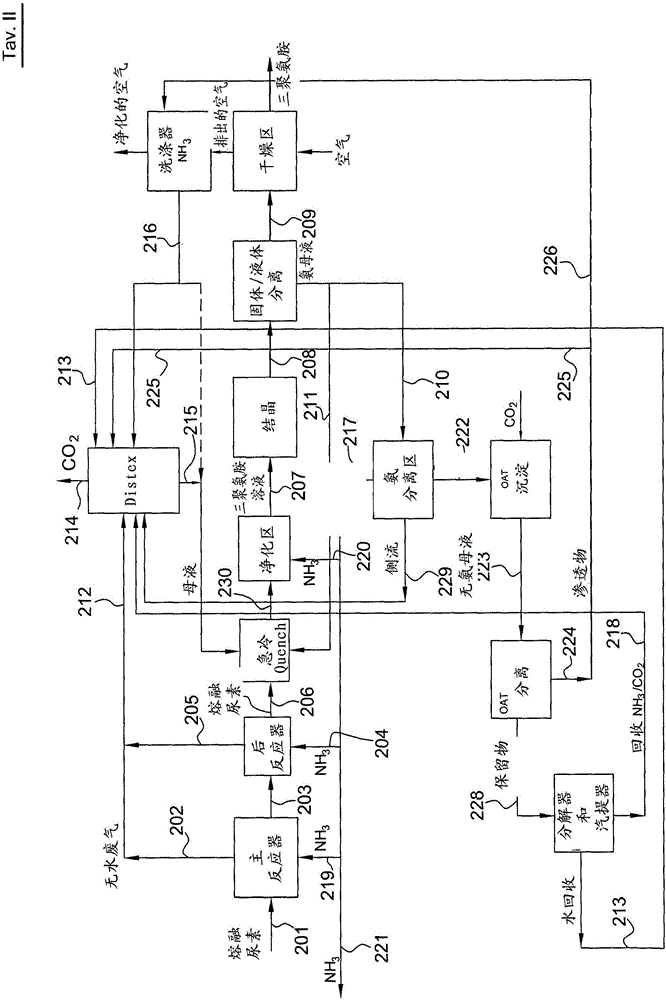
具體的,本發(fā)明涉及一種根據(jù)基于尿素的高壓熱解的合成方法,來生產(chǎn)高純度三聚氰胺的方法,并且同時分離和完全回收在該方法的不同階段所產(chǎn)生的高純度NH3和CO2。在工業(yè)實踐中,由尿素來生產(chǎn)三聚氰胺是在高溫,在NH3存在下,在低壓在合適的催化劑存在下,以及在高壓在不存在催化劑時進(jìn)行的。在兩種情況中,尿素轉(zhuǎn)化成三聚氰胺是根據(jù)以下總反應(yīng)來進(jìn)行的:6NH2CONH2→(CN)3(NH2)3+6NH3+3CO2(1)尿素三聚氰胺廢氣除了主產(chǎn)物(三聚氰胺)之外,還形成了NH3和CO2以及與之一起的更少的但非可忽略的量的本領(lǐng)域技術(shù)人員公知的副產(chǎn)物,在其中分別是氧-氨基-三嗪(OAT)和縮聚物,三聚氰胺熱解和隨后反應(yīng)的中間產(chǎn)物。從總反應(yīng)(1)的化學(xué)計量比,可以推斷出供給到三聚氰胺合成方法的50%的摩爾數(shù)的尿素理論上被轉(zhuǎn)化成NH3和CO2。因此,在離開合成反應(yīng)器的流出物中存在著一定量的CO2和NH3(等于至少1.86kg/1kg所生產(chǎn)的三聚氰胺),以及三聚氰胺。歸因于NH3的高經(jīng)濟(jì)價值,存在在全部三聚氰胺生產(chǎn)方法中回收這種反應(yīng)副產(chǎn)物的問題。用于生產(chǎn)三聚氰胺的最廣泛使用的方法之一是基于尿素的高壓熱解反應(yīng),并且在氨水溶液中回收和凈化三聚氰胺。在這種方法中,離開合成反應(yīng)器的流出物的組成為液相(其含有大部分所生產(chǎn)的三聚氰胺)和氣態(tài)相(其含有大部分的NH3和CO2副產(chǎn)物)。離開反應(yīng)器的全部流出物(氣體和液體)在下文稱作“急冷(Quench)”的具體設(shè)備中與來自于下游區(qū)域的含有CO2的氨水流接觸。含有所生產(chǎn)的全部三聚氰胺的液體流離開該急冷(Quench)的底部,其在除去了所存在的CO2之后,用氨處理來除去縮聚物,反應(yīng)副產(chǎn)物,將OAT保持在溶液中。來自于以上凈化的溶液,通過結(jié)晶和隨后干燥所分離的固體,獲得了高純度的三聚氰胺,并且滴定濃度高于99.8%。NH3和CO2的水飽和的氣態(tài)流(濕廢氣)是從急冷(Quench)頂部萃取的。這種氣態(tài)流通常再循環(huán)到尿素合成設(shè)備(尿素設(shè)備)來回收其中所含的NH3和CO2,因此通過它們(重新)轉(zhuǎn)化成尿素而使得它們立即重新使用。確保上述氣體的回收和再使用的經(jīng)濟(jì)便利性的不可或缺的條件是三聚氰胺設(shè)備是與尿素設(shè)備緊鄰布置的。但是,離開急冷(Quench)的濕廢氣流中水的存在(通常高于20重量%)使得NH3和CO2在尿素設(shè)備中的重新使用是費(fèi)力的,這導(dǎo)致首要的是當(dāng)尿素設(shè)備的規(guī)模小于三聚氰胺設(shè)備時,三聚氰胺生產(chǎn)的總成本的增加。上述的現(xiàn)有技術(shù)的三聚氰胺生產(chǎn)方法在下文中是參考附圖1和2來顯示的,其顯示了所述方法主運(yùn)行階段的簡化方塊圖。在圖1中,將來自于相鄰尿素設(shè)備的熔融尿素流101與無水NH3的氣態(tài)流114一起在135-140℃的溫度供給到熱解反應(yīng)器(反應(yīng)器)。該反應(yīng)器是連續(xù)運(yùn)行的,并且裝備有加熱系統(tǒng),其為反應(yīng)物混合物提供合成三聚氰胺所必需的熱能,將反應(yīng)環(huán)境保持在360-420℃的溫度。反應(yīng)壓力保持在高于70bar的值。該反應(yīng)器是單步反應(yīng)器,并且該反應(yīng)物混合物通過在尿素?zé)峤膺^程中所形成的氣體保持在高循環(huán)。在上述運(yùn)行條件下,熱解反應(yīng)產(chǎn)生了雙相流出物,其組成為含有粗熔融三聚氰胺的液相(其包含減少量的未轉(zhuǎn)化的尿素,和其他反應(yīng)副產(chǎn)物(在其中,最大量是已經(jīng)提及的縮聚物和氧-氨基-三嗪(OAT))和氣態(tài)相(其基本組成為NH3和CO2)。將該雙相流出物102送到急冷(Quench)(其位于所述反應(yīng)器的緊下游),來回收三聚氰胺。在該急冷(Quench)中,雙相流102與來自于設(shè)備其他區(qū)的含有CO2的氨水流103接觸,并且它的溫度降低到大約160℃。