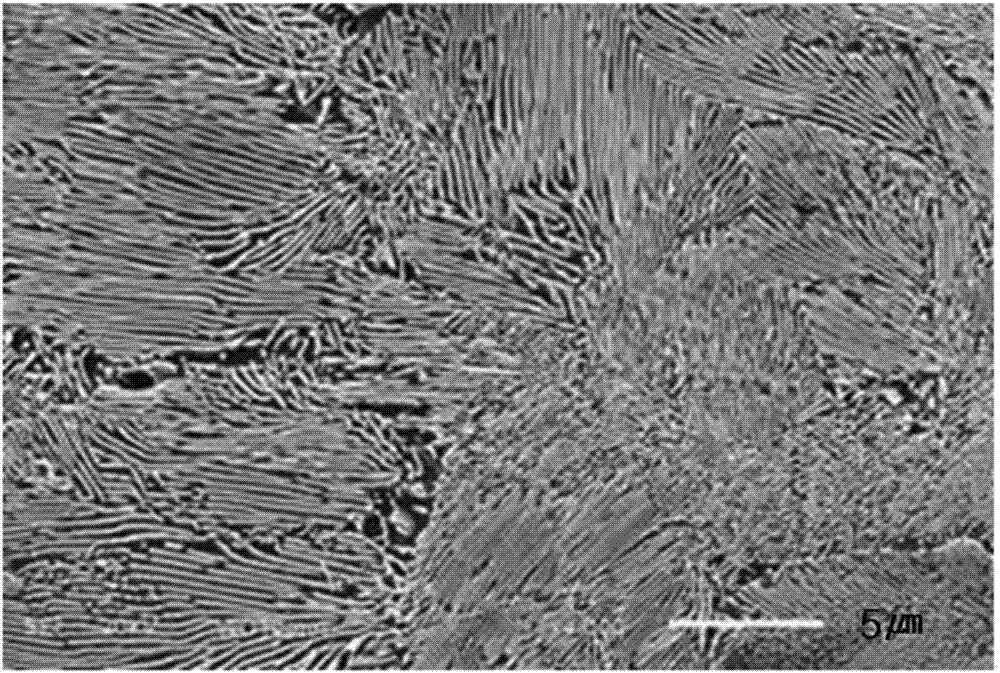
本發(fā)明涉及一種耐蝕性優(yōu)異的高碳鋼線材、鋼絲及其制造方法。
背景技術(shù):
:起重機(jī)繩索、普通橋梁用纜索等起到支撐構(gòu)筑物,或在船舶或其他位置移送物品時(shí)支撐負(fù)載的作用。在實(shí)際環(huán)境中,這些起重機(jī)繩索和普通橋梁用纜索不是以單根鋼絲的形狀被使用,而是以多根鋼絲擰成的形狀被使用,已知其厚度有多種,最小50mm到1000mm不等。繩索線直徑的增加表示構(gòu)筑物重量的增加,減少重量的最有效的方法是增加形成繩索的鋼絲的強(qiáng)度。鋼絲的強(qiáng)度直接關(guān)系到產(chǎn)品輕量化的問題,因此鋼絲用鋼種的研發(fā)方向以高強(qiáng)度化為主。鋼絲高強(qiáng)度化是依據(jù)1960年代恩伯里(Embury)和菲舍爾(Fisher)提出的實(shí)驗(yàn)式。根據(jù)該實(shí)驗(yàn)式,提高強(qiáng)度的最有效的方法有(1)增加材料的強(qiáng)度、(2)提高根據(jù)能夠防止位錯(cuò)運(yùn)行的初期組織的微細(xì)化的加工硬化率、(3)增加拉伸加工量等。根據(jù)材料強(qiáng)度增加及控制組織的加工硬化率的提高,主要利用添加合金元素,其中,C起到固溶強(qiáng)化及析出強(qiáng)化效果的作用,Cr起到在奧氏體中使C的擴(kuò)散低下及由此引起的成核位點(diǎn)增加所帶來(lái)的組織細(xì)微化及由此帶來(lái)的拉伸加工性的增加的作用,Si起到增加根據(jù)鐵素體內(nèi)固溶強(qiáng)化及珠光體組織微細(xì)化的初期強(qiáng)度的作用。最后,與前面所提及的根據(jù)添加合金元素的強(qiáng)度增加方法,拉伸加工量增加是能夠更有效地增加強(qiáng)度的方法,但是,已知根據(jù)實(shí)驗(yàn)室結(jié)果,增加拉伸加工量時(shí),強(qiáng)度將指數(shù)性地增加。其理由被解釋為,珠光體組織沿拉伸方向整體旋轉(zhuǎn)時(shí),以軟質(zhì)相與硬質(zhì)相層層存在的復(fù)合組織的形式存在,而且隨著拉伸加工量的增加,滲碳體內(nèi)存在的碳向鐵素體擴(kuò)散的含量會(huì)增加,并且這種碳過(guò)飽和于鐵素體內(nèi),從而起到與馬氏體相同的作用,這種組織的形成大大增加強(qiáng)度。但是,到目前為止主要是在理論上進(jìn)行說(shuō)明,還沒有得到實(shí)驗(yàn)驗(yàn)證。并且,上述構(gòu)筑物使用于鹽分較多的海邊等,為了抑制鹽分滲透到鋼中,作了以下努力:在鋼絲表面形成Zn、Zn-Al等鍍覆層,或如起重機(jī)繩索等的情況,在其表面涂上油來(lái)使對(duì)其的影響最小化。但是,在實(shí)際環(huán)境中,會(huì)不可避免地發(fā)生鍍層脫落或油被去除的情況,并且Fe與HCl、NaCl等產(chǎn)生反應(yīng),從而形成腐蝕坑,導(dǎo)致早起折損,從而只能更換繩索。