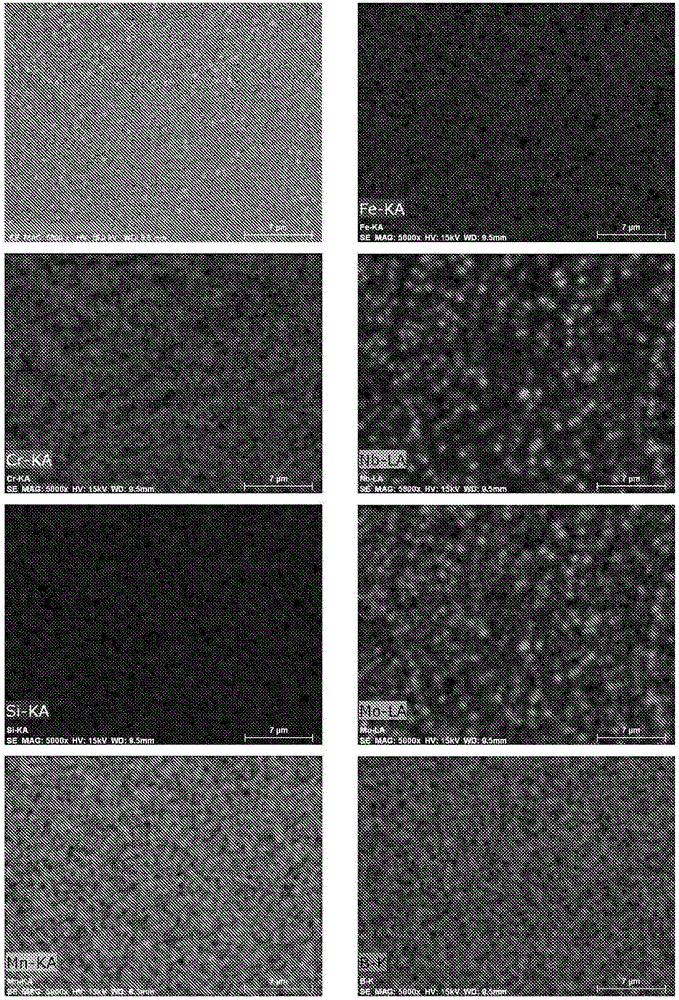
本申請要求于2014年5月16日提交的美國臨時專利申請序列號61/994758的益處,其通過引用完全并入本文。
技術(shù)領(lǐng)域:
本發(fā)明涉及合金和以逐層方式制備獨立的(freestanding)金屬性材料的方法。
背景技術(shù):
:在許多應(yīng)用例如鉆桿加硬帶、采礦卡車車罩和鍋爐管中,將鐵類金屬用作涂層,其中該涂層對相對不耐磨損的零件提供磨損和磨蝕抵抗性。可以通過各種技術(shù),例如HVOF或雙絲弧熱噴涂和PTAW或GMAW堆焊層將這些涂層施加到基材。通常,耐磨損的鐵類金屬涂層的特征在于相對低的成本和相對高的表面硬度,其使材料的耐磨損性成為可能,并保護下方的基材。用作耐磨損涂層的材料被設(shè)計成附著到基材并提供所需的表面性能,并因此在很大程度上依賴于基材的非表面性能例如強度和韌性。用于耐磨損的鐵類金屬涂層的例子包括鉻碳化物、復(fù)合碳化物、鈦碳化物、釩碳化物和工具鋼。在本文中,逐層構(gòu)造可理解為其中逐層堆積或鋪設(shè)材料層以制造零件的方法。逐層構(gòu)造的實例包括采用激光(PBF-L)或電子束(PBF-E)能量源的粉末床融合、定向能量沉積(DED)、粘合劑噴射(BJ)、片材層壓、材料擠出、材料噴射和光固化(Vatphotopolymerization)。與金屬一起使用的主要逐層構(gòu)造工藝包括PBF-L、PBF-E、DED和BJ。逐層構(gòu)造方法具有從各種延展性金屬,包括不銹鋼合金、鋁合金、鈦合金、鎳基合金和鈷鉻合金構(gòu)造零件的優(yōu)異能力。在用于金屬的液相逐層構(gòu)造工藝例如PBF-L、PBF-E和DED中,構(gòu)造材料從固相轉(zhuǎn)變?yōu)橐合?熔化),然后再轉(zhuǎn)變回固相(凝固)??梢詫⒂糜谌刍哪芰吭淳劢沟讲牧媳砻娴囊刍南鄬π〉膮^(qū)域,因此可以將熔化中的材料的體積控制到相對小的體積。與大的固體體積接觸的小的熔融體積具有以相對快速的方式凝固的能力。當(dāng)與鍛造金屬性能相比時,該快速凝固造成晶粒尺寸細化,并增加機械性能。盡管以這種方式構(gòu)造的零件的機械性能通常比鍛造過程相對高,但上述材料都不具有相對高硬度和耐磨損性的組合,并且具有最高硬度的那些通常需要熱處理工藝,如淬火和回火或固溶和時效,以得到相對高的硬度和耐磨損性。這樣的熱處理的附加步驟通常導(dǎo)致增加的產(chǎn)率損失和部分畸變,這是不期望的。表1列出了通過在應(yīng)力釋放和熱處理條件下的PBF-L產(chǎn)生的各種相對高硬度金屬的典型硬度。表1材料鋼種狀態(tài)微硬度(HV)不銹鋼17-4PH應(yīng)力釋放288不銹鋼17-4PHH900421不銹鋼15-5PH應(yīng)力釋放315不銹鋼15-5PHH900419不銹鋼316L應(yīng)力釋放的203不銹鋼316L200°F下持續(xù)2小時171鋼18%Ni馬氏體時效300應(yīng)力釋放的340鋼18%Ni馬氏體時效300915°F下持續(xù)6小時545鋼H13應(yīng)力釋放的613鋼H131076°F下持續(xù)1小時(x2)653鎳基因科內(nèi)爾718應(yīng)力釋放的263鎳基因科內(nèi)爾718AMS5662408鈦Ti6Al4V應(yīng)力釋放的362鈦Ti6Al4V1725°F下持續(xù)45分鐘316對于很多應(yīng)用,期望零件中的高硬度和耐磨損性以增加服役中的零件的耐久性(壽命)。