在這些條件下,將所述方法中形成的全部的三聚氰胺,未反應(yīng)的尿素和雜質(zhì)送入水溶液或者保持懸浮。將離開Quench的含水流104導(dǎo)向所述方法的隨后階段,而濕廢氣105(處于大約25bar的壓力,基本組成為濕氣飽和的NH3和CO2流)再循環(huán)到相鄰的尿素設(shè)備。除了粗三聚氰胺之外,離開Quench的含水流104包含溶解的,相同量的NH3和CO2,其是在所述方法隨后的步驟中,依靠水蒸氣汽提(CO2-汽提器區(qū))來除去的。CO2的除去對于幫助在隨后的凈化步驟中達(dá)到三聚氰胺的高純度是必需的。氣態(tài)流106離開CO2-汽提器的頂部,其與回收流113和124一起被送到吸收塔(NH3-CO2吸收器)。NH3-CO2吸收器允許在單個含水流103(其再循環(huán)到Quench)中全部回收上述流。沒有CO2(和沒有NH3)的含水流107(其含有在溶液中濃度為6-12重量%的三聚氰胺)與不可忽略量的OAT和縮聚物一起離開CO2-汽提器的底部。歸因于它們的低溶解度,在含有三聚氰胺的含水流進(jìn)行隨后結(jié)晶階段之前,必須除去該縮聚物。該縮聚物的除去是在凈化區(qū)中進(jìn)行的,這里在所加入的氨(流116)存在下將流107加熱到大約170℃,直到達(dá)到12-15重量%濃度。在上述條件下,縮聚物幾乎完全被轉(zhuǎn)化成三聚氰胺。三聚氰胺的氨水流108(基本上不含縮聚物)離開凈化區(qū)和供給到結(jié)晶區(qū),在這里將流108的溫度降低到40-50℃,因此允許大部分的三聚氰胺結(jié)晶。流108中NH3的存在將OAT保持在溶液中,使得高純度三聚氰胺晶體沉淀。將含有懸浮的三聚氰胺晶體的流109送到固體/液體分離區(qū),在其中分離了三聚氰胺的濕餅110和結(jié)晶母液的流111。流111用氨飽和并且包含全部的OAT,其是離開反應(yīng)器的那些以及通過三聚氰胺在生產(chǎn)方法隨后的步驟中水解所形成的那些二者。在水存在下,在高溫下,在進(jìn)行的方法步驟中,特別有利于OAT的形成。在干燥區(qū)中濕餅110最后依靠熱空氣來干燥,獲得了高純度產(chǎn)物,其三聚氰胺滴定濃度高于99.8%。用于干燥的排出的空氣流112通過在NH3洗滌器中水洗來凈化其中存在的NH3。將因此凈化的空氣排入環(huán)境中。通過NH3-CO2吸收器將含有所吸收的氨的含水清洗流113再循環(huán)到所述方法。將流111(由結(jié)晶母液組成,含有濃度為0.8-1.0重量%量級的三聚氰胺)送到氨分離區(qū)。在這個區(qū)域中,通過蒸餾分離了以下產(chǎn)物:無水NH3流115,其與加入的另外的無水NH3再循環(huán)到凈化區(qū);含有可能存在于母液111中的CO2的清洗流123;無NH3的含水流117(其基本上僅僅含有三聚氰胺和OAT)。將流117冷卻到60-70℃的溫度和通過加入CO2中和到pH7,來使得OAT沉淀。流118(其含有處于膠體懸浮的OAT)根據(jù)專利申請WO01/46159所述的內(nèi)容,通過超濾在燭狀陶瓷上進(jìn)行了OAT的分離方法。在OAT超濾區(qū)中,OAT是作為保留物(流119)從滲透物相應(yīng)的流120分離的。后者的流幾乎沒有OAT,并且再循環(huán)到急冷(Quench),來回收其中所含的殘留三聚氰胺。保留物流119(幾乎含有全部的OAT)在分解器-汽提器區(qū)中進(jìn)行了熱處理,在其中OAT,殘留三聚氰胺和其中存在的全部其他有機(jī)物質(zhì)幾乎完全通過水解轉(zhuǎn)化成NH3和CO2,并且形成了:-凈化的含水流(121),其可以排入環(huán)境中:-富含NH3和CO2的濕流(122),其再循環(huán)到NH3-CO2吸收器。上述方法,即使目前應(yīng)用于眾多的化工廠,其特征在于高蒸氣消耗和尿素向三聚氰胺的轉(zhuǎn)化率遠(yuǎn)低于化學(xué)計量比值。此外,該方法受累于氣態(tài)反應(yīng)產(chǎn)物NH3和CO2的費(fèi)力回收,其歸因于相當(dāng)大量的水存在于濕廢氣的流105中。實際上,再循環(huán)到相鄰尿素設(shè)備的濕廢氣中存在的水導(dǎo)致了尿素生產(chǎn)成本的增加,其明顯是通過三聚氰胺生產(chǎn)設(shè)備的管理來維持的。在過去已經(jīng)面臨這個問題,并且嘗試尋找從來自于三聚氰胺合成方法的廢氣和副產(chǎn)物的混合物中分離NH3和CO2的方法,用于獲得純凈氣體,其可以再循環(huán)到尿素設(shè)備,可以存儲和/或釋放到環(huán)境中(CO2)。