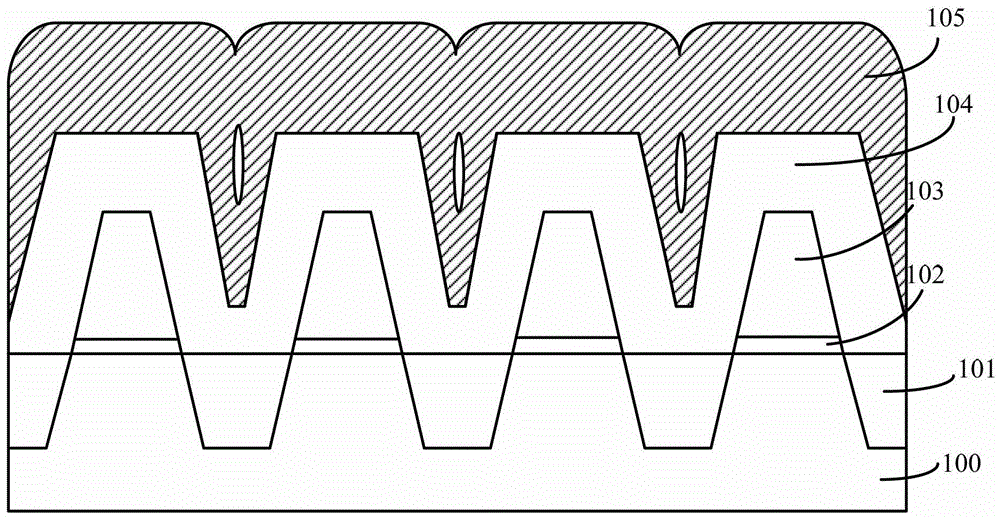
本發(fā)明涉及半導(dǎo)體制造技術(shù)領(lǐng)域,尤其涉及一種閃存的存儲(chǔ)單元的形成方法。
背景技術(shù):在現(xiàn)有的集成電路中,存儲(chǔ)器件已成為一種重要器件。在目前的存儲(chǔ)器件中,閃存(FlashMemory)的發(fā)展尤為迅速。閃存的主要特點(diǎn)是在不加電的情況下能長(zhǎng)期保持存儲(chǔ)的信息;且具有集成度高、存取速度快、易于擦除和重寫(xiě)等優(yōu)點(diǎn),因而在微機(jī)、自動(dòng)化控制等多項(xiàng)領(lǐng)域得到了廣泛的應(yīng)用?,F(xiàn)有技術(shù)中,閃存的存儲(chǔ)單元的形成過(guò)程如圖1至圖3所示,包括:請(qǐng)參考圖1,提供具有若干淺溝槽隔離結(jié)構(gòu)101的半導(dǎo)體襯底100,所述相鄰淺溝槽隔離結(jié)構(gòu)101之間的半導(dǎo)體襯底100表面具有氧化硅層102;在所述氧化硅層102表面形成浮柵層103。請(qǐng)參考圖2,在所述浮柵層103和淺溝槽隔離結(jié)構(gòu)101表面覆蓋介質(zhì)層104;在所述介質(zhì)層104表面覆蓋控制柵層105,所述控制柵層105的材料為多晶硅。請(qǐng)參考圖3,平坦化所述控制柵層105直至暴露出所述介質(zhì)層104表面;在所述介質(zhì)層104和控制柵層105表面形成電互連結(jié)構(gòu)106。然而,現(xiàn)有技術(shù)所形成的閃存的存儲(chǔ)單元性能較差,編程速度較低。更多閃存器件的結(jié)構(gòu)或形成方法的相關(guān)資料請(qǐng)參考公開(kāi)號(hào)為US2008/0108193的美國(guó)專(zhuān)利文件。
技術(shù)實(shí)現(xiàn)要素:本發(fā)明解決的問(wèn)題是提供一種閃存的存儲(chǔ)單元的形成方法,改善所形成的閃存的存儲(chǔ)單元的性能,提高編程速率。為解決上述問(wèn)題,本發(fā)明提供一種閃存的存儲(chǔ)單元的形成方法,包括:提供半導(dǎo)體襯底,所述半導(dǎo)體襯底內(nèi)具有若干淺溝槽隔離結(jié)構(gòu),所述相鄰淺溝槽隔離結(jié)構(gòu)之間的半導(dǎo)體襯底表面具第二介質(zhì)層、和第二介質(zhì)層表面的浮柵層,所述淺溝槽隔離結(jié)構(gòu)和浮柵層的側(cè)壁和頂部表面具有第一介質(zhì)層,所述相鄰浮柵層表面的第一介質(zhì)層之間具有溝槽;在所述第一介質(zhì)層表面形成填充滿所述溝槽的控制柵層;在形成所述控制柵層之后,進(jìn)行熱退火工藝;在所述熱退火工藝之后,去除高于所述第一介質(zhì)層表面的控制柵層??蛇x的,所述熱退火工藝的氣體包括二氧化氮和一氧化氮中的一種或兩種混合??蛇x的,所述熱退火工藝的氣體還包括氫氣??蛇x的,所述熱退火工藝的溫度為700攝氏度~950攝氏度,時(shí)間為5分鐘~60分鐘,流量為0.05標(biāo)準(zhǔn)升每分鐘~5標(biāo)準(zhǔn)升每分鐘,氣壓為0.08托~10托。可選的,所述控制柵層的材料為硅??