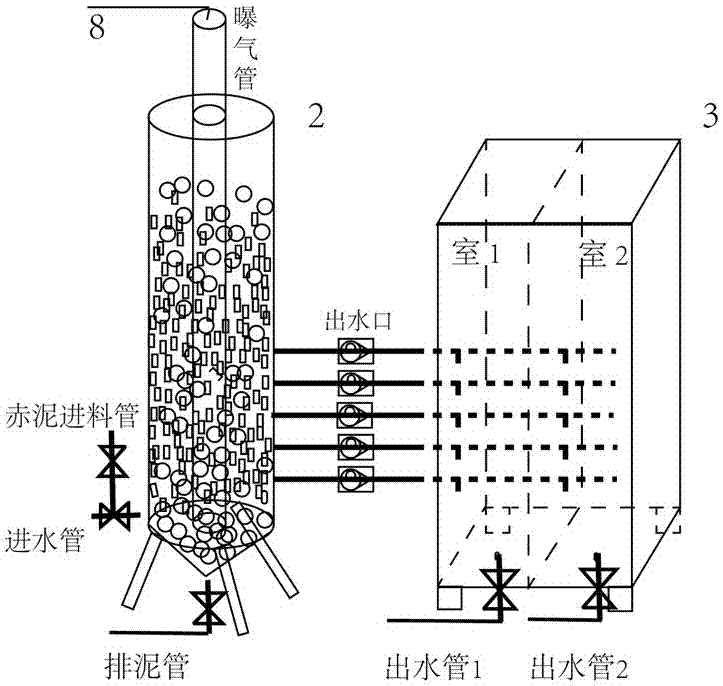
本發(fā)明涉及煉鋁赤泥脫堿和資源化利用的應(yīng)用領(lǐng)域,尤其是電滲析和樹(shù)脂在赤泥脫堿和堿液回收中的工藝應(yīng)用。
背景技術(shù):
:赤泥是煉鋁過(guò)程中產(chǎn)生的高堿性固體顆粒物,依據(jù)其來(lái)源可分為燒結(jié)法、拜耳法和聯(lián)合法赤泥。我國(guó)現(xiàn)階段主要為拜耳法工藝煉鋁產(chǎn)生的赤泥。赤泥從高壓溶出爐中分離出來(lái)后再進(jìn)行洗滌,其洗滌液回流到濕磨爐懸濁液中,洗滌后的殘?jiān)鳛閺U棄赤泥進(jìn)入堆場(chǎng)或進(jìn)行資源回收。我國(guó)赤泥產(chǎn)量達(dá)7000萬(wàn)噸/年,占全球產(chǎn)量的30%,赤泥的最終處置顯得尤為重要。在上世紀(jì)初期,赤泥主要以海洋排放方式為主。七十年代后期至今,赤泥的處置主要以濕法和干法堆存為主,最后進(jìn)行覆土掩埋。然而,這類(lèi)處置方式不僅需要大量的土地面積,也極易導(dǎo)致赤泥中的堿性和有害物質(zhì)進(jìn)入土壤和地下水中,而帶來(lái)嚴(yán)重的環(huán)境污染。赤泥呈灰色或暗紅色,其色度隨著含鐵量的不同而不同,具有較大比表面積(64.09~186.9m2/g),其比重可達(dá)2.1~3.1g/cm3,赤泥含水量86%~90%,90%左右的粒徑為0.075~0.005mm,pH通常高達(dá)12.5~14.0左右。赤泥中的堿主要以游離態(tài)堿和結(jié)合態(tài)堿(即硅鋁酸鈉)2種形式存在,而赤泥中的鈉元素則主要以4種形態(tài)存在,即苛性鈉、鋁酸鈉、硅酸鈉和硅鋁酸鈉。赤泥礦物組成主要為方鈉石(Na2O·Al2O3·1.68SiO2·1.73H2O)、一水硬鋁石(AlO(OH))、方解石(CaCO3)、鈣霞石(3NaAlSiO4·NaOH)、赤鐵礦(Fe2O3)、金紅石(TiO2)、水化石榴石(3CaO·Al2O3·mSiO2·nH2O)等礦物,赤泥中的稀土和稀有金屬則主要呈分散狀態(tài),不均勻地分布在赤泥中?,F(xiàn)有的脫堿技術(shù)主要有:水洗脫堿、石灰脫堿、亞熔鹽脫堿、濕法碳化脫堿、酸浸出、電滲析膜脫堿等。水洗赤泥法能夠有效地去除泥漿中的自由堿和附著堿,液固比5:1,洗滌5次以上,即可去除赤泥中95%以上的Na[張國(guó)立、李紹純、張馨元和王志開(kāi),青島理工大學(xué)學(xué)報(bào),2012,33,59-62]。但是該法需要長(zhǎng)時(shí)間的浸出和水洗,廢液產(chǎn)生多,后續(xù)無(wú)濃縮淡化處理。石灰脫堿是在水熱條件下將其轉(zhuǎn)變?yōu)殁}硅渣將鈉置換出來(lái)進(jìn)入溶液中而脫堿和回收。石灰脫堿法能夠顯著地去除赤泥中的游離堿和結(jié)合堿[ZL200410049747.2]。但活性石灰所加量較大,且難以有效地降低赤泥漿的pH,并增加赤泥量。此外,處理后的高鈣含量赤泥會(huì)對(duì)有價(jià)金屬的提取造成不利影響。亞熔鹽脫堿法。