述π-π共軛小分子為1-吡啶酸琥珀酰亞胺酯、卟啉或其組合,即可以是1-吡啶酸琥珀酰亞胺酯或卟啉,也可以是二者的混合物。根據(jù)本發(fā)明,步驟(1)所述混合時,石墨烯所占的質(zhì)量百分含量為0.5%~5%,例如0.5%、1%、1.5%、2%、2.5%、3%、4%、4.5%或5%等,石墨烯微片所占的質(zhì)量百分含量為2%~10%,例如2%、2.5%、3%、3.5%、4%、4.5%、5%、5.5%、6%、7%、9%或10%等,π-π共軛小分子所占的質(zhì)量百分含量為0.1%~1%,例如0.1%、0.2%、0.3%、0.4%、0.5%、0.6%、0.8%或1%等,水所占的質(zhì)量百分含量為84%~97.4%,例如84%、85%、87%、89%、90%、91%、93%、95%或97.4%等;上述石墨烯、石墨烯微片、π-π共軛小分子和水的質(zhì)量百分含量之和為100%。根據(jù)本發(fā)明,步驟(1)中所述石墨烯、石墨烯微片、π-π共軛小分子和水的質(zhì)量比還可以優(yōu)選為1~2:5~9:0.5~1:89.5~95,例如1:5:1:90、2:8:0.5:92、1:7:1:90、2:7:0.5:91、1:6:0.5:92或1:9:0.5:90等,優(yōu)選1:9:0.5:89.5。根據(jù)本發(fā)明,步驟(1)中所述預(yù)分散采用高速攪拌機和三輥研磨機進(jìn)行,其中高速攪拌機和三輥研磨機均采用本領(lǐng)域公知的設(shè)備進(jìn)行,本發(fā)明不做特殊限定,其目的均在于實現(xiàn)更好的分散效果。根據(jù)本發(fā)明,步驟(2)中所述再次分散采用超聲波細(xì)胞粉碎機進(jìn)行;所述超聲波細(xì)胞粉碎機的工作功率為200W~800W,例如200W、300W、350W、400W、500W、550W、600W、700W或800W等,優(yōu)選800W;所述超聲波細(xì)胞粉碎機的超聲時間為20min~60min,例如20min、30min、40min、45min、50min或60min等,優(yōu)選30min。本發(fā)明通過超聲波作用使π-π共軛類小分子與石墨烯、石墨烯微片的石墨層形成強烈的π-π堆積相互作用,形成小分子修飾的石墨烯-石墨烯微片水溶液,從而使其形成更好的分散液。根據(jù)本發(fā)明,步驟(2)中將預(yù)分散水溶液置于冰浴環(huán)境中,利用超聲波細(xì)胞粉碎機進(jìn)行再次分散,然后將得到的分散液放置于液氮中,快速冷卻,等完全凍結(jié)后置于冷凍干燥機中,將水除去,得到泡沫化預(yù)分散的石墨烯-石墨烯微片。根據(jù)本發(fā)明,步驟(3)中所述攪拌采用高速攪拌機進(jìn)行,所述研磨采用三輥研磨機進(jìn)行,其中高速攪拌機和三輥研磨機均采用本領(lǐng)域公知的設(shè)備進(jìn)行,本發(fā)明不做特殊限定。根據(jù)本發(fā)明,步驟(3)中所述氰酸酯樹脂可以選自雙酚A型氰酸脂、雙酚A型環(huán)氧樹脂或雙馬來酰亞胺樹脂中的任意一種或至少兩種的混合物,例如可以是雙酚A型氰酸脂、雙酚A型環(huán)氧樹脂或雙馬來酰亞胺樹脂中的任意一種,典型但非限制性的混合物為:雙酚A型氰酸酯和雙酚A型環(huán)氧樹脂,雙酚A型氰酸酯和雙馬來酰亞胺樹脂,優(yōu)選雙酚A型氰酸脂、雙酚A型環(huán)氧樹脂和雙馬來酰亞胺樹脂的混合物,當(dāng)采用三者的混合物時,所述雙酚A型氰酸脂、雙酚A型環(huán)氧樹脂和雙馬來酰亞胺樹脂的質(zhì)量比為90:7.5:2.5。