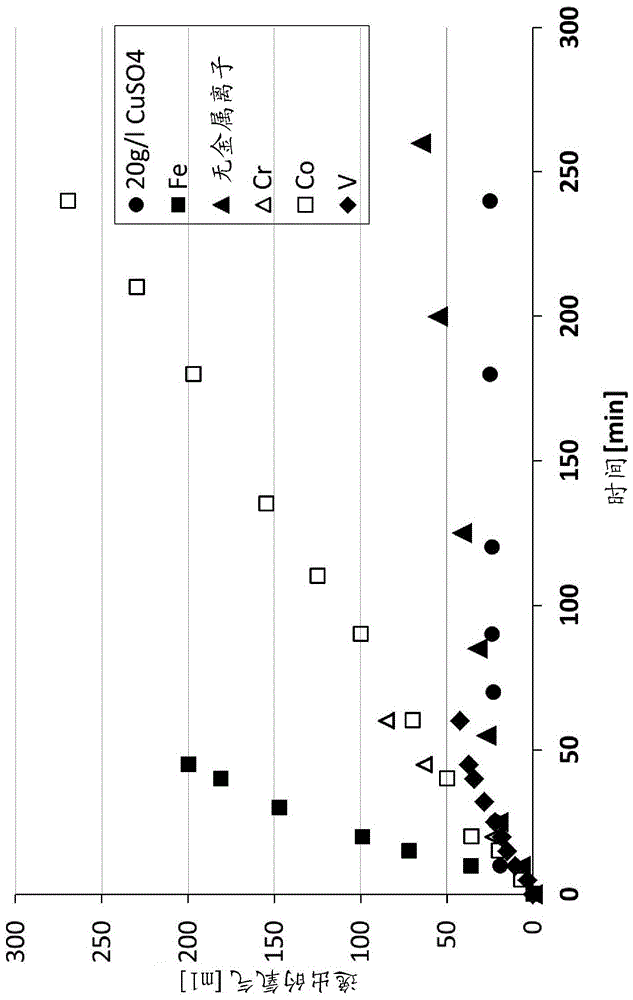
本發(fā)明涉及一種蝕刻溶液的組合物及一種使用該蝕刻溶液使制品的非導(dǎo)電塑料表面金屬化的方法。該蝕刻溶液基于穩(wěn)定的酸性高錳酸鹽溶液。在用該蝕刻溶液處理后,可以使該制品金屬化。【發(fā)明背景】由非導(dǎo)電塑料制成的制品可通過(guò)無(wú)電金屬化工藝或替代地通過(guò)直接電鍍工藝來(lái)金屬化。在兩種工藝中,制品首先被清潔和蝕刻。蝕刻通常通常借助于含鉻硫酸進(jìn)行。蝕刻用于使制品表面容易接受隨后的金屬化,使得制品表面在隨后的處理步驟中用相應(yīng)的溶液充分潤(rùn)濕,且沉積金屬最終在表面上具有足夠牢固的附著。在蝕刻后,借助于包含貴金屬的活化劑使塑料活化用于無(wú)電金屬化,且隨后將其無(wú)電金屬化。隨后,也可電解施加較厚金屬層。在直接電鍍工藝(其無(wú)需無(wú)電金屬化)的情況下,通常用鈀膠體溶液處理蝕刻表面。隨后,使表面與包含用配位劑配位的銅離子的堿性溶液接觸以增加導(dǎo)電率。該步驟導(dǎo)致在制品表面上形成具有增高導(dǎo)電率的銅層并因此為金屬層。此后,制品可進(jìn)行直接電解金屬化(EP1054081B1)。在蝕刻表面上提供充分導(dǎo)電層的另一種可能性是用金屬離子溶液和隨后用硫化物溶液對(duì)其進(jìn)行處理。這兩種處理步驟在通過(guò)直接電鍍使其金屬化之前在蝕刻表面上產(chǎn)生導(dǎo)電金屬硫化物層(EP1001052A2)。由于基于含鉻硫酸的蝕刻溶液是有毒的,該文獻(xiàn)描述了嘗試用包含高錳酸鹽的蝕刻溶液來(lái)替換它。EP2025708A1公開(kāi)了一種酸洗溶液及一種用于酸洗ABS塑料表面或ABS聚合物共混表面的酸洗工藝,隨后是這些表面的金屬化。酸洗溶液包含Mn(VII)離子及無(wú)機(jī)酸。酸洗溶液不含堿金屬及堿土金屬離子,其通過(guò)錳(II)鹽的陽(yáng)極氧化產(chǎn)生Mn(VII)離子來(lái)實(shí)現(xiàn)??商砑尤鏏g(I)、Bi(V)、V(V)、Mo(VI)、Cu(II)、Ti(II)、Au(I)、Fe(II)、Ce(III)或Sb(II)離子的氧化還原媒介以增加陽(yáng)極氧化的效率。堿金屬高錳酸鹽化合物的不存在克服了酸性高錳酸鹽溶液的快速自分解的問(wèn)題。EP2025708的酸洗溶液具有以下缺點(diǎn):制備費(fèi)力,且離析物(錳(II)鹽)是昂貴的,因?yàn)槠浔仨毑缓瑝A金屬及堿土金屬離子。酸洗工藝及包括該酸洗的金屬化方法需要實(shí)施該方法的額外設(shè)備,且相應(yīng)的工藝線甚至更昂貴和費(fèi)力。盡管酸性高錳酸鹽溶液可適用于蝕刻塑料表面,并可獲得沉積金屬層與塑料基材之間的足夠附著強(qiáng)度,但酸性高錳酸鹽溶液是不穩(wěn)定的。在蝕刻基材表面時(shí),高錳酸根離子被還原且最終產(chǎn)物為二氧化錳。二氧化錳催化其它二氧化錳及氧氣的形成,并導(dǎo)致高錳酸鹽的自分解。因此,新鮮制備的酸性高錳酸鹽溶液的蝕刻效果將在已經(jīng)若干小時(shí)之后變得不充分。酸性高錳酸鹽蝕刻溶液可通過(guò)添加高錳酸鹽來(lái)再銳化(re-sharpen),這造成了高錳酸鹽化合物的高消耗。另外,增加了二氧化錳的濃度。另外,二氧化錳形成難以從蝕刻溶液中移除的沉淀物。由于該富集,蝕刻溶液的粘度將增加到該蝕刻溶液必須被丟棄的程度,因?yàn)樵僖矡o(wú)法實(shí)現(xiàn)令人滿意的蝕刻結(jié)果。此外,沉積物分散在塑料表面的整個(gè)金屬化過(guò)程中并削弱金屬沉積,使得最終沉積具有缺陷或其它方面不足的金屬層。因此無(wú)法實(shí)現(xiàn)恒定高品質(zhì)的金屬化?!颈景l(fā)明的目標(biāo)】因此,本發(fā)明的目標(biāo)為提供一種容易制備、具有長(zhǎng)使用壽命且使高錳酸鹽消耗最小化的穩(wěn)定酸性高錳酸鹽溶液。另一目標(biāo)為提供一種具有足夠蝕刻效果的蝕刻非導(dǎo)電塑料表面的方法。另一目標(biāo)為提供一種使制品的非導(dǎo)電塑料表面金屬化的方法,其具有恒定高品質(zhì)的金屬化及沉積至塑料表面上的金屬層的足夠附著強(qiáng)度。技術(shù)實(shí)現(xiàn)要素:這些目標(biāo)通過(guò)以下溶液及方法來(lái)實(shí)現(xiàn)。一種用于處理非導(dǎo)電塑料表面的蝕刻溶液,其包含(i)至少一種酸,其中該至少一種酸的濃度基于一元酸計(jì)為0.02mol/l至0.6mol/l;及(ii)至少一種高錳酸鹽,選自堿金屬高錳酸鹽及堿土金屬高錳酸鹽,其中該高錳酸鹽以30g/l至250g/l的濃度存在于該蝕刻溶液中;及(iii)至少一種金屬離子源,其中該金屬離子的金屬選自鈦、鋯、鈮、鉬、釕、銠、鎳、銅、銀、鋅及鎘。根據(jù)(iii)的金屬離子使蝕刻溶液穩(wěn)定。這意味著根據(jù)(iii)的金屬離子的存在防止含有堿金屬高錳酸鹽及堿土金屬高錳酸鹽的酸性蝕刻溶液的自分解。一種用于蝕刻制品的非導(dǎo)電塑料表面的方法,其包括以下方法步驟:A)用處理非導(dǎo)電塑料表面的至少一種蝕刻溶液處理該塑料表面,該蝕刻溶液包含(i)至少一種酸,(ii)至少一種高錳酸鹽,選自堿金屬高錳酸鹽及堿土金屬高錳酸鹽,及(iii)至少一種金屬離子源,其中該金屬離子的金屬選自鈦、鋯、鈮、鉬、釕、銠、鎳、銅、銀、鋅及鎘。在蝕刻工藝中使用上述蝕刻溶液導(dǎo)致充分蝕刻的非導(dǎo)電塑料表面。一種使制品的非導(dǎo)電塑料表面金屬化的方法,其包括以下方法步驟:A)用處理非導(dǎo)電塑料表面的至少一種蝕刻溶液處理該塑料表面,該蝕刻溶液包含(i)至少一種酸,(ii)至少一種高錳酸鹽,選自堿金屬高錳酸鹽及堿土金屬高錳酸鹽,及(iii)至少一種金屬離子源,其中該金屬離子的金屬選自鈦、鋯、鈮、鉬、釕、銠、鎳、銅、銀、鋅及鎘,和B)用金屬化溶液使該塑料表面金屬化。在金屬化方法中使用上述蝕刻溶液導(dǎo)致無(wú)表面缺陷的金屬沉積物和沉積至塑料表面上的金屬層的足夠附著強(qiáng)度?!靖綀D描述】圖1:不含根據(jù)(iii)的金屬離子的對(duì)比酸性高錳酸鹽溶液中的氧氣逸出。圖2:含有根據(jù)(iii)的金屬離子的本發(fā)明酸性高錳酸鹽溶液中的氧氣逸出。圖3:在不存在或存在根據(jù)(iii)的金屬離子的情況下含有不同濃度的高錳酸鹽的溶液中的氧氣逸出。圖4:含有不同于根據(jù)(iii)的金屬離子的金屬離子的對(duì)比酸性高錳酸鹽溶液中的氧氣逸出?!緦?shí)施方式】本發(fā)明蝕刻溶液包含至少一種酸、至少一種選自堿金屬高錳酸鹽和堿土金屬高錳酸鹽的高錳酸鹽及至少一種根據(jù)(iii)的金屬離子源。堿金屬高錳酸鹽選自高錳酸鉀、高錳酸鈉、高錳酸鋰和高錳酸銣,優(yōu)選高錳酸鉀和高錳酸鈉。堿土金屬高錳酸鹽選自高錳酸鎂和高錳酸鈣,優(yōu)選高錳酸鈣。高錳酸鹽以30g/l至250g/l,優(yōu)選30g/l至180g/l,更優(yōu)選90g/l至180g/l的濃度存在于蝕刻溶液中。由于其溶解度,高錳酸鉀可以高至70g/l的濃度存在于蝕刻溶液中。高錳酸鈉可以高至250g/l的濃度存在于蝕刻溶液中。對(duì)于這兩種鹽每個(gè)的濃度下限通常為30g/l。高錳酸鈉的含量?jī)?yōu)選為90g/l至180g/l。在本發(fā)明的進(jìn)一步實(shí)施方案中,高錳酸鹽的濃度可能甚至更低。在該實(shí)施方案中,高錳酸鹽的濃度優(yōu)選為5g/l至250g/l,更優(yōu)選10g/l至180g/l,最優(yōu)選15g/l至150g/l。蝕刻溶液是酸性的,這意味著其含有至少一種根據(jù)(i)的酸。用于蝕刻溶液中的酸優(yōu)選為無(wú)機(jī)酸。蝕刻溶液中的無(wú)機(jī)酸選自硫酸、硝酸及磷酸。