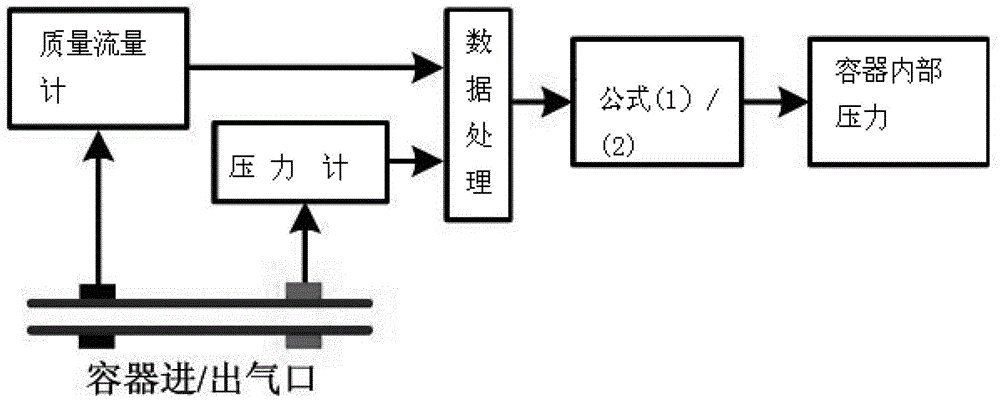
本發(fā)明涉及一種氣體壓力的測定方法,具體涉及一種固定容器在快速充放氣過程中利用氣體質(zhì)量流量傳感器和壓力傳感器間接、實時測量容器內(nèi)部壓力的方法。
背景技術(shù):定容快速充放氣過程(充、放氣時間總長為數(shù)十到數(shù)百毫秒)在許多領(lǐng)域中得到了廣泛應(yīng)用,例如航空航天儀表的精密潤滑,表面貼裝中的定量點膠,化生、醫(yī)藥及醫(yī)護(hù)行業(yè)試劑配制以及定量配藥給藥等。其特點是:(1)通過窄脈沖高壓氣體驅(qū)動密封在注射器中的液體材料從針頭擠出而進(jìn)行布施,而后通過氣動回路中的方向控制閥使容器入口快速與大氣連通,容器快速放氣,準(zhǔn)備進(jìn)入下一個脈沖作用周期,即充、放氣過程均通過容器入口實現(xiàn),而通過方向控制閥的切換來控制充、放氣動作;(2)每個周期擠出的液體量相對于注射器容積而言非常微小,因而在單一擠出周期中注射器內(nèi)氣體體積可視為不變,即為定容充放氣。在精密布施場合,需要精確控制擠出的液體量,為實現(xiàn)這一目標(biāo),必須準(zhǔn)確地測量容器內(nèi)氣體壓力。目前,對于精確測量定容快速充放氣過程中容器內(nèi)部壓力的方法尚未見報到,大多都是采用測量容器入口處壓力并以之代替容器內(nèi)部作用壓力。然而,在快速充放氣過程中,由于氣體作用時間很短,容器內(nèi)部壓力并沒達(dá)到穩(wěn)態(tài),因而容器內(nèi)部壓力與入口壓力之間有明顯區(qū)別,上述簡化引入了較大的誤差,難以實現(xiàn)材料的定量擠出。大量實驗表明,定容快速充氣過程,容器內(nèi)部壓力與入口壓力相近,但在放氣過程,內(nèi)部壓力遠(yuǎn)大于入口壓力。另一方面,由于受注射器結(jié)構(gòu)及密封性要求的限制,現(xiàn)有傳感器不能直接到達(dá)注射器內(nèi)部直接進(jìn)行壓力測量,因而需要開發(fā)有效的容器內(nèi)部瞬態(tài)壓力間接測量方法。
技術(shù)實現(xiàn)要素:為解決定容快速充放氣過程中容器內(nèi)部壓力測量不準(zhǔn)確問題,本發(fā)明提出了一種利用氣體質(zhì)量流量傳感器和壓力傳感器精確測量容器內(nèi)部壓力的方法。本發(fā)明的目的是這樣實現(xiàn)的:一種定容快速充放氣氣腔壓力的測量方法,包括以下步驟:步驟1)傳感器安裝:在緊鄰容器入口處的管道上安裝氣體壓力傳感器和質(zhì)量流量傳感器;步驟2)數(shù)據(jù)采集及計算:通過氣體壓力傳感器和質(zhì)量流量傳感器得到容器入口氣體壓力和質(zhì)量流量,后按下式(1)和(2)通過計算分別得到充氣及放氣時定容容器氣腔的壓力:a、快速充氣過程容器內(nèi)部壓力計算方法:在容器快速充氣過程中,容器氣腔壓力計算公式為其中,Pr為所求固定容器內(nèi)部壓力;Z為氣體的壓縮因子,為常值1.4;R為理想氣體常數(shù),R=8.31J/(mol·K);T為氣體溫度(K);V為容器體積(m3),Qin為容