根據(jù)本發(fā)明,步驟(3)所述混合時,氰酸酯樹脂所占的質(zhì)量百分含量為84%~94.9%,例如84%、86%、88%、90%、92%、93%、93.8%或94.9%等,泡沫化預(yù)分散的石墨烯-石墨烯微片所占的質(zhì)量百分含量為5.1%~16%,例如5.1%、5.7%、6%、6.5%、8%、9.5%、11%、13%、14.5%或16%等,所述氰酸酯樹脂和泡沫化預(yù)分散的石墨烯-石墨烯微片的質(zhì)量百分含量之和為100%。第二方面,本發(fā)明還提供了如第一方面所述的方法制備得到的石墨烯/氰酸酯復(fù)合材料。本發(fā)明所述制備得到的石墨烯/氰酸酯復(fù)合材料具有優(yōu)異的綜合性能,其不僅具有高電導(dǎo)率、高熱導(dǎo)率,而且熱膨脹系數(shù)低,具有良好的加工工藝性(粘度低),力學(xué)性能也會得到提高,是一種綜合性能優(yōu)良的復(fù)合材料。第三方面,本發(fā)明還提供了如第二方面所述的石墨烯/氰酸酯復(fù)合材料在航空航天材料中的用途。本發(fā)明提供的石墨烯/氰酸酯復(fù)合材料由于具有高電導(dǎo)率、高熱導(dǎo)率以及低熱膨脹系數(shù),綜合性能優(yōu)異,其可以廣泛適用于航天器導(dǎo)電、導(dǎo)熱、低熱膨脹系數(shù)結(jié)構(gòu)復(fù)合材料構(gòu)件中。與現(xiàn)有技術(shù)相比,本發(fā)明至少具有以下有益效果:(1)本發(fā)明通過采用石墨烯作為主要原料,其避免了采用氧化石墨烯帶來的導(dǎo)電、導(dǎo)熱性能下降的缺陷;(2)本發(fā)明通過采用增加將預(yù)分散后的水溶液置于冰浴環(huán)境中再次分散后從而得到泡沫化預(yù)分散的石墨烯-石墨烯微片的步驟,其大幅增加了石墨烯/氰酸酯樹脂的電導(dǎo)率和熱導(dǎo)率,降低了熱膨脹系數(shù);(3)本發(fā)明通過增加石墨烯微片作為部分原料,其能夠大幅降低石墨烯原料成本,并具有增加石墨烯原料分散的作用,從而使石墨烯原料與氰酸酯均勻混合,使其具有優(yōu)異的力學(xué)性能等。附圖說明圖1為本發(fā)明采用的石墨烯TEM圖;圖2為本發(fā)明采用的石墨烯微片TEM圖。下面對本發(fā)明進(jìn)一步詳細(xì)說明。但下述的實例僅僅是本發(fā)明的簡易例子,并不代表或限制本發(fā)明的權(quán)利保護(hù)范圍,本發(fā)明的保護(hù)范圍以權(quán)利要求書為準(zhǔn)。具體實施方式下面結(jié)合附圖并通過具體實施方式來進(jìn)一步說明本發(fā)明的技術(shù)方案。