酸濃度是低的,因?yàn)檫@進(jìn)一步有助于蝕刻溶液的穩(wěn)定性。酸濃度基于一元酸計(jì)為0.02mol/l至0.6mol/l。優(yōu)選在各情況下基于一元酸計(jì)為0.06mol/l至0.45mol/l,更優(yōu)選0.07mol/l至0.30mol/l。優(yōu)選使用0.035mol/l至0.15mol/l濃度的硫酸,對(duì)應(yīng)于基于一元酸計(jì)0.07mol/l至0.30mol/l的酸濃度。若含有上文指定的濃度范圍,本發(fā)明的蝕刻溶液的高錳酸鹽及酸有助于蝕刻溶液的穩(wěn)定性。酸性高錳酸鹽溶液極具反應(yīng)性。隨后,與塑料表面的氧化反應(yīng)形成沉淀析出的許多錳(IV)物質(zhì)。這些錳(IV)物質(zhì)主要為氧化錳(IV)或氧化錳(IV)水合物,且在下文中簡(jiǎn)單地稱為二氧化錳。若其保留在塑料表面上,二氧化錳沉淀物對(duì)于隨后的金屬化具有破壞性影響。二氧化錳還催化根據(jù)式(2)的高錳酸鹽與水的反應(yīng),且因此導(dǎo)致蝕刻溶液的不穩(wěn)定。式(2):因此,蝕刻溶液應(yīng)有利地保持不含二氧化錳。出人意料地,已發(fā)現(xiàn)當(dāng)根據(jù)(iii)的金屬離子存在于酸性高錳酸鹽蝕刻溶液中時(shí),難以除去的二氧化錳物質(zhì)的形成顯著減少。根據(jù)(iii)的金屬離子的金屬選自鈦、鋯、鈮、鉬、釕、銠、鎳、銅、銀、鋅及鎘。優(yōu)選地,金屬可選自銅、鎳及鋅。更優(yōu)選地,金屬可選自銅。根據(jù)(iii)的至少一種金屬離子源選自根據(jù)(iii)的金屬離子的上文所列金屬的水溶性鹽。優(yōu)選地,至少一種金屬離子源選自金屬離子的上文所列金屬的水溶性硫酸鹽、磷酸鹽、硝酸鹽及高錳酸鹽。更優(yōu)選地,至少一種金屬離子源選自硫酸銅、磷酸銅、硝酸銅、高錳酸銅、硝酸銀、硫酸鋅、硝酸鋅、高錳酸鋅、硫酸鎘、硝酸鎘、硫酸鈦、硝酸鈦、硫酸鋯、硫酸鎳、硝酸鎳、硫酸銠及其水合物。最優(yōu)選地,至少一種金屬離子源選自硫酸銅、磷酸銅、硝酸銅、高錳酸銅及其水合物。根據(jù)(iii)的金屬離子的濃度為1mmol/l至1mol/l,優(yōu)選10mmol/l至1mol/l,更優(yōu)選10mmol/l至100mmol/l,最優(yōu)選30mmol/l至100mmol/l。在本發(fā)明的進(jìn)一步實(shí)施方案中,根據(jù)(iii)的金屬離子的濃度優(yōu)選為1mmol/l至90mmol/l,更優(yōu)選1mmol/l至80mmol/l。根據(jù)(ii)的高錳酸根離子與根據(jù)(iii)的金屬離子的摩爾比為5:1至40:1,優(yōu)選10:1至20:1。本發(fā)明的方法中的步驟以指定順序?qū)嵤灰欢ňo接著連續(xù)實(shí)施。在各情況下,在步驟之間可能實(shí)施其它方法步驟和額外地沖洗步驟,優(yōu)選用水。本發(fā)明的用于蝕刻制品的非導(dǎo)電塑料表面的方法,其包括以下方法步驟:A)用處理非導(dǎo)電塑料表面的至少一種蝕刻溶液處理該塑料表面,該蝕刻溶液包含(i)至少一種酸,(ii)至少一種高錳酸鹽,選自堿金屬高錳酸鹽和堿土金屬高錳酸鹽,及(iii)至少一種金屬離子源,其中該金屬離子的金屬選自鈦、鋯、鈮、鉬、釕、銠、鎳、銅、銀、鋅及鎘。蝕刻溶液可在30℃至90℃,優(yōu)選55℃至75℃,最優(yōu)選65℃至72℃的溫度下使用。最佳處理時(shí)間取決于所處理的塑料表面及所選擇的蝕刻溶液的溫度。對(duì)于ABS及ABS/PC塑料表面,塑料表面與隨后施加的金屬層之間的最佳附著強(qiáng)度在5分鐘至30分鐘,優(yōu)選10分鐘至25分鐘,更優(yōu)選10分鐘至15分鐘的處理時(shí)間下實(shí)現(xiàn)。比30分鐘更長(zhǎng)的處理時(shí)間通常不會(huì)導(dǎo)致附著強(qiáng)度的進(jìn)一步提高。非導(dǎo)電塑料表面已由至少一種非導(dǎo)電塑料制造。在本發(fā)明的一個(gè)實(shí)施方案中,至少一種非導(dǎo)電塑料選自丙烯腈-丁二烯-苯乙烯共聚物(ABS共聚物)、聚酰胺(PA)、聚碳酸酯(PC)及ABS共聚物與至少一種其它聚合物的混合物。在本發(fā)明的一個(gè)優(yōu)選實(shí)施方案中,非導(dǎo)電塑料為ABS共聚物或ABS共聚物與至少一種其它聚合物的混合物。至少一種其它共聚物更優(yōu)選為聚碳酸酯(PC),這意味著尤其優(yōu)選為ABS/PC混合物。本發(fā)明的使制品的非導(dǎo)電塑料表面金屬化的方法,其包括以下方法步驟:A)用處理非導(dǎo)電塑料表面的至少所述蝕刻溶液處理該塑料表面,該蝕刻溶液包含(i)至少一種酸,(ii)至少一種高錳酸鹽,選自堿金屬高錳酸鹽和堿土金屬高錳酸鹽,及(iii)至少一種金屬離子源,其中該金屬離子的金屬選自鈦、鋯、鈮、鉬、釕、銠、鎳、銅、銀、鋅及鎘,及B)用金屬化溶液使該塑料表面金屬化。方法步驟A)如上文用于蝕刻非導(dǎo)電塑料表面的方法所描述的那樣實(shí)施。在本發(fā)明的一個(gè)優(yōu)選實(shí)施方案中,在方法步驟A)之前實(shí)施以下另一方法步驟:預(yù)處理步驟:在包含至少一種二醇化合物的水溶液中處理該塑料表面。該另一方法步驟在下文中稱為預(yù)處理步驟。該預(yù)處理步驟增加塑料與金屬層之間的附著強(qiáng)度。二醇化合物理解為表示具有以下通式(I)的化合物: (I)其中n為1至4的整數(shù);及R1和R2各自獨(dú)立地為-H、-CH3、-CH2-CH3、-CH2-CH2-CH3、-CH(CH3)-CH3、-CH2-CH2-CH2-CH3、-CH(CH3)-CH2-CH3、-CH2-CH(CH3)-CH3、-CH2-CH2-CH2-CH2-CH3、-CH(CH3)-CH2-CH2-CH3、-CH2-CH(CH3)-CH2-CH3、-CH2-CH2-CH(CH3)-CH3、-CH(CH2-CH3)-CH2-CH3、-CH2-CH(CH2-CH3)-CH3、-CO-CH3、-CO-CH2-CH3、-CO-CH2-CH2-CH3、-CO-CH(CH3)-CH3、-CO-CH(CH3)-CH2-CH3、-CO-CH2-CH(CH3)-CH3、-CO-CH2-CH2-CH2-CH3。根據(jù)通式(I),二醇化合物包括二醇自身及二醇衍生物。二醇衍生物包括二醇醚、二醇酯及二醇醚酯。該二醇化合物為溶劑。優(yōu)選的二醇化合物為乙二醇、二乙二醇、乙二醇單甲醚乙酸酯、乙二醇單乙醚乙酸酯、乙二醇單丙醚乙酸酯、乙二醇乙酸酯、二乙二醇單乙醚乙酸酯、二乙二醇單甲醚乙酸酯、二乙二醇單丙醚乙酸酯、乙二醇丁醚、乙二醇單丁醚、乙二醇二乙酸酯及其混合物。尤其優(yōu)選為二乙二醇單乙醚乙酸酯、乙二醇乙酸酯、乙二醇二乙酸酯、乙二醇丁醚及其混合物。在使用二醇酯及二醇醚酯的情況下,最好通過(guò)合適的措施將該二醇化合物的水溶液的pH保持在中性范圍內(nèi),以便盡可能抑制產(chǎn)生醇和羧酸的水解。一個(gè)實(shí)例為二乙二醇單乙醚乙酸酯的水解:二醇酯或二醇醚酯的溶液含有pH緩沖劑,因此將其保持在中性pH范圍內(nèi),這意味著清除通過(guò)溶劑的水解獲得的質(zhì)子。已發(fā)現(xiàn)磷酸鹽緩沖液混合物足夠適用于該目的。易溶的磷酸鉀在高至40vol%的溶劑濃度下允許足夠高的濃度與良好的緩沖能力。塑料表面的最佳處理時(shí)間取決于所使用的塑料、溫度及二醇化合物的性質(zhì)和濃度。在包含至少一種二醇化合物的水溶液中處理塑料表面有助于隨后沉積的金屬層的附著強(qiáng)度。預(yù)處理步驟的處理時(shí)間為1分鐘至30分鐘,優(yōu)選5分鐘至20分鐘,更優(yōu)選7分鐘至15分鐘。取決于所用溶劑或溶劑混合物的性質(zhì),處理溫度為20℃至70℃。