蛇x的,所述控制柵層的形成工藝為化學(xué)氣相沉積工藝:溫度為480~550攝氏度,反應(yīng)氣體包括SiH4和Si2H6中的一種或兩種,流量為0.1標(biāo)準(zhǔn)升每分鐘~5標(biāo)準(zhǔn)升每分鐘,氣壓為0.08托~10托。可選的,所述控制柵層內(nèi)具有摻雜離子??蛇x的,所述摻雜離子通過(guò)原位摻雜工藝摻雜入所述控制柵層??蛇x的,所述摻雜離子為磷或砷,摻雜濃度為1E19原子每平方厘米~5E20原子每平方厘米??蛇x的,所述溝槽的縱寬比為大于3??蛇x的,所述第二介質(zhì)層的材料為氧化硅。可選的,所述第一介質(zhì)層為氧化硅-氮化硅-氧化硅的復(fù)合結(jié)構(gòu)、或氮化硅-氧化硅-氮化硅-氧化硅氮化硅的復(fù)合結(jié)構(gòu)。可選的,所述浮柵層的材料為多晶硅??蛇x的,所述去除高于所述第一介質(zhì)層的控制柵層的工藝為化學(xué)機(jī)械拋光工藝??蛇x的,在去除高于所述第一介質(zhì)層的控制柵層之后,在所述第一介質(zhì)層和控制柵層表面形成電互連結(jié)構(gòu)。與現(xiàn)有技術(shù)相比,本發(fā)明的技術(shù)方案具有以下優(yōu)點(diǎn):在浮柵層表面形成第一介質(zhì)層,且相鄰浮柵層表面的第一介質(zhì)層之間具有溝槽;在所述第一介質(zhì)層表面形成填充滿所述溝槽的控制柵層之后,進(jìn)行熱退火工藝;所述熱退火工藝能夠使所述控制柵層的晶格進(jìn)行重新排列,從而消除位于所述溝槽內(nèi)的控制柵層內(nèi)的空隙,且使所述述控制柵層的材料均勻;首先,所述熱退火工藝避免了當(dāng)所述相鄰浮柵層表面的第一介質(zhì)層之間的溝槽縱寬比過(guò)大時(shí),使所形成的控制柵層內(nèi)具有空隙的問(wèn)題,進(jìn)而提高了所形成的閃存的存儲(chǔ)單元的編程速率;其次,經(jīng)過(guò)熱退火后的控制柵層的材料更為均勻,從而使所形成的閃存的存儲(chǔ)單元性能更為穩(wěn)定。進(jìn)一步的,所述熱退火工藝的氣體為二氧化氮和一氧化氮中的一種或兩種混合,而且溫度為700攝氏度~950攝氏度,氣壓為0.08托~10托;所述熱退火工藝的氣體含氧量較低,避免了在熱退火工藝中使所述控制柵層發(fā)生氧化;同時(shí),所述二氧化氮或一氧化氮能夠促進(jìn)所述控制柵層進(jìn)行晶格的重排列,有利于消除空隙;其次,所述熱退火的溫度較低,且氣壓較低,能夠進(jìn)一步避免所述控制柵層在熱退火的工藝中發(fā)生氧化,使所形成的控制柵層的質(zhì)量?jī)?yōu)異。附圖說(shuō)明圖1至圖3是現(xiàn)有技術(shù)的閃存的存儲(chǔ)單元的形成過(guò)程的剖面結(jié)構(gòu)示意圖;圖4至圖8是本發(fā)明的實(shí)施例所述的閃存的存儲(chǔ)單元的形成過(guò)程中的剖面結(jié)構(gòu)示意圖。具體實(shí)施方式如背景技術(shù)所述,現(xiàn)有技術(shù)所形成的閃存的存儲(chǔ)單元性能較差,編程速度較低。本發(fā)明的發(fā)明人經(jīng)過(guò)研究發(fā)現(xiàn),為了滿足集成電路和半導(dǎo)體器件的集成化的需求,閃存的存儲(chǔ)單元的特征尺寸在持續(xù)減小。