為更好地說明本發(fā)明,便于理解本發(fā)明的技術(shù)方案,本發(fā)明的典型但非限制性的實施例如下:實施例1(1)按照石墨烯:石墨烯微片:π-π共軛小分子:去離子水=0.5:10:0.5:89的質(zhì)量比配制,混合后,采用高速攪拌機、三輥研磨機進(jìn)行預(yù)分散;其中π-π共軛小分子為1-吡啶酸琥珀酰亞胺酯;(2)將預(yù)分散后的水溶液置于冰浴環(huán)境中,利用超聲波細(xì)胞粉碎機進(jìn)行再次分散,采用超聲波細(xì)胞粉碎機在800W的功率下超聲30min,然后將得到的分散液放置于液氮中,快速冷卻,等完全凍結(jié)后置于冷凍干燥機中,將水除去,得到泡沫化預(yù)分散的石墨烯-石墨烯微片;(3)將泡沫化預(yù)分散的石墨烯-石墨烯微片與氰酸酯樹脂混合,再次通過高速攪拌、三輥研磨,將石墨烯-石墨烯微片分散在氰酸酯樹脂中,其中泡沫化預(yù)分散的石墨烯-石墨烯微片所占的質(zhì)量百分含量為10%,氰酸酯樹脂所占的質(zhì)量百分含量為90%,其中氰酸酯樹脂由雙酚A型氰酸脂:雙酚A型環(huán)氧樹脂:雙馬來酰亞胺樹脂=90:7.5:2.5的質(zhì)量比配制而成;(4)按照上述配方比例均勻混合,混合過程中抽真空脫氣,并澆注固化成型,得到所述石墨烯/氰酸酯復(fù)合材料。實施例2(1)按照石墨烯:石墨烯微片:π-π共軛小分子:去離子水=1:9:0.5:89.5的質(zhì)量比配制,混合后,采用高速攪拌機、三輥研磨機進(jìn)行預(yù)分散;其中π-π共軛小分子為1-吡啶酸琥珀酰亞胺酯;(2)將預(yù)分散后的水溶液置于冰浴環(huán)境中,利用超聲波細(xì)胞粉碎機進(jìn)行再次分散,采用超聲波細(xì)胞粉碎機在500W的功率下超聲25min,然后將得到的分散液放置于液氮中,快速冷卻,等完全凍結(jié)后置于冷凍干燥機中,將水除去,得到泡沫化預(yù)分散的石墨烯-石墨烯微片;(3)將泡沫化預(yù)分散的石墨烯-石墨烯微片與氰酸酯樹脂混合,再次通過高速攪拌、三輥研磨,將石墨烯-石墨烯微片分散在氰酸酯樹脂中,其中泡沫化預(yù)分散的石墨烯-石墨烯微片所占的質(zhì)量百分含量為10%,氰酸酯樹脂所占的質(zhì)量百分含量為90%,其中氰酸酯樹脂由雙酚A型氰酸脂:雙酚A型環(huán)氧樹脂:雙馬來酰亞胺樹脂=90:7.5:2.5的質(zhì)量比配制而成;(4)按照上述配方比例均勻混合,混合過程中抽真空脫氣,并澆注固化成型,得到所述石墨烯/氰酸酯復(fù)合材料。實施例3(1)按照石墨烯:石墨烯微片:π-π共軛小分子:去離子水=5:10:1:84的質(zhì)量比配制,混合后,采用高速攪拌機、三輥研磨機進(jìn)行預(yù)分散;其中π-π共軛小分子為1-吡啶酸琥珀酰亞胺酯;(2)將預(yù)分散后的水溶液置于冰浴環(huán)境中,利用超聲波細(xì)胞粉碎機進(jìn)行再次分散,采用超聲波細(xì)胞粉碎機在400W的功率下超聲40min,然后將得到的分散液放置于液氮中,快速冷卻,等完全凍結(jié)后置于冷凍干燥機中,將水除去,得到泡沫化預(yù)分散的石墨烯-石墨烯微片;(3)將泡沫化預(yù)分散的石墨烯-石墨烯微片與氰酸酯樹脂混合,再次通過高速攪拌、三輥研磨,將石墨烯-石墨烯微片分散在氰酸酯樹脂中,其中泡沫化預(yù)分散的石墨烯-石墨烯微片所占的質(zhì)量百分含量為10%,氰酸酯樹脂所占的質(zhì)量百分含量為90%,其中氰酸酯樹脂由雙酚A型氰酸脂:雙酚A型環(huán)氧樹脂:雙馬來酰亞胺樹脂=90:7.5:2.5的質(zhì)量比配制而成;(4)按照上述配方比例均勻混合,混合過程中抽真空脫氣,并澆注固化成型,得到所述石墨烯/氰酸酯復(fù)合材料。