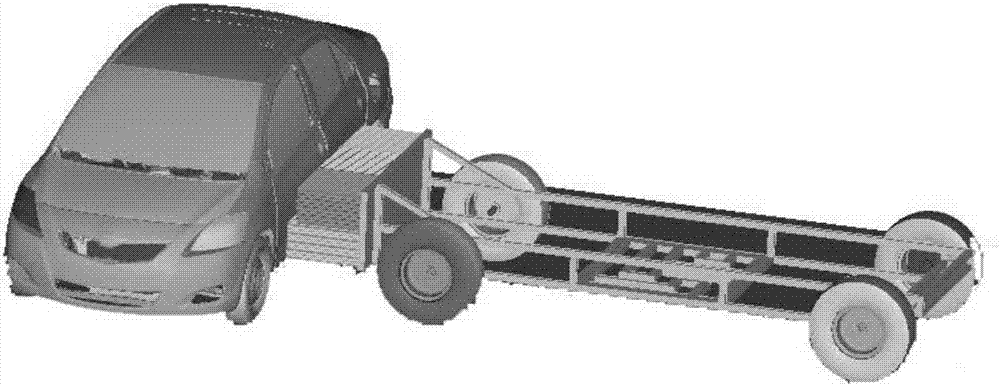
本發(fā)明屬于汽車輕量化及結構設計
技術領域:
,具體涉及一種梯度力學性能零件過渡區(qū)優(yōu)化設計方法。
背景技術:
:為了滿足汽車輕量化重大需求,超高強度鋼熱沖壓零件在汽車工業(yè)得到廣泛的應用。然而人們逐漸意識到汽車車身安全結構件在強度提升的同時,還應滿足碰撞吸能要求。具有梯度力學性能的汽車車身安全結構件實現(xiàn)了車身強度與碰撞安全性能的良好匹配。梯度力學性能零件是指同一零件的不同區(qū)域有著不同力學性能需求的一種新型功能零件。以汽車b柱為例,上部區(qū)域需要有足夠的強度與整車車身框架相連接,以保證車體的完整;下部區(qū)域則與底盤相連接需要有較好的延展性而吸收能量,以防止碰撞入侵。目前,部分學者研究了熱沖壓零件力學性能梯度分布規(guī)律,但是針對相鄰不同力學性能區(qū)域之間的過渡區(qū)(大小及強度分布)如何設計鮮有報道。為了使不同力學性能區(qū)域之間的變化為平滑過渡,針對零件力學性能過渡區(qū)分布規(guī)律的研究顯得非常重要。技術實現(xiàn)要素:本發(fā)明的目的在于提供一種梯度力學性能零件過渡區(qū)優(yōu)化設計方法,它可以使零件的不同力學性能區(qū)域之間的變化為平滑過渡,進而得到性能最優(yōu)的梯度力學性能零件。本發(fā)明解決其技術問題所采用的技術方案是:一種梯度力學性能零件過渡區(qū)優(yōu)化設計方法,包括對零件力學性能過渡區(qū)的分布規(guī)律進行優(yōu)化設計:以零件過渡區(qū)的大小作為設計變量、該零件的性能需求作為優(yōu)化目標、該零件的最優(yōu)性能需求作為約束條件,建立優(yōu)化數(shù)學模型;確定試驗組數(shù),針對每組試驗,在其中一個過渡區(qū)的取值范圍內確定各個取值,基于等強度變化率的原則,即任意相鄰力學性能區(qū)域的抗拉強度之差與位于該相鄰力學性能區(qū)域之間的過渡區(qū)的大小之間的比值為一定值,從而確定其它過渡區(qū)對應的取值,對每組試驗進行分析計算,得到一組最優(yōu)性能需求,即得到零件最優(yōu)的力學性能過渡區(qū)的大小。按上述技術方案,所述力學性能區(qū)域的抗拉強度為對零件的力學性能分布位置進行優(yōu)化得到的優(yōu)化的力學性能區(qū)域的抗拉強度:對零件所有力學性能區(qū)域的抗拉強度進行優(yōu)化設計,以零件的設計抗拉強度作為設計變量、該零件的性能需求作為優(yōu)化目標、該零件的設計性能需求作為約束條件,建立優(yōu)化數(shù)學模型,設計并實施正交試驗,得到第一組最優(yōu)性能需求,即得到一組優(yōu)化的力學性能區(qū)域的抗拉強度。按上述技術方案,所述零件的最優(yōu)性能需求為對該零件的力學性能區(qū)域大小進行優(yōu)化得到的第二組最優(yōu)性能需求:對零件所有力學性能區(qū)域的大小進行優(yōu)化設計,以零件的設計力學性能區(qū)域大小作為設計變量、該零件的性能需求作為優(yōu)化目標、第一組最優(yōu)性能需求作為約束條件,建立優(yōu)化數(shù)學模型,設計并實施正交試驗,得到第二組最優(yōu)性能需求,即得到一組優(yōu)化的力學性能區(qū)域的大小。按上述技術方案,采用遺傳算法對每組試驗進行分析計算。