請(qǐng)繼續(xù)參考圖2,由于半導(dǎo)體器件的尺寸的減小,相鄰浮柵層103之間的距離也相應(yīng)減小;同時(shí),為了保證所閃存存儲(chǔ)單元的性能,所述浮柵層103的厚度不能過(guò)分減小,以保證所述浮柵層103具有足夠的電荷存儲(chǔ)能力。然而,當(dāng)相鄰浮柵層103之間的距離減小,而所述浮柵層103的厚度不變時(shí),會(huì)導(dǎo)致相鄰浮柵層103之間形成的溝槽的縱寬比過(guò)大;即使在所述浮柵層103和淺溝槽隔離結(jié)構(gòu)101表面形成介質(zhì)層104之后,相鄰浮柵層103表面的介質(zhì)層104之間的溝槽依舊具有較大的縱寬比;當(dāng)采用沉積工藝在所述介質(zhì)層104表面形成控制柵層105時(shí),所述具有過(guò)大縱寬比的溝槽容易使多晶硅材料難以填充,繼而使所述溝槽內(nèi)的控制柵層105中形成空隙。由于所述空隙處無(wú)法通過(guò)載流子,從而導(dǎo)致所形成的閃存的存儲(chǔ)單元的編程速率下降。經(jīng)過(guò)本發(fā)明的發(fā)明人進(jìn)一步研究,在浮柵層表面形成第一介質(zhì)層,并在所述第一介質(zhì)層表面形成控制柵層之后,進(jìn)行熱退火工藝,使所述控制柵層的晶格進(jìn)行重新排列,從而消除相鄰浮柵層表面的第一介質(zhì)層之間的溝槽內(nèi)所形成的控制柵層內(nèi)的空隙,并使所述述控制柵層的材料均勻;避免了由于所述相鄰浮柵層表面的第一介質(zhì)層之間的溝槽縱寬比過(guò)大而使所形成的控制柵層內(nèi)具有空隙的問(wèn)題,進(jìn)而提高了所形成的閃存的存儲(chǔ)單元的編程速率;而且經(jīng)過(guò)熱退火后的控制柵層的材料更為均勻,從而使所形成的閃存的存儲(chǔ)單元性能更為穩(wěn)定。為使本發(fā)明的上述目的、特征和優(yōu)點(diǎn)能夠更加明顯易懂,下面結(jié)合附圖對(duì)本發(fā)明的具體實(shí)施方式做詳細(xì)的說(shuō)明。如圖4至圖8所示,是本發(fā)明的實(shí)施例所述的閃存的存儲(chǔ)單元的形成過(guò)程中的剖面結(jié)構(gòu)示意圖。請(qǐng)參考圖4,提供半導(dǎo)體襯底200,所述半導(dǎo)體襯底200內(nèi)具有若干淺溝槽隔離結(jié)構(gòu)201,所述相鄰淺溝槽隔離結(jié)構(gòu)201之間的半導(dǎo)體襯底200表面具有第二介質(zhì)層202,所述第二介質(zhì)層202表面具有浮柵層203。所述半導(dǎo)體襯底200用于為后續(xù)工藝提供工作平臺(tái);所述半導(dǎo)體襯底300為硅襯底、硅鍺襯底、碳化硅襯底、絕緣體上硅(SOI)襯底、絕緣體上鍺(GOI)襯底、玻璃襯底或III-V族化合物襯底(例如氮化硅或砷化鎵等)。所述淺溝槽隔離結(jié)構(gòu)201的材料為氧化硅,形成工藝為本領(lǐng)域技術(shù)人員所熟知,在此不作贅述;所述相鄰淺溝槽隔離結(jié)構(gòu)201之間用于形成單個(gè)閃存的存儲(chǔ)單元。所述第二介質(zhì)層202的材料為氧化硅,形成工藝為熱氧化工藝,或采用沉積工藝和沉積工藝之后的刻蝕工藝形成;所述第二介質(zhì)層202用于作為閃存的存儲(chǔ)單元中的隧穿氧化層,載流子能夠通過(guò)隧穿所述第二介質(zhì)層202實(shí)現(xiàn)在半導(dǎo)體襯底200和浮柵層203之間的遷移,從而達(dá)到擦除、存儲(chǔ)或編程的目的。