處理溫度優(yōu)選為20℃至50℃,處理溫度尤其優(yōu)選為20℃至45℃。預(yù)處理步驟中的塑料表面的處理可在包含一種二醇化合物的水溶液中或在包含兩種或更多種不同二醇化合物的水溶液中實(shí)施。水溶液中二醇化合物的總濃度為5vol%至50vol%,優(yōu)選10vol%至40vol%,更優(yōu)選20vol%至40vol%。若所述溶液含有一種二醇化合物,整體濃度對(duì)應(yīng)于這一種二醇化合物的濃度。若所述溶液含有兩種或更多種不同二醇化合物,總濃度對(duì)應(yīng)于存在的所有二醇化合物的濃度總和。在含有至少一種二醇化合物的溶液的情形下,對(duì)于一或多種二醇化合物以%給出的濃度數(shù)字始終被理解為表示以vol%給出的濃度。在本發(fā)明的一個(gè)優(yōu)選實(shí)施方案中,在方法步驟A)之后實(shí)施以下另一方法步驟:Ai)用堿性蝕刻溶液處理該塑料表面。方法步驟Ai)可在用于蝕刻制品的非導(dǎo)電塑料表面的方法中和/或在用于使制品的非導(dǎo)電塑料表面金屬化的方法中實(shí)施。若實(shí)施用于使非導(dǎo)電塑料表面金屬化的方法(包括方法步驟B)),方法步驟Ai)優(yōu)選在方法步驟A)之后且在方法步驟B)之前實(shí)施。優(yōu)選地,方法步驟Ai)在方法步驟A)與方法步驟B)之間實(shí)施。堿性蝕刻溶液包含:1.至少一種高錳酸鹽,選自堿金屬高錳酸鹽和堿土金屬高錳酸鹽,及2.氫氧根離子源。堿性蝕刻溶液的高錳酸鹽選自與對(duì)于酸性蝕刻溶液所列相同的高錳酸鹽;這些高錳酸鹽為根據(jù)(ii)的高錳酸鹽。獨(dú)立地選擇用于堿性和酸性蝕刻溶液的高錳酸鹽,這意味著兩種蝕刻溶液可含有相同高錳酸鹽或兩種蝕刻溶液可含有不同高錳酸鹽。該高錳酸鹽以如上文對(duì)于酸性蝕刻溶液所給定的濃度存在于堿性蝕刻溶液中。獨(dú)立地選擇用于堿性和酸性蝕刻溶液的高錳酸鹽的濃度,這意味著兩種蝕刻溶液可含有相同濃度的高錳酸鹽或兩種蝕刻溶液可含有不同濃度的高錳酸鹽。堿性蝕刻溶液中的氫氧根離子源選自堿金屬氫氧化物,包括氫氧化鈉、氫氧化鉀及氫氧化鋰。氫氧根離子源優(yōu)選為氫氧化鈉。獨(dú)立于金屬高錳酸鹽選擇堿性蝕刻溶液中的氫氧根離子源,這意味著堿性蝕刻溶液可包含具有相同堿金屬離子的氫氧根離子源和金屬高錳酸鹽,或堿性蝕刻溶液可包含具有不同堿金屬離子的氫氧根離子源和金屬高錳酸鹽。氫氧根離子源的濃度為1g/l至100g/l,優(yōu)選5g/l至50g/l,更優(yōu)選10g/l至30g/l。堿性蝕刻溶液可在20℃至90℃,優(yōu)選30℃至75℃,更優(yōu)選30℃至60℃的溫度下使用。在30℃至60℃的溫度范圍內(nèi)用堿性蝕刻溶液處理塑料表面產(chǎn)生更高的附著強(qiáng)度。堿性高錳酸鹽溶液的穩(wěn)定性在升高的溫度下稍微下降。然而,堿性高錳酸鹽溶液通常比酸性高錳酸鹽溶液穩(wěn)定得多。堿性高錳酸鹽溶液的穩(wěn)定性在40℃至60℃的范圍內(nèi)無(wú)需鑒別。使用堿性蝕刻溶液的最佳處理時(shí)間同樣取決于所處理的塑料表面和所選擇的蝕刻溶液的溫度。用堿性蝕刻溶液的處理時(shí)間為1分鐘至20分鐘,優(yōu)選1分鐘至15分鐘,更優(yōu)選1分鐘至5分鐘。比20分鐘更長(zhǎng)的處理時(shí)間一般不會(huì)在附著強(qiáng)度上產(chǎn)生任何進(jìn)一步提高。在本發(fā)明的一個(gè)優(yōu)選實(shí)施方案中,在方法步驟A)之后實(shí)施以下另一方法步驟:Aii)在包含用于二氧化錳的還原劑的溶液中處理該塑料表面。另一方法步驟Aii)也稱作還原處理。該還原處理將附著在塑料表面的二氧化錳還原成水溶性錳(II)離子。還原處理任選在Ai)之后進(jìn)行。方法步驟Aii)可在用于蝕刻制品的非導(dǎo)電塑料表面的方法中和/或在用于使制品的非導(dǎo)電塑料表面金屬化的方法中實(shí)施。若實(shí)施用于使非導(dǎo)電塑料表面金屬化的方法(包括方法步驟B)),方法步驟Aii)優(yōu)選在方法步驟A)之后且在方法步驟B)之前實(shí)施;更優(yōu)選在方法步驟Ai)之后且在方法步驟B)之前實(shí)施。優(yōu)選地,方法步驟Aii)在方法步驟A)與方法步驟B)之間實(shí)施。出于該目的而言,使用具有還原劑的酸性溶液。還原劑選自硫酸羥銨、氯化羥銨和過(guò)氧化氫。優(yōu)選為具有過(guò)氧化氫的酸性溶液,因?yàn)檫^(guò)氧化氫既無(wú)毒性也不形成配合物。還原處理溶液(還原溶液)中過(guò)氧化氫的含量為25ml/l至35ml/l的30%過(guò)氧化氫溶液(重量%),優(yōu)選30ml/l的30%過(guò)氧化氫溶液(重量%)。用于還原溶液中的酸為無(wú)機(jī)酸,優(yōu)選為硫酸。酸濃度在各情況下基于一元酸計(jì)為0.5mol/l至5.0mol/l,優(yōu)選1.0mol/l至3.0mol/l,更優(yōu)選1.0mol/l至2.0mol/l。在使用硫酸的情況下,濃度尤其優(yōu)選為50g/l的96%硫酸至100g/l的96%硫酸,對(duì)應(yīng)于基于一元酸計(jì)1.0mol/l至2.0mol/l的酸濃度。方法步驟Aii)中的還原處理在30℃至50℃,優(yōu)選40℃至45℃的溫度下實(shí)施。實(shí)施還原處理0.5分鐘至10分鐘,優(yōu)選1分鐘至6分鐘,更優(yōu)選3分鐘至6分鐘的時(shí)間段。為在活化之前實(shí)現(xiàn)托架(rack)的充分保護(hù),有利的是將還原溶液中的處理時(shí)間增加至3分鐘至10分鐘,優(yōu)選增加至3分鐘至6分鐘。在本發(fā)明的一個(gè)優(yōu)選實(shí)施方案中,通過(guò)無(wú)電金屬鍍層使蝕刻塑料表面金屬化。在該實(shí)施方案中,本發(fā)明的方法進(jìn)一步包括方法步驟Aiii),其中用金屬膠體或金屬化合物的溶液處理塑料表面。金屬膠體或金屬化合物的金屬選自元素周期表(PTE)的第I族過(guò)渡金屬和PTE的第VIII族過(guò)渡金屬。PTE的第VIII族過(guò)渡金屬選自鈀、鉑、銥、銠和這些金屬中兩種或更多種的混合物。PTE的第I族過(guò)渡金屬選自金、銀和這些金屬的混合物。金屬膠體中的優(yōu)選金屬為鈀。用保護(hù)性膠體使金屬膠體穩(wěn)定。保護(hù)性膠體選自金屬保護(hù)性膠體、有機(jī)保護(hù)性膠體和其它保護(hù)性膠體。作為金屬保護(hù)性膠體,優(yōu)選錫離子。有機(jī)保護(hù)性膠體選自聚乙烯醇、聚乙烯吡咯啶酮及明膠,優(yōu)選聚乙烯醇。在本發(fā)明的一個(gè)優(yōu)選實(shí)施方案中,方法步驟Aiii)中的金屬膠體溶液為具有鈀/錫膠體的活化劑溶液。該膠體溶液獲自鈀鹽、錫(II)鹽和無(wú)機(jī)酸。優(yōu)選的鈀鹽為氯化鈀。優(yōu)選的錫(II)鹽為氯化錫(II)。無(wú)機(jī)酸可包括鹽酸或硫酸,優(yōu)選為鹽酸。膠體溶液通過(guò)借助于氯化錫(II)將氯化鈀還原成鈀來(lái)形成。氯化鈀至膠體的轉(zhuǎn)化是完全的;因此,膠體溶液不再含有任何氯化鈀。若在隨后方法步驟中使塑料表面無(wú)電金屬化,膠體溶液中鈀的濃度基于Pd2+計(jì)為5mg/l至100mg/l,優(yōu)選20mg/l至50mg/l,更優(yōu)選30mg/l至45mg/l。若在隨后方法步驟中借助于直接電鍍使塑料表面金屬化,膠體溶液中鈀的濃度基于Pd2+計(jì)為50mg/l至200mg/l,優(yōu)選75mg/l至150mg/l,更優(yōu)選100mg/l至150mg/l,且更優(yōu)選80mg/l至120mg/l。