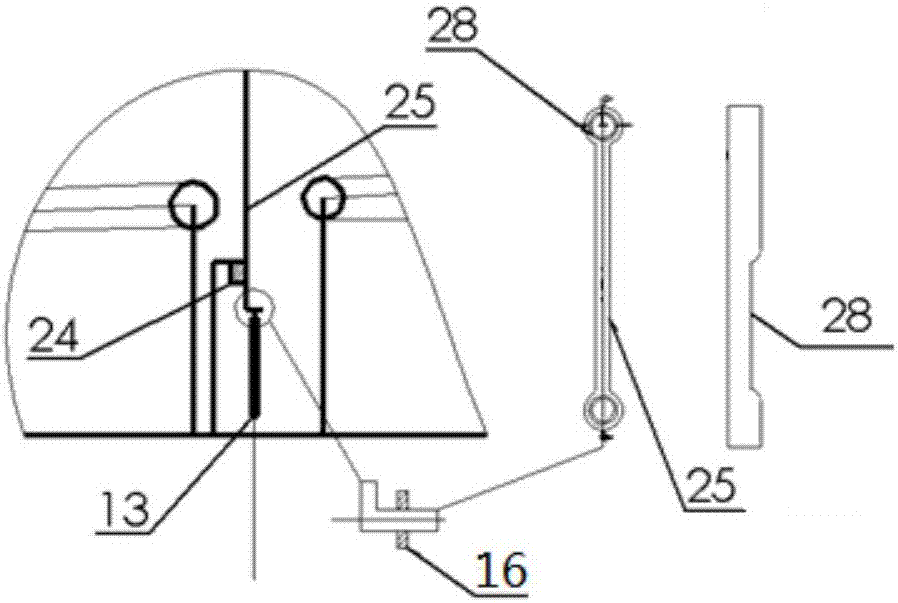
本發(fā)明屬于復(fù)合材料成形鑄造領(lǐng)域,具體涉及一種鋁基復(fù)合材料薄壁件一體化成形設(shè)備及方法。
背景技術(shù):近代科學(xué)技術(shù)的發(fā)展,對材料的性能提出了更高的要求,既希望它們具有良好的綜合性能,又期望它們能夠在高溫、高壓、高真空及輻照等極端環(huán)境條件下服役。顆粒增強鋁基復(fù)合材料不僅兼有金屬的高韌性、高塑性優(yōu)點,而且有增強體顆粒高硬度、高模量、高熱穩(wěn)定性等優(yōu)點,可采用傳統(tǒng)的金屬加工工藝進行加工,因而得到研究者廣泛重視。美國學(xué)者Logsdon曾提出鋁基復(fù)合材料未來的發(fā)展前景主要在于非長纖維增強,特別是碳化硅顆粒增強鋁基復(fù)合材料。1986年,美國DuralAluminumComposites公司發(fā)明了碳化硅顆粒增強鋁硅合金的攪拌鑄造新技術(shù),實現(xiàn)了鑄造鋁基復(fù)合材料的大規(guī)模生產(chǎn),以鑄錠的形式供給多家鑄造廠制造各種零件。目前,攪拌鑄造法制備鋁基復(fù)合材料技術(shù)已相對成熟,但如何進行規(guī)?;a(chǎn)品開發(fā)?北京有色金屬研究總院發(fā)明了一種鋁基復(fù)合材料大型薄壁殼體的制備加工方法,采用粉末冶金或攪拌鑄造工藝制備鋁基復(fù)合材料錠坯,并開坯鍛造成鍛棒,然后孔預(yù)制成空心坯料→等溫復(fù)合擠壓,制備出管坯→多道次熱強旋變薄旋壓,得到后續(xù)復(fù)合旋壓管坯→熱-溫復(fù)合旋壓成形,獲得復(fù)合材料大型薄壁殼體,由于工藝比較復(fù)雜,不適用工業(yè)化生產(chǎn)。而鋁基復(fù)合材料制備工藝中,顆粒增強鑄造鋁基復(fù)合材料由于鑄造工藝簡單,設(shè)備要求低,適合規(guī)模化生產(chǎn)。目前,顆粒增強鑄造鋁基復(fù)合材料鑄造基本上采用復(fù)合材料重熔后鑄造的工藝。與普通鋁合金相比,鋁合金復(fù)合材料重熔過程中,由于顆粒和熔體之間的界面反應(yīng)以及比重差異,復(fù)合熔體的粘度增大,除氣難度加大,澆注過程中卷入氣體,容易造成鑄件氣孔和夾雜。
技術(shù)實現(xiàn)要素:本發(fā)明旨在提供一種鋁基復(fù)合材料薄壁件一體化成形設(shè)備及方法,以克服現(xiàn)有技術(shù)中由于鋁合金復(fù)合材料重熔過程中因吸氣而導(dǎo)致鑄件中氣孔、夾雜、冷隔等缺陷較多,使鋁基復(fù)合材料復(fù)雜薄壁件難以成形的技術(shù)問題。本發(fā)明的鋁基復(fù)合材料薄壁件一體化成形的裝置及方法尤其適合用在復(fù)雜的薄壁件制備中。具體而言,本發(fā)明提供一種鋁基復(fù)合材料薄壁件一體化制備成形設(shè)備,其特征在于,所述制備成形設(shè)備包括用于制備鋁基復(fù)合材料的制備-澆注罐和加壓罐,所述制備-澆注罐與所述加壓罐相鄰的側(cè)壁上設(shè)有輸送窗口,與所述加壓罐相通,所述輸送窗口上設(shè)有密封機構(gòu)用于保持所述制備-澆注罐與加壓罐之間的彼此相對密封,所述制備-澆注罐內(nèi)置有熔煉爐、坩堝、第一澆注模具驅(qū)動裝置、澆鑄模具和第一滑道,并且所述制備-澆注罐與抽真空裝置相連通,所述制備-澆注罐的頂部還設(shè)置有穿過