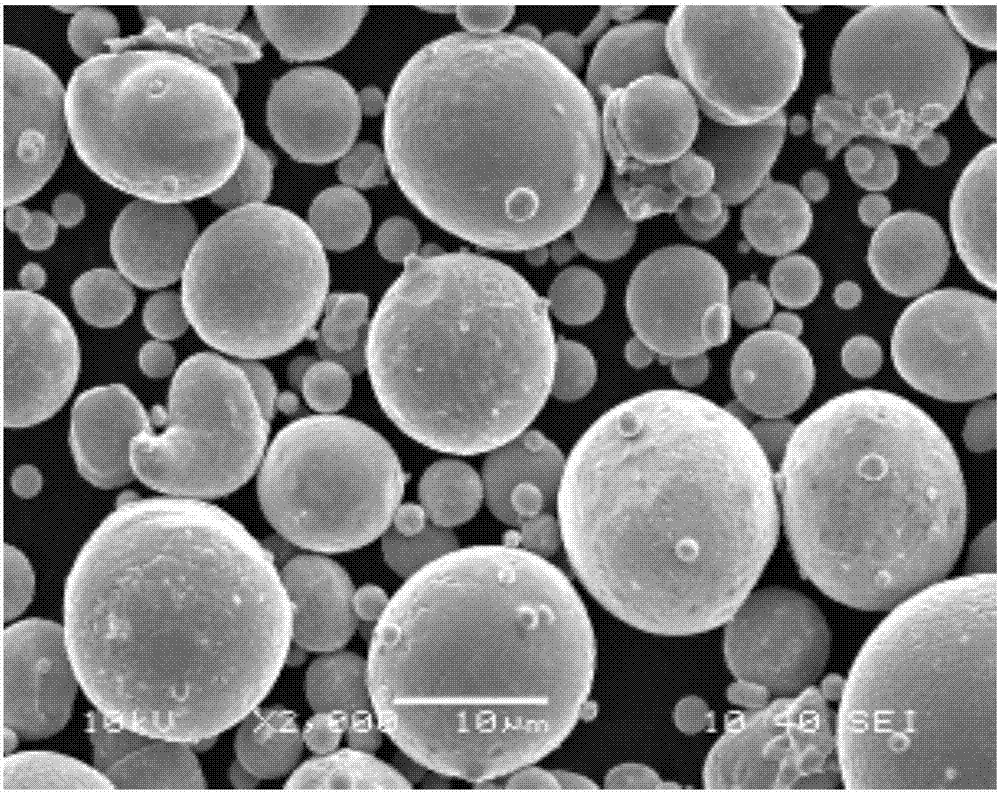
本發(fā)明涉及鈷鉻合金粉末及其制備方法和應(yīng)用,屬于牙科增材制造技術(shù)領(lǐng)域。
背景技術(shù):牙科患病率在世界范圍內(nèi)都很高,僅僅中國的牙病患者就達(dá)8億之多。其中牙體缺損和牙列缺失是最常見的牙科病患,通常采用義齒進(jìn)行修復(fù)。鎳鉻合金是傳統(tǒng)牙科鑄造工藝中最為常見的合金材料,但是鎳鉻合金中因?yàn)楹墟囋兀菀讓?dǎo)致過敏反應(yīng),因此這種合金材料已經(jīng)逐漸被淘汰。鈷鉻合金因其具有良好的機(jī)械性能、生物相容性以及耐腐蝕性,成為了目前最常用的牙科合金材料,被廣泛應(yīng)用于制造金屬烤瓷冠橋和可摘局部金屬支架等牙科修復(fù)體。目前常用鈷鉻合金修復(fù)體的加工方式為熔模失蠟鑄造法,但其加工過程繁瑣、耗時(shí)長、原材料品質(zhì)保障率低,且修復(fù)體精確性和質(zhì)量會因操作人員的不同存在較大誤差,鑄造過程中化學(xué)雜質(zhì)容易嵌入牙冠,形成大量縮孔和沙眼,影響精度和金瓷結(jié)合力。因此熔模失蠟鑄造的加工方法已經(jīng)不能滿足當(dāng)前高性能、自動快速的修復(fù)體制作要求。金屬增材制造成型技術(shù)作為一種新型的精密制造手段,結(jié)合計(jì)算機(jī)三維建模與計(jì)算機(jī)輔助設(shè)計(jì),使其具有替代傳統(tǒng)義齒鑄造工藝的潛能。增材制造技術(shù)具有個(gè)性化程度高、工序簡單、制作周期短、材料利用率高等優(yōu)點(diǎn),恰好可以滿足口腔修復(fù)個(gè)性化、復(fù)雜化、高難度的技術(shù)要求,同時(shí)彌補(bǔ)現(xiàn)有技術(shù)的不足,因此金屬增材制造已經(jīng)越來越多的被應(yīng)用到口腔修復(fù)體的制造當(dāng)中,成為了口腔數(shù)字化加工不可或缺的新興技術(shù)。金屬增材制造應(yīng)用在牙科加工中,需要使用與加工技術(shù)相匹配的金屬粉末。但是目前在牙科增材制造中使用的鈷鉻合金粉末存在以下問題:1.鈷鉻合金粉末大部分采用氣霧化方法加工,生產(chǎn)出來的粉末球形度較差,衛(wèi)星球顆粒多,流動性差,直接影響增材制造的加工質(zhì)量。且氣霧化制備的鈷鉻粉末氧含量和氮含量高,粉末還會存在空心球,導(dǎo)致最終成型件內(nèi)部有氣孔,影響使用性能。2.目前的鈷鉻合金粉末為了保證后續(xù)的機(jī)械性能,會加入鈹、鎘和鎳等元素,這些元素的存在會影響鈷鉻合金的生物相容性。修復(fù)體安裝到患者口內(nèi)后,會因?yàn)橛泻饘匐x子析出,影響患者健康。3.目前的鈷鉻粉末基本都是針對工業(yè)制造生產(chǎn)的,因此粉末的粒徑范圍、松裝密度等理化參數(shù)無法很好的與增材制造要求相匹配。因此,亟需一種牙科增材制造專用鈷鉻合金粉末的制備方法,使制備出的粉末能夠滿足增材制造和牙科修復(fù)的嚴(yán)格要求。