并且,由于Zn由滑移系少的六方密堆積(HCP,hexagonalclosepacking)結(jié)構(gòu)構(gòu)成,從而具有大大降低拉伸性等使制造成本上升等問題,因此認(rèn)為應(yīng)通過(guò)鋼種設(shè)計(jì)及工序控制來(lái)減少上述問題。因此,需要開發(fā)一種強(qiáng)度優(yōu)異且即使沒有人為地形成鍍層也能夠具有優(yōu)異的耐蝕性的高碳鋼線材、鋼絲及其制造方法。技術(shù)實(shí)現(xiàn)要素:要解決的技術(shù)問題本發(fā)明的目的在于,提供一種抑制微細(xì)組織及合金組成,從而強(qiáng)度及耐蝕性優(yōu)異的高碳鋼線材、鋼絲及其制造方法。此外,本發(fā)明的技術(shù)問題并不限定于上述內(nèi)容,本發(fā)明的技術(shù)問題可由本說(shuō)明書的整體內(nèi)容來(lái)理解,對(duì)于本領(lǐng)域的技術(shù)人員來(lái)說(shuō),理解本發(fā)明的附加的技術(shù)問題沒有任何困難。技術(shù)方案本發(fā)明的一方面涉及一種強(qiáng)度及耐蝕性優(yōu)異的高碳鋼線材,其中,以重量%計(jì),所述高碳鋼材包含:0.9~1.1%的C、0.7~1.5%的Si、0.07~0.1%的Mn、0.3~0.8%的Cr、0.030%以下的P、0.010%以下的S、余量Fe及其他不可避免的雜質(zhì),并且微細(xì)組織包含95面積%以上的珠光體。本發(fā)明的另一方面涉及一種強(qiáng)度及耐蝕性優(yōu)異的高碳鋼鋼絲,其中,以重量%計(jì),所述高碳鋼鋼絲包含:0.9~1.1%的C、0.7~1.5%的Si、0.07~0.1%的Mn、0.3~0.8%的Cr、0.030%以下的P、0.010%以下的S、余量Fe及其他不可避免的雜質(zhì),并且微細(xì)組織包含95面積%以上的珠光體。本發(fā)明的另一方面涉及一種強(qiáng)度及耐蝕性優(yōu)異的高碳鋼線材的制造方法,所述方法包括以下步驟:將含有上述合金組成的鋼坯在1000~1100℃下維持90~120分鐘;在950~1050℃下對(duì)所述鋼坯進(jìn)行精軋,并以980~1050℃的最終軋制入口溫度進(jìn)行最終軋制,由此制得線材;以及在850~950℃下對(duì)所述線材進(jìn)行收卷,并在斯太爾摩冷卻區(qū)域以8~10℃/秒的冷卻速度進(jìn)行冷卻。補(bǔ)充而言,所述技術(shù)問題的解決方法中,并沒有全部列舉了本發(fā)明的特征。本發(fā)明的各種特征及由此帶來(lái)的優(yōu)點(diǎn)和效果,可以通過(guò)參照以下的具體實(shí)施方式理解得更加詳細(xì)。有益效果本發(fā)明帶來(lái)的效果為,提供強(qiáng)度及耐蝕性優(yōu)異的高碳鋼線材、鋼絲及其制造方法,并且由于具有優(yōu)異的耐蝕性,可以省略額外的Zn、Zn-Al等鍍覆處理、油(Oil)類的外部附著等,從而能夠減少制造成本,使得在產(chǎn)品競(jìng)爭(zhēng)力中具有優(yōu)勢(shì)。附圖說(shuō)明圖1為拍攝發(fā)明例1的線材的微細(xì)組織的照片。圖2為拍攝比較例5的線材的微細(xì)組織的照片。具體實(shí)施方式以下,對(duì)本發(fā)明的優(yōu)選實(shí)施方式進(jìn)行說(shuō)明。然而,本發(fā)明的實(shí)施方式可以變形為各種其它不同的方式,本發(fā)明的范圍并不限定于以下說(shuō)明的實(shí)施方式。此外,本發(fā)明的實(shí)施方式是為了向本