亞熔鹽法是通過(guò)NaOH亞熔鹽在低溫低壓條件下可使氧化鋁的總?cè)艹雎蔬_(dá)到95%以上,溶出后赤泥中Na2O含量13%左右。往該泥漿中加入一定量CaO,在170℃和0.9MPa壓力下可使Na2O含量降至0.90%,鈉硅比降到0.04,符合排放要求,并可作為建筑材料利用[鐘莉和張亦飛,中國(guó)有色金屬學(xué)報(bào),2008,18,70-73]。亞熔鹽脫堿法雖能達(dá)到較好的脫堿和回收效率,但其操作復(fù)雜,需要額外加入NaOH再回收,對(duì)設(shè)備性能要求高,工作環(huán)境差,難以在工程上進(jìn)行有效的應(yīng)用。濕法碳化脫堿法。CO2是酸性氣體,以一定流速通入赤泥漿中可以與堿液進(jìn)行中和。濕法碳化脫堿技術(shù)能夠有效地對(duì)赤泥進(jìn)行脫堿,減輕對(duì)堆場(chǎng)環(huán)境及地下水體的污染,同時(shí)也能夠有效的減少溫室氣體的排放,有助于減輕全球溫室氣體排放的壓力。但CO2的加壓浸出對(duì)浸出設(shè)備的要求較高,需要具有良好的抗壓性和防震性。此外,濕法碳化脫堿法不利于對(duì)赤泥漿中的堿液回收,輸送至生產(chǎn)鋁工藝中重復(fù)利用。酸浸出法。酸浸出法可以有效地中和赤泥中的堿性物質(zhì)并增大其比表面積,浸出赤泥中稀有金屬等。據(jù)報(bào)道,鹽酸對(duì)赤泥的浸出可以將pH降至8,進(jìn)一步的水洗能夠很好地將鈉洗掉[張國(guó)立、李紹純、張馨元和王志開(kāi),無(wú)機(jī)鹽工業(yè),2012,44,40-42]。但不可忽略的是,酸的加入對(duì)堿結(jié)構(gòu)的破壞和鹽化以及所引進(jìn)的陰離子會(huì)對(duì)堿的回收利用造成影響。但其操作環(huán)境差、酸浸出廢液量大并可能帶來(lái)的重金屬浸出風(fēng)險(xiǎn)而造成二次污染的問(wèn)題不可忽略[ZL201380010871.5;ZL201310312592.6]。電滲析膜脫堿法。電滲析脫堿法能夠穩(wěn)定、低成本地處理赤泥附液,但在對(duì)赤泥漿脫堿處理時(shí),容易導(dǎo)致電滲析膜的損壞,壽命較短,進(jìn)而影響使用效率。因此,必須考慮赤泥漿對(duì)膜組件的影響并對(duì)膜組件進(jìn)行改良。僅僅依靠電滲析技術(shù)難以實(shí)現(xiàn)高效低成本的脫堿處理,必須與其他處理工藝相結(jié)合[ZL201511026861.8;ZL201410487005.1]。赤泥的脫堿離不開(kāi)兩種主要手段:中和、轉(zhuǎn)移。由以上
背景技術(shù):
分析可知,加酸中和存在著諸如二次污染、堿液難重復(fù)利用等多種問(wèn)題,而堿液又無(wú)法與赤泥固液完全分離。因此,在水洗轉(zhuǎn)移赤泥附著堿液進(jìn)入液相的基礎(chǔ)上,本發(fā)明提出了一種耦合電滲析和離子交換樹(shù)脂的赤泥脫堿和回收工藝。說(shuō)明內(nèi)容本發(fā)明目的在于提供一種工藝簡(jiǎn)單、能有效脫除赤泥中堿度并實(shí)現(xiàn)資源化利用的一種耦合電滲析和離子交換樹(shù)脂的赤泥脫堿工藝。