與現(xiàn)有技術(shù)(其也已經(jīng)描述了CO2蒸餾來獲得高純度CO2的氣態(tài)流(IT1387832,它的方法方案顯示在附圖2中))已知的內(nèi)容相反,本申請人現(xiàn)在令人驚訝地發(fā)現(xiàn)特別的運(yùn)行條件允許獲得一種方法,用于由尿素來制備三聚氰胺,并且分離和回收高純度CO2和NH3,其是改進(jìn)的和優(yōu)化的,以減少量的水來運(yùn)行的,并且在能耗方面具有令人驚訝的結(jié)果。本發(fā)明的目標(biāo)因此是克服目前的現(xiàn)有技術(shù)所揭示的缺點(diǎn)。本發(fā)明的一個目標(biāo)實際上涉及一種由尿素生產(chǎn)三聚氰胺,并且分離和回收高純度CO2和NH3的方法,包括以下運(yùn)行步驟:a)在NH3存在下,通過熱解熔融尿素流在主反應(yīng)器中合成三聚氰胺,獲得熔融粗三聚氰胺流和含有NH3和CO2的廢氣流;b)任選地,在氣態(tài)氨存在下,在后反應(yīng)器中處理離開主反應(yīng)器的熔融粗三聚氰胺流,以完成尿素的熱解反應(yīng),獲得基本上不含未轉(zhuǎn)化的尿素和CO2的熔融粗三聚氰胺流,和主要由NH3組成并且含有反應(yīng)中形成的全部CO2的廢氣流;c)使來自于步驟a)的廢氣流,和如果存在時來自于步驟b)的廢氣流在含水萃取溶劑存在下蒸餾,獲得高純度CO2的氣態(tài)流和含有CO2的氨水流;d)使來自于步驟c)的氨水流進(jìn)行汽提以除去仍然存在的CO2;e)通過使獲自步驟a)的熔融粗三聚氰胺流和當(dāng)存在時來自步驟b)的熔融粗三聚氰胺流與來自步驟c)的氨水流接觸,冷卻和溶解獲自步驟a)的熔融粗三聚氰胺流和當(dāng)存在時來自步驟b)的熔融粗三聚氰胺流,獲得含有溶解的三聚氰胺,縮聚物雜質(zhì)和OAT的氨水溶液;f)通過在NH3存在下保持將縮聚物轉(zhuǎn)化成三聚氰胺,以凈化來自于步驟e)的三聚氰胺的氨水溶液;g)使離開步驟f)的凈化的水溶液中存在的三聚氰胺結(jié)晶,并且使三聚氰胺晶體與所述溶液分離,獲得三聚氰胺濕餅和含有僅僅OAT、溶解的三聚氰胺殘留物和NH3的結(jié)晶母液流;h)蒸餾離開步驟g)的母液,獲得高純度NH3流和無氨的含水流,其含有OAT和三聚氰胺殘留物,其隨后在方法的專門的下游加工區(qū),例如在分解器/汽提器區(qū)中,回收和/或除去;i)用熱空氣干燥來自于步驟g)的三聚氰胺濕餅,獲得具有高純度的干燥的三聚氰胺晶體和含有氨的排出空氣流;所述方法要求用于來自于步驟a)的廢氣流和如果存在時來自于步驟b)的廢氣流的萃取蒸餾的步驟c)在含水萃取溶劑存在下,在55-250bar,優(yōu)選70-170bar的壓力下進(jìn)行。含水萃取溶劑優(yōu)選是水或者無氨的水溶液,甚至更優(yōu)選是再循環(huán)的無氨的水溶液。含水萃取溶劑的存在量是3-6,優(yōu)選4-5噸溶劑/1噸所生產(chǎn)的三聚氰胺。此外,萃取蒸餾步驟c)優(yōu)選在分離裝置(蒸餾塔或者Distex)中進(jìn)行,其由適于經(jīng)受住所需的運(yùn)行條件的材料來生產(chǎn),例如諸如基本組成為鎳、鉻和鉬的組合的合金,或者金屬例如鋯、鈦或者這樣的材料的適合的組合。本發(fā)明的方法所以由一種生產(chǎn)三聚氰胺的方法組成,其對現(xiàn)有技術(shù)進(jìn)行了增強(qiáng)和優(yōu)化,其除了允許以相當(dāng)大的產(chǎn)率增加和降低的成本來生產(chǎn)高純度三聚氰胺之外,還允許-同時分離和回收在三聚氰胺的生產(chǎn)循環(huán)和凈化中所產(chǎn)生/所用的高純度CO2和NH3;-降低水的總用量和將它在三聚氰胺生產(chǎn)方法中完全再循環(huán),和因此消除了液體排出;-CO2的萃取蒸餾在高壓進(jìn)行,其中使用所述壓力允許直接蒸餾離開反應(yīng)器和可能的離開高壓三聚氰胺合成方法的后反應(yīng)器的廢氣,而無需中間處理來將它們處于如現(xiàn)有技術(shù)的方法所述的萃取塔的運(yùn)行壓力(其在低于50bar的壓力運(yùn)行);-CO2的萃取蒸餾,其即使在高壓進(jìn)行,也具有減小的能耗,其可以甚至相對于低壓運(yùn)行時減半。此外,本發(fā)明方法的一個基本方面是設(shè)計來處理含有CO2和NH3的廢氣,來獲得高純度CO2和NH3,其中高純度CO2的氣態(tài)流在第一步驟中分離,并且高純度NH3流在隨后的步驟中分離。此外,在三聚氰胺的生產(chǎn)和凈化循環(huán)中所產(chǎn)生的/所用的含有CO2和NH3的廢氣流(其是根據(jù)本發(fā)明的方法處理的)可以在同一設(shè)備(其中存在萃取性蒸餾塔)中產(chǎn)生,或者它們可以來自于其他三聚氰胺生產(chǎn)設(shè)備(通常稱作高壓或者低壓設(shè)備,沒有裝備萃取塔或者Distex)的單個或多個組合。