按上述技術方案,所述梯度力學性能零件為b柱加強板,所述性能需求包括對應駕駛員胸部處的最大侵入量、對應駕駛員胸部處的最大侵入速度、對應駕駛員腹部處的最大侵入量以及對應駕駛員腹部處的最大侵入速度,所述設計性能需求包括優(yōu)化前對應駕駛員胸部處的最大侵入量、優(yōu)化前對應駕駛員胸部處的最大侵入速度以及優(yōu)化前對應駕駛員腹部處的最大侵入速度。本發(fā)明,具有以下有益效果:本發(fā)明以零件過渡區(qū)的分布規(guī)律為優(yōu)化對象,采用等強度變化率的設計方案確定各組試驗中過渡區(qū)大小的取值,可以使得不同力學性能之間的變化為平滑過渡,進而得到性能最優(yōu)的梯度力學性能零件。這種方法原理簡單、易于實現(xiàn),能夠有效地對零件力學性能過渡區(qū)分布規(guī)律進行優(yōu)化設計,促進了梯度力學性能零件在汽車上的應用。附圖說明下面將結合附圖及實施例對本發(fā)明作進一步說明,附圖中:圖1為本發(fā)明實施例的流程圖。圖2為本發(fā)明實施例中整車側面碰撞有限元模型圖。圖3a為本發(fā)明實施例中b柱加強板梯度力學性能分布位置優(yōu)化設計變量圖。圖3b為本發(fā)明實施例中b柱加強板梯度力學性能區(qū)域大小優(yōu)化設計變量圖。圖4a為本發(fā)明實施例中b柱加強板梯度力學性能過渡區(qū)的優(yōu)化設計變量圖。圖4b為本發(fā)明實施例中b柱加強板梯度力學性能過渡區(qū)的力學性能變化規(guī)律圖。具體實施方式為了使本發(fā)明的目的、技術方案及優(yōu)點更加清楚明白,以下結合附圖及實施例,對本發(fā)明進行進一步詳細說明。應當理解,此處所描述的具體實施例僅用以解釋本發(fā)明,并不用于限定本發(fā)明。在本發(fā)明的較佳實施例中,一種梯度力學性能零件過渡區(qū)優(yōu)化設計方法,包括對零件力學性能過渡區(qū)的分布規(guī)律進行優(yōu)化設計:以零件過渡區(qū)的大小作為設計變量、該零件的性能需求作為優(yōu)化目標、該零件的最優(yōu)性能需求作為約束條件,建立優(yōu)化數(shù)學模型;確定試驗組數(shù),針對每組試驗,在其中一個過渡區(qū)的取值范圍內確定各個取值,基于等強度變化率的原則,即任意相鄰力學性能區(qū)域的抗拉強度之差與位于該相鄰力學性能區(qū)域之間的過渡區(qū)的大小之間的比值為一定值,從而確定其它過渡區(qū)對應的取值,對每組試驗進行分析計算,得到一組最優(yōu)性能需求,即得到零件最優(yōu)的力學性能過渡區(qū)的大小。在本發(fā)明的優(yōu)選實施例中,為了進一步加強優(yōu)化效果,力學性能區(qū)域的抗拉強度為對零件的力學性能分布位置進行優(yōu)化得到的優(yōu)化的力學性能區(qū)域的抗拉強度:對零件所有力學性能區(qū)域的抗拉強度進行優(yōu)化設計,以零件的設計抗拉強度作為設計變量、該零件的性能需求作為優(yōu)化目標、該零件的設計性能需求作為約束條件,建立優(yōu)化數(shù)學模型,設計并實施正交試驗,得到第一組最優(yōu)性能需求,即得到一組優(yōu)化的力學性能區(qū)域的抗拉強度。