器內(nèi)氣體質(zhì)量流量(m3/s),若忽略氣體泄漏,則可認(rèn)為容器內(nèi)氣體質(zhì)量流量等于容器入口氣體質(zhì)量流量,而后者可通過在容器入口安裝氣體質(zhì)量流量傳感器來測量,亦即獲得了Qin;b、快速放氣過程容器內(nèi)部壓力計算方法:在容器放氣過程中,容器氣腔壓力計算公式為其中,P0,T0,r0分別為標(biāo)準(zhǔn)狀態(tài)下氣體的壓力、溫度和密度,其值分別為101.3kPa,273K,1.293kg/m3;T為容器內(nèi)部氣體溫度(K),其值與容器充氣過程中的數(shù)值相同;c為流出系數(shù),其值等于實際流量除以理論流量,此處取值為1;e為氣體的可壓縮系數(shù),e=1.4;b為容器入口管道直徑與固定容器直徑之比;Pa為容器入口處的壓力(kPa);d2為容器入口管道直徑(m);Qout為流出容器的氣體質(zhì)量流量(m3/s),即等于容器入口氣體質(zhì)量流量,可通過在容器入口安裝氣體質(zhì)量流量傳感器測得。本發(fā)明提供的定容快速充放氣氣腔壓力的測量方法,在定容快速充放氣過程中,容器內(nèi)部壓力值的獲得可以通過在緊鄰容器入口處的管道上安裝氣體質(zhì)量流量傳感器和壓力傳感器得到質(zhì)量和壓力數(shù)據(jù),將得到的數(shù)據(jù)經(jīng)過計算即可得到容器內(nèi)部壓力響應(yīng),該測量方法相對于直接在容器入口檢測容器內(nèi)部壓力,檢測結(jié)果精度顯著提高,可用于在線檢測,實際使用表明,所測容器內(nèi)部壓力與理論壓力相比,平均誤差為9.6%;而若以容器入口壓力直接替代容器內(nèi)部壓力,其平均誤差為24.1%,因而本發(fā)明所述方法明顯提高了定容快速充放氣過程容器內(nèi)部壓力測量精度。附圖說明下面結(jié)合附圖對本發(fā)明作進(jìn)一步說明。圖1為定容快速充放氣過程示意圖。圖2為容器內(nèi)部壓力測量方案流程圖。圖3(a)為t=14ms時容器內(nèi)壓力云圖(充氣)。圖3(b)為t=20ms時容器內(nèi)壓力云圖(放氣)。圖3(c)為t=70ms時容器內(nèi)壓力云圖(充氣)。圖3(d)為t=105ms時容器內(nèi)壓力云圖(放氣)。圖4為充放氣周期40ms情況下容器入口壓力與容器內(nèi)部理論壓力比較。圖5為充放氣周期125ms情況下容器入口壓力與容器內(nèi)部理論壓力比較。圖6為容器入口壓力、內(nèi)部理論壓力、內(nèi)部計算壓力三者關(guān)系比較。具體實施方式附圖1所示為固定容器在快速充放氣過程中的示意圖,緊鄰容器入口處的管道上安裝有氣體質(zhì)量流量傳感器和壓力傳感器,用來實時測量容器在充放氣過程中的氣體質(zhì)量流量和容器入口處的瞬態(tài)壓力。因為容器在充氣過程和放氣過程中容器內(nèi)部壓力變化規(guī)律不同,以下分別從容器快速充氣過程和放氣過程來說明容器內(nèi)部壓力測量方法??