技術(shù)領(lǐng)域:
的技術(shù)人員更加完整地說(shuō)明本發(fā)明而提供的。本發(fā)明人為了增加目前使用的起重機(jī)繩索、一般橋梁用索等中使用的鋼絲的強(qiáng)度,以及提高它們的耐蝕性,以能夠省略額外的Zn、Zn-Al等的鍍覆處理、油(Oil)類的外部附著而進(jìn)行了深入的研究。其結(jié)果,本發(fā)明人確認(rèn),通過(guò)添加高含量的Cr能夠確保強(qiáng)度及耐蝕性,在此基礎(chǔ)上進(jìn)一步添加Ni時(shí),其效果會(huì)增加,當(dāng)進(jìn)一步復(fù)合添加Ni及Cu時(shí),其效果會(huì)進(jìn)一步增加,從而完成了本發(fā)明。強(qiáng)度及耐蝕性優(yōu)異的高碳鋼線材以下,對(duì)本發(fā)明的一方面的強(qiáng)度及耐蝕性優(yōu)異的高碳鋼線材進(jìn)行詳細(xì)的說(shuō)明。本發(fā)明的一方面的抗氫致開裂性優(yōu)異的線材,以重量%計(jì),包含0.9~1.1%的C、0.7~1.5%的Si、0.07~0.1%的Mn、0.3~0.8%的Cr、0.030%以下的P、0.010%以下的S、余量Fe及其他不可避免的雜質(zhì),并且微細(xì)組織包含95面積%以上的珠光體。首先,對(duì)本發(fā)明的合金組成進(jìn)行詳細(xì)的說(shuō)明。以下各合金元素的單位是重量%。C(碳):0.9~1.1%已知碳為提高材料強(qiáng)度的最有效的元素,在珠光體鋼中,當(dāng)C增加0.1%時(shí),能夠增加100Mpa的強(qiáng)度。當(dāng)添加超過(guò)0.9%的C時(shí),強(qiáng)度增加量逐漸減少,這是因?yàn)槠鰠^(qū)內(nèi)碳濃度增加,以及在該區(qū)域內(nèi)形成先共析滲碳體及形成厚的滲碳體的可能性大。當(dāng)C含量小于0.9%時(shí),難以確保高強(qiáng)度,當(dāng)C含量超過(guò)1.1%時(shí),大大增加中心偏析。因此C含量?jī)?yōu)選為0.9~1.1%。Si(硅):0.7~1.5%Si起到根據(jù)鐵素體固溶強(qiáng)化及微細(xì)化珠光體組織的增加強(qiáng)度的作用,當(dāng)添加0.1%的Si時(shí),提高14~16Mpa水平的強(qiáng)度。并且,Si由于存在于鐵素體與滲碳體界面,因此熱處理時(shí)起到抑制C的擴(kuò)散的作用,因此纜索等中使用的Si含量較高。當(dāng)Si含量小于0.7%時(shí),上述效果不充分,當(dāng)Si含量超過(guò)1.5%時(shí),表面上形成與母材緊貼性較大的Fe2SiO4氧化皮,從而降低氧化皮剝離性。Cr(鉻):0.3~0.8%Cr為僅次于C、N的能夠有效提高強(qiáng)度的元素,當(dāng)珠光體鋼中增加0.1%時(shí),能夠增加40~50Mpa的強(qiáng)度。