技術(shù)實(shí)現(xiàn)要素:針對以上問題,本發(fā)明解決的技術(shù)問題是提供一種牙科增材制造專用的鈷鉻合金粉末。本發(fā)明鈷鉻合金粉末,其化學(xué)成分由以下重量百分比的組分組成:Cr:24~27%,Mo:6~9%,Cu:2~4%,Mn:1~2%,O:<0.05%,N:<0.02%,余量為Co。優(yōu)選由以下重量百分比的組分組成:Cr:24.5%,Mo:7.5%,Cu:3.5%,Mn:1.5%,O:<0.05%,N:<0.02%,余量為Co。進(jìn)一步的,所述鈷鉻合金粉末的粒徑為15~106μm,松裝密度為4~5g/cm3,霍爾流動性為28~35s/50g。作為優(yōu)選方案,所述鈷鉻合金粉末的粒徑為15~45μm,松裝密度為4.4~4.5g/cm3,霍爾流動性為33~35s/50g;或者所述鈷鉻合金粉末的粒徑為20~63μm,松裝密度為4.3~4.4g/cm3,霍爾流動性為26~30s/50g;或者所述鈷鉻合金粉末的粒徑為45~106μm,松裝密度為4.3~4.4g/cm3,霍爾流動性為28~30s/50g。本發(fā)明解決的第二個(gè)技術(shù)問題是提供一種鈷鉻合金粉末的制備方法。本發(fā)明鈷鉻合金粉末的制備方法,包括如下步驟:a、熔化和霧化:在惰性氣體氛圍的制粉倉中,采用等離子體火炬將鈷鉻合金絲熔化和霧化,形成高溫小液滴;b、冷卻:向制粉倉中通入溫度為300~500℃的惰性氣流,層流冷卻高溫小液滴,得到鈷鉻合金粉末;其中,a步驟的惰性氣體和b步驟的惰性氣流均為氬氣或氦氣。進(jìn)一步的,所述鈷鉻合金絲直徑為3~20mm。優(yōu)選的,所述鈷鉻合金絲采用如下方法制備:將金屬單質(zhì)粉末按照權(quán)利要求1或2所述的組分及重量百分比混合,然后通過熱等靜壓方法壓制成預(yù)合金塊,再采用滑動拉絲機(jī),將預(yù)合金塊加工成直徑為3~20mm的絲材;其中熱等靜壓的條件為950~1050℃,100~150Mpa,保溫160~180分鐘。進(jìn)一步的,b步驟中,所述惰性氣流的進(jìn)氣口處氣壓為0.2~0.5Mpa。進(jìn)一步的,制粉倉中的氧含量不超過0.1%。本發(fā)明還提供本發(fā)明鈷鉻合金粉末在牙科增材制造中的應(yīng)用。與現(xiàn)有技術(shù)相比,本發(fā)明具有如下有益效果:1)本發(fā)明的鈷鉻合金粉末,采用特定的成分及配比,不僅使合金密度降低,實(shí)現(xiàn)了最終產(chǎn)品的輕量化,還在保證使用性能的同時(shí),杜絕了最終的牙科鈷鉻合金中鈹、鎘和鎳帶來的毒性,大大增強(qiáng)了鈷鉻合金的生物相容性,是牙科修復(fù)的理想材料。2)本發(fā)明的鈷鉻合金粉末的制備方法,操作簡單,制備得到的粉末具有球形度好、空心球顆粒少、流動性好等優(yōu)勢,完全能夠滿足金屬增材制造對于粉末的要求。附圖說明圖1是本發(fā)明實(shí)施例1制備的鈷鉻合金粉末的微觀形貌圖。(篩分后,粒徑范圍為15~45微米)圖2是本發(fā)明對比例1制備的鈷鉻合金粉末的微觀形貌圖。具體實(shí)施方式本發(fā)明鈷鉻合金粉末,其化學(xué)成分由以下重量百分比的組分組成:Cr:24~27%,Mo:6~9%,Cu:2~4%,Mn:1~2%,O:<0.05%,N:<0.02%,余量為Co。與傳統(tǒng)鈷鉻合金相比,本發(fā)明在元素配比中取消了W元素的加入,加入了Mn元素,用于取代W元素固溶強(qiáng)化作用;增加了Mo元素的含量,保證了鈷鉻合金的硬度和耐磨性;不加入Be(鈹)元素和Cd(鎘)元素,不加入Ni元素,增加Cu元素的含量,用于代替Be元素和Cd元素增加合金塑性的作用,并代替Ni元素的活性元素作用。