氯化錫(II)的濃度基于Sn2+計(jì)為0.5g/l至10g/l,優(yōu)選1g/l至5g/l,更優(yōu)選2g/l至4g/l。鹽酸的濃度為100ml/l至300ml/l(37重量%的HCl)。另外,鈀/錫膠體溶液額外包含通過(guò)錫(II)離子的氧化形成的錫(IV)離子。在方法步驟B)期間膠體溶液的溫度為20℃至50℃且優(yōu)選為35℃至45℃。使用活化劑溶液的處理時(shí)間為0.5min至10min,優(yōu)選2min至5min,更優(yōu)選3min至5min。在本發(fā)明的另一實(shí)施方案中,在方法步驟Aiii)中,使用金屬化合物的溶液替代金屬膠體。所使用的金屬化合物的溶液為包含酸和金屬鹽的溶液。金屬鹽中的金屬包括上文所列的PTE的第I族和第VIII族過(guò)渡金屬中的一種或多種。金屬鹽可以是鈀鹽,優(yōu)選氯化鈀、硫酸鈀或乙酸鈀,或銀鹽,優(yōu)選乙酸銀。酸優(yōu)選為鹽酸。替代地,也有可能使用金屬配合物,例如鈀配合物鹽,例如鈀-氨基吡啶配合物的鹽。方法步驟Aiii)中的金屬化合物以基于金屬計(jì)40mg/l至80mg/l的濃度存在。金屬化合物的溶液可在25℃至70℃,優(yōu)選25℃的溫度下使用。使用金屬化合物的溶液的處理時(shí)間為0.5min至10min,優(yōu)選2min至6min,更優(yōu)選3min至5min。在方法步驟Aiii)之前,可實(shí)施以下另一方法步驟:托架保護(hù):用包含碘酸根離子的溶液處理塑料表面。在使固定于托架的塑料制品金屬化時(shí),托架保護(hù)步驟導(dǎo)致保護(hù)托架的塑料外殼免于金屬沉積。托架保護(hù)在20℃至70℃,更優(yōu)選45℃至55℃的溫度下實(shí)施。碘酸根離子為金屬碘酸鹽形式。金屬碘酸鹽選自碘酸鈉、碘酸鉀、碘酸鎂、碘酸鈣及其水合物。金屬碘酸鹽的濃度為5g/l至50g/l,優(yōu)選15g/l至25g/l。使用碘酸根離子處理托架的持續(xù)時(shí)間為1分鐘至20分鐘,優(yōu)選2分鐘至15分鐘,更優(yōu)選5分鐘至10分鐘。包含碘酸根離子的溶液可進(jìn)一步包含酸。無(wú)機(jī)酸是優(yōu)選的。該無(wú)機(jī)酸選自硫酸和磷酸,優(yōu)選硫酸。酸濃度在各情況下基于一元酸計(jì)為0.02mol/l至2.0mol/l,優(yōu)選0.06mol/l至1.5mol/l,更優(yōu)選0.1mol/l至1.0mol/l。在使用硫酸的情況下,濃度尤其優(yōu)選為5g/l的96%硫酸至50g/l的96%硫酸,對(duì)應(yīng)于基于一元酸計(jì)0.1mol/l至1.0mol/l的酸濃度。在方法步驟Aii)與方法步驟Aiii)之間,可實(shí)施以下另一方法步驟:初步浸漬:在酸性水溶液中處理該塑料表面。用于初步浸漬步驟的酸性水溶液稱作初步浸漬溶液。該初步浸漬溶液具有與方法步驟B)中的膠體溶液相同的組成,而不存在膠體及其保護(hù)性膠體中的金屬。在方法步驟Aiii)中使用鈀/錫膠體溶液的情況下,初步浸漬溶液僅包含鹽酸,若膠體溶液同樣包含鹽酸的話。對(duì)于初步浸漬,在環(huán)境溫度下短暫沉浸到初步浸漬溶液中是足夠的。在不沖洗塑料表面的情況下,其在初步浸漬溶液中處理之后直接用方法步驟B)的膠體溶液進(jìn)一步處理。初步浸漬步驟優(yōu)選在方法步驟Aiii)涉及用金屬膠體溶液處理塑料表面時(shí)實(shí)施。初步浸漬步驟也可在方法步驟Aiii)涉及用金屬化合物的溶液處理塑料表面時(shí)實(shí)施。在包括無(wú)電金屬鍍層的實(shí)施方案中,可在方法步驟Aiii)與方法步驟B)之間實(shí)施以下其它方法步驟:Aiv)在酸性水溶液中處理塑料表面,及Av)在金屬化溶液中使塑料表面無(wú)電金屬化。這些其它方法步驟Aiv)和方法步驟Av)在通過(guò)無(wú)電金屬化工藝使制品金屬化(即通過(guò)無(wú)電工藝將第一金屬層施加到塑料表面)時(shí)使用。若方法步驟Aiii)中的活化已用金屬膠體實(shí)施,在方法步驟Aiv)中用加速劑溶液處理塑料表面以從塑料表面除去膠體溶液中的膠體成分(例如保護(hù)性膠體)。若方法步驟Aiii)中的膠體溶液中的膠體為鈀/錫膠體,所使用的加速劑溶液優(yōu)選為酸的水溶液。該酸例如選自硫酸、鹽酸、檸檬酸及四氟硼酸。在鈀/錫膠體的情況下,加速劑溶液有助于除去用作保護(hù)性膠體的錫化合物。替代地,在方法步驟Aiv)中,當(dāng)在方法步驟Aiii)中已使用金屬化合物的溶液替代金屬膠體用于活化時(shí),實(shí)施還原劑處理。若金屬化合物的溶液為氯化鈀的鹽酸溶液或銀鹽的酸性溶液,用于該目的的還原劑溶液包含鹽酸及氯化錫(II)。還原劑溶液還可包含另一還原劑,例如NaH2PO2或硼烷或硼氫化物,如堿金屬硼烷或堿土金屬硼烷或二甲氨基硼烷。在還原劑溶液中優(yōu)選使用NaH2PO2。方法步驟Aiv)和任選的一個(gè)或多個(gè)沖洗步驟之后為其中使塑料表面無(wú)電金屬化的方法步驟Av)。例如使用常規(guī)鎳浴實(shí)現(xiàn)無(wú)電鍍鎳,所述常規(guī)鎳浴尤其包含硫酸鎳、作為還原劑的次磷酸鹽(例如次磷酸鈉)以及有機(jī)配位劑和pH調(diào)節(jié)劑(例如緩沖劑)。所使用的還原劑可同樣為二甲氨基硼烷或次磷酸鹽與二甲氨基硼烷的混合物。替代地,有可能使用無(wú)電銅浴用于無(wú)電鍍銅,該無(wú)電銅浴通常包含銅鹽(例如硫酸銅或次磷酸銅),以及還原劑(例如甲醛或次磷酸鹽(如堿金屬或銨鹽)或次磷酸),和額外一種或多種配位劑(例如酒石酸),以及pH調(diào)節(jié)劑(例如氫氧化鈉)。因此呈現(xiàn)導(dǎo)電性的表面隨后可進(jìn)一步電解金屬化以獲得功能性或裝飾性表面。在本發(fā)明的另一實(shí)施方案中,借助于直接電鍍使塑料表面金屬化,這意味著塑料表面不是通過(guò)無(wú)電而是直接通過(guò)電解金屬化工藝來(lái)金屬化。在該實(shí)施方案中,在方法步驟A)與方法步驟B)之間實(shí)施以下另一方法步驟:Aiv)在轉(zhuǎn)化溶液中處理該塑料表面。優(yōu)選地,方法步驟Aiv)在方法步驟Aiii)與方法步驟B)之間實(shí)施。該步驟Aiv)為替代性方法步驟。其替代其中通過(guò)無(wú)電金屬鍍層使蝕刻塑料表面金屬化的實(shí)施方案的步驟Aiv)和步驟Av)。其余方法步驟與關(guān)于無(wú)電金屬鍍層的實(shí)施方案和關(guān)于直接電鍍的實(shí)施方案相同。在轉(zhuǎn)化溶液中處理塑料表面的作用是在塑料表面上形成足以用于直接電解金屬化的導(dǎo)電層而無(wú)需先前的無(wú)電金屬化。若方法步驟Aiii)中膠體溶液中的膠體為鈀/錫膠體,所使用的轉(zhuǎn)化溶液優(yōu)選為通過(guò)配位劑配位的銅離子的堿性溶液。例如,轉(zhuǎn)化溶液可包含有機(jī)配位劑,如酒石酸、乙二胺四乙酸(EDTA)或乙醇胺和/或其鹽,及銅鹽,如硫酸銅。轉(zhuǎn)化溶液可包含(a)可溶性金屬鹽、(b)第IA族金屬氫氧化物和(c)用于根據(jù)(a)的可溶性金屬鹽的金屬離子的配位劑。根據(jù)(a)的可溶性金屬鹽的金屬可選自Cu、Ag、Au、Ni及其混合物。根據(jù)(a)的可溶性金屬鹽可選自Ag(I)、Ag(II)、Au(I)、Au(II)、Ni(II)和Cu(II)鹽。優(yōu)選地,根據(jù)(a)的可溶性金屬鹽可為Cu(II)鹽。根據(jù)(a)的可溶性金屬鹽可以0.2mmol/l至200mmol/l,優(yōu)選1mmol/l至100mmol/l,更優(yōu)選5mmol/l至20mmol/l的濃度存在于轉(zhuǎn)化溶液中。根據(jù)(b)的第IA族金屬氫氧化物的金屬可選自Li、Na、K、Rb、Cs及其混合物,優(yōu)選為L(zhǎng)i、Na、K及其混合物。