所述浮柵層203的材料為多晶硅,所述浮柵層203由沉積工藝和沉積工藝之后的刻蝕工藝形成;所述浮柵層203能夠在施加偏壓的狀態(tài)下俘獲或失去電荷,從而使閃存的存儲(chǔ)單元達(dá)到擦除、存儲(chǔ)或編程的目的。在一實(shí)施例中,所述淺溝槽隔離結(jié)構(gòu)201、第二介質(zhì)層202和浮柵層203的形成工藝為:在半導(dǎo)體襯底200表面沉積第二介質(zhì)薄膜;在所述第二介質(zhì)薄膜表面沉積浮柵薄膜;刻蝕部分所述浮柵薄膜和第二介質(zhì)薄膜,在所述半導(dǎo)體襯底200表面形成若干分立的第二介質(zhì)層202和浮柵層203;以所述第二介質(zhì)層202和浮柵層203為掩膜,采用各項(xiàng)異性的干法刻蝕工藝刻蝕所述半導(dǎo)體襯底,在相鄰的第二介質(zhì)層202和浮柵層203之間的半導(dǎo)體襯底200內(nèi)形成溝槽;在所述溝槽內(nèi)填充滿絕緣材料,形成淺溝槽隔離結(jié)構(gòu)201。在另一實(shí)施例中,所述淺溝槽隔離結(jié)構(gòu)201、第二介質(zhì)層202和浮柵層203的形成工藝為:在半導(dǎo)體襯底內(nèi)形成若干溝槽隔離結(jié)構(gòu)201;采用熱氧化工藝或沉積工藝在所述半導(dǎo)體襯底表面形成第二介質(zhì)薄膜;在所述第二介質(zhì)薄膜表面形成浮柵薄膜;刻蝕部分所述浮柵薄膜和第二介質(zhì)薄膜,直至暴露出所述淺溝槽隔離結(jié)構(gòu)為止,在所述半導(dǎo)體襯底200表面形成第二介質(zhì)層202和浮柵層203。請(qǐng)參考圖5,在所述淺溝槽隔離結(jié)構(gòu)201、半導(dǎo)體襯底200、浮柵層203和第二介質(zhì)層202表面覆蓋第一介質(zhì)層204,所述相鄰浮柵層203表面的第一介質(zhì)層204之間具有溝槽205。所述第一介質(zhì)層204為氧化硅-氮化硅-氧化硅的復(fù)合結(jié)構(gòu)、或氮化硅-氧化硅-氮化硅-氧化硅氮化硅的復(fù)合結(jié)構(gòu);所述第一介質(zhì)層的形成工藝為沉積工藝,較佳的是化學(xué)氣相沉積工藝;所述第一介質(zhì)層204用于隔離所述浮柵層203與后續(xù)形成的控制柵層。由于氮化硅的介電常數(shù)比氧化硅高,因此當(dāng)?shù)枧c氧化硅具有相同的電學(xué)厚度時(shí),氮化硅的物理厚度比氧化硅更厚;進(jìn)而,當(dāng)電學(xué)厚度相同的情況下,由于氮化硅的物理厚度更厚,因此氮化硅的電隔離效果更好;尤其是隨著集成電路或半導(dǎo)體器件的集成化,所需形成的閃存的存儲(chǔ)單元的尺寸持續(xù)縮小,純氧化硅材料已無(wú)法滿足浮柵層203和后續(xù)形成的控制柵層之間的電隔離需求;因此,需要形成氧化硅-氮化硅-氧化硅的復(fù)合結(jié)構(gòu)的第一介質(zhì)層204,以增強(qiáng)浮柵層203和控制柵層之間的電隔離。