本發(fā)明主要是采用曝氣水洗法將赤泥附著堿洗脫至液相中,使得赤泥與堿液分離,將赤泥pH降低至10.5以下;再采用電滲析方法進(jìn)行堿液處理和回收,返回至煉鋁工藝中。淡化堿液與水洗后期的低堿度堿液混合,進(jìn)入樹(shù)脂處理系統(tǒng)進(jìn)行深度處理,處理后的淡化出水直接返回至曝氣水洗塔循環(huán)利用(pH=10.0~10.5,TDS=0.5~1g/L)。樹(shù)脂失效后,在本專(zhuān)利中的樹(shù)脂深度處理系統(tǒng)中直接接入電源,即可再生樹(shù)脂并回收堿液。本發(fā)明提出的一種耦合電滲析和離子交換樹(shù)脂的赤泥脫堿工藝,所述赤泥脫堿工藝由赤泥脫堿裝置實(shí)現(xiàn),所述裝置包括水洗塔、電滲析系統(tǒng)和樹(shù)脂處理及再生系統(tǒng),水洗塔由曝氣水洗赤泥塔和儲(chǔ)水塔組成,儲(chǔ)水塔分為室1和室2;所述電滲析系統(tǒng)分為上下兩層,上層為電滲析單元,下層為電極液混合調(diào)節(jié)室和儲(chǔ)水室單元,利用上下層的重力流和蠕動(dòng)泵,進(jìn)行電導(dǎo)液混合循環(huán);包括以下步驟:(1)赤泥預(yù)處理:將煉鋁廠(chǎng)赤泥沉降槽的底泥進(jìn)行轉(zhuǎn)移和攪拌,得到均一分散的赤泥漿,所述赤泥漿的含水率為55~65%;(2)將步驟(1)得到的赤泥漿,用泵輸入至曝氣水洗赤泥塔;(3)在步驟(2)的曝氣水洗赤泥塔中,加水并曝氣水洗,將以附著形式存在于赤泥中的堿經(jīng)過(guò)多次洗脫,進(jìn)入儲(chǔ)水塔中;控制泥水比1:3~1:9;曝氣強(qiáng)度為1L/min~5L/min,每次曝氣時(shí)間為1~3min;(4)在步驟(3)的過(guò)程中,每次水洗結(jié)束后,將曝氣水洗的泥漿進(jìn)行靜置,經(jīng)泥水分離,得到水洗堿液,所得水洗堿液根據(jù)含堿量的不同分別進(jìn)入儲(chǔ)水塔的室1或室2,即初期高堿度的水洗堿液(pH>12.0~12.5,TDS>10g/L)進(jìn)入室1,后期低堿度的水洗堿液(pH<11.0~12.0,TDS<5g/L)進(jìn)入室2;底部脫堿赤泥直接排出,進(jìn)一步壓縮處理并回收利用;(5)將步驟(4)中所產(chǎn)生的高堿度的水洗堿液收集,輸送到電滲析系統(tǒng)中,進(jìn)行濃縮和淡化,回收濃縮堿液并淡化出水;(6)將步驟(4)中所產(chǎn)生的低堿度的水洗堿液和步驟(5)所產(chǎn)生的淡化出水,輸送到樹(shù)脂處理及再生系統(tǒng)中,進(jìn)行深度凈化處理,得到深度處理凈化水;(7)步驟(6)中的樹(shù)脂失效后,采用電滲析-電再生法,再生樹(shù)脂并回收水洗堿液;(8)將步驟(6)產(chǎn)生的深度處理凈化水,輸送至水洗塔中曝氣水洗,多次循環(huán)利用,不產(chǎn)生任何二次污染。本發(fā)明中,從曝氣水洗赤泥塔出來(lái)的水洗堿液,根據(jù)泥水比1:3~1:9,從曝氣水洗赤泥塔的1/2、1/3、1/4、1/5、1/6處通過(guò)重力流進(jìn)入儲(chǔ)水塔中。