實施例4(1)按照石墨烯:石墨烯微片:π-π共軛小分子:去離子水=1:9:0.5:89.5的質(zhì)量比配制,混合后,采用高速攪拌機、三輥研磨機進(jìn)行預(yù)分散;其中π-π共軛小分子為1-吡啶酸琥珀酰亞胺酯;(2)將預(yù)分散后的水溶液置于冰浴環(huán)境中,利用超聲波細(xì)胞粉碎機進(jìn)行再次分散,采用超聲波細(xì)胞粉碎機在600W的功率下超聲45min,然后將得到的分散液放置于液氮中,快速冷卻,等完全凍結(jié)后置于冷凍干燥機中,將水除去,得到泡沫化預(yù)分散的石墨烯-石墨烯微片;(3)將泡沫化預(yù)分散的石墨烯-石墨烯微片與氰酸酯樹脂混合,再次通過高速攪拌、三輥研磨,將石墨烯-石墨烯微片分散在氰酸酯樹脂中,其中泡沫化預(yù)分散的石墨烯-石墨烯微片所占的質(zhì)量百分含量為10%,氰酸酯樹脂所占的質(zhì)量百分含量為90%,其中氰酸酯樹脂由雙酚A型氰酸脂:雙酚A型環(huán)氧樹脂:雙馬來酰亞胺樹脂=90:7.5:2.5的質(zhì)量比配制而成;(4)按照上述配方比例均勻混合,混合過程中抽真空脫氣,并澆注固化成型,得到所述石墨烯/氰酸酯復(fù)合材料。實施例5(1)按照石墨烯:石墨烯微片:π-π共軛小分子:去離子水=1:9:0.5:89.5的質(zhì)量比配制,混合后,采用高速攪拌機、三輥研磨機進(jìn)行預(yù)分散;其中π-π共軛小分子為1-卟啉;(2)將預(yù)分散后的水溶液置于冰浴環(huán)境中,利用超聲波細(xì)胞粉碎機進(jìn)行再次分散,采用超聲波細(xì)胞粉碎機在550W的功率下超聲35min,然后將得到的分散液放置于液氮中,快速冷卻,等完全凍結(jié)后置于冷凍干燥機中,將水除去,得到泡沫化預(yù)分散的石墨烯-石墨烯微片;(3)將泡沫化預(yù)分散的石墨烯-石墨烯微片與氰酸酯樹脂混合,再次通過高速攪拌、三輥研磨,將石墨烯-石墨烯微片分散在氰酸酯樹脂中,其中泡沫化預(yù)分散的石墨烯-石墨烯微片所占的質(zhì)量百分含量為10%,氰酸酯樹脂所占的質(zhì)量百分含量為90%,其中氰酸酯樹脂由雙酚A型氰酸脂:雙酚A型環(huán)氧樹脂:雙馬來酰亞胺樹脂=90:7.5:2.5的質(zhì)量比配制而成;(4)按照上述配方比例均勻混合,混合過程中抽真空脫氣,并澆注固化成型,得到所述石墨烯/氰酸酯復(fù)合材料。實施例6(1)按照石墨烯:石墨烯微片:π-π共軛小分子:去離子水=1:9:0.5:89.5的質(zhì)量比配制,混合后,采用高速攪拌機、三輥研磨機進(jìn)行預(yù)分散;其中π-π共軛小分子為1-卟啉;(2)將預(yù)分散后的水溶液置于冰浴環(huán)境中,利用超聲波細(xì)胞粉碎機進(jìn)行再次分散,采用超聲波細(xì)胞粉碎機在750W的功率下超聲55min,然后將得到的分散液放置于液氮中,快速冷卻,等完全凍結(jié)后置于冷凍干燥機中,將水除去,得到泡沫化預(yù)分散的石墨烯-石墨烯微片;(3)將泡沫化預(yù)分散的石墨烯-石墨烯微片與氰酸酯樹脂混合,再次通過高速攪拌、三輥研磨,將石墨烯-石墨烯微片分散在氰酸酯樹脂中,其中泡沫化預(yù)分散的石墨烯-石墨烯微片所占的質(zhì)量百分含量為15%,氰酸酯樹脂所占的質(zhì)量百分含量為85%,其中氰酸酯樹脂由雙酚A型氰酸脂:雙酚A型環(huán)氧樹脂:雙馬來酰亞胺樹脂=90:7.5:2.5的質(zhì)量比配制而成;(4)按照上述配方比例均勻混合,混合過程中抽真空脫氣,并澆注固化成型,得到所述石墨烯/氰酸酯復(fù)合材料。