采用本發(fā)明的合金元素配比,制備出的牙科鈷鉻合金理論密度將小于8.3g/cm3,遠(yuǎn)低于傳統(tǒng)鈷鉻合金的8.9g/cm3。采用本發(fā)明的成分配比,不僅使合金密度降低,實(shí)現(xiàn)了最終產(chǎn)品的輕量化,還在保證使用性能的同時(shí),杜絕了最終的牙科鈷鉻合金中鈹、鎘和鎳帶來的毒性,大大增強(qiáng)了鈷鉻合金的生物相容性。進(jìn)一步的,優(yōu)選由以下重量百分比的組分組成:Cr:24.5%,Mo:7.5%,Cu:3.5%,Mn:1.5%,O:<0.05%,N:<0.02%,余量為Co。本發(fā)明的鈷鉻合金粉末,其粒徑為15~106μm,松裝密度為4~5g/cm3,霍爾流動性為28~35s/50g。進(jìn)一步的,優(yōu)選所述鈷鉻合金粉末的粒徑為15~45μm,松裝密度為4.4~4.5g/cm3,霍爾流動性為33~35s/50g;或者所述鈷鉻合金粉末的粒徑為20~63μm,松裝密度為4.3~4.4g/cm3,霍爾流動性為26~30s/50g?;蛘咚鲡掋t合金粉末的粒徑為45~106μm,松裝密度為4.3~4.4g/cm3,霍爾流動性為28~30s/50g。其中,15~45μm和20~63μm的粒徑范圍可用于激光熔化粉床式成型技術(shù),45~106μm的粒徑范圍可用于激光同軸送粉或電子束熔化粉床式成型技術(shù)。本發(fā)明鈷鉻合金粉末的制備方法,包括如下步驟:a、熔化和霧化:在惰性氣體氛圍的制粉倉中,采用等離子體火炬將鈷鉻合金絲熔化和霧化,形成高溫小液滴;b、冷卻:向制粉倉中通入溫度為300~500℃的惰性氣流,層流冷卻高溫小液滴,得到鈷鉻合金粉末;其中,a步驟的惰性氣體和b步驟的惰性氣流均為氬氣或氦氣。其中,所述鈷鉻合金絲直徑優(yōu)選為3~20mm。本發(fā)明方法可以采用工業(yè)化的鈷鉻合金絲作為原料。但是,為了獲得更適合牙科修復(fù)體要求的鈷鉻合金成分,本發(fā)明鈷鉻合金絲優(yōu)選采用如下方法制備得到:將高純度的金屬單質(zhì)粉末按照本發(fā)明所述的鈷鉻合金組分以重量百分比的嚴(yán)格要求(即保證合金的組分如下:Cr:24~27%,Mo:6~9%,Cu:2~4%,Mn:1~2%,余量為Co),均勻混合,然后通過熱等靜壓方法壓制成預(yù)合金塊,再采用滑動拉絲機(jī),將預(yù)合金塊加工成直徑為3~20mm的均勻絲材;其中熱等靜壓的條件為950~1050℃,100~150Mpa,保溫160~180分鐘。a步驟中,采用等離子火炬作為絲材合金熔化和霧化的手段。優(yōu)選等離子體火炬采用氬氣作為工作氣體。氬氣電離后產(chǎn)生等離子體,提供數(shù)千度的溫度,可以瞬間熔化高熔點(diǎn)難熔金屬;同時(shí),等離子體內(nèi)電能轉(zhuǎn)化為動能,產(chǎn)生高速高溫的氬氣流,將熔化后的金屬液霧化成球形粉末。制粉過程中,絲材原料以均勻速度流入制粉倉,到達(dá)等離子火炬加工熔化區(qū)之后,金屬絲材被等離子體瞬間融化,接著被高速高溫的氬氣流霧化成球形粉末。本發(fā)明的制粉過程中,合金熔化和霧化幾乎是在同時(shí)進(jìn)行,減少了合金熔煉過程中被氧化或氮化的可能。而且對比氣霧化制備的粉末,空心球顆粒很少。