本發(fā)明現(xiàn)在鑒定了合金和相應(yīng)的制造工序,其提供通過逐層堆積制備的分層金屬性材料,顯示出相對高硬度和耐磨損性的獨特組合。此外,現(xiàn)在可以通過消除施加到現(xiàn)有的逐層堆積已知金屬的上述熱處理工藝來實現(xiàn)這樣的性能。另外,本文的性能不需要淬火和/或回火。技術(shù)實現(xiàn)要素:將逐層構(gòu)造施加到合金以產(chǎn)生相對高的硬度和耐磨損的獨立材料。合金包含含有至少50原子%Fe和選自Ti、Zr、Hf、V、Nb、Ta、Cr、Mo、W、Al、La、Ce、Pr、Nd、Sm、Eu、Gd、Tb、Dy、Ho、Er、Tm、Yb、和Lu中的至少一種元素;和選自B、C、N、O、P和S中的至少一種元素的鐵類合金。根據(jù)2010年的ASTMG65-10ProcedureA,硬度值是在900-1800HV的范圍內(nèi),和耐磨損性的值是在6-53mm3的范圍內(nèi)。實現(xiàn)了這樣的值,而無需用熱后處理各層堆積繼之以淬火和/或回火。逐層構(gòu)造允許形成可用于應(yīng)用例如泵、閥和軸承中的金屬性零件。本發(fā)明還更具體地涉及金屬性部件的逐層構(gòu)造方法,其包括:提供顆粒形式的合金,其包含有59.0重量%至78.0重量%水平的Fe、3.0重量%至5.0重量%水平的B、14.0重量%至20.0重量%水平的Cr、0.5重量%至7.0重量%水平的C、任選至多11.0重量%水平的Mo、任選至多2.5重量%水平的Mn、任選至多4.5重量%水平的Nb、任選至多2.0重量%水平的Si、任選至多7.0重量%水平的W;提供基材;通過將所述合金熔化成熔化狀態(tài)和冷卻并形成凝固層,將所述合金的一個或多個層施加到所述基材上,其中每個所述固體層具有形成狀態(tài)的5.0至200.0微米的厚度;和任選地除去所述基材以形成獨立的金屬性部件,并且其中所述一個或多個固體層顯示在900-1800HV范圍內(nèi)的硬度。附圖說明通過結(jié)合附圖并參照實施方案的以下描述,本公開的上述和其他特征以及實現(xiàn)它們的方式將變得更加清楚和更好理解,其中:圖1是通過PBF-L加工的鐵類合金的SEM顯微照片,示出了存在于富Fe基體中的碳化物和碳化硼相。圖2包含通過PBF-L制得的合金1的元素圖(elementalmap),其顯示了包含在各相中的主要元素Fe、Cr、Nb、Si、Mo、Mn和B。通過在掃描電子顯微鏡中的能量分散x射線光譜儀中產(chǎn)生所述元素圖。圖3示出了用非優(yōu)化的參數(shù)逐層構(gòu)造的相對高硬度的鐵類材料(1250HV的硬度)的截面。圖4示出了用優(yōu)化的參數(shù)逐層構(gòu)造的相對高硬度的鐵類材料(1250HV的硬度)的截面。圖5示出了用優(yōu)化的逐層構(gòu)造參數(shù)制造的無裂紋的、高硬度的功能性軸承部件;圖6示出相對高硬度(1540HV)和高耐磨損性的截面,和逐層構(gòu)建的高硬度鐵類金屬的無裂紋部分的截面,否則其因誘發(fā)應(yīng)力而易于開裂。詳細說明本發(fā)明涉及構(gòu)造獨立和相對硬和耐磨損的鐵基金屬性材料的方法,以通過在初始基材上的逐層堆積連續(xù)金屬層提供構(gòu)建的金屬性結(jié)構(gòu)。