實施例7(1)按照石墨烯:石墨烯微片:π-π共軛小分子:去離子水=2:9:1:88的質(zhì)量比配制,混合后,采用高速攪拌機、三輥研磨機進(jìn)行預(yù)分散;其中π-π共軛小分子為1-卟啉;(2)將預(yù)分散后的水溶液置于冰浴環(huán)境中,利用超聲波細(xì)胞粉碎機進(jìn)行再次分散,采用超聲波細(xì)胞粉碎機在650W的功率下超聲50min,然后將得到的分散液放置于液氮中,快速冷卻,等完全凍結(jié)后置于冷凍干燥機中,將水除去,得到泡沫化預(yù)分散的石墨烯-石墨烯微片;(3)將泡沫化預(yù)分散的石墨烯-石墨烯微片與氰酸酯樹脂混合,再次通過高速攪拌、三輥研磨,將石墨烯-石墨烯微片分散在氰酸酯樹脂中,其中泡沫化預(yù)分散的石墨烯-石墨烯微片所占的質(zhì)量百分含量為11.5%,氰酸酯樹脂所占的質(zhì)量百分含量為88.5%,其中氰酸酯樹脂由雙酚A型氰酸脂:雙酚A型環(huán)氧樹脂:雙馬來酰亞胺樹脂=90:7.5:2.5的質(zhì)量比配制而成;(4)按照上述配方比例均勻混合,混合過程中抽真空脫氣,并澆注固化成型,得到所述石墨烯/氰酸酯復(fù)合材料。實施例8(1)按照石墨烯:石墨烯微片:π-π共軛小分子:去離子水=5:2:0.1:92.9的質(zhì)量比配制,混合后,采用高速攪拌機、三輥研磨機進(jìn)行預(yù)分散;其中π-π共軛小分子為1-卟啉;(2)將預(yù)分散后的水溶液置于冰浴環(huán)境中,利用超聲波細(xì)胞粉碎機進(jìn)行再次分散,采用超聲波細(xì)胞粉碎機在200W的功率下超聲60min,然后將得到的分散液放置于液氮中,快速冷卻,等完全凍結(jié)后置于冷凍干燥機中,將水除去,得到泡沫化預(yù)分散的石墨烯-石墨烯微片;(3)將泡沫化預(yù)分散的石墨烯-石墨烯微片與氰酸酯樹脂混合,再次通過高速攪拌、三輥研磨,將石墨烯-石墨烯微片分散在氰酸酯樹脂中,其中泡沫化預(yù)分散的石墨烯-石墨烯微片所占的質(zhì)量百分含量為6%,氰酸酯樹脂所占的質(zhì)量百分含量為94%,其中氰酸酯樹脂由雙酚A型氰酸脂:雙酚A型環(huán)氧樹脂:雙馬來酰亞胺樹脂=90:7.5:2.5的質(zhì)量比配制而成;(4)按照上述配方比例均勻混合,混合過程中抽真空脫氣,并澆注固化成型,得到所述石墨烯/氰酸酯復(fù)合材料。對比例1與實施例1相比,除采用氧化石墨烯替代石墨烯,即步驟(1)采用如下操作外,其它與實施例1相同。(1)按照氧化石墨烯:石墨烯微片:π-π共軛小分子:去離子水=0.5:10:0.5:89的質(zhì)量比配制,混合后,采用高速攪拌機、三輥研磨機進(jìn)行預(yù)分散;其中π-π共軛小分子為1-吡啶酸琥珀酰亞胺酯。對比例2與實施例1相比,除采用氧化石墨烯替代石墨烯微片外,即步驟(1)采用如下操作外,其它與實施例1相同。(1)按照石墨烯:氧化石墨烯:π-π共軛小分子:去離子水=0.5:10:0.5:89的質(zhì)量比配制,混合后,采用高速攪拌機、三輥研磨機進(jìn)行預(yù)分散;其中π-π共軛小分子為1-吡啶酸琥珀酰亞胺酯。