并且,在拉伸公司進(jìn)行熱處理后能夠抑制滲碳體的異常組織的出現(xiàn)及形成厚的滲碳體。但是由于會(huì)增加鐵素體內(nèi)的位錯(cuò)密度,因此,使鐵素體延展性低下,從而在拉伸成極細(xì)線時(shí),有可能引起斷線。當(dāng)Cr含量小于0.3%時(shí),難以確保強(qiáng)度,當(dāng)Cr含量超過(guò)0.8%時(shí),碳化物形成所帶來(lái)的相變完成時(shí)間增加,導(dǎo)致制造效率下降。因此,Cr含量?jī)?yōu)選為0.3~0.8%。Mn(錳):0.07~0.1%Mn雖然也起到增加強(qiáng)度的作用,但是添加Mn的目的在于,當(dāng)客戶公司進(jìn)行鉛浴槽熱處理時(shí),確保用于充分延遲相變初起(nose)的淬透性。并且,由于容易與鋼中的S結(jié)合,因此也以脫硫作為目的而使用。為了脫硫,需要添加0.07%以上的量,本發(fā)明中因Cr與Si的含量高,能夠顯示出充分的淬透性效果,因此優(yōu)選將Mn的含量限制在0.1%以下。P:0.030%以下P為雜質(zhì),其含量沒有特別規(guī)定,但如同現(xiàn)有鋼絲,從確保延展性的方面考慮,其含量?jī)?yōu)先為0.030%以下。S:0.010%以下S為雜質(zhì),其含量沒有特別規(guī)定,但本發(fā)明中將Mn含量控制在低含量,因此為了容易進(jìn)行脫硫處理,S含量?jī)?yōu)選為0.010%以下。本發(fā)明中余量成分為鐵(Fe)。不過(guò),在通常的制造過(guò)程中,由于可能從原料或周圍環(huán)境中不可避免地混入雜質(zhì),因此不能排除這種情況。由于通常制造過(guò)程中的技術(shù)人員都知曉這些雜質(zhì),因此,在本發(fā)明中并不特別提及所述雜質(zhì)的所有內(nèi)容。此時(shí),通過(guò)在上述合金組成中進(jìn)一步添加0.2~0.6%的Ni,能夠進(jìn)一步提高耐蝕性,通過(guò)進(jìn)一步添加0.2~0.6%的Ni及0.6%以下的Cu(0%除外),能夠再進(jìn)一步提高耐蝕性。Ni:0.2~0.6%Ni為提高耐蝕性的元素,通過(guò)添加Ni,使銹的粒度微細(xì)化,降低鐵離子的溶解活性,從而銹和鋼界面的低pH化被抑制,并且形成的銹層的陽(yáng)離子選擇透過(guò)性增大,從而抑制氯離子滲透于銹層內(nèi),因此大幅提高了耐蝕性。Ni添加量越多,越能提高耐蝕性等。當(dāng)添加小于0.2%時(shí),沒有效果,當(dāng)添加0.6%以上時(shí),雖然耐蝕效果很大,但是價(jià)格昂貴,因此將其含量?jī)?yōu)選限制為0.6%以下。Cu(銅):0.6%以下(0%除外)Cu為通過(guò)銹層粒子的微細(xì)化及細(xì)密化來(lái)提高鋼的耐蝕性的元素,其含量越增加,耐蝕性越有效,但再加熱時(shí),低熔點(diǎn)的Cu會(huì)滲透到鋼的晶界中,從而當(dāng)進(jìn)行熱軋時(shí)會(huì)引起發(fā)生裂紋的熱脆性(hotshortness),因此優(yōu)選限制在0.6%以下。