本發(fā)明的另一個目標(biāo)涉及從來自于生產(chǎn)三聚氰胺的設(shè)備的廢氣中分離和回收高純度CO2和NH3的特別的系統(tǒng),所述系統(tǒng)包括以下元件:萃取CO2的第一蒸餾塔,其適于用含水萃取溶劑例如水來運(yùn)行;第二分離塔,其適于從頂部回收離開第一萃取蒸餾塔底部的料流中存在的CO2和NH3;第三分離塔,其適于從頂部回收離開第二塔頂部的料流中存在的NH3,所述元件適于進(jìn)行從所述廢氣中分離和回收高純度CO2和NH3的料流的步驟。所述系統(tǒng)可用于修整現(xiàn)有的生產(chǎn)三聚氰胺的設(shè)備的情況中和/或用于集成現(xiàn)有的生產(chǎn)三聚氰胺的設(shè)備與生產(chǎn)尿素的設(shè)備。本發(fā)明系統(tǒng)目標(biāo)例如可以用于分離和回收在由尿素來生產(chǎn)三聚氰胺的方法中所產(chǎn)生的高純度CO2和NH3,包括前述運(yùn)行步驟a)-i)。本發(fā)明提出的方法使用簡單,但是相對于現(xiàn)有技術(shù)已知的方法來說發(fā)生了明顯改變。附圖說明圖1是現(xiàn)有技術(shù)的三聚氰胺生產(chǎn)方法的圖。圖2是現(xiàn)有技術(shù)的三聚氰胺生產(chǎn)方法的圖。圖3是本發(fā)明的由尿素來合成三聚氰胺的方法的圖。本發(fā)明的由尿素來合成三聚氰胺的方法以及來自于其的優(yōu)點(diǎn)可以從下面的說明書而更清楚地理解,其參考了圖3,其顯示了一種優(yōu)選的實施方案的主運(yùn)行步驟的簡化的方案。說明書和相關(guān)的方法方案應(yīng)當(dāng)被認(rèn)為是本發(fā)明的示例,決不代表對于附加權(quán)利要求范圍的限制。應(yīng)當(dāng)首先觀察本發(fā)明下面的特有特征,即,不再限制尿素設(shè)備與三聚氰胺生產(chǎn)單元相鄰,因為本發(fā)明的方法不再產(chǎn)生含有NH3和CO2的任何廢氣混合物(濕廢氣或者無水廢氣),僅僅歸因于這種相鄰,含有NH3和CO2的任何廢氣混合物的回收和傳送到尿素設(shè)備才是經(jīng)濟(jì)上可行的。另外,在本發(fā)明方法的萃取蒸餾步驟中具體的壓力條件允許獲得一種優(yōu)化的方法,其是以降低量的水來運(yùn)行的,并且具有在能耗方面令人驚訝的結(jié)果。這些具體特征使得本發(fā)明的方法相對于迄今所用的和/或所提出的用于由尿素來生產(chǎn)三聚氰胺的全部高壓技術(shù)是獨(dú)特的。將熔融尿素流301供給到第一反應(yīng)器(主反應(yīng)器),其中高壓熱解方法在常規(guī)條件下進(jìn)行,即在無水氨(流319)存在下,在360-420℃的溫度和高于70bar的壓力進(jìn)行。與圖2所示的現(xiàn)有技術(shù)的三聚氰胺生產(chǎn)方法相反,熱解反應(yīng)所產(chǎn)生的流出物的兩種組分(即,由NH3和CO2組成的無水廢氣流302和由熔融粗三聚氰胺組成的液體流303)是分別從主反應(yīng)器,或者從圖3未示出的位于下游的合適的相分離器來萃取的,并且分別處理。在圖3所示的本發(fā)明的實施方案中,將流303送到第二反應(yīng)步驟(后反應(yīng)器),在其中在與主反應(yīng)器相同的溫度和壓力條件下和在無水氨的連續(xù)流(流304)存在下運(yùn)行,完成了離開主反應(yīng)器的流303中仍然存在的未反應(yīng)的尿素的轉(zhuǎn)化,同時完成了導(dǎo)致形成三聚氰胺的中間反應(yīng)。同時,該后反應(yīng)器中存在的條件(在其中氨分壓遠(yuǎn)高于主反應(yīng)器)也導(dǎo)致主反應(yīng)器中所產(chǎn)生的熔融粗三聚氰胺中的縮聚物和OAT的減少。存在后反應(yīng)器的另一有益效果是降低了液相(即,熔融粗三聚氰胺流)中存在的CO2的量,這也歸因于連續(xù)進(jìn)入的NH3氣態(tài)流的汽提效應(yīng)。但是,該方法的步驟b)是任選的。本發(fā)明的方法實際上允許生產(chǎn)高純度三聚氰胺,以及無需后反應(yīng)器的幫助,來分別回收NH3和CO2。兩種分別的流也離開后反應(yīng)器,都不含水:廢氣流305(主要由NH3組成)和液體流306(由熔融粗三聚氰胺組成,幾乎不含尿素和CO2,含有非常有限量的高沸點(diǎn)副產(chǎn)物例如OAT和縮聚物)。