對比例3與實施例1相比,除采用氧化石墨烯替代石墨烯和石墨烯微片外,即步驟(1)采用如下操作外,其它與實施例1相同。(1)按照氧化石墨烯:π-π共軛小分子:去離子水=10.5:0.5:89的質(zhì)量比配制,混合后,采用高速攪拌機、三輥研磨機進(jìn)行預(yù)分散;其中π-π共軛小分子為1-吡啶酸琥珀酰亞胺酯。對比例4與實施例1相比,除省略π-π共軛小分子,即步驟(1)采用如下操作外,其它與實施例1相同。(1)按照石墨烯:石墨烯微片:去離子水=0.5:10:89.5的質(zhì)量比配制,混合后,采用高速攪拌機、三輥研磨機進(jìn)行預(yù)分散。將實施例1~8和對比例1~4制備得到的石墨烯/氰酸酯復(fù)合材料進(jìn)行性能測試,其測試結(jié)果如表1~2所示。表1表2項目對比例1對比例2對比例3對比例4拉伸強度(MPa)72.671.670.668.2拉伸模量(GPa)3.463.543.423.33彎曲強度(MPa)123.5126.3125.1112.8彎曲模量(GPa)3.893.923.723.64電導(dǎo)率(S/m)2.65×10-42.6×10-81.2×10-81.38×10-3熱導(dǎo)率(Wm-1k-1)0.4160.3100.350.386熱膨脹系數(shù)5.29×10-55.34×10-55.31×10-55.35×10-580℃粘度(Pa.s)0.510.760.680.64通過上述結(jié)果可以看出,本發(fā)明制備的石墨烯-石墨烯微片在氰酸酯樹脂中分散良好,在低含量、低粘度下,電導(dǎo)率、熱導(dǎo)率和力學(xué)性能提高,熱膨脹系數(shù)降低,可用于航天器導(dǎo)電、導(dǎo)熱、低熱膨脹系數(shù)結(jié)構(gòu)復(fù)合材料構(gòu)件中。申請人聲明,本發(fā)明通過上述實施例來說明本發(fā)明的詳細(xì)結(jié)構(gòu)特征,但本發(fā)明并不局限于上述詳細(xì)結(jié)構(gòu)特征,即不意味著本發(fā)明必須依賴上述詳細(xì)結(jié)構(gòu)特征才能實施。所屬
技術(shù)領(lǐng)域:
的技術(shù)人員應(yīng)該明了,對本發(fā)明的任何改進(jìn),對本發(fā)明所選用部件的等效替換以及輔助部件的增加、具體方式的選擇等,均落在本發(fā)明的保護(hù)范圍和公開范圍之內(nèi)。以上詳細(xì)描述了本發(fā)明的優(yōu)選實施方式,但是,本發(fā)明并不限于上述實施方式中的具體細(xì)節(jié),在本發(fā)明的技術(shù)構(gòu)思范圍內(nèi),可以對本發(fā)明的技術(shù)方案進(jìn)行多種簡單變型,這些簡單變型均屬于本發(fā)明的保護(hù)范圍。另外需要說明的是,在上述具體實施方式中所描述的各個具體技術(shù)特征,在不矛盾的情況下,可以通過任何合適的方式進(jìn)行組合,為了避免不必要的重復(fù),本發(fā)明對各種可能的組合方式不再另行說明。此外,本發(fā)明的各種不同的實施方式之間也可以進(jìn)行任意組合,只要其不違背本發(fā)明的思想,其同樣應(yīng)當(dāng)視為本發(fā)明所公開的內(nèi)容。當(dāng)前第1頁1 2 3