由于微量添加時(shí)也有效果,因此對(duì)下限不進(jìn)行特別的限定,但是當(dāng)添加0.2%以上時(shí),其效果會(huì)更加明顯。并且,當(dāng)不添加Ni而只添加Cu時(shí),在熱軋過(guò)程中熔融Cu會(huì)擴(kuò)散到晶界,從而發(fā)生缺陷,因此與Ni一起添加。以下,對(duì)本發(fā)明一方面的抗氫致開裂性優(yōu)異的線材的微細(xì)組織進(jìn)行說(shuō)明。本發(fā)明一方面的抗氫致開裂性優(yōu)異的線材的微細(xì)組織包含95面積%以上的珠光體。除了珠光體以外,可以包含5面積%以下的先共析滲碳體。并且,所述珠光體的平均層間距優(yōu)選為110~120nm。具有上述合金組成及微細(xì)組織的本發(fā)明的線材,具有1400Mpa以上的拉伸強(qiáng)度,斷面收縮率(ReductionofArea)為15%以上。強(qiáng)度及耐蝕性優(yōu)異的高碳鋼線材的制造方法對(duì)上述本發(fā)明的線材的制造方法不作特別限制,根據(jù)本發(fā)明的一種方法,強(qiáng)度及耐蝕性優(yōu)異的高碳鋼線材的制造方法包括以下步驟:將滿足上述合金組成的鋼坯在1000~1100℃下維持90~120分鐘;在950~1050℃下對(duì)所述鋼坯進(jìn)行精軋,并以980~1050℃的最終軋制入口溫度進(jìn)行最終軋制,由此制得線材;以及在850~950℃下對(duì)所述線材進(jìn)行收卷,并在斯太爾摩冷卻區(qū)域以8~10℃/秒的冷卻速度進(jìn)行冷卻。根據(jù)上述制造方法制造的線材包含95面積%以上的珠光體,具有1400Mpa以上的拉伸強(qiáng)度,斷面收縮率為15%以上。強(qiáng)度及耐蝕性優(yōu)異的高碳鋼鋼絲本發(fā)明的另一方面的強(qiáng)度及耐蝕性優(yōu)異的高碳鋼鋼絲具有上述合金組成,并且微細(xì)組織包含95面積%以上的珠光體。所述珠光體通過(guò)拉斯加工,可以具有以拉伸方向的方向性。此時(shí),所述珠光體的平均層間距可以為20~30nm。這是因?yàn)橥ㄟ^(guò)鉛浴淬火(LP)熱處理及拉伸工序,珠光體的平均層間距比線材更為微細(xì)化。并且,當(dāng)鋼絲表面形成銹時(shí),所述銹可以包含26面積%以上的晶粒大小為20nm以下的α-FeOOH(α-氫氧化鐵)。所述銹的余量部分由β-FeOOH(β-氫氧化鐵)、γ-FeOOH(γ-氫氧化鐵)等組成。非晶質(zhì)的α-FeOOH是抑制銹形成的相,β-FeOOH是使γ-FeOOH內(nèi)容易形成龜裂而促進(jìn)銹形成的相。晶粒越微細(xì)銹形成得越細(xì)密,從而耐候性方面有利,因此晶粒大小為20nm以下的α-FeOOH的面積分?jǐn)?shù)重要,當(dāng)包含26面積%以上的晶粒大小為20nm以下的α-FeOOH的面積分?jǐn)?shù)時(shí),可以確保優(yōu)異的耐候性及耐蝕性。α-FeOOH的面積分?jǐn)?shù)越高,越能提高耐蝕性,因此沒必要特別限定其上限,但由于難以形成50面積%以上,因此其上限可以是50面積%。具有上述合金組成及微細(xì)組織的本發(fā)明的鋼絲可以具有2400Mpa以上的拉伸強(qiáng)度,耐蝕性優(yōu)異,并且可能對(duì)扭轉(zhuǎn)加工的抵抗性優(yōu)異。