其頂壁的加料桶和加料-攪拌器,所述坩堝置于所述熔煉爐內(nèi),用于容納并熔化鋁錠,所述坩堝和所述熔煉爐上設(shè)置有水口,所述熔煉爐上設(shè)有傾轉(zhuǎn)機構(gòu)用以驅(qū)動熔煉爐使其向所述澆注模具傾轉(zhuǎn),所述澆鑄模具位于所述熔煉爐側(cè)部、所述水口下方并且放置于所述第一滑道上,所述第一澆鑄模具驅(qū)動裝置與所述澆注模具相連,用于驅(qū)動所述澆鑄模具在所述第一滑道上運動;所述加壓罐包括加壓裝置、模具輸入輸出口、第二澆注模具驅(qū)動裝置和第二滑道,并與抽真空裝置相連。所述第一滑道和所述第二滑道分別位于所述輸送窗口的兩側(cè),以允許所述澆注模具在澆注完成后經(jīng)所述輸送窗口從所述制備-澆注罐被推送至所述加壓罐。在一種優(yōu)選實現(xiàn)方式中,所述密封機構(gòu)包括第一密封圈、密封滑板、導(dǎo)桿、升降氣缸以及導(dǎo)套,所述升降氣缸與所述密封滑板之間用所述導(dǎo)套連接,所述升降氣缸、所述導(dǎo)套和所述導(dǎo)桿各2個,分別置于所述密封滑板兩側(cè),所述密封滑板沿兩側(cè)的所述導(dǎo)桿運動,所述第一密封圈用于實現(xiàn)所述密封滑板與所述制備-澆注罐的密封。在另一種優(yōu)選實現(xiàn)方式中,所述制備-澆注罐的頂部設(shè)置有密封蓋板,所述制備-澆注罐的上部采用所述密封蓋板與外部隔離,所述加料桶穿過所述密封蓋板并指向所述坩堝。在另一種優(yōu)選實現(xiàn)方式中,所述第二澆注模具驅(qū)動裝置前端設(shè)有連接環(huán),所述澆注模具的對應(yīng)位置設(shè)有鎖緊機構(gòu),所述鎖緊機構(gòu)包括推桿、彈簧,所述彈簧置于所述推桿上,所述彈簧和所述推桿的組合體有2個,彼此相對放置構(gòu)成鎖緊機構(gòu),所述鎖緊機構(gòu)可套住所述第二澆注模具驅(qū)動裝置前端的連接環(huán),實現(xiàn)連接。在另一種優(yōu)選實現(xiàn)方式中,所述加料-攪拌器采用六葉片結(jié)構(gòu)。在另一種優(yōu)選實現(xiàn)方式中,所述加料桶內(nèi)為上下層結(jié)構(gòu),且與外部完全隔離,上層裝有變質(zhì)劑和細化劑,下層裝有SiCp粉末,所述加料桶內(nèi)上下層分別設(shè)置球閥,所述球閥用于控制加料速度。在另一種優(yōu)選實現(xiàn)方式中,所述水口內(nèi)置有陶瓷過濾網(wǎng)。在另一種優(yōu)選實現(xiàn)方式中,所述抽真空裝置與所述制備-澆注罐側(cè)壁相連通,加壓裝置與所述加壓罐側(cè)壁相連通。另一方面,本發(fā)明提供一種采用上述設(shè)備進行鋁基復(fù)合材料薄壁件一體化制備成形的方法,其特征在于,所述方法包含如下步驟:步驟1、在真空環(huán)境下將鋁合金錠熔化并攪拌;步驟2、待鋁合金錠完全熔化后,將溫度控制在690℃~710℃,逐漸加入SiCp粉末,同時進行反向攪拌,轉(zhuǎn)速在100-120轉(zhuǎn)/分;步驟3、間隔2-5分鐘正向攪拌,循環(huán)往復(fù)15-20min;步驟4、將熔體溫度降到590℃~620℃,正向攪拌,轉(zhuǎn)速提升到1100-1300轉(zhuǎn)/分,間隔5-10分鐘反向攪拌,循環(huán)往復(fù)30-40min;步驟5、將熔體逐步升溫,同時減小正反向攪拌轉(zhuǎn)速,溫度升至690℃~710℃,緩慢加入變質(zhì)劑和細化劑,轉(zhuǎn)速在200-300轉(zhuǎn)/分,正向和反向攪拌總時間10-20min;步驟6、對澆注模具進行預(yù)熱,并利用所獲得的熔體進行澆注;步驟7、澆注結(jié)束后,立即對澆注模具進行加壓,壓力升至500-800Pa,保壓5-10min;步驟8、凝固結(jié)束時,泄壓到大氣壓。