逐層堆積是指熔化金屬性合金并冷卻和凝固以形成材料層(其成為用于額外的熔化合金層的隨后施加的下方固體層),接著再次冷卻的整體工序。由該逐層工序形成的構(gòu)建結(jié)構(gòu)中可以或可以不包括基材。因此,提到獨立的金屬性材料,在本文中理解為這種情況:其中在基材上的逐層堆積用于形成給定的構(gòu)建結(jié)構(gòu),該結(jié)構(gòu)可以隨后在各種應(yīng)用中用作金屬性部件。用于引發(fā)逐層堆積的合適基材可以包括奧氏體、鐵素體和馬氏體鋼材,且可具有在3mm-100mm范圍內(nèi)的厚度。正如所指出的,通常不包括基材作為最終結(jié)構(gòu)的一部分,且在建立結(jié)構(gòu)后,可以通過多種技術(shù)包括放電加工(EDM)和機械鋸切分開該基材和結(jié)構(gòu)。本文的逐層工序考慮了各具有5.0微米至200.0微米的厚度的單一層的堆積。然后,可提供該逐層工序用于總厚度為5微米至大于50.0mm并且更典型地大于250.0mm的沉積。因此,對于堆積層的合適的厚度范圍是5.0微米和更高。然而,更常見的是,厚度范圍是從5.0微米至250.0mm。當(dāng)在液相逐層構(gòu)造工藝中加工時,考慮鐵基合金的相對高硬度是相對精細尺度的顯微結(jié)構(gòu)(晶粒尺寸),和存在于鐵基合金中的相的結(jié)果。更具體地,本文中的鐵類合金是這樣的:當(dāng)在高溫下形成本文的液相并使其冷卻和凝固且形成給定層時,顯微結(jié)構(gòu)優(yōu)選由在富鐵基體中均勻分布的碳化物和碳化硼相構(gòu)成,其中碳化物和碳化硼相的尺寸范圍為約10.0nm-10,000nm。示例性鐵類合金包含至少50%的Fe和選自Ti、Zr、Hf、V、Nb、Ta、Cr、Mo、W、Al、La、Ce、Pr、Nd、Sm、Eu、Gd、Tb、Dy、Ho、Er、Tm、Yb和Lu中的至少一種元素;和選自B、C、N、O、P和S中的至少一種元素。在本發(fā)明的特定方面,該合金將具有由式Fe(100-x-y)M(x)B(y)(原子百分數(shù))表示的組成,其中M表示選自Ti、Zr、Hf、V、Nb、Mo、Ta、Cr、W和Mn中的至少一種元素,其中15≥x≥4,其中25≥y≥2,并且其中35≥(x+y)≥7。B是指硼。該合金還可以含有X(Si、Ge、P、Ga等)和/或T(Au、Co、Ni等)。本發(fā)明的合金優(yōu)選包含少于11種元素,并且可以更優(yōu)選包含少于七種元素。此外,該合金可包含少于五種元素。通常,本發(fā)明的合金在其成中具有四至六種元素。這些元素是鐵、鉻、硼和/或磷以及鉬和鎢中的一種或兩種。值得注意的是,上述合金具有相對高的開裂敏感性,并且通常用作具有相對高水平的開裂的涂層。因此,沒有預(yù)期到這種合金對于如本文所述的逐層工序是有用的,并出人意料地提供逐層堆積和金屬性零件,其具有意想不到的硬度和磨損性能。也就是說,在液相逐層構(gòu)造中加工時,鐵類合金呈現(xiàn)出在富鐵基體中各種均勻分布的相對小的、硬的碳化物相,例如硼碳化物、鉻碳化物、鉬碳化物和鈮碳化物,其提供了鐵類合金中相對高的硬度。由于過程的快速冷卻,各相的尺寸是相對小的,并優(yōu)選小于10.0微米,更優(yōu)選小于5.0微米,且最優(yōu)選小于1.0微米。