強(qiáng)度及耐蝕性優(yōu)異的高碳鋼鋼絲的制造方法本發(fā)明的另一方面的強(qiáng)度及耐蝕性優(yōu)異的高碳鋼鋼絲的制造方法包括以下步驟:將根據(jù)上述線材的制造方法制造的線材加熱到950℃以上,并維持2分鐘以上;在鉛浴中進(jìn)行淬火,然后在580℃以上的溫度下維持1分鐘以上,然后進(jìn)行水冷卻;以及以100m/分以上的拉伸速度、以80%以上總變形量進(jìn)行干式拉伸,從而獲得鋼絲。根據(jù)所述制造方法制造的鋼絲的微細(xì)組織,包含95面積%的珠光體,具有2600Mpa以上的拉伸強(qiáng)度,耐蝕性優(yōu)異,并且對(duì)扭轉(zhuǎn)加工的抵抗性優(yōu)異,從而可以優(yōu)選適用于起重機(jī)繩索、一般橋梁用索等。以下,將通過(guò)實(shí)施例對(duì)本發(fā)明進(jìn)行更具體的說(shuō)明。但需要說(shuō)明的是,下述實(shí)施例僅僅是為了更加詳細(xì)的說(shuō)明本發(fā)明而提出的,并不是為了限定本發(fā)明的權(quán)利范圍。本發(fā)明的權(quán)利范圍由權(quán)利要求書中記載的事項(xiàng)和由此合理推導(dǎo)的事項(xiàng)所決定。(實(shí)施例)本發(fā)明中進(jìn)行了用于制造最終鋼絲的拉伸強(qiáng)度為2400Mpa以上且具有耐蝕性優(yōu)異的特性的鋼絲的實(shí)驗(yàn)。鑄造50kg的具有下述表1的合金組成(但,C、Si、Cr、Mn、Cu及Ni含量的單位是重量%,P及S含量的單位是ppm)的錠(ingot),然后進(jìn)行鋼坯-錠焊接,并進(jìn)行線材軋制。線材軋制條件為如下,加熱爐:在1030℃下維持90分鐘,精軋出口:1000℃,減定徑(RSM)入口溫度:990℃,冷卻后收卷溫度:900℃,斯太爾摩冷卻速度:8℃/秒。以上述條件來(lái)制造13mm的線材。用高溫加熱爐將所述線材加熱到980℃并維持3分鐘,并用鉛浴槽進(jìn)行淬火,由此得到鉛浴淬火(LP,LeadPatenting)熱處理材料。將所述LP熱處理材料在590℃下維持1.5分鐘,并進(jìn)行水冷卻,從而確保微細(xì)珠光體組織,然后通過(guò)干式拉伸,拉伸到直徑為5.32mm為止,由此制造了鋼絲。對(duì)上述線材及LP熱處理材料的拉伸強(qiáng)度(TS)、斷面收縮率(RA)、珠光體平均層間間隙(lp)進(jìn)行測(cè)定,并對(duì)上述鋼絲的拉伸強(qiáng)度(TS)及扭轉(zhuǎn)特性進(jìn)行測(cè)定,并顯示于下表2中。并且,將熱脆性(HS,HotShortness)的發(fā)生與否顯示在表2中。