離開后反應(yīng)器或者來自于圖3未示出的位于下游的合適的分離器的廢氣流305,與離開主反應(yīng)器的廢氣流302合并,來在如下所述的特定萃取蒸餾塔(下文稱作“Distex”)中處理。另一方面,通過溶解在氨水溶液中,將離開后反應(yīng)器的熔融粗三聚氰胺流306送到三聚氰胺的回收步驟。這個步驟是在特定設(shè)備(下文稱作“Quench”)中進(jìn)行的,在其中熔融粗三聚氰胺流306在110-180℃,優(yōu)選150-170℃的溫度與主要由離開CO2汽提器的氨水流組成的氨水流(其含有顯著濃度的NH3,但是幾乎沒有CO2)(流315a)接觸。在這些條件下,縮聚物的初步破壞是在Quench設(shè)備中進(jìn)行的。離開Quench的三聚氰胺溶液然后送到凈化區(qū)(流330),用于縮聚物的完全破壞。離開Quench的含有三聚氰胺的水溶液330的凈化是在本領(lǐng)域已知的壓力和濃度條件下進(jìn)行的,但是處于較低的溫度。離開凈化區(qū)的凈化的三聚氰胺的氨水溶液307然后供給到結(jié)晶區(qū),在這里類似于圖2的現(xiàn)有技術(shù)的方法,該溶液的溫度降低到40-50℃,獲得極純?nèi)矍璋肪w的分離。將含有懸浮的三聚氰胺晶體的流308送到固/液分離區(qū),并且分離三聚氰胺的濕餅309和由結(jié)晶母液組成的含水流310。從干燥區(qū)中回收高純度的無水結(jié)晶三聚氰胺(滴定濃度高于99.8重量%)。含有氨的結(jié)晶母液流310部分直接再循環(huán)到Quench(流310a)和部分供給到氨分離區(qū)(流310b),它的主要功能是回收全部的高純度NH3。NH3在這個區(qū)中的分離是依靠蒸餾進(jìn)行的,類似于現(xiàn)有技術(shù)的三聚氰胺生產(chǎn)方法。氣態(tài)流312(其來源于兩種無水廢氣流302和305的組合,這二者分別來自于主反應(yīng)器和后反應(yīng)器,并且用三聚氰胺蒸氣飽和)在特定蒸餾塔(Distex)中,在選自水和無氨的水溶液的含水萃取溶劑存在下進(jìn)行萃取蒸餾,所述含水萃取溶劑在塔中從頂部向下行進(jìn)相對于上升的氣態(tài)流逆流。該含水萃取溶劑優(yōu)選是來自于分解器/汽提器區(qū)、來自于設(shè)備下游區(qū)域的再循環(huán)的無氨的水溶液(流313和325)。將由高純度CO2組成的氣態(tài)流314(NH3含量低于10ppm)在塔的運(yùn)行壓力下從Distex的頂部排出,而氨水流315(具有低含量的CO2,含有存在于流312中的三聚氰胺,其因此回收)從Distex的底部排出。將離開Distex的全部含水流315送到CO2汽提塔,用于從底部溶液中完全除去CO2,并且該底部溶液從這里送到Quench作為用于回收離開后反應(yīng)器的三聚氰胺的溶劑。將來自于NH3洗滌器的流316(其含有氨,其已經(jīng)作為濕三聚氰胺餅干燥的結(jié)果而形成)供給到Quench作為含水溶劑。純NH3流320也供給到Quench來獲得凈化步驟所需的NH3濃度。因此,從凈化區(qū)流向下游的氨水流307包含所述方法產(chǎn)生的全部NH3,即其來源于尿素?zé)峤?參見反應(yīng)(1))和其來源于水解反應(yīng)(特別是來自于下文所述的分解器/汽提器區(qū))。流310b中所含的氨總量以高純度(317)通過在氨分離區(qū)中蒸餾而分離。含有OAT和在溶液中溶解的三聚氰胺殘留物的無氨的水流322也從氨分離區(qū)中分離。本發(fā)明的方法目標(biāo)因此還允許在完全回收三聚氰胺生產(chǎn)方法中所產(chǎn)生的全部CO2(處于高純度)之后,完全回收在三聚氰胺生產(chǎn)區(qū)中所產(chǎn)生的全部氨(處于高純度)。形成流317的處于液態(tài)的純NH3部分地用于所述生產(chǎn)方法的不同點(diǎn),例如諸如主反應(yīng)器(流319),后反應(yīng)器(流304)和凈化區(qū)(流320),而多余的NH3(其代表了最相關(guān)的部分)被傳遞到設(shè)備界區(qū)(batterylimitoftheplant)(流321),并且可以轉(zhuǎn)移到尿素設(shè)備或者作為高商業(yè)價值的副產(chǎn)物來回收,其可以在其他工業(yè)方法中用作原材料。將作為氨分離區(qū)的底部產(chǎn)物排出的無氨的水流322送到分解器/汽提器區(qū),在其中除了存在的其他有機(jī)分子之外,將OAT和殘留三聚氰胺依靠高溫?zé)峤鈦矸纸獬砂焙投趸?。