根據(jù)(b)的第IA族金屬氫氧化物可以0.05mol/l至5mol/l,優(yōu)選0.1mol/l至3mol/l,更優(yōu)選0.5mol/l至2mol/l濃度存在于轉(zhuǎn)化溶液中。根據(jù)(c)的配位劑可選自單羧酸和多羧酸,如酒石酸、葡萄糖酸、乳酸、乙酸、琥珀酸;螯合劑,如乙二胺四乙酸(EDTA);烷醇胺,如乙醇胺;亞氨基琥珀酸和/或其衍生物;前述物質(zhì)的鹽;及其混合物。根據(jù)(c)的配位劑可以5mmol/l至5mol/l,優(yōu)選50mmol/l至3mol/l,更優(yōu)選100mmol/l至2mol/l的濃度存在于轉(zhuǎn)化溶液中。優(yōu)選地,轉(zhuǎn)化溶液為堿性溶液。更優(yōu)選地,轉(zhuǎn)化溶液的pH值為8至15,甚至更優(yōu)選10至15,最優(yōu)選12至15。在處理非導(dǎo)電塑料表面時(shí),轉(zhuǎn)化溶液的溫度可為40℃至80℃,優(yōu)選45℃至70℃。處理時(shí)間可為1分鐘至20分鐘,優(yōu)選2分鐘至10分鐘。因此已經(jīng)呈現(xiàn)導(dǎo)電性的塑料表面可隨后進(jìn)行進(jìn)一步電解金屬化,以獲得功能性或裝飾性表面。在本發(fā)明的另一優(yōu)選實(shí)施方案中,還借助于直接電鍍使塑料表面金屬化。在該實(shí)施方案中,在方法步驟A)與方法步驟B)之間實(shí)施以下替代性方法步驟:Aiv)在含硫化物的溶液中處理該塑料表面。優(yōu)選地,替代性方法步驟Aiv)在方法步驟A)或方法步驟Ai)之后實(shí)施。該替代性方法步驟Aiv)替代其中經(jīng)由轉(zhuǎn)化溶液處理通過(guò)直接電鍍使蝕刻塑料表面金屬化的實(shí)施方案的步驟Aiv),且替代性方法步驟Aiv)替代無(wú)電金屬鍍層使蝕刻塑料表面金屬化的實(shí)施方案的步驟Aiv)和步驟Av)。出人意料地,該處理在塑料表面上產(chǎn)生金屬硫化物層,其具有足以在之后實(shí)現(xiàn)直接電鍍的導(dǎo)電性。所產(chǎn)生的金屬硫化物的金屬源自方法步驟A)中施加到塑料表面的含有根據(jù)(iii)的金屬離子源的蝕刻溶液。例如,若在方法步驟A)中使用含有10g/l硫酸銅的蝕刻溶液,基材表面覆蓋有含約0.7g/m2錳的量的二氧化錳層。該二氧化錳層含有約100mg/m2銅離子的量的銅離子。該銅量足以在隨后方法步驟B)中實(shí)現(xiàn)直接電鍍。因此已經(jīng)呈現(xiàn)導(dǎo)電性的塑料表面可隨后進(jìn)行進(jìn)一步電解金屬化,以獲得功能性或裝飾性表面。因此,在該實(shí)施方案中有可能僅通過(guò)實(shí)施三個(gè)方法步驟使非導(dǎo)電塑料表面金屬化:A)如上文所描述的用含有根據(jù)(iii)的金屬離子的至少一種酸性蝕刻溶液處理塑料表面,Aiv)在含硫化物的溶液中處理該塑料表面,及B)通過(guò)直接電鍍使該塑料表面金屬化。上文所描述的所有進(jìn)一步方法步驟均不是必要的。另外,沉積的金屬層具有良好品質(zhì)并具有良好附著強(qiáng)度。因此,含有根據(jù)(iii)的金屬離子的酸性高錳酸鹽蝕刻溶液不僅是優(yōu)異穩(wěn)定的。其還提供塑料表面的良好蝕刻,這導(dǎo)致其上沉積的金屬層的良好附著強(qiáng)度。其進(jìn)一步實(shí)現(xiàn)僅以三個(gè)方法步驟使塑料表面直接金屬化。含硫化物的溶液中的硫化物源選自堿金屬硫化物、堿土金屬硫化物及硫化銨。硫化物可為單硫化物、二硫化物、四硫化物或多硫化物。優(yōu)選地,含硫化物的溶液中的硫化物源選自單硫化鈉、二硫化鈉、單硫化鉀及二硫化鉀。硫化物源的濃度為0.5g/l至50g/l,優(yōu)選0.5g/l至10g/l,更優(yōu)選2g/l至8g/l。含硫化物的溶液可進(jìn)一步為堿性溶液。含硫化物的溶液的pH值為8至12,優(yōu)選9至11。因此,含硫化物的溶液包含氫氧根離子源。含硫化物的溶液中的氫氧根離子源選自堿金屬氫氧化物、堿土金屬氫氧化物及氫氧化銨。優(yōu)選地,氫氧根離子源選自氫氧化鈉和氫氧化鉀。氫氧根離子源的濃度為1g/l至25g/l,優(yōu)選5g/l至10g/l。硫化物溶液的處理實(shí)施1分鐘至10分鐘,優(yōu)選2分鐘至7分鐘的時(shí)間。硫化物溶液的處理在20℃至60℃,優(yōu)選30℃至50℃的溫度下實(shí)施。用含硫化物的溶液處理具有兩個(gè)作用。其在方法步驟A)期間還原沉積在塑料基材的表面上的二氧化錳。因此,其除去二氧化錳從而有助于隨后沉積的金屬層的附著強(qiáng)度。另外,含硫化物的溶液與源自本發(fā)明蝕刻溶液的根據(jù)(iii)的金屬離子形成導(dǎo)電金屬硫化物層。出人意料地,盡管金屬離子包含在二氧化錳層內(nèi),根據(jù)(iii)的金屬離子不與二氧化錳一起被含硫化物的溶液除去。出人意料地,足夠量的根據(jù)(iii)的金屬離子保留在塑料基材的表面上,以產(chǎn)生具有足以用于隨后直接電鍍的導(dǎo)電性的金屬硫化物層。在該實(shí)施方案中,可在方法步驟A)之前實(shí)施預(yù)處理步驟:預(yù)處理步驟:在包含至少一種二醇化合物的水溶液中處理該塑料表面。該方法步驟已在上文中描述并如上文所述實(shí)施。該方法步驟為任選方法步驟;其對(duì)于使塑料表面呈現(xiàn)足以實(shí)現(xiàn)直接電鍍的導(dǎo)電性不是必需的。在該實(shí)施方案中,可在方法步驟A)之后實(shí)施方法步驟Ai):Ai)用堿性蝕刻溶液處理該塑料表面。該方法步驟已在上文中描述并如上文所述實(shí)施。優(yōu)選地,任選的方法步驟Ai)在方法步驟A)與方法步驟B)之間,更優(yōu)選在方法步驟A)與方法步驟Aiv)之間實(shí)施。若實(shí)施替代性方法步驟Aiii),任選的方法步驟Ai)優(yōu)選在方法步驟A)與替代性方法步驟Aiii)之間實(shí)施。方法步驟Ai)為任選的方法步驟;其對(duì)于使塑料表面呈現(xiàn)足以實(shí)現(xiàn)直接電鍍的導(dǎo)電性不是必需的。但若實(shí)施,任選的方法步驟Ai)有助于提高隨后沉積至非導(dǎo)電塑料表面上的金屬層的附著強(qiáng)度。在該實(shí)施方案中,可在方法步驟A)與方法步驟B)之間實(shí)施以下替代性方法步驟:Aiii)在含有金屬離子源的溶液中處理塑料表面。該替代性方法步驟Aiii)替代其中經(jīng)由轉(zhuǎn)化溶液處理通過(guò)直接電鍍使蝕刻塑料表面金屬化的實(shí)施方案的步驟Aiii),且替代性方法步驟Aiii)替代其中通過(guò)無(wú)電金屬鍍層使蝕刻塑料表面金屬化的實(shí)施方案的步驟Aiii)。根據(jù)Aiii)的金屬離子的金屬選自鈦、鋯、釩、鈮、鉻、鉬、釕、鈷、銠、鎳、鈀、銅、銀、鋅、鉍及鎘。優(yōu)選地,該金屬選自鈦、鋯、釩、鈮、鉻、鉬、釕、鈷、銠、鎳、鈀、銅、銀、鋅及鎘。更優(yōu)選地,該金屬選自銅、鎳、鋅、鉻及鈷。甚至更優(yōu)選地,該金屬為銅。根據(jù)Aiii)的至少一種金屬離子源選自上文所列的根據(jù)Aiii)的金屬離子的金屬的水溶性鹽。優(yōu)選地,至少一種金屬離子源選自上文所列的金屬離子的金屬的水溶性硫酸鹽、磷酸鹽、硝酸鹽及高錳酸鹽。更優(yōu)選地,至少一種金屬離子源選自硫酸銅、磷酸銅、硝酸銅、高錳酸銅、硝酸銀、硫酸鋅、硝酸鋅、高錳酸鋅、硫酸鎘、硝酸鎘、硫酸鈦、硝酸鈦、硫酸鋯、硫酸氧釩、三氧化鉻、三硫酸鉻(III)、硫酸鉻(II)、硝酸鉻、硫酸鈷、硝酸鈷、硫酸鎳、硝酸鎳、硫酸銠及其水合物。最優(yōu)選地,至少一種金屬離子源選自硫酸銅、磷酸銅、硝酸銅、高錳酸銅及其水合物。