在本實(shí)施例中,所述第一介質(zhì)層204為氧化硅-氮化硅-氧化硅的復(fù)合結(jié)構(gòu)、或氮化硅-氧化硅-氮化硅-氧化硅氮化硅的復(fù)合結(jié)構(gòu);其中,所述氮化硅能夠在保證不增加第一介質(zhì)層204的電學(xué)厚度的情況下,增加所述第一介質(zhì)層204的物理厚度,以防止載流子在浮柵層203和控制柵之間發(fā)生擴(kuò)散而產(chǎn)生漏電;同時(shí),由于電學(xué)厚度不改變,能夠保證所形成的閃存的存儲(chǔ)單元中的電場(chǎng)強(qiáng)度或工作電壓等參數(shù)能夠滿足工藝需求;此外,位于所述氮化硅上表面或下表面的氧化硅能夠避免所述第一介質(zhì)層204的厚度過(guò)厚,使所述第一介質(zhì)層204的厚度在工藝許可的范圍內(nèi);因此,當(dāng)所述第一介質(zhì)層204為氧化硅-氮化硅-氧化硅的復(fù)合結(jié)構(gòu)、或氮化硅-氧化硅-氮化硅-氧化硅氮化硅的復(fù)合結(jié)構(gòu)時(shí),所形成的閃存的存儲(chǔ)單元的性能更穩(wěn)定。此外,在本實(shí)施例中,由于所述第二介質(zhì)層202和浮柵層204形成于相鄰淺溝槽隔離結(jié)構(gòu)之間的半導(dǎo)體襯底200表面,因此相鄰的浮柵層204、第二介質(zhì)層202與淺溝槽隔離結(jié)構(gòu)201構(gòu)成開(kāi)口;又由于所形成的第一介質(zhì)層204的厚度有限,不宜過(guò)厚,因此即使在所述淺溝槽隔離結(jié)構(gòu)201、浮柵層203和第二介質(zhì)層202表面覆蓋第一介質(zhì)層204后,相鄰浮柵層203之間的第一介質(zhì)層204之間表面仍舊形成溝槽205;所述溝槽205的寬度尺寸受到相鄰浮柵層203之間的距離限制,而所述溝槽205的深度受到所述浮柵層203的厚度限制;然而,隨著半導(dǎo)體器件的尺寸不斷縮小,相鄰浮柵層203之間的距離也不斷減小,但所述浮柵層203的厚度不能相應(yīng)減小,以保證所述浮柵層203具有足夠的電荷存儲(chǔ)能力,使所形成的閃存器件具有較好的性能;因此,導(dǎo)致所述溝槽205的縱寬比過(guò)大,在大于3的范圍內(nèi);所述溝槽205的縱寬比過(guò)大會(huì)導(dǎo)致后續(xù)于所述溝槽205內(nèi)填充控制柵層206時(shí),所述溝槽內(nèi)的控制柵層內(nèi)形成空隙,使所形成的控制柵層質(zhì)量不良,影響所形成的閃存器件的性能。請(qǐng)參考圖6,在所述第一介質(zhì)層204表面形成填充滿所述溝槽205(如圖5所示)的控制柵層206。所述控制柵層206的材料為硅;所述控制柵層206的形成工藝為化學(xué)氣相沉積工藝,工藝參數(shù)包括:溫度為480~550攝氏度,反應(yīng)氣體包括SiH4和Si2H6中的一種或兩種混合,流量為0.1標(biāo)準(zhǔn)升每分鐘~5標(biāo)準(zhǔn)升每分鐘,氣壓為0.08托~10托。由于隨著閃存器件的尺寸減小,導(dǎo)致所述溝槽205的縱寬比過(guò)大,當(dāng)采用所述化學(xué)氣相沉積工藝在所述第一介質(zhì)層204表面形成填充滿所述溝槽205的控制柵層206時(shí),容易造成位于所述溝槽205內(nèi)難以填充所述控制柵層206的材料,導(dǎo)致形成于所述溝槽205內(nèi)的控制柵層206產(chǎn)生空隙210,繼而導(dǎo)致所形成的閃存器件性能不良。