在本發(fā)明的優(yōu)選實施例中,為了進一步加強優(yōu)化效果,零件的最優(yōu)性能需求為對該零件的力學性能區(qū)域大小進行優(yōu)化得到的第二組最優(yōu)性能需求:對零件所有力學性能區(qū)域的大小進行優(yōu)化設計,以零件的設計力學性能區(qū)域大小作為設計變量、該零件的性能需求作為優(yōu)化目標、第一組最優(yōu)性能需求作為約束條件,建立優(yōu)化數(shù)學模型,設計并實施正交試驗,得到第二組最優(yōu)性能需求,即得到一組優(yōu)化的力學性能區(qū)域的大小。在本發(fā)明的優(yōu)選實施例中,為了進一步加強優(yōu)化效果,采用遺傳算法對每組試驗進行分析計算。在本發(fā)明的優(yōu)選實施例中,當梯度力學性能零件為b柱加強板時,性能需求包括對應駕駛員胸部處的最大侵入量、對應駕駛員胸部處的最大侵入速度、對應駕駛員腹部處的最大侵入量以及對應駕駛員腹部處的最大侵入速度,設計性能需求包括優(yōu)化前對應駕駛員胸部處的最大侵入量、優(yōu)化前對應駕駛員胸部處的最大侵入速度以及優(yōu)化前對應駕駛員腹部處的最大侵入速度。本發(fā)明在具體應用時,包括以下步驟:s1、建立梯度力學性能零件的有限元模型,該零件具有n個力學性能區(qū)域以及n-1個過渡區(qū),每個力學性能區(qū)域的抗拉強度用σi表示,每個力學性能區(qū)域的大小用hi表示,每個過渡區(qū)的大小用hj表示,i=1、2、3、…、n,j=1、2、3、…、n-1;s2、采用分級優(yōu)化方法對零件力學性能的梯度分布進行優(yōu)化設計,首先針對零件的力學性能分布位置進行優(yōu)化設計,在此基礎上,對零件的力學性能區(qū)域大小進行優(yōu)化設計,兩步均采用正交試驗設計方法對零件力學性能梯度分布進行優(yōu)化設計:s201、先對零件的力學性能分布位置進行優(yōu)化設計,即對零件所有力學性能區(qū)域的抗拉強度σi進行優(yōu)化設計,以σi作為設計變量、該零件的性能需求y作為優(yōu)化目標、該零件的設計性能需求x作為約束條件,建立優(yōu)化數(shù)學模型,設計并實施正交試驗,得到第一組最優(yōu)性能需求yb1,即得到一組優(yōu)化的力學性能區(qū)域的抗拉強度;s202、再對該零件的力學性能區(qū)域大小進行優(yōu)化設計,即對零件n-1個力學性能區(qū)域的大小hi進行優(yōu)化設計,以hi作為設計變量、該零件的性能需求y作為優(yōu)化目標、步驟s201中得到的yb1作為約束條件,建立優(yōu)化數(shù)學模型,設計并實施正交試驗,得到第二組最優(yōu)性能需求yb2,即得到一組優(yōu)化的力學性能區(qū)域的大??;s3、基于等強度變化率優(yōu)化方案,采用遺傳算法對零件力學性能過渡區(qū)的分布規(guī)律進行優(yōu)化設計:以零件n-1個過渡區(qū)的大小hj作為設計變量、該零件的性能需求y作為優(yōu)化目標、步驟s202中得到的yb2作為約束條件,建立優(yōu)化數(shù)學模型,在其中一個過渡區(qū)的取值范圍內確定各個取值,并以步驟s201中得到的優(yōu)化的力學性能區(qū)域的抗拉強度結合等強度變化率優(yōu)化設計,確定其它過渡區(qū)對應的取值,即(σi+1-σi)/hj=(σi+2-σi+1)/hj+1,采用遺傳算法得到一組最優(yōu)性能需求yb3,即得到零件最優(yōu)的力學性能過渡區(qū)的大小,驗證優(yōu)化結果的合理性。