焖俪錃膺^程容器內(nèi)部壓力測量方法:在容器快速充氣過程中,根據(jù)理想氣體狀態(tài)方程和氣體連續(xù)性方程可以推導(dǎo)得到固定容器在充氣過程中容器內(nèi)部壓力計算公式為其中,Pr為容器內(nèi)部壓力,Z為氣體的壓縮因子,為常值1.4,R為理想氣體常數(shù),有R=8.31J/(mol·K),T為氣體溫度,對于快速充放氣來說,容器內(nèi)氣體來不及和外界進(jìn)行熱交換,故不考慮容器內(nèi)氣體溫度變化,一般取工作環(huán)境溫度即可,V為容器體積,Qin為流入容器內(nèi)的氣體質(zhì)量流量。由(1)式可知,在固定容器快速充氣過程中,只要在容器入口檢測到流入容器內(nèi)部的氣體質(zhì)量流量,即可根據(jù)公式求解得到容器內(nèi)部壓力響應(yīng)。因此,為了獲得充氣過程中容器內(nèi)部壓力響應(yīng),在容器入口處的管道上安裝氣體質(zhì)量流量傳感器實時檢測流入容器內(nèi)部的氣體質(zhì)量流量。快速放氣過程容器內(nèi)部壓力測量方法:在容器放氣過程中,容器內(nèi)部的高壓氣體經(jīng)過容器入口及管道流入外界環(huán)境,由氣體的連續(xù)性方程、伯努利方程及氣體的狀態(tài)方程可以推導(dǎo)得到固定容器在放氣過程中容器內(nèi)部壓力計算公式為其中,P0,T0,r0分別為標(biāo)準(zhǔn)狀態(tài)下氣體的壓力、溫度和密度,其值分別為101.3kPa、273K、1.293kg/m3,T為容器內(nèi)部氣體溫度,其值與容器充氣過程中的數(shù)值相同,c為流出系數(shù),其值等于實際流量除以理論流量,此處取值為1,e為氣體的可壓縮系數(shù),e=1.4,b為容器入口管道直徑與固定容器直徑之比,Pa為容器入口處的壓力,Qout為流出容器的氣體質(zhì)量流量,d2為容器入口管道直徑。由(2)式可知,在固定容器快速放氣過程中,只要檢測到容器入口處的氣體壓力以及流出容器的氣體質(zhì)量流量,即可根據(jù)公式求解得到容器內(nèi)部壓力響應(yīng)。因此,在容器入口處的管道上安裝了氣體質(zhì)量流體傳感器之后還需要安裝壓力傳感器才可以精確獲得固定容器在放氣過程中容器內(nèi)部壓力響應(yīng)。綜上所述,在定容快速充放氣過程中,容器內(nèi)部壓力值的獲得可以通過在緊鄰容器入口處的管道上安裝氣體質(zhì)量流量傳感器和壓力傳感器,如附圖1所示,把檢測得到的數(shù)據(jù)代入公式(1)、(2)中計算即可得到容器內(nèi)部壓力響應(yīng)。該測量方法相對于直接在容器入口檢測容器內(nèi)部壓力,檢測結(jié)果精度顯著提高,可用于在線檢測。測量方案流程圖如附圖2所示。具體實施步驟如下:首先,在緊鄰容器入口處分別安裝氣體壓力傳感器和質(zhì)量流量傳感器,實時檢測固定容器充放氣過程中容器入口處氣壓和氣體質(zhì)量流量。其次,對檢測得到的壓力和流量數(shù)據(jù)進(jìn)行平均化處理,消除白噪聲等干擾信號。最后,把經(jīng)過去噪得到的壓力和流量數(shù)據(jù)代入本發(fā)明所建立的容器內(nèi)部壓力計算公式,即可得到定容快速充放氣過程中容器內(nèi)部氣腔壓力。