本發(fā)明中,高濃度的水洗堿液進(jìn)入電滲析系統(tǒng),進(jìn)行淡化和濃縮處理,當(dāng)濃縮液的TDS達(dá)到50~100g/L時(shí),則回收至煉鋁工藝。本發(fā)明中,考慮到隨著pH的下降而產(chǎn)生的氫氧化鋁會(huì)對(duì)膜性能造成影響,電滲析系統(tǒng)淡化出水需要滿(mǎn)足pH為11.6~11.8,TDS為3.50~5.50g/L。本發(fā)明中,樹(shù)脂處理及再生系統(tǒng)中的樹(shù)脂與水洗堿液體積比比為5:1~1:5;此外,在樹(shù)脂處理及再生系統(tǒng)中加入曝氣裝置,以增大樹(shù)脂與堿液的接觸面積以及離子傳質(zhì)的速率。本發(fā)明中,樹(shù)脂處理及再生系統(tǒng)的耦合,達(dá)到了深度處理、再生樹(shù)脂和回收資源的目的。樹(shù)脂深度處理系統(tǒng)置于兩室電滲析結(jié)構(gòu)裝置中的一側(cè),進(jìn)行低濃度堿液的深度處理。兩室電滲析結(jié)構(gòu)裝置的另一側(cè)為陰極室,兩室中間采用陽(yáng)離子交換膜隔開(kāi),在樹(shù)脂再生時(shí)接通兩側(cè)的極板通入直流電源,即可再生并回收金屬鹽離子。本發(fā)明中,樹(shù)脂處理及再生系統(tǒng)的再生室,采用曝氣裝置增大樹(shù)脂和處理堿液的接觸面。同時(shí),在再生階段增大了氫離子和樹(shù)脂的再生接觸面并有利于樹(shù)脂的均勻再生。本發(fā)明中,為避免電滲析淡化出水的堿性偏高對(duì)樹(shù)脂深度處理系統(tǒng)的影響,低濃度的水洗堿液和電滲析淡化出水混合后(pH=11.0~11.8,TDS=3~6g/L),一起進(jìn)入樹(shù)脂深度處理系統(tǒng),出水滿(mǎn)足pH為10.0~10.5,TDS為0.5~1g/L。本發(fā)明中,樹(shù)脂失效后,在樹(shù)脂深度處理系統(tǒng)基礎(chǔ)上接通直流電源,切換到電滲析再生樹(shù)脂模式。本發(fā)明的有益效果如下:1)整個(gè)赤泥脫堿過(guò)程不采用任何藥劑、處理成本低;2)堿回收煉鋁工藝、淡化出水返回水洗塔,進(jìn)行循環(huán)利用;3)無(wú)二次污染,零排放。電滲析裝置全循環(huán)零排放處理、無(wú)工業(yè)廢渣、廢液、廢氣的排放;4)工藝流程適應(yīng)性強(qiáng)。本工藝流程可適于不同規(guī)模、不同工藝煉鋁廠(chǎng)的赤泥處理需求;5)資源回收利用價(jià)值高。較赤泥堆存而言,可大大降低赤泥的處理成本,并帶來(lái)資源回收利用的效益,脫堿后的赤泥堿性下降,可資源化利用;6)操作簡(jiǎn)便,占地面積少。反沖洗設(shè)備和傳送系統(tǒng)具備自動(dòng)化條件,且操作簡(jiǎn)單。在工廠(chǎng)生產(chǎn)運(yùn)行穩(wěn)定時(shí),幾乎不需人員操作。附圖說(shuō)明圖1為本發(fā)明的工藝流程圖。圖2為本發(fā)明中水洗塔裝置示意圖。圖3為本發(fā)明中電滲析系統(tǒng)裝置示意圖。圖4為本發(fā)明中樹(shù)脂處理及再生系統(tǒng)裝置示意圖。