因此,碳化硼相要存在于本文的鐵類合金的逐層構(gòu)造中,使得它們具有0.1微米至10.0微米,更優(yōu)選0.1微米至5.0微米,最優(yōu)選0.1微米至1.0微米的尺寸范圍。與上文有關(guān),可通過光學(xué)顯微鏡和/或掃描電子顯微鏡容易地確定碳化硼相的相尺寸以及晶粒尺寸。此外,在PBF-L工藝中所固有的相對高的冷卻速度在鐵類合金中產(chǎn)生特征在于相對小的晶粒的顯微結(jié)構(gòu),優(yōu)選低于10微米,更優(yōu)選低于5微米,最優(yōu)選小于1微米。因此,存在于本文中的逐層構(gòu)造中的晶粒以如下方式存在:它們具有0.1微米至10微米,更優(yōu)選0.1微米至5微米,最優(yōu)選0.1微米至1.0微米的尺寸范圍。在逐層構(gòu)造中所產(chǎn)生的鐵類合金的結(jié)構(gòu)導(dǎo)致相對高的硬度,優(yōu)選在900-1800HV的范圍內(nèi),更優(yōu)選在950-1700HV的范圍內(nèi),最優(yōu)選在980-1600HV的范圍內(nèi)。圖1示出了通過PBF-L加工的具有各種碳化物相的鐵類合金(合金1)的代表性顯微照片。圖2示出通過PBF-L產(chǎn)生的合金1的元素圖,顯示了包含在各相中的主要元素Fe、Cr、Nb、Si、Mo、Mn和B。用掃描電子顯微鏡中的能量分散x射線光譜儀產(chǎn)生所述元素圖。下面的表1列出了合金1和合金2的組成。表1從以上可以看出,F(xiàn)e以54.0重量%至78.0重量%的水平存在。B以3.0重量%至5.0重量%的水平存在,Cr以14.0重量%至20.0重量%的水平存在,Mo是可選的,并且以至多11.0重量%的水平存在,或在0.1重量%至11.0重量%的范圍內(nèi),Mn是可選的,且以至多2.5重量%的水平存在或在0.1重量%至2.5重量%的范圍內(nèi),Nb是可選的,且以至多4.5重量%的水平或0.1重量%至4.5重量%的水平存在,Si是可選的,并且以至多2.0重量%的水平或0.1重量%至2.0重量%的水平存在,W是任選的,且以至多7.0重量%或0.1重量%至7.0重量%的水平存在,和C以0.5重量%至2.0重量%的水平存在。此外,從以上所述可以看出,本文的合金優(yōu)選含有在上述水平內(nèi)的Fe、B、Cr、Mo、Si、W和C。該合金還包括在上述水平內(nèi)的Fe、B、Cr、Nb、和C。此外,在本文中考慮了該合金含有在上述水平內(nèi)的Fe、B、Cr、Mo和C。優(yōu)選地,以顆粒形式提供用于本文中的逐層構(gòu)造的合金,這意味著存在的顆粒具在5.0微米至75.0微米,更優(yōu)選15.0微米至55.0微米,并且最優(yōu)選20.0微米至45.0微米的直徑。下表2鑒別和對比了用本文鑒定的合金通過鑄造和鍛造方法產(chǎn)生的常規(guī)Fe基合金與通過逐層構(gòu)造在合金1和合金2中實現(xiàn)的硬度值:表2合金硬度(HV)A36低碳鋼23915Cr-3Mo白口鐵472斯特萊特硬質(zhì)合金1-PTA1L51226Cr-Mo-4.5C64719Cr-5.2C705D2工具鋼71926Cr-Mo-B-4.5C1L745鐵類合金11540鐵類合金21250在本文所用的逐層構(gòu)造中,優(yōu)選使能量源(典型為激光或電子束),掃描材料表面,引起由能量源輻照的區(qū)域的局部材料層的至少部分熔化。