驗證實例如前所述,由于目前沒有傳感器能直接、有效地到達(dá)密封容積內(nèi)部測量其瞬時壓力,因而難以直接獲得容器內(nèi)真實壓力值,本驗證方案采用數(shù)值仿真方法,通過軟件平臺直接觀測并獲取容器充放氣過程中容器內(nèi)部壓力PM(理論壓力)、容器進(jìn)/出口氣體質(zhì)量流量Q、容器進(jìn)/出口壓力Pa三個重要參數(shù)(標(biāo)準(zhǔn)理論值),將Q、Pa代入計算公式(1)、(2)計算通過本發(fā)明所獲得的容器內(nèi)部瞬時壓力值Pr,并進(jìn)一步比較PM、Pa、Pr三者之間的關(guān)系,從而驗證本發(fā)明的必要性和有效性。首先應(yīng)用計算流體力學(xué)仿真軟件FLUENT對定容脈沖充放氣過程進(jìn)行數(shù)值仿真。數(shù)值建模時取直徑為30mm,長為70mm的圓柱形容器。氣體在容器內(nèi)的流動設(shè)為湍流,氣體的屬性設(shè)置為可壓縮氣體,且不考慮重力的影響。容器入口管道長為200mm,內(nèi)半徑為2mm,氣源壓力設(shè)置為:充氣時300kPa(氣壓源),放氣時為0kPa。過程恒溫為300K??紤]兩種充放氣模式:其一為窄脈沖快速充放氣,周期為40ms,其中充氣時間為15ms,放氣時間為25ms。其二為長時充放氣,周期為125ms,其中充氣100ms,放氣25ms。圖3(a)為脈沖充放氣14ms(充氣階段)時壓力云圖,可以看出,容器內(nèi)壓力并未達(dá)到穩(wěn)態(tài),容器底部壓力最大,但容器入口處壓力與容器內(nèi)部壓力值近似相等,在243kPa~250kPa之間有微小波動。圖3(b)為脈沖充放氣20ms(放氣階段)時壓力云圖,可見放氣時容器內(nèi)部壓力較均勻,容器入口處壓力與容器內(nèi)部壓力相差較大,容器入口壓力在100kPa左右,而容器內(nèi)部壓力在180kPa左右。圖3(c)為長時充放氣70ms(充氣階段)時壓力云圖,可見容器入口處壓力與容器內(nèi)部壓力值更接近;圖3(d)為長時充放氣105ms(放氣階段)時壓力云圖,可見容器內(nèi)壓力均勻,且明顯大于入口壓力,但壓力差值比脈沖快速充放氣時要小。為不失一般性,圖4、圖5分別給出了充放氣周期為40ms和125ms全過程中容器入口處壓力Pa與容器內(nèi)部理論壓力曲線PM,可以看出,兩種情況在充氣過程中,容器內(nèi)部壓力與容器入口處壓力基本相等;但在放氣過程中,容器內(nèi)部的壓力與容器入口處壓力相差較大,且充氣時間越短,放氣時壓差越大。圖6為周期為40ms情況下,PM、Pa、Pr三者之間的關(guān)系比較結(jié)果,以數(shù)值仿真壓力PM為參考標(biāo)準(zhǔn),評價不同測量方法的平均壓力誤差為:其中,i=1表示容器入口參量,i=2表示依據(jù)本發(fā)明所建模型計算得到的參量。計算得到入口觀測壓力相對于容器內(nèi)部壓力平均誤差為模型計算壓力相對于容器內(nèi)部壓力的平均誤差為因此,由本發(fā)明方法所測容器內(nèi)部壓力較在容器口直接安裝壓力傳感器測量內(nèi)部壓力有更高的準(zhǔn)確性。