由于霧化過程中使用的是高溫氬氣,使顆粒凝固被延遲,直到表面張力完成球化過程,得到高球形度。b步驟的冷卻采用的是熱氣流層流冷卻方法。本發(fā)明所述的層流冷卻為緩慢通入冷卻氣流,使制粉倉中的氣體保持緩慢的流速,霧化后的金屬粉末在重力的作用下緩慢下降并冷卻,防止金屬粉末間的碰撞以及與制粉倉壁的碰撞,從而影響球形度。本發(fā)明可以采用常規(guī)的方法實(shí)現(xiàn)熱氣流層流冷卻,優(yōu)選通過如下方法實(shí)現(xiàn):控制惰性氣流的進(jìn)氣口處氣壓為0.2~0.5Mpa。在冷卻氣流的進(jìn)氣口設(shè)置了足夠的氣壓,進(jìn)氣口和出氣口位于制粉倉不同的高度,能夠?qū)崿F(xiàn)冷卻氣流的層間流動,對粉末實(shí)現(xiàn)層流冷卻。層流冷卻的氣體流動,使粉末在冷卻過程中快速分散,防止粉末團(tuán)聚和粘附。用高于300℃的氬氣流冷卻粉末,延長液態(tài)顆粒冷卻為固態(tài)顆粒的時(shí)間,保證顆粒在凝固過程中有足夠時(shí)間在表面張力的作用下形成球形,防止制粉倉中的粉末冷卻過快,影響球形度和產(chǎn)生衛(wèi)星球。為了保證冷卻效果,通入氬氣流的溫度優(yōu)選不超過500℃。為了防止粉末受到氧化影響,優(yōu)選制粉倉中的氧含量不超過0.1%。本發(fā)明可采用常規(guī)設(shè)備來實(shí)現(xiàn)發(fā)明目的。優(yōu)選采用如下設(shè)備:該設(shè)備包括等離子體炬、霧化倉、向霧化倉送料的送料系統(tǒng)、與霧化倉相連的粉末收集裝置、與粉末收集裝置相連的氣體凈化循環(huán)系統(tǒng);所述氣體凈化循環(huán)系統(tǒng)包括氣體循環(huán)動力裝置;在霧化倉上設(shè)有進(jìn)氣口;所述氣體循環(huán)動力裝置與霧化倉的進(jìn)氣口管路連接;在氣體循環(huán)動力裝置與進(jìn)氣口的通路上設(shè)有加熱器和控制進(jìn)氣口處的進(jìn)氣壓的電磁閥;在霧化倉上設(shè)有排氣口,所述排氣口與進(jìn)氣口相對設(shè)置,所述排氣口與氣體循環(huán)動力裝置管路連接;所述排氣口位于霧化倉的頂部。制粉結(jié)束后,還可以對收集的粉末進(jìn)行篩分。優(yōu)選采用氬氣保護(hù)的超聲振動篩進(jìn)行粉末篩分,為了滿足金屬增材制造對粉末粒徑的要求,將粉末篩分成15~45μm、20~63μm和45~106μm三個(gè)粒徑范圍。本發(fā)明鈷鉻合金粉末,可作為原材料在牙科增材制造中使用,其中,15~45μm和20~63μm的粒徑范圍用于激光熔化粉床式成型技術(shù),45~106μm的粒徑范圍用于激光同軸送粉和電子束熔化粉床式成型技術(shù)。下面結(jié)合實(shí)施例對本發(fā)明的具體實(shí)施方式做進(jìn)一步的描述,并不因此將本發(fā)明限制在所述的實(shí)施例范圍之中。實(shí)施例1a、原材料制備階段將高純度的單質(zhì)合金粉末按照成分要求,均勻混合,然后通過熱等靜壓方法壓制成預(yù)合金塊。其中熱等靜壓的條件是1050℃,140Mpa,保溫160分鐘。本牙科鈷鉻合金按照以下化學(xué)成分進(jìn)行配比:Cr:24.5%,Mo:7.5%,Cu:3.5%,Mn:1.5%,余量為Co。