表1區(qū)分CSiCrMnCuNiPS比較例10.881.300.610.090.000.009699發(fā)明例10.981.300.620.100.000.009598發(fā)明例21.081.300.600.090.000.009999比較例21.181.300.600.100.000.009697比較例30.980.600.610.090.000.009599比較例40.981.550.620.090.000.009698比較例50.981.300.250.100.000.009595比較例60.981.290.920.100.000.009997發(fā)明例30.981.300.620.100.000.309598發(fā)明例40.981.300.620.100.000.609598比較例70.981.300.620.100.000.909598發(fā)明例50.981.300.620.100.100.309598發(fā)明例60.981.300.620.100.300.309598發(fā)明例70.981.300.620.100.600.309598比較例80.981.300.620.100.800.309598上述表1中C、Si、Cr、Mn、Cu及Ni含量的單位是重量%,P及S含量的單位是ppm。表2比較例1、2和發(fā)明例1、2顯示根據(jù)C含量變化的強(qiáng)度變化。對(duì)碳含量從0.88%增加到1.18%時(shí)的特性進(jìn)行了確認(rèn),其結(jié)果為,如已知技術(shù),雖然強(qiáng)度增加,但當(dāng)碳含量大幅增加時(shí),強(qiáng)度增加幅度減少。就比較例1而言,在最終拉伸后沒能達(dá)到目標(biāo)強(qiáng)度,就比較例2而言,進(jìn)行LP熱處理后拉伸時(shí)發(fā)生了斷裂。因此可以確認(rèn)C含量?jī)?yōu)選為0.9~1.1%。在將C含量固定為0.98%的狀態(tài)下,確認(rèn)了Si含量的影響力,通過(guò)發(fā)明例1、比較例3及比較例4可以知道其效果。Si是鐵素體固溶強(qiáng)化元素,因此添加Si時(shí)強(qiáng)度會(huì)增加,并且珠光體層間距也逐漸減少。當(dāng)Si含量為0.6%時(shí),最終鋼絲的拉伸強(qiáng)度為2335Mpa,低于目標(biāo)強(qiáng)度,當(dāng)Si含量為1.55%時(shí),不僅形成了Fe2SiO4氧化皮,并且LP熱處理后進(jìn)行拉伸時(shí)發(fā)生斷裂。Cr添加效果可以通過(guò)發(fā)明例1、比較例5及比較例6確認(rèn)。Cr如同Si,當(dāng)添加0.25%時(shí),強(qiáng)度增加的效果不大,添加0.9%時(shí),因形成碳化物等而在進(jìn)行拉伸時(shí)發(fā)生斷裂。圖1為拍攝發(fā)明例1的線材的微細(xì)組織的照片,圖2為拍攝比較例5的線材的微細(xì)組織的照片,比較圖1和比較例5,可以確認(rèn)添加Cr所帶來(lái)的片層(lamella)間隙的微細(xì)化。發(fā)明例1、3、4及比較例7是分別添加0%、0.3%、0.6%、0.9%的Ni的情況,可以確認(rèn)根據(jù)Ni含量的強(qiáng)度及扭轉(zhuǎn)變化。Ni雖然不是增加強(qiáng)度的元素,但大量添加時(shí),在進(jìn)行鉛浴槽熱處理時(shí),產(chǎn)生低溫組織。比較例7中的Ni含量為0.9%,因線材冷卻過(guò)程中所形成的馬氏體,拉伸試驗(yàn)時(shí)發(fā)生斷裂,同樣LP熱處理后也發(fā)生斷裂。