圖中標(biāo)號(hào):1.原赤泥漿;2.曝氣水洗赤泥塔;3.儲(chǔ)水塔;4.電滲析系統(tǒng);5.樹(shù)脂處理及再生系統(tǒng);6.水洗泥漿;7.低堿性赤泥;8.曝氣裝置;9.電極板;10.陽(yáng)離子交換膜;11.陰離子交換膜。具體實(shí)施方式下面通過(guò)實(shí)施例進(jìn)一步說(shuō)明本發(fā)明。針對(duì)不同類(lèi)型赤泥,本發(fā)明將結(jié)合實(shí)施例做詳細(xì)說(shuō)明。實(shí)施例1赤泥組分:SiO2Al2O3Fe2O3MgOCaOK2ONa2OCO320.76%20.40%6.44%0.37%17.56%0.88%17.33%12.87%該赤泥泥漿pH為13.78~13.89,堿液堿度為20.52~21.73CaCO3g/L,TDS為30.0~35.0g/L。如圖1所示,本實(shí)施例的工藝過(guò)程如下:1)赤泥預(yù)處理:將煉鋁廠(chǎng)赤泥沉降槽的底泥進(jìn)行轉(zhuǎn)移和攪拌,得到均一分散赤泥漿,含水率55~65%,為原赤泥漿;2)將步驟1)得到的赤泥漿,用泵輸入至水洗塔;3)在步驟2)的水洗塔中,加水形成泥水比為1:3~1:9并曝氣水洗1~3min,將以附著形式存在于赤泥中的堿進(jìn)行多次洗脫,轉(zhuǎn)移至液相;4)在步驟3)的過(guò)程中,每次水洗結(jié)束后靜置曝氣水洗泥漿20~60min,泥水分離,得到水洗堿液。底部脫堿赤泥直接排出,進(jìn)一步壓縮處理并回收利用;5)將步驟4)中赤泥水洗的前2至4次所產(chǎn)生的高含堿量的水洗堿液收集,輸送到電滲析系統(tǒng)中,進(jìn)行濃縮和淡化,回收濃縮堿液并淡化出水;6)將步驟4)中赤泥水洗的后2至3次所產(chǎn)生的低含堿量的水洗堿液和步驟5)所產(chǎn)生的淡化出水,輸送到樹(shù)脂深度處理系統(tǒng)中,進(jìn)行深度處理凈化;7)步驟6)中的樹(shù)脂失效后,采用電滲析法再生樹(shù)脂并回收堿液;8)將步驟6)產(chǎn)生的深度處理凈化水,輸送至水洗塔中曝氣水洗,以此多次循環(huán)利用,不產(chǎn)生任何二次污染。最終赤泥pH降至10.5以下,堿液堿度僅為1.0~2.0CaCO3g/L,TDS<0.5g/L。其中,所涉及的水洗塔裝置、電滲析系統(tǒng)和樹(shù)脂處理及再生系統(tǒng)如以下說(shuō)明(主要構(gòu)造材料為聚氯乙烯,管道材料均采用有機(jī)玻璃):圖2,水洗塔裝置,由曝氣水洗赤泥塔和儲(chǔ)水塔組成,并采用有機(jī)玻璃管靜態(tài)連接,儲(chǔ)水塔分為室1和室2。水洗塔出來(lái)的水洗堿液,根據(jù)泥水比1:3~1:9,從曝氣水洗赤泥塔的1/2、1/3、1/4、1/5、1/6處通過(guò)重力流進(jìn)入儲(chǔ)水塔中,根據(jù)水洗堿液的濃度,分別收集;圖3,電滲析系統(tǒng),分為上下兩層,上層為電滲析單元,下層為電極液混合調(diào)節(jié)室和儲(chǔ)水室單元。