(三)有益效果本發(fā)明所提供的一種鋁合金復(fù)合材料復(fù)雜薄壁件一體化成形設(shè)備及方法具有如下優(yōu)點:一、通過對制備-澆注罐抽真空后鋁合金復(fù)合材料制備和澆注,防止了鋁合金復(fù)合材料重熔過程中氧化、吸氣等,避免了鋁合金復(fù)合材料鑄件中出現(xiàn)嚴重的夾渣和氣孔等缺陷,同時,石膏型保溫性好且在高真空下澆注,利于復(fù)雜薄壁件成形。二、通過對澆注后石膏型在加壓罐中加壓,促使鋁合金復(fù)合材料熔液加速補縮,防止鑄件產(chǎn)生縮松缺陷,使合金組織致密,從而保證鑄件的內(nèi)部組織致密;三、本發(fā)明的設(shè)備結(jié)構(gòu)巧妙,可操作性強,將澆注罐與加壓罐巧妙地連接在一起,既方便了澆注模具的送入又保證了在送入澆注模具時的真空狀態(tài),并且澆筑完成后可以方便地對產(chǎn)品進行加壓保壓,制備過程一氣呵成,使產(chǎn)品的性能更加優(yōu)異。因此采用本發(fā)明的鋁合金復(fù)合材料復(fù)雜薄壁件一體化成形設(shè)備及方法,生產(chǎn)鋁合金復(fù)合材料薄壁件鑄件質(zhì)量穩(wěn)定:鑄件內(nèi)部無夾渣、縮松、氣孔等缺陷,組織致密,性能良好,滿足生產(chǎn)要求;該裝置易于推廣,適合鋁合金復(fù)合材料復(fù)雜薄壁件小規(guī)?;a(chǎn),鑄件成品率較高。附圖說明圖1為本發(fā)明的鋁基復(fù)合材料復(fù)雜薄壁件一體化制備成形設(shè)備的結(jié)構(gòu)示意圖;圖2為圖1中B位置放大圖及密封滑板25和導(dǎo)桿28的結(jié)構(gòu)示意圖;圖3為圖1中A位置第一石膏型推拉氣缸21與石膏型碰撞連接機構(gòu)的放大示意圖。圖4為本發(fā)明的鋁基復(fù)合材料復(fù)雜薄壁件一體化制備成形設(shè)備的加料-攪拌器結(jié)構(gòu)示意圖。圖5-6為本發(fā)明的鋁基復(fù)合材料復(fù)雜薄壁件一體化制備鋁合金復(fù)合材料顯微組織。具體實施方式下面結(jié)合說明書附圖和實施例,對本發(fā)明的具體實施方式作進一步詳細描述。以下實施例僅用于說明本發(fā)明,但不用來限制本發(fā)明的范圍。如圖1所示,本實施例記載了一種鋁合金復(fù)合材料復(fù)雜薄壁件一體化成形設(shè)備,該設(shè)備包括:鋁合金制備-澆注罐1和加壓罐6。制備-澆注罐1的上部采用密封蓋板2與外部隔離,密封蓋板2上設(shè)有加料桶3、加料-攪拌器4和第一觀察窗5。加料桶3內(nèi)置兩層,上層裝有變質(zhì)劑和細化劑,下層裝有SiCp粉末,分別通過兩個球閥15控制加料速度,且與外部完全隔離。加料-攪拌器的升降和攪拌機構(gòu)4置于密封蓋板2上部,攪拌裝置位于制備-澆注罐1內(nèi),用于對制備-澆注罐1內(nèi)的熔體進行加料及攪拌,加料-攪拌器16內(nèi)部采用上下各四個葉片,外部采用螺旋片狀結(jié)構(gòu)(如圖4所示)。