發(fā)明例1,3,4中沒有觀察到此現(xiàn)象,并且可以確認(rèn)強(qiáng)度及扭轉(zhuǎn)特性相似。不添加Ni而單獨(dú)添加Cu時(shí),在熱軋過(guò)程中熔融Cu擴(kuò)散到晶界,從而會(huì)發(fā)生缺陷。與Ni一起添加時(shí),Ni抑制熔融Cu擴(kuò)散到晶界,因此,本發(fā)明中通過(guò)發(fā)明例5、6、7及比較例8來(lái)欲觀察不是單獨(dú)添加Cu而將Cu和Ni復(fù)合添加所帶來(lái)的效果。發(fā)明例5、6、7及比較例8顯示添加0.3%的Ni的鋼根據(jù)Cu含量增加的特性。隨著Cu含量的增加,強(qiáng)度幾乎沒有變化,但可以確認(rèn)到以0.9%的大量添加的比較例8發(fā)生了熱脆性。除了強(qiáng)度以外重要的是腐蝕特性,就反復(fù)腐蝕特性而言,按照如下條件對(duì)鋼線實(shí)施實(shí)驗(yàn)并確認(rèn)。但無(wú)法制造最終鋼絲的比較例2、4、6、7及8除外。在5%鹽水量(NaCl)及65%濕度的條件下,進(jìn)行噴霧16小時(shí),然后干燥8小時(shí),并重復(fù)進(jìn)行該步驟,并且試驗(yàn)次數(shù)維持了30天和60天,并評(píng)價(jià)了耐蝕性特性。上述條件是模擬沖繩海邊,欲間接模擬在鹽分量0.8mdd的海岸上經(jīng)過(guò)2年(維持30天)及4年(維持60天)左右時(shí)的腐蝕程度的差異,其結(jié)果顯示于下述表3中。下述表3中凹坑(pit)深度(a)及(b)的單位是μm。表3可以確認(rèn)發(fā)明例1~7的腐蝕深度差均為11μm以下,耐腐蝕性優(yōu)異。并且,可以確認(rèn)這種耐腐蝕性與銹中晶粒大小為20nm以下的α-FeOOH的相分?jǐn)?shù)具有密切的關(guān)聯(lián),發(fā)明例1~7滿足本發(fā)明中限制的α-FeOOH的相分?jǐn)?shù),從而耐蝕性優(yōu)異。另一方面,比較例不滿足本發(fā)明中限制的α-FeOOH的相分?jǐn)?shù),從而耐蝕性處于劣勢(shì)。對(duì)這些具有影響的因素進(jìn)行了考察。重復(fù)進(jìn)行腐蝕實(shí)驗(yàn)時(shí),隨著時(shí)間的經(jīng)過(guò),在表面上會(huì)形成銹,通常而言,非晶質(zhì)α-FeOOH是抑制銹形成的相,β-FeOOH是促進(jìn)銹形成的相。這是因?yàn)棣?FeOOH內(nèi)容易形成龜裂。其中α-FeOOH分?jǐn)?shù)限制為晶粒大小為20nm以下的。就α-FeOOH分?jǐn)?shù)而言,確認(rèn)到當(dāng)添加Cr時(shí),會(huì)增加到26%,當(dāng)添加Ni時(shí),會(huì)增加到31%,復(fù)合添加Cu和Ni時(shí),最大增加到37%。以上,參照實(shí)施例進(jìn)行了說(shuō)明,但本
技術(shù)領(lǐng)域:
的技術(shù)人員可以理解為,在不超過(guò)權(quán)利要求書中記載的本發(fā)明的思想及領(lǐng)域的范圍內(nèi),可以對(duì)本發(fā)明進(jìn)行各種修改及變更。當(dāng)前第1頁(yè)1 2 3