將NH3和CO2在同一區(qū)域中通過汽提分離作為頂部產(chǎn)物和再循環(huán)(流318)到Distex,而將幾乎純凈水流從底部回收,并且再循環(huán)到Distex作為萃取蒸餾(325)的溶劑或者送到洗滌器以清洗來自于干燥器(流313)或者干燥區(qū)的排出的空氣。該干燥步驟可以實際上用熱空氣或者本領(lǐng)域技術(shù)人員已知的其他手段來進(jìn)行??赡艽嬖谟诹?10(結(jié)晶母液)中的少量CO2是在氨分離區(qū)中以CO2的氨水混合物的形式分離,如現(xiàn)有技術(shù)已知的,并且傳送(清洗流329)到Distex來回收它們。在生產(chǎn)循環(huán)中所形成的全部CO2(通過熱解和水解)然后以高純度下在Distex中作為頂部產(chǎn)物分離,并且在設(shè)備界區(qū),在70-170bar的優(yōu)選壓力下可利用(流314)。類似于NH3,CO2也可以轉(zhuǎn)移到尿素設(shè)備或者作為原材料回收,用于其他工業(yè)方法中。根據(jù)本文所示的實施方案,用于由尿素來生產(chǎn)三聚氰胺,并且分離回收高純度副產(chǎn)物氨和二氧化碳的方法,包括以下基本操作步驟:-將離開三聚氰胺合成反應(yīng)器的廢氣流在萃取蒸餾塔中,使用水作為萃取溶劑或者水溶液進(jìn)行蒸餾,和優(yōu)選以3-6,優(yōu)選4-5噸溶劑/噸三聚氰胺的量回收含水流,并且在55-250bar,優(yōu)選70-170bar的壓力下運(yùn)行,獲得高純度CO2氣態(tài)流和氨水流,用于回收和凈化在所述反應(yīng)中所生產(chǎn)的三聚氰胺,并且特別地降低了能耗。由結(jié)晶下游的固/液分離步驟所形成的氨水流然后蒸餾,獲得高純度氨流和無氨的水流,其含有殘留三聚氰胺,OAT和其他少量有機(jī)雜質(zhì)(送去回收或者除去)。在本發(fā)明方法的一種優(yōu)選的實施方案中,所回收的高純度NH3和CO2流合適地分別供給到尿素設(shè)備,相對于包含在廢氣流中、但是沒有分離的這些物質(zhì)的供料流具有特別的優(yōu)點(diǎn)??蛇x擇地,上述流之一或者二者適于用作其他工業(yè)生產(chǎn)方法中的原材料。本發(fā)明所以涉及一種新的循環(huán),以在三聚氰胺生產(chǎn)方法中,通過尿素?zé)峤猓瑏慝@得高純度NH3和CO2的分離和回收,所述循環(huán)包括:-由主反應(yīng)器和后反應(yīng)器組成的反應(yīng)區(qū),其中進(jìn)行熱解,并且尿素高轉(zhuǎn)化成三聚氰胺,并且分離了由NH3、CO2和三聚氰胺蒸氣組成的無水廢氣流;-萃取蒸餾塔(Distex),其連接到所述反應(yīng)區(qū)上,并且從該反應(yīng)區(qū)接收所述廢氣流,所述Distex優(yōu)選使用來自于三聚氰胺的回收和凈化循環(huán)的無氨的水溶液作為萃取溶劑,分離了由高純度CO2組成的頂部產(chǎn)物和含有NH3和殘留三聚氰胺的含水底部流;該高純度CO2流是在優(yōu)選的壓力70-170bar(即,在與它離開反應(yīng)器時相同的壓力)下蒸餾的,而無需任何中間處理;汽提區(qū),用于從無氨的水溶液中除去殘留CO2;-Quench區(qū)和凈化區(qū),用于依靠來自于所述生產(chǎn)循環(huán),可能加入了NH3的氨水流來回收和凈化三聚氰胺;-凈化的三聚氰胺的結(jié)晶沉淀區(qū),其連接到產(chǎn)物的分離和干燥區(qū);-氨分離區(qū),由結(jié)晶母液來通過蒸餾生產(chǎn)高純度氨,用于所述循環(huán)的內(nèi)部所需,多余的NH3以高純度傳遞到界區(qū),來轉(zhuǎn)移到尿素設(shè)備或者用于市場銷售;-其用于處理離開氨分離區(qū)的無氨的母液的區(qū)域,由此進(jìn)行對包含在其中的三聚氰胺的合適的回收,和/或熱破壞所存在的全部其他有機(jī)物質(zhì),并且全部回收所形成的NH3和CO2;來源于這個作業(yè)系列的含水流形成了Distex的大部分萃取溶劑需求。本發(fā)明的目標(biāo),通過高壓熱解尿素來生產(chǎn)高純度三聚氰胺的方法允許相對于現(xiàn)有技術(shù)已知的方法來獲得下面的優(yōu)點(diǎn):1)以高純度和分別地完全回收在三聚氰胺合成反應(yīng)(反應(yīng)(1))中所產(chǎn)生的或者在三聚氰胺的回收和凈化循環(huán)中形成的氣態(tài)副產(chǎn)物CO2和NH3。相對于現(xiàn)有技術(shù)已知的廢氣(濕的或者無水)再循環(huán)到尿素設(shè)備的實踐,作為本發(fā)明目標(biāo)的CO2和NH3的新回收模式能夠解決與現(xiàn)有技術(shù)實踐運(yùn)行相關(guān)的全部問題。