接著采用滑動拉絲機(jī),將鈷鉻合金塊加工成直徑為10mm的均勻絲材。b、等離子熔化和霧化階段制粉過程中,絲材原料以均勻速度流入制粉倉,到達(dá)以氬氣為工作氣體的等離子火炬加工熔化區(qū)之后,金屬絲材被等離子體瞬間融化,接著被高速高溫的氬氣流霧化成球形粉末。c、熱氣流層流冷卻階段粉末冷卻和回收過程中,通入溫度為320℃的氬氣流層流冷卻,控制氬氣流的進(jìn)氣口處氣壓為0.2Mpa。在制粉倉安裝了氧含量監(jiān)測儀,實(shí)時(shí)監(jiān)測內(nèi)部氧含量,當(dāng)氧含量超過0.1%時(shí),制粉過程會中斷并報(bào)警,防止粉末受到氧化影響。d、超聲振動篩分階段本階段將制備結(jié)束后收集的粉末進(jìn)行篩分。采用氬氣保護(hù)的超聲振動篩進(jìn)行粉末篩分,為了滿足金屬增材制造對粉末粒徑的要求,將粉末篩分成15~45μm、20~63μm和45~106μm三個(gè)粒徑范圍。其中15~45μm和20~63μm的粒徑范圍用于激光熔化粉床式成型技術(shù),45~106μm的粒徑范圍用于激光同軸送粉和電子束熔化粉床式成型技術(shù)。篩分之后對粉末進(jìn)行檢驗(yàn)測試,測試粉末化學(xué)成分、顆粒球形度、松裝密度和流動性等參數(shù),得到測量數(shù)據(jù)之后,出具每一批材料的材質(zhì)書。其中制備出的鈷鉻合金粉末化學(xué)成分如表1所示,其中粉末的含氧量低于0.05%,含氮量低于0.02%。制備出的鈷鉻合金粉末如圖1所示為高球形、顆粒均勻,且衛(wèi)星球顆粒少。其中松裝密度和流動性數(shù)據(jù)如表2所示。:實(shí)施例2按照實(shí)施例1的方法,僅改變鈷鉻合金的成分,按照以下化學(xué)成分進(jìn)行配比:Cr:24%,Mo:6%,Cu:4%,Mn:2%,余量為Co。得到的制備出的鈷鉻合金粉末化學(xué)成分如表1所示,松裝密度和流動性數(shù)據(jù)如表2所示。實(shí)施例3按照實(shí)施例1的方法,僅改變鈷鉻合金的成分,按照以下化學(xué)成分進(jìn)行配比:Cr:27%,Mo:9%,Cu:2%,Mn:1%,余量為Co。得到的制備出的鈷鉻合金粉末化學(xué)成分如表1所示,松裝密度和流動性數(shù)據(jù)如表2所示。實(shí)施例4按照實(shí)施例1的方法,僅在熱氣流層流冷卻階段,通入溫度為350℃的氬氣流層流冷卻,控制氬氣流的進(jìn)氣口處氣壓為0.5Mpa。合金成分及其余步驟均同實(shí)施例1。由此制備得到的鈷鉻合金粉末,為高球形、顆粒均勻,且衛(wèi)星球顆粒少。其中松裝密度和流動性數(shù)據(jù)如表2所示。對比例1在熱氣流層流冷卻階段,通入室溫氬氣層流冷卻,合金成分及其余步驟均同實(shí)施例1。由此制備得到的鈷鉻合金粉末,球形度不夠好,而且衛(wèi)星球顆粒增多,導(dǎo)致粉末流動性變差。粉末微觀形貌如圖2所示,其中松裝密度和流動性數(shù)據(jù)如表2所示。對比例2在熱氣流層流冷卻階段,控制氬氣流的進(jìn)氣口處氣壓為0.8Mpa,合金成分及其余步驟均同實(shí)施例1。由此制備得到的鈷鉻合金粉末,衛(wèi)星球顆粒也增多,影響粉末流動性,其中松裝密度和流動性數(shù)據(jù)如表2所示。表1鈷鉻合金粉末成分及密度表2鈷鉻合金粉末理化性能