制備-澆注罐1的內(nèi)部設(shè)置熔煉爐19、坩堝20、第一石膏型推拉氣缸21、石膏型22、第一滑道23。制備-澆注罐1與加壓罐6并排緊貼放置,二者的相鄰側(cè)壁上設(shè)有輸送窗口,該輸送窗口可以開啟以便使制備-澆注罐1與加壓罐6相通,輸送窗口正常狀態(tài)下為關(guān)閉狀態(tài),其采用密封機構(gòu)實現(xiàn)相對于加壓罐6的密封。坩堝20置于熔煉爐19內(nèi),用于容納并熔化鋁錠,坩堝20和熔煉爐19上設(shè)置有水口18,水口18內(nèi)置有陶瓷過濾網(wǎng)。熔煉爐19上設(shè)有傾轉(zhuǎn)機構(gòu)17用以驅(qū)動坩堝20使其向石膏型22傾轉(zhuǎn),其采用氣缸推動實現(xiàn)澆注,從而實現(xiàn)澆注時坩堝20液面平穩(wěn),通過陶瓷過濾網(wǎng)防止熔體表面覆蓋著氧化物卷入液流澆入石膏型22中。石膏型22位于熔煉爐19側(cè)部水口18下方并且放置于第一滑道23上,第一石膏型推拉氣缸21與石膏型22相連,用于驅(qū)動石膏型22在第一滑道23上運動,二者的連接可以根據(jù)需要而斷開。如圖2所示,密封機構(gòu)包括第一密封圈24、密封滑板25、導(dǎo)桿28、升降氣缸13以及導(dǎo)套16,升降氣缸13、導(dǎo)套29和導(dǎo)桿28各2個,分別置于密封滑板25兩側(cè),密封滑板25在兩側(cè)升降氣缸13的帶動下依靠兩側(cè)導(dǎo)桿28上下運動,升降氣缸13與密封滑板25之間用導(dǎo)套29連接。在需要保持密封時,密封滑板25正對輸送窗口并通過密封圈24保持密封,在需要開啟輸送窗口時,通過升降氣缸13帶動密封滑板25向上移動,進而允許石膏型22通過。石膏型22上設(shè)有鎖緊機構(gòu),如圖3所示,第二石膏型推拉氣缸11前端設(shè)有連接環(huán),鎖緊機構(gòu)包括推桿27、彈簧26,彈簧26置于推桿27上,彈簧26和推桿27的組合體有兩個,彼此相對放置,鎖緊機構(gòu)可套住石膏型推拉氣缸11前端的連接環(huán),實現(xiàn)連接。繼續(xù)參照圖1,加壓罐6內(nèi)置有第二滑道12、第二石膏型推拉氣缸11,加壓罐6上部開有第二觀察窗7,右側(cè)開有鉸接門10,用于模具的輸入輸出,用第二密封圈9和鉸接門10卡緊實現(xiàn)密封,加壓罐6內(nèi)側(cè)壁上有加壓氣體管道8,與加壓裝置相連。在使用時,可以將干凈的鋁合金錠切塊置于坩堝20中,同時在加料桶3內(nèi)先后加入預(yù)處理的SiCp粉末(粒度在5-30μm不等)、變質(zhì)劑和細化劑,并將制備-澆注罐1上的密封蓋板2、密封滑板25以及加料桶3上端蓋鎖緊密封,啟動抽真空裝置14,通過制備-澆注罐1側(cè)壁上的抽真空管道對制備-澆注罐1抽真空。抽真空是為了使后續(xù)制備過程中的鋁合金熔液與空氣完全隔離,可避免鋁合金熔液吸氣和氧化。