如果希望的話,可以調(diào)節(jié)能量源以便也熔化下方材料的一定深度。例如,可以調(diào)節(jié)能量源以熔化在至多250微米的范圍內(nèi)的深度。熔化材料與下方材料冶金結(jié)合,并隨著能量源移開而凝固。還向凝固的材料添加額外的材料,然后用能量源輻照以引起熔化和凝固。隨著重復(fù)這個過程,構(gòu)造中的部件的厚度增加。如從上面可以看出,相對于合金1和合金2的例子,形成的凝固層或多個凝固層的硬度可以更具體地落在約1200HV至1600HV的范圍內(nèi)。相對高硬度的材料典型地具有相對低的延展性和相對低的韌性,從而使它們易于因熱誘導(dǎo)應(yīng)力而開裂和歷史地難以經(jīng)由液相逐層構(gòu)造而加工。因此,必須采用應(yīng)力減少的方法以減輕熱誘導(dǎo)的應(yīng)力,和使高硬度材料的無裂紋逐層構(gòu)造成為可能。每次能量源熔化材料層,熱通過下方的構(gòu)建部件傳導(dǎo),導(dǎo)致在下方材料加熱時膨脹和冷卻時收縮,這歸因于材料的固有熱膨脹性能。此外,在新層的輻照期間產(chǎn)生的熔化層與下方的層形成冶金結(jié)合,然后在冷卻時經(jīng)歷收縮。在新層和下方的層之間的結(jié)合約束合金在界面處的收縮,并由此在新層中誘發(fā)壓縮應(yīng)力。因此,該材料必須能夠承受由于在熱循環(huán)過程中誘發(fā)的應(yīng)力所導(dǎo)致的開裂,所述熱循環(huán)由在逐層構(gòu)造的循環(huán)能量源引起。通過降低熔化金屬的溫度(對于鐵類合金,其通常是在900℃至2000℃的范圍內(nèi))和下方材料的溫度(對于鐵類合金,其通常是在25-1400℃的范圍內(nèi))之間的差異減少這些應(yīng)力。熔化金屬的溫度和下方材料的溫度之間的差異可大至1950℃。差異越小,應(yīng)力越小,最低應(yīng)力的情況下是無差異,且無所產(chǎn)生的應(yīng)力。因此,下方材料的加熱對于降低熱應(yīng)力具有大的效果。優(yōu)選的是,將下方材料加熱至在40-1000℃的范圍內(nèi),更優(yōu)選在400-1000℃的范圍內(nèi),最優(yōu)選在800-1000℃的范圍內(nèi)的溫度。逐層構(gòu)造總是始于基材,從該基材構(gòu)建部件。一旦完成部件構(gòu)造,可以通過多種技術(shù)包括EDM和機械鋸從基材移除該部件。在構(gòu)造部件中施加到基材的第一材料層是重要的層,因為它用作界面,從該界面構(gòu)建部件。當(dāng)能量源輻照并至少部分地熔化第一層時,其與基材形成冶金結(jié)合,和在冷卻時,第一層收縮。如果基材和第一層包含具有不同熱膨脹性能的不同材料,那么在熱膨脹性能方面存在顯著失配。失配的熱膨脹將在界面處賦予應(yīng)力,因為每一材料將要以其自身的速率膨脹和收縮,但它們彼此受限。這導(dǎo)致應(yīng)力的發(fā)展,其可在高硬度材料中導(dǎo)致開裂?;牟牧吓c第一層材料的熱膨脹性能之間差異的減少在很大程度上減少了由失配的熱膨脹引起的應(yīng)力。通過組合利用對第一層具有上述熱膨脹性能匹配的基材,以及基材和構(gòu)建層的熱加,該熱應(yīng)力可以在很大程度上得到減少,使某些材料的逐層構(gòu)造成為可能,否則其易于因誘導(dǎo)的應(yīng)力而開裂。