作為傳統(tǒng)的廢氣流再循環(huán)的替代選項,將高純度NH3和CO2分別再循環(huán)到尿素設(shè)備,其導(dǎo)致了:a)CO2到尿素的各途徑轉(zhuǎn)化率(conversionforeachpassage)相當(dāng)大的增加,和因此以相同的投資獲得了增加了生產(chǎn)能力,和降低了尿素的生產(chǎn)成本;b)顯著降低了運(yùn)行尿素設(shè)備所必需的能耗例如蒸氣和/或電能,另外還相當(dāng)大地改進(jìn)了來自于相同尿素設(shè)備的能量回收模式;c)供料流到尿素設(shè)備的壓縮成本的降低,特別是CO2,其是在三聚氰胺設(shè)備的界區(qū),在優(yōu)選的壓力70-170bar下可利用的;d)中間處理成本的降低,其將離開三聚氰胺反應(yīng)器的廢氣帶到壓力低于50bar,在此蒸餾塔根據(jù)現(xiàn)有技術(shù)運(yùn)行;e)在再循環(huán)中所涉及的裝置和生產(chǎn)線較少的腐蝕問題;f)尿素合成方法的整體改進(jìn)的運(yùn)行可靠性和可利用性;2)本發(fā)明的生產(chǎn)三聚氰胺的方法不需要供給另外的NH3和CO2流。該方法要求實際上是通過將在不同的方法步驟副產(chǎn)的和回收的NH3部分地再使用/再循環(huán)而集成的和專門滿足的;3)通過水解三聚氰胺所形成的OAT減少,這不僅歸因于降低了高溫運(yùn)行裝置的數(shù)目和體積的效果,而且還是作為溫度本身降低的結(jié)果。該凈化實際上可以在比現(xiàn)有技術(shù)低了5-10度的溫度下進(jìn)行。除了作為尿素的更高轉(zhuǎn)化率(歸因于后反應(yīng)器的插入)的結(jié)果而獲得的產(chǎn)率提高之外,這導(dǎo)致了所述方法總產(chǎn)率的進(jìn)一步增加;4)在生產(chǎn)尿素之外的工業(yè)方法中使用NH3和CO2二者的可能性;因為兩種化合物是以高純度和分別回收的,它們可用于不同的用途和具有可能更高的附加值;5)水的總用量減少,并且它完全再循環(huán)到三聚氰胺的生產(chǎn)方法,結(jié)果是消除了液體排出;6)CO2的萃取蒸餾雖然在高壓進(jìn)行,但是具有降低的能耗;7)本發(fā)明的三聚氰胺生產(chǎn)方法可以與在任何已知技術(shù)的現(xiàn)有尿素設(shè)備中進(jìn)行的生產(chǎn)尿素的方法相結(jié)合,這明顯降低了停機(jī)時間和用于所述設(shè)備現(xiàn)代化和改造所必需的介入性技術(shù)改變。下文提供了本發(fā)明方法的一種實施例子,用于本發(fā)明的說明性和非限定性目的。實施例1在根據(jù)本發(fā)明所構(gòu)建的生產(chǎn)高純度三聚氰胺的設(shè)備中,如圖3所示,將熔融尿素流301以流速22650kg/h與1500kg/h量的無水氨流319一起送到主反應(yīng)器。然后將離開主反應(yīng)器的液體流303送到隨后的后反應(yīng)器,在這里在幾乎沒有CO2的環(huán)境中完成了三聚氰胺的合成反應(yīng),這也歸因于通過在底部上連續(xù)引入的1600kg/h的氣態(tài)NH3流304的汽提效應(yīng)。然后從該后反應(yīng)器中獲得液體流出物(流306),其等于7600kg/h的粗三聚氰胺,含有減少量的OAT和縮聚物(分別是0.6和1.0重量%)。兩個反應(yīng)器都是在380℃的溫度和80bar的壓力下運(yùn)行的。將由三聚氰胺蒸氣飽和的NH3和CO2所組成的氣相302和305從所述兩個反應(yīng)器中分離,并且合成單個流312,將其送到萃取蒸餾塔(Distex),用于三聚氰胺回收和高純度CO2分離。該Distex是在壓力75bar下使用的,采用來自于隨后的運(yùn)行階段的30000kg/h的含水流325作為萃取溶劑。具體的,相對于同等方法(在其中Distex中的蒸餾是在壓力35bar進(jìn)行的),用作本發(fā)明方法中的萃取溶劑的含水流的量小于280%。8950kg/h的極純的和基本上無水的CO2(并且NH3含量低于10ppm)從Distex頂部分離,形成氣態(tài)流314,其在界區(qū)在75bar壓力下是可用的。從Distex底部排出的含水流315包含了與流318,325和329一起進(jìn)入所述方法的全部的氨和三聚氰胺,并且具有極小量的殘留CO2。將含水流315送到CO2汽提器來從該含有氨和三聚氰胺的含水流中全部除去CO2。將塔頂部的流(315b,其含有流315全部的CO2和部分的氨)送到氨的分離區(qū);將底部流315a送到Quench,來回收來自于后反應(yīng)器的粗三聚氰胺(306流)。