在一實(shí)施例中,所述控制柵層206內(nèi)具有摻雜離子,所摻雜的離子通過(guò)原位摻雜工藝或離子注入工藝摻雜入所述控制柵層206內(nèi),所摻雜的離子濃度為1E19原子每平方厘米~5E20原子每平方厘米;較佳的,所述摻雜離子通過(guò)原位摻雜工藝進(jìn)行摻雜,能夠在形成控制柵層206的同時(shí)摻雜離子,簡(jiǎn)少工藝步驟;所摻雜離子較佳的為N型離子,包括磷或砷,所述N型離子能夠促進(jìn)電子在控制柵層206內(nèi)的遷移,從而提高所形成閃存器件的編程速率。請(qǐng)參考圖7,在形成所述控制柵層206之后,進(jìn)行熱退火工藝。由于采用化學(xué)氣相沉積工藝形成于溝槽205(如圖5所示)內(nèi)的控制柵層206內(nèi)容易產(chǎn)生空隙210(如圖6所示),因此需要通過(guò)所述熱退火工藝去除所述空隙210,以改善所述控制柵層206的質(zhì)量,提高所形成的閃存器件的編程速率。所述熱退火工藝的氣體包括二氧化氮和一氧化氮中的一種或兩種混合;所述熱退火工藝的溫度為700攝氏度~950攝氏度,時(shí)間為5分鐘~60分鐘,流量為0.05標(biāo)準(zhǔn)升每分鐘~5標(biāo)準(zhǔn)升每分鐘,氣壓為0.08托~10托。所述熱退火工藝通過(guò)使所述控制柵層206的晶格重排列,以去除所述控制柵層206中的空隙210;本發(fā)明的發(fā)明人經(jīng)過(guò)研究發(fā)現(xiàn),氧氣、二氧化氮或一氧化氮均能夠促進(jìn)所述控制柵206的硅材料的晶格重新排列,達(dá)到去除空隙210的目的;然而,氧氣在熱退火工藝過(guò)程中,容易造成硅材料的氧化而形成氧化硅,造成控制柵層206絕緣,無(wú)法用于閃存器件;而所述二氧化氮或一氧化氮的含氧量較低,在使所述控制柵層206的硅材料晶格重排列的同時(shí),不會(huì)造成所述控制柵層206的氧化,能夠達(dá)到去除空隙210的目的,又不會(huì)污染所述控制柵層206。其次,所述熱退火的溫度為700攝氏度~950攝氏度,氣壓為0.08托~10托,其溫度和氣壓均較低,能夠進(jìn)一步抑制在熱退火工藝過(guò)程中的氧化;在去除所述控制柵才206中的空隙的同時(shí),避免了所述控制柵層206受到污染,從而使所形成的閃存器件的性能優(yōu)良。在另一實(shí)施例中,所述熱退火工藝的氣體還包括氫氣,能夠進(jìn)一步促進(jìn)晶格的重排列,并用于分散熱退火氣體,使熱退火工藝的效果更充分。請(qǐng)參考圖8,在所述熱退火工藝之后,去除高于所述第一介質(zhì)層204表面的控制柵層206,直至暴露出所述第一介質(zhì)層204為止。所述去除高于第一介質(zhì)層204的控制柵層206的工藝為化學(xué)機(jī)械拋光工藝,拋光直至暴露出所述第一介質(zhì)層204為止;在去除高于所述第一介質(zhì)層204的控制柵層206之后,在所述第一介質(zhì)層204和控制柵層206表面形成電互連結(jié)構(gòu)(未示出);在本實(shí)施例中,所述電互連結(jié)構(gòu)的材料為多晶硅。