根據(jù)Aiii)的金屬離子的濃度為1mmol/l至1mol/l,優(yōu)選10mmol/l至1mol/l,更優(yōu)選10mmol/l至100mmol/l,最優(yōu)選30mmol/l至100mmol/l。含有根據(jù)Aiii)的金屬離子源的溶液可在20℃至60℃,優(yōu)選30℃至50℃的溫度下使用。含有根據(jù)Aiii)的金屬離子源的溶液的處理實(shí)施1分鐘至10分鐘,優(yōu)選2分鐘至7分鐘的時(shí)間。含有根據(jù)Aiii)的金屬離子源的溶液可為堿性溶液。pH值可為7.5至12.5,優(yōu)選8至12。pH調(diào)節(jié)劑選自氨和/或胺。胺可為單乙醇胺和/或三乙醇胺。該替代性方法步驟Aiii)為任選的方法步驟;其對(duì)于使塑料表面呈現(xiàn)足以實(shí)現(xiàn)直接電鍍的導(dǎo)電性不是必需的。對(duì)于塑料表面金屬化的工業(yè)規(guī)模應(yīng)用,通常將制品固定于托架。這些是允許用連續(xù)溶液同時(shí)處理大量制品進(jìn)行個(gè)別方法步驟和用于電解沉積一個(gè)或多個(gè)金屬層的最后步驟的金屬載體系統(tǒng)。該托架自身一般涂覆有塑料,例如聚氯乙烯(PVC)。因此,托架原則上同樣構(gòu)成用于在塑料表面上的金屬化工藝的基材。然而,額外的托架金屬化是不期望的,因?yàn)樵谕扛仓破分蟊仨氃俅螐耐屑苌铣ソ饘賹?。這意味著額外的成本和去除的不便,以及額外的化學(xué)品消耗。此外,在這種情況下金屬化設(shè)備的生產(chǎn)力是較低的,因?yàn)橥屑苁紫缺仨氃谥匦卵b載制品之前去金屬化。若必須使用半濃鹽酸和/或使用硝酸進(jìn)行去金屬化,產(chǎn)生蒸氣和氣溶膠并且這些物質(zhì)在環(huán)境中導(dǎo)致腐蝕。另一問(wèn)題在于,在發(fā)生托架金屬化時(shí),不再可能以可重復(fù)的方式實(shí)現(xiàn)限定的電流密度,因?yàn)橥屑艿母采w程度通常是未知的,并且托架的準(zhǔn)確表面積同樣是未知的。隨后,結(jié)果通常為施加到電鍍塑料制品上的金屬層過(guò)薄。在本發(fā)明的另一實(shí)施方案中,可通過(guò)使不受本發(fā)明蝕刻溶液蝕刻的塑料材料的條在托架的塑料涂層上滑動(dòng)來(lái)防止托架金屬化。優(yōu)選地,在包括在含硫化物的溶液中處理塑料表面的方法步驟的本發(fā)明的實(shí)施方案中,可通過(guò)使不受本發(fā)明蝕刻溶液蝕刻的塑料材料的條在托架的塑料涂層上滑動(dòng)來(lái)防止托架金屬化。通過(guò)該方法步驟來(lái)防止托架金屬化尤其有利于包括在含硫化物的溶液中處理塑料表面的方法步驟的實(shí)施方案。不受本發(fā)明蝕刻溶液蝕刻的塑料材料選自聚四氟乙烯(PTFE)、聚偏二氟乙烯(PVDF)、六氟丙烯(HFP)和偏二氟乙烯(VDF或VF2)的共聚物、四氟乙烯(TFE)、偏二氟乙烯(VDF)和六氟丙烯(HFP)的三元共聚物或含全氟甲基乙烯醚(PMVE)的彈性體。不受本發(fā)明蝕刻溶液蝕刻的塑料材料的其它實(shí)例為T(mén)FE、VDF和丙烯的三元共聚物;以及由VDF、HFP、TFE、PMVE和乙烯組成的含氟彈性體。優(yōu)選地,不受本發(fā)明蝕刻溶液蝕刻的塑料材料可為熱收縮塑料材料。優(yōu)選地,不受本發(fā)明蝕刻溶液蝕刻的塑料材料的條也可具有可收縮套管(tubing),優(yōu)選熱收縮套管形式。使不受本發(fā)明蝕刻溶液蝕刻的塑料材料的條在其中金屬硫化物的導(dǎo)電層將導(dǎo)致托架金屬化的托架位置的塑料涂層上滑動(dòng)。優(yōu)選地,這些位置非常接近托架的電接點(diǎn)。不受本發(fā)明蝕刻溶液蝕刻的塑料材料的條未用導(dǎo)電金屬硫化物層覆蓋。因此,其中斷到涂覆在托架的部分原始塑料涂層上的導(dǎo)電金屬硫化物層的電接觸,并因此在直接電鍍期間防止托架金屬化。因此,使不受本發(fā)明蝕刻溶液蝕刻的塑料材料的條在托架的塑料涂層上滑動(dòng)的方法步驟可在方法步驟A)之前,優(yōu)選在預(yù)處理步驟之前實(shí)施。本發(fā)明的方法步驟B)為用金屬化溶液使塑料表面金屬化。方法步驟B)中的金屬化可以電解方式實(shí)現(xiàn)。對(duì)于電解金屬化,有可能使用任何所需的金屬沉積浴,例如用于沉積鎳、銅、銀、金、錫、鋅、鐵、鉛或其合金。本領(lǐng)域技術(shù)人員熟悉這樣的沉積浴。通常使用Watts鎳浴作為亮鎳浴,其包含硫酸鎳、氯化鎳和硼酸,以及糖精作為添加劑。用作亮銅浴的組合物實(shí)例為包含硫酸銅、硫酸、氯化鈉和有機(jī)硫化合物的一種組合物,其中所述硫處于低氧化態(tài),例如有機(jī)硫化物或二硫化物作為添加劑。具體地,作為弱酸性至堿性的電沉積浴組合物適用于包括在含硫化物的溶液中處理塑料表面的方法步驟的本發(fā)明的實(shí)施方案。適用于該實(shí)施方案的電沉積浴的pH值為3至10。方法步驟B)中的塑料表面金屬化的作用在于用金屬涂覆塑料表面,該金屬選自上文所列的用于沉積浴的金屬。在本發(fā)明的另一實(shí)施方案中,在方法步驟B)之后,實(shí)施以下另一方法步驟:Bi)在升高的溫度下儲(chǔ)存金屬化塑料表面。隨著在其中通過(guò)濕式化學(xué)手段用金屬涂覆非導(dǎo)體的所有電鍍工藝中,金屬與塑料基材之間的附著強(qiáng)度在施加金屬層之后的第一時(shí)間段內(nèi)增加。在室溫下,該方法在約三天之后是完全的。其可通過(guò)在升高的溫度下儲(chǔ)存來(lái)顯著加速。這樣的步驟可能涉及在50℃至80℃的升高的溫度下處理由ABS塑料制成的金屬化制品5分鐘至60分鐘的時(shí)間段,優(yōu)選在70℃的溫度下。在升高的溫度下處理或儲(chǔ)存金屬化塑料表面的作用在于,進(jìn)一步提高初始相對(duì)低的附著強(qiáng)度,使得在方法步驟Bi)之后實(shí)現(xiàn)在至少或大于0.6N/mm的期望范圍內(nèi)的施加到塑料表面的金屬層的附著強(qiáng)度。因此,本發(fā)明的方法能夠在良好的方法可靠性和隨后施加的金屬層的優(yōu)異附著強(qiáng)度的情況下實(shí)現(xiàn)制品的非導(dǎo)電塑料表面的金屬化。在這種情形下,不僅平面塑料表面通過(guò)本發(fā)明的方法金屬化而具有高附著強(qiáng)度;而且,不均勻形狀的塑料表面也可具有均勻且強(qiáng)力附著的金屬涂層。實(shí)施例實(shí)施例1在電鍍生產(chǎn)線中,電鍍ABS/PC共混部件(MiniFrontFinishers,由BayblendT45PG制成)。為實(shí)現(xiàn)該目標(biāo),生產(chǎn)線包括以下方法步驟:在25±1℃下含有40%的二乙二醇乙醚乙酸酯溶液的390l槽(預(yù)處理步驟,7分鐘)、在70℃下含有100g/l高錳酸鈉和10g/l硫酸(96%)的溶液的525l槽(不具有根據(jù)(iii)的金屬離子的對(duì)比酸性蝕刻溶液;代替本發(fā)明方法步驟A)的蝕刻步驟,10分鐘)、含有由25ml/l(96%)硫酸和30ml/l的30%過(guò)氧化氫制成的溶液的340l槽(在40℃下的方法步驟Aii))、預(yù)浸漬溶液(初步浸漬步驟,在環(huán)境溫度下300ml/l的36%鹽酸)、活化劑浴(方法步驟Aiii),膠體鈀,40mg/l,37℃下進(jìn)行5分鐘)、加速劑(方法步驟Aiv),Atotech的AdhemaxACC1,在45℃下進(jìn)行5分鐘)、無(wú)電鎳浴(方法步驟Av),Atotech的AdhemaxNiLFS,在40℃下進(jìn)行10分鐘),隨后銅電鍍步驟進(jìn)行70分鐘(來(lái)自Atotech的CupracidHT,3.5A/dm2,室溫;方法步驟B))。在所有步驟之間,用水兩次沖洗用于清潔塑料表面,并防止溶液進(jìn)入隨后的方法浴中。