圖3示出了以200℃的基材溫度和2μm/mm·℃的在基材和第一層之間的熱膨脹系數(shù)的失配逐層構(gòu)造的1250HV硬度的高硬度鐵類材料的截面。該合金組合物是如上所述的合金2。如本文所理解的,優(yōu)選避免在2μm/m·℃以上的熱膨脹系數(shù)的失配。因此,在本文的分層構(gòu)造中所施加的合金與基材的熱膨脹系數(shù)的差異優(yōu)選小于2μm/m·℃。圖4顯示了在800℃加熱的基材上逐層構(gòu)造的相同的合金的截面,該基材由相同的合金構(gòu)造,使得基材和第一層具有10.4μm/m·℃的熱膨脹系數(shù),由此不存在失配。利用基材加熱和將基材與第一層之間的熱膨脹系數(shù)失配控制到不大于2μm/m·℃的水平,更優(yōu)選不大于1μm/m·℃,并且最優(yōu)選不大于0.5μm/m·℃,就可以生產(chǎn)出無裂紋的部件,其中在具有50X放大倍率的顯微鏡中沒有可辨別的裂縫。圖5示出了用這一技術(shù)從合金2生產(chǎn)的無裂紋的功能性軸承部件,其具有1060HV的硬度和99.9%的致密度,其中體積的0.1%由孔構(gòu)成,且余量是無開裂的固體金屬。但是應(yīng)當(dāng)理解的是,本文中的分層構(gòu)造因此是提供金屬性部件的分層構(gòu)造,在所述部件中沒有在具有50x放大倍數(shù)的顯微鏡中可辨別的裂紋、孔或其它類型的空隙。此外,該金屬部件是這樣的:存在固體疇,其中存在的一個或多個層限定了95%以上為固體的金屬性部件。這是指這樣的特征:部件體積的95%以上的特征在于存在金屬性區(qū)域,剩余部分是裂紋、孔或其他類型的開放空間(本文統(tǒng)稱標(biāo)識為空隙)。更優(yōu)選地,一個或多個層限定了金屬性部件是97%固體或更多,甚至更優(yōu)選99%至100%的固體。因此,一個或多個層現(xiàn)在提供了分層構(gòu)造作為獨立的部件,其95體積%以上是固體金屬性材料,具有相對小百分比的空隙(小于5%)。圖6示出了逐層構(gòu)建的高硬度鐵類金屬的無裂紋截面,其易于因誘導(dǎo)應(yīng)力而開裂。圖6中的合金組成是如上所述的合金1。各個層具有70微米的厚度且整體厚度為約10mm。通過采用500℃加熱的基材(從UNSS42000構(gòu)造的),以10.3μm/m·℃的熱膨脹系數(shù)構(gòu)造了無裂紋的材料,其在基材和第一層之間僅有0.3μm/m·℃的失配。盡管高硬度并不必然導(dǎo)致高的耐磨損性,但在大多數(shù)情況下導(dǎo)致,因此可以考慮通過逐層構(gòu)造在鐵類合金中產(chǎn)生的高硬度導(dǎo)致在突出的耐磨損性。在表2中顯示了對鐵類合金2進行的ASTMG65-10ProcedureA磨損試驗,測量了24.0mm3的體積損失。在這種情況下,優(yōu)選地,本文的逐層構(gòu)造優(yōu)選具有24.0mm3(+/-5.0mm3)的耐磨損性。雖然說明了本公開的優(yōu)選實施方案,但是應(yīng)當(dāng)理解的是,可以在其中進行各種變化、改變和修改而不脫離本公開的精神和所附權(quán)利要求書的范圍。因此不應(yīng)該參照上面的描述來確定本公開的范圍,而是應(yīng)該參照所附權(quán)利要求書及其等同物的全部范圍來確定。當(dāng)前第1頁1 2 3