將離開Quench的全部產(chǎn)物(流330)送到凈化區(qū),其在壓力25bar和溫度165℃運(yùn)行。將等于9000kg/h量的另外的氨(流320)加入凈化區(qū)來獲得縮聚物向三聚氰胺的完全轉(zhuǎn)化。將凈化的三聚氰胺的含水流307(其含有小于100ppm的縮聚物)冷卻到40-50℃,并且在結(jié)晶區(qū)中減壓至大氣壓,在其中獲得了三聚氰胺晶體沉淀。三聚氰胺晶體在母液中的懸浮液(流308)然后從結(jié)晶器送到離心機(jī)潷析器,因此將濕晶體餅與結(jié)晶母液分離。該餅然后在特定干燥區(qū)中干燥,生產(chǎn)了7500kg/h的無水三聚氰胺,其具有高純度(滴定濃度高于99.8重量%和濕度低于0.1重量%)。離開離心機(jī)潷析器的結(jié)晶母液的流310然后送到氨分離區(qū),這里在20bar壓力下運(yùn)行,回收了18800kg/h的極純氨,并且其部分地用于同一生產(chǎn)三聚氰胺的方法(流304,319和320)和大部分作為設(shè)備的副產(chǎn)物在界區(qū)可利用(流321)(6700kg/h的液態(tài)NH3)。在氨分離區(qū)底部所產(chǎn)生的流322由71000kg/h的無氨的母液組成。流322包含了在設(shè)備上游區(qū)域所產(chǎn)生的全部OAT,并且在結(jié)晶條件下用三聚氰胺飽和(大約0.8-1.0重量%)。將流322送到所述設(shè)備的最后區(qū)(分解器/汽提器)用于通過OAT的高溫水解來破壞殘留三聚氰胺和其他有機(jī)副產(chǎn)物。流322實際上首先加熱到280℃,然后送到分解器/汽提器區(qū),在這里全部的有機(jī)材料(OAT,三聚氰胺,其他副產(chǎn)物)通過水解被破壞和轉(zhuǎn)化成NH3和CO2,在這些氣體在汽提器中分離之后留下幾乎純凈的含水流(流313)作為液體殘留物,其含有小于100ppm的總固體產(chǎn)物和小于10ppm的游離NH3,將其用于清洗在洗滌器中所排出的空氣流。在分解器中形成的氣體和在同一區(qū)的汽提器頂部所分離的那些(流318)在Distex中進(jìn)行了萃取蒸餾,來回收CO2和然后回收NH3。將離開分解器的部分的無氨的含水流用作Distex的萃取溶劑。該生產(chǎn)方法的總產(chǎn)率被證實等于0.33kg的三聚氰胺/1kg尿素,其對應(yīng)于3.02kg尿素/1kg所生產(chǎn)的高純度三聚氰胺的特定消耗。以下流也獲自所述方法:-純度高于99.9%(基于濕物)和在75bar壓力下的CO2流,其量等于0.395kg/1kg所消耗的尿素;-無水和液體NH3流,滴定濃度是99.9%,其量是0.296kg/1kg所消耗的尿素。此外,相對于同等方法(在其中Distex中的蒸餾是在35bar壓力下進(jìn)行的,并且萃取溶劑的量等于85000kg/h),本發(fā)明方法的能量平衡如下:實施例2用下面的Distex運(yùn)行壓力來重復(fù)實施例1所述的方法:-55bar-170bar。在下表1中,在這些壓力所測量的值還與根據(jù)WO01/46159的教導(dǎo)在35bar和根據(jù)實施例1在75bar下進(jìn)行的的測試過程中所測量的相應(yīng)的值進(jìn)行了比較。表1壓力355575170bar吸收到Distex的水流速(流325)85000575003000011250kg/h液體流318流速4200420042004200kg/hDistex所需蒸氣的小時流速2300016500990013000kg/hCO2汽提器所需蒸氣的小時流速1200011500107004700kg/h上表所示結(jié)果顯示了相對于根據(jù)WO01/46159的教導(dǎo)在35bar進(jìn)行的Distex,在用Distex在55bar,75bar和170bar進(jìn)行的方法的情況中,總蒸氣消耗的如下減少:55bar=-4000kg/h75bar=-14400kg/h170bar=-17300kg/h此外,在能量平衡中,為了還考慮在較高的壓力將溶劑和再循環(huán)流引入萃取性蒸餾塔的能耗,測量了表2所示的值。表2表2的內(nèi)容顯示了甚至考慮為了達(dá)到萃取蒸餾塔中更高的壓力所消耗的能量時,相對于根據(jù)WO01/46159的教導(dǎo)在35bar進(jìn)行的Distex,在用Distex在55bar,75bar和170bar進(jìn)行的本發(fā)明的方法的情況中,也獲得了蒸氣總消耗的相當(dāng)大的減少。當(dāng)前第1頁1 2 3