每天使用所描述的電鍍生產(chǎn)線布置電鍍2m2塑料表面。每天使用光度法(在520nm處的吸收)檢測(cè)蝕刻步驟中的高錳酸鹽的濃度。利用結(jié)果,隨后補(bǔ)充消耗的高錳酸鹽。在操作的第一周期間,未發(fā)現(xiàn)大量消耗。在第二周時(shí),添加約2.5kg的高錳酸鈉,在下一周添加11.5kg并且在操作的第五周時(shí)添加幾乎23kg。在第五周之后,將20g/l硫酸銅五水合物添加至酸性蝕刻溶液中,得到含有銅離子作為根據(jù)(iii)的金屬離子的本發(fā)明蝕刻溶液的組合物。在操作的第六和第七周時(shí),不再發(fā)現(xiàn)高錳酸鹽的大量消耗。然而,在第六和第七周期間電鍍的ABS/PC共混部件完全覆蓋有金屬,且具有與在第一至第五周期間電鍍的部件相同的高附著強(qiáng)度。因此,通過(guò)本發(fā)明蝕刻溶液及方法蝕刻的ABS/PC部件具有良好的品質(zhì)。由于蝕刻導(dǎo)致的高錳酸鹽的消耗幾乎無(wú)法檢測(cè),并且由于自分解導(dǎo)致的高錳酸鹽的消耗沒(méi)有出現(xiàn)在本發(fā)明蝕刻溶液中。實(shí)施例2在應(yīng)用實(shí)驗(yàn)室中,電鍍具有不同組合物的塑料部件:ABS(NovodurP2MC)和ABS-PC共混物(BayblendT45PG)。使用兩個(gè)70l槽,對(duì)于ABS-PC在25℃下含有40%的二乙二醇乙醚乙酸酯溶液,和對(duì)于ABS在45℃下10%乙二醇丁醚和15%二乙二醇乙醚乙酸酯的溶液。ABS-PC部件在其相應(yīng)溶液中預(yù)處理7分鐘,和ABS部件在其相應(yīng)溶液中預(yù)處理10分鐘(預(yù)處理步驟)。170l蝕刻槽含有酸性高錳酸鹽溶液(100g/l高錳酸鈉,10g/l96%硫酸,70℃)。所有塑料部件均用酸性高錳酸鹽溶液處理10分鐘(不具有根據(jù)(iii)的金屬離子的對(duì)比酸性蝕刻溶液;代替本發(fā)明方法步驟A)的蝕刻步驟)。所有其它方法步驟均與已在實(shí)施例1中描述的方法步驟相同,僅以70l的較小體積。在電鍍一周之后,必須從蝕刻槽底部除去約5kg濕二氧化錳淤渣。淤渣影響了蝕刻工藝,導(dǎo)致隨后方法步驟中的一些漏鍍。在清潔槽和使用酸性過(guò)氧化氫溶液從槽壁除去二氧化錳之后,將蝕刻溶液泵送回到槽中。將20g/l硫酸銅五水合物添加至酸性蝕刻溶液,得到含有銅離子作為根據(jù)(iii)的金屬離子的本發(fā)明蝕刻溶液的組合物。在操作一周之后,再次將本發(fā)明酸性蝕刻溶液泵出。僅發(fā)現(xiàn)痕量的二氧化錳淤渣。因此,實(shí)施例1中顯示的高錳酸鹽消耗下降伴隨著二氧化錳的形成減少。實(shí)施例3在生產(chǎn)線中,電鍍ABS塑料基材。為實(shí)現(xiàn)該目標(biāo),用10%乙二醇丁醚和15%二乙二醇乙醚乙酸酯的溶液填充3500l槽,并保持在45℃下且在其中處理基材(預(yù)處理步驟進(jìn)行10分鐘)。在一次用水的沖洗步驟之后,在70℃下在保持100g/l高錳酸鈉和10g/l硫酸的溶液的4800l槽中處理塑料基材10分鐘(不具有根據(jù)(iii)的金屬離子的對(duì)比酸性蝕刻溶液;代替本發(fā)明方法步驟A)的蝕刻步驟)。將該槽連接至層狀澄清器(350l體積)以從溶液分離淤渣。在一次沖洗之后,在60℃下在堿性高錳酸鹽溶液(30g/lNaMnO4和20g/lNaOH)中處理塑料基材10分鐘;方法步驟A°i)。隨后,使用酸性過(guò)氧化氫(在40℃下的25ml/l96%硫酸和30ml/l30%過(guò)氧化氫;方法步驟Aii))清潔塑料表面除去二氧化錳。隨后,如實(shí)施例1中所述初步浸漬塑料基材(初步浸漬步驟),并在45℃下在鈀膠體(100mg/l鈀,NeoLink活化劑,Atotech產(chǎn)品)中將其活化(方法步驟Aiii))。為獲得沉積的鈀膠體的導(dǎo)電層,在55℃下將該基材浸入基于銅離子的轉(zhuǎn)化溶液(來(lái)自Atotech的NeoLink,方法步驟Aiv))中3分鐘。通過(guò)在20℃下將它們引入銅電鍍?cè)?CupracidUltra,來(lái)自Atotech,方法步驟B))中60分鐘并施加3.5A/dm2電流來(lái)將所有基材鍍銅。在操作一周且僅處理3m2塑料表面之后,通過(guò)層狀澄清器分離約30kg二氧化錳淤渣。在第一周之后,將20g/l硫酸銅五水合物添加至酸性蝕刻溶液中,得到含有銅離子作為根據(jù)(iii)的金屬離子的本發(fā)明蝕刻溶液的組合物。在下一周,蝕刻約15m2ABS塑料基材。在這周之后,僅發(fā)現(xiàn)痕量的二氧化錳淤渣。實(shí)施例4如前述實(shí)施例所示,本發(fā)明酸性蝕刻溶液的高錳酸鹽主要消耗用于蝕刻塑料基材的表面。因此,形成二氧化錳,其分離至蝕刻溶液中。在酸存在下,二氧化錳催化水的氧化,產(chǎn)生更多的二氧化錳。在該方法中,釋放氧氣。因此,逸出的氧氣是高錳酸鹽的分解反應(yīng)的指示劑。用具有逸出氣體的出口的玻璃塞封閉總體積為約一升的圓底玻璃燒瓶。將來(lái)自出口的硅膠管引入水浴中,其中倒置填充有水的刻度玻璃量筒以收集所有逸出的氣體。將圓底燒瓶放置于保持在70℃下具有水的燒杯中。將精確600ml預(yù)加熱的高錳酸鹽溶液(100g/l高錳酸鈉、10g/l96%硫酸)放入玻璃燒瓶中。在該高錳酸鹽溶液中,預(yù)先蝕刻3dm2預(yù)處理的ABS塑料基材10分鐘(不具有根據(jù)(iii)的金屬離子的對(duì)比酸性蝕刻溶液;代替本發(fā)明方法步驟A)的蝕刻步驟)。從高錳酸鹽溶液中除去基材。將塞子施加于燒瓶,并在允許幾分鐘調(diào)節(jié)溫度之后,收集逸出的氣體。在特定時(shí)間間隔期間收集的氧氣量概括于表1中,且第一試驗(yàn)的數(shù)據(jù)顯示于圖1中。重復(fù)該試驗(yàn)。這次,酸性高錳酸鹽溶液含有10g/l硫酸銅五水合物,并因此對(duì)應(yīng)于含有銅離子作為根據(jù)(iii)的金屬離子的本發(fā)明蝕刻溶液。在特定時(shí)間間隔期間收集的氧氣量概括于表2中,且第一試驗(yàn)的數(shù)據(jù)顯示于圖2中。在對(duì)比酸性高錳酸鹽溶液中,氧氣逸出穩(wěn)定持續(xù),且所產(chǎn)生的氧氣量顯著高于含有根據(jù)(iii)的金屬離子的本發(fā)明酸性高錳酸鹽溶液。另外,氧氣的逸出在本發(fā)明的高錳酸鹽溶液中接近閾值。因此,在一段時(shí)間之后,本發(fā)明的高錳酸鹽溶液中氣體逸出停止。表1:不具有根據(jù)(iii)的金屬離子的酸性高錳酸鹽溶液中的氧氣逸出持續(xù)時(shí)間[min]010325585123166200260320氧氣[ml]072027324148556574表2:具有根據(jù)(iii)的金屬離子的酸性高錳酸鹽溶液中的氧氣逸出持續(xù)時(shí)間[min]0224575100150195255320氧氣[ml]51321232829293132實(shí)施例5沉積于蝕刻塑料表面上的金屬層的附著強(qiáng)度在25±1℃下,將四個(gè)ABS/PC共混部件(MiniFrontFinishers,由BayblendT45PG制成)浸入40%的二乙二醇乙醚乙酸酯溶液的溶液中7分鐘(預(yù)處理步驟)。在流水下沖洗所有部件1分鐘。隨后,將部件1和3引入100g/l高錳酸鈉和10g/l96%硫酸的浴(不具有根據(jù)(iii)的金屬離子的對(duì)比酸性蝕刻溶液;代替本發(fā)明方法步驟A)的蝕刻步驟)中10分鐘。同時(shí),將部件2和4浸入100g/l高錳酸鈉、10g/l96%硫酸和20g/l硫酸銅五水合物的浴中,將其保持在70℃下(本發(fā)明的酸性蝕刻溶液;方法步驟A))。