其中,電滲析單元采用的是三膜四室結(jié)構(gòu),極板為鍍釕鈦極板,兩張陽(yáng)離子交換膜,一張陰離子交換膜。利用上下層的重力流和蠕動(dòng)泵,進(jìn)行電導(dǎo)液混合循環(huán),有效地控制系統(tǒng)溫度的升高,并保持離子平衡和偏中性環(huán)境。此外,本電滲析裝置中加入了曝氣裝置來(lái)加速離子的傳質(zhì),有效地減少了濃差極化的產(chǎn)生。圖4,樹(shù)脂處理及再生系統(tǒng),分為兩個(gè)部分:樹(shù)脂深度處理系統(tǒng)、失效樹(shù)脂再生系統(tǒng)。樹(shù)脂深度處理系統(tǒng)置于兩室電滲析結(jié)構(gòu)裝置中的一側(cè),進(jìn)行低濃度堿液的深度處理。兩室電滲析結(jié)構(gòu)裝置的另一側(cè)為陰極室,兩室中間采用陽(yáng)離子交換膜隔開(kāi),在樹(shù)脂再生時(shí)接通兩側(cè)的極板通入直流電源,即可再生并回收金屬鹽離子。在樹(shù)脂處理及再生系統(tǒng)中加入曝氣裝置,以增大樹(shù)脂與堿液的接觸面積以及離子傳質(zhì)的速率。實(shí)施例2赤泥組分:SiO2Al2O3Fe2O3MgOCaOK2ONa2OTiO316.0%33.1%5.43%2.58%27.2%0.29%10.08%3.47%該赤泥泥漿pH為12.80~13.00,堿液堿度為10.00~15.56CaCO3g/L,TDS為10.0~15.0g/L?;谙嗨频脑砗头椒?,針對(duì)不同性質(zhì)赤泥(赤泥堿度較低時(shí)),與實(shí)施例1相比,本工藝過(guò)程可以補(bǔ)充為:1)赤泥預(yù)處理:將煉鋁廠(chǎng)赤泥沉降槽的底泥進(jìn)行轉(zhuǎn)移和攪拌,得到均一分散赤泥漿,含水率55~65%;2)將步驟1)得到的赤泥漿,用泵輸入至水洗塔;3)在步驟2)的水洗塔中,加水形成泥水比為1:3~1:9并曝氣水洗1~3min,將以附著形式存在于赤泥中的堿進(jìn)行多次洗脫,進(jìn)入液相中;4)在步驟3)的過(guò)程中,每次水洗結(jié)束后靜置曝氣水洗泥漿20~60min,泥水分離,得到水洗堿液。底部脫堿赤泥直接排出,進(jìn)一步壓縮處理并回收利用;5)將步驟4)中赤泥水洗的前1至2次所產(chǎn)生的高含堿量的水洗堿液收集,輸送到電滲析裝置中,進(jìn)行濃縮和淡化,回收濃縮堿液并淡化出水;6)將步驟4)中赤泥水洗的后1至3次所產(chǎn)生的低含堿量的水洗堿液和步驟5)所產(chǎn)生的淡化出水,輸送到樹(shù)脂深度處理系統(tǒng)中,進(jìn)行深度處理凈化;7)步驟6)中的樹(shù)脂失效后,采用電滲析法再生樹(shù)脂并回收堿液;8)將步驟6)產(chǎn)生的深度處理凈化水,輸送至水洗塔中曝氣水洗,以此多次循環(huán)利用。本發(fā)明所公開(kāi)的工藝,以上雖然列出了較少的實(shí)施例,但對(duì)于本領(lǐng)域的技術(shù)人員,其對(duì)本發(fā)明所做的任何改動(dòng)、改型、改進(jìn)、替換、重新組合等都在本發(fā)明要求保護(hù)的范圍之內(nèi)。當(dāng)前第1頁(yè)1 2 3