需要說(shuō)明的是,在形成所述電互連結(jié)構(gòu)之前,在所述浮柵層203和第二介質(zhì)層202未覆蓋所述第一介質(zhì)層204和控制柵層206的兩側(cè)形成側(cè)墻(未示出);以所述第一介質(zhì)層204和側(cè)墻為掩膜,在所述浮柵層206兩側(cè)的半導(dǎo)體襯底200內(nèi)形成源區(qū)和漏區(qū)(未示出),并于所述源區(qū)和漏區(qū)表面形成金屬硅化物層(未示出);之后,形成連接所述源區(qū)和漏區(qū)表面的金屬硅化物層、浮柵層203和半導(dǎo)體襯底200的導(dǎo)電插塞(未示出)。所述形成于所述第一介質(zhì)層204和控制柵層206表面的電互連結(jié)構(gòu)不僅能夠電連接所述控制柵層,還能夠與所述導(dǎo)電插塞電連接,以實(shí)現(xiàn)對(duì)所形成的閃存器件施加偏壓。本實(shí)施例的閃存的存儲(chǔ)單元的形成方法中,第一介質(zhì)層204表面形成填充滿所述溝槽205的控制柵層206之后,采用熱退火工藝去除所述控制柵層206內(nèi)的空隙210,從而改善所形成的控制柵層的質(zhì)量,以提高所形成的閃存的存儲(chǔ)單元的編程速率;而且,所述熱退火工藝的氣體包括二氧化氮或一氧化氮,其含氧量低,避免了所述控制柵層206在熱退火的過(guò)程中受到氧化而被污染;此外,所述熱退火工藝的溫度和氣壓較低,進(jìn)一步抑制了所述控制柵層206在熱退火工藝過(guò)程中的氧化,能夠進(jìn)一步提高了所形成的控制柵層的質(zhì)量。綜上所述,在浮柵層表面形成第一介質(zhì)層,且相鄰浮柵層表面的第一介質(zhì)層之間具有溝槽;在所述第一介質(zhì)層表面形成填充滿所述溝槽的控制柵層之后,進(jìn)行熱退火工藝;所述熱退火工藝能夠使所述控制柵層的晶格進(jìn)行重新排列,從而消除位于所述溝槽內(nèi)的控制柵層內(nèi)的空隙,且使所述述控制柵層的材料均勻;首先,所述熱退火工藝避免了當(dāng)所述相鄰浮柵層表面的第一介質(zhì)層之間的溝槽縱寬比過(guò)大時(shí),使所形成的控制柵層內(nèi)具有空隙的問(wèn)題,進(jìn)而提高了所形成的閃存的存儲(chǔ)單元的編程速率;其次,經(jīng)過(guò)熱退火后的控制柵層的材料更為均勻,從而使所形成的閃存的存儲(chǔ)單元性能更為穩(wěn)定。進(jìn)一步的,所述熱退火工藝的氣體為二氧化氮和一氧化氮中的一種或兩種混合,而且溫度為700攝氏度~950攝氏度,氣壓為0.08托~10托;所述熱退火工藝的氣體含氧量較低,避免了在熱退火工藝中使所述控制柵層發(fā)生氧化;同時(shí),所述二氧化氮或一氧化氮能夠促進(jìn)所述控制柵層進(jìn)行晶格的重排列,有利于消除空隙;其次,所述熱退火的溫度較低,且氣壓較低,能夠進(jìn)一步避免所述控制柵層在熱退火的工藝中發(fā)生氧化,使所形成的控制柵層的質(zhì)量?jī)?yōu)異。本發(fā)明雖然已以較佳實(shí)施例公開(kāi)如上,但其并不是用來(lái)限定本發(fā)明,任何本領(lǐng)域技術(shù)人員在不脫離本發(fā)明的精神和范圍內(nèi),都可以利用上述揭示的方法和技術(shù)內(nèi)容對(duì)本發(fā)明技術(shù)方案做出可能的變動(dòng)和修改,因此,凡是未脫離本發(fā)明技術(shù)方案的內(nèi)容,依據(jù)本發(fā)明的技術(shù)實(shí)質(zhì)對(duì)以上實(shí)施例所作的任何簡(jiǎn)單修改、等同變化及修飾,均屬于本發(fā)明技術(shù)方案的保護(hù)范圍。