之后,在60℃下使部件3和4在堿性高錳酸鹽溶液中(30g/lNaMnO4和20g/lNaOH)經(jīng)受另一蝕刻10分鐘;方法步驟A°i)。隨后,清潔所有部件以在50g/l96%硫酸和30ml/l30%過(guò)氧化氫的溶液中除去沉積的二氧化錳(方法步驟Aii))。在短暫浸入300ml/l36%鹽酸溶液中之后(方法步驟初步浸漬),在45℃下在基于鈀膠體的膠體活化劑(來(lái)自Atotech的AdhemaxAktivatorPL,25ppm鈀)中使部件1和2活化3分鐘(方法步驟A°iii))。以相同方式使部件3和4活化(來(lái)自Atotech的AdhemaxAktivatorPL,100ppm鈀)。在50℃下從部件1和2除去鈀粒子的保護(hù)殼進(jìn)行5分鐘(來(lái)自Atotech的AdhemaxACC1加速劑,方法步驟A°iv))。隨后,在45℃下在無(wú)外部電流的情況下使部件1和2鍍鎳10分鐘(AdhemaxLFS,來(lái)自Atotech,方法步驟A°v))并沖洗。為獲得沉積的鈀膠體的導(dǎo)電層,在55℃下將部件3和4浸入基于銅離子的轉(zhuǎn)化溶液(來(lái)自Atotech的NeoLink,方法步驟Aiv))中3分鐘。通過(guò)在20℃下將它們引入銅電鍍?cè)?CupracidUltra,來(lái)自Atotech,方法步驟B))中60分鐘并施加3.5A/dm2電流使所有部件鍍銅。將所有部件儲(chǔ)存在80℃下30分鐘(方法步驟Bi))。隨后,用刀切出寬度為約1cm的金屬化塑料板的條,并使用拉力試驗(yàn)機(jī)(來(lái)自Instron)將金屬層從塑料拉出(2009年重新批準(zhǔn)的ASTMB5331985)。所獲得的附著強(qiáng)度概括于表3中。表3:沉積于不同蝕刻的塑料表面上的金屬層的附著強(qiáng)度實(shí)施例6在45℃下,將由ABS(NovodurP2MC)制成的尺寸為15cm×5cm×0.3cm的板浸入15%二乙二醇乙醚乙酸酯和10%乙二醇單丁醚的溶液中10分鐘(預(yù)處理步驟)。用磷酸鉀緩沖液將溶液調(diào)節(jié)至pH7。用冷水沖洗該板,之后將其浸入100g/l高錳酸鈉和10g/l96%硫酸和10g/l硫酸銅五水合物的浴中,將其保持在70℃下(本發(fā)明的酸性蝕刻溶液;方法步驟A))10分鐘。在另一沖洗步驟之后,在40℃下將該板浸入5g/l硫化鈉溶液中3分鐘,以獲得導(dǎo)電層(方法步驟Aiv))。板表面的顏色由深褐色變至米黃色。隨后,使該板經(jīng)受Watts鎳鍍?cè)〔⑴c電流源電連接。將該板與陽(yáng)極之間的電壓調(diào)節(jié)至3.5V。用鎳電鍍?cè)摪?分鐘(方法步驟B))并沖洗。之后,在20℃下通過(guò)施加3.5A/dm2的電流在酸性銅浴(Cupracid210,AtotechDeutschlandGmbH的產(chǎn)品)中用銅電鍍?cè)摪?0分鐘(方法步驟B))。鎳層和銅層完全覆蓋該板表面并且不具有缺陷。實(shí)施例7使用由ABS/PC(BayblendT45)制成的且具有與實(shí)施例6中使用的板相同尺寸的板重復(fù)實(shí)施例6。在銅層沉積之后,將ABS/PC板在70℃下儲(chǔ)存60分鐘(方法步驟Bi))。隨后,如實(shí)施例5中所述測(cè)量鎳和銅的沉積層堆疊的附著強(qiáng)度。該附著強(qiáng)度為0.7N/mm至0.9N/mm。實(shí)施例8在22℃下,將由ABS(Polylac727,ChiMeiCorp.的產(chǎn)品)制成的且尺寸為15cm×5cm×0.3cm的板浸入40vol%的二乙二醇乙醚乙酸酯溶液中10分鐘(預(yù)處理步驟)。之后,如實(shí)施例6中所述用硫化物溶液處理該板并用鎳和銅電鍍。隨后,如實(shí)施例5中所述測(cè)量鎳和銅的沉積層堆疊的附著強(qiáng)度。附著強(qiáng)度為0.8N/mm至1.1N/mm。實(shí)施例9使由HFP和VDF的共聚物(Viton,DuPont的產(chǎn)品)制成的套管部件在PVC涂覆的固持托架的觸點(diǎn)上滑動(dòng)(預(yù)處理步驟之前的方法步驟)。套管覆蓋金屬觸點(diǎn)與PVC涂層之間的接合點(diǎn)。用于固定待電鍍的制品的部分金屬觸點(diǎn)沒(méi)有套管。套管部件具有約5mm的長(zhǎng)度。對(duì)于該實(shí)施例,選擇具有特別強(qiáng)的托架金屬化傾向的舊固持托架。將ABS模制件固定于固持托架的觸點(diǎn)。如實(shí)施例6中所述處理模制件和托架。在沒(méi)有任何缺陷的情況下ABS模制件完全覆蓋有鎳層和銅層,同時(shí)托架不含任何金屬沉積物。實(shí)施例10:在45℃下,將四個(gè)ABS模制件(由Polylac727制成的閥蓋,ShimeiCorp.的產(chǎn)品)浸入15%二乙二醇乙醚乙酸酯和10%乙二醇單丁醚的溶液中2分鐘(預(yù)處理步驟)。用磷酸鉀緩沖液將溶液調(diào)節(jié)至pH7。之后,用冷水澈底沖洗模制件。將模制件(1至4)浸到由10g/l96%硫酸、20g/l硫酸銅五水合物和不同濃度的高錳酸鈉(參見(jiàn)表4)組成的根據(jù)本發(fā)明的溶液中(方法步驟A))。本發(fā)明蝕刻溶液具有70℃的溫度。用本發(fā)明蝕刻溶液處理模制件1至4進(jìn)行10分鐘。之后,清潔模制件以在50g/l96%硫酸和30ml/l30%過(guò)氧化氫的溶液中除去沉積的二氧化錳(方法步驟Aii))。在短暫浸入300ml/l36%鹽酸溶液中之后(方法步驟初步浸漬),在45℃下在基于鈀膠體的膠體活化劑(來(lái)自Atotech的AdhemaxAktivatorPL,25ppm鈀)中使模制件活化5分鐘(方法步驟A°iii))。在40℃下除去鈀粒子的保護(hù)殼進(jìn)行5分鐘(來(lái)自Atotech的AdhemaxACC1加速劑,方法步驟A°iv))。隨后,在40℃下在沒(méi)有外部電流的情況下使模制件鍍鎳10分鐘(AdhemaxLFS,來(lái)自Atotech,方法步驟A°v))并沖洗。隨后,通過(guò)在25℃下將它們引入銅電鍍?cè)?Cupracid5000,來(lái)自Atotech,方法步驟B))中60分鐘并施加4A/dm2電流使模制件鍍銅。將模制件在80℃下儲(chǔ)存30分鐘(方法步驟Bi))。隨后,如實(shí)施例5中所述測(cè)量沉積的金屬層的附著強(qiáng)度。所獲得的附著強(qiáng)度概括于表4中。表4:沉積在不同蝕刻的塑料表面上的金屬層的附著強(qiáng)度高錳酸鹽濃度[g/l]附著強(qiáng)度[N/mm]101.59202.07302.17實(shí)施例11如實(shí)施例4中所述,在不存在和存在根據(jù)(iii)的金屬離子的情況下測(cè)量具有不同高錳酸鹽濃度的酸性高錳酸鹽溶液中所產(chǎn)生的氧氣量。高錳酸鹽溶液的組分濃度和測(cè)量結(jié)果概括于表5中并顯示于圖3中。表5:在不存在和存在根據(jù)(iii)的金屬離子的情況下酸性高錳酸鹽溶液中的氧氣逸出「---」意味著:未測(cè)量到。實(shí)施例12如實(shí)施例4中所述,在不存在和存在根據(jù)(iii)的金屬離子(根據(jù)本發(fā)明)以及存在不同于根據(jù)(iii)的金屬離子的金屬離子(對(duì)比)的情況下,測(cè)量酸性高錳酸鹽溶液中所產(chǎn)生的氧氣量。高錳酸鹽溶液的組分濃度及測(cè)量結(jié)果概括于表6中且顯示于圖4中。表6:在不存在及存在根據(jù)(iii)的金屬離子的情況下酸性高錳酸鹽溶液中的氧氣逸出「---」意味著:未測(cè)量到。將16.2g/l硫酸鈀(II)添加至由100g/l高錳酸鈉和10g/l96%硫酸組成的溶液中。隨即,溶液幾乎以爆發(fā)方式分解。當(dāng)前第1頁(yè)1 2 3