本發(fā)明采用分級優(yōu)化,先后對強度分布和強度區(qū)域大小進行優(yōu)化設計,以使設計變量單一,簡化變強度設計的優(yōu)化過程,再將零件各個力學性能過渡區(qū)的分布規(guī)律設為等強度變化率,結合遺傳算法對零件力學性能過渡區(qū)的分布規(guī)律進行優(yōu)化設計,使得不同力學性能之間的變化為平滑過渡,進而得到性能最優(yōu)的梯度力學性能零件。這種方法原理簡單、易于實現(xiàn),能夠有效地對零件力學性能過渡區(qū)分布規(guī)律進行優(yōu)化設計,促進了梯度力學性能零件在汽車上的應用。上述步驟s3具體包括以下步驟:s301、確定優(yōu)化設計目標、約束,并根據(jù)等強度變化率優(yōu)化方案,確定設計變量及各設計變量的取值空間,優(yōu)化設計數(shù)學模型為式中,y表示設計目標函數(shù),s.t表示約束條件,xi為x的第i個約束函數(shù),ximin為約束函數(shù)xi的下限,ximax為約束函數(shù)xi的上限;s302、對每組設計方案進行仿真計算,得到相應的仿真值;s303、采用遺傳算法得到最優(yōu)的設計結果,即最優(yōu)的力學性能過渡區(qū)分布規(guī)律;s304、驗證優(yōu)化后結果的合理性。本發(fā)明中均采用ls-dyna有限元軟件對設計方案進行仿真計算。下面以汽車b柱加強板的力學性能過渡區(qū)優(yōu)化設計為例,對本發(fā)明作進一步詳細說明。如圖1所示,本發(fā)明包括以下步驟:s1、采用hypermesh有限元軟件建立如圖2所示的整車側面碰撞有限元模型,移動變形壁障的速度為50km/h,碰撞時間為120ms;s2、采用分級優(yōu)化方法對零件力學性能的梯度分布進行優(yōu)化設計:s201、首先針對零件的力學性能分布位置進行優(yōu)化設計,圖3a為b柱加強板梯度力學性能區(qū)域位置優(yōu)化設計變量,根據(jù)需求確定設計變量的備選數(shù)值及水平,得到如表1所示的因素-水平表,以6個區(qū)域的抗拉強度為設計變量,對應駕駛員胸部及腹部處的最大侵入量和最大侵入速度為優(yōu)化目標,根據(jù)優(yōu)化前b柱加強板對應駕駛員胸部處的最大侵入量和最大侵入速度以及腹部處的最大侵入速度為約束條件,可定義優(yōu)化數(shù)學模型如下式中,damax、dbmax分別表示b柱加強板對應駕駛員胸部和腹部處的最大侵入量,vamax、vbmax分別表示b柱加強板對應駕駛員胸部和腹部處的最大侵入速度;采用自適應響應面優(yōu)化方法,得到了合理的梯度力學性能區(qū)域位置分布,如表2所示,優(yōu)化設計目標及約束條件對比結果如表3所示;表1表2區(qū)域iiiiiiivvvi強度(mpa)800600100010001000600表3damax/mmvamax/(m·s-1)dbmax/mmvbmax/(m·s-1)優(yōu)化前157.1295.298199.5666.301力學性能分布位置優(yōu)化后143.5194.871185.9505.865s202、在此基礎上,對零件的力學性能區(qū)域大小進行優(yōu)化設計,圖3b為b柱加強板梯度力學性能區(qū)域大小優(yōu)化設計變量,根據(jù)需求確定設計變量的備選數(shù)值及水平,得到如表4所示的因素-水平表,以5個區(qū)域大小為設計變量,對應駕駛員胸部及腹部的最大侵入量和最大侵入速度為優(yōu)化目標,根據(jù)力學性能分布位置優(yōu)化后b柱加強板對應駕駛員胸部處的最大侵入量和最大侵入速度以及腹部處的最大侵入速度為約束條件,可定義優(yōu)化數(shù)學模型如下式中,damax、dbmax分別表示b柱加強板對應駕駛員胸部和腹部處的最大侵入量;vamax、vbmax分別表示b柱加強板對應駕駛員胸部和腹部處的最大侵入速度;采用與上述相同的優(yōu)化方法,得到了合理的梯度力學性能區(qū)域大小分布,如表5所示,優(yōu)化設計目標及約束條件對比結果如表6所示;表4表5區(qū)域h1h2h3h4h5高度(mm)160240240220200表6damax/mmvamax/(m·s-1)dbmax/mmvbmax/(m·s-1)力學性能分布位置優(yōu)化后143.5194.871185.9505.865力學性能區(qū)域大小優(yōu)化后141.4144.432183.3425.428s3、基于等強度變化率優(yōu)化方案,結合遺傳算法對零件力學性能過渡區(qū)的分布規(guī)律進行優(yōu)化設計:s301、如圖4a、圖4b所示,本發(fā)明采用的是等強度變化率優(yōu)化方案,所以可以簡化為單變量優(yōu)化問題,選取過渡區(qū)①為設計變量,備選區(qū)域大小為20mm、30mm、40mm、50mm,結合表2的區(qū)域強度大小可以確定過渡區(qū)②和過渡區(qū)③的備選區(qū)域大小,力學性能過渡區(qū)優(yōu)化設計的試驗方案如表7所示;表7試驗號過渡區(qū)①/mm過渡區(qū)②/mm過渡區(qū)③/mm120404023060603408080450100100s302、采用ls-dyna有限元軟件對每組設計方案進行仿真計算,得到相應的b柱加強板碰撞性能,然后以過渡區(qū)①的大小為設計變量,對應駕駛員胸部及腹部的最大侵入量和最大侵入速度為優(yōu)化目標,根據(jù)上述優(yōu)化后的梯度力學性能b柱加強板對應駕駛員胸部處的最大侵入量和最大侵入速度以及腹部處的最大侵入速度為約束條件,可定義優(yōu)化數(shù)學模型如下式中,damax、dbmax分別表示b柱加強板對應駕駛員胸部和腹部處的最大侵入量,vamax、vbmax分別表示b柱加強板對應駕駛員胸部和腹部處的最大侵入速度;s303、采用遺傳算法,得到了此方案下的最優(yōu)過渡區(qū)分布,其中三個過渡區(qū)域的強度變化率相同,如表8所示,表8s304、為了驗證優(yōu)化后結果的合理性,將優(yōu)化設計目標及約束條件進行對比,如表9所示,可以看出,采用本發(fā)明所述的力學性能過渡區(qū)優(yōu)化方法,使得汽車b柱加強板的碰撞性能得到顯著提升。表9damax/mmvamax/(m·s-1)dbmax/mmvbmax/(m·s-1)力學性能梯度分布優(yōu)化后141.4144.432183.3425.428力學性能過渡區(qū)優(yōu)化后138.0994.319181.9795.254應當理解的是,對本領域普通技術人員來說,可以根據(jù)上述說明加以改進或變換,而所有這些改進和變換都應屬于本發(fā)明所附權利要求的保護范圍。當前第1頁12