真空度達到5-10Pa,通電開始使鋁錠熔化,待坩堝20中鋁錠熔化后,降下加料-攪拌器4,通過在加料-攪拌器4上放入小塊鋁錠實現(xiàn)二次加料;待鋁錠完全熔化后,溫度控制在690℃~710℃,加料桶3緩慢加入SiCp粉末,同時加料-攪拌器4進行反向攪拌,轉(zhuǎn)速在100-120轉(zhuǎn)/分,間隔2-5分鐘正向攪拌,循環(huán)往復(fù)15-20min;之后將熔體溫度降到590℃~620℃,正向攪拌,轉(zhuǎn)速提升到1100-1300轉(zhuǎn)/分,間隔5-10分鐘反向攪拌,循環(huán)往復(fù)30-40min;將熔體逐步升溫,同時減小正反向攪拌轉(zhuǎn)速,觀察液面平穩(wěn)情況繼續(xù)降低速度,溫度升至690℃~710℃,緩慢加入變質(zhì)劑和細化劑,轉(zhuǎn)速在200-300轉(zhuǎn)/分,正/反向時間10-20min;熔體制備完成,等待澆注。熔體制備完成后,打開加壓罐6上的鉸接門10,將預(yù)熱石膏型22(預(yù)熱溫度200℃-300℃)置于加壓罐6內(nèi)第二滑道12上,鎖緊鉸接門10后,啟動抽真空裝置14,使加壓罐6真空度達到5-10Pa時,開啟升降氣缸13,打開密封滑板25,將石膏型22推至制備-澆注罐1內(nèi)第一滑道23上。待石膏型22到達第一滑道23上后,第一石膏型推拉氣缸21碰觸到石膏型22上的鎖緊機構(gòu)時,依靠石膏型向下推力將兩邊推桿27頂開,并依靠兩側(cè)推桿27上的彈簧26的彈力將第一石膏型推拉氣缸21前端連接環(huán)套住,實現(xiàn)與石膏型22連接。調(diào)整石膏型22位置,以保證鋁合金復(fù)合材料熔液以平穩(wěn)速度在石膏型22型腔內(nèi)流動。啟動坩堝傾轉(zhuǎn)機構(gòu)17將坩堝20傾斜進行澆注,同時左右移動石膏型22,通過鋁合金復(fù)合材料制備后即刻澆注,在高真空狀態(tài)下澆注避免石膏型“憋氣”,同時防止了鋁合金復(fù)合材料熔體因吸氣、氧化而導(dǎo)致的熔體流動性降低,這樣既能防止鑄件產(chǎn)生氣孔和夾雜缺陷,又能保證復(fù)雜薄壁件的順利成形。鋁合金復(fù)合材料熔體石膏型澆注結(jié)束后,立即用第一石膏型推拉氣缸21將石膏型22推入加壓罐6中第二滑道12,因第二滑道12相對較平而與推拉氣缸21瞬間脫開。放下密封滑板25并到位后開啟第二石膏型推拉氣缸11推動石膏型22頂緊密封滑板25。利用加壓裝置對加壓罐6加壓,通過對石膏型22鋁液表面施加壓力,促使鋁合金復(fù)合材料熔液加速補縮,防止鑄件產(chǎn)生縮松缺陷,使合金組織致密,從而有利于提高薄壁件的內(nèi)在質(zhì)量。然后,壓力升至500-800Pa,保壓5-10min;熔體凝固后,將加壓罐6泄壓到大氣壓,開啟鉸接門10,取出石膏型22。重復(fù)澆注、凝固的步驟即可實現(xiàn)連續(xù)生產(chǎn)。圖5-6為本發(fā)明的鋁基復(fù)合材料復(fù)雜薄壁件一體化制備鋁合金復(fù)合材料顯微組織,明顯可見SiCp(粒度121m)在基體中基本均勻分布,很少出現(xiàn)團聚。這種高質(zhì)量的薄壁件通過其他制備設(shè)備或方法很難得到。雖然上面結(jié)合本發(fā)明的優(yōu)選實施例對本發(fā)明的原理進行了詳細的描述,本領(lǐng)域技術(shù)人員應(yīng)該理解,上述實施例僅僅是對本發(fā)明的示意性實現(xiàn)方式的解釋,并非對本發(fā)明包含范圍的限定。實施例中的細節(jié)并不構(gòu)成對本發(fā)明范圍的限制,在不背離本發(fā)明的精神和范圍的情況下,任何基于本發(fā)明技術(shù)方案的等效變換、簡單替換等顯而易見的改變,均落在本發(fā)明保護范圍之內(nèi)。